Электрохимия, 2020, T. 56, № 2, стр. 133-140
Слоистые твердоэлектролитные мембраны на основе диоксида циркония: особенности технологии изготовления
О. Ю. Задорожная a, *, Е. А. Агаркова b, О. В. Тиунова c, Ю. К. Непочатов a
a АО “НЭВЗ-КЕРАМИКС”
630049 Новосибирск, Красный просп., 220, Россия
b Федеральное государственное автономное образовательное учреждение высшего образования
“Московский физико-технический институт (государственный университет)”
117303 Московская обл., Долгопрудный, Институтский пер., 9, Россия
c Федеральное государственное автономное образовательное учреждение высшего образования
“Национальный исследовательский Томский политехнический университет”
634050 Томск, просп. Ленина, 30, Россия
* E-mail: olgazador@mail.ru
Поступила в редакцию 25.12.2018
После доработки 12.03.2019
Принята к публикации 13.06.2019
Аннотация
Мембрана из твердого электролита является ключевой частью твердооксидного топливного элемента (ТОТЭ). В данной работе приводятся результаты исследования влияния дисперсности исходных порошков, композиции органических добавок в суспензии и технологических параметров изготовления на качество трехслойных керамических пластин твердого электролита размером 100 × 100 мм и толщиной 0.15 мм, изготовленных методом литья на движущуюся ленту. В качестве состава для центрального слоя использован 10Sc1YSZ (10 мол. % Sc2O3, 1 мол. % Y2O3, 89 мол. % ZrO2) – материал с наиболее высокой кислород-ионной проводимостью среди твердых растворов на основе диоксида циркония. Для крайних слоев выбран 6ScSZ (6 мол. % Sc2O3, 94 мол. % ZrO2). Трехслойная архитектура твердоэлектролитных мембран позволяет улучшить механические характеристики при сохранении необходимых функциональных свойств (в первую очередь – анионной проводимости). Работа посвящена оптимизации технологии изготовления таких слоистых мембран методом пленочного литья.
ВВЕДЕНИЕ
Твердооксидные топливные элементы (ТОТЭ) представляют собой устройства преобразования энергии, способные генерировать электроэнергию с высоким КПД (до 60% по электрической энергии и до 90% с учетом тепловой энергии), и считаются одной из ключевых технологий для будущей экономики водородной энергетики. Электролиты производимых в настоящее время ТОТЭ состоят из диоксида циркония, стабилизированного иттрием (YSZ) и/или скандием (ScSZ), поскольку эти материалы обладают высокой ионной проводимостью и отличной химической, термической и механической стабильностью. Помимо этих характеристик, электролит должен быть газонепроницаемым с плотностью выше 94–95% от теоретической. При изготовлении ТОТЭ планарного типа наиболее распространенным методом для производства тонких пластин является пленочное литье, поскольку эта технология позволяет получить керамические листы контролируемой толщины, имеющие большую площадь. Ранее нами докладывались результаты по изготовлению однослойных мембран толщиной 200–250 мкм данным методом [1]. Метод пленочного литья позволяет получить компоненты ТОТЭ электролит- и анод-поддерживающей конструкций [2–5] толщиной 0.01–1.5 мм [6–8].
Одним из наиболее значимых факторов процесса пленочного литья является состав шликера, оказывающий влияние на характеристики как неотожженных, так и спеченных лент. Основные требования, предъявляемые к шликеру для пленочного литья:
– высокое содержание твердой фазы для формирования прочной ленты в процессе литья и сушки;
– отсутствие агломератов частиц и оптимальный гранулометрический состав керамического порошка для получения однородной ленты;
– реологические свойства, позволяющие получить ленту без дефектов.
Ламинирование неспеченных лент позволяет повысить толщину электролита и сформировать многослойную структуру [9, 10]. Характеристики спеченных пластин также зависят от условий спекания: скорости, температуры, времени выдержки при максимальной температуре и приложенной во время спекания нагрузки [11–13].
Целью настоящей работы было исследование ключевых параметров на различных стадиях изготовления пластин твердого электролита на свойства финальных пластин и оценка оптимального дисперсного состава порошков, состава шликера и технологических параметров, позволяющих эффективно осуществлять массовое производство пластин твердого электролита размером 100 × 100 × 0.15 мм для ТОТЭ. Трехслойная структура изготавливаемых мембран была ранее запатентована [14].
МЕТОДИКА ЭКСПЕРИМЕНТА
Для проведения работ использовали порошки диоксида циркония, стабилизированного скандием 6ScSZ (94 мол. % ZrO2 + 6 мол. % Sc2O3), и диоксида циркония, стабилизированного скандием и иттрием 10Sc1YZ (89 мол. % ZrO2 + + 10 мол. % Sc2O3 + 1 мол. % Y2O3) производства ЗАО “Неохим”, Россия.
Технологическая схема изготовления трехслойных пластин твердого электролита для ТОТЭ приведена на рис. 1. На первом этапе приготовления шликера проводили помол в полиэтиленовом барабане шарами из диоксида циркония (диаметр 10 мм) исходного порошка 6ScSZ или 10Sc1YSZ с растворителями, представляющими собой азеотропную смесь метилэтилкетона (марка “ч.”, массовая доля основного вещества не менее 99.5%) и пропанола-1 (“х. ч.”, массовая доля основного вещества не менее 99.5%). В качестве диспергатора использовали рыбий жир Menhaden Fish Oil (Sigma Chemical Company, США). Для определения динамики помола и оценки изменения распределения частиц по размерам проводили помол порошка 6ScSZ в течение 24 и 44 ч при массовом соотношении “материал : шары : растворители” = 2 : 5 : 1. После 24 ч помола в полученную суспензию вводили пластификаторы: полиэтиленгликоль ПЭГ-2000 (Sigma-Aldrich, США), Santicizer (Valtris Specialty Chemicals, США) и связующее поливинилбутираль Butvar (Showiningan, Англия). Затем смесь перемешивали в течение 24 ч, отделяли полученный шликер от шаров и проводили его дегазацию в течение 6–12 ч со скоростью не более 10 об/мин.
Выбор оптимальной композиции органических добавок в шликере проводили на основе характеристик полученной после сушки керамической ленты, таких как однородная микроструктура, отсутствие макроскопических дефектов, а также легкость отделения от несущей пленки после сушки для предотвращения возникновения растягивающих напряжений при съеме ленты. С этой целью было разработано 4 состава шликеров (R1–R4, табл. 1), различающихся между собой количеством растворителей, соотношением и количеством пластификаторов. В первом составе (R1) соотношение пластификаторов “Santicizer: ПЭГ-2000” составляло 70 : 30 об. %, а в R2 “Santicizer: ПЭГ-2000” – 55 : 45 об. %. Состав R3 отличается от состава R2 увеличением количества пластификаторов на 6% при том же их соотношении. R4 – состав со сниженным количеством пластификаторов при соотношении “Santicizer: ПЭГ-2000” = 50 : 50 об. % для литья на пленку из полиэтилентерефталата (ПЭТФ) с силиконовым покрытием.
Таблица 1.
Рецептуры шликеров для литья пленок 10Sc1YSZ
Наименование компонента | Назначение компонента | Содержание, об. % | |||
---|---|---|---|---|---|
состав R1 |
состав R2 |
состав R3 |
состав R4 |
||
Порошок 10Sc1YSZ | Керамический порошок | 18.4 | 18.3 | 19.3 | 19.5 |
Метилэтилкетон | Растворитель | 43.5 | 43.2 | 41.7 | 44.5 |
Изопропиловый спирт | Растворитель | 19.7 | 19.6 | 19.1 | 20.2 |
Рыбий жир | Диспергатор | 1.9 | 1.9 | 2.0 | 2.0 |
Santisizer | Пластификатор | 5.9 | 4.9 | 5.2 | 2.8 |
ПЭГ-2000 | Пластификатор | 2.6 | 4.1 | 4.3 | 2.8 |
Поливинилбутираль | Связующее | 8.0 | 8.0 | 8.4 | 8.2 |
Тип несущей пленки | – | ПЭТФ без покрытия | ПЭТФ без покрытия | ПЭТФ без покрытия | ПЭТФ с покрытием силиконом |
Литье и сушку керамических лент 6ScSZ и 10Sc1YSZ осуществляли на установке линии КЕКО (Словения), при температуре 20–22°С с использованием в качестве несущей пленки в зависимости от композиции органических добавок в шликере ПЭТФ без покрытия или с силиконовым покрытием (табл. 1).
Резка лент на листы проводилась на установке нарезки керамических листов SC-25MNC (KEKO, Словения). Ламинирование пакетов 6ScSZ/10Sc1YSZ/6ScSZ проводилось с использованием изостатической ламинационной системы ILS-66 (KEKO, Словения) при максимальном давлении 30–40 МПа и температуре 50–70°С. Резка на пластины проводилась на машине автоматической резки СМ-15 (KEKO, Словения). Полученные пластины обжигали на пористых огнеупорных плитах из оксида алюминия в высокотемпературной камерной печи Nabertherm 276 (Германия) до максимальной температуры 1500°С с выдержкой в течение 1.5 ч. Нагрузка от плиты-груза составила 1.7 г/см2 площади пластины.
Определение среднего размера частиц керамических порошков проводили на анализаторе Analysette 22 NanoTec plus (Fritsch, Германия) методом лазерной дифракции. Анализ удельной площади поверхности порошков проводился методом низкотемпературной адсорбции–десорбции азота на анализаторе Сорбтометр (ЗАО “Катакон”, Россия). Микрофотографии порошков и образцов керамики были получены с помощью сканирующих электронных микроскопов JSM‑6010 LA (Jeol, Япония) и Supra 50vp (Сarl Zeiss, Германия). Вязкость шликеров измеряли на ротационном вискозиметре Brookfield DV-I Prime (Brookfield Engineering Laboratories, США).
Кажущуюся плотность и водопоглощение образцов после обжига определяли методом гидростатического взвешивания по ГОСТ 24409–80.
Рентгенограммы порошков регистрировали с использованием дифрактометра Siemens D-500 (Cu${{K}_{{{{\alpha }_{1}}}}}$-излучение) в диапазоне углов 2θ = 20°–135°.
РЕЗУЛЬТАТЫ И ОБСУЖДЕНИЕ
Анализ дифрактограмм исходных порошков (рис. 2) показал, что основной фазой порошка 6ScSZ является тетрагональная. Рефлекс малой интенсивности на угле отражения 28.3° свидетельствует о наличии следов примеси. Порошок 10Sc1YSZ представлен только кубической фазой. Оценка среднего размера кристаллитов по формуле Шеррера для 6ScSZ составила 95 нм, а для 10Sc1YSZ – 170 нм. Микрофотографии исходных порошков 6ScSZ и 10Sc1YSZ приведены на рис. 3а и 3б соответственно.
По описанию производителя исходных порошков, для улучшения технологических свойств после синтеза порошков проводилась их термообработка при температуре 1000°С в течение 2 ч. В табл. 2 приведены основные характеристики исходных порошков 6ScSZ и 10Sc1YSZ. На рис. 4 представлены кривые распределения по размерам частиц порошка 10Sc1YSZ. Как видно из табл. 2, рис. 3б и рис. 4, порошок 10Sc1YSZ не содержит агломератов частиц размером более 2 мкм; частицы имеют форму, близкую к сферической; значение d50 – 0.7 мкм, d90 – 1.3 мкм; распределение частиц по размерам мономодальное. Такое распределение частиц не способствует плотной упаковке частиц в процессе приготовления шликера, поскольку имеющиеся пустоты между частицами заполняются растворителями, что приводит к возрастанию вязкости. С другой стороны, мономодальное распределение частиц по размеру способствует формированию более однородной структуры при спекании керамики, так как не наблюдаются анизотропия коэффициента усадки и аномальный рост зерен [15].
Таблица 2.
Характеристики исходных порошков 6ScSZ и 10Sc1YSZ
Порошок | Распределение частиц по размерам, мкм | Sуд, м2/г | Влажность, % | ||
---|---|---|---|---|---|
d10 | d50 | d90 | |||
6ScSZ | 0.2 | 7.0 | 123.6 | 5.19 | 0.19 |
10Sc1YSZ | 0.4 | 0.7 | 1.3 | 4.9 | 0.18 |
Интегральное и дифференциальное распределение по размерам частиц порошка 6ScSZ до и после мокрого помола в течение 24 и 44 ч, приведено на рис. 5. Исходный порошок (d50 – 7.0 мкм, d90 – 123.6 мкм) имеет полимодальное распределение частиц по размерам и содержит крупные агломераты, разрушающиеся при помоле в течение 24 ч до значений d50 – 0.6 мкм, d90 – 6.7 мкм, распределение частиц порошка по размерам бимодальное. Дальнейший помол до 44 ч не приводит к заметному изменению распределения частиц по размеру. Таким образом, необходимо снижать температуру прокаливания порошка 6ScSZ, поскольку при 1000°С формируются крупные и достаточно прочные агломераты порошка, не разрушающиеся до d90 менее 2 мкм даже в течение 44 ч помола. Наличие агломерированных зерен на этапе спекания керамики приводит к нерегулярности микроструктуры и неравномерности усадки.
Рис. 5.
Распределение по размерам частиц 6ScSZ исходного порошка и порошков после помола в течение 24 и 44 ч.
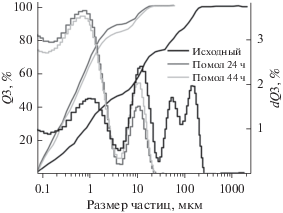
На рис. 6 приведены зависимости вязкости шликеров 6ScSZ и 10Sc1YSZ, приготовленных по составу R1, от скорости сдвига. Шликеры демонстрируют псевдопластическое поведение, при котором вязкость снижается с возрастанием скорости сдвига. Микрофотографии структуры лент из шликеров 6ScSZ и 10Sc1YSZ, приготовленных по рецептуре R1, приведены на рис. 7. Как видно, наличие в порошке 6ScSZ, не разрушенных при помоле агломератов, привело к нерегулярности структуры ленты и появлению пор размером до 2 мкм.
Рис. 7.
Микрофотографии структуры лент 6ScSZ (а) и 10Sc1YSZ (б), приготовленных из шликеров рецептуры R1.
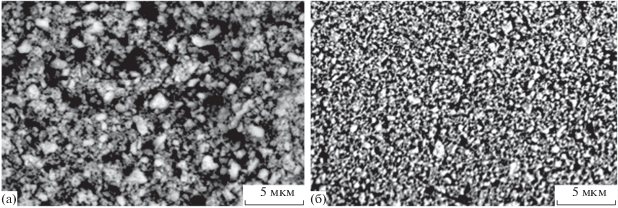
Отсутствие крупных агломератов и мономодальное распределение по размерам частиц 10Sc1YSZ приводит к более однородной структуре отлитой ленты вне зависимости от состава шликера. Микрофотографии лент 10Sc1YSZ, полученных из шликеров по составам R1–R4, приведены на рис. 8. Соотношение органических компонентов в составе шликера на основе порошка 10Sc1YSZ оказало существенное влияние на процесс отделения ленты от несущей пленки. В табл. 3 приводятся свойства лент, полученных из шликеров на основе 10Sc1YSZ, приготовленных из рецептур R1–R4.
Рис. 8.
SEM-изображение лента 10Sc1YSZ, приготовленных из шликеров составов R1 (а), R2 (б), R3 (в) и R4 (г).
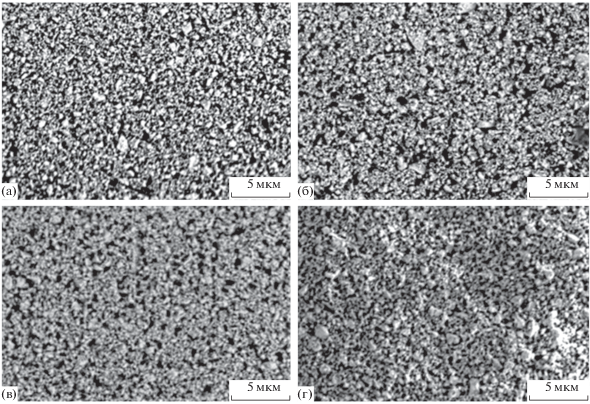
Таблица 3.
Свойства лент, полученных из шликера 10Sc1YSZ по рецептурам R1–R4
Состав шликера | R1 | R2 | R3 | R4 |
---|---|---|---|---|
Качество керамической ленты | Дефектов нет | Дефектов нет | Дефектов нет | Складки, частичные разрывы |
Отделение ленты от несущей пленки после сушки | Отделяется от несущей пленки с приложением усилия | Отделяется от несущей пленки с приложением усилия, сминается | Отделяется от несущей пленки с приложением небольшого усилия (рис. 9а) | Отделяется от несущей пленки в процессе сушки (рис. 9б) |
Внешний вид лент 10Sc1YSZ, отлитых из шликеров, приготовленных по рецептурам R3 и R4, показан на рис. 9. Лента, отлитая на ПЭТФ-пленку без покрытия, отличается более высокой адгезией к пленке, отсутствием складок и смятия после сушки. В результате анализа свойств лент, полученных из шликеров 10Sc1YSZ с различным соотношением органических компонентов, для дальнейших работ был выбран шликер состава R3, позволяющий получить ленту с однородной микроструктурой без дефектов, отделяющуюся от несущей ПЭТФ-пленки с приложением небольшого усилия.
Рис. 9.
Ленты 10Sc1YSZ, отлитые из шликера рецептуры R3 на ПЭТФ пленку без покрытия (а) и состава R4 на ПЭТФ-пленку с силиконовым покрытием (б).
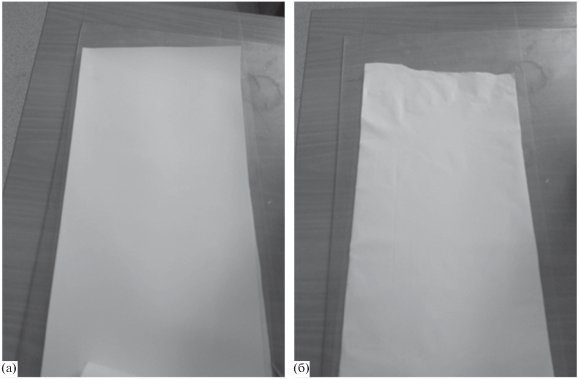
Отлитые ленты 6ScSZ и 10Sc1YSZ нарезали для дальнейшего ламинирования в изостатическом прессе. Полученные трехслойные пакеты (6ScSZ/10Sc1YSZ/6ScSZ) обжигали на пористых огнеупорных плитах из оксида алюминия до максимальной температуры 1500°С с выдержкой в течение 1.5 ч. При загрузке пластин были использованы как нешлифованные, так и шлифованные огнеупорные плиты.
Внешний вид пластин 100 × 100 × 0.15 мм, полученных после их спекания на нешлифованных и шлифованных огнеупорных плитах приведен на рис. 10а и рис. 10б соответственно. Пластины, обожженные с использованием нешлифованных огнеупоров, имеют дефекты в виде вытянутых или отколотых углов. Это связано с отклонением от плоскостности огнеупорных плит и вследствие этого локальным прижатием керамической пластины плитой-грузом к опорной плите, что препятствует движению определенного участка пластины в процессе усадки при спекании. Пластины, обожженные на шлифованных огнеупорных плитах (б), ровные и не имеют отклонений от плоскостности и от параллельности. Кажущаяся плотность полученных пластин составила 5.7 г/см3.
Рис. 10.
Внешний вид пластин после обжига: а – на нешлифованных плитах (характерные вытягивание и откалывание углов отмечены кругами), б – на шлифованных плитах (пластины без видимых дефектов).
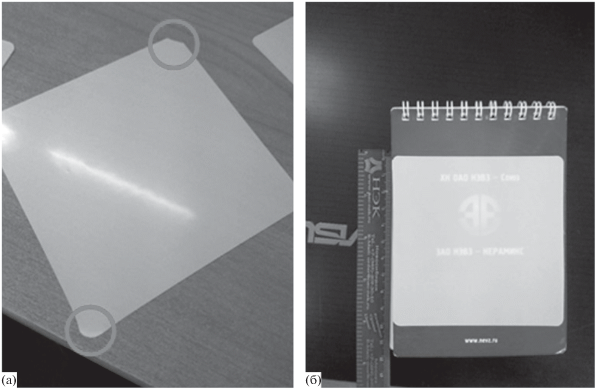
На рис. 11 представлены микроструктура поверхности (а) и излома (б) пластины 6ScSZ/10Sc1YSZ/6ScSZ после спекания. Структура поверхности однородная, размер зерен 6ScSZ не превышает 3 мкм. Наблюдается присутствие отдельных пор диаметром не более 1 мкм. Поперечное сечение пластины имеет ярко выраженную трехслойную структуру с толщинами 30 и 80 мкм для внешних и внутреннего слоев соответственно. Присутствующие по всей толщине образца микропоры диаметром менее 1 мкм не образуют связной системы и не должны оказывать существенного влияния ни на транспортные, ни на механические характеристики полученных пластин.
ЗАКЛЮЧЕНИЕ
В данной работе были представлены результаты, полученные при отработке технологии изготовления слоистых твердоэлектролитных мембран на основе диоксида циркония методом пленочного литья (литья на движущуюся ленту). Мембраны предполагается использовать при производстве планарных твердооксидных топливных элементов с конструкцией поддерживающего электролита. Мембраны имеют размер 100 × 100 мм и толщину менее 150 мкм. Гибкость мембран значительно упрощает изготовление топливных элементов и батарей на их основе. Показано, что мембраны соответствуют требованиям, предъявляемым к геометрии и микроструктуре. Функциональные характеристики будут доложены в следующих работах.
Список литературы
Тиунова, О.В., Задорожная, О.Ю., Непочатов, Ю.К., Бурмистров, И.Н., Курицына, И.Е., Бредихин, С.И. Керамические мембраны на основе скандий-стабилизированного ZrO2, полученные методом пленочного литья. Электрохимия. 2014. Т. 50. С. 801. [Tiunova, O.V., Zadorozhnaya, O.Yu., Nepochatov, Yu.K., Burmistrov, I.N., Kuritsyna, I.E., and Bredikhin, S.I., Ceramic Membranes Based on Scandium-Stabilized ZrO2 Obtained by Tape Casting Technique, Russ. J. Electrochem., 2014, vol. 50, p. 719.]
Minh, N.Q., Ceramic fuel cells., J. Am. Ceram. Soc., 1993, vol. 76, p. 563.
Andujar, J.M. and Segura, F., Fuel cells: history and updating. A walk along two centuries, Renew Sustain Energy Rev., 2009, vol. 13, p. 2309.
Ormerod, R.M., Solid oxide fuel cells, Chem Soc Rev., 2003, vol. 32, p. 17.
Singhal, S.C. and Kendall, K., High-temperature Solid Oxide Fuel Cells: Fundamentals, Design and Applications: Fundamentals, Design and Applications, Oxford: Elsevier, 2003, p. 424.
Cheng, J.G., Fu, Q.X., Liu, X.Q., et al., Key Engineering Materials, 2202, vol. 224–226, p. 173.
Fu, C.J., Chan, S.H., Liu, Q.L., et al., Intern. J. Hydrogen Energy, 2010, vol. 35, p. 301.
Costa, R., Hafsaoui, J., Almeida De Oliveira, A.P., et al., J. Appl. Electrochem., 2009, vol. 39, p. 485.
Gurauskis, J., Sanchez-Herencia, A.J., and Baudın, C., Joining green ceramic tapes made from water-based slurries by applying low pressures at ambient temperature, J. Eur. Ceram. Soc., 2005, vol. 25, p. 3403.
Timurkutluk, B., The role of lamination conditions on electrochemical and mechanical performance of ceramic electrolytes for solid oxide fuel cells, Ceram Int., 2015, vol. 41, p. 2057.
Capdevila, X.G., Folch, J., Calleja, A., et al., High-density YSZ tapes fabricated via the multi folding lamination process, Ceram Int. 2009, vol. 35, p. 1219.
Park, H.-G., Moon, H., Park, S.-C., et al., Performance improvement of anode-supported electrolytes for planar solid oxide fuel cells via a tape-casting/lamination/co-firing technique, J. Power Sources, 2010, vol. 195, p. 2463.
Lee, S.-H., Messing, G.L., Awano, M., Sintering arches for co-sintering camber-free SOFC multilayers, J. Am. Ceram. Soc., 2008, vol. 91, p. 421.
Агарков, Д.А., Бредихин, С.И., Бурмистров, И.Н., Курицына, И.Е., Непочатов, Ю.К., Тиунова, О.В. Мембрана твердого электролита для твердооксидных топливных элементов. Пат. 161024 (Россия). 2016. [Agarkov, D.A., Bredikhin, S.I., Burmistrov, I.N., Kuritsyna, I.E., Nepochatov, Yu.K., Tiunova, O.V., Membrane of solid electrolyte for solid oxide fuel cells, Patent 161024 (Russia). 2016.]
Goulart, C. and de Souza, D., Critical analysis of aqueous tape casting, sintering, and characterization of planar Yttria-Stabilized Zirconia electrolytes for SOFC, Int. J. Appl. Ceram. Technol., 2017, p. 1.
Дополнительные материалы отсутствуют.