Электрохимия, 2022, T. 58, № 3, стр. 140-149
Влияние микроструктуры на коррозионную стойкость трубной стали 20 в условиях углекислотной коррозии
В. К. Лауринавичюте a, *, Т. В. Шибаева b, **, Л. В. Пуголовкин a, М. В. Железный b, И. Ю. Пышминцев c, А. Н. Мальцева c, Ф. Д. Чепик c
a Московский государственный университет им. М.В. Ломоносова, Химический факультет
Москва, Россия
b Институт металлургии и материаловедения им. А.А. Байкова РАН
Москва, Россия
c Российский научно-исследовательский институт трубной промышленности
Челябинск, Россия
* E-mail: nika@elch.chem.msu.ru
** E-mail: t.shibaeva@gmail.com
Поступила в редакцию 22.05.2021
После доработки 06.07.2021
Принята к публикации 04.08.2021
- EDN: YTONXZ
- DOI: 10.31857/S0424857022010091
Аннотация
Коррозионная стойкость трубной стали 20 в состоянии поставки (т), а также после закалки (з), отпуска (о) или нормализации (н) изучена в ацетатных буферных растворах, насыщенных CO2 и содержащих 0–0.85 M NaCl. Поляризационные измерения и испытания в отсутствие внешней поляризации показали, что коррозионная стойкость уменьшается в следующем порядке: о ~ н > з > т. Более низкие скорости коррозии для образцов о и н связаны с меньшим содержанием перлита и его более равномерным распределением в микроструктуре. Показано, что преимущественное растворение феррита во время коррозии сопровождается обнажением перлитного компонента и увеличением катодных токов, что способствует дальнейшему ускорению коррозии.
ВВЕДЕНИЕ
Углекислый газ, являясь сопутствующим газом при добыче нефти и газа, способствует ускоренной коррозии трубного металла. Подробные обзоры, посвященные проблеме углекислотной коррозии [1–5], демонстрируют, что растворенный СО2 может как выступать в качестве деполяризатора и способствовать коррозии (например, при восстановлении ионов Н+, Н2CO3), так и облегчать образование защитных оксидно-карбонатных пленок на поверхности металла [6‒8]. Первый эффект может объясняться непосредственным участием H+, Н2CO3 в катодных процессах [9–12], а также буферирующими свойствами углекислоты, поддерживающей постоянную концентрацию протонов в приповерхностной области [12]. Эффект пассивации определяется низкой растворимостью карбонатов и гидрокарбонатов железа и зависит от микроструктуры поверхности, температуры, солевого и газового состава раствора. Оба этих разнонаправленных эффекта зависят от рН и определяются формой нахождения СО2 в растворе.
Со стороны самой стали, ее состав и микроструктура также влияют на протекание коррозионных процессов и, по данным работ [13–16], в значительной степени определяют стабильность пленок продуктов коррозии. В частности, есть данные о зависимости скорости коррозии от содержания хрома [17], углерода [19], и микролегирующих элементов (Si, Mo, V и Cu [18]) в стали. Однако данные об этих эффектах зачастую противоречивы [13], что связано со сложностью независимого варьирования микроструктуры и химического состава стали.
Существенную роль при протекании углекислотной коррозии играет солевой состав раствора. Влияние минерализации может быть двояким [19]: с одной стороны, повышение концентрации растворенных солей приводит к снижению растворимости СО2, что способствует замедлению коррозии, а с другой стороны, стабильность пассивных пленок также уменьшается [20], и коррозия ускоряется. Подробный обзор по коррозионной стабильности низкоуглеродистых и слаболегированных сталей приведен в работе [13].
Цель данной работы – оценка влияния микроструктуры стали 20 на ее коррозионное поведение в условиях углекислотной коррозии в нейтральной среде. Данная сталь широко применяется в нефтегазопроводах, поэтому в качестве рабочих растворов выбраны растворы c рН 6.5, насыщенные CO2 и содержащие 0–0.85 М NaCl, что моделирует типичные среды крупнейших газоконденсатных месторождений России. Насколько известно авторам, в литературе отсутствуют данные о коррозионном поведении стали 20 в аналогичных условиях, и основной массив известных данных относится к коррозии аналогичных слаболегированных сталей в слабокислых средах (рН от 3.5 до 5.0) [14, 16, 19, 21] и/или при повышенных температурах [16, 21]. Вместе с тем в нейтральной среде можно ожидать существенное увеличение концентрации бикарбонат ионов, которые являются более коррозионно-активными ионами по сравнению с H2CO3aq [22–24].
ЭКСПЕРИМЕНТАЛЬНАЯ ЧАСТЬ
Образцы отрезали от трубы из стали 20 таким образом, чтобы рабочая поверхность была расположена по толщине стенки трубы в направлении прокатки. Результаты определения химического состава стали представлены в табл. 1.
Таблица 1.
Результаты определения химического состава (мас. %) стали 20 с помощью оптико-эмиссионного спектрометра Bruker Q4 Tasman
С | Mn | Si | P | S | Cr | Ni | Cu | Mo | Al | N |
---|---|---|---|---|---|---|---|---|---|---|
0.22 | 0.42 | 0.20 | 0.006 | 0.003 | 0.09 | 0.10 | 0.14 | 0.02 | 0.01 | 0.005 |
Перед измерениями электроды шлифовали на абразивных шкурках с последовательным уменьшением зернистости от 120 до 1000 грит, полировали пастами с абразивными частицами 3 и 0.05 мкм (MetaDiTM Supreme, Beuhler) до зеркального блеска, промывали спиртом и сушили. Готовые образцы хранили перед экспериментами в эксикаторе не более 2 сут. Место контакта и все поверхности образца, кроме рабочей, изолировали смолой Апьезон W.
Влияние структурных факторов на коррозионную стойкость оценивали на образцах стали 20 после термообработки, проведенной в лабораторных условиях по следующим режимам:
1. Закалка (з): нагрев до 910°С с выдержкой в течение 30 мин и последующим охлаждением в воде.
2. Нормализация (н): нагрев до 910°С с выдержкой в течение 30 мин и последующим охлаждением на воздухе.
3. Закалка при 910°С с последующим отпуском при 700°С (1 ч) и охлаждением на воздухе (о).
Структуру исследовали на шлифах, предварительно протравленных в растворе 3% азотной кислоты в спирте, с помощью оптического микроскопа ZEISS с анализатором изображения “Thixomet”. Дополнительную идентификацию компонентов микроструктуры проводили с помощью твердомера FALCON 511.
Электрохимические измерения выполняли при помощи потенциостата Autolab PGSTAT 30. Перед измерениями проводили предварительную оценку сопротивления методом спектроскопии импеданса (типичные значения составляли 1–2 Ом), большую часть которого (90–95%) компенсировали автоматически в ходе циклирования, оставшееся сопротивление докомпенсировали при обработке данных. Ниже все данные приведены после полной компенсации омических потерь. Измерения проводили в трехэлектродной ячейке (Euro Cell™, “Gamry”) в 0.1 М ацетатном буферном растворе, содержащем 0–0.85 М NaCl при 23 ± 1°С. Для приготовления растворов использовали реактивы марок “ч.”, “х. ч.”. Раствор предварительно продували CO2 (99.995%) с расходом 2–3 мл/мин в течение часа. В качестве вспомогательного электрода выступал графит с геометрической площадью не менее 7 см2. Площадь рабочей поверхности стали составляла 0.9–1.2 см2.
Вольтамперограммы снимали до воспроизводимости (3–5 циклов) в пределах от –1.0 до –0.1 В отн. Аg/AgCl, KСlнас со скоростью развертки 5 мВ/с, если не указано иное. Токи коррозии (iкор), тафелевы наклоны для анодного (ba) и катодного (bк) процессов определяли по экстраполяции обратного хода вольтамперограмм в тафелевских координатах (рис. 2б) по методике, подробно описанной ранее [25]. Все данные усредняли по трем и более параллельным измерениям, полученным после переполировки поверхности образцов. Ниже все потенциалы даны в шкале насыщенного хлоридсеребряного электрода.
Коррозионные тесты проводились следующим образом: подготовленные, как описано выше, образцы помещали в 180–200 мл ацетатного буферного раствора, постоянно продуваемого СО2 на 24 ч. Периодические потенциодинамические измерения (1–2 в час со скоростью 1 мВ/с) в ограниченном диапазоне потенциалов (OCP ± 20 мВ) проводились для оценки изменения коррозионной стойкости со временем. Ожидаемая при этом суммарная потеря металла за счет электрохимического окисления не превышает 0.7 мкM Fe (до концентрации 4 × 10–6 M). По истечении 24 ч для каждого теста раствор подкисляли добавкой 30 мл HNO3 (конц) и нагревали в течение ~1 ч при 80–90°C. Полученный раствор дополнительно подкисляли, добавляли свежеприготовленный раствор NaSCN и определяли содержание железа по стандартной тиоцианатной методике, измеряя поглощение железо-тиоцианатного комплекса при 482 нм [26].
РЕЗУЛЬТАТЫ И ОБСУЖДЕНИЕ
Микроструктура
Микроструктура трубной стали 20 в исходном состоянии (т) представляет собой грубые чередующиеся между собой полосы светлых участков феррита и темных участков перлита (рис. 1а, табл. 2). Нормализация (н) приводит к формированию равномерно распределенных зерен феррита и их измельчению, а также появлению участков пластинчатого перлита (рис. 1б). После аустенитизации при 910°С и последующего охлаждения в воде (з) по границам аустенитного зерна образуется феррит и преимущественно смешанные микроструктуры с повышенной плотностью дислокаций (бейнит, мартенсит) (рис. 1в). Выдержка при температуре 700°С (о) приводит к отпуску смешанных кристаллографически упорядоченных микроструктур и сопровождается образованием структуры сорбита отпуска с сохранением феррита по границам аустенитного зерна (рис. 1г). По границам ферритного зерна, бывших пакетов и реек α-фазы происходит выделение карбидов.
Рис. 1.
Микроструктура образцов стали 20 в состоянии поставки и после термообработки: а – исходная сталь; б – после нормализации; в – после закалки и г – отпуска при 700°С.
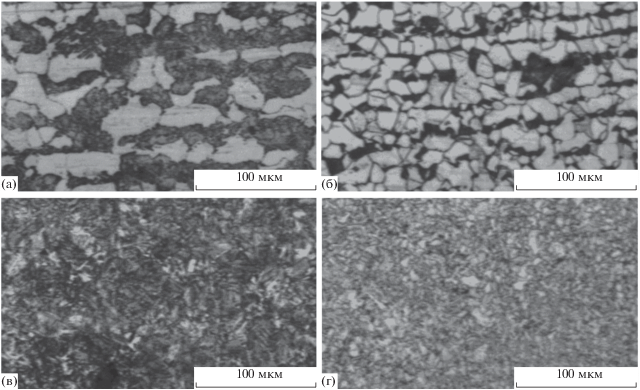
Таблица 2.
Микроструктура и твердость стали 20 после различной термообработки
Образец | Термообработка | Основные фазы (об. %) | Средний размер зерен феррита, мкм | HV10 |
---|---|---|---|---|
т | Нет (состояние поставки) | Ф(40)–П(60) | 25 | 167 |
н | Аустенитизация при 910°С, охлаждение на воздухе | Ф(70)–П(30) | 15 | 141 |
з | Аустенитизация при 910°С, закалка в воде | Ф(5)–M(90)–П(5) | 5 | 282 |
о | Аустенитизация при 910°С, отпуск при 700°С | Ф(5)–С(95) | 5 | 162 |
Объемная доля структурных составляющих приведена табл. 2. Дополнительное исследование твердости стали показывает некоторое снижение твердости с нормализацией, что может быть связано со снижением объемной доли перлита. Как и ожидалось, закалка в воде приводит к существенному увеличению твердости (до HV10 = 282) за счет образования структуры с высокой плотностью дислокаций. В свою очередь отпуск приводит к снижению количества дефектов и твердости образца (до HV10 = 162) за счет распада продуктов сдвигового превращения.
Коррозионная стойкость
Влияние концентрации NaCl. В отсутствие Cl–-ионов вольтамперограмма, полученная на образцах стали т, имеет характерный вид (рис. 2, кривая 1): при низких потенциалах наблюдаются существенные катодные токи при Е < –0.6 B, свидетельствующие об участии растворенного СО2 в катодных процессах. Рост тока при потенциалах >–0.6 В отвечает активному растворению металла, за которым следует область пассивации (‒0.2…–0.1 В). Добавки NaCl приводят к росту тока в пассивной области (рис. 2а, кривые 2 и 3), вплоть до ее исчезновения при максимальной концентрации соли, что свидетельствует об улучшении растворимости солей железа за счет образования хлоридных комплексов. Замена СО2 на О2 приводит к более чем 10-кратному снижению токов коррозии (табл. 3), что согласуется с меньшей растворимостью кислорода (0.15–0.30 мМ по сравнению с 30 мМ для О2 и СО2, соответственно) и подтверждает участие растворенных форм СО2 в коррозионных процессах.
Анализ токов в активной области (рис. 2б, табл. 3) показывает рост токов коррозии с добавками NaCl. Аналогичный эффект отмечен ранее для углекислотной коррозии при более высокой температуре [20]. Анодные тафелевские наклоны (ba) составляют 110–120 мВ/декаду и практически не зависят от содержания NaCl в растворе. Согласно литературным данным [27–29], для углекислотной коррозии в целом характерны значения ba в диапазоне от 30 до 120 мВ/декаду, причем низкие величины (30–40 мВ/декаду) наблюдаются в кислых и слабокислых (рН < 4) растворах [27, 28], а переход к большим значениям ba наблюдали при повышении рН [29] и/или перенапряжения [15, 29]. Таким образом, наблюдаемые значения ba (табл. 3) являются типичными для слабокислых сред.
Таблица 3.
Результаты анализа коррозионной стойкости стали 20 (т) в 0.1 М ацетатном буферном растворе, содержащем 0–0.85 М NaCl и насыщенном СО2 или О2
c(NaCl), M | iкор, мА/см2 | ba, В/декаду | bк, В/декаду |
---|---|---|---|
Раствор, насыщенный CO2 | |||
0 | 0.16 ± 0.03 | 0.119 | –0.285 |
0.25 | 0.22 ± 0.05 | 0.108 | –0.294 |
0.85 | 0.85 ± 0.04 | 0.110 | –0.530 |
Раствор, насыщенный O2 | |||
0.85 | 0.032 ± 0.003 | 0.107 | –0.590 |
Интересно отметить, что в отличие от коррозии при высоких температурах [19] увеличение концентрации NaCl не оказывает влияния на анодный процесс в области активной коррозии, однако оказывает существенное влияние в катодной области. Катодные тафелевские наклоны bк увеличиваются до 0.53 В/декаду с добавками NaCl, что может быть связано с изменением механизма восстановления. Противоположный эффект был ранее описан [19, 30] для сталей C1018 (UNS G10180) и API-X100: снижение катодных токов с ростом концентрации NaCl наблюдалось в слабокислой среде (pH 4–4.8). Это противоречие может быть отнесено к различной форме нахождения CO2 в нейтральной и слабокислой среде: увеличение pH от 4 до 6 сопровождается уменьшением концентрации H2CO3 и увеличением Можно ожидать, что электровосстановление на отрицательно заряженной поверхности электрода замедлено и может ускоряться за счет катионного катализа с добавками NaCl.
При пассивации поверхности стали продуктами коррозии увеличение минерализации приводит к меньшей устойчивости образующихся пассивных пленок (сравните токи при E > –0.2 В, рис. 2a, 2б). Чтобы минимизировать этот эффект, дальнейшее изучение влияние микроструктуры на коррозию стали 20 проводили в растворах с минимальной концентрацией NaCl (0–0.25 М).
Рис. 2.
Поляризационные кривые стали 20 в обычных (а) и в тафелевских (б) координатах, полученные при измерениях в 0.1 М ацетатном буферном растворе (pH 6.0), содержащем 0 (1), 0.25 (2) и 0.85 (3) M NaCl, насыщенном СО2. Скорость сканирования потенциала 5 мВ/с.
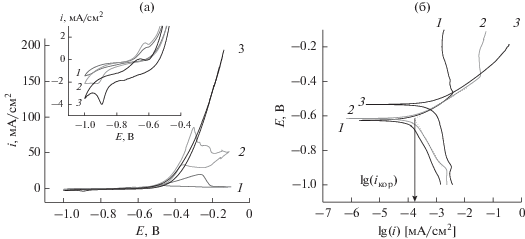
Влияние микроструктуры. Циклические вольтамперограммы, полученные в ацетатном буферном растворе, содержащем 0.25 M NaCl, для всех исследуемых сталей близки. При представлении вольтамперограмм в тафелевских координатах (рис. 3) видно, что изменение микроструктуры не оказывает значимого влияния на процесс электроокисления, и наблюдаемые наклоны ba не зависят от типа микроструктуры (табл. 4). Отметим, что в отличие от данных работы [16], полученных в условиях сформированного слоя продуктов коррозии (после выдержки >400 ч), наблюдаемые токи в области пассивации близки для всех изученных образцов.
Рис. 3.
Поляризационные кривые стали 20 после различной термообработки, полученные в 0.1 М ацетатном буферном растворе, содержащем 0.25 М NaCl и насыщенном СО2. Скорость сканирования потенциала 5 мВ/с.
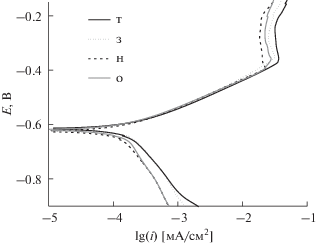
Таблица 4.
Результаты анализа коррозионной стойкости стали 20 после различной термообработки в 0.1 М ацетатном буферном растворе, содержащем 0.25 М NaCl и насыщенном СО2
Образец | iкор, мA/см2 | ba, В/декаду | bк, В/декаду |
---|---|---|---|
т | 0.22 ± 0.05 | 0.108 | –0.294 |
з | 0.17 ± 0.01 | 0.092 | –0.240 |
о | 0.13 ± 0.04 | 0.097 | –0.430 |
н | 0.12 ± 0.02 | 0.085 | –0.402 |
Единственный эффект варьирования микроструктуры проявляется в катодной области: для исходного и закаленного образцов характерны несколько более высокие катодные токи, меньшие значения bк и, соответственно, более высокие токи коррозии iкор (табл. 4). Такое же поведение отмечено в растворах, не содержащих NaCl.
Ранее аналогичный рост катодных токов наблюдали [31] для стали API-X100 после предварительной выдержки образцов в СО2-содержащей среде (90°C, pH 4), что авторы связывают с образованием более толстого слоя токопроводящих продуктов коррозии на перлитных участках. Однако образования значительного коррозионного слоя едва ли можно ожидать в наших экспериментах, поскольку предварительная выдержка образцов в CO2-насыщенных растворах перед измерениями не превышала 1 ч. Более вероятной причиной увеличения токов представляется большая объемная доля перлита (мартенсита), на котором катодные процессы протекают с меньшим перенапряжением [32].
Перлитные компоненты микроструктуры могут играть двойную роль в коррозии углеродистых сталей [14, 31] в зависимости от стадии процесса: во-первых, они могут способствовать ускорению коррозии за счет увеличения катодных реакций, а во-вторых, они могут стабилизировать на поверхности защитную пленку карбонатов/гидрокарбонатов. Для более подробного изучения этих эффектов были проведены 24-часовые коррозионные испытания стали 20 после различной термообработки.
Коррозионные тесты (24 ч). Для оценки влияния времени коррозии (и, соответственно, состояния поверхности) на коррозионную стойкость во время тестов регистрировали потенциал разомкнутой цепи (рис. 4а), а также проводили периодические короткие потенциодинамические измерения в узком диапазоне потенциалов (рис. 4б). Полученные зависимости (рис. 4б) демонстрируют постепенный рост катодных токов со временем, что, как будет показано ниже, может быть связано с постепенным увеличением площади “катодных” участков поверхности.
Рис. 4.
Изменение потенциала разомкнутой цепи (OCP) во время тестирования образца т в ацетатном буферном растворе, насыщенном CO2 (линия, a), поляризационные измерения (б) и соответствующие им оценки Rp/iкор (точки, a).
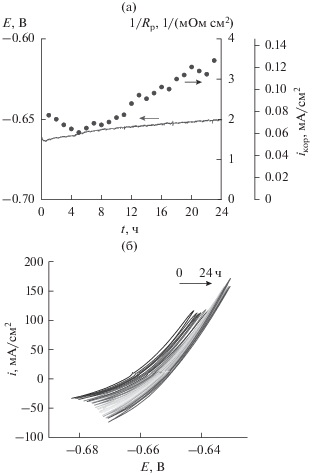
Грубая оценка сопротивления поляризации (Rp) была проведена вблизи потенциала разомкнутой цепи (OCP ± 5 мВ) как Rp = (ΔE/Δi)ΔE→ 0. Полученное значение Rp позволяет оценить плотность тока коррозии c помощью известного уравнения Штерна–Гери [33]:
Для расчета использовали экспериментальные значения тафелевских коэффициентов ba и bк (табл. 3). Полученные таким образом значения iкор увеличиваются со временем от 0.7 × 10–4 до 1.3 × 10–4 А/см2 (точки на рис. 6a), что несколько ниже значений iкор полученных ранее из тафелевской аппроксимации ((1.6 ± 0.3) × 10–4 А/см2, табл. 3). Наблюдаемые отличия могут быть вызваны как различием в состоянии поверхности образцов (возникающим в процессе испытаний), так и низкой точностью оценки iкор из поляризационных измерений в узком диапазоне потенциалов. Наиболее важным результатом является наблюдаемое 2-кратное увеличение скорости коррозии во время 24-часовых тестов. Такая же тенденция была отмечена для образцов н, о и, в меньшей степени, для образца з.
Микроструктура поверхности образцов стали после 24 ч выдержки в коррозионном растворе (рис. 5б, 5г, 5е, 5з) демонстрирует более активное растворение феррита по сравнению с перлитом. Этот эффект особенно выражен в случае образцов т и н, для которых характерно присутствие больших зерен феррита (сравните рис. 5а и 5б или 5в и 5г). Отметим также характерную перлитную микроструктуру, проявляющуюся на поверхности образца н после 24 ч выдержки в CO2-насыщенном растворе (вставка на рис. 5г). Для образцов после закалки проявление перлитных компонентов микроструктуры в процессе коррозии менее выражено, вероятно, из-за меньшего размера карбидсодержащих компонентов микроструктуры и зерен феррита (табл. 1 и рис. 5д–5з).
Рис. 5.
SEM-микрофотографии поверхности образцов стали 20 в состоянии поставки (a, б) и после нормализации (в, г), закалки (д, е) и отпуска (ж, з). Микроструктуры после химического травления поверхности (а, в, д, ж) и после 24 ч коррозии при разомкнутой цепи в CO2 насыщенных растворах (б, г, е, з) приведены на левой и правой панелях соответственно.
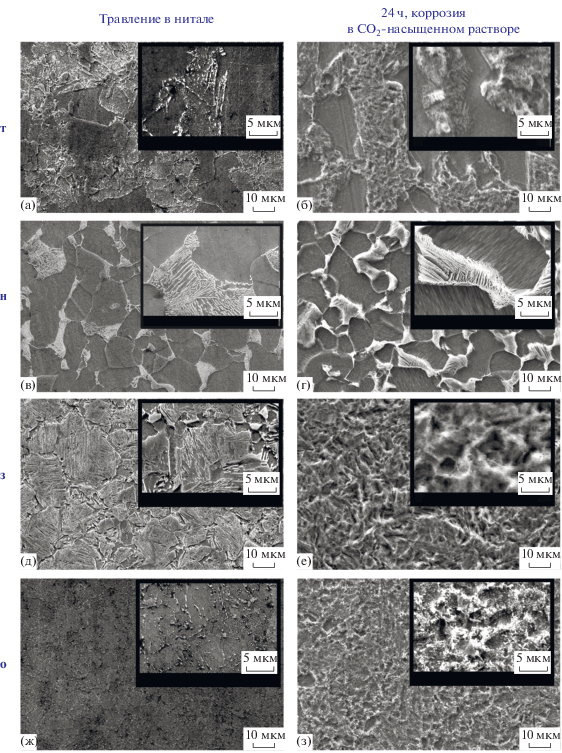
Отметим также, что выраженного формирования пленок продуктов коррозии не наблюдалось, ни на SEM-изображениях поверхности образцов после тестирования (рис. 5б, 5г, 5е, 5з), ни на поляризационных кривых, измеренных в коротком диапазоне потенциалов при иммерсионных испытаниях. Независимая проверка скоростей коррозии для стали после различной термообработки была проведена путем анализа содержания Fe в коррозионных средах. Оцененные таким образом концентрации железа согласуются с токами коррозии, полученными из тафелевого анализа (колонки и точки на рис. 6, соответственно). Оба метода указывают на более высокие скорости коррозии для образцов т и з, как и описано [13, 32, 34, 35] для углекислотной коррозии сталей в слабокислых средах. Например, авторы [14] указывают, что нормализация и отпуск стали API spec 5L X42 приводит к снижению токов коррозии от 0.180 до 0.166 и 0.146 мА/см2 в растворе 0.5 M NaCl, насыщенном CO2 (pH 3.5).
Эти наблюдения свидетельствуют о том, что ускорение катодных реакций на перлитных участках происходит не только при восстановлении водорода из ионов гидроксония или H2CO3 (преобладающих при низких значениях рН), но и из бикарбонат-ионов (преобладающих при высоких рН).
Рис. 6.
Сравнение токов коррозии (точки), полученных из поляризационных измерений и общего содержания железа в коррозионном растворе (колонки) через 24 ч коррозии при разомкнутой цепи в 0.1 М ацетатном буферном растворе, насыщенном CO2. Все концентрации нормированы на площадь образцов стали. Горизонтальная пунктирная линия отвечает концентрации Fe2+, необходимой для осаждения FeCO3 при данном рН. Максимальное значение шкалы концентраций (6.1 × 10–4 M) количественно соответствует максимальному значению шкалы токов коррозии (iкор = 0.225 мA/см2).
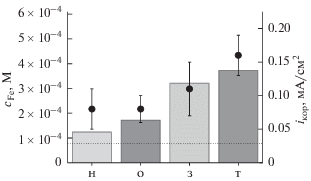
Подводя итог, можно сказать, что как тафелевский анализ, так и 24-часовые испытания при разомкнутой цепи подтвердили более высокую скорость коррозии для исходного образца стали 20 с крупнозернистой ферритно-перлитной микроструктурой. Эту высокую скорость коррозии можно объяснить высоким содержанием зерен перлита, выступающих в качестве катодных участков во время коррозии [31]. Сравнение со сталью после отжига и нормализации с аналогичной феррито-перлитной микроструктурой показывает, что уменьшение объемной доли перлита с 60 до 30 об. % приводит к двукратному снижению скорости коррозии (0.16 и 0.08 мА/см2 для образцов т и н, соответственно). Таким образом, как и в [36], на начальной стадии коррозии высокая катодная площадь в перлите, по-видимому, играет более важную роль в электрохимическом поведении, чем плохо сформированный продукт FeCO3. Также были обнаружены высокие скорости коррозии стали после закалки, обладающей неравновесной мартенситной микроструктурой с более высокой твердостью/механической прочностью и многочисленными дефектами внутреннего строения. Последние могут действовать как дополнительные участки коррозии, ускоряя общий процесс коррозии.
ЗАКЛЮЧЕНИЕ
Скорость коррозии для трубной стали в присутствии CO2 увеличивается с увеличением концентрации NaCl, что коррелирует с ускорением катодных процессов. Электрохимические измерения вместе с тестированием при разомкнутой цепи в насыщенных CO2 ацетатных буферных растворах показали, что коррозионная стойкость стали зависит от ее микроструктуры и снижается со временем в течение 24 ч тестирования. Наибольшие скорости коррозии были найдены для стали в состоянии поставки и для закаленных образцов, а наименьшие для образцов после нормализации и отпуска. В первом случае более высокие токи коррозии коррелируют с большим содержанием перлита в микроструктуре. Увеличение доли последнего по мере вытравливания ферритной составляющей приводит к увеличению площади катодных участков и ускорению коррозии.
Список литературы
Mishra, B., Al-Hassan, S., Olson, D.L., and Salama, M.M., Development of a predictive model for activation controlled corrosion of steel in solutions containing carbon dioxide, Corrosion, 1997, vol. 53, p. 852. https://doi.org/10.5006/1.3290270
Kahyarian, A., Singer, M., and Nesic, S., Modeling of uniform CO2 corrosion of mild steel in gas transportation system. A review, J. Nat. Gas Sci. Eng., 2016, vol. 29, p. 530. https://doi.org/10.1016/j.jngse.2015.12.052
Kermani, M.B. and Morshed, A., Carbon dioxide corrosion in oil and gas production—A compendium, Corrosion, 2003, vol. 59, p. 659. https://doi.org/10.5006/1.3277596
Кашковский, Р.В., Ибатуллин, К.А. Научно-технические аспекты коррозионного разрушения промысловых металлоконструкций в присутствии углекислого газа: обзор. Коррозия: материалы, защита. 2016. Т. 11. С. 1. [Kashkovskiy, R.V. and Ibatullin, K.A., Scientific-and-technical aspects of corrosion destruction of field metal facilities in presence of carbon dioxide. Review, Korroziya: Materialy, Zashchita, 2016, vol. 11, p. 1.]
Моисеева, Л.С. Углекислотная коррозия нефтегазопромыслового оборудования. Защита металлов. 2005. Т. 41. С. 82. [Moiseeva, L.S., Carbon dioxide corrosion of oil and gas field equipment, Protection of Metals, 2005, vol. 41, p. 76.]
Nordsveen, M., Nešić, S., Nyborg, R., and Stangeland, A., A mechanistic model for carbon dioxide corrosion of mild steel in the presence of protective iron carbonate films–part 1: theory and verification, Corr. Sci., 2003, vol. 59, p. 443. https://doi.org/10.5006/1.3277576
Nešić, S., Nordsveen, M., Nyborg, R., and Stangeland, A., A mechanistic model for carbon dioxide corrosion of mild steel in the presence of protective iron carbonate films–part 2: a numerical experiment, Corr. Sci., 2003, vol. 59, p. 489. https://doi.org/10.5006/1.3277579
Nešić, S. and Lee, K.-L.J., A mechanistic model for carbon dioxide corrosion of mild steel in the presence of protective iron carbonate films–part 3: Film growth model, Corr. Sci., 2003, vol. 59, p. 616. https://doi.org/10.5006/1.3277592
Nesic, S., Postlethwaite, J., and Olsen, S., An electrochemical model for prediction of corrosion of mild steel in aqueous carbon dioxide solutions, Corr. Sci., 1996, vol. 52, p. 280. https://doi.org/10.5006/1.3293640
Hurlen, T., Gunvaldsen, S., Tunold, R., Blaker, F., and Lunde, P.G., Effects of carbon dioxide on reactions at iron electrodes in aqueous salt solutions, J. Electroanal. Chem., 1984, vol. 180, p. 511. https://doi.org/10.1016/0368-1874(84)83604-7
Wieckowski, A., Ghali, E., Szklarczyk, M., and Sobkowski, J., The behavior of iron electrode in CO2-saturated neutral electrolyte-. I. Electrochemical study, Electrochim. Acta, 1983, vol. 28, p. 1619. https://doi.org/10.1016/0013-4686(83)85226-8
Linter, B.R. and Burstein, G.T., Reactions of pipeline steels in carbon dioxide solutions, Corr. Sci., 1991, vol. 41, p. 117. https://doi.org/10.1016/S0010-938X(98)00104-8
Lopez, D.A., Perez, T., and Simison, S.N., The influence of microstructure and chemical composition of carbon and low alloy steels in CO2 corrosion. A state-of-the-art appraisal, Mater. Design, 2003, vol. 24, p. 561. https://doi.org/10.1016/S0261-3069(03)00158-4
Ochoa, N., Vega, C., Pebere, N., Lacaze, J., and Brito, J.L., CO2 corrosion resistance of carbon steel in relation with microstructure changes, Mater. Chem. Phys., 2015, vol. 156, p. 198. https://doi.org/10.1016/j.matchemphys.2015.02.047
Kahyarian, A., Brown, B., and Nesic, S., Electrochemistry of CO2 corrosion of mild steel: Effect of CO2 on iron dissolution reaction, Corr. Sci., 2017, vol. 129, p. 146. https://doi.org/10.1016/j.corsci.2017.10.005
Mishra, B., Al-Hassan, S., Olson, D.L., and Salama, M.M., Effect of microstructure on corrosion of steels in aqueous solutions containing carbon dioxide, Corrosion, 1998, vol. 54, p. 480. https://doi.org/10.5006/1.3284876
Xu, L., Wang, B., Zhu, J., Li, W., and Zheng, Z., Effect of Cr content on the corrosion performance of low-Cr alloy steel in a CO2 environment, Appl. Surf. Sci., 2016, vol. 379, p. 39. https://doi.org/10.1016/j.apsusc.2016.04.049
Kermani, M.D., Gonzaґles, J.C., Linne, C., Dougan, M., and Cochrane, R., Development of low carbon Cr-Mo steels with exceptional corrosion resistance for oilfield applications. Corrosion, 2001, Paper 01065, Houston, TX: NACE International, 2001.
Eliyan, F.F., Mohammadi, F., and Alfantazi, A., An electrochemical investigation on the effect of the chloride content on CO2 corrosion of API-X100 steel, Corr. Sci., 2012, vol. 64, p. 37. https://doi.org/10.1016/j.corsci.2012.06.032
Liu, Q.Y., Mao, L.J., and Zhou, S.W., Effects of chloride content on CO2 corrosion of carbon steel in simulated oil and gas well environments, Corr. Sci., 2014, vol. 84, p. 165. https://doi.org/10.1016/j.corsci.2014.03.025
Videm, K. and Koren, A.M., Corrosion, passivity, and pitting of carbon steel in aqueous solutions of
CO2, and Cl–, Corrosion, 1993, vol. 49, p. 746. https://doi.org/10.5006/1.331612710.5006/1.3316127Моисеева, Л.С., Рашевская, Н.С. Влияние величины рН на коррозионное поведение стали в водных средах, содержащих СО2. Журн. прикладной химии. 2002. Т. 75. Вып. 10. С. 1659. [Moiseeva, L.S. and Rashevskaya, N.S., Effect of pH value on corrosion behavior of steel in CO2-containing aqueous media. Russ. J. Appl. Chem., 2002, vol. 75, no. 10, p. 1625.]
Wright, R.F., Brand, E.R., Ziomek–Moroz, M., Tylczak, J.H., and Ohodnicki, P.R., Effect of
on electrochemical kinetics of carbon steel corrosion in CO2-saturated brines, Electrochim. Acta, 2018, vol. 290, p. 626. https://doi.org/10.1016/j.electacta.2018.09.11410.1016/j.electacta.2018.09.114Han, J., Zhang, J., and Carey, J.W., Effect of bicarbonate on corrosion of carbon steel in CO2 saturated brines, Int. J. Greenh. Gas Contr., 2011, vol. 5, p. 1680. https://doi.org/10.1016/j.ijggc.2011.08.003
Shibaeva, T.V., Laurinavichyute, V.K., Tsirlina, G.A., Arsenkin, A.M., and Grigorovich, K.V., The effect of microstructure and non-metallic inclusions on corrosion behavior of low carbon steel in chloride containing solutions, Corr. Sci., 2014, vol. 80, p. 299. https://doi.org/10.1016/j.corsci.2013.11.038
Taylor, E.W., The Examination of Waters and Water Supplies, J. and A. Churchikk Ltd., London, 1958.
Heusler, K.E., Der einfluss der wasserstoffionenkonzentration auf das elektrochemische verhalten des aktiven eisens in sauren losungen, Berichte der Bunsengsellschaft fur physikalische chemie, 1958, bd 62, s. 582. https://doi.org/10.1002/bbpc.19580620510
Bockris, J.O’M., Drazic, D., and Despic, A.R., The electrode kinetics of the deposition and dissolution of iron, Electrochim. Acta, 1961, vol. 4, p. 325. https://doi.org/10.1016/0013-4686(61)80026-1
Nesic, S., Thevenot, N., Crolet, J.-L., and Drazic, D.M., Electrochemical properties of iron dissolution in the presence of CO2. Basics revisited, NACE Corros. 1996, p. 3.
Fang, H., Brown, B., and Nešic, S., Sodium chloride concentration effects on general CO2 corrosion mechanisms, Corrosion, 2013, vol. 69, p. 297. https://doi.org/10.5006/0222
Eliyan, F.F. and Alfantazi, A., On the theory of CO2 corrosion reactions—Investigating their interrelation with the corrosion products and API-X100 steel microstructure, Corr. Sci., 2014, vol. 85, p. 380. https://doi.org/10.1016/j.corsci.2014.04.055
Kahyarian, A., Brown, B., and Nešic, S., Technical note: electrochemistry of CO2 corrosion of mild steel: effect of CO2 on cathodic currents, Corrosion, 2018, vol. 74, p. 851. https://doi.org/10.5006/2792
Stern, M. and Geary, A.L., Electrochemical polarization I. A theoretical analysis of the shape of polarization curves, J. Electrochem. Soc., 1957, vol. 104, p. 56. https://doi.org/10.1149/1.2428496
Dugstad, A., Hemmer, H., and Seiersten, M., Effect of steel microstructure on corrosion rate and protective iron carbonate film formation, Corrosion, 2001, vol. 57, p. 369. https://doi.org/10.5006/1.3290361
Юдин, П.Е., Пугачева, Т.М., Кондратьева, Л.А., Богатов, М.В. Исследование влияния микроструктуры стали 20 на скорость углекислотной коррозии. Металловедение и термическая обработка металлов. 2020. Т. 6. Вып. 780. С. 61. [Yudin, P.E., Pugacheva, T.M., Kondrateva, L.A., and Bogatov, M.V., Investigation of the influence of the microstructure on the corrosion rate of steel 20 in a carbon dioxide environment. Metal Sci Heat Treat., 2020, vol. 5-6, p. 415.]
Mora-Mendoza, J.L. and Turgoose, S., Fe3C influence on the corrosion rate of mild steel in aqueous CO2 system under turbulent flow conditions, Corr. Sci., 2002, vol. 44, p. 1223. https://doi.org/10.1016/S0010-938X(01)00141-X
Дополнительные материалы отсутствуют.