Журнал физической химии, 2021, T. 95, № 12, стр. 1909-1916
Поверхностное натяжение расплавов Fe–Mn–C
Н. И. Синицин a, *, О. А. Чикова a, b, В. В. Вьюхин a
a Уральский федеральный университет имени первого президента России Б.Н. Ельцина
620002 Екатеринбург, Россия
b Уральский государственный педагогический университет
620017 Екатеринбург, Россия
* E-mail: n.i.sinitsin@urfu.ru
Поступила в редакцию 12.04.2021
После доработки 15.05.2021
Принята к публикации 24.05.2021
Аннотация
Приведены результаты измерения коэффициента поверхностного натяжения расплавов системы Fe–Mn–С с содержанием Mn от 5.0 до 25.0 мас. % и С от 0.4 до 2.2 мас. %. Обнаружены аномалии температурных зависимостей коэффициента поверхностного натяжения расплавов Fe–Mn–С, которые интерпретируются как свидетельства необратимого разрушения микрогетерогенности. Определена температура разрушения микрогетерогенности.
Сплавы Fe–Mn–С нашли широкое применение в промышленности в качестве конструкционных материалов, совершенствование технологии их изготовления имеет большое практическое значение. Марганцовистые стали обладают уникальным сочетанием прочности и пластичности, что обеспечивает их стойкость по отношению к ударно-абразивному износу. Главная проблема технологии марганцовистых сталей – нестабильность механических свойств отливок. При охлаждении литых заготовок из расплава выпадают карбиды железа и марганца (Fe3C, Mn3C), их фосфиды (FeP, MnP) и незначительное количество нитридов (FeN, MnN). Выпадение карбидов, фосфидов, нитридов, оксидов марганца и железа по границам зерна аустенита разупрочняет металл: падают прочностные, пластичные и вязкостные механические характеристики [1, 2]. Все исследования, направленные на повышение прочностных и эксплуатационных свойств готовых изделий из марганцовистых сталей, сводятся к температурному воздействию на закристаллизованный слиток или к легированию расплава. Актуальны исследования физико-химических свойств высокомарганцовистых сталей в жидком состоянии с целью оптимизации технологии их литья и снижения вероятности возникновения дефектов в процессе кристаллизации. Принципиально новую возможность для оптимизации технологии сплавов Fe–Mn–С открывает концепция микрогетерогенного состояния жидких многокомпонентных сплавов [3]. Под микрогетерогенным состоянием расплава понимается наличие в нем дисперсных частиц, обогащенных одним из компонентов, которые взвешены в окружающей среде иного состава и отделены от нее межфазной поверхностью. Микрогетерогенное состояние разрушается в результате энергетического воздействия на расплав, например, нагрева до определенной температуры Т*. После необратимого разрушения микрогетерогенного состояния расплав переходит в состояние истинного раствора, изменяются условия его кристаллизации, меняется микроструктура, кристаллическое строение и механические свойства слитка [4]. Ранее авторами обнаружены аномалии температурных зависимостей кинематической вязкости, удельного электросопротивления расплавов Fe–(5.0–25.0) мас. % Mn–(0.4–2.2) мас. % C, которые интерпретируются как свидетельства необратимого разрушения микрогетерогенности [5, 6]. Определены значения температур T*, при нагреве до которых происходит разрушение микрогетерогенного состояния расплава Fe–Mn–С определенного химического состава [5, 6]. Авторами также обнаружены аномалии температурных зависимостей кинематической вязкости, удельного электросопротивления и поверхностного натяжения жидкой стали Гадфильда (Fe–12 мас. % Mn–1 мас. % C), которые интерпретируются как свидетельства необратимого разрушения микрогетерогенности, определена температура T* = 1770 К, при нагреве до которой происходит разрушение микрогетерогенного состояния расплава [7]. Концепция микрогетерогенного состояния жидких многокомпонентных сплавов [3] согласуется с представлениями о структурном переходе “жидкость–жидкость” (liquid–liquid structure transition, LLT) и способе температурной обработки расплава (melt superheating treatment, MST).
Структурный переход “жидкость–жидкость” (LLT) при определенных условиях часто наблюдается во многих металлах и сплавах и играет важную роль в окончательной микроструктуре и свойствах твердых сплавов. Применение LLT в качестве стратегии создания металлов и сплавов с заранее заданными свойствами доказало свою практичность и эффективность [8]. R. Kuritaa, H. Tanakaa приводят экспериментальные доказательства связи между кристаллизацией и LLT для молекулярной жидкости – трифенилфосфита [9]. Обнаружено, что частота зародышеобразования кристаллов резко увеличивается при кратковременном предварительном отжиге вблизи, но выше температуры спинодали LLT, что вызвано снижением межфазной энергии на границе “кристалл–жидкость” из-за присутствия флуктуаций параметра порядка, подобных критическим. Сделан вывод о том, что можно не только контролировать частоту зародышеобразования кристаллов с помощью LLT, но и обеспечивать способ управления структурой кристаллических зерен, которая является решающим фактором контроля механических и термических свойств материалов [9].
“Обработка расплава перегревом” (MST) применяется для повышения механических свойств отливок. Большинство работ направлено на исследование влияния MST на микроструктуру и механические свойства закристаллизованного металла [10, 11]. MST применяется с целью достижения эффекта сверхупрочняемости стали. Путем испытаний на прокаливаемость и дилатометрии показано, что обработка приводит к значительному и повторяемому увеличению прокаливаемости из-за сильного замедления реакций феррит/перлит и бейнит [12]. Исследовано влияние MST на морфологию границы раздела “твердое–жидкое” (S/L) при затвердевании и установлено, что обработка расплава перегревом увеличивает стабильность поверхности раздела S/L и оказывает существенное влияние на характеристики твердого металла [13].
Таким образом, актуально изучение поверхностного натяжения расплавов Fe–Mn–C в контексте возможных структурных переходов в жидкости и условий кристаллизации. Поверхностное натяжение расплавов Fe–Mn–С изучалось ранее [14–24]. Установлено отсутствие избыточного молярного объема расплавов Fe–(3–10) мас. % Mn, а также согласие опытных значений поверхностного натяжения с рассчитанными по формуле Батлера [14]. Обнаружена линейная зависимость поверхностного натяжения расплавов системы Fe–Mn от температуры и снижение величины поверхностного натяжения с увеличением содержания Mn и C [15]. Поверхностное натяжение расплавов Fe–Mn было измерено во всем диапазоне составов [17]. Ранее авторами изучены температурные зависимости поверхностного натяжения расплавов Fe–(0.5–14.5 мас. %) Mn с целью определения температур разрушения микрогетерогенного состояния Т* [24]. Изучено влияние добавок Mn на поверхностное натяжение жидкого железа [18]. Рассчитаны коэффициенты активности Mn в бесконечно разбавленном растворе Fe по формуле Батлера [20]. Исследована адсорбция Mn на поверхности расплавов Fe–Mn [21].
Данная работа – продолжение экспериментальных исследований расплавов Fe–(5.0–25.0) мас. % Mn–(0.4–2.2) мас. % C, изучены температурные зависимости поверхностного натяжения. Полученные результаты обсуждены в рамках концепции микрогетерогенного состояния расплавов [3] с целью определения температуры Т*, нагрев до которой приводит к разрушению микрогетерогенного состояния расплава, которая согласуется с представлениями физической химии металлургических процессов о природе LLT и MST.
ЭКСПЕРИМЕНТАЛЬНАЯ ЧАСТЬ
Сплавы Fe–Mn–С с содержанием марганца от 5.0 до 25.0 мас. % и углерода от 0.5 до 2.2 мас. % получали в лабораторных условиях в защитной атмосфере высокочистого гелия при нагреве до температуры 1870 К с последующим охлаждением со скоростью ~1 К/с. Шихтовыми материалами служили ферромарганец ФМн78 (ГОСТ 4755-91) и карбонильное железо марки 13–2 (“ос.ч.”; чистота 99.98%). Химический состав образцов определяли с помощью спектрометра SPECTROMIDEX (SPECTRO Analytical Instruments GmbH, Germany). Результаты химического анализа представлены в табл. 1.
Таблица 1.
Химический состав сплавов Fe–Mn–С, мас. %
Сплав | Mn | C | Si | S | P | Fe |
---|---|---|---|---|---|---|
1 | 5.0 | 0.4 | 0.4 | <0.01 | <0.01 | ост. |
2 | 7.5 | 0.6 | 0.6 | <0.01 | <0.01 | ост. |
3 | 10.1 | 0.9 | 0.8 | <0.01 | <0.01 | ост. |
4 | 11.9 | 1.1 | 0.8 | <0.01 | <0.01 | ост. |
5 | 15.1 | 1.3 | 1.2 | 0.01 | <0.01 | ост. |
6 | 17.5 | 1.5 | 1.4 | 0.01 | <0.01 | ост. |
7 | 20.3 | 1.8 | 1.6 | 0.01 | <0.01 | ост. |
8 | 25.0 | 2.2 | 2.0 | 0.02 | 0.01 | ост. |
Поверхностное натяжение измеряли методом сидящей капли в режиме нагрева до 2050 К и последующего охлаждения образца. Использовали подложки из BeO. Рабочую камеру предварительно вакуумировали до 0.001 Па. Затем запускали гелий до давления ~105 Па. Образцы выдерживали в камере с инертной средой в течение 5–8 мин при температуре плавления, затем производили нагрев до 2050 К с шагом 30–40 К, после чего в режиме охлаждения получали изображения профиля капли с шагом по температуре 30–40 К. Изотермические выдержки в точках отсчета составляли не менее 15 мин как в режиме нагрева, так и в режиме охлаждения образца. Геометрические размеры профиля капли определяли с помощью программы анализа изображений SIAMS 700 с точностью 0.3–0.6%. Признаков испарения расплава, уменьшения объема капли не наблюдали. Погрешность определения значений поверхностного натяжения не превышала 5%. Метод измерения поверхностного натяжения металлических расплавов (метод сидящей капли) и установка для его реализации ранее описаны в работах [25, 26].
ОБСУЖДЕНИЕ РЕЗУЛЬТАТОВ
На рис. 1, 2 представлены результаты измерения поверхностного натяжения сплавов Fe–(5.0–25.0) мас. % Mn–(0.5–2.2) мас. % C в жидком состоянии в режиме охлаждения. Поверхностная активность растворенного вещества на границе раздела “расплав–инертный газ” определяется соотношением [27]: $G = --{{\left( {\frac{{\partial \sigma }}{{\partial X}}} \right)}_{{X \to 0}}}$, если G > 0, то растворенное вещество – поверхностно-активное, если G < 0, то растворенное вещество – поверхностно-инактивное. Опытным путем установлено, что марганец поверхностно-активный по отношению к железу элемент [25], углерод же по отношению жидкому железу обладает слабой поверхностной активностью [27, 28]. Оценка мольной доли компонентов в поверхностном слое расплавов из Fe–Mn–С позволяет сделать вывод о том, что при увеличении содержания в жидком сплаве марганца от 5.0 до 10.0 мас. % и углерода от 0.5 до 0.9 мас. % увеличивается содержание поверхностно-активных компонентов с одновременным снижением содержания поверхностно-инактивных компонентов (табл. 2). Можно также предположить, что с увеличением содержания в расплаве марганца до 10.0 мас. % и углерода до 0.9 мас. % образуются карбиды FeC и MnC. При достижении содержания марганца 10.0 мас. % и углерода – 0.9 мас. % происходит насыщение расплава карбидами, и с дальнейшим увеличением содержания марганца и углерода карбиды не образуются [29].
Рис. 1.
Температурные зависимости поверхностного натяжения расплавов Fe–Mn–С. Сплошная линия – результат расчета по уравнению (1).
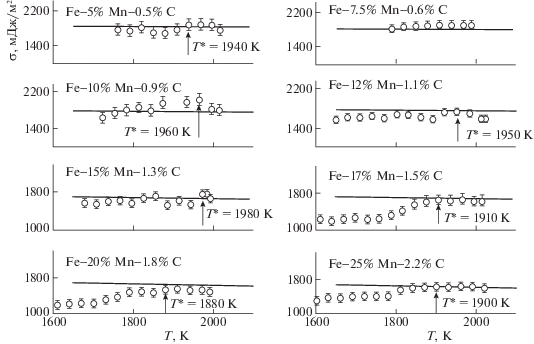
Рис. 2.
Зависимость поверхностного натяжения расплавов Fe–Mn–С от содержания марганца. Сплошная линия – результат расчета по уравнению (1) при Т = 1920 К.
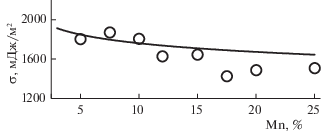
Таблица 2.
Значения температуры Т* (нагрев до которой приводит к разрушению микрогетерогенности расплавов Fe–Mn–С, определенные из анализа температурной зависимости поверхностного натяжения σ(T)) и поверхностной энтропии расплава $\eta = --d\sigma {\text{/}}dT$ в определенном температурном интервале ΔT
Сплав | Содержание в поверхностном слое, мол. доли | Т*, K | ΔT, К | $\eta = --d\sigma {\text{/}}dT$, мДж/(м2 K) | ||
---|---|---|---|---|---|---|
Fe | Mn | C | ||||
Fe−5.0% Mn−0.4% C | 0.76 | 0.20 | 0.04 | 1940 | 1890–1940 | –3.29 |
1940–2020 | 1.35 | |||||
Fe−7.5% Mn−0.6% C | 0.68 | 0.28 | 0.04 | – | 1790–1990 | 0.41 |
Fe−10.0% Mn−0.9% C | 0.60 | 0.34 | 0.60 | 1690 | 1720–1960 | –1.71 |
1960–2010 | 5.06 | |||||
Fe−12.0% Mn−1.1% C | 0.56 | 0.38 | 0.06 | 1950 | 1890–1950 | –2.58 |
1950–2020 | 2.23 | |||||
Fe−15.0% Mn−1.3% C | 0.49 | 0.44 | 0.07 | 1980 | 1860–1980 | –0.38 |
1980–2000 | 4.49 | |||||
Fe−17.5% Mn−1.5% C | 0.44 | 0.48 | 0.08 | 1910 | 1760–1910 | –2.95 |
1910–2020 | 0.08 | |||||
Fe−20.0% Mn−1.8% C | 0.41 | 0.51 | 0.08 | 1880 | 1610–1880 | –1.44 |
1880–1990 | 0.57 | |||||
Fe−25.0% Mn−22% C | 0.34 | 0.57 | 0.09 | 1900 | 1780–1900 | –1.62 |
1900–2020 | 0.14 |
Поверхностное натяжение расплавов Fe–(5.0–25.0) мас. % Mn–(0.5–2.2) мас. % C во всех опытах уменьшается с понижением температуры, а температурный коэффициент поверхностного натяжения $\frac{{d\sigma }}{{dT}}$ меняет знак (рис. 1). Известно, что положительные значения температурного коэффициента поверхностного натяжения связаны с изменением адсорбции компонентов в расплаве, и при достижении некоторой температуры знак температурного коэффициента поверхностного натяжения может поменяться с положительного на отрицательный [28]. Ранее подобное аномальное поведение температурного коэффициента поверхностного натяжения также было обнаружено для ряда двойных и тройных монотектических жидких сплавов [30, 31], характеризующихся наличием купола несмешиваемости на диаграмме состояния. Автор [32] на основании данных о поверхностном натяжении таких систем предположил, что температурный коэффициент поверхностного натяжения меняет свой знак с отрицательного на положительный вблизи линии поверхностного фазового перехода. Данный переход обусловлен конкуренцией между адсорбцией различных компонентов расплава. Согласно теории J.W. Cahn’s, в многокомпонентных неоднородных жидкостях будет происходить поверхностный фазовый переход первого рода: минимизация свободной энергии системы будет приводить к двум решениям при различном содержании поверхностно-активных компонентов; при этом фазовом переходе будет меняться химический состав поверхностного слоя [33]. Будем рассматривать температурный коэффициент поверхностного натяжения как величину удельной поверхностной энтропии $--\frac{{d\sigma }}{{dT}} = \eta ,$ согласно подходу Б.Д. Сумма [34]. Обнаружено, что при достижении определенной для каждого состава температуры Т* поверхностная энтропия η меняет знак с отрицательного на положительный, что косвенно свидетельствует о структурном переходе (LLT), связанном с разрушением микрогетерогенного состояния. В табл. 2 приведены значения удельной поверхностной энтропии η в определенном температурном интервале ΔT, где поверхностная энтропия имеет отрицательный или положительный знак. Значения температур T*(табл. 2), при которых η меняет знак и происходит разрушение микрогетерогенного состояния расплавов Fe–(5.0–25.0) мас. % Mn–(0.4–2.2) мас. % C, согласуются с аналогичными значениями, определенными ранее авторами по аномалиям температурных зависимостей кинематической вязкости, удельного электросопротивления [5, 6].
Рассчитали значение поверхностного натяжения расплавов Fe–Mn–С по уравнению, предложенному для двухкомпонентных систем (сплошная линия на рис. 1 и 2) [35]:
(1)
$\frac{{\Delta G_{{A,\alpha /\beta }}^{E} - \Delta G_{{A,ba}}^{E}}}{{{{\omega }_{{A,\alpha /\beta }}}}} = \frac{{\omega _{{B,\alpha /\beta }}^{0}}}{{{{\omega }_{{B,\alpha /\beta }}}}}\sigma _{{B,\alpha /\beta }}^{0} + $Рассчитано значение температурного коэффициента поверхностного натяжения $d\sigma {\text{/}}dT$ расплавов Fe–Mn–C по уравнению, предложенному в [36]:
(2)
$\begin{gathered} \frac{{d\sigma }}{{dT}} = {{S}_{1}}\frac{{d{{\sigma }_{1}}}}{{dT}} + {{S}_{2}}\frac{{d{{\sigma }_{2}}}}{{dT}}--{{S}_{1}}\left( {1--\frac{{2{{\alpha }_{{p.1}}}T}}{3}} \right)\frac{{{{\sigma }_{1}}--{{\sigma }_{2}}}}{T} + \\ + \;\left( {1--\frac{{2({{S}_{1}}{{\alpha }_{{p.1}}} + {{S}_{2}}{{\alpha }_{{p.2}}})}}{3}} \right)\frac{R}{{{{\omega }_{2}}}}\ln \left( {\frac{{X_{2}^{\omega }}}{{{{X}_{2}}}}} \right), \\ \end{gathered} $Температурный коэффициент поверхностного натяжения $\frac{{d\sigma }}{{dT}}$ расплавов Fe–Mn–C рассчитывали по уравнению (2) (рис. 3). Расплав Fe–Mn–C представляли как бинарную систему, состоящую из жидкого сплава Fe–C и жидкого марганца. Использовали опытные данные о поверхностном натяжении жидкого марганца [38], плотности жидкого марганца [39], поверхностном натяжении расплавов Fe–C [40], плотности расплавов Fe–C [41]. Расчетные зависимости обнаружили уменьшение величины $\frac{{d\sigma }}{{dT}}~$ с увеличением температуры и изменение знака $\frac{{d\sigma }}{{dT}}$ с положительного на отрицательный при температурах, близких к Т* (рис. 3, табл. 2). Только для расплава с содержанием марганца 20.0 мас. % рассчитанные значения температурного коэффициента поверхностного натяжения $\frac{{d\sigma }}{{dT}}$ были отрицательны во всем температурном интервале от 1800 до 2100 К. Такое поведение $\frac{{d\sigma }}{{dT}}(Т)$ объясняется снижением доли площади поверхности, занимаемой расплавом Fe–C с положительным температурным коэффициентом поверхностного натяжения, с одновременным уменьшением величины $\frac{{X_{2}^{\omega }}}{{{{X}_{2}}}}$ от 3.62 для расплава Fe–5 мас. % Mn–0.4 мас. % C до 2.4 для расплава Fe–20 мас. % Mn–1.8 мас. % C. Ранее авторы [42] для расплавов Sn–Ag и Sn–Cu получили $\frac{{X_{2}^{\omega }}}{{{{X}_{2}}}} > 2.67$ при положительных значениях температурного коэффициента поверхностного натяжения $~\frac{{d\sigma }}{{dT}}$. Так как в [36] отмечено, что применение формулы (2) для расчета температурного коэффициента поверхностного натяжения применимо для расплавов, в которых плотность вещества в поверхностном слое больше плотности в объеме [36], для сплавов Fe–Mn–C в жидком состоянии дополнительно провели оценку плотности вещества в поверхностном слое и в объеме расплава: плотность вещества в объеме расплава определяли по аддитивной зависимости, в поверхностном слое – по формуле [43]:
(3)
${{\rho }^{\omega }} = f_{{{\text{FeC}}}}^{{--3/2}}{{\rho }_{{{\text{FeC}}}}}\left\{ {1 + \left[ {{{{\left( {\frac{{{{f}_{{{\text{Mn}}}}}}}{{{{f}_{{{\text{FeC}}}}}}}} \right)}}^{{--3/2}}}\frac{{{{\rho }_{{{\text{Mn}}}}}}}{{{{\rho }_{{{\text{FeC}}}}}}}--1} \right]\phi _{{{\text{Mn}}}}^{s}} \right\},$Оказалось, что для расплавов Fe–Mn–C, содержащих менее 17.3 мас. % марганца, плотность вещества поверхностного слоя выше, чем в объеме. Следовательно, для этих составов поверхностный слой будет формироваться как жидким марганцем, так и расплавом Fe–C. Для расплавов Fe–Mn–C, содержащих более 17.3 мас. % марганца, плотность вещества поверхностного слоя ниже, чем в объеме. В этом случае не будет механизма, препятствующего полностью абсорбироваться атомам марганца на поверхности расплава. Сделали вывод о том, что уравнение (3) применимо только для расплавов Fe–Mn–C, содержащих менее 17.3 мас. % марганца.
Рис. 3.
Температурные зависимости $~\frac{{~d\sigma }}{{dT}}~$ расплавов Fe–(5.0–17.5%)Mn–(0.4–1.5%)C, рассчитанные по уравнению (3).
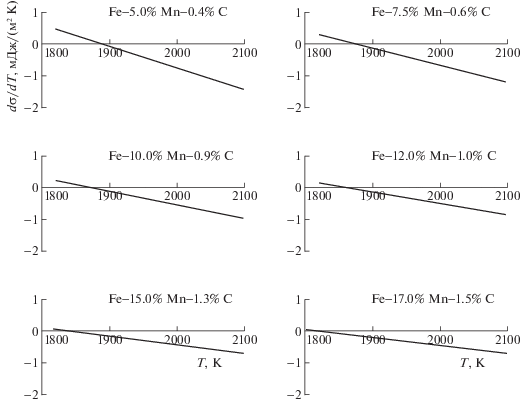
ЗАКЛЮЧЕНИЕ
Получены оригинальные экспериментальные данные о поверхностном натяжении расплавов Fe–Mn–C с содержанием марганца от 5 до 25 мас. % и содержанием С от 0.5 до 2.2 мас. %. Обнаружены аномалии (изломы) на температурных зависимостях коэффициента поверхностного натяжения расплавов Fe–Mn–C, которые сопровождаются скачкообразным изменением первой производной поверхностного натяжения по температуре $\frac{{d\sigma }}{{dT}}$. Температурный коэффициент поверхностного натяжения $\frac{{d\sigma }}{{dT}}$ рассматривается как величина поверхностной энтропии. Обнаружено, что при достижении расплавом Fe–Mn–С определенной для каждого состава температуры Т* поверхностная энтропия скачкообразно меняет свой знак с положительного на отрицательный. Предположено, что наличие излома температурной зависимости коэффициента $\frac{{d\sigma }}{{dT}}$ расплавов Fe–Mn–C свидетельствует о структурном переходе при нагреве до Т*, выражающемся в разрушении его микрогетерогенной структуры. Отмечено увеличение поверхностного натяжения расплавов Fe–Mn–C с ростом температуры, что аномально для металлических расплавов. Расчет температурного коэффициента поверхностного натяжения $\frac{{d\sigma }}{{dT}}$ расплавов Fe–Mn–C обнаружил изменение знака $\frac{{d\sigma }}{{dT}}~$ с положительного на отрицательный при температурах, близких к Т*. Расчетные зависимости $\frac{{d\sigma }}{{dT}}\left( Т \right)~$ обнаружили изменение знака $~\frac{{d\sigma }}{{dT}}$ с положительного на отрицательный при температурах, близких к Т*. Значения температур T*, при нагреве до которых происходит разрушение микрогетерогенного состояния расплавов Fe−(5.0−25.0) мас. % Mn−(0.4−2.2) мас. % C, согласуются с определенными ранее авторами по аномалиям температурных зависимостей кинематической вязкости, удельного электросопротивления данных расплавов.
Исследование выполнено при финансовой поддержке Российского фонда фундаментальных исследований (код проекта № 19-33-90198).
Список литературы
Grässel O., Frommeyer G. // Mater. Sci. Technol. 1998. V. 14. № 12. P. 1213.https://doi.org/10.1179/mst.1998.14.12.1213
Huang B.X., Wang X.D., Rong Y.H. et al. // Mater. Sci. Eng. A. 2006. V. 438–440. P. 306. https://doi.org/10.1016/j.msea.2006.02.150
Попель П.С. // Расплавы. 2005. № 1. С. 22.
Calvo-Dahlborg M., Popel P.S., Kramer M.J. et al. // J. Alloys Compd. 2013. V. 550. P. 9.
Чикова О.А., Синицин Н.И., Вьюхин В.В. // Журн. физ. химии. 2021. Т. 95. № 2. С. 177. DOI: Chikova O.A., Sinitsin. N.I., V’yukhin. V.V. //Russ. J. Phys. Chem. A. 2021. V. 95. № 2. P. 244. https://doi.org/10.1134/S003602442102008410.1134/S0036024421020084https://doi.org/10.31857/S0044453721020084
Синицин Н.И., Чикова О.А., Вьюхин В.В. // Неорган. материалы. 2021. Т. 57. № 1. С. 89. Sinitsin N.I., Chikova O.A., V’yukhin V.V. // Inorganic Materials. 2021. V. 57. № 1. P. 86. https://doi.org/10.1134/S002016852101012X10.1134/S002016852101012Xhttps://doi.org/10.31857/S0002337X21010127
Чикова О.А., Синицин Н.И., Вьюхин В.В. // Журн. физ. химии. 2019. Т. 93. № 8. С. 1138. Chikova O.A., Sinitsin N.I., V’yukhin V.V. // Russ. J. Phys. Chem. A. 2019. V. 93. № 8. P. 1435.https://doi.org/10.1134/S003602441908006510.1134/S0036024419080065.https://doi.org/10.1134/S0044453719080065
He Y., Li J.-Sh., Wang J. et al. // Transactions of Nonferrous Metals Society of China. 2020. V. 30. № 9. P. 2293. https://doi.org/10.1016/S1003-6326(20)65380-8
Kuritaa R., Tanakaa H. // Appl. Phys. Sci. 2019. V. 116. № 50. P. 24949.
Gu Z.H., Wang H.Y., Zheng N. et al. // J. Mater. Sci. 2008. V. 43. № 3. P. 980. https://doi.org/10.1007/s10853-007-2275-5
Piątkowski J. // Solid State Phenom. 2011. V. 176. P. 29. DOI: 10.4028/www.scientific.net/SSP.176.29.
Mostert R.J., Van Rooyen G.T. // Metall. Mater. Trans. A. 1984. V. 15A. № 12. P. 2185. https://doi.org/10.1007/BF02647101
Wang C., Zhang J., Liu L. et al. // J. Mater. Sci. Technol. 2011. V. 27. № 7. P. 668. https://doi.org/10.1016/S1005-0302(11)60123-0
Lee J., Shin M. // Metall. Mater. Trans. B. 2011. V. 42. № 3. P. 546. https://doi.org/10.1007/s11663-011-9490-9
Hoai L.T., Lee J. // J. Mater. Sci. 2012. V. 47. № 24. P. 8303. https://doi.org/10.1007/s11663-011-9555-9
Dubberstein T., Heller H.-P., Klostermann J. et al. // Ibid. 2015. V. 50. № 22. P. 7227. https://doi.org/10.1007/s10853-015-9277-5
Попель С.И., Царевский Б.В., Джемилев Н.К. // ФММ. 1964. Т. 18. № 3. С. 468.
Ван Цзин-Тан, Карасев Р.А., Самарин А.М. // Изв. АН СССР. ОТН. 1960. № 2. С. 49.
Офицеров А.А. // Изв. АН СССР. Металлы. 1971. Т. 4. С. 64.
Nakamoto M., Tanaka T. // ISIJ Int. 2020. V. 60. № 10. P. 2141. https://doi.org/10.2355/isijinternational.ISIJINT-2019-796
Wang J., Bian M., Ma L. // Acta MetallurgicaSinica. 1986. V. 22. № 3. P. a270.
Keene B.J. // Int. Mater. Rev. 1988. V. 33. № 1. P. 1. https://doi.org/10.1179/imr.1988.33.1.1
Царевский Б.В., Попель С.И. // Изв. вузов. Черная металлургия. 1960. № 12. С. 12.
Синицин Н.И., Чикова О.А., Вьюхин В.В. // Там же. 2020. Т. 63. № 1. P. 40. Sinitsin N.I., Chikova. O.A., V’yukhin V.V. // Steel in Translation. 2020. V. 50. № 1. P. 16. https://doi.org/10.3103/S0967091220010118
Найдич Ю.В., Еременко В.Н. // ФММ. 1961. Т. 6. № 11. P. 883.
Глазов В.М., Вобст М., Тимошенко В.М. Методы исследования свойств жидких металлов и полупроводников. М.: Металлургия, 1989. 384 с.
Еременко В.Н., Иванов М.И., Лукашенко Г.М. и др. Физическая химия неорганических материалов. Т. 2. Поверхностное натяжение и термодинамика металлических расплавов. Киев: Наукова думка, 1988. 192 с.
Попель С.И. Поверхностные явления в расплавах. М.: Металлургия, 1994. 440 с.
Вержболович С.А., Сингер В.В., Радовский И.З. и др. // Изв. вузов. Черная металлургия. 1985. № 2. P. 66.
Serre C., Wynblatt P., Chatain D. // Surf. Sci. 1998. V. 415. № 3. P. 336. https://doi.org/10.1016/S0039-6028(98)00567-6
Serre C., Chatain D., Muris M. et al. // Metall. Mater. Trans. A. 2001. V. 32. № 11. P. 2851. https://doi.org/10.1007/s11661-001-1035-4
Kaptay G. // Calphad. 2005. V. 29. № 1. P. 56. https://doi.org/10.1016/j.calphad.2005.04.004
Cahn J.W. // J. Chem. Phys. 1977. V. 66. № 8. P. 3667. https://doi.org/10.1063/1.434402
Сумм Б.Д. // Вестн. МГУ. 1999. Т. 40. № 6. P. 400.
Kaptay G.A. // Adv. Colloid Interface Sci. 2020. V. 283. P. 102212. https://doi.org/10.1016/j.cis.2020.102212
Santos M.S., Reis J.C.R. // J. Alloys Compd. 2021. V. 864. P. 158839. https://doi.org/10.1016/j.jallcom.2021.158839
Shmakova K., Chikova O., Tsepelev V. // Phys. Chem. Liq. 2018. V. 56. № 1. P. 1–8. https://doi.org/10.1080/00319104.2016.1233184
Keene B.J. // Int. Mater. Rev. 1993. V. 38. № 4. P. 157–192. https://doi.org/10.1179/imr.1993.38.4.157
Korobeinikov Iu., Endo R., Seetharaman S. et al. // Metall. Mater. Trans. B. 2021. V. 52. P. 571–575. https://doi.org/10.1007/s11663-020-02044-y
Keene B.J. // Int. Mater. Rev. 1988. V. 33. № 1. P. 1–37. https://doi.org/10.1179/imr.1988.33.1.1
Ниженко В.И., Флока Л.И. Поверхностное натяжение жидких металлов и сплавов (одно- и двухкомпонентные системы). М.: Металлургия. 1981. 208 с.
Lee J., Shimoda W., Tanaka T. // Mater. Trans. 2004. V. 45. № 9. P. 2864–2870. https://doi.org/10.2320/matertrans.45.2864
Santos M.S.R., Reis J.C. // Materials Today Communications. 2020. V. 24. P. 100932. https://doi.org/10.1016/j.mtcomm.2020.100932
Дополнительные материалы отсутствуют.
Инструменты
Журнал физической химии