Журнал физической химии, 2022, T. 96, № 6, стр. 811-815
Электроосаждение сплавов цинк-никель из оксалатно-аммонийных электролитов
Р. Ф. Шеханов a, *, С. Н. Гридчин a, А. В. Балмасов a
a Ивановский государственный химико-технологический университет
Иваново, Россия
* E-mail: ruslanfelix@yandex.ru
Поступила в редакцию 12.10.2021
После доработки 12.10.2021
Принята к публикации 12.10.2021
- EDN: BSPKPX
- DOI: 10.31857/S0044453722060255
Аннотация
Исследованы кинетические закономерности электрохимического осаждения сплавов Zn-Ni из оксалатно-аммонийных электролитов. Измерены значения pHs приэлектродного слоя в процессе электролиза. Рассчитаны парциальные поляризационные кривые электроосаждения цинка, никеля и выделения водорода. Предложен вероятный механизм электроосаждения никеля и цинка из оксалатно-аммонийных электролитов.
Электроосаждение сплавов металлов является одним из эффективных методов улучшения качества гальванических покрытий. Электролитические сплавы цинка с одним или несколькими металлами имеют более высокую коррозионную стойкость по сравнению с нелегированными покрытиями [1]. Вместе с этим процесс электроосаждения сплавов является более сложным и требует решения комплекса теоретических и технологических задач, обеспечивающих получение необходимого химического и фазового составов покрытий. Известные [2, 3] сульфатные электролиты для осаждения сплавов цинка имеют низкую рассеивающую способность, а получаемые покрытия часто не обеспечивают необходимые функциональные свойства.
Перспективным направлением при разработке новых составов растворов для электроосаждения металлов и сплавов является использование соединений, образующих растворимые комплексы с ионами осаждаемых металлов [4–17]. Одним из эффективных комплексообразующих компонентов электролита, в частности, является оксалат аммония, характеризующийся также возможностью разложения образуемых комплексов в сточных водах. Ранее нами [18–23] была продемонстрирована эффективность применения этого соединения при электроосаждении защитных покрытий цинксодержащими сплавами. Использование соответствующих комплексных электролитов позволяет стабилизировать состав растворов, выполнить основное условие для электроосаждения сплавов – равенство электродных потенциалов осаждения компонентов сплава и добиться необходимого химического и фазового состава покрытий. Однако подбор компонентов электролитов производят зачастую эмпирическим путем без учета сложного ионного состава таких растворов. Поэтому установление закономерностей соосаждения компонентов сплавов из электролитов на основе солей щавелевой кислоты с учетом ионных равновесий, устанавливающихся в растворах, имеет важное значение для разработки новых составов низкоконцентрированных комплексных электролитов и способствует развитию новых технологий нанесения гальванических покрытий.
В литературе [24] показано, что при преобладании в аммиакатном электролите высококоординированных комплексных частиц, таких как Zn(NH3)$_{4}^{{2 + }}$, на катоде разряжаются низкокоординированные комплексы Zn(NH3)$_{2}^{{2 + }}$ и Zn(NH3)2+, поскольку энергия, требующаяся для разряда низкокоординированных комплексов меньше, чем для высококоординированных. Точно так же в оксалатном растворе преобладает комплекс Zn(C2O4)$_{3}^{{4 - }}$, а разряжаются Zn(C2O4) и простые ионы цинка Zn2+. В щелочном цинкатном растворе преобладает комплекс Zn(OH)$_{4}^{{2 - }}$, но разряжаются Zn(OH)+ и Zn(OH)2. В работе [25] установлено, что при электровосстановлении ионов никеля (II) в системе Ni2+–C2O$_{4}^{{2 - }}$ комплекс Ni(C2O4)$_{2}^{{2 - }}$ во всех случаях не принимает участия в электродном процессе. Исследователями [26] предложен следующий механизм разряда никеля из аммиачных комплексов:
(1)
${{[{\text{Ni}}{{({\text{N}}{{{\text{H}}}_{{\text{3}}}})}_{n}}]}^{{2 + }}} + {\text{e}} \to {{[{\text{Ni}}{{({\text{N}}{{{\text{H}}}_{{\text{3}}}})}_{m}}]}^{ + }} + (n - m){\text{N}}{{{\text{H}}}_{3}},$(2)
${{[{\text{Ni}}{{({\text{N}}{{{\text{H}}}_{{\text{3}}}})}_{m}}]}^{ + }} \to [{\text{Ni}}{{({\text{N}}{{{\text{H}}}_{{\text{3}}}})}_{m}}]_{{{\text{(ads)}}}}^{ + },$(3)
$[{\text{Ni}}{{({\text{N}}{{{\text{H}}}_{{\text{3}}}})}_{m}}]_{{{\text{(ads)}}}}^{ + } + {\text{e}} \to {\text{Ni}} + {\text{mN}}{{{\text{H}}}_{3}}.$В литературе отсутствует информация о механизме электроосаждения сплавов цинка с металлами подгруппы железа из электролитов, содержащих одновременно аммиачные и оксалатные комплексы металлов. Поэтому в настоящей работе выполнено исследование процессов катодного осаждения сплавов Zn–Ni из оксалатно-аммонийных электролитов.
ЭКСПЕРИМЕНТАЛЬНАЯ ЧАСТЬ
Растворы электролитов готовили из реактивов квалификации “ч.д.а.” на дистиллированной воде путем растворения каждого компонента электролита в отдельном объеме с последующей фильтрацией и сливом растворов в общую емкость. Электроосаждение проводили в ячейке из органического стекла объемом 120 мл. Покрытия осаждали с помощью лабораторного источника питания MPS-3005L-3 Matrix. В качестве катодов использовали образцы из стали 08кп. Подготовка образцов включала обезжиривание в растворе, содержащем 20 г/л Na2CO3 ⋅ 10H2O, 20 г/л Na3PO4 ⋅ ⋅ 12H2O, 3 г/л синтанола ДС-10, при температуре 60–65°С (15 мин) и травление в 10% растворе HCl с промежуточными промывками. Качество покрытий определяли по внешнему виду и сцеплению с основным металлом соответственно согласно ГОСТ 9.301-86 и ГОСТ 9.302-88. Процесс осаждения проводили при температуре 20–60°С и катодных плотностях тока 0.5–5.0 А/дм2. Толщина покрытий составляла 6 мкм. Исследование кинетики электрохимического осаждения Zn–Ni сплавов проводили путем снятия катодных поляризационных кривых из оксалатно-аммонийных электролитов. Потенциодинамические кривые снимали с использованием потенциостата P-30J “Элинс” со скоростью развертки потенциала 5 мВ/с. Электродом сравнения служил насыщенный хлоридсеребряный электрод ЭВЛ-1М1, вспомогательным – платиновый. Полученные значения потенциала пересчитывали относительно стандартного водородного электрода (С.В.Э.). Выход по току рассчитывали по методике [3]. Парциальные поляризационные кривые были построены на основании результатов количественного анализа элементного состава покрытий методом рентгеновского дисперсионного микроанализа на сканирующем электронном микроскопе Tescan Vega 3 SBH с учетом выхода по току осаждаемых металлов в каждой точке парциальной кривой. Для измерения pH и рНs использовали иономер лабораторный И-160МП. Измерение pHs приэлектродного слоя в ходе электролиза проводилось методом зондирования рН приэлектродного слоя с помощью стеклянного электрода с обтягивающей его никелевой сеткой (исследуемым электродом) согласно методике [27]. Данные по величинам рНs и элементному составу покрытий были получены при гальваностатическом режиме поляризации.
ОБСУЖДЕНИЕ РЕЗУЛЬТАТОВ
Существенным недостатком традиционных сульфатно-хлоридных электролитов для электроосаждения сплавов цинк-никель является узкий интервал рабочих значений рН растворов. Применение комплексных электролитов позволяет сохранить их стабильность при изменении кислотности. Результаты расчетов ионных равновесий в системе Zn2+–Ni2+–${\text{SO}}_{4}^{{2 - }}$–${{{\text{C}}}_{{\text{2}}}}{\text{O}}_{4}^{{2 - }}$–NH3 [18, 19] свидетельствуют о том, что при совместном присутствии ионов цинка и никеля в интервале значений рН от 3.5 до 8.0 основную долю частиц в растворе составляют оксалатные комплексы осаждаемых металлов (рис. 1), обеспечивающие высокую стабильность электролита. При увеличении рН более 8 равновесные концентрации оксалатных комплексов резко снижаются, при этом также быстро возрастает доля аммиакатных комплексов цинка и никеля.
Рис. 1.
Диаграмма распределения никеля и цинка в электролите, содержащем 0.704 моль/л оксалата аммония, 0.063 моль/л сульфата никеля и 0.063 моль/л сульфата цинка: 1 – NiC2O4, 2 – Ni(C2O4)$_{2}^{{2 - }}$, 3 – Ni(C2O4)34-, 4 – Ni(NH3)$_{3}^{{2 + }}$, 5 – Ni(NH3)$_{4}^{{2 + }}$, 6 – Ni(NH3)$_{5}^{{2 + }}$, 7 – Ni(NH3)$_{6}^{{2 + }}$, 8 – ZnC2O4, 9 – Zn(C2O4)$_{2}^{{2 - }}$, 10 – Zn(C2O4)$_{3}^{{4 - }}$, 11 – Zn(NH3)$_{3}^{{2 + }}$, 12 – Zn(NH3)$_{4}^{{2 + }}$, C – равновесная концентрация.
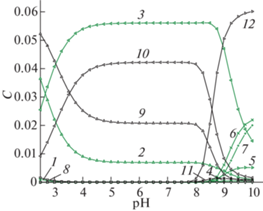
Для оценки влияния содержания ионов металлов на закономерности их разряда из оксалатно-аммонийных электролитов были проведены эксперименты по электроосаждению сплавов цинк-никель с различным соотношением концентраций компонентов. Осаждение цинк-никелевых сплавов из оксалатно-аммонийных электролитов происходит в области между потенциалами осаждения никеля и цинка (рис. 2). Результаты исследований, проведенных ранее [20, 21] методом циклической вольтамперометрии, также свидетельствуют о том, что наименьшая катодная поляризация, преимущественно диффузионного характера, наблюдается при осаждении цинка, а наибольшая – для никеля. При соотношении концентраций NiSO4 : ZnSO4 = 1 : 2 выход по току сплава имеет относительно высокие значения (98% при j = 1 А/дм2). На основании результатов элементного анализа покрытий были построены частные поляризационные кривые выделения цинка, никеля и водорода (рис. 3), свидетельствующие о том, что скорость осаждения цинка в рабочем интервале плотностей тока в несколько раз превышает скорости осаждения никеля и выделения водорода. При равных концентрациях сульфатов цинка и никеля в растворе (электролит № 2) выход по току цинк-никелевого сплава несколько снижается по сравнению с электролитом № 1 (74% при j = 1 А/дм2), скорость осаждения цинка также снижается и при высоких потенциалах становится равной скорости выделения водорода. При увеличении содержания никеля в электролите выход по току цинк-никелевого сплава снижается относительно других исследуемых электролитов (71% при j = 1 А/дм2), скорость осаждения цинка также снижается и при высоких потенциалах скорость выделения водорода превышает скорость осаждения цинка.
Рис. 2.
Суммарные поляризационные кривые катодного осаждения никеля (1), сплавов никеля и цинка (2–4), цинка (5) при 50°С из растворов оксалата аммония (0.704 моль/л), содержащих: 1 – 0.063 моль/л NiSO4, 2 – 0.084 моль/л NiSO4 и 0.042 моль/л ZnSO4, 3 – 0.042 моль/л NiSO4 и 0.084 моль/л ZnSO4, 4 – 0.063 моль/л NiSO4 и 0.063 моль/л ZnSO4, 5 – 0.063 моль/л ZnSO4.
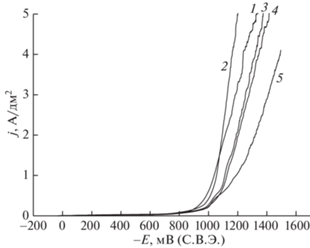
Рис. 3.
Парциальные кривые осаждения цинка, никеля и выделения водорода из растворов оксалата аммония (0.704 моль/л), содержащих 0.042 моль/л NiSO4 и 0.084 моль/л ZnSO4 (а), 0.063 моль/л NiSO4 и 0.063 моль/л ZnSO4 (б), 0.084 моль/л NiSO4 и 0.042 моль/л ZnSO4 (в).
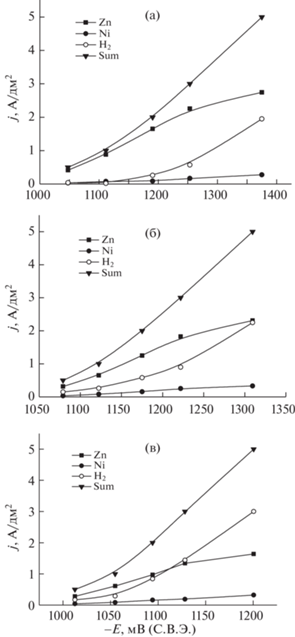
При исследовании процесса осаждения сплавов Zn–Ni из оксалатно-аммонийных электролитов было установлено, что после включения тока в течение нескольких секунд электролиза рНs прикатодного слоя резко увеличивается (рис. 4). Рост рНs приэлектродного слоя связан с протеканием параллельной реакции выделения водорода, имеющей место при катодном осаждении электроотрицательных металлов. При этом равновесные составы частиц в объеме электролита (при pH 6.1–6.5) и в приэлектродном слое (при pHS 9.0–9.4) существенно различаются (рис. 1). При рН < 8 поведение системы Zn2+–Ni2+–${\text{SO}}_{4}^{{2 - }}$–${{{\text{C}}}_{2}}{\text{O}}_{4}^{{2 - }}$–NH3 определяется главным образом процессами образования оксалатных бис- и трис-комплексов цинка и никеля(II). В более щелочной области происходит разрушение указанных комплексов, и оксалат-ионы замещаются молекулами аммиака. Изменение состава комплексов, доминирующих в приэлектродном слое, может оказывать большое влияние на скорость восстановления компонентов сплавов.
Рис. 4.
Изменение рНs прикатодного слоя в ходе электролиза (j = 1 А/дм2 и t = 20°C) в электролите, содержащем 0.704 моль/л оксалата аммония, 0.063 моль/л сульфата никеля и 0.063 моль/л сульфата цинка, τ – время электролиза.
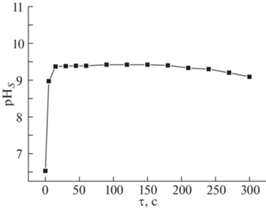
Для выяснения механизма процесса электроосаждения металлов из оксалатно-аммонийных электролитов парциальные поляризационные кривые для процесса разряда ионов никеля перестраивали в полулогарифмических координатах (рис. 5). Для цинка перестроение в полулогарифмические координаты не производили, так как в этом случае существенный вклад в торможение процесса вносит стадия транспорта ионов металла. Было установлено, что при увеличении содержания никеля в растворе имеет место уменьшение тафелевской постоянной b с 0.19 до 0.13 В, свидетельствующее об облегчении процесса разряда ионов никеля. В таком случае их разряд протекает ступенчато в две одноэлектронные стадии. Совокупность полученных в настоящей работе данных и результатов работ [18, 19] позволяет предложить следующий наиболее вероятный механизм электроосаждения никеля и цинка из оксалатно-аммонийных электролитов:
(4)
${{[{\text{M}}{{({{{\text{C}}}_{{\text{2}}}}{{{\text{O}}}_{{\text{4}}}})}_{3}}]}^{{4 - }}} + n{\text{N}}{{{\text{H}}}_{3}} \to {{[{\text{M}}{{({\text{N}}{{{\text{H}}}_{{\text{3}}}})}_{n}}]}^{{2 + }}} + 3{{{\text{C}}}_{{\text{2}}}}{\text{O}}_{4}^{{2 - }},$(5)
${{[{\text{M}}{{({\text{N}}{{{\text{H}}}_{{\text{3}}}})}_{n}}]}^{{2 + }}} + {\text{e}} \to {{[{\text{M}}{{({\text{N}}{{{\text{H}}}_{{\text{3}}}})}_{m}}]}^{ + }} + (n - m){\text{N}}{{{\text{H}}}_{3}},$(6)
${{[{\text{M}}{{({\text{N}}{{{\text{H}}}_{{\text{3}}}})}_{m}}]}^{ + }} \to [{\text{M}}{{({\text{N}}{{{\text{H}}}_{{\text{3}}}})}_{m}}]_{{{\text{(ads)}}}}^{ + },$(7)
$[{\text{M}}{{({\text{N}}{{{\text{H}}}_{{\text{3}}}})}_{m}}]_{{{\text{(ads)}}}}^{ + } + {\text{e}} \to {\text{M}} + m{\text{N}}{{{\text{H}}}_{3}}.$(8)
$2{{{\text{H}}}_{{\text{2}}}}{\text{O}} + 2{\text{e}} \to {{{\text{H}}}_{2}} + 2{\text{O}}{{{\text{H}}}^{ - }}$Рис. 5.
Парциальные поляризационные кривые электроосаждения никеля из электролитов, содержащих оксалат аммония (0.704 моль/л), 0.042 моль/л NiSO4 и 0.084 моль/л ZnSO4 (1), 0.063 моль/л NiSO4 и 0.063 моль/л ZnSO4 (2), 0.084 моль/л NiSO4 и 0.042 моль/л ZnSO4 (3).
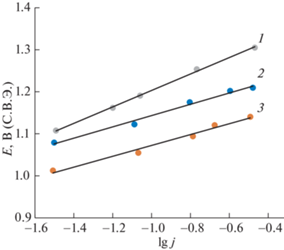
Ранее [18, 19] методом рентгенодифракционного анализа в составе покрытий сплавами цинк-никель, полученных из оксалатно-аммонийных электролитов, было обнаружено присутствие интерметаллических соединений NiZn и Ni5Zn21. В частности, в составе покрытий Zn–Ni, полученных на медных образцах из оксалатно-аммонийных электролитов № 2 и № 3, рентгенографически установлено присутствие гомогенной фазы интерметаллического соединения Ni5Zn21. Образование интерметаллических соединений NiZn и Ni5Zn21 обеспечивает высокую коррозионную стойкость покрытий, осажденных из оксалатно-аммонийных электролитов.
Исследование выполнено в рамках государственного задания на выполнение НИР. Тема № FZZW-2020-0010. Исследование проведено с использованием ресурсов Центра коллективного пользования научным оборудованием ИГХТУ (при поддержке Минобрнауки России, соглашение № 075-15-2021-671).
Список литературы
Окулов В.В. Цинкование. Техника и технология. М.: Глобус, 2008. 252 с.
Мельников П.С. Справочник по гальванопокрытиям в машиностроении. М.: Машиностроение, 1991. С. 156.
Бахчисарайцьян Н.Г., Борисоглебский Ю.В., Буркат Г.К. Практикум по прикладной электрохимии. Л.: Химия, 1990. 304 с.
Винокуров Е.Г. // Физикохимия поверхности и защита материалов. 2010. Т. 46. № 5. С. 543.
Винокуров Е.Г., Бондарь В.В. // Изв. вузов. Химия и хим. технология. 2009. Т. 52. № 2. С. 33.
Hammami O., Dhouibi L., Bercot P., Rezrazi E.A. // Can. J. Chem. Eng. 2013. V. 91. P. 19.
Ortiz-Aparicio J.L., Meas Y., Trejo G., Ortega R. et al. // J. Appl. Electrochem. 2011. V. 41. P. 669.
Kahoul A., Azizi F., Bouaoud M. // Trans. IMF. 2017. V. 95. N. 2. P. 106.
Kamel M.M., Anwer Z.M., Abdel-Salam I.T., Ibrahim I.S. // Trans. IMF. 2010 V. 88. № 4. P. 191.
Karimzadeh A., Aliofkhazraei M., Walsh F.C. // Surf. Coat. Technol. 2019. V. 372. P. 463.
Соцкая Н.В., Сапронова Л.В., Долгих О.В. // Электрохимия. 2014. Т. 50. № 12. С. 1271.
Vidu R., Perez-Page M., Quach D.V. et al. // Electroanalysis. 2015. V. 27. P. 2845.
Ченцова Е.В., Почкина С.Ю., Соловьева Н.Д., Лопухова М.И. // Изв. вузов. Химия и хим. технология. 2019. Т. 62. № 4. С. 128.
Bengoa L.N., Pary P., Conconi M.S., Egli W.A. // Electrochim. Acta. 2017. V. 256. P. 211.
Jovic B.M., Lanjevac U., Krstaji N.V., Jovic V.D. // Ibid. 2013. V. 114. P. 813.
Lacnjevac U., Jovic B.M., Jovic V.D. // J. Electrochem. Soc. 2012. V. 159. № 5. P. D310.
Красиков А.В., Красиков В.Л. // Журн. прикл. химии. 2012. Т. 85. № 5. С. 735.
Шеханов Р.Ф., Гридчин С.Н., Балмасов А.В. // Электрохимия. 2018. Т. 54. № 4. С. 408.
Шеханов Р.Ф., Гридчин С.Н., Балмасов А.В., Румянцева К.Е. // Изв. вузов. Химия и хим. технол. 2015. Т. 58. № 11. С. 54.
Шеханов Р.Ф., Гридчин С.Н., Балмасов А.В. // Электронная обработка материалов. 2020. Т. 56. № 2. С. 9.
Камышева К.А., Шеханов Р.Ф., Гридчин С.Н., Балмасов А.В. // Изв. АН. Сер. хим. 2020. № 7. С. 1272.
Шеханов Р.Ф., Гридчин С.Н., Балмасов А.В. // Физикохимия поверхности и защита материалов. 2017. Т. 53. № 3. С. 316.
Шеханов Р.Ф., Гридчин С.Н., Балмасов А.В., Мокрецов Н.Е. // Изв. вузов. Химия и хим. технология. 2021. Т. 64. № 10. С. 72.
Стромберг А.Г. // Журн. физ. химии. 1957. Т. 31. № 8. С. 1704.
Турьян Я.И. // Электрохимия. 1984. Т. 20. № 12. С. 1589.
Grujicic D., Pesic B. // Electrochim. Acta. 2006. V. 51. P. 2678.
Бенсон В.В., Китаев И.В. // Изв. вузов. Химия и хим. технология. 1996. Т. 39. № 1–2. С. 36.
Дополнительные материалы отсутствуют.
Инструменты
Журнал физической химии