Физика и химия стекла, 2019, T. 45, № 6, стр. 578-589
Искровое плазменное спекание функциональных керамик специального назначения на основе UO2, ZrO2, Fe3O4/α-Fe2O3
Е. К. Папынов 1, 2, О. О. Шичалин 1, 2, *, М. А. Медков 1, Д. Н. Грищенко 1, И. А. Ткаченко 1, А. Н. Федорец 2, В. С. Печников 2, А. В. Голуб 1, И. Ю. Буравлев 1, 2, И. Г. Тананаев 1, 2, В. А. Авраменко 1, 2
1 Институт химии Дальневосточного отделения РАН
690022 Владивосток, пр. 100-лет Владивостоку, 159, Россия
2 Дальневосточный федеральный университет
690091 Владивосток, ул. Суханова, 8, Россия
* E-mail: oleg_shich@mail.ru
Поступила в редакцию 05.09.2017
Аннотация
В работе изучены возможности получения керамики специального назначения по технологии искрового плазменного спекания по принципу низковольтного электроимпульсного консолидирования порошковых в условиях внешней механической нагрузки. Получена керамика для атомной, медицинской и электротехнической отрасли. Впервые представлены методологическое описание и особенности данной методики получения ядерной керамики в виде таблеточного топливного изделия UO2, с теоретической плотностью более 97.6% композитной биокерамики (на основе ZrO2, допированного гидроксиаппатитом) с регулируемой (мезо-, макро-) пористостью и высокой прочностью при сжатии ∼400 МПа, магнитной керамики, устойчивой к перемагничиванию, на основе наноструктурированных фаз оксидов железа Fe3O4/α-Fe2O3, с намагниченностью насыщения 50 эме/г.
ВВЕДЕНИЕ
Принцип технологии искрового плазменного спекания (ИПС) основан на электроимпульсном нагревании порошков прямым импульсным током под действием внешней механической нагрузки. Эффективность ИПС зависит от электропроводности спекаемого материала [1, 2]. Механизм спекания токопроводящих порошков основан на эффекте перколяции. За счет повышения плотности тока и выделения большого количества энергии (тепло Джоуля–Ленца) в местах контактов частиц происходит мгновенное локальное нагревание, частичное поверхностное испарение и диффузия, в результате которых материал спекается. Спекание диэлектриков методом ИПС заключается в нагревании токопроводящей пресс-формы с последующей передачей тепла от ее нагретых стенок в объем спекаемого материала. В отдельных случаях данный эффект сравнивают с эффектом Пельтье, при котором возникает термоэлектрическое явление в местах контакта двух различных по электропроводности материалов (спекаемого диэлектрика и токопроводящих элементов пресс-формы).
Основными преимуществами технологии ИПС в сравнении с традиционными способами получения керамики являются: высокая скорость нагревания (более 200–300°С/мин) и более низкая температура спекания (в среднем ниже на 30%); минимальное время цикла (несколько минут); равномерное распределение тепла по образцу и его гомогенное спекание; достижение максимальной плотности материала (99.9% от теоретической); контролируемая пористость; минимальное влияние на микроструктуру (минимальный рост зерна); отсутствие связующих добавок; испарение поверхностных примесей (очистка и активация поверхности) [1, 2].
В настоящем исследовании продемонстрированы высокотехнологичные возможности ИПС на примере синтеза функциональной керамики специального назначения: современной ядерной, биоактивной и магнитной керамики исключительного качества, которая чрезвычайно востребована в атомной, медицинской и электротехнической отраслях.
ЭКСПЕРИМЕНТАЛЬНАЯ ЧАСТЬ
Реактивы и оборудование
Для получения керамики использовали порошки диоксида урана (UO2.12) (обедненного по изотопу урана-235), диоксида циркония (ZrO2) марки “х. ч.”, карбоната кальция (CaCO3) марки “х. ч.”, гидрофосфата аммония ((NH4)2HPO4) марки “х. ч.”, оксида железа магнетит–гематит (Fe3O4/α-Fe2O3), синтезированного по методике [3].
ИПС порошков проводили на установке SPS-515S (“Dr. Sinter*LABTM”, Япония) с использованием графитовых пресс-форм с рабочим размером 15.5 × 30 мм. Для предотвращения припекания спекаемого порошка к пресс-форме и плунжерам использовали графитовую фольгу толщиной 200 мкм. Температуру ИПС процесса контролировали с помощью пирометра, сфокусированного на отверстие глубиной 5.5 мм, расположенного на середине плоскости внешней стенки пресс-формы. Периодичность генерируемого низковольтового импульса в режиме ON/OFF составила 12/2, длительность 3.3 мс, частота 50 Гц.
Методика синтеза
ИПС порошков проводили по следующей схеме: навеску заданной массы исходного порошка помещали в пресс-форму (давление прессования 20.7 МПа). Далее пресс-форму с порошком помещали в вакуумную камеру (остаточное давление 6 Па), после чего проводили спекание при различных температурах и давлении с последующим охлаждением.
Керамическое ядерное топливо на основе UO2. Температура ИПС порошков UO2 была 1250, 1450, 1650°С при постоянном давлении прессования 24.5 Мпа. Скорость нагревания составила 206°С/мин, время выдержки при достижении максимальной температуры – 5 мин, длительность охлаждения до комнатной температуры 30 мин. Данные о полученных образцах представлены в табл. 1.
Таблица 1.
Характеристики образцов таблеток на основе UO2, полученных методом ИПС
№ п/п | Тспекания, °С | Фазовый состав | mисх., г | mконеч., г | ρ, г/см3 | ρ(теор), % |
---|---|---|---|---|---|---|
1 | 1250 | UO2.00; UO2.13 | 3.474 | 3.404 | 10.71 | 97.62 |
2 | 1450 | 3.523 | 3.459 | 10.77 | 98.17 | |
3 | 1650 | 3.502 | 3.423 | 10.76 | 98.09 |
Биоактивная керамика на основе гидроксиапатита ZrO2/ГАП. Для ИПС использовали многокомпонентную смесь состава (мас. %): 80ZrO2, 15 (CaCO3 и (NH4)2HPO4) и 5 MgO. Дополнительно применяли порообразователь – мелкодисперсный порошок технического углерода фракцией 1–500 мкм в количестве 2, 5, 10 и 15 мас. %. Температура ИПС составляла 900 и 1300°С, скорость нагревания 170°С/мин, постоянное давление прессования 22.3 МПа, время выдержки при максимальной температуре 5 мин, длительность охлаждения до комнатной температуры 30 мин. Дополнительную обработку образцов для удаления технического углерода проводили в муфельной печи в атмосфере воздуха при температуре 1000°С со скоростью нагревания 5°С/мин и временем выдержки 30 мин. Серия полученных образцов представлена в табл. 1.
Магнитная керамика на основе Fe3O4/α-Fe2O3. Температура ИПС консолидации порошков составила 700, 800, 900, 1000, 1100°С, при постоянной нагрузке 24.5 МПа, скорость нагревания 170°С/мин, время выдержки 5 мин, длительность охлаждения до комнатной температуры 30 мин. Серия полученных образцов также представлена в табл. 1.
Методы исследования
Идентификацию фаз полученных образцов осуществляли с помощью рентгенофазового анализа (РФА) на дифрактометре D8 Advance, (Bruker AXS, Германия). Распределение пор по размерам определяли на ртутном поромере AutoPore IV (Micromeritics GmbH, США). Поверхность и пористость твердых тел анализировали методом физической адсорбции (БЭТ) на приборе ASAP 2020 (Micromeritics GmbH, США). Изображения микроструктуры исследуемых материалов получены методом растровой электронной микроскопии (РЭМ) на приборах S-3400N (Hitachi, Япония) и двулучевой установке (Dual Beam) Carl Zeiss CrossBeam 1540 XB (Германия). Магнитные характеристики исследовали на СКВИД-магнитометре (Quantum Design, США). Измерение удельной плотности проводили методом гидростатического взвешивания на весах AdventurerTM (Ohaus Corporation, США). Механическую прочность на сжатие для образцов цилиндрической формы определяли на разрывной машине Autograph AG-X plus 50 kN (Shimadzu, Япония). Внутреннюю структуру образцов магнитной керамики исследовали с использованием метода травления ионным пучком “Focused Ion Beam” (FIB) на электронном микроскопе Helios NanoLab 450S “FEI” (США) и пучком Ga-ионов для получения внутреннего среза.
РЕЗУЛЬТАТЫ И ИХ ОБСУЖДЕНИЯ
Керамическое ядерное топливо
Получение высокопрочного керамического топлива (топливных таблеток) на основе UO2, UN, UC, UC2, а также топливных композиций (U,Pu)O2, (U,Th)C2, (U,Pu)C, представляющих собой тугоплавкие материалы с температурой плавления более 2600°С, является сложной технологической задачей [4]. В мировой практике широко применяют технологии спекания в отсутствие и под давлением, что обеспечивает формирование топливных таблеток требуемой теоретической плотности (95–97.5%), необходимой пористости, высокой механической прочности и термической стойкости. Существует ряд недостатков при изготовлении готовых изделий указанными подходами. Специалисты отмечают неравномерность усадки материала по высоте, а также нарушение геометрической формы конечного изделия, и, как следствие, увеличение количества бракованных изделий. Предлагаемые решения для повышения плотности изделий за счет усиления нагрузки прессования являются нецелесообразными. В этом случае возможна перепрессовка материала, вследствие чего заготовки таблеток расслаиваются при выпрессовке из-за внутреннего напряжения в материале. При больших нагрузках происходит быстрый износ дорогостоящих пресс-форм и пуансонов. Добавление веществ-лубрикаторов в исходный порошок не способствует получению высокой плотности изделий за счет избыточного порообразования при выгорании смазки. Энергозатраты остаются ключевой проблемой традиционного спекания, так как температурные и временные режимы процесса значительно высоки и для UO2 составляют 1700–1800°С при многочасовой выдержке [5]. Перспективность ИПС производства UO2 керамики высокой плотности (более 96% от теоретической) при температуре от 1050°С за минимальный цикл от 30 с, доказана некоторыми зарубежными исследователями [6, 7]. В России передовые возможности технологии ИПС применительно к получению топливной керамики ядерного назначения изучены лишь на примере получения нитрида урана [8]. Исследования по ИПС UO2 топлива из порошков, промышленно производимых отечественными предприятиями, ранее никем не проводились.
В настоящей работе исследована особенность ИПС товарного порошка UO2, дополнительно термически обработанного. Основными реализуемыми задачами были эффективное спекание порошка UO2 в таблетку с теоретической плотностью более 97% и снижение температуры и времени спекания по сравнению с традиционными методами.
Результатом спекания порошков UO2 методом ИПС стали образцы плотных таблеток. Состав исходного порошка (по данным РФА) представляет собой смесь диоксидов урана различного стехиометрического состава UO2.00 и UO2.13 (табл. 1). Состав кристаллических фаз порошка остается неизменным при различных температурах спекания. Установлено, что условия нагревания определяют форму и размер зерна в образцах. В образцах, синтезированных при менее низких температурах 1250 и 1450°С, наблюдаются открытые поры. Этот тип пор формируется на начальной стадии спекания (рис. 1а, 1б). Размер открытых пор зависит от степени и контакта спекаемых частиц. В высокотемпературных образцах (температура выше 1450°С) открытая пористость просматривается в меньшей степени, так как в области высоких температур активизируются твердофазные процессы (деформация, пластическое течение, диффузия, плавление и др.). Это приводит к интенсивному росту зерна, как показано на примере образца, спеченного при 1650°С (рис. 1в). Следует отметить, что средний размер зерен диоксида урана выше 5 мкм, что значительно больше, чем у низкотемпературных образцов (температура ниже 1450°С).
Биоактивная керамика на основе ZrO2/ГАП
Инертность к биологической среде, химическая и коррозионная стойкость, а также высокие прочностные характеристики керамики на основе ZrO2 позволяют успешно использовать ее для изготовления имплантов [9, 10]. Такая керамика имеет существенный недостаток, так как вследствие экранирования механических нагрузок постепенно происходит нежелательная резорбция костной ткани, прилегающей к имплантату [11]. Это связано со значительным различием физико-химических свойств импланта и костной ткани, что препятствует остеоинтеграции, отвечающей за анатомическую взаимосвязь между живой костью и поверхностью импланта [12]. Решение проблемы может быть найдено, во-первых, за счет придания или повышения биоактивных свойств керамики на основе ZrO2. В этом случае керамика, включающая в свой состав резорбируемые фазы, например трикальцийфосфат, или гидроксиапатит, имеет способность к биорезорбции, и при имплантации выполняет функцию строительного материала кости. Во-вторых, на стимулирующую активность также оказывает микроструктура костного импланта, в частности пористость отвечает за глубину прорастания биологической ткани в имплант. В этом случае при синтезе биокерамики развивают параметры кривизны, степень кристалличности и пористости. В-третьих усиливают механические характеристики керамики за счет различных методов порошковой металлургии [13]. Известно, что традиционные методы в большинстве случаев не обеспечивают неизменность микроструктуры материала ввиду жестких технологических условий синтеза.
Опираясь на перспективность технологии ИПС для синтеза керамики из ZrO2, продемонстрированную в [14], в настоящем исследовании предложен более оригинальный способ синтеза биокерамики подобного типа. Уникальность подхода получения композита ZrO2/ГАП обусловлена применением реакционного ИПС метода, где формирование биоактивной фазы (ГАП) в составе керамики происходит в ходе химической реакции “in situ” инициируемой в момент ИПС порошка ZrO2, в который добавляют CaCO3 и (NH4)2HPO4.
В ходе экспериментальной работы было проведено ИПС порошков ZrO2, содержащих реакционную смесь исходных компонентов биоактивной фазы (CaCO3 и (NH4)2HPO4), в том числе с добавкой порообразователя технического углерода. Соотношение реагирующих компонентов было выбрано по опыту, описанному в [15], и составило Ca/P = 1.66.
Степень протекания реакции при синтезе керамики можно оценить по формированию фаз трикальцийфосфата и(или) гидроксиапатита, выступающих в роли биоактивных добавок, образование которых осуществляли “in situ” в момент ИПС порошка ZrO2. Оптимальным температурным режимом ИПС для данной системы принято считать 1300°С. Этой температуры будет достаточно для спекания порошка ZrO2 и для глубокого химического взаимодействия компонентов реакционной смеси, образования кристаллических фаз. В результате экспериментов была получена серия образцов плотной керамики из ZrO2 с различными физико-химическими характеристиками (табл. 2).
Таблица 2.
Характеристики образцов керамики на основе ZrO2/ГАП
№ п/п | Исходный компонентный состав | Тспекания, °С | Фазовый состав | Прочность при сжатии, МПа | Sуд. (БЭТ), м2/г |
---|---|---|---|---|---|
1 | ZrO2 + РС* | 900 | ZrO2(монокл.); ZrO2(тетрагон); Ca10(PO4)6(OH)2 | 9 | 0.68 |
2 | ZrO2 + РС* | 1300 | 400 | 0.12 | |
3 | ZrO2 + РС + ТУ** 2% | 1300 | 362 | 0.24 | |
4 | ZrO2 + РС + ТУ** 5% | 1300 | 242 | 0.25 | |
5 | ZrO2 + РС + ТУ** 10% | 1300 | 150 | 0.29 | |
6 | ZrO2 + РС + ТУ** 15% | 1300 | 47 | 0.35 |
По результатам РФА состав твердых фаз образцов керамики ZrO2/ГАП в независимости от выбранной температуры соответствует смеси оксидов циркония в моноклинной и тетрагональной модификациях, содержащих гидроксиапатит (табл. 2). Добавка порообразователя (технического углерода) не влияет на конечный фазовый состав керамики, в табл. 2 образцы № 3 и 6 идентичны друг другу.
Морфология поверхности полученной керамики на основе ZrO2/ГАП представлена на РЭМ изображениях (рис. 2). Установлено, что микроструктура исследуемого образца пористая и состоит из частиц ZrO2 со средним размером 200–500 нм. Выявлено наличие некоторых областей, где частицы образуют бесформенные агломераты.
Рис. 2.
РЭМ изображения образца композитной керамики, полученной на основе 80 мас. % ZrO2 и 15 мас. %, с добавкой углеродного темплата (10 мас. %), методом реакционного ИПС при 1300°С (образец № 5, табл. 2).
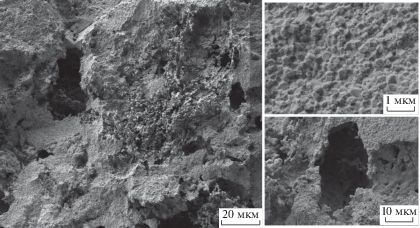
Установлено наличие макропор размером 10–20 мкм (рис. 3), образование которых в первую очередь достигнуто за счет порообразователя. Для формирования пористого каркаса керамики с заданными характеристиками был применен способ введения технического углерода, в исходную спекаемую систему с последующим его выжиганием дополнительной термоокислительной обработкой. Перспективность такого подхода была доказана ранее на примере синтеза высокопористой биоинертной силикатной керамики [16]. Предлагаемый способ позволяет регулировать размер и объем пор в полученной ИПС керамике, как показано на РЭМ изображениях и установлено методом порометрии (рис. 3, табл. 2). Происходит увеличение объема пор в зависимости от количества вводимого технического углерода (2, 5, 15 вес. %). Происходит формирование материала с различным распределением пор по размерам. Образец, полученный в отсутствие технического углерода, имеет микро- и мезопоры, что отражено на интрузионной кривой в области высоких давлений, а также на дифференциальной зависимости (рис. 3, кривая 1) в пределах 5–50 нм, а также некоторое количество макропор размером ∼500 нм. Образование такого типа пор в первую очередь связано с упаковкой мелкодисперсных частиц спекаемого порошка. Введение порообразователя приводит к исключению микро- и мезопор, в результате чего снижается величина удельной поверхности (табл. 2). Однако формируются большие макропоры размером от 1 мкм и более (рис. 3).
Рис. 3.
Зависимость общей (а) и дифференциальной (б) интрузии ртути в керамических образцах на основе ZrO2, полученные методом ИПС при 1300°С: №2 (без углерода) (1); № 3 (2 мас.% ТУ) (2); № 4 (5 мас. % ТУ) (3); № 6 (15 мас. % ТУ) (4). Номера образцов представлены в соответствии с табл. 2.
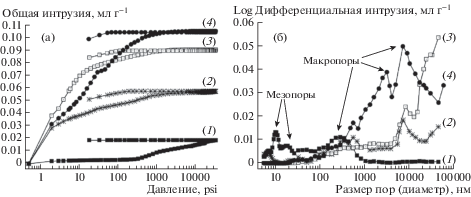
Еще одной вероятной причиной формирования пор различного размера в образцах керамики является образование большого количества газообразных продуктов химической реакции при взаимодействии CaCO3 с (NH4)2HPO4, по уравнению (1) и (2). При выделении газов в процессе спекания порошка возможно образование пустот в объеме образующейся керамики. Целесообразно предположить, что поверхность такого типа пор характеризуется повышенным содержанием кальций-фосфатных соединений – продуктов реакции, которые выстилаются на их внутренней поверхности.
Предлагаемый в работе способ реакционного ИПС обеспечивает получение керамики высокой конструкционной прочности, величина прочности при сжатии достигает 400 МПа (табл. 2), наряду с наличием объемной макропористости.
Магнитная керамика на основе Fe3O4/α-Fe2O3
Магнитная керамика занимает особое место в различных областях промышленности, науке и технике, где применяется в большинстве случаев как альтернатива металлическим магнитам. Высокое электрическое сопротивление керамики на основе оксидов железа, в частности ферритов, позволяет значительно снижать вихревые токи и связанные с ними потери энергии на перемагничивание [17]. Однако существует ряд сложностей синтеза магнитной керамики. Магнитные зависят от ряда факторов: фазового состава, размера, формы зерен и пор, наличия дефектов и др. [18]. Состав и микроструктура керамики могут влиять на магнитную анизотропию, вызывать/исключать возникновение упругих напряжений, тем самым влиять на магнитные характеристики материалов [18].
Технология ИПС имеет исключительное преимущество в получении магнитных материалов. Воздействие электромагнитного поля на консолидируемый порошок способствует упорядочению пространственного расположения магнитных моментов ионов металла в кристаллической решетке материала [19], что влияет на его магнитные свойства. Очевидные изменения магнитных характеристик отмечены на примере ИПС антиферромагнетика гематита в работах [20]. Для магнетита, а также порошков сложного состава из оксидов железа подобные исследования ранее не проводились. В настоящей работе изучен процесс ИПС магнитного порошка состава Fe3O4/α-Fe2O3 в области высоких температур (700–1100°С) с учетом фазовых и структурных превращений при формировании керамики, и их влияние на конечные магнитные свойства керамики.
Экспериментальным путем была получена серия образцов магнитной керамики с различными физико-химическими характеристиками (табл. 3).
Таблица 3.
Характеристики образцов керамики на основе Fe3O4/α-Fe2O3
№ п/п | Tспекания, °С | Фазовый состав | Sуд. (БЭТ), м2/г | Ms, эме/г | Hc, Э |
---|---|---|---|---|---|
300 K | 300 K | ||||
1 | Исходный | Магнетит (Fe3O4) Гематит (α-Fe2O3) | 47.3 | 23 | 130 |
2 | 700 | Магнетит (Fe3O4) | 7.7 | 50 | 90 |
3 | 800 | Гематит (α-Fe2O3) Магнетит (Fe3O4) | 0.17 | 15.5 | 70 |
4 | 900 | Гематит (α-Fe2O3) Магнетит (Fe3O4) | 0.15 | 12 | 115 |
5 | 1000 | Гематит (α-Fe2O3) Магнетит (Fe3O4) Углерод (C) | 0.1 | 7 | 98 |
6 | 1100 | Гематит (α-Fe2O3) Магнетит (Fe3O4) Углерод (C) | 0.1 | 18 | 110 |
По данным РФА установлено, что фазовый состав консолидируемого оксидного порошка изменяется после обработки ИПС. На начальном этапе при 700°С присутствует только магнетит. С повышением температуры в образце появляется наряду с магнетитом и гематит (табл. 3). Наличие углерода в высокотемпературных образцах обусловлено его диффузией с поверхности пресс-форм [20].
Согласно морфологии поверхности консолидированных образцов видно, что в ходе процесса ИПС в начале происходит уплотнение образца, затем массоперенос через границы зерен (рис. 4а). Уплотнение образца и дисперсность частиц спекаемого порошка определяют размер и объем внешних пор, наличие которых в объеме керамики выявлено методом травления ионным пучком “Focused Ion Beam” (FIB) (рис. 4б). Отмечено, что повышение температуры ИПС сопровождается снижением величины удельной поверхности (Sуд) до минимальных значений (0.1 м2/г), (табл. 3), что, вероятно, приводит к повышению механической прочности исследуемых керамических образцов, как это было показано в [20]. Наличие внутренней пористости, которая свойственна исходному порошку [3] с величиной Sуд = 47.3 м2/г, в полученных образцах не выявлено. Высокие температуры ИПС интенсифицируют процессы диффузии, пластической деформации, ползучести и соответственно текучести материала, что приводит к деструкции внутренней пористости частиц порошка.
Рис. 4.
РЭМ изображения микроструктуры магнитной керамики, полученной методом ИПС при 900°С: поверхность (а) и поперечный срез, подготовленный методом FIB (б).
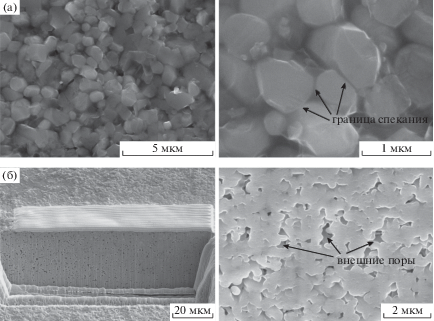
Зависимость намагниченности полученной керамики от напряженности приложенного внешнего магнитного поля и обратной восприимчивости от температуры представлена на рис. 5. Согласно результатам, намагниченность насыщения (Ms) керамики Fe3O4/α-Fe2O3, полученной спеканием в токе электрического поля при 700°С выше в два раза по сравнению с исходным образцом (табл. 3). Последующее увеличение температуры ИПС в интервале 800–1000°С сопровождается снижением значения Ms с 50 до 7 эме/г (рис. 5а). ИПС при 1100°С приводит к повышению намагниченности до 18 эме/г. Значения коэрцитивной силы находятся в одном интервале для всех синтезированных образцов, не зависят от температуры ИПС и характеризуют керамику как магнитожесткую систему (табл. 3). Наиболее вероятным объяснением изменений магнитных свойств образцов являются их фазовый состав, микроструктура, физические характеристики. В процессе спекания широко распространены фазовые превращения оксидов железа [21, 22]. В нашем случае этот процесс происходит при высокотемпературной обработке свыше 1000°С (табл. 3) [20]. Второй вероятной причиной, влияющей на магнитность получаемой керамики, являются рост зерна, микроструктура, пористость [20]. Физическим обоснованием магнитного поведения является воздействие постоянного импульсного тока на домены и доменные стенки, в которых стабилизируется направление намагниченности за счет обменной или однонаправленной магнитной анизотропии [23]. Несимметричность относительно начала координат петель гистерезиса свидетельствует о наличии в образцах обменного взаимодействия типа ферро/ферримагнетик – антиферромагнетик, что подтверждает предположения об изменениях фазового состава исходной смеси в процессе получения керамики. Анализ температурных зависимостей обратной магнитной восприимчивости образцов керамики показывает, что из аппроксимации T → 0 следует, что постоянная Кюри–Вейсса является отрицательной и это характерно для ферримагнитных веществ.
ЗАКЛЮЧЕНИЕ
В настоящей работе исследованы высокотехнологичные возможности ИПС метода применительно к получению новой функциональной керамики специального практического назначения. Впервые представлено методологическое описание, а также особенности ИПС синтеза керамик исключительного качества, чрезвычайно востребованных для атомной, медицинской и электротехнической отрасли.
Синтезировано керамическое ядерное топливо на основе порошков UO2, которые производят отечественные предприятия. Высокое качество изделия в виде таблеточного UO2 топлива обусловлено высокой удельной плотностью, более 97% от теоретического значения, получение которого возможно в мягких режимах спекания порошка (температура от 1250°С, время синтеза не более 14 мин).
Успешно получена биокерамика совместимого с живыми тканями композитного состава на основе ZrO2 допированного ГАП, перспективная в качестве костно-керамических имплантов, с функцией направленной резорбции. Биокерамика характеризуется уникальным набором структурных и прочностных характеристик: макропористость в широком диапазоне размера пор от 1 до 100 мкм и более, прочность на сжатие достигает 400 МПа. Кроме того, предложен оригинальный способ формирования биорезорбируемой фазы ГАП в объеме керамики методом “in situ” в ходе реакционного ИПС. Описан способ направленного формирования пористой структуры керамики, с учетом сохранения ее высокой конструкционной прочности.
Показана перспективность применения ИПС технологии для создания ранее неизученной магнитной керамики наноструктурированного типа, на основе смешaнного состава железо-оксидных фаз Fe3O4/α-Fe2O3, с высокой устойчивостью к перемагничиванию и востребованной в электротехнике. Установлена целесообразность электроимпульсной консолидации магнитных порошков для получения структурированно-пористых магнитных керамокомпозитов, с величиной магнитного насыщения до 50 эме/г.
Представленные исследования указывают на большой потенциал технологии ИПС как перспективного метода для создания новейших функциональных керамик специальной практической направленности.
Научная работа состоит из комплекса исследований, которые проведены при финансовой поддержке: Российского научного фонда, проект № 17-73-20097 (раздел “Керамическое ядерное топливо”); гранта Президента Российской Федерации для молодых ученых, проект МК-177.2017.3 (раздел “Биоактивная керамика”); Российского фонда фундаментальных исследований, грант 16-33-00986 “мол_а” (раздел “Магнитная керамика”).
Список литературы
Tokita M. Trends in Advanced SPS Spark Plasma Sintering Systems and Technology // J. Soc. Powd. Tech (Japan). 1993. V. 30. P. 1149–1178.
Guillon O., Gonzalez-Julian J., Dargatz B., Kessel T., Schierning G., Räthel J., Herrmann M. Field-assisted sintering technology/spark plasma sintering: Mechanisms, materials, and technology developments // Adv. Eng. Mater. 2014. V. 16. P. 830–849.
Papynov E.K., Portnyagin A.S., Cherednichenko A.I., Tkachenko I.A., Modin E.B., Maiorov V.Y., Dran’kov A.N., Sokol’nitskaya T.A., Kydralieva K.A., Zhorobekova S.Z., Avramenko V.A. Uranium sorption on reduced porous iron oxides // Dokl. Phys. Chem. 2016. V. 468. P. 67–71.
Жиганов А.И., Гузеев В.В., Андреев Г.Г. Технология диоксида урана для керамического ядерного топлива. Томск: STT, 2002. 326 с.
Carrea A.J. Sintering of uranium dioxide in an atmosphere of controlled hydrogen content // J. Nucl. Mater. 1963. V. 8. P. 275–277.
Ge L., Subhash G., Baney R.H., Tulenko J.S., McKenna E. Densification of uranium dioxide fuel pellets prepared by spark plasma sintering (SPS) // J. Nucl. Mater. V. 2013. 435. P. 1–9.
Cologna M., Tyrpekl V., Ernstberger M., Stohr S., Somers J. Sub-micrometre grained UO2 pellets consolidated from sol gel beads using spark plasma sintering (SPS) // Ceram. Int. 2016. V. 42. P. 6619–6623.
Шорников Д.П., Бурлакова М.А., Тарасов Б.А., Никитин С.Н., Якуткина Т.В., Юрлова М.С. Получение и компактирование методами плазменно-искрового и электроимпульсного спекания нанопорошков нитрида урана // Вектор Науки ТГУ. 2013. Т. 3. № 25. С. 95–98.
Dubok V.A. Bioceramics – Yesterday, Today, Tomorrow // Powd. Metal. Met. Ceram. 2001. V. 39. P. 381–394.
Medkov M.A., Rudnev V.S., Grishchenko D.N., Djuizen I.V., Lukiyanchuk I.V., Papynov E.K., Portnyagin A.S., Gridasova E.A. Nano-sized calcium-phosphate powders and glass-ceramic coatings for medical purposes // Bioglass: Properties, Functions and Applications. 2016. P. 55–100.
Juhasz J.A., Best S.M. Bioactive ceramics: Processing, structures and properties // J. Mater. Sci. 2012. V. 47. P. 610–624.
Fini M., Giavaresi G., Torricelli P., Borsari V., Giardino R., Nicolini A., Carpi A. Osteoporosis and biomaterial osteointegration // Biomed. Pharm. 2004. V. 58. P. 487–493.
Rapacz-Kmita A., Ślósarczyk A., Paszkiewicz Z. Mechanical properties of HAp-ZrO2 composites // J. Europ. Ceram. Soc. 2006. V. 26. P. 1481–1488.
Yoshimura M., Ohji T., Sando M., Niihara K. Rapid rate sintering of nano-grained ZrO2-based composites using pulse electric current sintering method // J. Mater. Sci. Lett. 1998. V. 17. P. 1389–1391.
Safronova T.V., Putlyaev V.I., Ivanov V.K., Knot’ko A.V., Shatalova T.B. Powders Mixtures Based on Ammonium Pyrophosphate and Calcium Carbonate for Preparation of Biocompatible Porous Ceramic in the CaO–P2O5 System // Refract. Indust. Ceram. 2016. V. 56. P. 502–509.
Papynov E.K., Mayorov V.Y., Portnyagin A.S., Shichalin O.O., Kobylyakov S.P., Kaidalova T.A., Nepomnyashiy A.V., Sokol’nitskaya T.A., Zub Y.L., Avramenko V.A. Application of carbonaceous template for porous structure control of ceramic composites based on synthetic wollastonite obtained via Spark Plasma Sintering // Ceram. Int. 2015. V. 41. P. 1171–1176.
Buschow K.H.J., de Boer F.R. Physics of Magnetism and Magnetic Materials. Springer US, 2003. 182 p.
Liu Y., Sellmyer D.J., Shindo D. Handbook of Advanced Magnetic Materials. Springer US, 2006. 1794 p.
Liu J.P., Fullerton E., Gutfleisch O., Sellmyer D.J. Nanoscale Magnetic Materials and Applications. Springer: US, 2009. 719 p.
Papynov E.K., Tkachenko A.I., Portnyagin A.S., Modin E.B., Avramenko V.A. Fabrication of magnetic ceramic materials based on nanostructured hematite powder by spark plasma sintering // ARPN J Eng. Appli. Sci. 2016. V. 11. P. 5864–5870.
Adnan J., O’Reilly W. The transformation of γ-Fe2O3 to α-Fe2O3: Thermal activation and the effect of elevated pressure // Phys. Earth. Planet. Inter. 1999. V. 110. P. 43–50. https://doi.org/10.1016/S0031-9201(98)00128-9
Murakami M., Hirose K., Ono S., Tsuchiya T., Isshiki M., Watanuki T. High pressure and high temperature phase transitions of FeO // Phys. Earth. Planet. Inter. 2004. V. 146. P. 273–282.
Stöhr J., Siegmann H.C. Magnetism: From Fundamentals to Nanoscale Dynamics. Springer Berlin Heidelberg: Berlin, 2006. 812 p.
Дополнительные материалы отсутствуют.
Инструменты
Физика и химия стекла