Физика и химия стекла, 2020, T. 46, № 6, стр. 649-657
Синтез и исследование свойств жаростойких покрытий на основе композиции Si–B4C–ZrB2–ZrO2
А. Н. Николаев 1, И. Б. Баньковская 1, *, Д. В. Коловертнов 1
1 Институт химии силикатов им. И.В. Гребенщикова РАН
199034 Санкт-Петербург, наб. Макарова, 2, Россия
* E-mail: inbankov@isc1.nw.ru
Поступила в редакцию 25.02.2020
После доработки 28.07.2020
Принята к публикации 06.08.2020
Аннотация
Проведено исследование влияния наноразмерных частиц диоксида циркония на свойства жаростойкого покрытия, синтезируемого суспензионно-обжиговым методом на основе композиции кремний–карбид бора–диборид циркония. Изучена жаростойкость покрытий на подложках из графита и высокоглиноземной керамики, определен фазовый состав, морфология, твердость и электросопротивление покрытий.
ВВЕДЕНИЕ
Развитие металлургии, энергетики, радиотехники, микроэлектроники, космонавтики и авиастроения связано с решением задачи создания новых материалов конструкционного назначения для работы в экстремальных условиях – при высоких температурах, в агрессивных средах и при эрозионных воздействиях. В связи с этим поставлена задача – получить новые материалы с улучшенными свойствами.
В последние несколько лет тугоплавкие бориды, карбиды, нитриды широко используются как диффузионные барьеры в многослойных кремниевых интегральных схемах. Применение тугоплавких соединений в микроэлектронике позволяет получить тонкопленочные резисторы прецизионного класса с комплексом различных химических и физических свойств [1].
Высокоогнеупорные оксиды широко применяются в теплоизоляционных и теплозащитных покрытиях. Это обусловлено низкой теплопроводностью, жаростойкостью, химической инертностью большинства оксидов, их доступностью и дешевизной. В последнее время достигнуто существенное повышение их сопротивления термическому удару. Наиболее низкую теплопроводность в широком интервале температур имеют диоксиды циркония. Потери массы вследствие испарения, особенно из тонких покрытий и пористых материалов с высокой удельной поверхностью, ограничивает срок их службы. Наиболее низкой испаряемостью в вакууме при высоких температурах обладают оксиды циркония и тория.
Реализация многих современных микротехнологий и нанотехнологий связана с использованием композиционных порошков, представляющих собой частицы с модифицированной поверхностью. При этом в качестве исходных порошков могут использоваться материалы различной природы: металлы и оксиды [2]. В частности, чрезвычайно востребован диоксид циркония. Вещества на основе диоксида циркония обладают широким спектром полезных свойств, позволяющих использовать их в различных сферах науки и техники. Диоксид циркония, стабилизированный иттрием, благодаря высокой температуре плавления, фазовой стабильности, химической инертности, высокой твердости и ионной проводимости является не только востребованным термобарьерным и защитным материалом, но и чрезвычайно перспективен в качестве газочувствительного материала в химических сенсорах [3].
Повысить стойкость материалов к окислению можно различными способами. В работе [4] введение в состав добавок оксидов редкоземельных элементов позволило получить стекло с большей вязкостью, что в свою очередь понизило диффузию кислорода. В работе [5] изучено окисление керамики при добавлении силицидов. При введении такой добавки стойкость к окислению выше. В работе [6] рассматриваются многофазные керамические покрытия, которые были получены путем втирания различных порошков боридов (Zr, Hf, Та) в поверхность графитовых пластин.
Армирование оксидов металлическими волокнами является одним из перспективных методов повышения прочности и термостойкости. Волокна увеличивают поверхностную энергию сопротивления распространению трещин при термическом нагружении, а также критическую степень деформации в момент разрушения. Это связано с ветвлением трещин в матрице, упруго-хрупким и пластическим деформированием волокон, приводящим к остановке трещин [7].
В работе [8] проводится исследование влияния волокон Hi-Nicalon SiC на HfB2 в присутствии различных спекающих добавок, таких как Si3N4 или ZrSi2. Для формирования образцов используется метод искрового плазменного спекания. В результате исследований было показано, что волокна способствуют образованию колец HfC, которые увеличивают термостойкость системы.
В работе [9] исследована зависимость кинетики спекания искровой плазмой ультравысокотемпературной керамики. Установлено, что очистка исходного порошка ускоряет спекание искровой плазмой, уменьшает температуру спекания, а также способствует большей скорости усадки при более низкой температуре.
В настоящей работе, которая является продолжением ранее проведенных исследований [10, 11], покрытия синтезированы в воздушной среде, без использования дорогостоящего оборудования.
ЭКСПЕРИМЕНТАЛЬНАЯ ЧАСТЬ
Покрытия различных составов (табл. 1) наносили суспензионно-обжиговым методом на графит марки ГМЗ с целью его защиты от окисления и на высокоглиноземистую керамику (ВГК) для защиты от эрозии и придания темной окраски. Технологическая схема приготовления покрытий представлена в работе [12]. Онa основанa на приготовлении суспензии, содержащей исходные компоненты, нанесении на подложку из графита или ВГК слоя шликера, высушивания его и дальнейшего обжига при заданной температуре. В качестве связующего вещества при приготовлении шликера использовали двухпроцентный водный раствор карбоксиметилцеллюлозы.
Таблица 1.
Характеристика исходных компонентов
Наименование вещества | Химическая формула | Гранулометрический состав | Марка |
---|---|---|---|
Диборид циркония | ZrB2 | 5–30 мкм | ч |
Кремний | Si | 50 мкм | Кр-1 |
Карбид бора | B4С | 5–30 мкм | ГОСТ 5744-51 |
Диоксид циркония | ZrO2 стаб. Y2 O3 | <0.071 мкм | – |
Наноразмерные частицы диоксида циркония были получены из волокон, синтезированных темплатным методом [13, 14]. Покрытия наносили до достижения удельной толщины 80–100 мг/см2.
В процессе обжига происходит формирование покрытий, сопровождающееся физическими и химическими процессами.
Обжиг проводили в печи с нагревателями из карбида кремния. Покрытия формировали и испытывали по различным режимам (неизотермическому, изотермическому и “щадящему”) и испытывали при температурах 1000, 1200, 1300°С в течение 90 мин. Проводили по два параллельных опыта.
В работе использовали следующие методы анализа: рентгенофазовый (РФА), дифференциально-термический (ДТА), термогравиметрический, а также определяли электросопротивление.
РФА проводили на установке ДРОН-2 с использованием СuKα-излучения. Исследовали как порошкообразные образцы, так и поверхность покрытий на подложках (графит и ВГК). Для идентификации фаз использовали данные картотеки PDF-2: Si (75-0589), ZrB2 (75-1050), ZrO2 (Т) (80-0965), SiO2 (82-1410).
ДТА проводили на приборе системы Paulik–Paulik–Erdey Q-1500C (МОМ, Венгрия): порошкообразные образцы исходных компонентов без добавок оксида алюминия нагревали от комнатной температуры до 1000°С со скоростью 10°С/мин.
ОБСУЖДЕНИЕ РЕЗУЛЬТАТОВ
В результате взаимодействия исходных компонентов с кислородом из воздуха в интервале температур 500–1300°С формируется борокремнеземный стеклообразующий расплав, капсулирующий исходные компоненты и препятствующий проникновению кислорода воздуха внутрь образца. Был использован “щадящий” режим формирования (20–1000°С, ν = 100°С/мин; 1000–1300°С, ν = 10°С/мин).
Из рис. 1 видно, что температуры максимальных эффектов, связанных c окислением карбида бора и диборида циркония – 640–690°С, а в интервале 300–400°С происходит окисление кремния, который покрывается оболочкой из диоксида кремния, которая тормозит дальнейшее окисление. При введении модифицирующих добавок ход кривой ДТА существенно не меняется. Аналогичные результаты по окислению порошка кремния получены в работе [15].
После проведения ДТА порошкообразных смесей исходного состава, исходного состава с добавлением 15% диоксида циркония и с добавлением шунгита при нагревании от 20 до 1000°С установлено наличие трех экзотермических эффектов (для кремния – 350°С, а для карбида бора и диборида циркония – 640–690°С).
После проведения ДТА образцы представляли собой два слоя: нижний – порошкообразный, верхний – остеклованный. Поверхностный слой находился в контакте с кислородом воздуха, что приводило к образованию стеклообразующего расплава, препятствующего проникновению кислорода к внутреннему слою.
Дифрактограммы 1 (без термообрабоки) и 1 идентичны, следовательно, термообработка до 1000°С не повлияла на фазовый состав (рис. 2).
Рис. 2.
Дифрактограммы порошков исходной композиции без термообработки (1 без термообр.) и составов 1, 4, 5 (табл. 2) после термообработки по режиму 20–1000°С.
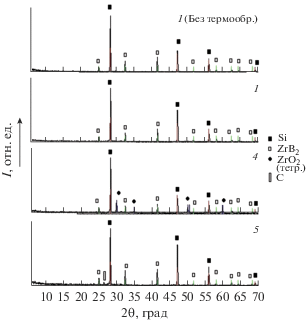
Проведение РФА продуктов окисления порошков после ДТА показало наличие исходных компонентов – кремния и диборида циркония, а также диоксида циркония и шунгита при введении их в состав (рис. 3).
Рис. 3.
Дифрактограммы поверхности графита с покрытиями, после термообработки при 1000 и 1300°C в течение 90 мин, составы 1, 4, 5 (табл. 2).
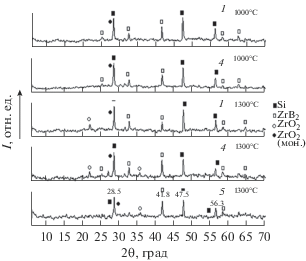
Основываясь на данных РФА и литературных данных, можно предположить протекание следующих реакций:
(1)
${\text{Zr}}{{{\text{B}}}_{{\text{2}}}} + 2.5{{{\text{O}}}_{{\text{2}}}} = {\text{Zr}}{{{\text{O}}}_{2}} + {{{\text{B}}}_{{\text{2}}}}{{{\text{О}}}_{{\text{3}}}}{\text{,}}$(3)
${{{\text{B}}}_{{\text{4}}}}{\text{С}} + 4{{{\text{O}}}_{{\text{2}}}} = 2{{{\text{B}}}_{{\text{2}}}}{{{\text{O}}}_{3}} + {\text{C}}{{{\text{O}}}_{{\text{2}}}},$Термодинамическая вероятность протекания реакций 1–3 была подтверждена в [10].
Покрытия на керамике (рис. 4) сохраняют прирост массы при 1000°С в течении 120 мин.
Рис. 4.
Изменение массы образцов керамики с покрытиями при 1000°С в течение 120 мин. Примечание. Образцы предварительно сформированы по неизотермическому режиму (20–1000°С)(ν = 10°C/мин).
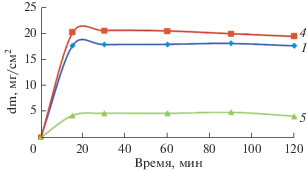
При повышении температуры до 1300°С наблюдается сохранение прироста массы в течении 90 мин.
Рис. 5.
Изменение массы образцов керамики с покрытиями при 1300°С в течение 90 мин. Примечание. Образцы сформированы по режиму (1000–1300°С) (ν = 2°С/мин).
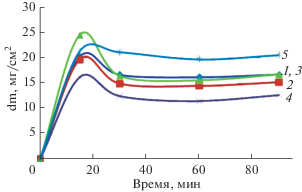
Покрытия были опробованы на нейтральной подложке (ВГК) и подтверждена их стойкость к окислению на воздухе. В отличие от ВГК на графите наблюдается незначительное выгорание.
Как видно из рис. 6, при термообработке образцов от 500 до 1300°С графит выгорает незначительно, благодаря тому что термоциклирование сопровождается залечиванием трещин.
Рис. 6.
Влияние температуры на жаростойкость образцов графита с покрытиями составов 1–5 (табл. 2) после выдержки при 500–1300°С на воздухе.
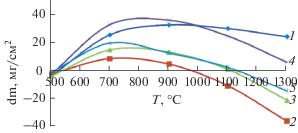
При изотермическом режиме (рис. 7) наблюдается прирост массы за 90 мин в диапазоне от 8 до 18 мг/см2, выгорания графита не наблюдается.
Рис. 7.
Изменение массы образцов графита с покрытиями составов 1–5 (табл. 2), термообработанных по режиму (1000–1300°С) + 1300°С на воздухе в течение 90 мин.
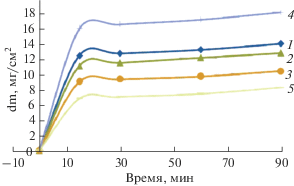
При испытании покрытий на графит в ряде случаев наблюдалось выгорание графита, связанное с образованием незначительных трещин. Ввиду наличия стеклообразующего расплава трещины залечивались. При сравнении результатов кинетики окисления образцов с покрытиями на ВГК и на ГМЗ было установлено, что при испытании при 1000, 1200 и 1300°C в течение 90 мин привес не превышает 20 мг/см2.
Определение электросопротивления
Измерение электросопротивления проводили в электрической печи с нагревателями из нихрома с использованием керамической измерительной ячейки двухконтактным методом. По полученным значениям был рассчитан lg ρ, и построена его зависимость от температуры. Из нее следует, что введение частиц ZrO2 или шунгита не оказывает существенного влияния на величину удельного электросопротивления, которая при 50°С достигает величины порядка 105 Ом · см. При повышении температуры до 800°С сопротивление образцов падает до величины порядка 103 Ом · см.
При введении наноразмерных частиц диоксида циркония или шунгита темно-серый цвет образцов сохранился. Они имеют заметный блеск, что говорит об образовании стеклофазы на их поверхности, причем, чем выше температура испытания, тем больше блеск. С помощью экспресс-метода было установлено, что все образцы являются малопористыми.
Рис. 8.
Зависимость удельного электросопротивления образцов графита с покрытиями составов 1–5 (табл. 2) от температуры.
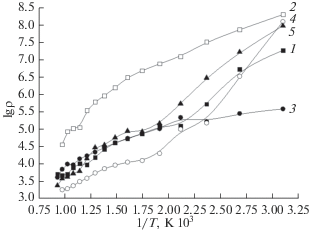
Твердость исследуемых покрытий
Измерения проводили с помощью маятникового прибора Персоза. Методика измерения проводилась по ГОСТ 5233-89 “Метод определения твердости по маятниковому прибору”.
Для исследования твердости покрытия были изготовлены три графитовых пластинки с покрытиями составов 1, 4 и 5 (табл. 2). Образцы были сформированы по режиму 1000–1300°С.
Таблица 2.
Составы исследованных композиций (по синтезу)
№ состава | Содержание компонентов, мас. % | |||
---|---|---|---|---|
Si | B4C | ZrB2 | ZrO2 | |
1 | 70 | 10 | 20 | – |
2 | 66.5 | 9.5 | 19 | 5 |
3 | 63 | 9 | 18 | 10 |
4 | 59.5 | 8.5 | 17 | 15 |
5 | 66.5 | 9.5 | 19 | 5 (шунгит) |
Исходя из данных представленных в табл. 3 следует, что исследуемые покрытия являются достаточно твердыми по отношению к эталонной пластине из стекла (твердость равна 1 у. е.). Добавки диоксида циркония и шунгита увеличивают твердость покрытий.
Внешний вид образцов графита и ВГК с покрытиями
До термообработки образцы имеют светло-серую окраску, вводимые добавки не влияют на внешний вид. Как на графите, так и на ВГК наблюдается прочное сцепление покрытий с подложкой после термообработки. Покрытия имеют темно-серый цвет, причем на поверхности графита наблюдается больший блеск, а при введении шунгита на обеих подложках цвет образцов становится более темным.
В работе [10] наноразмерные частицы оксида алюминия вводили в композицию для получения алюмоборосиликатного стеклообразующего расплава, который, благодаря большей вязкости, затрудняет диффузию кислорода в расплав. Частицы диоксида циркония вводили в состав композиции для повышения термостойкости, за счет увеличения гетерогенности покрытия.
Прирост массы образцов графита и керамики с покрытиями во всем диапазоне температур 1000–1300°С составлял в среднем 10 мг/см2 для графита и 15 мг/см2 для керамики независимо от природы добавки. Добавки существенно не влияют на прирост массы образцов в течение всего времени обжига (рис. 5). У образцов графита с покрытиями наблюдается частичное выгорание с последующим залечиванием дефектов с помощью стеклообразующего расплава. В случае керамики наибольший прирост массы происходит в первые 15 мин обжига.
В ходе проведения РФА в обоих случаях не удается обнаружить B4C в связи с его малым количеством в составе покрытия. Шунгит, как видно на рис. 2, фиксируется в составе исходного компонента после термообработки. Следует отметить, что шунгит придает покрытию более заметный блеск.
Шунгит вводился в состав покрытия для того, чтобы способствовать более равномерному распределению компонентов в составе покрытия [16].
ЗАКЛЮЧЕНИЕ
Синтезированы новые покрытия на основе композиции Si–B4С–ZrB2, модифицированной наноразмерными частицами диоксида циркония или шунгита. Использовались две подложки – графит и ВГК. Покрытия получены по энергосберегающей технологии, которая заключается в получении стеклообразующего расплава in situ на воздухе при нагревании.
Введение модифицирующих добавок существенного влияния на прирост массы образцов с покрытиями при термообработке не оказывает, но сохраняется термостойкость, повышается твердость, наблюдается хорошее сцепление с обеими подложками и удешевляется состав.
Авторы выражают благодарность И.Г. Поляковой за проведение РФА и ДТА.
Список литературы
Дворина Л.А., Драненко А.С. Применение тугоплавких соединений в микроэлектронике // Порошковая металлургия. 2000. № 9/10. С. 116–221.
Кац С.М. Высокотемпературные теплоизоляционные материалы. М.: Металлургия, 1981. 232 с.
Хамова Т.А. Разработка и исследование композиционных материалов на основе модифицированных кремнезолей и дисперсных оксидов алюминия. Автореферат. Санкт-Петербург: ИХС РАН, 2010. 20 с.
Gonzalez-Julian J., Cedillos-Barraza O., Doring S., Nolte S. Enhanced oxidation resistance of ZrB2/SiC composite through in situ reaction of gadolinium oxide in patterned surface cavities // Journal of the European Ceramic Society. 2014. V. 34. P. 4157–4166.
Grigoriev O.N., Galanov B.A., Lavrenko V.A., Pansasyuk A.D. Oxydation of ZrB2–SiC–ZrSi2 ceramics in oxygen // J. European Ceramic Society. 2010. V. 30. P. 2397–2405.
Yang J., Liu Z., Wang J., Wang H., Guo Q., Song J., Liu L. The structure of MB2-MC-C (M = Zr, Hf, Ta) multi-phase ceramic coatings on graphite // J. European Ceramic Society. 2014. V. 34. P. 2895–2904.
Симоненко Н.П., Попов В.С., Симоненко Е.П., Севастьянов В.Г., Кузнецов Н.Т. Получение тонких пленок 8% Y2O3–92% ZrO2 (8YSZ) с применением золь-гель технологии // Журн. неорган. хим. 2015. Т. 60. № 7. С. 878–886.
Silvestroni L., Nyngren M., Sciti. D. Study of the interactions between HfB2 and Hi-Nicalon fiber // J. European Ceramic Society. 2013. V. 33. P. 2879–2888.
Zamora V., Ortiz A. L., Guiberteau F., Nygren M. Crystal-Size dependence of the spark-plasma-sintering kinetics of ZrB2 ultra-high-temperature ceramics // J. European Ceramic Society. 2013. V. 33. P. 271–276.
Николаев А.Н., Баньковская И.Б., Коловертнов Д.В., Полякова И.Г. Синтез и исследование жаростойких покрытий на основе композиции кремний–карбид бора–борид циркония–оксид алюминия // Физика и химия стекла. 2018. Т. 44. № 5. С. 450–454.
Николаев А.Н., Баньковская И.Б., Пугачев К.Э., Коловертнов Д.В. Исследование морфологии и твердости покрытий на основе композиции Si–B4C–ZrB2 // Физика и химия стекла. 2019. Т. 45. № 2. С. 196–200.
Баньковская И.Б., Васильева И.А., Коловертнов Д.В. Процессы окисления композиций Si–B–ZrB2 в интервале температур 1000–1300°С // Физика и химия стекла. 2012. Т. 38. № 3. С. 409–416.
Ulyanova T.M., Krut’ko N.P. Nanoparticle Formation in the Synthesis of Nanostructured Fibers and Powders of Refractory Oxides // International J. Nanotechnology. 2006. V. 3. № 1. P. 47–56.
Ulyanova T.M., Vitiaz P.A., Krut’ko N.P., Titova L.V., Medichenko S.V., Shevchonok A.A. Nano-Structured ZrO2(Y2O3)–Al2O3 Fibrous Powders for Composite Materials // Issue “PM2010 World Congress–Nanotechnology”, Florence, Italy, 11–14 October 2010. V. 2. Manuscript 421. P. 126–133.
Попок В.Н., Бычин Н.В. Исследование параметров окисления порошков металлов и неметаллов в среде воздуха // Электронный научный журн. “Исследовано в России”. С. 405–415.
Васина Е.С., Матвейчикова П.В., Сычев М.М., Красовский А.Н., Новиков Д.В., Рожкова Н.Н. Фрактально-кластерная структура BaTiO3 в матрице цианэтилового эфира поливинилового эфира в присутствии шунгита // Международный симпозиум “Химия для биологии, медицины, экологии и сельского хозяйства” ISCHEM 2015. 2015. С. 101.
Дополнительные материалы отсутствуют.
Инструменты
Физика и химия стекла