Физика и химия стекла, 2021, T. 47, № 1, стр. 65-77
Металлизация алмаза как способ повышения работоспособности сверхтвердых материалов
Л. П. Ефименко 1, 2, *, С. П. Богданов 1, М. М. Сычев 1, 3
1 Санкт-Петербургский государственный технологический институт (технический университет)
190013 Санкт-Петербург, Московский проспект, 26, Россия
2 Санкт-Петербургский государственный электротехнический университет “ЛЭТИ”
197376 Санкт-Петербург, ул. Профессора Попова, 5, Россия
3 Институт химии силикатов им. И.В. Гребенщикова РАН
199034 Санкт-Петербург, наб. Макарова, 2, Россия
* E-mail: efimenkolp37@mail.ru
Поступила в редакцию 17.04.2020
После доработки 24.07.2020
Принята к публикации 06.08.2020
Аннотация
Рассмотрено современное состояние разработок в области металлизации алмазных порошков как способа повышения рабочих характеристик режущих и буровых инструментов путем повышения уровня удержания алмазов в матрице сверхтвердого материала. Последние годы основное внимание уделяется технологиям получения покрытий на основе карбидообразующих металлов (Cr, Ti, W, Mo и др.), обеспечивающих прочную химическую связь матрицы с поверхностью алмаза. Дан физико-химический анализ имеющихся в литературе экспериментальных данных по структуре переходной зоны “алмаз–металл”, ответственной за уровень алмазоудержания. Приведены результаты испытаний, свидетельствующие о существенном повышении работоспособности алмазных инструментов при использовании металлизированных алмазов (по ряду эксплуатационных показателей на 40–50% и выше).
Сверхтвердые материалы – активно растущий сегмент мирового рынка режущих и буровых инструментов. Алмаз обладает уникальными физико-химическими характеристиками и среди сверхтвердых материалов имеет самую высокую твердость и износостойкость, наиболее высокую теплопроводность и самый низкий коэффициент трения. В процессе работы режущего инструмента высокая теплопроводность алмаза обеспечивает отвод тепла из рабочей зоны резания и, как результат, изготовление изделия с бесприжоговой поверхностью.
Алмазные инструменты широко используются в различных отраслях техники и промышленности для резки, шлифовки, сверления и полировки твердых материалов, таких как камень, бетон, цементированные карбиды, оптическое стекло, керамика и другие труднообрабатываемые материалы и сплавы. Например, в нефтегазодобывающей отрасли для бурения скальных пород применяются вращательные долота, оснащенные PDC (Polycrystalline Diamond Cutter) фрезами [1].
Для повышения рабочих характеристик режущего и бурового инструмента разрабатываются различные методы и подходы, в том числе использование алмазных зерен разной дисперсности, что дает возможность обеспечить более плотную упаковку сверхтвердых частиц. Например [2], для повышения износостойкости и коррозионной стойкости буровых долот, предназначенных для прохода глубоких нефтегазовых скважин, предложено на все рабочие поверхности бурового долота наносить защитное покрытие, содержащее как алмазные микрочастицы (размером 1–28 мкм), так и алмазные наночастицы (размером ~4–6 нм), равномерно распределенные между более крупными микрочастицами, в соотношении: микрочастицы – 5.0–25.0 об. %, наночастицы – 2.0–5.0 об. %, остальное – металл. Оптимальная толщина защитного покрытия 10–500 мкм.
В сверхтвердых инструментах алмаз – основной рабочий компонент; функция матрицы – удерживать зерна алмаза в процессе эксплуатации, при этом скорость изнашивания матрицы и зерен алмаза должна быть соизмеримы.
Алмазные композиты спекаются при высоких давлениях и температурах, что обуславливает их высокую стоимость, и в промышленно развитых странах идут активные исследования по совершенствованию как существующих, так и разработке новых, более экономичных технологий производства алмазного инструмента.
Срок службы и рабочие характеристики алмазного инструмента в решающей степени определяются алмазоудерживающей способностью матрицы. В настоящее время исследования по повышению служебных свойств режущего алмазного инструмента идут по следующим основным направлениям [3]. Предварительная обработка поверхности алмаза: металлизация или придание дополнительной шероховатости поверхности алмазных частиц. Модификация металлической матрицы путем введения в ее состав карбидообразующих металлов, редкоземельных элементов или неметаллических элементов (Si, P и B). Усовершенствование технологии компактирования композиционного алмазосодержащего материала (спекание, горячее прессование и т.д.).
При модификации состава матрицы путем введения в ее состав карбидообразующих металлов требуется повышение температуры или времени термообработки компактирования композиционного материала, для обеспечения диффузионного массопереноса карбидообразующих металлов из объема матрицы к поверхности алмаза и реакционное образование связующего карбидного слоя. Модификация поверхности частиц порошка путем формирования на их поверхности функциональных слоев, в том числе получение наноструктур ядро–оболочка (core–shell particles) – технологический прием, позволяющий придать композиции полифункциональность свойств и существенно повысить служебные характеристики нового композиционного материала [4].
Наиболее технологичным путем повышения рабочих характеристик сверхтвердых материалов является металлизация алмазных зерен, т.е. формирование на поверхности алмаза покрытий, обеспечивающих прочную связь алмаза с матрицей сверхтвердого материала. Для получения металлизированных алмазов совершенствуются технологии физического и химического осаждения из газовой фазы (PVD, CVD), гальванические методы, магнетронное распыление, осаждение в расплавах солей и т.д. Идет активная разработка новых методов и подходов по получению функциональных покрытий на алмазе.
В России разработка методов металлизации алмаза проводится в различных научных центрах и организациях, в том числе: Институт физико-технических проблем Севера им. В.П. Ларионова СО РАН, Якутск; Северо-Восточный федеральный университет им. М.К. Аммосова, Якутск; Волгоградский государственный технический университет; Санкт-Петербургский государственный технологический институт (технический университет); Институт химии твердого тела и механохимии СО РАН, Новосибирск; Новосибирский государственный университет; Московский государственный институт стали и сплавов (технологический университет); Кабардино-Балкарский государственный университет им. Х.М. Бербекова, Нальчик; Ивановский государственный химико-технологический университет; ФГУП “НИИграфит”, Москва и др.
За рубежом последние несколько лет наиболее активные исследования по повышению эксплуатационных характеристик алмазных инструментов проводятся в Китайской Народной Республике, при этом главным направлением является металлизация алмазов.
В данном обзоре основное внимание уделено разработкам последних лет, проводимым в России и за рубежом, по повышению рабочих характеристик сверхтвердого материала путем предварительной металлизации алмаза, как наиболее технологичного способа повышения алмазоудержания – основного параметра, определяющего длительную работоспособность режущего и бурового инструмента.
МЕТАЛЛИЗАЦИЯ АЛМАЗОВ КАРБИДООБРАЗУЮЩИМИ МЕТАЛЛАМИ
В последние годы основное внимание разработчиков уделяется методам и способам получения покрытий на основе карбидообразующих металлов, обеспечивающих прочную химическую связь матрицы с поверхностью алмаза и, следовательно, значительно повышающих рабочие характеристики сверхтвердого материала.
В работах [5–8] разработан комбинированный технологический подход по получению алмазосодержащих композиционных материалов, совмещающий в одном цикле работы вакуумной печи термодиффузионную металлизацию алмаза хромом, спекание матрицы на основе твердосплавной порошковой композиции с одновременной пропиткой медью.
Показана возможность получения композиционных материалов системы алмаз– Cr (покрытие)–WC–Co–Cu (матрица) в рамках одностадийного технологического цикла нагревания–охлаждения печи [5]. Использованы натуральные алмазы дисперсностью 315/250, 250/200. Каждое зерно алмаза было “завернуто” в оболочку из тонкодисперсного порошка Cr толщиной не менее 1 мм. Предварительную термообработку проводили при 600°С в течение 30–45 мин, формирование композита – при 1100°С, 5 мин. Методами физико-химического анализа в переходном слое алмаз–матрица толщиной 6–9 мкм зафиксированы карбиды Cr3C2, Cr7C3, Cr23C6. Сравнительные испытания экспериментальных образцов показали эффективность металлизации алмазных зерен как способа повышения алмазоудержания и, следовательно, эксплуатационных свойств алмазного инструмента. Удельная производительность образцов с металлизированными алмазами на 39% выше производительности материалов, полученных на алмазах без металлизации.
В работе [8] исследовано влияние металлизации алмаза на удельную производительность правящих карандашей с WC–Co–Cu матрицей на основе твердосплавной порошковой смеси марки ВК6 с пропиткой медью. Вдоль оси правящего карандаша распределялось пять алмазов со средней массой 0.21 кар. каждый (рис. 1). Перед укладкой в твердосплавную шихту, алмазы заворачивали в тонкую медную фольгу, в которую, в количестве равном массе алмаза, засыпали порошок хрома и равномерно распределяли вокруг зерен алмаза.
Рис. 1.
Установка для спекания правящего карандаша по гибридной схеме с самодозируемой пропиткой медью (а) и алмазное зерно, завернутое в медную фольгу с порошком хрома (б) [8].
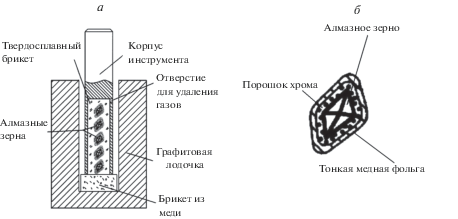
Для испытаний были изготовлены также контрольные образцы на основе неметаллизированных алмазов, в которых алмазоудержание определяется механическим сцеплением затвердевшего медного инфильтрата с микропорами и шероховатостями поверхности алмазных зерен, образующихся в результате каталитической графитизации алмаза и его частичного растворения в матрице.
Установлено, что в опытных образцах в переходной зоне “алмаз–матрица” в результате термодиффузионной металлизации хромом образуется карбидный слой толщиной ~5 мкм, плотно сцепленный с алмазным зерном, состава близкого Cr3C2 (рис. 2).
Рис. 2.
Структура матрицы вблизи переходной зоны алмаз–матрица контрольного (а) и опытного (б) образцов правящего карандаша [8].
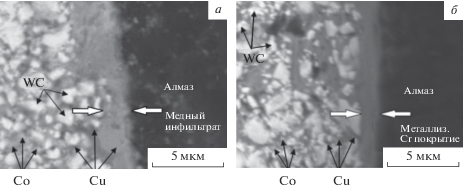
Проведены сравнительные испытания контрольного и опытного правящих карандашей на удельную производительность при правке шлифовального круга из зеленого карбида кремния. Испытания показали высокую эффективность металлизации алмазов для композиционных материалов инструментального назначения. Удельная производительность алмазного карандаша, изготовленного по основе металлизированных алмазов повысилась на 44.7% по сравнению с аналогичным показателем контрольного алмазного карандаша, полученного по традиционной схеме спекания без металлизации алмазных зерен.
Обнаружено принципиальное отличие в характере выкрашивания алмазов из матрицы в процессе испытаний опытного и контрольного правящих карандашей. В контрольных образцах в результате низкого алмазоудержания матриц, обусловленного только механическим сцеплением, идет выпадение целых зерен алмаза. В опытных карандашах зерна алмазов, прочно удерживаемые в матрице благодаря металлизации поверхности, выкрашиваются постепенно по механизму хрупкого транскристаллитного скола (небольшими отколами).
В работе [9] металлизация алмазных частиц проведена термодиффузионным методом, основанным на сублимации металла в вакууме с последующим осаждением на поверхности алмазных частиц. Для металлизации использованы синтетические (АС2–АС6) и природные (А10, А25) алмазы. На зерна алмазов нанесено покрытие на основе карбидообразующего металла – хрома, имеющего относительно низкую температуру сублимации 992°С. Порошки алмаза и хрома смешивали в разных соотношениях и нагревали в вакууме до температур, превышающих порог сублимации металла.
Установлено, что при температуре металлизации 1100°С на гетерогенной границе раздела алмаз-покрытие образуется промежуточный пористый слой, снижающий механические свойства структуры. Авторы дают две версии образования пористого слоя: разная скорость диффузионного массопереноса атомов углерода и хрома через растущий слой продуктов реакции (карбидов) и поверхностная графитизация алмаза в присутствии хрома, каталитически снижающего температуру перехода алмаза в графит.
Определена оптимальная температура 1000°С, при которой на частицах алмаза получено плотное покрытие с металлическим блеском, прочно сцепленное с подложкой. На рентгенограммах зафиксированы дифракционные максимумы Cr и карбидов Cr7C3, Cr3C2. Установлено, что скорость роста металлического покрытия зависит от температуры и времени термообработки, соотношения компонентов в исходной реакционной смеси (алмаз : хром), а также дисперсности реагентов. Скорость роста слоя покрытия замедляется во времени и после ~4 ч термообработки составляет ~300 нм (рис. 3).
Рис. 3.
Зависимость толщины покрытия на алмазе АС6 100/80 от времени металлизации хромом при температуре 1000°С [9].
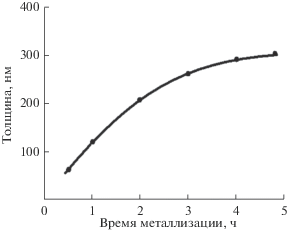
Испытания синтетических алмазов АС2–АС6 на раздавливание показали, что металлизация хромом повышает прочность зерен в 1.5–2 раза благодаря “залечиванию” микротрещин и дефектов поверхности частиц алмазов.
Преимуществом технологии [9] является относительная технологическая простота и возможность многократного использования порошка хрома для металлизации нескольких партий алмазных порошков. Разработка [9] внедрена на заводе точных технических камней (Челябинская обл.) и АО “Волгоградский завод тракторных деталей и нормалей”. При одинаковых условиях испытаний металлизированные природные алмазы “Сплиттер” надежно крепились в державке и работали до полного износа, в то время как алмазы без металлического покрытия использовались не более, чем на 60%, выпадали из державки и разрушались. Стойкость правящих карандашей на основе металлизированных синтетических алмазов АС15 25/200 превышала в 1.5–2 раза стойкость правящих карандашей 3908-0064 ГОСТ 607 производства АО “Терек”.
В работах [10–12] показана возможность использовать метод йодного транспорта для металлизации алмаза в реакторах без градиента температуры. В большинстве газотранспортных систем летучее соединение образуется в одной зоне реактора и его перенос в другую зону реактора осуществляется целенаправленно путем создания градиента температуры или давления.
В разработанном методе йодного транспорта [10–12] направленный градиент температуры или давления в реакторе специально не создавался. Для металлизации использованы карбидообразующие металлы (W, Ti, Cr), сильное химическое взаимодействие на гетерогенной границе алмаз–металл обеспечивало градиент химического потенциала, необходимый для массопереноса йодидов к реакционной поверхности алмаза. Образование летучих йодидов металлов идет при температурах порядка 300–700°С.
Смесь порошков алмаза, металла (W, Ti, Cr) и йода загружали в вакуумируемый кварцевый реактор. Использованы порошки алмаза в широком диапазоне дисперсности от 1/0 до 500/400 мкм. По результатам эксперимента на алмазах получены металлокерамические покрытия. В табл. 1 даны оптимальные температуры получения покрытий и их фазовый состав. Установлено, что с повышением температуры и времени эксперимента в покрытиях снижается содержание металлической фазы и повышается содержание карбидной.
Методом йодного транспорта титана получены пленки на зернах детонационного наноалмаза расчетной толщины 0.5–3 нм. Компактирование металлизированных порошков наноалмаза удалось провести при давлении 4–5 ГПа и температуре 1300–1700°С. Получены сверхтвердые материалы с открытой пористостью менее 1%, общей пористостью 3–10%. Прочность образцов на сжатие достигала 6–12 ГПа; микротвердость 50–90 ГПа, что соизмеримо с микротвердостью поликристаллических алмазных материалов, полученных при давлениях 7–14 ГПа. На основе нанопорошков алмаза без металлизации получить компактные материалы не удалось при давлениях ниже 7 ГПа.
В работе [13] разработан метод получения WC-покрытия на алмазе в расплавах солей Na2CO3–NaCl при температурах 630–680°С по химической реакции:
(3)
${\text{W}} + {\text{N}}{{{\text{a}}}_{{\text{2}}}}{\text{C}}{{{\text{O}}}_{{\text{3}}}} \to 0.6{\text{WC}} + 0.4{\text{N}}{{{\text{a}}}_{{\text{2}}}}{\text{W}}{{{\text{O}}}_{{\text{4}}}} + 0.4{\text{N}}{{{\text{a}}}_{{\text{2}}}}{\text{C}}{{{\text{O}}}_{3}} + 0.2{\text{N}}{{{\text{a}}}_{{\text{2}}}}{\text{O}}.$Использованы синтетические алмазные порошки дисперсностью 10–20 мкм. Поверхность частиц вольфрама предварительно окисляли на воздухе при температуре 400°С в течение 1 ч. Соотношение солей в расплаве Na2CO3 : NaCl отвечало эвтектической точке (631.7°С), что дало возможность провести обработку алмазов и получить WC-покрытие при температурах ниже температур плавления Na2CO3 (856°С) и NaCl (800.7°С).
Разработан способ получения сверхтвердого алмазного материала для режущих и буровых инструментов путем нанесения W–WC–F-покрытий на алмазные зерна [14]. Первый адгезионный слой, формируемый непосредственно на алмазе, содержит порошки вольфрама и карбида вольфрама, сплавленные с фтором. При оптимальном содержании фтор повышает реакционную способность вольфрама по отношению к углероду, а также механические свойства вольфрама. Установлено, что повышение адгезионных, механических и защитных свойств покрытия достигается в узкой области содержания фтора 0.001–0.12 мас. %. При содержании менее 0.001 мас. % фтора недостаточно для повышения реакционной способности вольфрама и улучшения механических и защитных свойств покрытия. При содержании выше 0.12 мас. % F возрастает риск ухудшения адгезии покрытия, в особенности, если инструмент работает при повышенных температурах и в агрессивных средах. Разработанное покрытие является термостойким при температурах до 800°С и выше, обеспечивает защиту алмазов от окисления, а также от агрессивных металлов, при этом покрытие улучшает удерживание алмазов в режущих и буровых инструментах.
Показана возможность использования микроволнового нагревания для получения титановых покрытий на алмазе [15]. Использованы синтетические алмазы со средним размером ~120 мкм.
Формирование покрытия проведено по следующим химическим реакциям:
(1)
${\text{Ti}}{{{\text{H}}}_{2}}\left( {{\text{тв}}} \right) \to {\text{Ti}}\left( {{\text{тв}}} \right) + {{{\text{H}}}_{{\text{2}}}}\left( {\text{г}} \right){\text{,}}$(2)
${\text{Ti}}\left( {{\text{тв}}} \right) + {\text{C}}\left( {{\text{тв}}} \right) = {\text{TiC}}\left( {{\text{тв}}} \right){\text{.}}$Термообработку композиций проводили в микроволновой печи в атмосфере аргона в температурном интервале 660–860°С в течение 1 ч, скорость нагревания составляла ~80°С/мин. После обжига методом рентгенофазового анализа показано наличие в композиции фаз алмаза, Ti и TiC, при этом с повышением температуры обжига интенсивность дифракционных максимумов карбида TiC возрастала. Определена оптимальная температура формирования плотного покрытия, наиболее прочно сцепленного с алмазом – 760°С. Толщина слоя покрытия ~257 нм.
Кинетика роста слоя TiC по реакции (2) контролируется скоростью диффузионного массопереноса атомов Ti и C через растущий слой карбида TiC, при этом коэффициент диффузии Ti в TiC (2.6 × 10–18 м2/с) значительно выше коэффициента диффузии C в TiC (9.9 × 10–23 м2/с) [15]. Установлено, что на поверхности частиц алмаза присутствует наружный слой чистого Ti, т.к. скорость осаждения Ti по реакции (1) выше скорости его диффузионного массопереноса в слое карбида TiC по реакции (2).
Преимуществом микроволновой технологии является высокая скорость нагревания и относительно небольшое время термообработки композиции (~1 ч), что дает возможность снизить уровень графитизации алмаза [15].
Показана возможность использования метода искрового плазменного напыления для получения Ti-покрытий на алмазе [16]. Электроразрядной обработке подвергали порошковые смеси, содержащие алмазные зерна размером 90–106 мкм и порошок титана. При использовании исходной порошковой композиции в диапазоне составов 2.5–20 мас. % Ti получены двухфазные покрытия (TiC, Ti), химически связанные с поверхностью алмазных зерен. Металлизация повысила предел прочности зерен алмаза при сжатии на 15.7% (по сравнению с исходными порошками алмаза).
В работе [17] на искусственных поликристаллических алмазах марки АСБ-4 методом ионно-плазменного напыления (вакуум 10–2 Па, 600°С) получены наноразмерные двухслойные пленки “титан/нихром”. Рентгенофазовый анализ пленок после напыления показал наличие фаз: Ni4Ti3, Cr7Ni3, Cr2Ti, NiTi, Cr, C. Дополнительная термообработка алмаза с пленкой при температуре 1200°С в течение 4 мин не привела к существенному изменению фазового состава. Наиболее интенсивное взаимодействие идет между металлическими нанослоями покрытия “Ti/(Ni,Cr)” с образованием интерметаллидов. В работе [17] карбидов титана и хрома не зафиксировано, что может быть объяснено наноразмерной толщиной внутреннего карбидного слоя, формирующегося непосредственно на алмазе, и достаточно низкой чувствительностью метода рентгенофазового анализа.
В работах [18, 19] исследовано влияние наноразмерного двухслойного покрытия “титан/никель” на удельную производительность правящих карандашей на основе поликристаллических синтетических алмазов марки АРС-4. Показано, что при правке шлифовальных кругов двухслойное покрытие “Ti/Ni” повышает удельную производительность карандашей на 40–55%. Алмазы без покрытия теряют работоспособность после износа 70–75% от своего первоначального объема и выпадают из матрицы. При таких же условиях испытаний алмазы с двухслойным покрытием “Ti/Ni” теряют свою работоспособность только после износа более 90%.
В последние годы идет активная разработка алмаз-медных и алмаз-алюминиевых композиционных материалов с высокими показателями теплопроводности для применения в электронных приборах [20–26]. Предварительную металлизацию алмазных частиц все более часто используют как метод повышения сцепления алмазных зерен с матрицей, при этом для покрытий, в основном, используют карбидообразующие металлы Cr, Mo, Ti, W.
В работе [24] WC-покрытие на алмазных частицах получено в расплавах солей NaCl : KCl = 1 : 1 с использованием порошков синтетического алмаза MBD8 размером частиц ~ 70 мкм и порошков оксида WO3 размером ~45 мкм. Обработка алмазных зерен в солевой ванне проведена при температурах 900–1050°С в течение 1 ч. Наиболее равномерное покрытие получено при температуре 1050°С толщиной слоя ~1 мкм. Рентгенофазовый анализ показал наличие в покрытии фаз WC, а также WO3, W, W2C. При одинаковых условиях компактирования использование металлизированных частиц алмаза дало возможность повысить плотность алмаз-медных композитов с 97.5% до 99.5%.
В работах [25, 26] металлизация проведена диффузионным методом в порошковых композициях и на алмазах получены Ti- и W-покрытия . Определен оптимальный режим получения W-покрытия – 900°С, 1 ч [25]. Использованы синтетические алмазы размером ~400 мкм, толщина слоя покрытия ~310 нм. После термообработки методом рентгенофазового анализа в композиции зафиксированы фазы WC, W2C, W. Использование металлизированных алмазов дало возможность повысить показатели теплопроводности алмаз-медных композиционных материалов, получаемых методом горячего прессования [25, 26].
Методом химического осаждения из газовой фазы (rotary chemical vapor deposition (RCVD)) на поверхности синтетических алмазов получены вольфрам- и никельсодержащие покрытия [27]. В качестве газообразных прекурсоров использованы карбонил вольфрама W(CO)6 и никелоцен Ni(C5H5)2. На основе металлизированных порошков получены теплопроводящие алмаз-медные материалы. Компактирование порошков, содержащих 50 об. % алмаза с размером частиц 50, 100, 200 мкм, проводили методами электроискрового спекания и горячего прессования. Установлено, что наибольшей относительной плотностью (97%) и теплопроводностью обладают композиты, полученные методом электроискрового спекания на основе алмазов размером ~50 мкм с покрытием из карбида вольфрама.
Компания Applied Diamond, Inc., США [28] предлагает различные виды металлизации алмазов для высокоэнергетического оборудования. Стандартная схема металлизации алмаза включает три слоя: карбидообразующий слой (Ti, W, Cr), имеющий прочную химическую связь с алмазом, толщина слоя ~100 нм; диффузионный барьер (Pd, Pt) для снижения взаимодействия химически активного внутреннего подслоя и наружного функционального слоя, толщина слоя ~100 нм; наружный металлический слой требуемого функционального состава, толщина слоя ~1 мкм.
В работах [29, 30] представлены результаты экспериментов, моделирующих условия формирования промежуточных слоев при высокотемпературном взаимодействии природного алмаза с карбидообразующими металлами – Fe, Cr, Co, Ti. Для получения контактных пар использованы природные алмазы – бриллианты с семнадцатью гранями, ограненные и отполированные в заводских условиях, масса ограненных алмазов ~0.01 карат. Кристаллы алмаза прозрачные и имеют слегка желтоватый оттенок. Температурно-временные режимы спекания контактных пар алмаз–металл соответствовали режиму работы вакуумной печи при получении твердосплавных матриц алмазосодержащих инструментов с пропиткой медью.
Проведены испытания на сдвиговую прочность полученных соединений алмаз–металл. Наивысшая прочность соединения при одинаковых условиях эксперимента достигается в случае контактной пары алмаз–железо (табл. 2). По результатам испытаний авторы делают вывод, что небольшие добавки частиц железа вокруг алмазных зерен могут значительно повысить уровень алмазоудержания металлокерамических матриц.
НИКЕЛИРОВАНИЕ АЛМАЗА
В последние годы только единичные работы посвящены металлизации алмаза некарбидообразующими металлами (в основном, никелем), когда адгезия покрытия с алмазом определяется механическим сцеплением.
Диаграмма состояния системы Ni–C – диаграмма простого эвтектического типа, в которой соединения отсутствуют. Метастабильный карбид Ni3C может быть получен только при высоких скоростях охлаждения расплава Ni–C или при повышенных давлениях. При металлизации на гетерогенной границе алмаз–Ni отсутствует сильное химическое взаимодействие и качественное сцепление покрытия с алмазом может быть достигнуто только механически на шероховатостях рельефа алмаза.
В работе [31] никелирование алмазов проведено методом химического восстановления ионов металла из раствора. Использованы синтетические алмазы разной дисперсности марок АС5 63/50, АС5С 100/80, АС5 160/125. Перед никелированием проводили предварительную обработку порошков алмазов в различных растворах травления, не содержащих соли олова и палладия, с целью повышения шероховатости рельефа и обеспечения лучшего сцепления никелевого слоя с поверхностью кристалла. Металлизация алмазов проведена при температуре 35–40°С в щелочном растворе, концентрированном по солям никеля и содержащем в качестве восстановителя гипофосфит натрия Na(PH2O2). После обработки в течение 1 ч металлизированные порошки содержали 35–45 мас. % Ni. По результатам исследования предложено вводить в раствор никелирования добавку, принадлежащую к группе нафталинсульфонатов, для ускорения процесса восстановления металла и получения никелевого покрытия с низкими внутренними напряжениями.
В работе [32] представлены результаты исследований по повышению эксплуатационных характеристик бурового инструмента, оснащенного синтетическими алмазами разной степени металлизации. Показатели работоспособности буровых коронок существенно повышаются при использовании металлизированных алмазов.
Оказывает положительное влияние никелирования алмазов на механическую скорость бурения и износостойкость буровых коронок конструкции ИСМ НАН Украины. Для испытаний использованы никелированные алмазы АС125 250/200 с разной степенью металлизации 25 и 50%. Толщина никелевого слоя составляла 3–5 мкм. Испытания коронок проведены в производственных условиях при бурении скважин в интервале глубин 50–1000 м.
По результатам испытаний установлено, что скорость износа коронок с металлизированными алмазами на 20–60% ниже скорости износа коронок на основе неметаллизированных алмазов (рис. 4). При использовании никелированных алмазов со степенью металлизации 50% средняя проходка на одну коронку возрастает в 1.56 раза, при этом удельный расход алмазов снижается на 37% (табл. 3).
Рис. 4.
Зависимость скорости износа коронок, оснащенных неметаллизированными (а) и металлизированными (б) алмазами, от величины осевого усилия при различной частоте вращения, мин–1: 600 (1), 750 (2), 950 (3), 1180 (4), 1500 (5) [32].
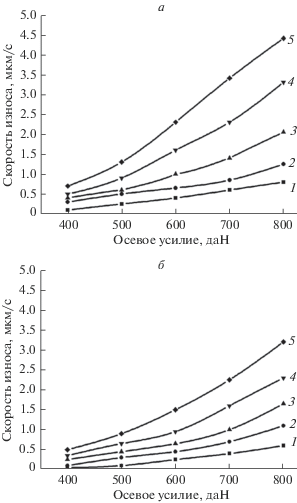
Таблица 3.
Влияние никелирования алмазов на показатели работоспособности буровых коронок [32]
Степень металлизации, % |
Механическая скорость бурения, м/ч |
Средняя проходка на коронку, м |
Удельный расход алмазов, кар/м |
---|---|---|---|
0 | 1.5 | 12.2 | 1.066 |
25 | 1.6 | 14.6 | 0.890 |
50 | 1.8 | 19.2 | 0.677 |
ЗАКЛЮЧЕНИЕ
Работоспособность алмазного инструмента в решающей степени определяется алмазоудерживающей способностью матрицы сверхтвердого материала. С целью повышения работоспособности алмазных инструментов последние годы продолжается активная разработка новых физико-химических методов и подходов по металлизации алмаза, в которых используется широкий круг прекурсоров, температурный интервал формирования покрытий охватывает температуры от комнатных до 1000–1100°С (табл. 4). Каждый из разрабатываемых технологических подходов имеет свои преимущества и недостатки.
Таблица 4.
Ряд новых методов и подходов по металлизации алмаза
Метод нанесения | Прекурсоры | Температура, °С | Ссылка |
---|---|---|---|
Термодиффузионная металлизация | Cr | 1000 | [9] |
Термодиффузионная металлизация | Cr | 1100 | [5–8] |
Термодиффузионная металлизация | Ti, W | 900 | [25] |
Химическое осаждение из газовой фазы (RCVD) | W(CO)6 + Ni(C5H5)2 | [27] | |
Йодный транспорт | Ti, I | 600–1000 | [10–12] |
Микроволновой нагрев | TiH2 | 760 | [15] |
Искровое плазменное напыление | Ti | [16] | |
В расплавах солей Na2CO3–NaCl | W, Na2CO3 | 630–680 | [13] |
В расплавах солей NaCl–KCl | WO3 | 900–1050 | [24] |
Химическое восстановление ионов металла из раствора | Соли Ni + Na(PH2O2) | 35–40 | [31] |
Работы последних лет показывают, что наиболее технологичным направлением повышения алмазоудержания является металлизация с использованием карбидообразующих металлов, обеспечивающих прочную химическую связь с поверхностью алмаза (Cr, Ti, W, Mo и др.).
При никелировании (некарбидообразующий металл) необходима предварительная обработка зерен алмаза, например, в растворах травления или плазме для повышения шероховатости поверхности с целью улучшения механического сцепления металлического покрытия с поверхностью алмаза.
Покрытия на основе карбидов тугоплавких металлов характеризуются высокой твердостью, износостойкостью, коррозионной стойкостью и обеспечивают защиту материалов при работе в различных агрессивных средах с абразивным износом [33, 34].
Покрытия на основе карбидов тугоплавких металлов являются также антиокислительным барьерным слоем, предотвращающим доступ кислорода к поверхности алмаза и его окисление при повышенных температурах. Алмаз начинает активно окисляется на воздухе при температурах ~700°С. В работе [35], например, исследованы защитные антиокислительные свойства покрытий системы Ti–B–C с разным содержанием бора и углерода. Термогравиметрическим анализом показано, что TiC-покрытия, содержащие 11 ат. % B, обладают низкими защитными свойствами – при нагревании до 1000°С начинается активная потеря массы образцов, обусловленная окислением алмаза и улетучиванием CO2↑. В противоположность этому, TiB2-покрытия, содержащие 60 ат. % B, обеспечивают защиту алмаза от окисления на воздухе при температуре 1000°С в течение 1 ч и более благодаря образованию расплава B2O3, как барьерного слоя, герметизирующего поверхность зерен алмаза.
При работе инструментов, полученных на основе металлизированных алмазов, выкрашивание алмазов из матрицы сверхтвердого материала идет не целыми зернами, а постепенно, по механизму хрупкого транскристаллитного скола (небольшими отколами).
Литературные данные последних лет по результатам опытных и промышленных испытаний новых сверхтвердых материалов показывают, что металлизация алмазов, как карбидообразующими, так и некарбидообразующими металлами, позволяет повысить работоспособность режущих и буровых инструментов на 40–50% и более.
Работа выполнена при финансовой поддержке Российского научного фонда (проект № 20-13-00054).
Список литературы
Сергейчев К.Ф. Алмазные CVD-покрытия режущих инструментов (обзор) // Успехи прикладной физики. 2015. Т. 3. № 4. С. 342–376.
Полушин Н.И., Маслов А.Л., Лаптев А.И., Кушхабиев А.С., Котельникова О.С., Варшавский Ю.С. Буровое долото, армированное алмазными режущими элементами // Патент РФ № 2 625 832. Опубликовано: 19.07.2017 Бюл. № 20. Патентообладатель: МИСиС.
Xiaojun Zhao, Longchen Duan. A Review of the Diamond Retention Capacity of Metal Bond Matrices // Metals. 2018. V. 8(5). P. 307–327.
Оленин А.Ю., Лисичкин Г.В. Получение и применение химически модифицированных наночастиц благородных металлов (обзор) // Журн. прикладной химии. 2018. Т. 91. № 9. С. 1219–1240.
Sharin P.P., Yakovleva S.P., Makharova S.N., Vasileva M.I., Popov V.I. Structural and phase characteristics of the diamond/matrix interfacial zone in high-resistant diamond composites // Composite Interfaces. 2018. V. 25. № 5. P. 1–13.
Шарин П.П., Акимова М.П., Яковлева С.П., Попов В.И. Структура переходной зоны алмаз–матрица и стойкость инструмента, полученного при металлизации алмаза хромом в процессе спекания WC–Сo-брикета c пропиткой медью // Известия высших учебных заведений. Порошковая металлургия и функциональные покрытия. 2018. № 3. С. 64–75.
Шарин П.П., Акимова М.П., Попов В.И. Взаимосвязь структуры межфазной зоны алмаз – матрица с работоспособностью инструмента, полученного технологией, совмещающей металлизацию алмазов со спеканием матрицы // Вопросы материаловедения. 2018. № 2(94). С. 111–123.
Шарин П.П., Акимова М.П. Влияние структуры переходной зоны алмаз-твердосплавная матрица на удельную производительность инструмента, полученного при металлизации алмазов в процессе их спекания с пропиткой медью // Вестник Пермского национального исследовательского политехнического университета. Машиностроение, Материаловедение. 2018. Т. 20. № 4. С. 57–66.
Локтюшин В.А., Гуревич Л.М. Получение нанотолщинных металлических покрытий на сверхтвердых материалах методом термодиффузионной металлизации // Известия Волгоградского государственного технического университета. 2009. № 11(59). С. 50–54.
Гаршин А.П., Богданов С.П. Тугоплавкие порошки ядро-оболочка для аддитивных производств // Машиностроение: сетевой электронный научный журн. 2017. Т. 5. № 2. С. 44–48.
Богданов С.П. Получение покрытий на порошках методом йодного транспорта // Физика и химия стекла. 2011. Т. 37. № 2. С. 229–237.
Богданов С.П. Йодотранспортный метод получения покрытий на порошках // Известия Санкт-Петербургского государственного технологического института (технического университета). 2012. № 16(42). С. 24–28.
Okada T., Fukuoka K., Arata Y., Yonezawa S., Kiyokawa H., Takoshima M. Tangsten carbide coating on diamond particles in molten mixture of Na2CO3 and NaCl // Diamond and Related Materials. 2015. V. 52. P. 11–17.
Жук Ю., Лахоткин Ю. Суперабразивный материал с защитным адгезивным покрытием и способ изготовления такого покрытия // Патент РФ № 2666390. Опубликовано: 07.09.2018 Бюл. № 25. Патентообладатель: Хардайд ПиЭлСи (GB)
Gu Q., Peng J., Xu L., Srinivasakannan C., Zhang L., Xia Y., Wu Q., Xia H. Preparation of Ti-coated diamond particles by microwave heating // Applied Surface Science. 2016. V. 390. P. 909–916.
Chang R., Zang J., Wang Y., Yu Y., Lu J., Xu X. Study of Ti-coated diamond grits prepared by spark plasma coating // Diamond & Related Materials. 2017. V. 77. P. 72–78.
Беров З.Ж., Манукянц А.Р., Касумов Ю.Н., Созаев В.А. Фазообразование и структурные особенности двухслойных покрытий “титан/нихром” на искусственных поликристаллических алмазах // Физико-химические аспекты изучения кластеров, наноструктур и наноматериалов. 2018. № 10. С. 106–114.
Беров З.Ж., Хапачев Б.С., Нартыжев Р.М., Беров А.З. Анализ влияния металлизации алмазов на эффективность использования инструментов // Известия Кабардино-Балкарского государственного университета. 2015. Т. 5. № 1. С. 38–41.
Беров З.Ж., Балкаров Т.С. Повышение надежности закрепления алмазов и их износостойкости в инструменте // СТИН. 2018. № 12. С. 7–13.
Ma S., Zhao N., Shi C., Liu E., He C., He F., Ma L. Mo2C coating on diamond: different effects on thermal conductivity of diamond/Al and diamond/Cu composites // Applied Surface Science. 2017. V. 402. P. 372–383.
Che Z., Wang Q., Wang L., Li J., Zhang H., Zhang Y., Wang X., Wang J., Kim M. Interfacial structure evolution of Ti-coated diamond particle reinforced Al matrix composite produced by gas pressure infiltration // Composites Part B Engineering. 2017. V. 113. P. 285–290.
Ji G., Tan Z., Lu Y. Heterogeneous interfacial chemical nature and bonds in a W-coated diamond/Al composite // Materials Characterization. 2016. V. 112. P. 129–133.
Liu X.Y., Wang W.G., Wang D. Effect of nanometer TiC coated diamond on the structure and thermal conductivity of diamond/Al composites // Materials Chemistry and Physics. 2016. V. 182. P. 256–262.
Kang Q., He X., Ren S., Liu T., Liu Q., Wu M., Qu X. Microstructure and thermal properties of copper-diamond composites with tungsten carbide coating on diamond particles // Materials Characterization. 2015. V. 105. P. 18–23.
Zhang C., Wang R., Cai Z., Peng C., Feng Y., Zhang L. Effect of dual-layer coatings on microstructure and thermal conductivity of diamond/Cu composites prepared by vacuum hot pressing // Surface and Coatings Technology. 2015. V. 277. P. 299–307.
Zhang C., Wang R., Peng C., Tang Y., Cai Z. Influence of titanium coating on the microstructure and thermal behavior of Dia./Cu composites // Diamond & Related Materials. 2019. V. 97.
Ухина А.В., Дудина Д.В., Самошкин Д.А., Галашов Е.Н., Сковородин И.Н., Бохонов Б.Б. Влияние модифицирования поверхности синтетических алмазов никелем или вольфрамом на свойства композиций медь-алмаз // Неорганические материалы. 2018. Т. 54. № 5. С. 446–453.
Caйт “Applied Diamond, Inc.” / URL: usapplieddiamond.com
Шарин П.П., Акимова М.П. Структура и прочность межфазной зоны при термохимическом взаимодействии алмаза с переходными металлами // Известия Самарского НЦ РАН. 2018. Т. 20. № 1. С. 11–17.
Шарин П.П., Яковлева С.П., Гоголев В.Е., Попов В.И. Строение и прочность переходной зоны при твердофазном высокотемпературном взаимодействии алмаза с карбидообразующими металлами – хромом и кобальтом // Перспективные материалы. 2016. № 7. С. 47–60.
Строгая Г.М., Юдина Т.Ф., Ершова Т.В., Бейлина Н.Ю., Кривцов А.К. Химическое никелирование синтетических алмазов // Известия высших учебных заведений. Серия: Химия и химическая технология. 2014. Т 57. № 5. С. 80–84.
Исонкин А.М., Богданов Р.К. Влияние металлизации алмазов на показатели работоспособности буровых коронок // Науковi працi ДонНТУ. Серiя “Прничо-геологiчна”. 2011. Вып. 14(181). С. 158–163.
Стулов Ю.В., Долматов В.С., Дубровский А.Р., Кузнецов С.А. Покрытия карбидов тугоплавких металлов: получение в солевых расплавах, свойства, применение // Журн. прикладной химии. 2017. Т. 90. № 5. С. 537–544.
Кузнецов Ю.А., Марков М.А., Красиков А.В., Быстров Р.Ю., Беляков А.Н., Быкова А.Д., Макаров А.М., Фадин Ю.А. Формирование износостойких и коррозионностойких керамических покрытий комбинированными технологиями напыления и микродугового оксидирования // Журн. прикладной химии. 2019. Т. 92. № 7. С. 819–826.
Sun Y., Zhang C., Wu J., Wu J., Meng Q., Liu B., Gao K., He L. Enhancement of oxidation resistance via titanium boron carbide coatings on diamond particles // Diamond & Related Materials. 2019. V. 92. P. 74–80.
Дополнительные материалы отсутствуют.
Инструменты
Физика и химия стекла