Физика и химия стекла, 2021, T. 47, № 2, стр. 201-208
Условия получения нанопористой керамики на основе муллита
Л. В. Морозова *
Институт химии силикатов им. И.В.Гребенщикова РАН
199034 Санкт-Петербург, наб. Макарова, 2, Россия
* E-mail: morozova_l_v@mail.ru
Поступила в редакцию 26.12.2019
После доработки 27.07.2020
Принята к публикации 06.08.2020
Аннотация
Разработана технология получения нанопористой керамики на основе муллита (3Al2O3 ∙ 2SiO2). Механохимическое активирование оксидов, участвующих при синтезе муллита (γ-Al2O3 и аморфный SiO2), позволяет получить однофазный 3Al2O3 ∙ 2SiO2 и снизить его температуру спекания до 1300°С. Установлено влияние давления прессования и количества порообразующей добавки (карбоната аммония) на величину открытой пористости, объем пор и распределение пор по размерам в спеченной керамике 3Al2O3 ∙ 2SiO2. Получена муллитовая нанокерамика с открытой пористостью 42–47%, размером пор <200 нм и прочностью при сжатии 50–65 МПа.
ВВЕДЕНИЕ
Интерес к оксидной керамике, используемой в качестве фильтрационных мембран, применяемых при тонкой очистке жидких и газовых сред в различных отраслях промышленности, продиктован тем, что данная керамика обладает особым комплексом свойств : высокой химической и коррозионной стойкостью, термической стабильностью при температурах эксплуатации ≥500°С, стабильностью геометрических размеров, длительным ресурсом работы и возможностью многократной регенерации.
Несмотря на хрупкость и относительно высокую стоимость керамических фильтров, они быстро окупаются за счет высоких эксплуатационных показателей и длительного срока службы (до 10 лет и выше вместо 1 г. для полимерных мембран) [1]. В современном материаловедении является актуальной проблема разработки и внедрения технологий производства фильтрационных мембран с открытой пористостью >40%, а также с заданным распределением пор по размерам и со средними размерами пор ~30–300 нм. Керамический мембранный фильтр состоит из пористой подложки, которая обеспечивает механическую прочность, и мембранного слоя, определяющего тонкость фильтрации. Композиции на основе оксида алюминия (α-Al2O3, MgAl2O4) наиболее часто применяют в качестве пористой основы [2–5], на которую шликерным литьeм или золь-гель методом наносят селективные слои, позволяющие существенно снизить размер пор (до 100–200 нм) и сделать их распределение мономодальным [1, 6, 7]. Соединение оксида алюминия c диоксидом кремния – муллит также целесообразно использовать при создании фильтрационных мембран [8].
При синтезе муллита из природных образцов (каолин, шамот, кварцевый песок, кремнезем) при температуре ≥1500°С даже в относительно чистых материалах практический выход муллита составляет не более 50–60% от теоретического [9]. Основная трудность получения муллита данным способом заключается в необходимости использования высоких температур, для повышения диффузионной подвижности катионов алюминия и кремния через слой 3Al2O3 ∙ 2SiO2, образующегося на границе между частицами исходных оксидов [10]. Это препятствует формированию требуемой поровой структуры в муллитовой керамике. Важно проведение исследований в направлении разработки технологических приемов для получения 3Al2O3 ∙ 2SiO2 из синтетических компонентов с заданными параметрами открытой пористости и распределением пор по размерам. На данный момент в научной литературе практически отсутствуют сведения об условиях формирования пористой структуры в муллите с размером пор <300 нм. Авторы патента [11] описывают получение керамики 3Al2O3 ∙ 2SiO2 с открытой пористостью ~50% и размером частиц 10–100 мкм в температурном интервале 1400–1700°С, однако, в таком крупнодисперсном керамическом материале крайне сложно достичь равномерного распределения пор по размерам, не говоря уже о создании поровой структуры необходимой для фильтрационных мембран. Для снижения температуры образования муллита и получения на его основе тонкопористой керамики желательно использовать дисперсные компоненты [12], что позволит сформировать в конечном изделии нанопористую структуру.
Применение механохимического активирования (МА) при синтезе 3Al2O3 ∙ 2SiO2 дает возможность увеличить не только дисперсность порошков, но и создает дополнительные структурные дефекты, позволяющие интенсифицировать процесс образования и спекания муллитовой керамики при температурах ≤1300°С [13]. В исследованиях [14–17], посвященных механохимическому активированию синтеза муллита, также отмечается положительное влияние МА на процесс формирования 3Al2O3 ∙ 2SiO2 и указывается на возможность снижения температуры спекания муллитовой керамики на 200–300°С по сравнению с методом твердофазного синтеза.
Цель работы – синтез однофазного муллита, используя механохимическое активирование γ-Al2O3 и аморфного SiO2, получение на его основе керамики с контролируемой открытой пористостью (~40–45%) и размером пор менее 200 нм.
ЭКСПЕРИМЕНТАЛЬНАЯ ЧАСТЬ
Методы исследования
Рентгенофазовый анализ (РФА, дифрактометр D8-Advance фирмы Bruker) применяли для идентификации структуры и фазового состава порошков. Съемку проводили в интервале углов 2θ: 15°–65° при комнатной температуре. Средний размер кристаллов порошков и зерен в спеченной керамике рассчитывали по формуле Селякова–Шерера: d = 0.9 λ/(β cos θ) [18]. Методом низкотемпературной адсорбции азота (БЭТ) оценивали площадь удельной поверхности порошков (анализатор сорбции газов Quantachrom NOVA 1200e). Дифференциальный термический анализ (ДТА, дериватограф Q-1000 фирмы МОМ) применяли для изучения процессов термического разложения в интервале температур 20–1000°С. Термическую обработку порошков и спрессованных компактов проводили в интервале температур 500–1300°С (электрическая печь фирмы Naberterm с программным управлением). Методом гидростатического взвешивания определяли открытую пористость керамических образцов [19]. Методом ртутной порометрии установили общий объем пор и распределение пор по размерам в спеченной керамике (порометр фирмы Carlo Erba Strumentazione модель 2000). Применяли метод определения предела прочности при сжатии [20] и методы определения кислотостойкости и щелочестойкости термостойкой керамики [21].
Синтез порошков-прекурсоров для получения муллита
С учетом результатов работы [22], в которой отмечено, что при синтезе муллита из алюмосиликатов существенное значение имеет дисперсность оксида алюминия, а также принимая во внимание исследования по выбору оптимальных компонентов для получения 3Al2O3 ∙ 2SiO2 [14–17], для синтеза однофазного муллита использованы нанодисперсный γ-Al2O3 и аморфный SiO2, полученные из реагентов, приведенных в табл. 1.
γ-Al2O3
Таблица 1.
Исходные реагенты для синтеза керамики 3Al2O3 ∙ 2SiO2
Наименование реагента | Химическая формула | Марка реактива | ГОСТ |
---|---|---|---|
Азотнокислый алюминий | Al(NO3)3 ∙ 9H2O | “х. ч.” | 3757–75 |
Аммиак водный | NH4OH | “ч. д. а.” | 3760–79 |
Кремниевая кислота | SiO2 ∙ nH2O | “ч. д. а.” | 4214–78 |
Карбонат аммония | (NH4)2CO3 | “ч.” | 3770–75 |
Из соли Al(NO3)3 ∙ 9H2O был приготовлен разбавленный раствор с концентрацией 0.1 М, из которого осуществляли осаждение гидроксида алюминия водным раствором NH4OH (~1 М). Процесс осаждения проводили при температуре 0–2°С на водно-ледяной бане для уменьшения степени агломерации Al(OH)3. Значение pH в реакционном сосуде поддерживали на уровне 9.0–9.5 единиц, чтобы избежать растворения уже образовавшегося гидроксида алюминия. Гелеобразный осадок Al(OH)3 подвергали вакуумной фильтрации, а затем термообрабатывали при 150°С (1 ч) в сушильном шкафу SNOL до образования бемита (AlOOH) (рис. 1а).
Рис. 1.
Дифрактограммы порошков, полученных при термическом разложении гидроксида алюминия: бемит (150°С) (а), γ-Al2O3 (500°С) (б). ⚪ – AlOOH, □ – γ-Al2O3.
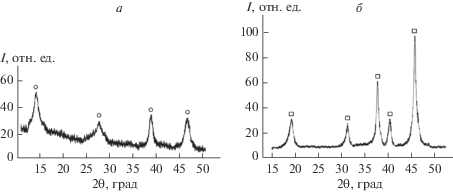
Методом дифференциального термического анализа исследовано термическое поведение AlOOH (рис. 2а). В интервале температур 100–300°С происходит дегидратация бемита. На кривой ДТА регистрируется экзотермический эффект (420–485°С), соответствующий кристаллизации оксида алюминия. Далее РФА порошка, после обжига AlOOH при 500°С (1 ч), свидетельствуют об образовании γ-Al2O3, средний размер кристаллов которого составляет 18–20 нм, а площадь удельной поверхности ~115 м2/г. Экзоэффекты при 760 и 980°С указывают на фазовые переходы γ-Al2O3 → → δ-Al2O3 и δ-Al2O3 → α-Al2O3 соответственно.
SiO2
Для получения аморфного SiO2 кремниевую кислоту подвергали термическому разложению. На рис. 2б видно, что в интервале температур 100–250°С фиксируется глубокий эндотермический эффект, характеризующий дегидратацию SiO2 ∙ nН2О. Именно в этом интервале температур происходит основная потеря массы образца (~54%, кривая ТГ) и кремниевая кислота переходит в аморфный SiO2 (рис. 3а). Площадь удельной поверхности диоксида кремния после термообработки при 250°С (1 ч) составляет ~300 м2/г. По данным РФА, в интервале температур 250–850°С диоксид кремния не претерпевает фазовых изменений и образец остается рентгеноаморфным. Выше 850°С наблюдается незначительный экзотермический эффект, обусловленный, по данным РФА (рис. 3б), кристаллизацией α-кристобалита из аморфного оксида кремния.
Получение пористой муллитовой керамики
В исследованиях [14–17], отмечается, что алюмосиликатная структура начинает формироваться в процессе МА и последующее нагревание МА-порошка ведет к образованию фазы со шпинельной структурой, которая превращается в муллит при 1100°С [15]. Учитывая вышесказанное, смешение γ-Al2O3 и аморфного SiO2 в соотношении Al2O3 : SiO2 = = 3 : 2 (как в муллите) осуществляли в режиме сухого помола в планетарной мельнице фирмы Fritch в течение 15 мин (соотношение массы мелющих шаров из высокоплотной алюмооксидной керамики к общей массе порошка составляло 10 : 1).
Для формирования пористой структуры в 3Al2O3 ∙ 2SiO2 использовали метод выгорающих добавок, основанный на введении и последующем выжигании порообразующего компонента. Данный метод перспективен для получения проницаемой керамики с порами каналообразной формы [23]. В МА-смеси добавляли порообразователь (карбонат аммония) в количестве 10 и 20 мас. % к общей массе порошка и перемешивали еще в течение 10 мин для гомогенного распределения (NH4)2CO3 во всем объеме смеси, чтобы после его выгорания получить равномерную пористую структуру в конечном изделии.
Из МА-смесей порошков методом одноосного двухстороннего прессования на гидравлическом прессе (ПГР-10) при давлениях 70 и 100 МПа прессовали таблетки (d = = 30 мм, h = 2–3 мм). Спрессованные образцы обжигали на воздухе при температурах 1100, 1200 и 1300°С (2 ч), скорость нагревания составляла ~400°C/ч [8, 9]. Охлаждение образцов не регулировали и проводили вместе с печью. По результатам РФА после обжига при 1100°С получены образцы муллита с небольшой примесью фазы α-кристобалита (рис. 4а), и открытой пористостью 53 и 57% в зависимости от количества (NH4)2CO3. Образцы оказались непрочными и разрушались под воздействием небольших механических нагрузок. При дальнейшем повышении температуры 1100°С → → 1200°С фаза α-кристобалита растворяется в 3Al2O3 ∙ 2SiO2, образуя твердый раствор диоксида кремния в муллите [24]. После обжига при 1300°С получены однофазные образцы 3Al2O3 ∙ 2SiO2 (рис. 4б). Значения линейной усадки, открытой пористости и среднего размера зерен в спеченных образцах муллита приведены в табл. 2.
Рис. 4.
Дифрактограммы муллита, полученного при 1100°С (а) и при 1300°С (б). ◇ – 3Al2O3 ∙ 2SiO2, ◻ ‒ α‑кристобалит.
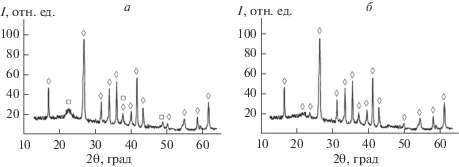
Таблица 2.
Условия получения и свойства пористой керамики 3Al2O3 ∙ 2SiO2
Состав МА-шихты | Давление прессования, МПа | Температура спекания, °С |
Линейная
усадка, % |
Средний размер зерна, нм | Открытая пористость, % | Объем пор, см3/г |
Предел прочности при сжатии, МПа | Химическая стойкость, % | |
---|---|---|---|---|---|---|---|---|---|
HNO3 | NaOH | ||||||||
3Al2O3 ∙ 2SiO2 + + 10 мас. % (NH4)2CO3 |
75 | 1300 | 3 | 85 | 40 | 0.310 | 62 | 96.5 | 84.7 |
100 | 1300 | 5 | 73 | 38 | 0.295 | 65 | 97.1 | 85.1 | |
3Al2O3 ∙ 2SiO2 + + 20 мас. % (NH4)2CO3 |
75 | 1300 | 7 | 97 | 47 | 0.437 | 55 | 96.1 | 83.7 |
100 | 1300 | 5 | 89 | 45 | 0.415 | 59 | 96.8 | 84.3 |
Поскольку пористая проницаемая алюмооксидная керамика востребована в качестве фильтрующих элементов, работающих в условиях воздействия на них как кислот, так и щелочей, была проведена оценка химической стойкости полученных образцов муллита. Для определения химической стойкости были выбраны образцы 3Al2O3 ∙ 2SiO2, спеченные при 1300°С. Оценку химической стойкости проводили по методике [21]. Образцы перед исследованиями сушили до постоянства массы при температуре 120°С, а затем помещали в азотную кислоту (концентрация 2 М) или в гидроксид натрия (концентрация 2 М) и выдерживали в течение 1 ч при температуре 60°С. После этого образцы промывали дистиллированной водой, сушили до постоянства массы и определяли химическую стойкость по потере массы. Образцы пористого муллита имеют достаточно высокие значения кислотостойкости и щелочестойкости (табл. 2). Полученные данные хорошо коррелируют с результатами, приведенными в работе [25].
Методом ртутной порометрии исследована пористая структура образцов 3Al2O3 ∙ 2SiO2, спеченных при 1300°С. Установлено, что после прессовки МА-смесей под давлением 70 МПа получается керамика с бимодальным распределением пор по размерам. Использование (NH4)2CO3 в количестве 20 мас. % увеличивает размер пор приблизительно в 1.5 раза, по сравнению с 10 мас. % бикарбоната аммония (рис. 5). Увеличение давления прессования МА-смесей до 100 МПа приводит к образованию керамики с достаточно узким мономодальным распределением пор по размерам 80–125 нм для 10 мас. % (NH4)2CO3 и 102–153 нм для 20 мас. % (NH4)2CO3 (рис. 6). В табл. 2 приведен объем пор во всех исследованных образцах. Также установлено, что пористая структура муллита влияет на предел прочности муллитовой керамики при сжатии, чем меньше размер и объем пор, тем больше значения прочности (табл. 2, рис. 6).
Рис. 5.
Распределение пор по размерам в керамике 3Al2O3 ∙ 2SiO2 (Рпрес = 70 МПа, 1300°C, 2 ч). 10 мас. % (NH4)2CO3 (а); 20 мас. % (NH4)2CO3 (б).
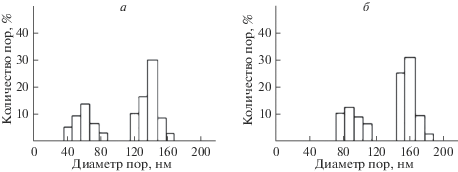
Рис. 6.
Распределение пор по размерам в керамике 3Al2O3 ∙ 2SiO2 (Рпрес = 100 МПа, 1300°C, 2 ч). 10 мас. % (NH4)2CO3 (а); 20 мас. % (NH4)2CO3 (б).
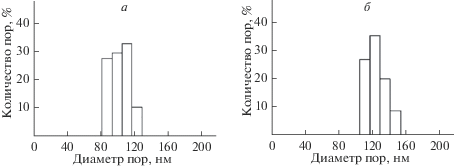
Учитывая тот факт, что размер пор в образцах 3Al2O3 ∙ 2SiO2 не превышает 200 нм, а открытая пористость составляет 40–47%, полученный муллит можно использовать без селективных слоев в определенных случаях фильтрации жидкостей. Это является положительным аспектом, поскольку при нанесении селективных слоев на пористую подложку методом шликерного литья, который наиболее часто используется, появляется проблема устранения пузырьков, образующихся в процессе изготовления шликера и его фиксации на керамике. В результате термообработки для закрепления селективных слоев в нем будут формироваться пустоты и это может приводить к образованию крупных пор и растрескиванию мембранного покрытия.
ЗАКЛЮЧЕНИЕ
Предложен способ получения однофазной нанопористой муллитовой керамики, включающий механохимическое активирование γ-Al2O3 и аморфного SiO2, введение в МА-смесь порообразователя (карбонат аммония) и спекание спрессованных образцов при температуре 1300°С (2 ч). Установлено влияние количества (NH4)2CO3, вводимого в МА-смесь, и давления прессования на открытую пористость керамики, объем пор и распределение пор по размерам. Показана возможность получения керамики 3Al2O3 ∙ 2SiO2 с открытой пористостью ~45% и мономодальным распределением пор в интервале от 80 до 150 нм, которую целесообразно использовать при создании фильтрационных элементов для разделения жидкостей, а также в системах подготовки питьевой воды.
Автор благодарит д. х. н. А.Е. Лапшина за проведение рентгенофазового анализа и к. х. н. Е.А. Васильеву за помощь в обсуждении данных, полученных методом ртутной порометрии.
Работа проведена в рамках темы НИР “Неорганический синтез и исследование керамических и органо-неорганических композиционных материалов и покрытий”.
№ государственной регистрации (ЦИТ и С): АААА-А19-119022290091-8.
Список литературы
Комоликов Ю.И., Благинина Л.Л. Технология керамических микро- и ультрафильтрационных мембран (обзор) // Огнеупоры и техническая керамика. 2002. № 5. С. 20–28.
Буякова С.П., Кульков С.Н. Формирование структуры пористой керамики, спеченной из нанокристалических поршков // Огнеупоры и техническая керамика. 2005. № 11. С. 6–11.
Красный Б.Л., Тарасовский В.П., Красный А.Б., Кутейникова А.Л. Свойства пористой проницаемой керамики на основе монофракционных порошков корунда и нанодисперсного связующего // Стекло и керамика. 2009. № 6. С.18–21.
Морозова Л.В., Калинина М.В., Шилова О.А. Получение и свойства пористой керамики на основе алюмомагниевой шпинели и диоксида циркония // Перспективные материалы. 2017. № 3. С. 59–69.
Васильева Е.А., Морозова Л.В., Лапшин А.Е., Конаков В.Г. Пористая керамика на основе алюмомагниевой шпинели // Журн. прикладной химии. 2002. Т. 75. Вып. 6. С. 898–902.
Зырянов В.В. Многослойные керамические мембраны с селективной проницаемостью // Конструкции из композиционных материалов. 2007. № 1. С.32–49.
Витязь П.А., Прохоров О.А., Шелехина В.М., Пилиневич Л.П. Технология изготовления керамических мембранных фильтров с градиентной микро- и нанопористой структурой // Вестник ДГТУ. 2008. Т. 8. № 1. С. 37–41.
Матренин С.В., Слосман А.И. Техническая керамика: Учебное пособие. Томск: Изд-во ТПУ. 2004. 75 с.
Дятлова Е.М., Какошко Е.С., Подболотов К.Б. Влияние вида сырья и активирующих добавок на процесс спекания, свойства, и структуру керамики на основе системы Аl2О3–SiO2 // Огнеупоры и техническая керамика. 2013. № 7–8. С. 12–18.
Стрелов К.К. Теоретические основы технологии огнеупорных материалов: учебное пособие. М.: Металлургия, 1985. 480 с.
Патент РФ № 2182569 / Владимиров В.С., Мойзис С.Е., Карпухин И.А., Корсун С.Д., Долгов В.И. / Пористый огнеупорный муллитовый материал и способ его получения. Официальный бюллетень Федеральной службы по интеллектуальной собственности (Роспатент) 2002, № 12.
Гусев А.И., Ремпель А.А. Нанокристаллические материалы. М.: Физматлит. 2001. 223 с.
Зырянов В.В. Механохимическая керамическая технология // Механохимический синтез в неорганической химии. Новосибирск: Наука, 1991. 102 с.
Карагедов Г.Р., Любушко Г.И. Механохимически стимулированный синтез однофазного муллита // Химия в условиях устойчивого развития. 1998. Т. 6. № 2–3. С. 161–163.
Temuujin J., Okada K., Mackenzie K.D. Comparative study of mechanochemical preparation of aluminosilicate precursors and amorphous silica // Brit. Ceram. Trans. 2000. V. 99. № 1. P. 76–79.
Патент РФ № 2 463 275 / Аввакумов Е.Г., Лепезин Г.Г., Сереткин Ю.В. / Способ получения муллита. Официальный бюллетень Федеральной службы по интеллектуальной собственности (Роспатент) 2012, № 2.
Пимков Ю.В., Филатова Н.В., Косенко Н.Ф., Безруков Р.М. Физико-химический анализ механоактивированного процесса муллитизации // Огнеупоры и техническая керамика 2014. № 4–5. С. 22–31.
Гусев А.И., Курлов А.С. Аттестация нанокристаллических материалов по размеру частиц (зерен) // Металлофизика и новейшие технологии. 2008. Т. 30. № 5. С. 679–694.
Межгосударственный стандарт ГОСТ 2409–2014.
Национальный стандарт Российской Федерации ГОСТ Р 7875–83.
Межгосударственные стандарты ГОСТ 473.1–81 и ГОСТ 473.2–81.
Назарова Т.И., Игнатова Т.С., Перепелицын В.А, Кудрявцева Т.Н. Влияние микроструктуры на свойства синтетических алюмосиликатных изделий // Огнеупоры. 1981. № 12. С. 44–47.
Гузман И.Я. Высокоогнеупорная пористая керамика. М.: Металлургия, 1971. 208 с.
Беляков А.В. Твердые растворы оксида кремния в муллите // Стекло и керамика. 2003. № 12. С. 17–20.
Морозова Л.В., Лапшин А.Е., Дроздова И.А. Получение и исследование пористой алюмосиликатной керамики // Физика и химия стекла. 2008. Т. 34. № 4. С. 578–584.
Дополнительные материалы отсутствуют.
Инструменты
Физика и химия стекла