Физика и химия стекла, 2021, T. 47, № 6, стр. 653-666
Спекание поликристаллических компактов из плакированных порошков детонационного наноалмаза
В. Н. Волов 1, *, С. П. Богданов 2, **
1 ООО “Новые алмазные технологии”
197706 Санкт-Петербург, Сестрорецк, ул. Воскова, 2, лит. Ю., Россия
2 Санкт-Петербургский государственный технологический институт (технический университет)
190013 Санкт-Петербург, Московский пр., д. 26, Россия
* E-mail: vnicni@yandex.ru
** E-mail: BogdanovSP@mail.ru
Поступила в редакцию 08.06.21
После доработки 13.07.21
Принята к публикации 06.08.21
Аннотация
Предложены технологические режимы производства сверхтвердого композиционного материала из алмазных нанопорошков детонационного синтеза методом горячего прессования в условиях высоких температур при сверхвысоком давлении. Пластины размерами до ∅13 × 8 и массой до 18 карат спекали на прессах ДО 044 в аппаратах высокого давления со вставками-матрицами из стали Р6М5 при давлении 5.5–6.5 ГПа и температуре 1500–1550°С. Достигнуты следующие параметры композита: микротвердость образцов – до 86 ГПа при нагрузке на индентор 200 г, максимальная прочность на сжатие образцов – до 12 ГПа при пикнометрической плотности до 3.35 г/см3; открытой пористости 0–1% и общей пористости 3–10%.
ВВЕДЕНИЕ
Материалы из алмазных нанопорошков детонационного синтеза (ПКДНА) еще не достигли уровня свойств поликристаллических сверхтвердых композиционных материалов, промышленно выпускаемых из микропорошков нитрида бора и алмаза (PCBN и PSDA). Они уступают последним по многим показателям (в первую очередь твердости, прочности, размерам) из-за технологических трудностей, связанных с их очень высокой удельной поверхностью и наличием большого количества сорбированных примесей.
Разработке технологий получения новых сверхтвердых материалов с использованием компонентов нанометрического диапазона посвящен ряд исследований [1–7]. В работах [3–5] показано, что различные виды воздействия на исходные нанопорошки алмазов и подготовленную шихту: химическое модифицирование поверхности частиц в сочетании с вакуумной очисткой и дегазацией, предварительная механическая активация, а также использование активирующих процесс спекания добавок — позволяет улучшить физико-механические свойства спеченных материалов.
В работе [1] в качестве исходного материала использованы смеси нанопорошков алмаза статического синтеза АСМ5 0.1/0 и АСМ5 0.5/0, активатором спекания служил CoO. Подготовленные смеси активировали методом многократного изостатического прессования при давлениях от 1.1 до 5.0 ГПа. Спекание шихты проводили при давлении 8.0 ГПа, температуре 2000 К, продолжительность спекания составляла 20–30 с. Получили композит с твердостью от 65.8 ГПа (при нагрузке на индентер 5 Н) и до 43.6 ГПа (при нагрузке на индентер 50 Н).
Авторы работы [6] отмечают, что спеканием “взрывного” наноалмаза в отсутствие активирующих добавок не удается достичь удовлетворительных механических свойств компактов. Использование в качестве активирующих добавок металлов-катализаторов (растворителей углерода) всерьез не рассматривали применительно к спеканию наноалмаза по очевидной причине — рекристаллизации алмаза в присутствии растворителя углерода. В работе [2] предприняли попытку спекания наноалмазов, полученных взрывным методом (тип DP, Mypolex, Microdiamant AG). Спекание наноалмаза осуществляли методом инфильтрации кобальтом при давлении 8 ГПа и температуре 1700–1800 К. Микротвердость образцов по методу Виккерса при нагрузке на алмазный индентер 4.9 Н составила в различных зонах образца от 15 до 55 ГПа.
Попытка спекания детонационных наноалмазов (ДНА) при давлении 5–7 ГПа и температуре 1200–2300°С для изготовления теплоотводов были предприняты авторами [7]. Сведений о механических свойствах, полученного материала авторы не приводят.
Нанопорошки алмаза обладают большой сорбционной емкостью из-за высокой удельной поверхности: 150−450 м2/г [8, 9]. По данным работ [10, 11] до 12–20% массы ДНА составляют сорбированные на их поверхности неуглеродные материалы: кислород, азот, водород и их соединения. Несгораемые примеси состоят из оксидов, карбидов и солей различных элементов, таких как Fe, Ti, Cr, Cu, K, Ca, Si, Zn, Pb и т. д. [10]. Примеси Fe, Ca, Si, Zn, Pb, наследуемые с исходным ДНА и попадающими в него из материала контейнера при спекании поликристаллов, существенно ухудшают их физико-механические свойства.
Сорбированные газы оказывают сильное влияние на результат спекания и ведут к снижению плотности поликристаллов. С уменьшением размера частиц алмаза до 0.3 мкм противодавление газов при 1600°С может подниматься до 6–8 ГПа [12]. Перед спеканием алмазных нанопорошков обязательной операцией является не только удаление сорбированных примесей, герметизация рабочего объема, но и модификация поверхности частиц ДНА для уменьшения содержания на них карбонильных и гидроксильных групп [13, 14]. Сообщается о результатах работы по спеканию поликристаллических компактов из ДНА после их отжига в вакууме: при динамическом спекании при 90 ГПа и температуре 2900°С – 3.05 г/см3 с твердостью 25 ГПа [15]. Статическое спекание в АВД типа “тороид” с диаметром углубления 13 мм позволяет спекать компакты при давлении около 8 ГПа в виде цилиндров диаметром 3 и высотой до 2.5 мм. В силу малого объема камеры и низкой плотности заготовок, вес компакта составляет 0.2–0.25 карата. Спекание в (АВД) с диаметром углубления 20 мм позволяет получать компакты при давлении около 8 ГПа в виде цилиндров диаметром до 6 и высотой до 4 мм и с весом компакта 1.5–1.8 карата. По литературным данным, достигнутый уровень свойств компактов сравнительно невысок: максимальная плотность при 8 ГПа и температуре 1200°С – 2.89 г/см3 [16], при 8 ГПа и температурах 1400–1500°С – 2.88 г/см3 [17]. В сочетании с модификацией поверхности ДНА в работе [14] при 8 ГПа и температуре 1550°С получены компакты с плотностью 2.86 г/см3 и твердостью 28 ГПа (измерение по методу Кнупа при нагрузке на индентер 9.8 Н). В работе [13] приведены похожие результаты спекания ДНА, модифицированного с помощью добавок B, Ti, Si – плотность 2.74–2.85 г/см3 и твердость 25–31 ГПа. Отмечено, что компакты содержат от 5 до 20% пор. На компактах, полученных из ДНА с добавкой AlN [18], достигнута плотность до 3.1–3.25 г/см3 и твердость 13–20 ГПа. Компакты из ультрадисперсных алмазов (УДА) статического синтеза, полученные в аналогичных условиях, имеют более высокие показатели: плотность до 3.1 г/см3, твердость 31–34 ГПа и трещиностойкость KIC = 7.5 ± 0.8 МН/м3/2 [19]. В работе [20] композит алмаз–карбид вольфрама на основе алмазного порошка АСМ 1/0 был изготовлен спеканием при давлении 8 ГПa в течение 20 с. Максимальная твердость до 22–23 ГПa была получена при добавлении 2.5 об. % W при 1530°C. В работе [21] показано, что введение карбидов переходных металлов и бора в состав поликристаллов алмаза при прочих равных условиях позволяет повысить их прочность в 1.2–1.3 раза. Возможность изготовления композитов методом инфильтрации Co [2, 16] или Si ограничена низкой глубиной проникновения расплава (до 2.2 мм), причем в порошки ДНА менее 0.5 мкм инфильтрация Si не наблюдается [22] из-за противодействия капиллярных сил.
В ООО “Новые Алмазные Технологии”, г. Санкт-Петербург, совместно с СПбГТИ(ТУ) были проведены следующие работы: исследованы исходные порошки ДНА; разработана технология модификации поверхности порошков ДНА различными материалами: опробованы 80 составов композиционного материала, где в качестве модификаторов использовались бор, титан, кремний, алюминий, никель, кобальт, железо, азот, водород, галогены и различные комбинации этих элементов, их долей и условий нанесения; опытным путем выбраны наиболее перспективные для поставленных целей активаторы; разработана конструкция реакторов для модификации ДНА; разработана конструкция реакционной ячейки для спекания ПКДНА в аппаратах высокого давления типа “чечевица” со вставкой-матрицей из стали Р6М5, обеспечивающая создание стабильного и высокого давления до 6.5 ГПа; отработаны режимы спекания ПКДНА: опытным путем подобран оптимальный ступенчатый режим создания давления и температуры в АВД; изучена структура ПКДНА методом оптической металлографии, рентгенофазовым и рентгеноструктурным анализами; проведена оценка качества ПКДНА: однородности (визуально), плотности (геометрической и пикнометрической), открытой и закрытой пористости, микротвердости по методу Виккерса, прочности компактов при раздавливании между твердосплавными дисками, прочности единичного зерна, полученного после дробления спеков, раздавливанием между пластинами из поликристаллов PCBN для зерна размером 2.5–0.05 мм и истиранием в специальном приборе для порошков 630–50 мкм.
ОБЪЕКТЫ И МЕТОДЫ ИССЛЕДОВАНИЯ
Рентгенофазовый анализ проводили на дифрактометре ДРОН-3. Использовали CuKα-излучение, рабочее напряжение 30 кВ при токе 20 мА. Съемку образцов вели в диапазоне углов 2θ от 10° до 150° с шагом 0.04°.
Измерение параметров рефлексов проводили с помощью программы Difwin1. Автоматически определяли центр тяжести, интенсивность, площадь и ширину на половине высоты пика. Во время измерений дуплет разделяли на две ветви. Для характеристики структуры использовали левые ветви Кα-дуплета Кα1 (λ1 = 0.154051 нм). Форму рефлексов описывали уравнением Гаусса–Коши. Для идентификации фаз использовали картотеку ICDD PDF.
Плотность определяли гидростатическим взвешиванием после кипячения в воде в течение 3 ч. Открытая пористость измерена методом водопоглощения.
Микротвердость (Hμ) измеряли на микротвердомере ПМТ-3 с алмазной пирамидой Виккерса при нагрузке 1.962 Н по ГОСТ 9450-76.
В работе использованы нанопорошки алмаза детонационного синтеза (ДНА) производства ООО “Реал-Дзержинск” (г. Н.-Новгород). До классификации частицы ДНА представляли собой агломераты размером 0–2 мкм с преобладанием частиц размером 0.2–0.8 мкм. Данный порошок был классифицирован в ООО “Новые Алмазные Технологии” на узкие фракции от 0.05/0 до 2/1 мкм. Для получения ПКДНА использовали фракции с размером от 200 нм до 1.0 мкм в разном соотношении.
По данным рентгенофазового анализа (рис. 1) основная фаза материала – алмаз. На углах до 30 град 2θ присутствуют размытые пики, положение которых совпадает с линиями углерода С60 и С8. Порошок ДНА является мелкокристаллическим с несовершенной структурой и размером блоков (областей когерентного рассеивания, ОКР) около 17 нм. Зольность (содержание несгораемых примесей) – 0.8%: определена сжиганием 15 карат ДНА при 1000°С в течение 3 ч (зола представляет собой стеклообразную массу). Зола, так же, как и в работе [8], состоит из оксидов, карбидов и солей Fe, Ti, Cr, Cu, K, Ca, Si, Zn, Pb. Исходные нано-порошки ДНА имеют низкий насыпной вес – 0.15–0.25 г/см3.
Для удаления сорбированных газов проводили термическую обработку порошков ДНА при температуре до 900°С в вакууме. Нагревание исходного ДНА в вакууме приводит к резкому увеличению давления в камере (с 10 до 20–30 Па), что свидетельствует о большом содержании сорбированных примесей. Наиболее интенсивно выделение примесей происходит в интервале температур 300–350°С. После отжига с изотермической выдержкой в течение 2 ч при температуре 400–420°С выделение газов из образца прекращается и давление в системе падает. После такой термообработки образцы ДНА выдерживали при остаточном давлении 4 Па в течение суток. Убыль массы исходных ДНА составила 5%. После извлечения из реактора образец начинает интенсивно сорбировать воздух и влагу, что заметно по постоянному приросту его массы во время взвешивания.
МОДИФИЦИРОВАНИЕ ПОВЕРХНОСТИ ДНА
С целью активации спекания и повышения прочности поликристаллов ДНА за счет изменения примесного состава поверхности порошков [23] их модифицировали методом йодного транспорта [24] титаном, бором, кремнием [21, 22, 25], а также алюминием и кобальтом [2, 13] в количестве 2–7 мас. % от суммарной массы с алмазом.
Эксперименты показали, что методом йодного транспорта можно наносить на поверхность ДНА покрытие из TiС. При этом температура, необходимая для реакции (Ti + С → TiС) должна быть не менее 400°С. Согласно расчетам при содержании титана в исходной смеси 6 вес. % и среднем диаметре частиц (агрегатов) алмаза 1.6 мкм, толщина покрытия TiС составляет 0.016 мкм (рис. 2). При использовании бора и кремния не удается получить на поверхности алмаза покрытий из карбидов В4С или SiС соответственно вплоть до 950°С. После вакуумирования и модифицирования поверхности насыпной вес порошков составлял – 0.65–0.85 г/см3. После прессования в пресс-форме при давлении 0.25–0.3 ГПа удавалось получить заготовки с плотностью 1.25–1.35 г/см3 и пористостью более 60%.
Рентгенофазовый анализ не позволяет однозначно идентифицировать состав фаз, образующихся при нанесении модифицирующих покрытий из-за их малой толщины от 2 до 20 нм. Только в опытах с использованием большого количества (более 4%) титана или кремния удавалось выделить линии TiC или β-SiC соответственно.
После спекания компактов дифрактограмма еще больше усложняется – выделить какие-либо фазы, кроме алмаза, практически невозможно: вероятно, это должны быть сложные оксикарбонитриды модификаторов (бора, кремния и титана) переменного состава.
СПЕКАНИЕ КОМПАКТОВ ПКДНА
Спекание ДНА проводили методом горячего прессования в условиях высоких температур при сверхвысоком давлении (HTHP). Заготовки с исходным размером ∅16 × × (12.5–14) мм и весом 16–18 карат прессовали в пресс-форме при давлении 0.25–0.30 ГПа. Высокая пористость заготовок (более 60%) накладывала существенные ограничения на давление в реакционной ячейке и на размер конечного спека. В работе использовали пресс ДО 044 усилием 2500 т.с. и АВД со вставками-матрицами из стали Р6М5 с твердостью 62–64 HRC конструкции Института сверхтвердых материалов. Для спекания компактов ПКДНА применяли реакционную ячейку (РЯ) с реакционным объемом 12–15 см3, специально разработанная для данных целей, позволяющая обеспечивать высокую теплоизоляцию реакционного объема и повысить рабочее давление до 5.5–6.5 ГПа. Калибровку РЯ проводили по методике [26], по давлению от усилия пресса, по температуре от мощности нагревание. Использовали температуры плавления образцов металлов-свидетелей (алюминий, медь, кремний, никель, титан) с учетом поправки на давление (рис. 3). Давление 6.5 ГПа, видимо, следует считать предельным для данного типа стальных АВД.
Рис. 3.
Зависимость температуры в реакционной ячейке от мощности нагревания, при давлении 5.5 ± 0.2 ГПа.
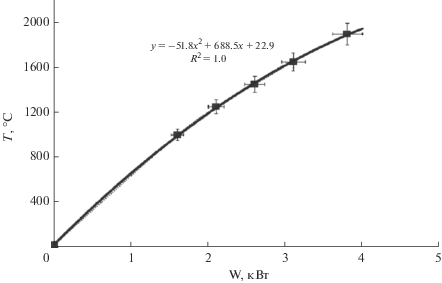
Общая продолжительность процесса спекания компакта составляла 5–7 мин, активная фаза спекания при температуре 1400–1800°С составляла 20 ± 5 с.
После спекания получали поликристаллы (ПКДНА) или спеки-компакты размерами ∅10.5–13.5 × 8.0–9.0 и массой до 18 карат. Для оптимизации технологических режимов было использовано 80 варианта шихты с различной комбинацией качественного и количественного состава плакированных порошков. С учетом спекания композиций одинакового состава при различных режимах, было наработано 950 различных вариантов ПКДНА.
ИЗУЧЕНИЕ СПЕЧЕННЫХ ОБРАЗЦОВ ПКДНА
Для подбора оптимального режима спекания, ряд образцов были изучены методом РФА (рис. 4, 5). На всех дифрактограммах видно существенное уменьшение ширины рефлексов алмаза, размер областей когерентного рассеивания (блоков) вырос с 3 нм для исходного ДНА до 68 нм для ПКДНА. Одновременно произошло увеличение параметра кристаллической решетки алмаза с 0.3554 нм у ДНА до 0.3566 нм у композита. Такие изменения в кристаллической решетке алмаза говорят о росте зерна и растворении в нем легирующих элементов в результате перекристаллизации. Набор других рефлексов на дифрактограмме не пренадлежащих алмазу зависит от типа и количества введенных в композицию активирующих спекание добавок. Так, в композиции из смеси порошков алмаза, плакированных титаном, бором и алюминием (рис. 4), кроме пиков алмаза, однозначно можно интерпретировать только пики TiC. Даже самый интенсивный пик на 43.05° можно интерпретировать или как кубический алмаз со значительно увеличенным параметром кристаллической решетки до 0.364 нм, или как новую фазу, образованная в результате взаимодействия компонентов шихты.
Рис. 5.
Дифрактограммы порошков 125/100 мкм (3), 40/7 мкм (2) и минус 7 мкм (1), полученных после дробления поликристаллов ПКДНА.
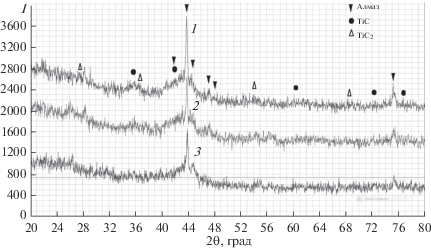
Зерно дробленого ПКДНА из плакированных титаном ДНА содержит фазы карбида и оксида титана и алмазные пики, которые могут принадлежать как кубической модификации, так и ромбоэдрическому алмазу 21R (рефлексы на 41.7, 43.1 и 46.4 ) или гексагональному алмазу 6H (рефлексы на 42.0 и 47.1), или гексагональному алмазу 8H (рефлексы на 42.8, 44.7 и 47.1) (рис. 5).
Спекание порошков ДНА покрытых титаном и карбидом титана приводит к полному переходу титана в форму карбида. На некоторых рентгенограммах фиксируются посторонние пики, которые можно идентифицировать как оксиды и/или нитриды титана. Это говорит о том, что металл, не связанный в карбид на поверхности порошка ДНА, во время спекания под давлением интенсивно окисляется воздухом, находящемся в порах.
Рентгенофазовый анализ спеченных образцов, модифицированных кремнием, показывает, что взаимодействие кремния с алмазом практически не происходит в условиях спекания, что согласуется с результатами работы [27]. На рентгенограммах превалируют рефлексы кремния и алмаза, изредка можно обнаружить рефлексы карбида кремния. Методом РФА не удалось зафиксировать взаимодействие с алмазом бора.
Пикнометрическая плотность образцов определена по разнице веса образца на воздухе и в дистиллированной воде. Для всех образцов была рассчитана максимальная теоретическая плотность исходя из их фазового состава. Средняя пикнометрическая плотность спеков из разных опытов 3.14–3.35 г/см3; открытая пористость 0–1%, общая пористость 3–10%. Усадка при спекании поликристаллов до плотности 3.35 г/см3 составляла более 60%.
Измерение восстановленной микротвердости проводили по ГОСТ 9450-76 на полированных поверхностях спеченных образцов. Для полировки поверхностей ПКДНА применяли специальные чугунные диски, используемые для огранки бриллиантов, с гальваническим закреплением микропорошков АСМ10/7. Компакт при полировке закрепляли в специальном приспособлении, опускаемом на полотно вращающегося диска. Скорость диска в зоне обрабатываемого изделия составляла 40–60 м/с. Усилие прижима полируемого образца к диску – до 15–20 Н.
Для измерения восстановленной микротвердости использована четырехгранная алмазная пирамида Виккерса. Была отмечена неоднородность спеков: как и в работе [27], наблюдаются участки различного оттенка, имеющие различную микротвердость. Методика измерения твердости была выбрана исходя из данного обстоятельства и учитывала другие особенности измерения микротвердости у сверхтвердых материалов. Характер зависимости величины микротвердости от размера диагонали отпечатка показан на рис. 6. В лучшем случае, абсолютная ошибка определения длины диагонали отпечатка примерно равна одному делению шкалы окуляра (цена деления 0.3 мкм). При нагрузке на индентер 200 г для отпечатков с размером диагонали 70 дел. (21 мкм) микротвердость Hμ равна 8.41 ГПа, абсолютная ошибка ±0.24 ГПа, относительная ошибка 2.9%. Если диагональ отпечатка уменьшиться в два раза до 35 дел. (10.5 мкм), то Hμ = 33.63 ГПа, абсолютная ошибка ±2.0 ГПа, относительная ошибка увеличивается в три раза до 6%. Для малых отпечатков (менее 10 мкм) ошибка измерения становится очень велика.
Рис. 6.
Зависимость восстановленной микротвердости от размера диагонали отпечатка при использовании четырехгранной алмазной пирамиды Виккерса при нагрузке на идентер 200 г.
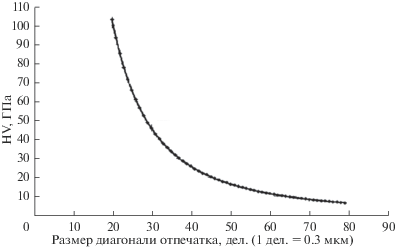
Известно, что величина твердости, измеренная по методу восстановленного отпечатка, зависит от нагрузки на индентер [28, 29]. Для увеличения точности измерения можно использовать пирамиду Кнупа, но в большинстве публикаций, которые удобно использовать для сравнения результатов, был использован индентер Виккерса.
Учитывая трудности объективной оценки твердости, нами были построены зависимости восстановленной Hμ от нагрузки на индентер для 4-х образцов различного диапазона твердости (рис. 7). Представленные кривые позволяют объективно сравнить полученные нами результаты с данными, полученными при иных условиях испытаний. Зависимости микротвердости ПКДНА от нагрузки имеют степенной характер – при нагрузке на индентер 200 г и более кривые становятся пологими: снижение измеренного значения микротвердости оказывается ниже погрешности измерения. Поэтому для дальнейшей оценки твердости была использована четырехгранная алмазная пирамида Виккерса при нагрузке на индентер 200 г. Точность определения размера диагонали отпечатка принимали равной 3–5 делениям (1–1.5 мкм), т.е. 20–50% для 60–80 ГПа.
Рис. 7.
Зависимость восстановленной микротвердости ПКДНА от нагрузки, при использовании четырехгранной алмазной пирамиды Виккерса.
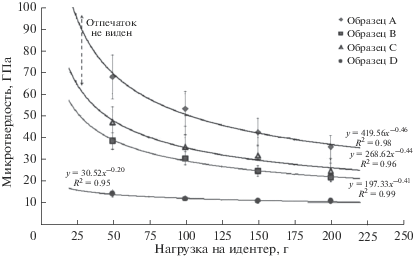
Микротвердость спеков сильно зависит от температуры спекания. Установлено, что эта зависимость носит экстремальный характер и имеет максимум при температуре 1500–1550°С, что соответствует мощности 2.65–2.70 кВт. Зависимость микротвердости спеков от мощности нагревания при их спекании для некоторых составов шихты приведена на рис. 8. Приведенные зависимости от мощности или времени спекания наблюдаются для многих процессов спекания поликристаллов из СТМ, например, похожи на зависимости прочности и плотности от температуры спекания, приведенные в работах [13, 17, 20, 29], а максимальные значения прочности и твердости компактов получены также при температурах 1500–1550°С. Такой характер изменения свойств можно объяснить как и в работе [12] – противодавлением сорбированных газов, не позволяющих частицам ДНА сближаться при спекании. Давление газов внутри компакта при высокой температуре становится выше, чем внешнее приложенное давление.
Далее в работе изучены свойства компактов, спекание которых проводили в области оптимальных температур.
Средняя микротвердость полученных спеков составляет 30–70 ГПа и сильно зависит от пористости. Отдельные компакты имели среднюю твердость до 86 ГПа и максимальную до 105 ГПа. Данный уровень микротвердости соизмерим с микротвердостью монокристаллов алмаза [28, 29] и поликристаллов алмаза АРК [30], мегадаймонд и СВ [29]. Отмечается высокая вязкость разрушения спеков: при замерах микротвердости по приведенной выше методике и с учетом методики, описанной в работе [31], микротрещин в зоне воздействия идентера не обнаружено, но в этой зоне наблюдается повышение прозрачности (“осветление”) материала – вероятно из-за местного повышения его плотности. Необходимо принять во внимание возможность появления фазовых переходов при идентировании, описанных в работе [32]. В работе [33] показан эффект значительного повышения трещиностойкости поликристаллов из-за остановки развития трещин в результате их взаимодействия с микропорами. У поликристаллических алмазов типа карбонадо (АРК), изученных в работе [30], также не удалось определить трещиностойкость по этой методике из-за отсутствия трещин вокруг отпечатка. Трещиностойкость ПКДНА существенно выше, чем у монокристаллов алмаза, имеющего KIC = (6.5–10.4) МН/м3/2 [28, 29, 34, 35]. В работе [34] показано, что напряженное состояние вокруг отпечатка мало чувствительно к форме пирамиды, и данные по трещиностойкости для пирамид Берковича и Виккерса сопоставимы.
Измерение прочности на сжатие компактов и пластин производили с помощью гидравлического пресса усилием 25 т. с. Перед замером образцы шлифовали и полировали с двух противоположных сторон и затем измеряли площадь шлифованных участков, принимающих усилие, с относительной точностью ±(5–10)%. Образцы помещали шлифованными плоскостями между двух параллельных дисков толщиной 20 мм из твердого сплава ВК6, запрессованных с натягом около 1 ГПа в кольца из стали 35ХГСА. Нагружение образцов проходило со скоростью 2–3 кН/с. Момент раздавливания компактов фиксировали визуально и по звуку. Точность измерения момента разрушения по усилию пресса ±2.5 кН. Относительная точность измерения прочности на сжатие ±15%. Погрешность измерения увеличивается с ростом твердости и прочности компактов. Фактические значения прочности для образцов с прочностью выше 6 ГПа могут быть ниже на 20–30% из-за упругих и пластических деформаций опор из твердого сплава, передающих усилие. Плоская схема нагружения образцов будет переходить к параболической, что снижает в них радиальные и тангенциальные напряжения. Можно предположить, что у всех исследователей при измерении прочности СТМ на сжатие по аналогичным методикам могло наблюдаться подобное искажение схемы нагружения.
Результаты измерения прочности ПКДНА на сжатие представлены на рис. 9, 10. Приведены данные для образцов, спеченных при температуре 1500–1550°С.
Рис. 9.
Зависимость прочности на сжатие пластин из ПКДНА и компактов, спеченных при температуре 1500–1550°С, от их микротвердости. Маркеры на рисунках обозначают спекание при давлении: “квадрат” и “кружки” – спекание при 5.5 ГПа, “треугольники” – при 6.0 ГПа; “ромбики” – при 6.5 ГПа. “Ромбики” в диапазоне твердости 25–52 ГПа – прочность пластин ∅(9.52–12.7) × (3.2–4.76) мм, изготовленных из компактов ПКДНА, спеченных при давлении около 5.5 ГПа.
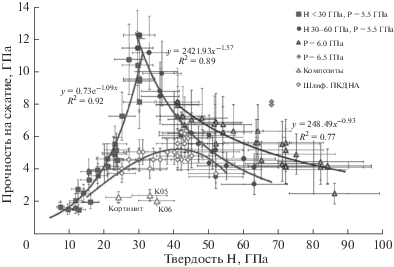
Рис. 10.
Сравнение ПКДНА по прочности и микротвердости с другими инструментальными материалами, а также со сверхтвердыми поликристаллическими материалами.
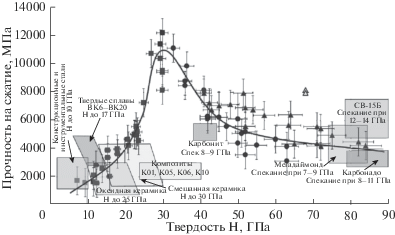
Прочность компактов имеет ярко выраженный максимум до 12 ГПа при микротвердости около 30 ГПа. Повышение прочности на участке микротвердости 0–30 ГПа происходит по экспоненциальному закону, а снижение на участке 30–90 ГПа – по степенному закону, что говорит об изменении характера процесса спекания ДНА: вероятно, в образцах с микротвердостью до 30 ГПа спекание происходило во всем объеме компакта и остановилось на этом этапе, выше 30 ГПа спекание ДНА продолжалось уже только в объеме микроагрегатов с их обособлением друг от друга и ослаблением границ между ними.
На шлифованных образцах, изготовленных из ПКДНА, спеченных при давлении около 5.5 ГПа, максимальная прочность до 6.2 ГПа получена для образцов с твердостью 40–45 ГПа. При этом зависимость прочности от твердости не имеет ярко выраженного максимума. Прочность и твердость у шлифованных образцов ниже, вероятно, из-за снятия напряжений при шлифовке и неоднородной усадки [36] поликристаллов при спекании – внутренняя часть спеков может быть более дефектной и пористой из-за остаточных газов. Характеристики, полученные на шлифованных образцах ПКДНА, близки к уровню поликристаллов марки АСПК-3 и карбонита [37, 38], спекаемого при 8–9 ГПа, и по прочности в 2 раза выше, чем у композитов марок кортинит, К05 и К06 (также измеренные в условиях этой работы).
Прочность на сжатие данных спеков зависит также от их дефектности: пористости, однородности, наличия трещин. Максимальная прочность 8–12 ГПа получена для спеков с твердостью 30 ± 5 ГПа, что 2–3 раза выше, чем прочность карбидо-вольфрамового твердого сплава и соизмерима с прочностью монокристаллов алмаза [36] (рис. 10).
Резкое снижение прочности у компактов ПКДНА с твердостью более 30–40 ГПа может быть связано с неоднородностью спекания нанопорошков алмаза, сопровождающейся местной усадкой и появлением ослабленных областей – с микротрещинами и микропорами, где концентрируются десорбированные газы. Графитизация алмаза происходит по границам его агрегатов и становится заметной уже при температурах спекания выше 1000°С [17] из-за взаимодействия ДНА с газами и соединениями, содержащими кислород [13]. Это предположение также подтверждают следующие наблюдения в данной работе:
1) значительный разброс в твердости, увеличивающийся у образцов со средней твердостью выше 40 ГПа: с 20 до 50% в одном образце,
2) зависимость прочности компактов от давления в АВД: для образцов со средней твердостью 68 ГПа, спеченных при давлении около 6.5 ГПа, прочность была в 2 раза выше, чем у образцов, спеченных при давлении около 5.5 ГПа.
Снижение прочности поликристаллов с повышением их твердости в данном случае не связано с противодавлением сорбированных газов [12], т.к. эти образцы спекались при постоянной мощности и максимальная температура спекания не превышала 1600°С. Также можно не учитывать рекристаллизацию зерна наноалмаза: по данным [12] заметный рост зерен начинается при температурах выше 1800–2000°С и при этом сорбированные газы тормозят процессы роста границ и зерен.
Поликристаллические компакты из ДНА обладают достаточно высокой термостойкостью: при отжиге ПКДНА в течение 2 ч при температуре 900°С снижение микротвердости составило 30–40% (на 15–25 ГПа). При этом компакты сохраняли свою целостность, в то время как поликристаллы типа АРК при 1200 К подвергаются интенсивному растрескиванию из-за наличия металлических включений [30].
ЗАКЛЮЧЕНИЕ
Литературные сведения и результаты проведенных исследований показывают, что использование для спекания неподготовленного порошка ДНА приводит к образованию непрочного компакта. Росту плотности поликристаллов с повышением температуры выше 1600°С может препятствовать развивающееся высокое противодавление сорбированных газов [12]. Для увеличения прочности компактов необходимо десорбировать примеси с поверхности алмазного порошка. Для эффективной очистки поверхности необходима термообработка порошка в вакууме при температуре не менее 500°С (верхний предел не определялся, но очевидно, что он ограничен температурой начала графитизации ДНА). Наиболее прочные, плотные и твердые компакты получены при использовании порошков ДНА, модифицированных В и Ti. Модифицирование осуществлено методом газового транспорта в присутствии йода. Присутствие в спекаемых порошках металлического титана нежелательно, т.к. это приводит к его окислению в процессе спекания, что ухудшает свойства спека. Для полного превращения Ti в TiС при нанесении покрытия необходима температура не менее 800°С. Установлены оптимальные параметры процесса спекания ПКДНА в условиях высокой температуры и сверхвысоких давлений (HTHP): температура 1500–1550°С при давлении 5.5–6.5 ГПа. В данной работе достигнуты следующие показатели качества компактов ПКДНА: общая пористость 3–10%, плотность до 3.35 г/см3, средняя микротвердость – до 86 ГПа, прочность на сжатие 8–12 ГПа (при микротвердости 30–40 ГПа) и 4–7 ГПа (для образцов с микротвердостью 50–90 ГПа), а также высокая трещиностойкость и термостойкость. Максимальная микротвердость – на отдельных образцах достигала 105 ГПа. Перспективным направлением для создания сверхтвердых композиционных материалов специального назначения может быть использование добавок в ДНА синтетических алмазов различных зернистостей, применение многослойных покрытий и смесей порошков с различными покрытиями.
Исследование выполнено за счет гранта Российского научного фонда (проект № 21-73-30019).
Список литературы
Соколов А.Н. Сверхтвердый наноалмазный композит инструментального назначения // Ж. Рос. хим. об-ва им. Д.И. Менделеева. 2006. Т. L. № 1. С. 50–53.
Екимов Е.А. Спекание наноалмаза в условиях инфильтрации кобальтом при высоких давлениях и температурах // Электронный научный журн. “Исследовано в России” 2008. С. 458–462.
Сверхтвердые материалы, получение и применение. Монография в 6 томах/ Под обшей ред. Н.В. Новикова. Т. I. Синтез алмаза и подобных материалов / Отв. Ред. А.А. Шульженко. Киев: ИСМ им. В.Н. Бакуля, ИПЦ “Алкон” НАНУ, 2003, 320 с.
Шульженко А.А., Соколов А.Н., Гаргин В.Т. Породоразрушающий и металлообрабатывающий инструмент – техника и технология его изготовления и применения: Сборник научных трудов. Киев: ИСМ им. В.Н. Бакуля, НАН Украины, 2004. Вып. 7. С. 101–106.
Сенють В.Т., Мосунов Е.И. Исследование физико-механических свойств нанокристаллических материалов на основе ультрадисперсных алмазов // Физика твердого тела. 2004. Т. 46. № 4. С. 746–748.
Ekimov E.A., Gavriliuk A.G., Palosz B., Gierlotka S., Dluzewski P., Tatianin E., Kluev Yu., Naletov A.M., Presz A. High -pressure, high-temperature synthesis of SiC–diamond nanocrystalline ceramics // Appl. Phys. Lett. 2000. V. 77. № 7. P. 954–596.
Kidalov S.V., Shakhov F.M., Vul A.Ya. Thermal conductivity of sintered nanodiamonds and microdiamonds // Diamond and Related Materials. 2008. V. 17. № 4. P. 844–847.
Долматов В.Ю. Ультрадисперсные алмазы детонационного синтеза: свойства и применение // Успехи химии. 2001. Т. 70. № 7. С.687–708.
Сакович Г.В., Комаров В.Ф., Петров Е.А. Синтез, свойства, применение и производство наноразмерных синтетических алмазов. Часть 1. Синтез и свойства // Сверхтвердые материалы. 2002. № 3. С. 3–18.
Губаревич Т.М., Кулагина Ю.В., Полева Л.И., Пятериков В.Ф., Долматов В.Ю. Меллитовая кислота из конденсированного алмазсодержащего углерода детонационной природы // ЖПХ. 1993. Т. 66. С. 1882–1885.
Кулакова И.И. Химия поверхности наноалмазов // Физика твердого тела. 2004. Т. 46. Вып. 4. С. 621–628.
Бочечка А.А. Влияние десорбированных газов на спекание алмазных порошков под действием высокого давления // Сверхтвердые материалы. 1998. № 4. С. 10–16.
Шульженко А.А., Бочечка А.А., Романко А.А., Кацай А.М., Гаргин В.Г. Особенности спекания нанометричных алмазных порошков, термообработанных в вакууме // Сверхтвердые материалы. 2000. № 6. С. 50–56.
Бочечка А.А. Свойства поликристаллов, спеченных при высоких давлениях из алмазных нанопорошков детонационного синтеза // Сверхтвердые материалы. 2002. № 6. С. 37–42.
Kondo K., Sawai S. Diamond compact of nano-sized grains // Science and Technology of New Diamond. KTK Scientific Publishing Company. Tokyo. Japan. 1990. P. 245–249.
Шульженко А.А., Бочечка А.А., Гаргин В.Г., Гонтарь А.Г., Романко Л.А., Ткач В.Н. Структура и свойства поликристаллов, спеченных из нанометричных алмазных порошков // Сверхтвердые материалы. 1998. № 4. С. 46–52.
Даниленко В.В., Петруша И.А., Олейник Г.С., Даниленко Н.В. Эволюция структуры компакта при спекании нанодисперсных алмазов в условиях высоких давлений // Сверхтвердые материалы. 1998. № 4. С. 53–61.
Витязь П.А., Сенють В.Т. Компактирование наноалмазов детонационного синтеза и свойства композиционных и поликристаллических материалов на их основе // Физика твердого тела. 2004. Т. 46. Вып. 4. С. 743–745.
Шульженко А.А., Бочечка А.А., Олейник Г.С., Гаргин В.Г., Романко Л.А, Белявина Н.Н., Дуб С.Н., Рогов В.В. Спекание алмазного нанопорошка статического синтеза и свойства поликристаллов на его основе // Сверхтвердые материалы. 2001. № 5. С. 29–37.
Назарчук С.Н., Свирид Е.А., Гаврилова В.С., Романко Л.А., Бочечка А.А. Свойства композита алмаз–карбид вольфрама на основе алмазного порошка АСМ 1/0 // Физика и техника высоких давлений. 2011. Т. 21. № 1. С. 33–37.
Елютин В.П., Поляков В.П., Лапин В.В., Калашников А.Я., Никольская И.В., Митоян К.В., Митоян М.А. Влияние переходных металлов 4–5 групп на физико-механические свойства алмазных поликристаллов. В кн.: Сверхтвердые материалы: синтез, свойства, применение: Докл. междунар. семинара / Под ред. Н.В. Новикова. Киев: Наук. думка. 1983. 236 с. С. 93–97.
Екимов Е.А., Громницкая Е.Л., Мазалов Д.А., Паль А.Ф., Пичугин В.В., Гиерлотка С., Палош Б., Козубовский Я.А. Микроструктура и механические свойства компактов наноалмаз – SiC // Физика твердого тела. 2004. Т. 46. Вып. 4. С. 734–736
Ефименко Л.П., Богданов С.П., Сычев М.М. Металлизация алмаза как способ повышения работоспособности сверхтвердых материалов // Физика и химия стекла. 2021. Т. 47. № 1. С. 65–77.
Богданов С.П. Йодотранспортный метод получения покрытий на порошках // Известия СПбГТИ(ТУ). 2012. № 16(42). С. 24–28.
Витязь П.А., Сенють В.Т. Компактирование наноалмазов детонационного синтеза и свойства композиционных и поликристаллических материалов на их основе // Физика твердого тела. 2004. Т. 46. Вып. 4. С. 743–745.
Богданов С.П. Роль размера частиц графитоподобного нитрида бора при нуклеации кубического нитрида бора // Физика и химия стекла. 2008. Т. 34. № 2. С. 274–280.
Бритун В.Ф., Курдюмов А.В. Структура поликристаллов, полученных спеканием алмазных порошков динамического синтеза // Сверхтвердые материалы. 1998. № 4. С. 36–41.
Физические свойства алмаза. Справочник / Под ред. Н.В. Новикова. Киев. Наукова думка. 1987. 192 с.
Поляков В.П., Ножкина А.В., Чириков Н.В. Алмазы и сверхтвердые материалы. Учебное пособие для вузов. М.: Металлургия, 1990. 327 с.
Кожогулов О.Ч., Хайдаров К.Х., Мальнев В.И. Исследование механических свойств алмазов АРК // Сверхтвердые материалы. 1993. № 1. С. 24–26.
Дуб С.Н. Методика испытаний на трещиностойкость монокристаллов синтетического алмаза.Сб. науч. трудов: Производство и применение сверхтвердых материалов. Киев. ИСМ АН УССР. 1983. С. 75–78.
Мильман Ю.В. Фазовые превращения под давлением при идентировании // Физика и техника высоких давлений. 2011. Т. 21. № 1. С. 7–13.
Сотник А.А., Васильев А.Д., Слысь И.Г. Влияние пористости на трещиностойкость хрупких порошковых материалов. Электронная микроскопия и прочность материалов. Сб. науч. тр., ИПМ им. И.Н. Францевича АН УССР. Киев. 1989. С. 34–40.
Дуб С.Н., Мальнев В.И. Особенности испытаний кристаллов алмаза и кубонита на трещиностойкость. Сб. статей: Методы исследования свойств сверхтвердых материалов. Киев: ИСМ АН УССР. 1981. С. 21–25.
Воронин Г.А., Воронина Г.В. Напряженно-деформированное состояние алмазных кристаллов при сжатии. Сб. статей: Методы исследования свойств сверхтвердых материалов. Киев: ИСМ АН УССР. 1981. С. 9–12.
Семенова-Тян-Шанская А.С., Овчинников А.А., Мартиросов А.Б. Связь физико-механических свойств карбонадо с эксплуатационными характеристиками резцов // Алмазы и сверхтвердые материалы. 1977. Вып. 3. С. 12–13.
Клячко Л.И., Вепринцев В.И., Колчин В.А., Кириллин Н.М. Синтетические поликристаллические алмазы для оснащения различных видов инструмента. В кн.: Сверхтвердые материалы: синтез, свойства, применение: Докл. междунар. семинара / Под ред. Н.В. Новикова. Киев: Наук. думка. 1983. 236 с. С. 134–137.
Новиков Н.В., Федосеев Д.В., Никитин Ю.И., Герасименко В.К., Полторацкий В.Г., Муковоз Ю.А., Карась В.И. Получение, физико-механические и эксплуатационные свойства карбонита // Сверхтвердые материалы. 1988. № 4. С. 3–6.
Дополнительные материалы отсутствуют.
Инструменты
Физика и химия стекла