Физика и химия стекла, 2022, T. 48, № 1, стр. 63-68
Инструментальные материалы, изготовленные из поликристаллических компактов детонационного наноалмаза
В. Н. Волов 1, *, С. П. Богданов 2
1 ООО “Новые алмазные технологии”
197706 Сестрорецк, Санкт-Петербург, ул. Воскова, 2, лит. Ю, Россия
2 Санкт-Петербургский государственный технологический институт (технический университет
190013 Санкт-Петербург, Московский пр., д. 26, Россия
* E-mail: vnicni@yandex.ru
Поступила в редакцию 08.06.21
После доработки 24.07.21
Принята к публикации 06.08.21
- EDN: LENBJM
- DOI: 10.31857/S0132665121060354
Аннотация
Предложены инструментальные материалы, изготовленные из поликристаллических компактов, синтезированных из алмазных нанопорошков детонационного синтеза. После дробления и классификации компактов получено поликристаллическое зерно с выходом зернистости +250 мкм более 40%. Прочность зерен зернистостей от 315 мкм до 2.5 мм соответствует маркам алмазных порошков АРК4–АРС3. Методом шлифования изготовлены круглые режущие пластины 9.525 × 3.18 и 12.7 × 4.76 мм. Методом лазерной резки изготовлены распылительные сопла.
ВВЕДЕНИЕ
В работе [1] показано, что введение карбидов переходных металлов и бора в состав поликристаллов алмаза при прочих равных условиях позволяет повысить их прочность в 1.2–1.3 раза. Металлизация порошков алмаза титаном, бором, кремнием, в том числе детонационного синтеза (ДНА), методом йодного транспорта является эффективным способом изменения примесного состава поверхности порошков с целью активации спекания и повышения прочности поликристаллов [2]. Ранее были описаны синтез и свойства сверхтвердого композиционного материала из алмазных нанопорошков детонационного синтеза (ПКДНА, “Физика и химия стекла”, № 6, 2021 г.). Наиболее прочные, плотные и твердые компакты получены при использовании порошков ДНА, модифицированных В и Ti, после спекания ПКДНА при температуре 1500–1550°С и давлении 5.5–6.5 ГПа: общая пористость 3–10%, плотность до 3.35 г/см3, средняя микротвердость – до 86 ГПа, прочность на сжатие 8–12 ГПа (при микротвердости 30–40 ГПа) и 4–7 ГПа (для образцов с микротвердостью 50–90 ГПа), а также высокая трещиностойкость и термостойкость. Максимальная микротвердость на отдельных образцах достигала 105 ГПа. Полученный поликристаллический композиционный материал, благодаря сочетанию высокой твердости и прочности с малым размером составляющих его зерен, может быть использован для изготовления различного инструмента. Высокие твердость и прочность позволяют рекомендовать его для режущего инструмента. Сочетание высокой твердости с мелкозернистой структурой может быть интересно при изготовлении абразивного инструмента. Важным требованием к материалам, используемым для изготовления волок, является также устойчивость к динамическим нагрузкам (высокая трещиностойкость), отсутствие металлических включений и высокая однородность их структуры [3]. Полученный ПКДНА обладает всеми этими качествами и может быть перспективным материалом для изготовления волок для вытягивания проволоки, в том числе из тугоплавких и твердых металлов.
ОБЪЕКТЫ И МЕТОДЫ ИССЛЕДОВАНИЯ
Для изготовления инструментальных материалов использованы ПКДНА, спеченные в условиях высокой температуры и сверхвысоких давлений (HTHP): температура 1500–1550°С при давлении 5.5–6.5 ГПа из плакированных порошков ДНА.
Микротвердость компактов (Hμ) измеряли на микротвердомере ПМТ-3 с алмазной пирамидой Виккерса при нагрузке 1.962 Н по ГОСТ 9450-76.
Прочность абразивного зерна определяли двумя методами. Механическую прочность единичного зерна (Н/зерно) всех зернистостей измеряли по ГОСТ 9206. У порошков зернистостей менее 630/500 мкм также еще измеряли и прочности на истирание МПи по методике, разработанной В.И. Шеманиным (ТУ 3978-019-05748371-97 Материалы шлифовальные из эльбора). МПи – это остаток зерна на сите в % мас. после воздействия на 1–2 карата зерна путем истирания 10 оборотами в ступке ∅30 мм грузом весом 1 кг с последующей классификацией (отсевом разрушенного зерна на соответствующем сите).
Измерение прочности зерна на сжатие производили с помощью динамометров с максимальным усилием 0.5 и 2.0 кН. Для измерения прочности зерно помещали между двух параллельных шлифованных пластин из поликристаллов кубического нитрида бора марки КП3 производства ООО “ПАЗИ” с микротвердостью около 35 ГПа, которые в свою очередь помещали вместе с динамометром в рабочее пространство ручного гидравлического пресса усилием 5 т. Нагрузку на образцы увеличивали со скоростью 10–20 Н/с. Момент раздавливания зерна фиксировали визуально и по звуку. Для каждой зернистости для проведения измерений на прочность отбирали случайным образом не менее 50 зерен. Данные обрабатывали согласно требованиям ГОСТ 9206. Точность измерения прочности на сжатие ±10%.
ИЗГОТОВЛЕНИЕ АБРАЗИВНОГО ЗЕРНА
Для изготовления абразивного зерна в данной работе были использованы спеки с низкими характеристиками по плотности и твердости и наиболее дефектные трещиноватые спеки. Это несомненно отразилось на распределении порошков после дробления и снижении их прочности.
Спеки дробили раздавливанием в прессформе на прессе усилием 25 т.с. между твердосплавными дисками. После дробления компактов зерно было овализовано в “пьяной бочке” с твердосплавными шарами и классифицировано по размеру на ситах и по форме на вибростоле. Были получены шлифпорошки и зерно крупностью до 2.5 мм, а также микропорошки от 40 мкм и ниже (рис. 1).
Рис. 1.
Распределение по зернистости готовых порошков и зерна после дробления спеков ПКДНА, овализации и классификации. П.1 – партия порошков, полученных из ПКДНА с твердостью 10–30 ГПа, П.2 – партия порошков, полученных из ПКДНА с твердостью 30–80 ГПа.
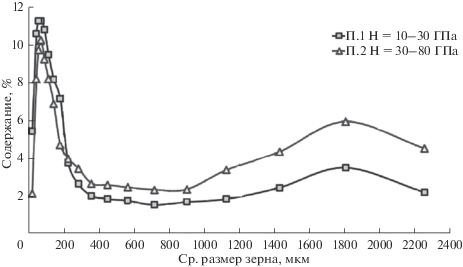
На диаграмме представлены распределения по зернистостям двух партий порошков, для изготовления первой партии использовали спеки с твердостью от 10 до 30 ГПа (среднее значение около 25 ГПа), а для второй партии были использованы спеки с твердостью от 30 до 80 ГПа (среднее 45 ГПа). Во второй партии выход зерна зернистостей более 1.0 мм был в 2 раза выше, чем в первой.
Установлено, что прочность зерна на сжатие зависит от твердости исходных компактов и имеет максимум для материала из компактов с твердостью 40 ГПа. Зависимости прочности для зернистостей 1.25/1.0 и 1.0/0.8 мм для 6 опытов приведены на рис. 2. Такой характер совпадает с характером взаимосвязи прочности на сжатие с твердостью для исходных спеков [4 ] . Определение прочности зерна согласно ГОСТ 9206 показало, что по этому показателю материал соответствует маркам поликристаллических алмазов АРС3–АРК4.
Рис. 2.
Зависимость механической прочности зерна 1.25/1.0 и 1.0/0.8 мм от твердости исходных компактов ПКДНА.
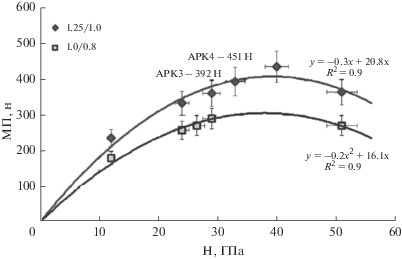
Дробленые порошки ПКДНА зернистости 250/100 мкм соответствуют по прочности порошкам АС15–АС32, зернистости 630/300 мкм – маркам АС50 и АРВ1. Дробленые порошки ПКДНА зернистости 1500/500 мкм соответствуют по прочности зерну АРС3 и приближаются к прочности порошков АС100. Полученное зерно 2.5/1.5 мм имеет показатели прочности выше, чем для зерна АРК4 [4, 5 ] (см. диаграммы на рис. 3, 4).
ИЗГОТОВЛЕНИЕ ИНСТРУМЕНТА
Из-за очень высокой твердости и вязкости ПКДНА изготовление режущих пластин из этого композита сопряжено с низкой производительностью и повышенным расходом инструмента при шлифовке. Для повышения производительности была проведена работа по подбору специального инструмента и оптимизации технологии обработки ПКДНА. Лучшие результаты получены при шлифовке алмазным инструментом производства ООО “Петербургский Абразивный завод “Ильич” на керамической связке: шлифпорошок АС32, концентрация 125–150%, связка К11, твердость Т1–Т2. Для полировки шлифованных поверхностей использовали специальные чугунные диски с гальваническим закреплением микропорошков АСМ зернистости 10/7 мкм, используемые для огранки бриллиантов. В результате была изготовлена партия круглых режущих пластин размером 9.525 × 3.18 и 12.7 × 4.76 мм по ГОСТ 28762-90 “Пластины режущие сменные из сверхтвердых материалов. Технические условия”. Испытания пластин на износ по задней поверхности показали, что они полностью удовлетворяют требованию ГОСТ, таким образом, ПКДНА может быть успешно использован в качестве режущего материала.
Спеки-компакты из ДНА не содержат металлических примесей, благодаря чему хорошо поддаются лазерной резке. Этим методом из ПКДНА в ООО “Новые Алмазные Технологии” были изготовлены распылительные сопла. Из одной пластины ∅13 × 3.2 мм с помощью лазера вырезали по 7 распылительных сопел ∅3.5 × 3.2 мм с отверстиями от ∅0.15 до 0.5 мм. Данные изделия были успешно использованы в установке для дезинтеграции нано- и микропрошков алмаза в пульпе для их последующей классификации по размеру в центрифугах.
ЗАКЛЮЧЕНИЕ
Уровень характеристик произведенного абразивного зерна 2.5/1.0 мм сопоставим по прочности с уровнем поликристаллических алмазов марки АРК4, а порошки фракции 1000/630 мкм приближаются к прочности порошков алмаза марки АС100.
Абразивное зерно и шлифпорошки из ПКДНА можно рекомендовать для изготовления буровых коронок и шлифовального инструмента для обработки высокотвердой керамики. Микропорошки из ПКДНА можно рекомендовать для полирования высокотвердой керамики (например, сапфира).
Подтверждено, что сверхтвердый композиционный материал, полученный спеканием алмазных нанопорошков детонационного синтеза (ПКДНА), может быть использован для изготовления как поликристаллического абразивного зерна, так и монолитного инструмента. Из ПКДНА изготовлены резцы и распылительные сопла, которые прошли успешные испытания .
На основании опыта применения аналогичных по качеству поликристаллических алмазов, пластины из ПКДНА с твердостью 30–40 ГПа (и повышенной прочностью) можно рекомендовать для обработки материалов (кроме сталей) с высокой вязкостью и при точении с ударом. Пластины с твердостью более 50 ГПа можно использовать для обработки твердых керамических материалов.
Исследование выполнено за счет гранта Российского научного фонда (проект № 21-73-30019).
Список литературы
Елютин В.П., Поляков В.П., Лапин В.В., Калашников А.Я., Никольская И.В., Митоян К.В., Митоян М.А. Влияние переходных металлов 4–5 групп на физико-механические свойства алмазных поликристаллов. В кн.: Сверхтвердые материалы: синтез, свойства, применение: Докл. междунар. семинара / Под ред. Н.В. Новикова // Киев: Наук. думка, 1983. С. 93–97.
Ефименко Л.П., Богданов С.П., Сычев М.М. Металлизация алмаза как способ повышения работоспособности сверхтвердых материалов // Физика и химия стекла. 2021. Т. 47. № 1. С. 65–77.
Бочечка А.А. Спекание алмазных заготовок для волок. В сб. науч. тр.: Сверхтвердые материалы в ускорении научно-технического прогресс // Киев, ИСМ АН УССР, 1987. С. 7–11.
Дополнительные материалы отсутствуют.
Инструменты
Физика и химия стекла