Физика и химия стекла, 2022, T. 48, № 3, стр. 325-333
Физико-механические свойства композиционной керамики в системе ZrB2–SiC–MoSi2
Е. С. Мотайло 1, *, Л. А. Лисянский 1, С. В. Вихман 1, Д. Д. Несмелов 1
1 Санкт-Петербургский государственный технологический институт (технический университет)
190013 Санкт-Петербург, Московский проспект, 26, Россия
* E-mail: ceramic-department@yandex.ru
Поступила в редакцию 13.05.21
После доработки 28.07.21
Принята к публикации 06.08.21
- EDN: GHGMSQ
- DOI: 10.31857/S0132665121060263
Аннотация
Исследованы спекаемость и механические характеристики полученных спеканием материалов в системе ZrB2–SiC–MoSi2. Определены плотность, линейный коэффициент термического расширения 4.9–6.1 × 10–6 К–1, предел прочности при изгибе образцов керамик (σmax = 460 МПа) и модуль упругости (до 360 МПа), исследована микроструктура. Фазовый состав некоторых керамик, кроме исходных компонентов, содержит новые фазы – MoB, ZrC и Mo4.8Si3C0.6.
ВВЕДЕНИЕ
Керамические конструкционные материалы, эксплуатируемые при высоких температурах в окислительных средах, должны обладать нетривиальным комплексом механических, физико-химических, теплофизических и других характеристик. Анализ термодинамически стабильных систем соединений для создания материалов с таким комплексом свойств указывает на перспективность применения химических соединений эвтектических систем. В литературе описаны фазовые равновесия в квазибинарных эвтектических системах SiC–MeVISi2 [1–4], SiC–MedB2 [5] и MedB2–MeVISi2 [6, 7], где MeVI – Mo и W, а Med – d-металлы IV–VI групп. Большинство систем являются термодинамически стабильными при температурах ниже ликвидуса, что дает основание рассматривать их в качестве основы для высокотемпературных керамических материалов. Важнейшая область применения подобных материалов – создание деталей и узлов летательных аппаратов, подвергающихся экстремальным воздействиям температуры, воздушных и газовых потоков, механических нагрузок. Одним из важных свойств материалов, предназначенных для авиационно-космической отрасли, является плотность. При создании композиционных керамик, в состав которых входят химические соединения с различной плотностью, появляется возможность ее регулирования в зависимости от концентрации исходных компонентов.
Материалы системы SiC–MeVISi2 обладают относительно невысокой плотностью (в зависимости от концентрации SiC – 3.3–6.2 г/см3). Керамика системы SiC–MedSi2 обладает хорошей стойкостью к окислению до температуры около 1600–1700°С [8]. Несмотря на то, что существующая в системах Si–C–MeVI тройная фаза Новотного [9, 10] не находится непосредственно на разрезе SiC–MeVISi2, в реальных условиях при синтезе и спекании материалов на основе SiC и MoSi2 может наблюдаться формирование Mo4.8Si3C0.6, обладающей высокой стойкостью в условиях нагрева на воздухе.
Среди систем MedB2–MeVISi2 [11–13] наиболее широко изучены материалы системы ZrB2–MoSi2 [12, 13]. Такая керамика имеет более высокую плотность (6.08–6.26 г/см3), чем композиты на основе SiC–MoSi2, однако она также находит применение при создании элементов реактивных двигателей и теплонагруженных элементов конструкции летательных аппаратов – носовых обтекателей, кромок крыла и т.д. Это обусловлено, в первую очередь, высокой температурой плавления ZrB2 (3250°С) и связанным с этим сохранением высокого уровня прочности при экстремальных температурах. Однако ZrO2, образующийся при окислении ZrB2, не формирует сплошной оксидной пленки, что ограничивает применимость таких материалов в окислительной среде. Решением этой проблемы является создание материалов на основе систем MedB2–SiC [14–19]. При окислении таких материалов формируются хорошо защищающие поверхность от дальнейшего взаимодействия с кислородом боросиликатные стекла при температурах около 1200°С и силикат MedSiO4 при более высоких температурах.
В последние годы наблюдается рост интереса к материалам систем с 2-мя и более числом компонентов, в частности, системам MedB2–SiC–MoSi2, где MedB2 – тугоплавкий борид металла IV–V групп [20–28]. Переход от квазибинарных систем к квазитройным не только позволяет интегрировать характеристики рассмотренных квазибинарных систем, но и реализовать ряд специфических преимуществ многокомпонентных эвтектик. Свойственное эвтектическим системам снижение температуры появления жидкой фазы (по сравнению с чистыми компонентами) позволяет активировать процессы уплотнения при спекании (горячем прессовании, SPS), а многокомпонентность системы создает заметный эффект взаимной блокировки роста зерен каждой из фаз [29]. Вследствие этого после спекания формируется структура керамики с минимальной пористостью. При этом наблюдается 2–5 кратный рост размера фазовых составляющих в процессе спекания, что примерно в 5–10 раз меньше роста зерен однофазных материалов в аналогичных условиях. Хорошей иллюстрацией описанных явлений служат данные работы [20], авторы которой горячим прессованием получали материал на основе системы ZrB2–SiC–MoSi2, продемонстрировавший предел прочности при изгибе до 863 ГПа, твердость до 16.8 ГПа и трещиностойкость до 3.7 Мпа ⋅ м1/2. При изучении аналогичного материала, полученного свободным спеканием в работе [30], достигнута прочность при изгибе 480 МПа при относительной плотности выше 99%. Высокую плотность продемонстрировали материалы в системе MoSi2–SiC–TiB2 [31]. При этом наивысшие показатели механических характеристик (предел прочности на изгибе – 520 МПа, твердость – 22.1 ГПа) показал материал, содержащий 50, 15 и 35% (об.) MoSi2, SiC, и TiB2 соответственно, полученный свободным спеканием при 1950°C.
Материалы на основе MoSi2, SiC и диборидов переходных металлов перспективны в качестве защитных покрытий. Так, в работах [32–36] описано получение защитных покрытий для C/C композитов, стойких против окисления до температуры 1500°С.
Все вышеизложенное позволяет заключить, что системы MedB2–SiC–MoSi2 представляют большой интерес для создания на их основе композиционных керамик рассчитанных для эксплуатации при высоких температурах.
МЕТОДИКИ ЭКСПЕРИМЕНТА
В работе использовали порошки ZrB2 производства АО “ДЗХР” с размером частиц d50 = 7–10 мкм, содержанием основной фазы не менее 98%, SiC марки Sika Sintex 13C (Saint-Gobain) чистотой 98.5% (d50 = 1.15 мкм), MoSi2, содержащий не менее 98% основной фазы (d50 = 10–15 мкм). Измельчение порошков осуществляли с помощью лабораторной вибрационной мельницы в среде растворителя БР-2 мелющими телами из высокоплотного SiC при массовом соотношении материала (M), среды помола (F) и мелющих тел (B) M : F : B = 1 : 1 : 10 в течение 48 ч. Размер частиц после помола составил ≤3 мкм, что подтверждено данными, полученными на лазерном анализаторе размеров частиц Shimadzu SALD-7500nano. Вследствие абразивного износа мелющих тел в смесь дополнительно внесено 3 мас. % SiC, что учтено при дозировании навесок. Смешение компонентов в соотношениях согласно табл. 1 осуществляли в барабанном смесителе. В качестве мелющих тел использовали шары из высокоплотного SiC.
Таблица 1.
Объемные соотношения компонентов в составах системы ZrB2–SiC–MoSi2
№ | 1 | 2 (Е1) | 3 | 4 | 5 | 6 | 7 | 8 | 9 | 10 | 11 | 12 | 13 | 14 | 15 |
---|---|---|---|---|---|---|---|---|---|---|---|---|---|---|---|
SiC | 11 | 10 | 26 | 80 | 20 | 5 | 12 | 60 | 22 | 33 | 40 | 45 | 20 | 20 | 15 |
MoSi2 | 86 | 84 | 66 | 10 | 69 | 78 | 70 | 20 | 43 | 33 | 20 | 10 | 15 | 10 | 8 |
ZrB2 | 3 | 6 | 8 | 10 | 11 | 17 | 18 | 20 | 34 | 34 | 40 | 45 | 65 | 70 | 77 |
Из молотых порошков одноосным полусухим прессованием при давлении 70 МПа получали образцы в виде дисков диаметром 15 мм и высотой 4 мм и прямоугольных призм длиной 32 мм, шириной 4 мм и высотой 4 мм. Вторичную консолидацию керамических материалов проводили спеканием без приложения внешнего давления. Образцы спекали в вакуумной печи сопротивления СШВЭ 1.2.5 (СНВГ 1.2.1) при давлении остаточных газов 10–2 Па с изотермической выдержкой в течение 1 ч при температурах 1750°C (все составы) и 1820°C (составы 1, 5).
Рентгенофазовый анализ спеченных образцов осуществляли с помощью дифрактометра Rigaku SmartLab 3 (CuKα-излучение с Ni–фильтром, шаг 0.01°). Анализ структуры и микрорентгеноспектральный анализ проводили на аншлифах с помощью растрового электронного микроскопа Tescan Vega 3SBH с детектором Aztec X-Act (Oxford Instruments).
Теплопроводность образцов материалов определена методом лазерной вспышки на аппарате NETZSCH LFA 457 MicroFlash. Теплопроводность измеряли на дисках диаметром 12.5 мм.
Коэффициент линейного термического расширения материалов измеряли на приборе Shimadzu ТМА-60 при нагревании от комнатной температуры до 1000°C.
Плотность и пористость спеченных образцов определяли методом гидростатического взвешивания.
Твердость материалов измеряли методом Виккерса в соответствии с ГОСТ Р ИСО 6507-1 2007 на твердомере ПМТ-3 при нагрузке 1.96 Н (0.2 кг с) в течение 15 с. Для каждого образца измерение отпечатка пирамиды Виккерса проводили на различных участках 5–10 раз. Твердость высчитывали по формуле:
где P – приложенная нагрузка, Н; d – диагональ отпечатка, мкм.Трещиностойкость K1C измеряли по схеме Палмквиста при нагрузке 14.7 Н (1.5 кг с). Для каждого образца измерение проводили на различных участках 5–10 раз. Длину трещин измеряли по электронным микрофотографиям, и дальнейший расчет проводили согласно формуле [37]:
где P – нагрузка, Н; l – измеренная длина трещины от угла отпечатка, мкм.Модуль упругости измеряли на спеченных образцах на приборе неразрушающего акустического контроля ЗВУК-130 методом резонанса.
Предел прочности при поперечном изгибе определен по модели трехточечного изгиба на образцах в виде прямоугольных призм 5 × 5 мм, длиной 30 мм.
РЕЗУЛЬТАТЫ И ОБСУЖДЕНИЕ
Конечная температура спекания выбрана путем измерения усадки образцов. Значения объемной усадки составили более 40% для составов, содержащих менее 60 об. % карбида кремния (табл. 2). В области составов, содержащих от 15 до 40 об. % MoSi2 на спеченных образцах получена относительная плотность, превышающая расчетную, что обусловлено химическим взаимодействиям между компонентами с образованием новых фаз с большей плотностью, чем у исходных компонентов. С помощью РФА (состав 9, рис. 1) обнаружены фазы борида молибдена тетрагональной модификации (плотность 8.65 г/см3) и карбида циркония кубической модификации (6.73 г/см3). Аналогичные результаты зафиксированы для состава 14. Возможной причиной образования указанных компонентов, следы которых зафиксированы для образцов составов 4, 8, 9, 13, 14, может являться восстановление поверхностных оксидных слоев на частицах дисилицида молибдена в процессе совместной термообработки с диборидом циркония, который, в свою очередь, затрачивая бор на образование борида молибдена, вступает в реакцию с углеродом, источником которого наиболее вероятно является капсельный припас. Для материалов с преимущественным содержанием дисилицида молибдена, содержащих малые количества диборидного компонента (составы 1–3, табл. 1) с помощью РФА (рис. 1) установлено образование гексагонального Mo4.8Si3C0.6 с плотностью 7.9 г/см3, что может быть связано с дефицитом кремния в дисилициде молибдена, в связи с частичным окислением на стадиях помола и перемешивания, сопровождающимся образованием Mo5Si3 при повышенных температурах, и внедрением углерода с образованием фазы Новотного.
Таблица 2.
Плотность, пористость и усадка образцов материалов системы ZrB2–SiC–MoSi2 после спекания
№ | 1 | 2 (Е1) | 3 | 4 | 5 | 6 | 7 | 8 | 9 | 10 | 11 | 12 | 13 | 14 | 15 |
---|---|---|---|---|---|---|---|---|---|---|---|---|---|---|---|
ρкаж, ±0.1 г/см3 | 5.5 | 4.0 | 4.7 | 5.3 | 5.6 | 5.5 | 4.9 | 5.3 | 2.5 | 5.4 | 4.1 | 5.2 | 4.7 | 5.8 | 5.8 |
ρотн, ±1% | 93 | 71 | 86 | 80 | 82 | 83 | 89 | >99 | 65 | 95 | 93 | >99 | 97 | >99 | >99 |
Усадка об, ±2% | 45 | 35 | 43 | 42 | 43 | 44 | 43 | 46 | 17 | 45 | 41 | 46 | 45 | 48 | 43 |
Поткр, ±0.1% | 4.8 | 5.2 | 4.2 | 11.4 | 9.9 | 3.2 | 4.3 | 2.6 | 9.5 | 2.1 | 3.3 | 2.8 | 3.9 | 1.6 | 1.3 |
Побщ, ±2% | 8 | 22 | 15 | 24 | 21 | 16 | 9 | 7 | 29 | 19 | 12 | 4 | 6 | 1 | 3 |
Lср, ±0.5 мкм | 2.1 | 3.0 | 3.1 | 2.0 | 7.4 | 1.4 | 1.6 | 2.3 | 1.7 | 2.7 | 13.0 | 2.1 | 1.8 | 1.4 | 1.3 |
Результаты определения модуля упругости материалов (табл. 3) показывают его зависимость от общей пористости образцов, и, в меньшей степени, от содержания высокомодульного компонента – ZrB2. Однако для составов, содержащих большие количества диборида определены наиболее высокие величины модуля упругости (E), достигающие 75% от теоретической величины (составы 13 и 14). В отличие от них, образцы составов 10 и 11, также характеризующиеся высокой величиной относительной плотности, обладают заметно меньшими значениями относительного модуля упругости (Еотн), которые составляют 45 и 60% от расчетного, вероятно, это связано с образованием продуктов взаимодействия между фазами, о которых упоминалось выше. Наибольшую прочность при изгибе показали образцы, содержащие более 60 об. % ZrB2. Данные образцы характеризуются высокими значениями относительной плотности (>95%) и минимальными размерами зерен компонентов (менее 1 мкм у диборида циркония и менее 1.5 мкм у дисилицида молибдена), и минимальной общей пористостью, не превышающей 3–5%, при этом средний размер пор составляет 1.4–1.8 мкм (рис. 2).
Таблица 3.
Модуль упругости, прочность и твердость образцов материалов системы ZrB2–SiC–MoSi2
№ | 1 | 2 (Е1) | 3 | 4 | 5 | 6 | 7 | 8 | 9 | 10 | 11 | 12 | 13 | 14 | 15 |
---|---|---|---|---|---|---|---|---|---|---|---|---|---|---|---|
Е, ГПа ±5% | 308 | 252 | 219 | 177 | 267 | 266 | 261 | 198 | 266 | 269 | 293 | 266 | 361 | 345 | 320 |
σ, МПа ±10% | 140 | 220 | 230 | 90 | 180 | 250 | 180 | 160 | 320 | 180 | 270 | 410 | 460 | 300 | 350 |
HV, ±2 ГПа | 12 | 13 | 10 | - | 10 | 10 | 12 | 10 | 15 | 12 | 10 | 11 | 11 | 16 | 12 |
Рис. 2.
Микрофотографии образцов материалов системы ZrB2–SiC–MoSi2, соответствующие составам: 2 (а), 9 (б), 8 (в), 13 (г).
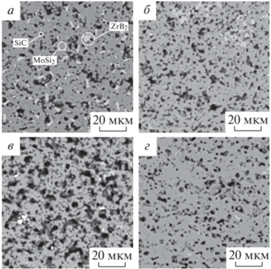
Увеличение концентрации диборида циркония в составах с преимущественным содержанием дисилицида молибдена повышает твердость материалов. Несмотря на то, что состав 8 содержит 60 об. % карбида кремния (наиболее твердого компонента), он продемонстрировал низкие показатели твердости, что связано с его небольшой относительной плотностью – 94%. Твердость составила 10 ГПа при величине К1С = 6.8 Мпа ⋅ м1/2. Наибольшие значения твердости по Виккерсу получены на материале состава 14, содержащем 70 об. % ZrB2, HV = 15.8 ГПа при К1С = 3.8 Мпа ⋅ м1/2 (рис. 3). Для материалов с преобладающей долей дисилицида молибдена (70–85%) твердость составила 11–13 ГПа при К1С от 4.0 до 4.3 Мпа ⋅ м1/2.
Определен размер зерен MoSi2 и ZrB2 в структуре спеченных при температурах 1750 и 1820°C материалов. Так, у составов, содержащих более 60 об. % MoSi2, наблюдается тенденция к росту зерен дисилицида молибдена и диборида циркония с увеличением температуры спекания. Однако количественная оценка затруднена, так как разница в результатах измерения находится в пределах погрешности метода.
С увеличением количества вводимого в состав карбида кремния, вследствие которого наблюдалось ухудшение спекаемости материалов, увеличивается также открытая и закрытая пористость. У образцов 4 и 8, содержащих более 60 об. % SiC, общая пористость превышает 20%, общая пористость для состава 11 – более 10%, общая пористость материала состава 13 не превышает 6%. Средний размер пор материалов этих составов – 2.0–2.3 мкм (табл. 2).
Изучение коэффициентов линейного термического расширения (КЛТР) керамик (рис. 4) подтвердило закономерное снижение КЛТР (ɑ) при уменьшении концентрации дисилицида молибдена в материале, приближаясь к справочным величинам, соответствующим значению КЛТР диборида циркония (4.7 × 10–6 К–1). Минимальным значением КЛТР характеризуется образец, содержащий 60 об. % карбида кремния –4.5 × 10–6 K–1.
Анализируя результаты измерения теплопроводности (рис. 5), можно выделить два основных фактора, влияющих на полученную опытным путем величину теплопроводности (λ) в порядке убывания их влияния: пористость, включая распределение пор по размерам; концентрация самого теплопроводящего компонента – SiC. При введении в материал 40–60 об. % карбида кремния, при получении материалов с относительной плотностью более 90%, его теплопроводность достигает λ ≥ 45 Вт/(м К). В случае низкой плотности (не более 65% от теоретической), при введении в состав материала 80 об. % карбида кремния, теплопроводность материала при комнатной температуре не превышает 40 Вт/(м К). Высокоплотные материалы с преимущественным содержанием дисилицида молибдена характеризуются λ = 30–40 Вт/(м К), обогащенные диборидом – 40–50 Вт/(м К).
ЗАКЛЮЧЕНИЕ
Исследованы образцы материалов в широком интервале концентраций компонентов в системе ZrB2–SiC–MoSi2, спеченные при температурах 1750 и 1820°C. На образцах проведены измерения комплекса механических и технических характеристик: прочность, модуль упругости, твердость по Виккерсу, КЛТР, теплопроводность.
При выбранных температурах спекания получена керамика с плотностью, близкой к теоретической при концентрации дисилицида молибдена более 85 об. % и диборида циркония от 30 до 70 об. %.
Существенного различия в размере зерен MoSi2 и ZrB2 структур керамик, спеченных при температурах 1750 и 1820°C, не отмечено – средний размер зерен составил 4–5 мкм. В исследованном температурном диапазоне увеличение концентрации карбида кремния привело к ухудшению спекаемости материалов, а также увеличению открытой и закрытой пористости. У образцов, содержащих более 60 об. % SiC, по причине недостаточной спекаемости, открытая пористость превысила 20%, а закрытая более 15%, тогда как у материала, содержащего преимущественно диборид циркония, общая пористость составила не более 10%. Средний размер пор у этих материалов не превышает 2.5 мкм.
Наибольшим пределом прочности при изгибе – 460 МПа характеризуется материал, содержащий 65 об. % ZrB2 и 20 об. % SiC. Тогда как максимальный модуль упругости (360 ГПа) получен у материала с преимущественным содержанием ZrB2 > 60 об. %.
Твердость материалов с увеличением концентрации диборида циркония повышается до 16 ГПа. С изменением концентрации и типа основного компонента материала возможно получить спеченные керамики, характеризующиеся КЛТР от 4.9 × 10–6 K–1 для материалов с преимущественным содержанием SiC, до 6.1 × 10–6 K–1 для материалов на основе MoSi2. Причем у материалов с преимущественным содержанием диборида циркония КЛТР находится в пределах 5.3–5.5 × 10–6 K–1.
На основе экспериментального исследования можно выделить два основных фактора, влияющие на теплопроводность (в порядке убывания их влияния): пористость, включая распределение пор по размерам и концентрация SiC, как самого теплопроводящего компонента. Высокоплотные материалы с преимущественным содержанием дисилицида молибдена характеризуются теплопроводностью λ = 30–40 Вт/(м К), обогащенные диборидом – 40–50 Вт/(м К).
Работа выполнена при финансовой поддержке гранта РНФ № 19-73-10180, с использованием оборудования инжинирингового центра СПбГТИ(ТУ).
Список литературы
Silva E.A.C., Kaufman M.J. Phase relations in the Mo–Si–C system relevant to the processing of MoSi2–SiC composites // Metallurgical and Materials Transactions A. 1994. T. 25. № 1. C. 5–15.
Орданьян С.С., Вихман С.В., Ларенцева С.А., Смирнов В.В. Строение разреза SiC–MoSi2 в системе Mo–Si–C // Огнеупоры и техническая керамика. 2006. № 11. С. 2–4.
Орданьян С.С., Булина Е.Н., Вихман С.В., Смирнов В.В. Взаимодействие в системе SiC–WSi2 // Огнеупоры и техническая керамика. 2007. № 2. С. 3–5.
Орданьян С.С., Вихман С.В., Булина Е.Н., Смирнов В.В. Взаимодействие в системе SiC–MeVSi2 // Огнеупоры и техническая керамика. 2008. № 5. С. 14–17.
Орданьян С.С. Закономерности взаимодействия в системах SiC–MeIV–VIB2 // Журн. прикладной химии. 1993. Т. 66. № 11. С. 2439–2444.
Орданьян С.С., Вихман С.В., Нагаева Ю.В., Овсепян А.О. О взаимодействии в системах MoSi2–MeIVB2 // Известия НАН РА и ГИУА. Серия ТН. 2011. Т. 64. № 1. С. 36–43.
Орданьян С.С., Вихман С.В., Нагаева Ю.В. Композиционные материалы WSi2–MeVB2 в системах W–Si–MeV–B // Новые огнеупоры. 2009. № 3. С. 41–44.
Meier S., Heinrich J.G. Processing–microstructure–properties relationships of MoSi2–SiC composites // J. European Ceramic Society. 2002. T. 22. № 13. C. 2357–2363.
Гнесин Б.А., Гнесин И.Б. Синтез фазы Новотного Mo4.8Si3C0.6 из смесей Mo5Si3 с углеродом // Неорганические материалы. 2015. Т. 51. № 10. С. 1073–1080.
Gnesin B.A., Gnesin I.B., Nekrasov A.N. The interaction of carbon with Mo5Si3 and W5Si3 silicides. Nowotny phase synthesis // Intermetallics. 2013. T. 41. C. 82–95.
Sciti D., Silvestroni L., Celotti G., Melandri C., Guicciardi S., Sintering and mechanical properties of ZrB2–TaSi2 and HfB2–TaSi2 ceramic composites // J. American Ceramic Society. 2008. T. 91. № 10. C. 3285–3291.
Sciti D., Guicciardi S., Bellosi A., Pezzotti G. Properties of a pressureless-sintered ZrB2–MoSi2 ceramic composite // J. American Ceramic Society. 2006. T. 89. № 7. C. 2320–2322.
Sciti D., Monteverde F., Guicciardi S., Pezzotti G., Bellosi A., Microstructure and mechanical properties of ZrB2–MoSi2 ceramic composites produced by different sintering techniques // Materials Science and Engineering: A. 2006. T. 434. № 1–2. C. 303–309.
Rezaie A., Fahrenholtz W.G., Hilmas G.E. Oxidation of zirconium diboride–silicon carbide at 1500°C at a low partial pressure of oxygen // J. American Ceramic Society. 2006. T. 89.,№ 10. C. 3240–3245.
Monteverde F., Bellosi A. The resistance to oxidation of an HfB2–SiC composite // J. European Ceramic Society. 2005. T. 25. № 7. C. 1025–1031.
Monteverde F., Bellosi A. Microstructure and properties of an HfB2-SiC composite for ultra high temperature applications // Advanced Engineering Materials. 2004. T. 6. № 5. C. 331–336.
Monteverde F. Ultra-high temperature HfB2–SiC ceramics consolidated by hot–pressing and spark plasma sintering // J. Alloys and Compounds. 2007. T. 428. № 1–2. C. 197–205.
Mallik M., Ray K.K., Mitra R. Oxidation behavior of hot pressed ZrB2–SiC and HfB2–SiC composites // J. European Ceramic Society. 2011. T. 31. № 1–2. C. 199–215.
Nguyen V.H., Delbari S.A., Asl M.S. Namini A.S., Kakroudig M.G., Azizian-Kalandaragh Y., Van Le Q., Mohammadi M, Shokouhimehrc M. Role of hot-pressing temperature on densification and microstructure of ZrB2–SiC ultrahigh temperature ceramics // International J. Refractory Metals and Hard Materials. 2020. T. 93. C. 105355.
Guo S.Q., Nishimura T., Mizuguchi T. Kagawa Y. Mechanical properties of hot–pressed ZrB2–MoSi2–SiC composites // J. European Ceramic Society. 2008. T. 28. № 9. C. 1891–1898.
Monteverde F. The addition of SiC particles into a MoSi2–doped ZrB2 matrix: effects on densification, microstructure and thermo-physical properties // Materials Chemistry and Physics. 2009. T. 113. № 2–3. C. 626–633.
Mashhadi M., Shambuli M., Safi S. Effect of MoSi2 addition and particle size of SiC on pressureless sintering behavior and mechanical properties of ZrB2–SiC–MoSi2 composites // J. Materials Research and Technology. 2016. T. 5. № 3. C. 200–205. 16.
He R., Tong Z., Zhang K., Fang D. Mechanical and electrical properties of MoSi2-based ceramics with various ZrB2–20 vol % SiC as additives for ultra-high temperature heating element // Ceramics International. 2018. T. 44. № 1. C. 1041–1045.
Yang Y., Li,M., Xu L., Xu J., Qian Y., Zuo J., Li T. Oxidation behaviours of ZrB2–SiC–MoSi2 composites at 1800°C in air with different pressures // Corrosion Science., 2019. T. 157. C. 87–97.
Ghadami S., Taheri-Nassaj E., Baharvandi H.R. Novel HfB2–SiC–MoSi2 composites by reactive spark plasma sintering // J. Alloys and Compounds. 2019. T. 809. C. 151705.
Ghadami S., Taheri–Nassaj E., Baharvandi H.R., Ghadami F. Effect of in situ VSi2 and SiC phases on the sintering behavior and the mechanical properties of HfB2-based composites // Scientific Reports. 2020. T. 10. № 1. C. 1–13.
Bai Y., Sun M., Li M., Fan S., Cheng L. Improved fracture toughness of laminated ZrB2–SiC–MoSi2 ceramics using SiC whisker // Ceramics International. 2018. T. 44. № 8. C. 8890–8897.
Potanin A.Y., Astapov A.N., Rupasov S.I., Vorotilo S., Kochetov N.A., Kovalev D.Y., Levashov E.A. Structure and properties of MoSi2–MeB2–SiC (Me= Zr. Hf) ceramics produced by combination of SHS and HP techniques // Ceramics International. 2020. T. 46. № 18. C. 28725–28734.
Орданьян С.С., Унрод В.И. Эвтектики в системах с участием тугоплавких соединений и их модели, спеченные композиции // Новые огнеупоры. 2005. № 7. С. 42–48.
Markov M.A., Krasikov A.V., Bykova A.D., Staritsyn M.V., Ordan’yan S.S., Vikhman S.V., Perevislov S.N. Preparation of MoSi2–SiC–ZrB2 Structural Ceramics by Free Sintering // Refractories and Industrial Ceramics. 2019. V. 60. № 4. P. 385–388. .
Perevislov S.N., Markov. M.A., Motailo E.S., Vikhman S.V., Titov D.D. Physical and mechanical properties of composite materials in the MoSia2–SiC–TiB2 system // IOP Conference Series: Materials Science and Engineering: 5. Moscow. 30 октября–01 ноября 2019 года. Moscow. 2020. P. 012067.
Fu Q.G., Jing J.Y., Tan B.Y., Yuan R.M., Zhuang L., Li L. Nanowire-toughened transition layer to improve the oxidation resistance of SiC–MoSi2–ZrB2 coating for C/C composites // Corrosion Science. 2016. T. 111. C. 259–266.
Wang P., Li H., Ren X., Yuan R., Hou X., Zhang Y. HfB2–SiC–MoSi2 oxidation resistance coating fabricated through in situ synthesis for SiC coated C/C composites // J. Alloys and Compounds., 2017. T. 722. C. 69–76.
Wang P., Li H., Yuan R., Xie W., Zhang Y. An oxidation and ablation protective WSi2–HfB2–SiC coating for SiC coated C/C composites at 1973 K and above // Corrosion Science. 2020. T. 177. C. 108 964.
Bezzi F., Burgio F., Fabbri P., Grilli S., Magnani G., Salernitano E., Scafè M. SiC/MoSi2 based coatings for Cf/C composites by two step pack cementation // J. European Ceramic Society. 2019. T. 39. № 1. C. 79–84.
Sinitsyn D.Y., Anikin V.N., Eremin S.A., Vanyushin V.O., Shvetsov A.A., Bardin N.G. Heat-Resistant Coatings of ZrB2–MoSi2–SiC on Carbon–Carbon Composite Materials for Aerospace Applications // Refractories and Industrial Ceramics. 2020. C. 1–7.
Nesmelov D.D., Novoselov E.S.., Lysenkov A.S., Vikhman S.V., Perevislov S.N. Hardness and fracture-toughness of hot-pressed LaB6–TiB2 ceramics // IOP Conference Series: Materials Science and Engineering: 5. Moscow. 30 октября–01 ноября 2019 года. Moscow. 2020. P. 012059. .
Дополнительные материалы отсутствуют.
Инструменты
Физика и химия стекла