Физика и химия стекла, 2022, T. 48, № 3, стр. 374-380
Особенности покрытия, модифицированного пористым стеклом
Т. А. Цыганова 1, 3, *, О. В. Рахимова 2
1 Институт химии силикатов им. И.В. Гребенщикова РАН
199034 Санкт-Петербург, наб. Макарова, 2, Россия
2 Санкт-Петербургский государственный электротехнический университет “ЛЭТИ”
им. В.И. Ульянова (Ленина)
197376 Санкт-Петербург, ул. Профессора Попова, 5, Россия
3 Санкт-Петербургский Научный центр РАН
199034 Санкт-Петербург, Университетская наб., 5, Россия
* E-mail: Tsyganova2@yandex.ru
Поступила в редакцию 19.07.21
После доработки 03.08.21
Принята к публикации 06.08.21
- EDN: YAZWUY
- DOI: 10.31857/S0132665121060330
Аннотация
В работе представлены результаты исследования эксплуатационных характеристик покрытия, образуемого “Грунт-эмалью по ржавчине 3 в 1” при добавлении в состав высококремнеземного пористого стекла в различных концентрациях. Введение пористых стекол обусловлено необходимостью регулирования влажности в современных жилых помещениях и понижению токсичности строительных материалов. Модифицирование покрытия привело к улучшению адгезионных свойств, укрывистости и вязкости. Полученные результаты открывают перспективы разработок в этом направлении, связанные с организацией эргономичного дома.
ВВЕДЕНИЕ
Высокие технические требования, предъявляемые в настоящее время к современным материалам, используемым в промышленности, медицине и экологии, влекут за собой необходимость разработки и изучения новых материалов с точки зрения их экобиологической безопасности. Если говорить о лакокрасочных материалах (ЛКМ), то, к сожалению, снизить их токсичность практически невозможно ввиду входящих в состав незаменимых, но токсичных, компонентов. Одним из путей решения данной проблемы является улучшение свойств получаемого покрытия путем введения в состав специальных добавок-модификаторов, способных улучшить прочностные показатели покрытия и таким образом снизить частоту контакта человека с вредными химическими соединениями [1]. Отсутствие широкого выбора модификаторов подтверждает актуальность их поиска.
Целью работы было исследование эксплуатационных характеристик покрытия, полученного на основе “Грунт-эмаль по ржавчине 3 в 1”, модифицированного порошком высококремнеземного пористого стекла (ПС). Грунт-эмаль по ржавчине прекращает развитие коррозии металла и является быстросохнущей, атмосферостойкой, влагостойкой, а также хорошо распыляемой. Она сочетает в себе свойства преобразователя ржавчины, антикоррозионного грунта и декоративной эмали. Образуемое ею покрытие устойчиво к воздействию атмосферных факторов, соленой воды, масла (ТУ 2313-045-32811438-2003). С другой стороны, в последнее время мезопористые материалы стали использоваться для контроля влажности и снижения энергопотребления [2, 3] благодаря своим физико-химическим свойствам, таким как высокая удельная поверхность, значительная пористость, структура пор, что увеличивает их способность контролировать влажность в окружающей среде. К числу таких материалов относится ПС, обладающее всеми вышеперечисленными свойствами [4]. В представляемой работе выбор высококремнеземного ПС в качестве модификатора обусловлен несколькими причинами. Прежде всего, это высокое содержание двуокиси кремния, которая широко используется в качестве наполнителя и пленок для защиты поверхности от коррозии [5–7]. Кроме того, недавние исследования авторов11 показали низкий или практически нулевой уровень токсичности высококремнеземных ПС. Стоит отметить, что в отличие от цеолитов и керамики, ПС можно изготовить любой формы (шарики, волокна, хлопья), что делает их более применимыми на практике. Так в [8] ПС, полученные на основе стекла Vicor, предлагается использовать для модифицирования штукатурного материала в организации микроклимата эргономичного дома.
ЭКСПЕРИМЕНТАЛЬНАЯ ЧАСТЬ
Объект исследования − “Грунт-эмаль по ржавчине 3 в 1” серого цвета производства ООО Новбытхим, качественный состав которой включает органические растворители (толуол, ксилол, ацетон), синтетические смолы (перхлорвиниловая, эпоксидная, нефтеполимерная), пластификатор (хлорпарафин), антикоррозионные пигменты (фосфат цинка, железооксидные). В качестве модификатора было выбрано высококремнеземное пористое стекло ПС 8Б состава 96.6SiO2·3.20B2O3·0.2Na2O (мол. %) [9] в виде порошка (размер частиц порошка 0.16–0.63 мкм), которое известно своими адсорбционными свойствами по отношению к парам воды и различным органическим растворителям [4]. Выбор модификатора обусловлен областью применения “Грунт-эмали по ржавчине 3 в 1”: металлические конструкции, эксплуатирующиеся в атмосферных условиях, в том числе и при высокой влажности воздуха. ПС добавлялось в “Грунт-эмаль по ржавчине 3 в 1” в количестве 0.5, 1.0 и 1.5 мас. %.
Для испытаний в качестве подложек для лакокрасочного покрытия использовались пластины, представленные в табл. 1.
Таблица 1.
Материал подложек
Материал подложки | Толщина, мм | Метод испытания покрытия |
---|---|---|
Стеклянные пластинки специального назначения по ТУ 21-0284461-058-90 | 1.2–1.8 | Определение твердости, блеска, прочности к истиранию |
Листы и ленты алюминиевые по ГОСТ 21631-76 и ГОСТ 13726-97 | 0.25–0.30 | Испытание на изгиб (эластичность) |
Сталь листовая марки 08кп и 08пс по ГОСТ 16523-97 и ГОСТ 9045-93 | 0.5–1.0 | Определение адгезии |
Получение лакокрасочного покрытия (ЛКП) осуществлялось согласно ГОСТ 8832-76.
В ходе экспериментов были исследованы следующие характеристики ЛКП: вязкость до и после термостатирования, блеск, адгезия, стойкость покрытия к царапанию, прочность к истиранию, твердость.
Определение вязкости образцов “Грунт-эмали по ржавчине 3 в 1”, модифицированных ПС, проводилось с помощью визкозиметра ВЗ-246 (сопло 4 мм) сразу после приготовления замесов на лабораторном перемешивающем устройстве IKA Eurostar 20 (время перемешивания 1 ч) и после термостатирования при 50°С в течение 168 ч с последующим помещением в среду атмосферного воздуха на 2 ч (ГОСТ 1583-89, ГОСТ 5689-79, ГОСТ 2060-2006).
Для определения блеска образцов “Грунт-эмали по ржавчине 3 в 1”, модифицированных ПС, использовался фотоэлектрический метод определения блеска с помощью фотоэлектрического блескомера ФБ-2, который заключается в измерении величины фототока, возбуждаемого в фотоприемнике под действием пучка света, отраженного от поверхности испытуемого ПК. Определение блеска выражается через количественную оценку с погрешностью не более ±4% (ГОСТ 896).
Определение адгезии проводили методом отрыва при температуре 23 ± 2°С и относительной влажности 50 ± 5% (ГОСТ 29317-92 (ИСО 3270-84)). Силу отрыва прикладывают в направлении, перпендикулярном к плоскости окрашенной поверхности, и увеличивают с равномерной скоростью, но не более 1 МПа/с, чтобы разрушение испытуемого образца произошло в течение 90 с (ГОСТ 32299-2013). Адгезия ПК $\delta $ методом отрыва рассчитывает по формуле:
где F – сила отрыва, кгс; d – диаметр основания, приклеиваемого к ПК, мм2.Стойкость покрытия к царапанию определялась методом нанесения царапин на испытуемое покрытие и последующей визуальной оценкой стойкости покрытия к механическому воздействию при температуре воздуха (23 ± 2)°С и относительной влажности (50 ± 5)% на механическом приборе Константа Ц2 со встроенной иглой (диаметр иглы 1 мм, длина царапин ≥60 мм, скорость нанесения царапин – 3–4 см/с). Оценка стойкости покрытия к царапанию выражается как минимальная нагрузка, необходимая для образования царапин (ISO 1518). Полученные результаты выражены через вес, действующий на индентор, при котором образуется нарушение покрытия до подложки.
Определения прочности лакокрасочных покрытий к истиранию проводилось с помощью устройства марки ИС-2 за 1 и 7 суток. Прочность ЛКП определяется минимальным числом полных оборотов пластинки, при котором под воздействием повреждающего элемента и расположенного на нем груза, происходит разрушение пленки покрытия. Прочность покрытия к истиранию (потеря массы) в граммах вычисляют по формуле:
где $K$ поправочный коэффициент шлифовальной шкурки; ${{m}_{1}}$ масса образца до истирания, г; ${{m}_{2}}$ масса образца после истирания, г.Поправочный коэффициент вычисляют по формуле:
где $m_{i}^{K}$ потеря массы контрольной цинковой пластинки, истертой шлифовальной шкуркой, г.За потерю массы контрольной цинковой пластинки принимают среднее значение не менее чем из девяти параллельных определений, при этом каждое определение весового износа вычисляют по формуле:
где $m_{1}^{K}$ масса контрольной цинковой пластины до истирания, г; $m_{2}^{K}$ масса контрольной цинковой пластины после истирания, г.Измерение твердости для каждого образца проводилось на маятниковом приборе марки М-3 на 1 и 7 сут после нанесения ЛКМ на пластины для испытаний. Сущность метода заключается в определении времени (числа колебаний), в течение которого амплитуда затухающих колебаний маятника, помещенного на ЛКП, уменьшается на заданную величину (ГОСТ 5233-89). Величину твердости Н в условных единицах вычисляют по следующей формуле:
где t1 – время затухания колебаний маятника от 6° до 2° на испытуемом лакокрасочном покрытии, с; t – время затухания колебаний маятника от 6° до 2° на стеклянной пластинке (“стеклянное число”).РЕЗУЛЬТАТЫ И ОБСУЖДЕНИЕ
На рис. 1–4 представлены результаты проведенных экспериментов. Величина адгезии была определена методом отрыва через 1 и 7 сут после нанесения на металлическую подложку и выражена как сила отрыва. Из полученных результатов следует, что добавление ПС в эмаль незначительно повышает адгезионные свойства покрытия после тестирования через 7 сут при содержании ПС в смеси 1.5 мас. % (на 3%) (рис. 1). Низкий показатель адгезии для 1 сут во всем диапазоне содержания ПС (0.5–0.15 мас. %), скорее всего, связан с коротким сроком выдерживания смеси, которая не успела достаточно прочно “схватиться” с поверхностью подложки.
Рис. 2.
Величина стойкости к царапанью (горизонтальные линии – показатель стойкости к царапанью для покрытия без ПС).
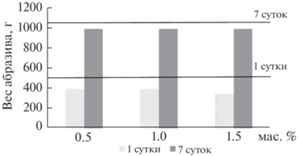
Рис. 3.
Величина износостойкости (горизонтальные линии – показатель износостойкости для покрытия без ПС).
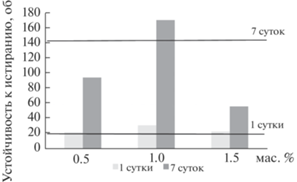
В то же время, показатели стойкости покрытия к царапанью (рис. 2) не демонстрируют явные преимущества добавки ПС в смесь по сравнению с исходной для любого времени выдержки.
Тестирование на износостойкость и укрывистость показало корреляцию результатов между этими свойствами и наличие максимума при содержании ПС 1.0 мас. %. В то же время, добавление ПС в смесь не оказало существенного влияния на износостойкость по сравнению с чистой эмалью, и лишь при содержании ПС 1.0 мас. % укрывистость увеличиласть в 2 раза.
В табл. 2 приведены некоторые другие характеристики покрытия с ПС. При оценке блеска отмечено, что все образцы были высокоэластичные, поскольку при изгибе на цилиндре наименьшего диаметра (1 мм) растрескивания поверхности эмали не наблюдалось (табл. 2).
Таблица 2.
Эксплуатационные характеристики покрытия с ПС
Характеристика | Время выдержки |
ПС 8Б | Исходное ЛКМ (ТУ 2313-045-32811438-2003) | ||
---|---|---|---|---|---|
количество, мас. % | |||||
0.5 | 1.0 | 1.5 | |||
Вязкость до термостатирования, мм2/с | 90 | 91 | 117 | Не менее 60 | |
Вязкость после термостат., мм2/с | 114 | 100 | 155 | ||
Твердость, у.е. | 1 сут | 0.21 | 0.24 | 0.16 | Не менее 0.3 |
7 сут | 0.34 | 0.34 | 0.30 | ||
Блеск, % | 10.8 | 8.1 | 6.6 | Матовая (4-19) (в соответствии с ГОСТ 9.032-74) |
Исследование устойчивости покрытий к воздействию повышенной температуры и влажности представлены в табл. 3. Для всего диапазона приложенных циклов от 3 до 14 характерны следы коррозии по торцам пластин (≈10%). С увеличением количества циклов наблюдается рост коррозии поверхности до 50%.
Таблица 3.
Результаты испытания ЛКП к воздействию повышенной температуры и влажности
Содержание ПС в покрытии, мас. % |
Кол-во циклов | Внешний вид покрытий после испытаний |
---|---|---|
0.5 | 3 | Без изменений |
8 | Следы коррозии по краям (торцам) пластин – ≈10% | |
14 | Следы коррозии по краям (торцам) пластин – ≈50% | |
1.0 | 3 | Без изменений |
8 | Следы коррозии по краям (торцам) пластин – ≈10% | |
14 | Следы коррозии на поверхности пластин – ≈10% + Следы коррозии по краям (торцам) пластин – ≈25% | |
1.5 | 3 | Без изменений |
8 | Следы коррозии по краям (торцам) пластин – ≈ 10% | |
14 | Следы коррозии на поверхности пластин – ≈10% + Следы коррозии по краям (торцам) пластин – ≈50% |
ЗАКЛЮЧЕНИЕ
Установлено, что при введении в “Грунт-эмаль по ржавчине 3 в 1” порошка высококремнеземного ПС улучшились некоторые эксплуатационные характеристики получаемого покрытия, а именно адгезионные свойства, укрывистость, вязкость. Полученные данные дают основание для продолжения исследования для улучшения перечисленных характеристик наряду с другими (устойчивость к царапанию, к истиранию и т.д.).
Синтез пористых стекол был проведен в рамках госзадания по Программе фундаментальных научных исследований государственных академий наук (на 2019/2021 г. № АААА-А19-119022290087-1) при поддержке Минобрнауки РФ.
Авторы благодарят генерального директора Ю.Э. Зевацкого и главного технолога И.В. Кочурова АО Новбытхим за предоставленную возможность провести исследования на базе научных подразделений организации.
Авторы заявляют об отсутствии конфликта интересов, требующего раскрытия в данной статье.
Список литературы
Ильина М.А., Машляковский Л.Н., Дринберг А.С., Хомко Е.В., Гарабаджиу А.В. Кремнийсодержащие эпоксидные композиционные материалы и их применение в технологии судовых покрытий // Журн. прикладной химии. 2019. Т. 92. Вып. 4. С. 491–503.
Vu Dinh-Hieu, Wang Kuen-Sheng, Nam Bui Xuan, Bac Bui Hoang, Chu Tien-Chun Preparation of humidity-controlling porous ceramics from volcanic ash and waste glass // Ceramics International. 2011. V. 37. № 7. P. 2845–2853.
Kimura T., Suzuki M., Maeda M., Tomura S. Water adsorption behavior of ordered mesoporous silicas modified with an organosilane composed of hydrophobic alkyl chain and hydrophilic polyethylene oxide groups // Microporous and Mesoporous Materials. 2006. V. 95. P. 213–219.
Мазурин О.В., Роскова Г.П., Аверьянов В.И., Антропова Т.В. Двухфазные стекла: структура, свойства, применение / Под ред. Б.Г. Варшала. Л.: Наука. 1991. 276 с.
Pourhashem S., Vaezi M.R., Rashidi A. Investigating the effect of SiO2 – graphene oxide hybrid as inorganic nanofiller on corrosion protection properties of epoxy coatings // Surface & Coatings Technology. 2017. № 311. P. 282–294.
Islam M., Azhar M.R., Fredj N., Burleigh T.D., Oloyede O.R. Almajid A.A. Influence of SiO2 nanoparticles on hardness and corrosion resistance of electroless Ni–P coatings // Surface & Coatings Technology. 2015. № 261. P. 141–148.
Ray S.S., Okamoto M. Polymer/layered silicate nanocomposites: a review from preparation to processing // Progress in Polymer Science. 2003. V. 28. № 11. P. 1539–1641.
Somorowksy F. Comfortable climate indoors with porous glass // Fraunhofer-Presse. Research news. 2014. 8. URL: https://ceramics.org/ceramic-tech-today/porous-glass-flakes-added-to-plaster-help-control-humidity-heating-and-cooling-costs (дата обращения 06.04.2021).
Крейсберг В.А., Антропова Т.В., Калинина С.В. Влияние состава и условий синтеза пористых стекол на их микро- и мезопористую структуры // Физика и химия стекла. 2014. Т. 40. № 5. С. 664–678.
Дополнительные материалы отсутствуют.
Инструменты
Физика и химия стекла