Физика и химия стекла, 2022, T. 48, № 5, стр. 616-624
Исследование возможностей синтеза вспененных геополимерных материалов на основе золошлаковых отходов ТЭЦ Арктической зоны РФ
Е. А. Яценко 1, *, Б. М. Гольцман 1, Ю. В. Новиков 1, В. М. Курдашов 1, Л. В. Климова 1
1 Южно-Российский государственный политехнический университет (НПИ) им. М.И. Платова
346428 Ростовская обл., Новочеркасск, ул. Просвещения, 132, Россия
* E-mail: e_yatsenko@mail.ru
Поступила в редакцию 09.12.2021
После доработки 27.04.2022
Принята к публикации 07.06.2022
- EDN: XHZIYL
- DOI: 10.31857/S0132665121100620
Аннотация
Рассмотрена возможность синтеза стеклокристаллических геополимерных материалов на основе золошлаковых отходов, образованных при сгорании угольного топлива на электростанциях. Разработаны составы шихт, проведен синтез геополимерных материалов. Проанализирована плотность и равномерность пористой структуры полученных образцов, выбраны вещества-порообразователи, оказывающие наибольшую вспенивающую активность, подобрано оптимальное количество щелочного активатора для синтеза геополимеров. Исследован фазовый состав полученных образцов.
ВВЕДЕНИЕ
На угольных электростанциях при сжигании угольного топлива образуется большое количество золошлаковых отходов (ЗШО), которые являются минеральной несгораемой частью угля, представляющей собой смесь золы-уноса и шлаковых отходов. Ежегодно в Российской Федерации образуется около 22 млн т ЗШО, а суммарное количество угольных отходов по разным оценкам составляет от 1.4 до 1.8 млрд т, располагающихся на территориях площадью более 20 тыс. кв. км [1, 2]. В настоящее время в РФ утилизируется (перерабатывается для дальнейшего использования в хозяйственной деятельности) не более 10–12% таких отходов [3]. Основным потребителем ЗШО является цементная промышленность, однако химический и фазовый состав позволяет использовать их в различных отраслях производства.
Геополимеры – это новый класс материалов, представляющих собой трехмерные стеклокристаллические алюмосиликатные материалы, состоящие из последовательностей тетраэдров [SiO4] и [AlO4], соединенных мостиковыми кислородами, где положительные ионы (Na+, K+, Li+, Ca2+ и др.) уравновешивают отрицательный заряд алюминий-кислородного тетраэдра [AlO4], обусловленный нескомпенсированностью зарядов кислорода О2– и алюминия Al3+ в четверной координации. При взаимодействии алюмосиликатных материалов с сильнощелочной средой протекают процессы гидролиза, олигомеризации, полимеризации и конденсации. Новообразованный полимерный гель связывает между собой непрореагировавшие или частично прореагировавшие частицы алюмосиликатов.
Геополимерные материалы обладают долговечностью, экологичностью, устойчивостью к воздействию тяжелых металлов, которые становятся частью геополимерной матрицы без ее деструкции [4]. Геополимеры нашли применение в строительстве, в качестве исходного материала для плит перекрытия, реставрации архитектурных сооружений [5]. Также имеются исследования [6, 7] которые свидетельствуют о высокой морозостойкости (150 циклов заморозки–оттаивания) геополимеров.
Осуществить производство геополимерных материалов можно как с применением природного сырья (магматические горные породы, метакаолинит, песок) так и сырья техногенного (стеклоотходы, в том числе свинец-содержащие, отходы переработки алюминиевого и сталеплавильного производства, отходы бокситов и т.д.) происхождения [8–11]. Для этих целей также весьма целесообразно применение ЗШО, так как последние содержат в своем составе значительные количества стекловидных алюмосиликатных фаз и обладают высокой дисперсностью [12]. Также этот процесс позволит превратить значительный объем отходов в полезный продукт.
Наиболее перспективными являются пористые геополимерные материалы, получаемые путем вспенивания геополимерной смеси добавками-порообразователями (вспенивающими агентами). Благодаря своей дешевизне, простоте технологического оформления процесса производства, высокой термической и химической стабильности, вспененные геополимеры являются одними из самых многообещающих неорганических композитных материалов [13–16]. Кроме того, они обладают низкой плотностью – менее 1000 кг/м3 и, как следствие, низкой теплопроводностью, что позволяет в перспективе использовать их в качестве недорогих теплоизоляционных материалов.
Наиболее технологичным методом вспенивания является химическое вспенивание с применением различных вспенивающих добавок (пероксид водорода, алюминиевый порошок), применение которых ведет к активному пенообразованию. С экономической точки зрения целесообразным является синтез геополимеров по низкотемпературной технологии, при температуре менее 100°С. Таким образом, целью данной работы является рассмотрение возможности получения геополимерных материалов на основе золошлаковых отходов от сжигания угля по низкотемпературной технологии.
ЭКСПЕРИМЕНТАЛЬНАЯ ЧАСТЬ
Для исследования было разработано две серии составов. В серии 1 основным сырьем был золошлак Апатитской ТЭЦ, в серии 2 – золошлак Северодвинской ТЭЦ-1. Истинную плотность золошлаков определяли пикнометрическим методом, для ЗШО Северодвинской ТЭЦ-1 она составляет 2034 кг/м3, для ЗШО Апатитской ТЭЦ – 1832 кг/м3. Химический состав применяемых сырьевых материалов, полученный с помощью рентгеноспектрального флуоресцентного анализа, приведен в табл. 1.
Таблица 1.
Химический состав применяемых сырьевых материалов
Источник ЗШО | Химический состав*, мас. % | ||||||||||
---|---|---|---|---|---|---|---|---|---|---|---|
SiO2 | Al2O3 | Fe2O3 | CaO | MgO | SO3 | TiO2 | K2O | Na2O | P2O5 | ППП | |
Апатитская ТЭЦ | 52.39 | 22.15 | 7.73 | 3.59 | 2.63 | 0.37 | 1.05 | 1.94 | 0.78 | 0.36 | 6.05 |
Северодвинская ТЭЦ-1 | 60.75 | 17.67 | 5.93 | 2.07 | 2.71 | 0.32 | 0.82 | 2.29 | 3.54 | 0.21 | 2.29 |
Жидкое стекло | 29.2 | 0.61 | 0.1 | 0.2 | – | 0.11 | – | – | 14.26 | – | 55.52 |
Основное сырье подвергалось помолу до размера частиц менее 250 мкм [17, 18]. Смешение компонентов осуществлялось согласно табл. 2 в следующей последовательности: в отдельной емкости смешивали твердый гидроксид натрия и воду до получения 12 М раствора, к которому далее доливали раствор силиката натрия (жидкое стекло), химический состав которого представлен в табл. 1, и перемешивали в течение 10 мин. Полученную смесь порциями вливали в подготовленный порошок измельченного сырья и перемешивали в течение 30 мин. К смеси добавляли порообразователь (порошок алюминия или 30% раствор пероксида водорода) и снова тщательно перемешивали. Полученную смесь заливали в цилиндрические формы диаметром 40 и высотой 40 мм. После выдержки в течение 24 ч образцы извлекали из форм и оставляли при комнатной температуре на 14 сут. После выдержки была исследована плотность образцов.
Таблица 2.
Пилотные составы геополимеров на основе ЗШО ТЭЦ Арктической зоны
№ | Содержание компонента, мас. % | Плотность кг/м3 | ||||
---|---|---|---|---|---|---|
ЗШО | NaOH (сухой) | жидкое стекло | пероксид водорода (сверх 100) | порошок Al (сверх 100) | ||
Северодвинская ТЭЦ-1 | ||||||
П1 | 73 | 2 | 25 | – | – | 1760 |
П2 | 73 | 2 | 25 | 0.4 | – | 1500 |
П3 | 73 | 2 | 25 | – | 0.1 | 1180 |
Апатитская ТЭЦ | ||||||
П1 | 73 | 2 | 25 | – | – | 1220 |
П2 | 73 | 2 | 25 | 0.4 | – | 1190 |
П3 | 73 | 2 | 25 | – | 0.1 | 1190 |
Линейные размеры цилиндрических образцов после отверждения определяли штангенциркулем с точностью ±0.1 мм. Массу образцов измеряли с точностью ±0.01 г. Плотность образцов d, кг/м3, определяли по формуле (1):
где m – масса образца, г, r – радиус основания цилиндрического образца, см, h – высота цилиндрического образца, см.Фазовый состав синтезированных образцов определяли с помощью порошкового рентгенофазового анализа (XRD). Образцы были измельчены и исследованы с помощью рентгеновского дифрактометра ARLX’TRA (Thermo Fisher Scientific, США). Использовано характерное излучение медного анода (длины волн CuKα1 1.5406 Å, CuKα2 1.5444 Å). Условия съемки: 35 кВ–30 мА. Интерпретация данных осуществлялась с использованием программного комплекса Crystallographica Search-Match Version 3 базы данных ICDD PDF 2 (Международный центр дифракционных данных).
ЭКСПЕРИМЕНТАЛЬНЫЕ РЕЗУЛЬТАТЫ И ИХ ОБСУЖДЕНИЕ
Были рассмотрены процессы структурообразования пористых геополимерных материалов с введением порообразующих добавок. Составы и результаты исследований представлены в табл. 2, а их структура на рис. 1.
Рис. 1.
Структура образцов геополимеров. С – золошлак Северодвинской ТЭЦ-1, А – золошлак Апатитской ТЭЦ.
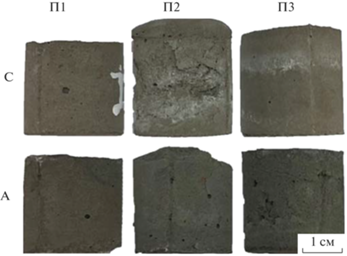
Исходя из результатов видно, что полученные образцы геополимеров обладают меньшей плотностью в сравнении с исходными сырьевыми материалами. Динамика вспенивания показала, что для образцов геополимеров на основе ЗШО Северодвинской ТЭЦ-1, лучшую порообразующую активность проявил порошок алюминия, пероксид водорода показал худший результат. Для образцов геополимеров на основе ЗШО Апатитской ТЭЦ порообразующая активность порошка алюминия и пероксида водорода показала одинаковый результат, так как плотность полученных образцов идентична.
Составы П1, П2, П3 на основе ЗШО Северодвинской ТЭЦ-1 не обладают развитой пористой структурой. Композиция П1 обладает наибольшей плотностью, так как в ее состав не вводился порообразователь, плотность композиции П3 наименьшая из исследуемых, что свидетельствует о наибольшей порообразующей активности алюминиевой пудры в данном случае.
Составы П1, П2, П3 на основе ЗШО Апатитской ТЭЦ также не обладают развитой пористой структурой. Все три образца имеют относительно близкую плотность и структуру, что свидетельствует в данном случае о низкой порообразующей активности как алюминиевой пудры, так и раствора пероксида водорода.
Механизм вспенивания исследованных смесей можно описать следующим образом. При смешивании силикатного сырья с раствором гидроксида натрия протекает реакция, описываемая схемой (2), в результате которой образуются щелочные гидроксиликаты. При дальнейшем нагреве из гидроксиликатов и жидкого стекла выделяется химически связанная вода, пары которой обеспечивают образование пористой структуры. Дополнительное введение раствора пероксида водорода ведут к его разложению по реакции (3). Введение порошка алюминия в щелочную среду ведет к образованию комплексных алюминатов и выделению газообразного водорода по реакции (4).
(3)
${\text{2}}{{{\text{H}}}_{{\text{2}}}}{{{\text{O}}}_{{\text{2}}}} \to 2{{{\text{H}}}_{{\text{2}}}}{\text{O}} + {{{\text{O}}}_{2}} \uparrow ,$(4)
${\text{2Al}} + {\text{2NaOH}} + 6{{{\text{H}}}_{{\text{2}}}}{\text{O}} \to 2{\text{Na}}\left[ {{\text{Al}}{{{\left( {{\text{OH}}} \right)}}_{{\text{4}}}}} \right] + 3{{{\text{H}}}_{2}}{\kern 1pt} \uparrow .$Интенсивность вспенивания синтезированных образцов была недостаточной, в связи с чем было принято решение об увеличении количества порообразователяи щелочного активатора, а также введении поверхностно-активного вещества – стеарата натрия, выполняющего функцию стабилизатора пены.
Кроме того, из полученных результатов видно, что образцы геополимеров на основе ЗШО Северодвинской ТЭЦ-1 проявили лучшую стабильность. Образцы на основе ЗШО Апатитской ТЭЦ обладали худшими эксплуатационными свойствами, особенно, механической прочностью. Данный фактор, вероятно, связан с недостаточным содержанием SiO2 в составе золошлака (на 8.36% меньше) и смещением соотношения Si/Na и Si/Al [19].
Дальнейшие исследования по подбору количества щелочного активатора были проведены с использованием ЗШО Северодвинской ТЭЦ-1. Модифицированные шихтовые составы пористых геополимеров приведены в табл. 3. Структура синтезированных образцов геополимеров приведена на рис. 2. Изменение плотности образцов геополимеров в зависимости от состава приведено на рис. 3.
Таблица 3.
Модифицированные шихтовые составы геополимеров
Номер состава | Содержание, мас. % | ||
---|---|---|---|
ЗШО | Щелочной активатор (“Жидкое стекло : NaOH : вода” = 25 : 2 : 4) |
Порообразователь (Al или Н2О2) | |
1 | 100 | 35 | 3 |
2 | 100 | 60 | 3 |
3 | 100 | 85 | 3 |
Рис. 2.
Внутренняя структура синтезированных образцов на основе ЗШО Северодвинской ТЭЦ-1. А – порообразователь Al, Н – порообразователь Н2О2, s – добавка 1 мас. % стеарата натрия.
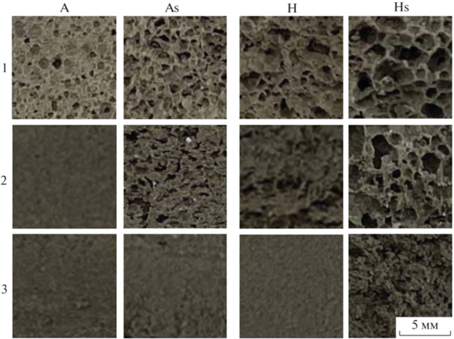
Исследования модифицированных шихтовых составов показали, что оптимальное количество щелочного активатора составляет 35%, т.е. составы серии 1. При введении 60 и 85% щелочного активатора геополимерная суспензия получается жидкой, что отрицательно сказывается на образовании пористой структуры образцов, т. к. происходит оседание образовавшейся пены. Наибольшее влияние на вспенивание оказал раствор пероксида водорода, порошок алюминия проявил меньшую вспенивающую активность. Добавка стабилизатора пены – стеарата натрия оказала положительное влияние на порообразование геополимеров, которое заключается в возрастании стабильности структуры пены, в которой истечение междупленочной жидкости в определенный момент прекращается, в связи с чем пенный каркас образца может сохраняться более длительное время [20]. Размер пор в образце состава А составляет 0.7–1.2 мм. Размер пор в образце состава Аs составляет 1–1.5 мм. Размер пор в образце состава H составляет 1–2.5 мм. Размер пор в образце состава Hs составляет 2–4 мм, они неправильной формы. Во всех составах поры распределены по всему объему образца геополимера. Оптимальным является состав H, так как он обладает наименьшей плотностью и не требует добавки стабилизатора пены стеарата натрия, что удешевляет получение геополимера. Данный состав обладает прочностью при сжатии 0.65 МПа, что соответствует требованиям СП 313.1325800.2017 “Дороги автомобильные в районах вечной мерзлоты. Правила проектирования и строительства” в части требований к прочности на сжатие материалов для теплоизоляционного слоя – не менее 0.4 МПа.
Далее для состава H был выполнен рентгенофазовый анализ. На рис. 4 приведена рентгенограмма ЗШО Северодвинской ТЭЦ-1 и полученного на его основе геополимера. Из рисунка видно, что интенсивность кристаллических пиков в синтезированном геополимере ниже, чем в ЗШО Северодвинской ТЭЦ-1 в 1.5 раза. Это указывает на образование аморфной фазы в образце. Основной кристаллической фазой является SiO2 в форме кварца и тридимита. Гало в интервале 20°–30° подтверждает наличие существенного объема аморфной фазы. Таким образом, и исходный золошлак, и полученный геополимер представляют собой стеклокристаллический материал с преобладанием аморфной фазы и растворенными в ней кристаллами SiO2 (ICCD PDF# 82-0512) и анортита (ICCD PDF# 41–1486).
Рис. 4.
Рентгенограмма ЗШО и геополимера на его основе расшифровка кристаллов: 1 – геополимер; 2 – ЗШО; ⚪ – кварц/тридимит (SiO2); □ – анортит (CaAl2Si2O8).
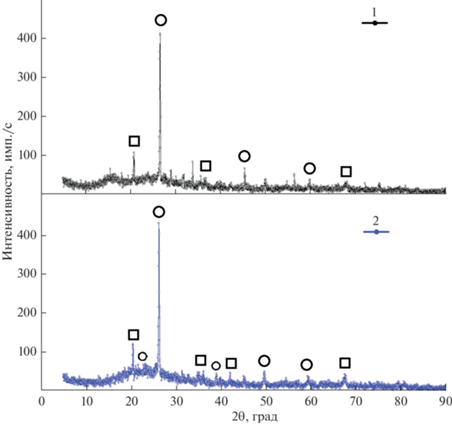
Синтезированные пористые геополимерные материалы на основе золошлаковых отходов угольной генерации могут найти применение при производстве широкого спектра изделий от гранул до сложных фасонных изделий. Данный вид материалов может быть использован в строительной отрасли для изготовления легкой огнестойкой изоляции внутренних перекрытий и ограждающих конструкций, а также при строительстве дорожного полотна.
ЗАКЛЮЧЕНИЕ
Таким образом, была установлена возможность синтеза стеклокристаллических геополимерных материалов на основе золошлаковых отходов угольных электростанций Арктической зоны РФ. Установлено, что наибольшую стабильность проявили образцы геополимеров на основе ЗШО Северодвинской ТЭЦ-1. Образцы на основе ЗШО Апатитской ТЭЦ обладали худшими эксплуатационными свойствами, что, вероятно, связано с недостаточным содержанием SiO2 в составе золошлака (на 8.36% меньше) и смещением соотношения Si/Na и Si/Al.
Установлено оптимальное содержание щелочного активатора – 35%, подобран порообразователь – пероксид водорода, проявивший лучшую вспенивающую активность, установлено стабилизирующее влияние добавки ПАВ. Проведен синтез геополимеров и исследование их пористой структуры, в ходе которой подобран оптимальный шихтовый состав. С помощью рентгенофазового анализа установлено существенное наличие аморфной фазы в образце геополимера, с растворенными в нем кристаллами SiO2 и анортита. Показано соответствие полученного материала требованиям к прочности на сжатие материалов для теплоизоляционного слоя дорожного полотна в районах вечной мерзлоты.
Работа выполнена в ЮРГПУ (НПИ) при финансовой поддержке Российского научного фонда, Соглашение № 21-19-00203 “Эффективные температуроотверждаемые экогеополимеры для дорожного строительства в условиях Арктической зоны Российской Федерации на основе отходов сжигания твердых топлив на местных ТЭЦ” (руководитель – Е.А. Яценко).
Список литературы
О состоянии и об охране окружающей среды Российской Федерации в 2020 году. Государственный доклад. М.: Минприроды России; МГУ им. М.В. Ломоносова, 2021. 1000 с.
Пичугин Е.А. Аналитический обзор накопленного в российской федерации опыта вовлечения в хозяйственный оборот золошлаковых отходов теплоэлектростанций // Проблемы региональной экологии. 2019. № 4. С. 77–87.
Yatsenko E.A., Goltsman B.M., Parshukov V.I. Analysis of suitability of TPP ash-slag waste as materials for hydrogen fuel storage // International J. Hydrogen Energy. 2021.
Davidovits J. Geopolymer chemistry and applications. 3rd edition. France, Saint-Quentin: Institute Geopolymer, 2011. 614 p.
Дудников А.Г., Реджани А. Геополимерный бетон и его применение // Строительные материалы, оборудование, технологии XXI в. 2018. № 1–2. С. 38–45.
Steinerova M. Mechanical properties of geopolymer mortars in relation to their porous structure // Ceramics – Silikáty. 2011. V. 55(4). P. 362–372.
Provis J.L., van Deventer J.S.J. Geopolymers Structure, processing, properties and industrial applications, Woodhead Publishing, 2009. 464 p.
Bai C., Colombo P. Processing, properties and applications of highly porous geopolymers: A review // Ceramics International. 2018. V. 44. P. 16103–16118.
Krishna R.S., Shaikh F., Mishra J., Lazorenko G., Kasprzhitskii A. Mine tailings-based geopolymers: Properties, applications and industrial prospects // Ceramics International. 2021. V. 47(13). P. 178 26–17 843.
Giro-Paloma J., Maldonado-Alameda A., Formosa J., Barbieri L., Chimenos J.M., Lancellotti I. Geopolymers based on the valorization of Municipal Solid Waste Incineration residues // IOP Conference Series: Materials Science and Engineering. 2017. V. 251(1). 012125. P. 1–11.
Bosnik V.B., Vaisman Ya.I., Ketov A.A., Krasnovskikh M.P., Rudakova L.V. Promising areas for producing bitumen-like materials based on synthetic polymers waste // Ecology and Industry of Russia. 2020. V. 24(5). P. 34–39.
Ahmed M.F., Nuruddin M.F., Shafiq N. Compressive Strength and Workability Characteristics of Low-Calcium Fly ash-based Self-Compacting Geopolymer Concrete // Intern. J. Civil and Environmental Engineering. 2011. № 3:2. P. 72–78.
Novais R.M., Pullar R.C., Labrincha J.A. Geopolymer foams: An overview of recent advancements // Progress in Materials Science. 2020. V. 109. P. 100621.
Łach M. Geopolymer Foams – Will They Ever Become a Viable Alternative to Popular Insulation Materials – A Critical Opinion // Materials. 2021. V. 14(13). P. 3568.
Zhang X. et al. Porous geopolymer composites: A review. // Composites Part A: Applied Science and Manufacturing. 2021. V. 150. P. 106629.
Pasupathy K., Ramakrishnan S., Sanjayan J. Enhancing the chemical foaming process using superplasticizer in aerated geopolymer concrete // Construction and Building Materials. 2022. V. 324. P. 126 535.
Yatsenko E.A., Goltsman B.M., Smolii V.A., Kosarev A.S. Foamed slag glass – Eco-friendly insulating material based on slag waste // 2015 IEEE 15th International Conference on Environment and Electrical Engineering, EEEIC 2015 – Conference Proceedings. 2015. P. 819–823.
Yatsenko E.A., Gol’tsman B.M., Smolii V.A., Gol’tsman N.S., Yatsenko L.A. Study on the Possibility of Applying Organic Compounds as Pore-Forming Agents for the Synthesis of Foam Glass // Glass Physics and Chemistry. 2019. V. 45(2). P. 138–142.
Zhao J., Tong L., Li D. et al. Eco-friendly geopolymer materials: A review of performance improvement, potential application and sustainability assessment // J. Cleaner Production. 2021. V. 307. P. 127 085.
Самошина Е.Н., Самошин А.П., Шитова И.Ю., Махамбетова К.Н. Исследование влияния стабилизирующих добавок на свойства пены при изготовлении пенокерамобетонов // Современные проблемы науки и образования. 2015. № 1. С. 145.
Дополнительные материалы отсутствуют.
Инструменты
Физика и химия стекла