Физика и химия стекла, 2022, T. 48, № 5, стр. 539-554
Исследование качественных характеристик марганецсодержащих фосфатных и борофосфатных стекол
Е. А. Беланова 1, *, М. Б. Ремизов 1, А. Ю. Чеснокова 1, П. В. Козлов 1, 2, Е. С. Шабурова 1
1 Производственное объединение “Маяк”
456783 Озерск, пр. Ленина, 30, Россия
2 Озерский технологический институт НИЯУ МИФИ
456783 Озерск, пр. Победы, 48, Россия
* E-mail: belanova_ea@mail.ru
Поступила в редакцию 17.12.2021
После доработки 23.05.2022
Принята к публикации 07.06.2022
- EDN: TAXVGL
- DOI: 10.31857/S0132665121100784
Аннотация
Проведены исследования свойств марганецсодержащих фосфатных и борофосфатных стекол: температура варки, вязкость расплавов, однородность, термическая и химическая устойчивость. Исследованные составы матриц удовлетворяют регламентным требованиям отделения остекловывания по температуре варки и вязкости расплавов. Практически все закаленные (исходные) стекла являются рентгеноаморфными. Термические испытания стекол при температуре 450°С приводят в основном к поверхностной кристаллизации образцов, в отдельных случаях – к объемной. Химически устойчивыми являются все фосфатные стекла при условии содержания Al2O3 в пределах регламентных величин (14–18 мас. %), борофосфатные стекла – при высоком содержании Al2O3 (около 19.6 мас. %). Показана возможность включения MnO2 в стекла в исследованном диапазоне (от 2 до 7.25 мас. %).
ВВЕДЕНИЕ
С момента ликвидации открытой акватории специального промышленного водоема В-9 – озера Карачай на радиохимическом заводе сформирован подход по включению жидких среднеактивных отходов (САО) в алюмофосфатные стекла. В связи с этим поступающие на отверждение растворы могут содержать в значимых количествах ряд элементов, влияние которых на свойства данных стекол ранее не прорабатывалось. К таким элементам можно отнести марганец, входящий в состав щелочных дезактивирующих растворов в виде соединения перманганата калия.
Кроме этого, в рамках проекта комплекса цементирования САО, как один из вариантов, предполагается направление избыточного количества α-излучающих нуклидов на остекловывание в составе коллекторов, в качестве которых может выступать MnO2 [1–3].
Поскольку в электропечь дозируются азотнокислые стеклообразующие растворы, в которых исключается наличие твердой фазы, в технологическом процессе потребуется нейтрализация и подкисление среднеактивных растворов, а также перевод марганца в растворимую двухвалентную форму.
По литературным данным [4] марганец может находиться в стекле в виде оксидов MnO, MnO2 и Mn2O3. От присутствия в расплаве других окислителей или восстановителей (к примеру, Fe2O3, FeO, CrO3, Cr2O3, CuO, Cu2O, SnO2, SnO) зависит в сторону какой формы будет смещено равновесие. Относительно недавние исследования поведения марганца в процессе варки фосфатных и борофосфатных стекол специалистами центральной заводской лаборатории были проведены в 2002 г. В данной работе марганец вводился в стеклообразующие растворы в виде перманганата калия или пиролюзита на стадии упаривания. Стекла варили как в присутствии восстановителя (этиленгликоля), так и без него. В результате было установлено, что все стекла имели красно-фиолетовый цвет, что свидетельствовало об отсутствии в них (в значимых количествах) MnO, который придает стеклу темно-зеленый цвет. На основании экспериментальных данных сделан вывод, что в расплаве фосфатного стекла марганец присутствует в форме MnO2. Также было показано, что MnO2 включается в фосфатное стекло в широком интервале концентраций (до 15–16 мас. %). При массовой доле MnO2 более 8% для достижения гомогенности стекла требуется более длительная выдержка расплава (около 8 ч). В борофосфатное стекло марганец включается так же, как и в фосфатное. В присутствии оксида бора температура варки несколько снижается.
Целью настоящей работы является исследование качественных показателей марганецсодержащих фосфатных и борофосфатных стекол применительно к технологии остекловывания на заводе РТ-1.
Согласно НП-019-2015, качество алюмофосфатных стекол с отвержденными отходами оценивается по ряду показателей: по однородности (отсутствие выделений дисперсных фаз); по химической устойчивости (определяется по скорости выщелачивания 137Cs, 90Sr, 239Pu), по термической устойчивости (отсутствие изменений структуры и водоустойчивости в результате хранения при температуре до +450°С).
Следует отметить, что в НП-019-2015 согласно приказу Ростехнадзора от 13 сентября 2021 г. № 299 (зарегистрирован Минюстом России 19 октября 2021 г., регистрационный № 65473) были внесены изменения в части условий хранения стеклоподобного компаунда и допустимых значений для термической устойчивости. Но поскольку постановка экспериментов проводилась на основании нормативных требований, сформулированных ранее, то в настоящей работе представлены соответствующие результаты исследований.
Для отверждения радиоактивных отходов (РАО) в штатном режиме на электропечи типа ЭП-500 необходимо соблюдение следующих технологических требований: температура расплава стекломассы допускается от 850 до 1150°С включительно. Из опыта эксплуатации электропечей следует отметить, что оптимальным температурным режимом для варки алюмофосфатных стекол является режим со средними показателями – 900–1050°С, что одновременно позволяет сохранить качественные показатели стекол, снизить энергозатраты, коррозию конструкционных материалов электропечи и увеличить срок ее эксплуатации. Данный режим поддерживается смешением флюсующих растворов с растворами ВАО в соотношении, которое позволяет получить смесь оксидов в конечном продукте с учетом регламентного содержания в стекле; оптимальный интервал вязкости расплава стекла для слива ограничивается величинами от 25 до 100 дПа с. Слив расплава стекла в штатном режиме осуществляется на 50–100°С ниже температуры варки. В результате температура сливаемого расплава составляет от 850 до 1000°С.
Пределы вязкости определяются в первую очередь временем слива расплава стекла. Так, время слива расплава стекломассы на электропечах типа ЭП-500 в контейнер объемом 200 л в указанном интервале вязкости составляет от 2 до 6 мин. Нижний предел вязкости, помимо этого, определяется снижением коррозионного влияния расплавов в присутствии агрессивных компонентов на конструкционные материалы электропечи. От вязкости расплава напрямую зависит его электропроводность, что немаловажно для варки стекла в печах прямого электрического нагрева. При внедрении составов матриц в технологию наибольшее предпочтение отдается длинным стеклам, которые исключают возможность резкого увеличения вязкости расплава при незначительном понижении температуры и, соответственно, непреднамеренную остановку процесса его слива в контейнер [5].
В настоящей работе рассмотрены все перечисленные показатели для оценки качества отвержденных отходов.
МЕТОДИЧЕСКАЯ ЧАСТЬ
В ходе работы были исследованы следующие системы стекол: фосфатные стекла, синтезированные на основе пульпы MnO2, фосфатные стекла, синтезированные на основе реактива MnO2 (“ч. д. а.”, ГОСТ 4470-79), фосфатные и борофосфатные стекла, синтезированные на основе реактива Mn(NO3)2, фосфатное и борофосфатное стекло без добавок марганца (образцы сравнения). С научной точки зрения пульпа MnO2 была использована для оценки условий варки стекла и изменений качества стекла, если в технологии остекловывания, гипотетически, исключить стадию восстановления марганца до двухвалентной (растворимой) формы.
Для приготовления пульпы диоксида марганца использовалась следующая реакция:
2KMnO4 + 3Mn(NO3)2 + 2H2O → 5MnO2↓ + 4HNO3 + 2KNO3.
Для полного осаждения MnO2 азотнокислая соль Mn(II) взвешивалась с 10% избытком относительно массы реактива, требуемой по стехиометрии реакции.
Суспензия готовилась на три порции в трех цилиндрах из расчета получения 2, 4 и 6 г MnO2 и исходной концентрации MnO2 до отстаивания 6.25 г/л (табл. 1). После отстаивания осветленная фаза порционно отделялась пипеткой до уровня, при котором не захватывалась мелкодисперсная твердая фаза. Пульпы использовались для варки стекол массой 106 г с содержанием MnO2 от 2 до 6 мас. % (с учетом избытка Mn(II), который по результатам анализа декантата соосадился с осадком).
Таблица 1.
Характеристика модельных суспензий MnO2
Показатель | Суспензия 1 | Суспензия 2 | Суспензия 3 |
---|---|---|---|
Исходный объем суспензии, мл | 320 | 640 | 960 |
Объем осадка после отстаивания в течение двух суток, мл | 73 | 170 | 250 |
Конечный объем суспензии после отбора осветленного раствора, мл | 90 | 180 | 270 |
Масса MnO2 в суспензии исходя из расчета, г | 2 | 4 | 6 |
Массовая концентрация MnO2 в суспензии в начале приготовления (до отделения осветленной фазы), г/л | 6.3 | ||
Массовая концентрация MnO2 в конечной суспензии (после отделения осветленного раствора), г/л | 22.2 |
Фосфатные и борофосфатные стекла варили из стеклообразующих растворов. Данные растворы получали растворением в дистиллированной воде азотнокислых солей натрия, алюминия, цезия, калия, марганца, борной кислоты с дальнейшим флюсованием фосфорной кислотой. Такой порядок синтеза стекол максимально приближен к реальным условиям технологического процесса, поскольку высокоактивные отходы от переработки ОЯТ представляют собой азотнокислые растворы, которые перед подачей в электропечь типа ЭП-500 флюсуются фосфорной кислотой. При приготовлении стеклообразующих растворов на основе пульпы MnO2 упомянутые соли вводились непосредственно в пульпу. Конечный объем стеклообразующего раствора (или суспензии) составлял 500 мл. Следует отметить, что реактив MnO2 вводился в стеклоуглеродные чаши в начале стадии упаривания стеклообразующих растворов, чтобы исключить его потери при переливании растворов из промежуточной посуды.
Во всех стеклообразующих растворах нитрат стабильного цезия имитирует радиоактивный цезий-137 и введен для оценки химической устойчивости стекол по выщелачиванию указанного элемента. Содержание нитрата цезия в растворах соответствует массовой доле его оксида в стеклах около 2%. Данная величина искусственно завышена для обнаружения цезия в среде выщелачивания. Чтобы исключить изменения свойств матриц, цезий включен в стекла замещением натрия (имеющего близкие химические свойства) в эквимолярном количестве.
Перед проведением процесса упаривания во все стеклообразующие растворы добавлялся этиленгликоль, исходя из расчета 25 г этиленгликоля на 100 г стекла.
В технологии остекловывания этиленгликоль используется для предотвращения уноса цезия и других легколетучих компонентов, смещая процесс денитрации в низкотемпературную область в присутствии фосфорной кислоты, а также способствуя созданию на поверхности расплава в электропечи пенного слоя, снижающего механический унос компонентов. В результате этого, в одной стадии совмещаются процессы восстановления, упаривания, денитрации и высушивания. Указанные процессы проводили на нагревательной плите ПЛС-02 при температуре 380°С с использованием лотка для песчаной бани.
Сухую смесь измельчали, помещали в алундовые тигли и кальцинировали в диапазоне температур от 300 до 750°С. В зависимости от поведения шихты во время процесса подъем температуры осуществляли постепенно. Стеклообразующий кальцинат плавили в диапазоне температур от 800 до 1100°С. Поскольку для каждого состава стекла характерна индивидуальная температура варки, через каждые 50°С проводили визуальный осмотр состояния содержимого тигля. Температуру варки стекла фиксировали в момент превращения кальцината в однородный расплав, для полной гомогенизации расплав выдерживали при данной температуре в течение 2 ч. Далее расплав стекла выливали в металлический поддон из нержавеющей стали, в результате чего он быстро охлаждался при комнатной температуре. Таким образом получали закаленные стекла.
В табл. 2 представлены составы исследованных стекол. Следует отметить, что для всех стекол (вне зависимости от способа приготовления) указана наиболее вероятная четырехвалентная форма марганца (MnO2). В процессе варки это подтверждалось красно-фиолетовым цветом стекол. В данных стеклах массовую долю MnO2 варьировали в пределах от 2 до 7.25%. Нижняя граница данного диапазона определяется количеством образующегося стекла, увеличение которого нецелесообразно при отверждении РАО, верхняя граница – ухудшением качества стекла за счет снижения содержания оксида алюминия.
Таблица 2.
Составы исследованных фосфатных и борофосфатных стекол
Номер стекла | Массовая доля оксидов в стекле, % | Тв, °С | ||||||
---|---|---|---|---|---|---|---|---|
Na2O | Cs2O | P2O5 | B2O3 | Al2O3 | MnO2 | K2O | ||
Фосфатные стекла, синтезированные на основе пульпы MnO2 | ||||||||
1П | 22.21 | 1.97 | 54.16 | 0 | 19.56 | 2 | 0.10 | 1050 |
2П | 17.45 | 4 | 0.21 | 1000 | ||||
3П | 15.35 | 6 | 0.31 | 1000 | ||||
Фосфатные стекла, синтезированные на основе реактива MnO2 (“ч. д. а.”, ГОСТ 4470-79) | ||||||||
1Р | 22.21 | 1.97 | 54.16 | 0 | 19.56 | 2 | 0.10 | 1100 |
2Р | 17.45 | 4 | 0.21 | 1050 | ||||
3Р | 15.35 | 6 | 0.31 | 1000 | ||||
Фосфатные стекла, синтезированные на основе Mn(NO3)2 | ||||||||
4 | 22.11 | 1.96 | 53.92 | 0 | 19.47 | 2.44 | 0.10 | 1050 |
5 | 22.01 | 1.95 | 53.68 | 17.29 | 4.86 | 0.21 | 1000 | |
6 | 21.91 | 1.94 | 53.44 | 15.15 | 7.25 | 0.31 | 1000 | |
Борофосфатные стекла, синтезированные на основе Mn(NO3)2 | ||||||||
8 | 22.11 | 1.96 | 50.93 | 2.99 | 19.47 | 2.44 | 0.10 | 1000 |
9 | 22.01 | 1.95 | 50.70 | 2.97 | 17.29 | 4.86 | 0.21 | 950 |
10 | 21.91 | 1.94 | 50.48 | 2.96 | 15.15 | 7.25 | 0.31 | 950 |
Стекла без добавок (образцы сравнения) | ||||||||
7 | 22.21 | 1.97 | 54.16 | 0 | 21.66 | 0 | 0 | 1100 |
11 | 22.21 | 1.97 | 51.16 | 3 | 21.66 | 0 | 0 | 1000 |
Синтезированные стекла повторно расплавляли при температуре 1050°С. В процессе естественного охлаждения в диапазоне температур от 1050 до 600°С проводили измерение вязкости расплавов на лабораторном вибрационном вискозиметре. Определение вязкости основано на измерении амплитуды колебания стержня на воздухе и в расплаве стекла и расчете значений вязкости ${{\eta }}$, дПа с, по формуле:
где ${{A}_{{{\text{воз}}}}}$ – амплитуда колебания стержня на воздухе, мВ; ${{А}_{{{\text{расп}}}}}$ – амплитуда колебания стержня в расплаве, мВ; $A$ и $B$ – коэффициенты градуировочной зависимости, безразмерные величины, находятся экспериментально, используя эталонные жидкости.Для исследования термической устойчивости стекол (устойчивости к кристаллизации) проводили отжиг образцов в статических условиях при температуре 450°С. Данная температура является предельной температурой для испытаний, установленной НП-019-2015. В работе использовали высокотемпературную электропечь ПВК-1.6–5. Кусочки закаленных стекол произвольной формы помещали в алундовые тигли и сверху накрывали аналогичными тиглями для исключения прямого теплового излучения на образцы от нагревателей печи, что позволяет создать тепловое поле с корректными значениями температур. Образцы подвергали термической обработке в течение 30 ч (пять рабочих дней по 6 ч). В конце каждого дня печь отключали, образцы оставляли охлаждаться в печи. После выдержки часть образцов измельчали в порошок для исследования кристалличности по всему объему, часть оставляли в виде фрагментов для исследования кристалличности на поверхности.
Закаленные и отожженные стекла исследовали методом рентгенофазового анализа (РФА) для проверки однородности. Съемку рентгенограмм проводили на дифрактометре рентгеновском Bruker D8 Advance в диапазоне углов отражения 2θ от 10° до 60° с длиной волны рентгеновского излучения 1.54060 Å (CuKα), шагом 0.02° по оси 2θ и временем экспозиции 0.4 с в каждой точке в непрерывном режиме. Обработку полученных данных выполняли с использованием программного пакета Diffrac.suite, Diffrac.eva, Diffrac.topas и базы данных порошковой дифрактометрии PDF-2 (версия 2014 г.). Для образцов закристаллизованных стекол был выполнен полуколичественный анализ содержания фаз по их корундовым числам.
Испытания на химическую устойчивость стекол проводили согласно ГОСТ Р 52126-2003 при температуре (25 ± 3)°С, масса образцов составляла 0.3 г, фракция – (0.16–0.25) мм, объем среды выщелачивания (бидистиллированная вода) – 50 мл. Контактный раствор меняли через 1, 3, 7, 10, 14, 21, 28, 35, 56, 91 сут от начала опыта. Химическую устойчивость стекол оценивали по скорости выщелачивания стабильного цезия (как более подвижного элемента), которую сопоставляли с нормативной величиной для 137Cs 1 × 10–5 г/(см2 сут), указанной в НП-019-2015. В качестве дополнительного параметра при оценке химической устойчивости матриц использовали степень выщелачивания элемента, которая является ненормируемой величиной, однако позволяет сделать более корректные выводы. Концентрацию цезия в среде выщелачивания анализировали на ICP масс-спектрометре Agilent 7500cx, погрешность определения метода составляет 10%.
РЕЗУЛЬТАТЫ И ОБСУЖДЕНИЕ
Результаты определения температуры варки марганецсодержащих стекол представлены в табл. 2. Из приведенных данных видно, что температура варки стекол находится в диапазоне от 950 до 1100°С. Как уже было отмечено ранее, оптимальный температурный режим для варки алюмофосфатного стекла в электропечи типа ЭП-500 находится в диапазоне от 900 до 1050°С включительно. Таким образом, указанным требованиям по режиму варки удовлетворяют все исследованные составы стекол, кроме составов № 1Р и № 7 (1100°С). В данных стеклах массовая доля Al2O3 составляет от 19.56 до 21.66%, что выходит за рамки регламентных величин (от 14 до 18 мас. %). Для снижения температуры варки необходима корректировка состава по указанному компоненту, а также увеличение массовой доли легкоплавкого Na2O.
Температура варки борофосфатных стекол ниже, чем у фосфатных на 50–100°С. С увеличением массовой доли MnO2 в стеклах температура варки уменьшается, что связано с уменьшением содержания тугоплавкого Al2O3.
Во время варки все расплавы стекол визуально были однородными и легко сливались. После слива и охлаждения стекла в основном получились прозрачными по всему объему, у стекол составов 4–6, 11 наблюдалась незначительная локальная кристаллизация в месте слива расплава стекла (в виде белых разводов). Стекло состава 1Р после застывания обладало частичной кристаллизацией с эффектом опалесценции по всей матрице. Данное стекло по своему составу идентично стеклам составов 1П и 4 (которые получились прозрачными) с тем отличием, что оно было сварено на основе реактива MnO2. При этом для всех трех стекол (1П, 1Р и 4) характерно высокое содержание Al2O3, при котором повышается вероятность кристаллизации стекла. Известно, что оксидные формы металлов в расплавах обладают низкой кинетикой растворения, что могло быть причиной создания центров кристаллизации. Очевидно, в стекле одновременно воздействуют два фактора – содержание Al2O3 и вводимая форма MnO2. В случае варки стекла состава 1П отсутствие кристаллических фаз, вероятно, связано с мелкодисперсностью твердой фазы MnO2, вводимой с пульпой. Стекло состава 2Р с массовой долей Al2O3 17.45%, синтезированное на основе реактива MnO2, визуально было прозрачным.
Стекло состава 7 (без добавки MnO2) получилось сильно закристаллизованным. Образец имел белый цвет без стекловидного блеска. Такое стекло было исключено из плана исследований ввиду его плохого качества.
Все марганецсодержащие стекла получились красно-фиолетового цвета.
Согласно РФА, из всех составов закаленных стекол только в одном образце была идентифицирована фаза AlPO4 – в стекле состава 1Р. Степень кристалличности данного образца составляет 1.3 мас. %, рефлексы AlPO4 на рентгенограмме находятся на уровне фона. Остальные стекла по результатам РФА являются рентгеноаморфными, что подтверждает их однородность.
В ходе работы также была исследована вязкость расплавов фосфатных стекол (рис. 1). Из представленных на рис. 1 данных видно, что с увеличением массовой доли MnO2 в фосфатных стеклах вязкость их расплавов существенно снижается. Так, верхняя граница оптимального интервала вязкости расплава стекла для слива (100 дПа с) при содержании MnO2 от 2 до 2.44 мас. % достигается при 860°С, от 6 до 7.25 мас. % – при 770°С. Температура достижения нижней границы оптимального диапазона вязкости расплава (25 дПа с) не установлена, однако известно, что при 1020°С вязкость расплавов стекол рассмотренных составов изменяется от 40 до 70 дПа с. Таким образом, в температурном диапазоне слива стекла (от 850 до 1000°С) вязкость расплавов фосфатных стекол принимает оптимальные величины. Следует отметить, что валентное состояние марганца на начальном этапе приготовления стеклообразующих растворов не влияет на вязкость расплавов. Очевидно, двухвалентный марганец в условиях варки стекол окисляется до четырехвалентного состояния, в результате составы стекол получаются идентичными.
Валентное состояние марганца в стекле пробовали определить косвенным путем, посредством РФА шихт, полученных в результате упаривания стеклообразующих растворов (табл. 3).
Таблица 3.
Результаты РФА стеклообразующих шихт (2 параллельных опыта)
Фаза | Номер шихты соответствующего стекла | ||||||
---|---|---|---|---|---|---|---|
1Р | 2Р | 3Р | 4 | 5 | 6 | ||
MnO2 | 1 | + | + | + | + | + | + |
2 | + | + | + | ||||
NaMnP2O7 | 1 | + | + | + | |||
2 |
Из данных, приведенных в табл. 3, видно, что марганец в основном встречается в виде MnO2, как в шихте, синтезированной на основе реактива MnO2, так и в шихте, приготовленной на основе Mn(NO3)2. В отдельных случаях идентифицирован трехвалентный марганец в составе соединения NaMnP2O7. В стеклообразующих шихтах 8–10 марганецсодержащие фазы не обнаружены, это может быть связано либо с неоднородностью шихты и малым содержанием данных фаз в отобранной пробе, либо включением марганца в аморфную структуру.
Фотографии стекол, отожженных в статических условиях при температуре 450°С, представлены на рис. 2. На основании внешней оценки образцов можно сделать вывод, что MnO2 является плавнем, так как фрагменты фосфатных стекол составов 2Р, 3Р и 6 в ходе термической обработки подверглись размягчению и совместному слипанию, приняв форму тигля. Фосфатное стекло 5 и борофосфатные стекла 8, 9 имели только поверхностную деформацию. У борофосфатного стекла состава 10 видимых изменений не замечено. Фосфатные стекла составов 1Р и 4 после отжига частично закристаллизовались с образованием локальных фиолетовых областей. Фрагменты стекла 4 слиплись между собой, по всему объему матрицы наблюдались многочисленные трещины. Фрагменты стекла 1Р сохранили свою форму, слипание образцов не произошло. Все стекла, которые имели частичную или полную деформацию, приобрели матовую фактуру (2Р–6, 8, 9).
Результаты РФА указанных стекол, а также полуколичественного анализа содержания фаз по их корундовым числам приведены в табл. 4 (для порошков), дифрактограммы – на рис. 3а. После отжига при 450°С практически все образцы остались рентгеноаморфными по всему объему, кроме фосфатных стекол составов 1Р, 4 и 5. В большей степени закристаллизовалось стекло состава 1Р (56.7 мас. %), которое уже изначально имело центры кристаллизации. Основными кристаллическими фазами в данном стекле являются фосфат алюминия AlPO4, пирофосфат натрия-алюминия NaAlP2O7 и оксид алюминия Al2O3.
Таблица 4.
Результаты РФА стекол, отожженных при температуре 450°С (анализ порошков), мас. %
Номер карты PDF, вид фазы и кристаллической решетки | Номер состава стекла | |||||
---|---|---|---|---|---|---|
1Р | 2Р | 3Р | 4 | 5 | 6, 8–11 | |
Рентгеноаморфная фаза | 43.3 | + | + | 83.1 | 89.8 | + |
PDF 01-084-2483 NaAlP2O7 | 16.7 | – | – | 9.4 | 6.6 | – |
PDF 00-046-0338 AlPO4, гексагональная кр. р. | 8.0 | – | – | – | – | – |
PDF 01-070-4690 AlPO4, моноклинная кр. р. | 7.0 | – | – | – | – | – |
PDF 01-070-7357 AlPO4, триклинная кр. р. | 6.0 | – | – | – | – | – |
PDF 01-070-6292 AlPO4 | – | – | – | 7.5 | 3.6 | – |
PDF 00-013-0430 Al(PO3)3 | 4.1 | – | – | – | – | – |
PDF 01-088-0107 Al2O3 | 14.9 | – | – | – | – | – |
Рис. 3.
Дифрактограммы порошков (а) и поверхности фрагментов (б) стекол, отожженных при температуре 450°С.
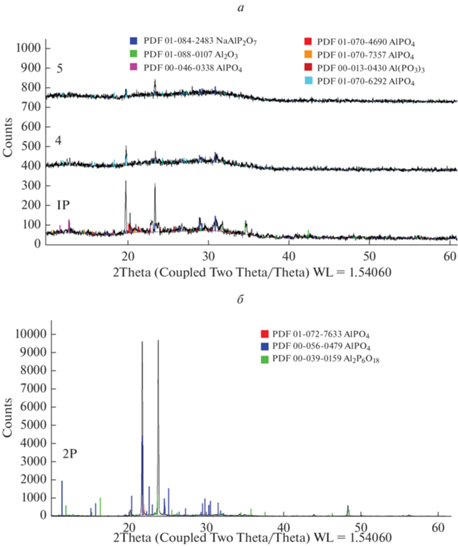
Стекло 4 по своему составу близко к стеклу 1Р, до отжига оно было однородным, без центров кристаллизации, однако термическая обработка привела к частичной кристаллизации (16.9 мас. %). Склонность фосфатных стекол составов 1Р и 4 к кристаллизации связана с высоким содержанием в данных матрицах Al2O3 (около 19.5 мас. %), концентрация которого находится на пороге его растворимости в расплавах.
Следует обратить внимание на борофосфатное стекло состава 8 с массовой долей Al2O3 19.47%, которое, в отличие от фосфатных стекол 1Р и 4, демонстрирует лучшую термическую устойчивость. Данное стекло после отжига остается рентгеноаморфным по всему объему, что связано с влиянием добавки В2О3, который обладает свойством подавлять кристаллизационные эффекты.
Различие стекол составов 2Р и 5 по своему поведению во время отжига не поддаются логическому объяснению.
Для выявления отличий между внутренней и внешней частями фрагментов по фазовой составляющей дополнительно был проведен РФА поверхности отожженных стекол. Результаты выборочного анализа стекол приведены в табл. 5. Полуколичественный анализ содержания фаз по их корундовым числам в данном случае не проводился, поскольку в монолитных образцах возникает текстурирование кристаллических плоскостей, в результате чего интенсивность рефлексов получается некорректной. На основании полученных результатов можно отметить, что кристаллизация поверхности происходит не только у фосфатных, но и у борофосфатных стекол, что объясняет их матовую фактуру при визуальной оценке. На поверхности исследованных образцов (2Р, 5, 9) в основном обнаруживается AlPO4 в различных полиморфных модификациях, у стекла состава 2Р, кроме этого, идентифицируется метафосфат алюминия Al2P6O18. Поскольку при анализе порошков стекла составов 2Р и 9 были рентгеноаморфными, то можно сделать вывод, что кристаллизация поверхности образцов несущественна на фоне общей массы стекла. В случае стекла состава 5 кристаллизация носит не только поверхностный, но и объемный характер (табл. 4). В качестве примера, на рис. 3б представлена дифрактограмма поверхности фрагмента стекла состава 2Р, отожженного при 450°С.
Таблица 5.
Результаты РФА поверхности стекол, отожженных при температуре 450°С (анализ фрагментов)
Номер карты PDF, вид фазы и кристаллической решетки | Номер состава стекла | ||
---|---|---|---|
2Р | 5 | 9 | |
Рентгеноаморфная фаза | + | + | + |
PDF 01-072-7633 AlPO4, орторомбическая кр. р. | + | – | – |
PDF 00-056-0479 AlPO4 | + | – | – |
PDF 01-070-4689 AlPO4, триклинная кр. р. | – | + | – |
PDF 01-070-6292 AlPO4, орторомбическая кр. р. | – | + | – |
PDF 00-045-0509 AlPO4, кубическая кр. р. | – | – | + |
PDF 00-003-0445 AlPO4, гексагональная кр. р. | – | – | + |
PDF 00-039-0159 Al2P6O18, моноклинная кр. р. | + | – | – |
Закаленные и термически обработанные при 450°С стекла были испытаны на химическую устойчивость. Результаты выщелачивания цезия из указанных стекол сведены в табл. 6 и представлены на рис. 4, 5.
Таблица 6.
Сведенные результаты скорости и степени выщелачивания цезия из закаленных и отожженных при 450°С стекол
Номер стекла | Содержание MnO2 в стекле, мас. % | Дифференциальная скорость выщелачивания, г/(см2 сут) |
Интегральная степень выщелачивания, % |
||||||
---|---|---|---|---|---|---|---|---|---|
закаленные стекла |
отожженные стекла | закаленные стекла | отожженные стекла | ||||||
на 1 сут | на 91 сут | на 1 сут | на 91 сут | за 1 сут | за 91 сут | за 1 сут | за 91 сут | ||
Фосфатные стекла, синтезированные на основе пульпы MnO2 | |||||||||
1П | 2 | 3.7 × 10–6 | 1.3 × 10–6 | Отжиг не проводился | 0.04 | 1.72 | Отжиг не проводился | ||
2П | 4 | 4.4 × 10–6 | 1.8 × 10–6 | 0.05 | 2.60 | ||||
3П | 6 | 7.4 × 10–6 | 3.2 × 10–6 | 0.09 | 4.43 | ||||
Фосфатные стекла, синтезированные на основе реактива MnO2 (“ч. д. а.”, ГОСТ 4470-79) | |||||||||
1Р | 2 | 3.4 × 10–6 | 2.4 × 10–7 | 7.4 × 10–5 | 8.4 × 10–6 | 0.04 | 0.37 | 0.88 | 22.69 |
2Р | 4 | 3.7 × 10–6 | 1.3 × 10–6 | 4.5 × 10–6 | 6.3 × 10–7 | 0.04 | 1.52 | 0.05 | 1.21 |
3Р | 6 | 5.7 × 10–6 | 2.4 × 10–6 | 5.7 × 10–6 | 1.9 × 10–6 | 0.07 | 3.27 | 0.07 | 2.72 |
Фосфатные стекла, синтезированные на основе Mn(NO3)2 | |||||||||
4 | 2.44 | 3.2 × 10–6 | 7.7 × 10–7 | 2.1 × 10–5 | 5.0 × 10–6 | 0.04 | 0.97 | 0.26 | 8.84 |
5 | 4.86 | 5.2 × 10–6 | 2.2 × 10–6 | 5.9 × 10–6 | 1.5 × 10–6 | 0.06 | 2.97 | 0.07 | 2.41 |
6 | 7.25 | 7.7 × 10–6 | 3.1 × 10–6 | 8.5 × 10–6 | 2.7 × 10–6 | 0.09 | 4.84 | 0.10 | 4.15 |
Борофосфатные стекла, синтезированные на основе Mn(NO3)2 | |||||||||
8 | 2.44 | 6.1 × 10–6 | 3.3 × 10–6 | 5.8 × 10–6 | 2.9 × 10–6 | 0.07 | 5.43 | 0.07 | 4.50 |
9 | 4.86 | 1.3 × 10–5 | 6.0 × 10–6 | 8.7 × 10–6 | 5.1 × 10–6 | 0.16 | 9.22 | 0.10 | 7.77 |
10 | 7.25 | 1.2 × 10–5 | 5.4 × 10–6 | 1.0 × 10–5 | 4.8 × 10–6 | 0.14 | 8.74 | 0.12 | 7.44 |
Борофосфатное стекло без добавок | |||||||||
11 | – | 4.2 × 10–6 | 1.3 × 10–6 | 3.7 × 10–6 | 1.3 × 10–6 | 0.05 | 3.14 | 0.04 | 2.27 |
Рис. 4.
Зависимость скорости выщелачивания Cs из закаленных фосфатных (1Р–3Р, 4–6) и борофосфатных стекол (8–11) от времени.
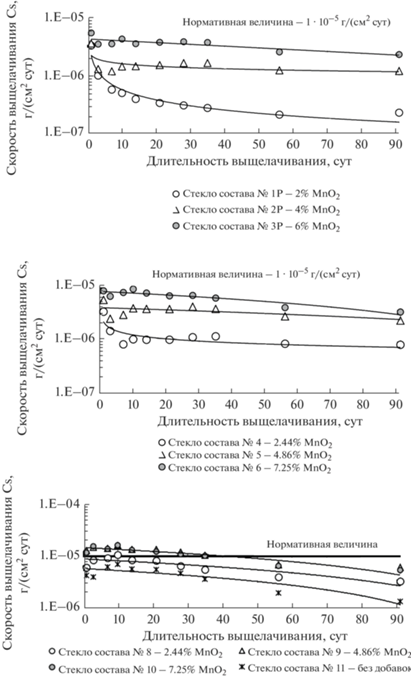
Рис. 5.
Зависимость скорости выщелачивания Cs из отожженных при 450°С фосфатных (1Р–3Р, 4–6) и борофосфатных стекол (8–11) от времени.
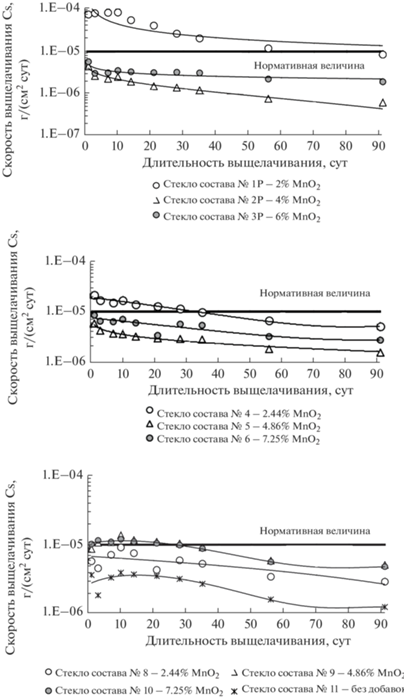
Из приведенных данных видно, что с увеличением включения MnO2 в стекла скорость и степень выщелачивания цезия из закаленных фосфатных матриц увеличивается, из борофосфатных стекол – сначала увеличивается (при массовой доле до 4.86%), потом остается на постоянном уровне (при массовой доле от 4.86 до 7.25%).
При сопоставлении показателей выщелачивания цезия из закаленных фосфатных стекол, синтезированных на основе пульпы MnO2, реактива MnO2 и Mn(NO3)2, в большинстве случаев не замечено существенного влияния данных факторов на химическую устойчивость стекол, даже при некотором расхождении исследуемых диапазонов содержания MnO2 (от 2 до 6% и от 2.44 до 7.25 мас. %). Исключение составляет закаленное стекло состава 1Р, которое уже изначально характеризовалось частичной кристаллизацией.
Так, скорость выщелачивания цезия на первые сутки из закаленных стекол составов 1П, 1Р и 4 с массовой долей MnO2 от 2 до 2.44% в среднем составляет 3.4 × 10‒6 г/(см2 сут). В дальнейшем, для стекла состава 1Р характерно более быстрое снижение скорости выщелачивания во времени, в результате чего степень выщелачивания цезия из указанного стекла за 91 сут составляет 0.37%, в отличие от стекол составов 1П (1.72%) и 4 (0.97%).
Скорость выщелачивания цезия на первые сутки из закаленных стекол составов 3П, 3Р и 6 с массовой долей MnO2 от 6 до 7.25% в среднем составляет 6.9 × 10–6 г/(см2 сут), степень выщелачивания за 91 сут – 4.2%.
После термической обработки фосфатных стекол при 450°С показатели выщелачивания цезия существенно изменяются только у образцов 1Р и 4. Так, начальная скорость выщелачивания цезия из отожженного стекла состава 1Р увеличивается в 22 раза, из отожженного стекла состава 4 – в 7 раз. Степень выщелачивания цезия из отмеченных стекол за 91 сут составляет 22.7 и 8.8% соответственно. В результате, системы с высоким содержанием Al2O3 (около 19.6 мас. %) проявляют свои кристаллизационные свойства не только на стадии варки стекол (1Р), но и в процессе термических испытаний (4), что негативно влияет на их химическую устойчивость. Различия скорости выщелачивания цезия из закаленных и отожженных стекол связано с образованием в термически обработанных стеклах кристаллической фазы фосфата и оксида алюминия. Кристаллизация алюминия (отвечающего за химическую устойчивость стекла) в виде отдельных соединений приводит к обеднению аморфной части стекла по данному элементу и обогащению по натрию и фосфору в локальных областях, вследствие чего данные области становятся более растворимыми, увеличивая выход компонентов в среду выщелачивания.
Таким образом, все закаленные фосфатные стекла по выщелачиванию цезия являются химически устойчивыми – скорость выщелачивания с начала испытаний не превышает нормативную величину (1 × 10–5 г/(см2 сут)). После отжига фосфатных матриц при 450°С химическую устойчивость сохраняют только стекла составов 2Р, 3Р, 5 и 6 (с массовой долей Al2O3 от 15 до 17.5%). Скорость выщелачивания цезия на первые сутки из отожженного стекла состава 4 незначительно превышает нормативную величину и достигает ее на 35 сут, однако химически устойчивым данное стекло считать нельзя, поскольку степень выщелачивания за 91 сут составляет неприемлемое значение (8.8%).
Скорость выщелачивания цезия из закаленного борофосфатного стекла состава 8 в течение всего периода испытаний удовлетворяет нормативным требованиям, степень выщелачивания цезия из указанного стекла за 91 сут составляет 5.4%. Следовательно, закаленное стекло состава 8 является химически устойчивым.
Скорость выщелачивания цезия из закаленных борофосфатных стекол составов 9 и 10 в течение 10 сут от начала испытаний изменяется в диапазоне от 1.2 × 10–5 до 1.7 × 10–5 г/(см2 сут) с последующим медленным снижением до нормативной величины к 35 сут. Скорость выщелачивания цезия из отмеченных стекол на 91 сут составляет в среднем 5.7 × 10–6 г/(см2 сут). Указанные величины скорости выщелачивания цезия из стекол составов 9 и 10, в первом приближении, соответствуют нормативным требованиям (находятся на их границе), однако к химически устойчивым такие стекла отнести нельзя, поскольку они имеют тенденцию к равномерному растворению, за счет чего степень выщелачивания цезия за 91 сут составляет 9%, в отличие от показателей выщелачивания из фосфатных стекол.
После отжига химическая устойчивость борофосфатных стекол по показателям выщелачивания цезия изменяется незначительно. Следует обратить особое внимание на противокристаллизационный эффект добавки В2О3 в стекле с высоким содержанием Al2O3 (до 19.5 мас. %) (состав 8), что позволяет стабилизировать качественные показатели матрицы – термическую и химическую устойчивость.
ЗАКЛЮЧЕНИЕ
В работе исследованы качественные характеристики марганецсодержащих фосфатных и борофосфатных стекол (температура варки, вязкость, однородность, химическая и термическая устойчивость). Показано, что температура варки большинства марганецсодержащих стекол находится в диапазоне от 950 до 1050°С, что удовлетворяет оптимальному режиму эксплуатации электропечи типа ЭП-500. Температура варки борофосфатных стекол ниже, чем у фосфатных на 50–100°С. С увеличением массовой доли MnO2 в стеклах температура варки уменьшается, что связано с уменьшением содержания тугоплавкого Al2O3. Вязкость расплавов фосфатных стекол оптимальна (от 25 до 100 дПа с) в температурном диапазоне слива стекла (от 850 до 1000°С).
Согласно РФА, практически все закаленные стекла являются рентгеноаморфными, что указывает на их однородность. Исключение составляет фосфатное стекло состава 1Р с массовой долей Al2O3 19.56%, которое обладает эффектом опалесценции. В данном стекле обнаружена фаза AlPO4.
В результате термических испытаний стекол в статическом режиме при 450°С происходит полное или частичное размягчение образцов, что является причиной поверхностной или объемной кристаллизации фрагментов стекла. Объемная кристаллизация в основном характерна для фосфатных стекол с высоким содержанием Al2O3 (от 17 до 19.6 мас. %). Введение добавки В2О3 в указанные стекла существенно снижает кристаллизационный эффект, однако поверхностная кристаллизация остается. Как в ранней, так и поздней редакции НП-019-2015 в 2021 г. при термических испытаниях исключаются структурные изменения матрицы. В результате этого все исследованные стекла считаются термически неустойчивыми (недопустима также и поверхностная кристаллизация). Таким образом, 450°С, как предельная температура хранения стеклоподобного компаунда согласно ранней редакции НП-019-2015, не обеспечивает сохранения требуемого качества стекла. В поздней редакции НП-019-2015 отмечается, что указанный параметр должен быть на 100°С ниже температуры стеклования соответствующего компаунда, соответственно, и термические испытания должны проводиться при более низкой температуре.
Фосфатные стекла являются химически устойчивыми по выщелачиванию цезия, как до отжига, так и после отжига, при условии, если массовая доля Al2O3 находится в рамках регламентных величин (от 14 до 18 мас. %), борофосфатные стекла – при содержании Al2O3 до 19.5 мас. %. Из этого следует, что добавку В2О3 целесообразнее применять в системах с высоким содержанием тугоплавких компонентов. На основании полученных данных показана возможность включения MnO2 в фосфатные и борофосфатные стекла в исследованном диапазоне (от 2 до 7.25 мас. %).
Варианты синтеза стекол незначительно влияют на их качественные характеристики, на основе чего можно сделать вывод, что в технологию остекловывания могут вовлекаться не только марганецсодержащие растворы (Mn(II)) (согласно штатной схеме), но и, гипотетически, суспензии на основе MnO2. В рамках лабораторных экспериментов могут использоваться следующие формы марганца: MnO2 (пульпа и реактив) и Mn(NO3)2.
Список литературы
Слюнчев О.М., Ремизова В.А., Бобров П.А. Исследование возможности цементирования смешанной пульпы гидроксида железа и диоксида марганца, содержащей α-излучающие радионуклиды // Вопросы радиационной безопасности. 2021. № 3. С. 26–34.
Одноволова А.М., Софронов Д.С., Брылева Е.Ю., Пузан А.Н., Матейченко П.В., Гудзенко Л.В., Десенко С.М., Беда А.А. Получение и сорбционный свойства частиц MnO(OH) // Журн. прикладной химии. 2015. Т. 88. Вып. 9. С. 1294–1299.
Земскова Л.А., Войт А.В., Баринов Н.Н., Николенко Ю.М., Шлык Д.Х. Композиционные сорбенты на основе синтетического оксида марганца и углеродного волокна // Журн. неорганической химии. 2016. Т. 61. № 12. С. 1628–1634.
Аппен А.А. Химия стекла. Изд-во “Химия”, 1970. С. 352.
Козлов П.В., Ремизов М.Б., Мартынов К.В., Беланова Е.А., Власова Н.В., Орлова В.А. Модификация состава алюмофосфатных стекол с имитаторами ВАО для повышения их устойчивости. 1. Влияние модификаторов на вязкость и кристаллизационную способность расплавов // Вопросы радиационной безопасности. 2019. № 1. С. 3–15.
Дополнительные материалы отсутствуют.
Инструменты
Физика и химия стекла