Физика и химия стекла, 2023, T. 49, № 1, стр. 34-46
Интенсификация процесса выщелачивания силикатных стекол кислыми газами
В. А. Шарагов 1, *, Г. И. Курикеру 1
1 Бельцкий государственный университет им. Алеку Руссо
MD-3121 Бельцы, ул. Пушкина, 38, Республика Молдова
* E-mail: sharagov@mail.ru
Поступила в редакцию 24.01.2022
После доработки 14.06.2022
Принята к публикации 18.08.2022
- EDN: CFYJLQ
- DOI: 10.31857/S0132665122600479
Аннотация
Анализируются и обобщаются результаты исследований по интенсификации процесса выщелачивания щелочносиликатных промышленных и синтезированных стекол кислыми газами. Идентифицирован состав продуктов реакции стекол с газообразными реагентами при помощи рентгенофазового анализа, рентгеноспектрального электронно-зондового микроанализа, термического анализа, пламенной фотометрии и количественного химического анализа. Определены физико-химические свойства промышленных стеклоизделий, модифицированных газообразными реагентами в лабораторных и заводских экспериментах. Обсуждаются пути интенсификации процесса выщелачивания силикатных стекол кислыми газами.
ВВЕДЕНИЕ
Многие столетия выщелачивание поверхности стекла печными газами являлось сопутствующим и неуправляемым процессом при отжиге разных видов стеклоизделий. Так, например, Безбородов М.А. отмечает: “В те времена, когда на стекольных заводах не было никакой измерительной аппаратуры в печах и многое определялось “на глаз”, стеклоделы подметили, что хорошо отожженные изделия покрыты белым налетом с голубоватым оттенком.” [1]. В 30-х гг. прошлого столетия было установлено, что налет на поверхности листового стекла [2] и бутылок [3] содержит сульфат натрия. Из этого следует, что диоксид серы выщелачивает стекло.
Впервые в работе [2] выяснено влияние температуры на массу Na2SO4, образовавшегося на поверхности листового стекла. Эксперименты также показали, что выщелачивание промышленных изделий SO2 повышает химическую устойчивость стекла в несколько раз, при этом возрастает его механическая прочность и термостойкость [1–3]. Уникальные исследования проведены по определению сопротивления внутреннему гидростатическому давлению (СВГД) бутылок, отожженных в лере с печными газами [4]. Испытав более 130 тыс. бутылок, автор пришел к заключению, что печные газы на 20–30% повышают их прочность.
В последующих исследованиях повышенное внимание уделялось механизму выщелачивания промышленных и модельных стекол кислыми газами. Интерес вызывают работы [5–7 и др.]. Всего проблеме выщелачивания силикатных стекол кислыми газами посвящено более 400 публикаций, а также издана единственная монография [8].
Главным недостатком метода выщелачивания кислыми газами является небольшая толщина выщелоченного слоя стекла. В зависимости от химического состава образцов и условий термохимической обработки толщина уплотненного слоя у промышленных стекол изменяется от долей мкм до 1 мкм. При транспортировании и эксплуатации стеклоизделий выщелоченный слой легко повреждается, вследствие чего их физико-химические свойства ухудшаются [8].
Цель настоящей работы состоит в анализе и обобщении результатов исследований по интенсификации процесса выщелачивания силикатных стекол кислыми газами.
ЭКСПЕРИМЕНТАЛЬНАЯ ЧАСТЬ
Объектами исследований являются промышленные изделия разного назначения и синтезированные двух- и трехкомпонентные стекла. В экспериментах применяли: листовое стекло; стеклянную тару (бутылки, банки, флаконы) из прозрачного обесцвеченного стекла; бутылки из темно-зеленого стекла; изделия из сортового прозрачного бесцветного и синего стекол; рассеиватели из розалинового и молочного стекол; изделия из прозрачного бесцветного медицинского стекла; изоляторы из прозрачного бесцветного и малощелочного стекол. Химические составы промышленных стекол, условия варки стекломассы, методы формования стеклоизделий разного назначения и их физико-химические свойства значительно отличаются друг от друга. Химические составы стекол представлены в табл. 1.
Таблица 1.
Химический состав промышленных стекол по данным заводских анализов
Вид стекла | Содержание оксидов (массовая доля, %) | ||||||||
---|---|---|---|---|---|---|---|---|---|
SiO2 | Al2O3 | Fe2O3 | CаO | MgO | Na2O | K2O | SO3 | другие | |
Листовое вертикального вытягивания | 72.65 | 1.55 | 0.11 | 7.60 | 3.71 | 13.62 | 0.35 | 0.31 | – |
Тарное обесцвеченное | 71.81 | 2.53 | 0.07 | 6.54 | 4.60 | 13.72 | 0.25 | 0.43 | – |
Бутылочное темно-зеленое | 69.68 | 4.83 | 0.69 | 9.68 | 0.35 | 14.37 | 0.21 | 0.34 | – |
Сортовое бесцветное | 71.95 | 4.22 | 0.04 | 6.52 | 0.20 | 17.15 | 0.10 | 0.12 | – |
Сортовое синее | 71.49 | 1.72 | 0.05 | 8.01 | 0.15 | 8.08 | 10.09 | 0.38 | 0.08 CoO |
Свето-техническое розалиновое | 71.48 | 2.74 | 0.04 | 7.32 | 0.22 | 17.30 | 0.36 | 0.31 | 0.02 Se 0.14 Sb |
Свето-техническое молочное | 65.03 | 7.03 | 0.04 | 3.84 | 0.11 | 19.53 | 0.16 | 0.10 | 4.88 F– |
Медицинское бесцветное | 72.81 | 4.52 | 0.05 | 6.05 | 0.82 | 8.15 | 1.64 | – | 6.11 B2O3 |
Изоляторное бесцветное | 72.31 | 2.44 | 0.10 | 7.67 | 3.61 | 9.73 | 3.86 | 0.21 | – |
Изоляторное малощелочное | 63.41 | 15.34 | 0.10 | 12.81 | 3.97 | 2.02 | – | 0.25 | 2.04 F– |
Для определения влияния некоторых компонентов стекла на химическое взаимодействие с газообразными реагентами применяли синтезированные стекла системы Na2O–R2O3–SiO2, где R2O3–Al2O3 и B2O3. Химические составы модельных стекол приведены в табл. 2.
Таблица 2.
Скорость выщелачивания Na+ из стекол системы Na2O–R2O3–SiO2 дифторхлорметаном (температура 550°С, количество вещества реагента на обработку – 0.67 моль, время – 15 мин)
Номер стекла |
Молярное отношение в стекле | Скорость выщелачивания, мкмоль Na+/(дм2 мин) |
|||
---|---|---|---|---|---|
Na2O | Al2O3 | B2O3 | SiO2 | ||
1 | 1 | – | – | 2 | 19.7* |
2 | 1 | – | – | 3 | 15.1 |
3 | 1 | 0.05 | – | 2 | 37.6* |
4 | 1 | 0.15 | – | 2 | 54.0* |
5 | 1 | 0.05 | – | 3 | 28.1 |
6 | 1 | – | 0.05 | 2 | 11.7 |
7 | 1 | – | 0.15 | 2 | 7.5 |
Для синтеза стекол использовали тонкомолотый безводный диоксид кремния квалификации “чистый” и химически чистые глинозем, борную кислоту и соду. Из сваренной стекломассы формовали плитки, а затем их отжигали, шлифовали и полировали. Отклонение компонентов стекла от заданного состава не превышало 1 мол. %.
Для термохимической обработки образцов стекла применяли диоксиды серы и азота, дифтордихлорметан, дифторхлорметан, газовые смеси из фторхлорпроизводных углеводородов и диоксида серы. В качестве источников фторида, хлорида и бромида водорода использовали растворы кислот HF, HCl, HBr. Эксперименты проводили в лабораторных и заводских условиях.
Лабораторные режимы термохимической обработки образцов стекла газообразными реагентами: температуру изменяли в диапазоне 300–600°С, количество вещества реагента на одну обработку составляло 0.05–1.50 моль, продолжительность 1–120 мин. В экспериментах устанавливали следующие свойства стекла: водо- и кислотоустойчивость, прочность при центрально-симметричном изгибе, ударную вязкость, микротвердость и термостойкость. Методику определения водо- и кислотоустойчивости разрабатывали с учетом химического состава промышленных стеклоизделий и условий их эксплуатации. Прочность листового стекла при центрально-симметричном изгибе устанавливали по методике [9]. Для определения ударной вязкости листового стекла учитывали рекомендации [10]. Микротвердость образцов измеряли на микротвердомере ПМТ-3М при разных нагрузках на индентор алмазной пирамиды. Для определения максимальной термостойкости стекла перепад температур увеличивали до полного разрушения всех образцов.
Режимы термохимической обработки полых стеклоизделий газообразными реагентами на стекольных заводах были следующими: температуру изменяли в диапазоне 450–600°С, объем газообразного реагента на одно изделие составлял 0.05–100.0 мл, длительность 1 с–80 мин. Стеклянную тару (бутылки, банки и флаконы) выщелачивали реагентами на стадии чистового выдувания изделий, на охлаждающих столиках стеклоформующих машин, на конвейере при транспортировании изделий к леру и во время отжига. Стеклоизделия испытывали на СВГД, микротвердость, термостойкость и водоустойчивость. Для банок дополнительно определяли сопротивление усилию сжатия в направлении перпендикулярном к стенкам корпуса. Для образцов устанавливали максимальные значения СВГД и сопротивления усилию сжатия в направлении перпендикулярном к стенкам корпуса, то есть нагрузку увеличивали до значения, при котором изделие разрушалось. Максимальную термостойкость промышленных стеклоизделий определяли по методике, аналогичной для образцов в лабораторных условиях.
Термохимическая обработка промышленных и синтезированных стекол газообразными реагентами в лабораторных и заводских условиях сопровождается образованием на поверхности образцов продуктов химической реакции. Состав налета выщелачивания идентифицировали при помощи рентгенофазового анализа, рентгеноспектрального электронно-зондового микроанализа, термического анализа, пламенной фотометрии и количественного химического анализа.
Фазовый состав продуктов реакции стекла с газообразными реагентами определяли на дифрактометре ДРОН-3.0 при СuKα-излучении. Для анализа применяли пластинки стекла, подвергнутые термохимической обработке газообразными реагентами, а также порошки продуктов реакции. Элементный состав налета выщелачивания и характер его распределения на поверхности стекла исследовали на электронном микроскопе ЭММА-2 с приставкой МАР для микрорентгеноспектрального анализа. В продуктах реакции анализировали наличие следующих элементов: Si, Al, Fe, Ca, Mg, K, F и Cl (Na не определялся). Термический анализ выполняли на дериватографе ОД-102. При помощи пламенного фотометра Flapho-4 в составе продуктов реакции выявляли присутствие Na+, K+ и Ca2+. На основе количественного химического анализа устанавливали ионный состав налета.
Для анализа состава и структуры поверхностных слоев промышленных и модельных синтезированных стекол применяли метод НF-секционирования. Сущность данного метода заключается в последовательном послойном растворении поверхностных слоев модельных двух- и трехкомпонентных стекол раствором HF слабой концентрации и анализе образовавшихся экстрактов [11]. Нами разработана методика секционирования раствором HF промышленных стекол разных составов [12]. Максимальная относительная погрешность определения толщины растворенного слоя составляла ±5%, а скорости травления ±4%. В вытяжках после травления стекла методом пламенной фотометрии определяли концентрации Na+, K+ и Ca2+.
РЕЗУЛЬТАТЫ И ИХ ОБСУЖДЕНИЕ
В лабораторных экспериментах термохимическая обработка образцов всех видов промышленных стекол газообразными реагентами в диапазоне температур 300–600°С приводит к образованию налета разной интенсивности. Чем выше температура обработки и больше содержание щелочных оксидов в составе стекла, тем более интенсивный налет образуется на поверхности образцов. Фазовый, элементный и ионный составы продуктов реакции всех видов промышленных и синтезированных стекол с газообразными реагентами идентифицировали при помощи комплексного анализа. Сначала определяли фазовый состав налета, а затем его сопоставляли с данными элементного и ионного составов. Необходимо подчеркнуть, что результаты разных методов анализа налета полностью совпали.
Термохимическая обработка промышленных стекол SO2 сопровождается образованием налета, состоящего из разных модификаций Na2SO4 и незначительного количества K2SO4, причем молярное соотношение между Na2SO4 и K2SO4 в продуктах реакции соответствует их содержанию в составе стекла. Поверхность малощелочного изоляторного стекла под воздействием диоксида серы покрывается слабым налетом из CaSO4. В составе продуктов реакции синтезированных стекол с SO2 выявлен Na2SO4. При реакции NO2 с промышленными стеклами появляется слабый налет, содержащий NaNO3.
При термохимической обработке промышленных стекол CF2Cl2, CHF2Cl и HCl их поверхность покрывается налетом, в состав которого входят NaCl и незначительное количество KCl. Соединения фтора в налете не выявлены. Малощелочное изоляторное стекло слабо реагирует с дифтордихлорметаном, образуя налет из CaCl2 и NaCl. На поверхности синтезированных стекол, выщелоченных CF2Cl2, обнаружен только NaCl. Реакция CF2Cl2 со стеклами системы Na2O–SiO2 протекает очень энергично, в результате чего на поверхности образцов идентифицирован не только NaCl, но и α-форма Na2Si2O5. Следовательно, несмотря на значительное различие между составами как промышленных, так и синтезированных стекол, и на разные режимы термохимической обработки в лабораторных и производственных условиях, в результате реакции образцов с CF2Cl2, CHF2Cl и HCl образуются продукты одного и того же состава.
На поверхности промышленных стекол, подвергнутых воздействию фторида водорода, установлено наличие NaF, KF и CaF2. Бромид водорода выщелачивает промышленные стекла с образованием налета, содержащего NaBr.
В состав продуктов реакции промышленных стекол со смесью CF2Cl2 и SO2 в объемном соотношении 1 : 1 входят, главным образом, разные модификации Na2SO4 и в меньшем количестве – NaCl и K2SO4. Полученные результаты означают, что при использовании газовых смесей интенсификация процесса выщелачивания стекла происходит за счет каталитического влияния фторхлорсодержащего реагента на диоксид серы.
Таким образом, характерным признаком выщелачивания стекла кислыми газами является образование на поверхности изделий налета, представляющего собой тонкую пленку продуктов реакции.
В литературе интенсивность выщелачивания промышленных и модельных стекол кислыми газами характеризуется массой образовавшихся продуктов реакции на единицу площади образца [2, 3, 5, 13 и др.]. Такой метод имеет существенные недостатки. Во-первых, невозможно сопоставлять реакционную способность разных кислых газов даже по отношению к стеклу одного и того же состава, так как продукты взаимодействия имеют разные химические составы. Во-вторых, нельзя сравнивать данные, полученные при различной продолжительности термохимической обработки. Другие критерии для оценивания интенсивности выщелачивания неорганических стекол кислыми газами в литературе отсутствуют.
На основе данных о составе налета и его геометрических параметрах (толщины, размеров, формы кристаллов и др.) и характеристики о составе и структуре выщелоченного слоя стекла нами разработаны пять критериев для оценивания интенсивности выщелачивания щелочносиликатных стекол кислыми газами: 1) скорость экстракции катионов щелочных металлов из поверхностного слоя стекла; 2) толщина налета выщелачивания на поверхности стекла; 3) толщина и степень выщелачивания поверхностного слоя стекла; 4) изменение химического состава и структуры поверхностного слоя стекла и 5) прирост микротвердости в выщелоченном слое стекла. Достоинства и недостатки критериев приведены в [14].
Анализ наших и литературных данных показал, что при обработке щелочных силикатных стекол кислыми газами образуется налет, в состав которого всегда входит Ме+ (Na+, K+ и др.). Из этого следует важный вывод – кинетику взаимодействия стекла с кислыми газами целесообразно характеризовать скоростью выщелачивания Ме+ [8]. В этом случае можно оценить способность стекла к выщелачиванию, независимо от состава продуктов реакций, причем при различной продолжительности обработки. Кроме того, определяя скорость экстракции Ме+, появляется возможность сопоставить интенсивность выщелачивания силикатных стекол при воздействии на них реагентов разной природы: кислых газов, воды, растворов кислот и т. п. Для расчета скорости экстракции Ме+ из стекла кислыми газами применяли формулу:
$\upsilon _{{{\text{M}}{{{\text{e}}}^{ + }}}}^{{}}$ = $C_{{{\text{M}}{{{\text{e}}}^{ + }}}}^{{}}$VS−1τ−1,
где $\upsilon _{{{\text{M}}{{{\text{e}}}^{ + }}}}^{{}}$ – скорость экстракции Ме+ из поверхностного слоя стекла, мкмоль Ме+/(дм2 поверхности стекла мин); $C_{{{\text{M}}{{{\text{e}}}^{ + }}}}^{{}}$ – концентрация Ме+ в растворе, полученном после смывания продуктов реакции дистиллированной водой, мкмоль Ме+/дм3; V – объем раствора, дм3; S – площадь поверхности образца, дм2; τ – продолжительность термохимической обработки, мин.
Предлагаются следующие пути интенсификации процесса выщелачивания силикатных стекол кислыми газами.
1. Оптимизация режимов термохимической обработки стекла кислыми газами.
Исследовано влияние разных факторов на скорость выщелачивания силикатных стекол газообразными реагентами: температуры, химического состава стекла и газовой среды, продолжительности термохимической обработки, концентрации и влажности газообразного реагента, дополнительной термообработки и состояния поверхности образцов.
Влияние температуры и состава некоторых газообразных реагентов на процесс выщелачивания светотехнического розалинового стекла представлено на рис. 1.
Рис. 1.
Зависимости скорости выщелачиванияυ+ из светотехнического розалинового стекла, обработанного SО2 (1), CHF2Cl (2), смесью CHF2Cl с SO2 в объемном соотношении 1 : 1 (3) и после дополнительной термообработки (4) от температуры.
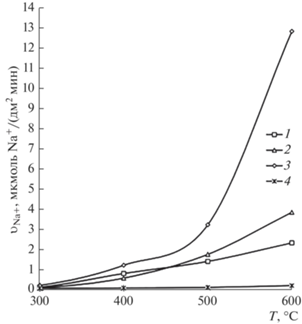
Скорость выщелачивания стекла при температуре ниже 300°С составляла 0.09 мкмоль Na+/(дм2 мин) и не отличалась от скорости выщелачивания образцов, промытых дистиллированной водой. При температуре 300°С и выше на поверхности стекла, обработанного всеми газообразными реагентами, образуется налет выщелачивания. Рис. 1 показывает, что CHF2Cl более интенсивно выщелачивает стекло, чем диоксид серы. Фторхлорпроизводные углеводородов активно реагируют с образцами при температуре выше 400°С, когда происходит их пиролиз с образованием фторида и хлорида водорода. Наиболее активно со стеклом взаимодействует смесь CHF2Cl с SO2.
Повышение температуры с 300 до 600°С увеличивает скорость выщелачивания Na+ из стекла газообразными реагентами многократно (см. рис. 1). Таким образом, чем выше температура, тем интенсивнее стекло выщелачивается газообразными реагентами. Благоприятное повышение температуры на интенсификацию процесса выщелачивания установлено при использовании разных по составу промышленных и синтезированных стекол и газообразных реагентов.
В некоторых исследованиях, например [15, 16 и др.] отмечается, что повторная термическая обработка изделий может изменить состояние поверхности стекла и его свойства. Дополнительную термическую обработку стекла проводили по режимам, аналогичным термохимической обработке, но без газовых реагентов. Данные графика 4 на рис. 1 иллюстрируют, что повторная термическая обработка незначительно повышает скорость выщелачивания стекла. Это свидетельствует о том, что увеличение скорости выщелачивания Na+ при термохимической обработке образцов полностью зависит от протекания химической реакции между щелочными компонентами стекла и газовыми реагентами и не связано с влиянием температуры на мобильность Na+.
Наиболее сложным и наименее изученным фактором является влияние компонентов стекла на процесс его выщелачивания. Известно, что наиболее интенсивно выщелачиваются оксидами серы стекла, содержащие в своем составе оксид алюминия [5]. Также интерес представляло выяснить влияние оксида бора на процесс выщелачивания модельных стекол газообразными реагентами, так как данный оксид уменьшает подвижность щелочных катионов в структурной сетке стекла. По этой причине нами исследовано выщелачивание стекол системы Na2O–R2O3–SiO2, где R2O3–Al2O3 и B2O3. В табл. 2 приведены значения скорости выщелачивания Na+ из синтезированных стекол, обработанных CHF2Cl.
Результаты экспериментов показывают, что при более высоком содержании Na2O в стеклах системы Na2O–SiO2 происходит более интенсивное выщелачивание CHF2Cl. Скорость выщелачивания натриевосиликатных стекол CHF2Cl в несколько раз превышала скорость выщелачивания промышленных стекол, обработанных тем же реагентом по аналогичному режиму. Это объясняется, во-первых, большим содержанием Na2О в модельных стеклах (от двух до трех раз), а во-вторых, в двухкомпонентных стеклах более высокая мобильность Na+ из глубинных слоев к поверхности.
Добавление Al2O3 в двухкомпонентные стекла значительно повышает скорость экстракции Na+CHF2Cl, в то время как введение такого же количества B2O3 снижает скорость выщелачивания. Увеличение содержания в стекле Al2O3 до 0.15 молярных долей резко усиливает выщелачивание Na+CHF2Cl, вследствие чего происходит “пригорание” налета к поверхности образцов. В этих опытах налет не полностью смывался водой, поэтому в табл. 2 для стекол № 1, 3 и 4 значения скорости выщелачивания Na+ не являются точными.
Важным фактором взаимодействия стекла с газообразными реагентами является продолжительность обработки. Учитывая, что наибольшая скорость выщелачивания стекла отмечалась при температуре 600°С, эксперименты проводились при этой температуре и количестве вещества газового реагента на одну обработку 0.67 моль. Результаты испытаний cортового бесцветного стекла представлены на рис. 2.
Рис. 2.
Зависимости скорости выщелачивания cортового бесцветного стекла дифторхлорметаном (1) и диоксидом серы (2) от продолжительности обработки.
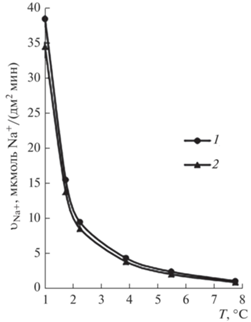
Из приведенных данных видно, что максимальная скорость выщелачивания стекла газовыми реагентами наблюдалась в течение первых 3 мин. При длительности обработки более 15 мин скорость выщелачивания Na+ из стекла значительно уменьшается. Такой же результат получен при термохимической обработке других промышленных стекол разными реагентами. Подобного характера зависимости получены при определении влияния концентрации и влажности газообразного реагента на скорость выщелачивания стекла. В промышленных условиях свежевыработанные горячие стеклоизделия более активно выщелачиваются реагентами, чем изделия, находившиеся на хранении и в эксплуатации.
На основе проведенных экспериментов определили следующий оптимальный режим термохимической обработки промышленных стекол в лабораторных условиях: температура – 600°С, количество вещества реагента на одну обработку – 0.67 моль, продолжительность – 15 мин. В производственных условиях оптимальный режим обработки стекла газообразными реагентами устанавливали только экспериментальным путем.
Термохимическая обработка промышленных стекол газообразными реагентами в лабораторных условиях повышает их водо- и кислотоустойчивость в несколько раз, прочность при статических и динамических нагрузках на 50–70%, микротвердость – на 10–20%, термостойкость – на 10–15%. Результаты производственных экспериментов представлены в [17].
Между скоростью выщелачивания катионов Ме+ кислыми газами, которые экстрагируются из поверхностного слоя стекла, его составом, структурой и физико-химическими свойствами изделий установлена тесная связь. В табл. 3 представлены результаты, взятые из работы [17], и дополненные данными по механической прочности и термостойкости листового стекла, выщелоченного разными газообразными реагентами.
Таблица 3.
Связь физико-химических свойств листового стекла с режимами термохимической обработки, скоростью выщелачивания Na+ газообразными реагентами и характеристикой выщелоченного слоя
Режим обработки | Скорость
выщелачивания, $\frac{{{\text{мкмоль}}\,{\text{N}}{{{\text{a}}}^{ + }}}}{{{\text{д}}{{{\text{м}}}^{{\text{2}}}}\,{\text{мин}}}}$ |
Свойства стекла | Характеристика выщелоченного стекла | |||||
---|---|---|---|---|---|---|---|---|
газооб-разный реагент | темпе-ратура, °С | водоустойчивость, мг Na2O/дм2 |
ударная вязкость, кДж/м2 | микро-твер-дость, ГПа | термо-стой- кость, °С |
толщина выщело-ченного слоя, мкм |
относи-тельная концент-рация Na+, Сmin/С0 |
|
CF2Cl2 | 300 | 0.22 | 0.50 | 2.9 | 4.23 | 111 | 0.3 | 0.8 |
400 | 0.55 | 0.40 | 3.0 | 4.45 | 112 | 0.4 | 0.7 | |
500 | 1.44 | 0.22 | 3.7 | 4.62 | 115 | 0.6 | 0.5 | |
600 | 3.48 | 0.14 | 4.4 | 4.97 | 122 | 0.8 | 0.4 | |
SO2 | 600 | 2.23 | 0.18 | 4.7 | 4.83 | 125 | 0.8 | 0.4 |
CF2Cl2 с SO2 (1 : 1) | 600 | 9.87 | 0.06 | 4.3 | 5.03 | 120 | 1.0 | 0.2 |
– | 20 | 0.09 | 0.52 | 2.8 | 4.22 | 110 | – | – |
Из табл. 3 следует, что максимальное повышение термомеханических свойств и химической устойчивости стекла достигается при наибольшей глубине выщелоченного слоя и степени его выщелачивания. Термохимическая обработка промышленных стекол газообразными реагентами не приводит к полному удалению Na+ из выщелоченного слоя (см. табл. 3). В наших исследованиях модельные двух- и трехкомпонентные стекла выщелачивали газовыми реагентами на глубину до 30 мкм и более.
2. Применение эффективных газовых реагентов для выщелачивания стекла на основе термодинамического анализа.
Поиск новых газовых реагентов, вступающих в реакцию с щелочными оксидами, выполняли на основе термодинамического анализа. Расчеты выполнены, как для реакций между щелочными оксидами и отдельными кислыми газами, так и для реакций с участием разных по составу газовых смесей. Изменение энергии Гиббса для уравнений наиболее вероятных химических реакций в интервале температур от 298 до 1000 К рассчитывали по методике [18]. В табл. 4 представлены расчеты изменения энергии Гиббса для реакций между оксидом натрия и газообразными реагентами при температурах 298 и 1000 К.
Таблица 4.
Изменение энергии Гиббса для уравнений наиболее вероятных реакций оксида натрия с газообразными реагентами при температурах 298 и 1000 К
Уравнения реакций оксида натрия с газообразными реагентами | ∆rG0 (298 K), кДж/моль |
∆rG (1000 K), кДж/моль |
---|---|---|
Na2O + 2HF = 2NaF + H2O | 163 | –17102 |
Na2O + 2HCl = 2NaCl + H2O | –428 | –4917 |
Na2O + 2HBr = 2NaBr + H2O | –452 | 51616 |
Na2O + CO2 = Na2CO3 | –274 | –5759 |
Na2O + SO2 = Na2SO3 | –376 | –5159 |
Na2O + SO3 = Na2SO4 | –519 | –11 681 |
2Na2O + 2SO2 + O2 = 2Na2SO4 | –1177 | –25 780 |
2Na2O + 4NO2 + O2 = 4NaNO3 | –919 | –94 358 |
Na2O + 2NH3 + 4O2 = 2NaNO3 + 3H2O | –1036 | –105 027 |
3Na2O + 2SO2 + O2 + 2HCl = 2Na2SO4 + 2NaCl + H2O | –1605 | –30 926 |
Данные табл. 4 свидетельствуют о том, что в стандартных условиях оксид натрия должен вступать в реакцию со всеми газообразными реагентами, за исключением фторида водорода. При температуре 1000 К отрицательные значения изменения энергии Гиббса резко возрастают для всех реакций и только бромид водорода не должен реагировать с оксидом натрия. Из представленных результатов также следует, что с термодинамических позиций оксид натрия наиболее активно должен взаимодействовать с газовыми смесями. Эксперименты подтвердили, что смеси газообразных реагентов более интенсивно выщелачивают силикатные стекла, чем отдельно взятые реагенты.
Получены графические зависимости изменения энергии Гиббса от температуры для химических реакций между компонентами промышленных стекол и газообразными реагентами. На рис. 3 показано влияние температуры на значение изменения энергии Гиббса для химической реакции хлорида водорода с щелочными оксидами.
Рис. 3.
Зависимости изменения энергии Гиббса от температуры для химической реакции хлорида водорода с оксидами натрия и калия. 1 – Na2O + 2HCl = 2NaCl + H2O, 2 – K2O + 2HCl = 2KCl + H2O.
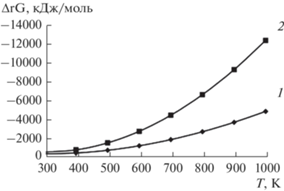
Данные рис. 3 свидетельствуют о прямо пропорциональной зависимости значения изменения энергии Гиббса от температуры для реакции хлорида водорода с оксидами натрия и калия.
3. Применение электрических и магнитных полей для интенсификации процесса выщелачивания стекла кислыми газами.
На протекание химических процессов большое влияние оказывают магнитные, электрические и акустические поля [19]. Информация о влиянии физических полей на выщелачивание стекла кислыми газами в литературе отсутствует. Нами исследован процесс выщелачивания промышленных стекол газообразными реагентами под воздействием электромагнитных полей. Пример влияния постоянного электрического поля на интенсивность выщелачивания светотехнического розалинового CНF2Cl показан на рис. 4.
Рис. 4.
Влияние температуры на скорость выщелачивания $\upsilon _{{{\text{N}}{{{\text{a}}}^{ + }}}}^{{}}$ светотехнического розалинового стекла дифторхлорметаном в постоянном электрическом поле (длительность – 15 мин, объем CHF2Cl – 15 л). 1 – U = 0, 2 – U = 0.5 кВ, 3 – U = 1.5 кВ.
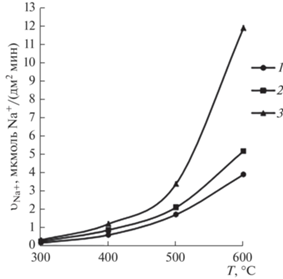
Представленные данные наглядно демонстрируют, что постоянное электрическое поле значительно интенсифицирует выщелачивания стекла CНF2Cl. Это можно объяснить ионизацией газовой среды, в результате которой облегчается процесс обмена катионов щелочных металлов на катионы водорода. На скорость выщелачивания стекла газами в электрическом поле влияют значение напряжения, размеры и форма электродов, расстояние между электродами, материал электродов и другие факторы.
Эксперименты показали, что переменное и импульсное электрические поля, постоянное, переменное и импульсное магнитные поля также усиливают процесс выщелачивания стекла газообразными реагентами. Влияние обработки бутылок газообразными реагентами и постоянным магнитным полем на их свойства дано в табл. 5.
Таблица 5.
Влияние обработки бутылок для соков вместимостью 0.5 л газообразными реагентами и магнитным полем на их свойства
Режим обработки | Состояние стекла | СВГД, МПа | Водоустойчивость стекла, мг Na2O |
---|---|---|---|
1 | Без обработки | 1.34 | 0.092 |
2 | Термомагнитная обработка (постоянное магнитное поле – 0.20 T, температура – 600°C) | 1.67 | 0.092 |
3 | Термохимическая обработка SO2 (температура – 600°C, расход – 0.5 мкмоль/м2) |
1.40 | 0.056 |
4 | Термохимическая обработка CF2Cl2 (температура – 600°C, расход – 0.5 мкмоль/м2) | 1.47 | 0.009 |
5 | Режим обработки 2, а затем 3 | 1.58 | 0.006 |
6 | Режим обработки 2, а затем 4 | 1.89 | 0.000 |
Табличные данные показывают, что термомагнитная обработка повышает механическую прочность на 25%, что согласуется с литературными данными [20]. Наши эксперименты показали, что эффект упрочнения изделий зависит от значения модуля вектора магнитной индукции, температуры стекла и продолжительности обработки. Водоустойчивость стекла под воздействием магнитного поля не изменяется [21].
Термохимическая обработка SO2 и CF2Cl2 резко повышает водоустойчивость стекла, при этом также повышается его механическая прочность, но в меньшей мере, чем при термомагнитной обработке. Совмещение термохимической и термомагнитной обработок приводит к наибольшему повышению механической прочности и водоустойчивости бутылок (см. табл. 5), микротвердости и термостойкости.
ЗАКЛЮЧЕНИЕ
Термохимическая обработка промышленных и синтезированных стекол SO2, NO2, HF, HCl, HBr, CF2Cl2, CHF2Cl и смесями газообразных реагентов приводит к образованию продуктов реакции, содержащих Na+ и K+.
Главными критериями для оценивания интенсивности выщелачивания щелочносиликатных стекол кислыми газами являются толщина и степень выщелачивания поверхностного слоя стекла и скорость экстракции Ме+ из образцов. Наибольшее влияние на интенсивность выщелачивания силикатных стекол газообразными реагентами оказывают температура, химические состава стекла и газовой среды.
Установлена тесная связь физико-химических свойств стекла с условиями термохимической обработки, а также скоростью выщелачивания Na+ кислыми газами, составом и структурой его поверхностного слоя. Анализ полученных результатов позволяет заключить, что для получения максимального эффекта в повышении механических свойств и химической устойчивости изделий термохимическую обработку газообразными реагентами необходимо проводить по режиму, обеспечивающему наибольшую толщину выщелоченного слоя стекла и степень его выщелачивания.
Интенсификации процесса выщелачивания силикатных стекол кислыми газами достигается оптимизацией режимов термохимической обработки и применением эффективных газообразных реагентов и электромагнитных полей.
Список литературы
Безбородов М.А. Химическая устойчивость силикатных стекол. Минск: Наука и техника, 1972. 304 с.
Boow J., Turner W.E.S. Effect of Annealing in a Sulphur Dioxide, Containing Atmosphere on the Modulus of Rupture of Sheet Glass // J. Soc. Glass Technol. 1938. V. 22. P. 356–371.
Coward J.N., Turner W.E.S. The Clouding of Soda-Lime- Silica Glass in Atmospheres Containing Sulphur Dioxide // J. Soc. Glass Technol. 1938. V. 22. P. 309–323.
Peddle C.J. Notes of Annealing Lehrs // J. Soc. Glass Technol. 1937. V. 21. P. 177–186.
Mochel E.L., Nordberg M.E., Elmer T.H. Strengthening of Glass Surfaces by Sulfur Trioxide Treatment // J. Amer. Ceram. Soc. 1966. V. 49. № 11. P. 585–589.
Hense C.R., Mecha J., Schaeffer H.A. Treatment of soda-lime-silica glass surfaces with fluorine-containing gases // Glasstech. Ber. Glass Sci. Technol. 1990. V. 63. № 5. P. 127–134.
Sheth N., Luo J., Banarjee J., Pantano C.G., Kim S.H. Characterization of surface structures of dealkalized soda lime silica glass using X-ray photoelectron, specular reflection infrared, attenuated total reflection infrared and sum frequency generation spectroscopies // J. Non-Cryst. Solids. 2017. V. 474. P. 24–31.
Шарагов В.А. Химическое взаимодействие поверхности стекла с газами. Кишинев: Штиинца, 1988. 130 с.
Пух В.П. Прочность и разрушение стекла. Л.: Наука. Ленингр. отд-ние, 1973. 156 с.
Шелюбский В.И. Особенности определения удельной работы разрушения при ударном изгибе стекла // Стекло и керамика. 1969. № 9. С. 9–12.
Чаквари Б., Бокшаи З., Букэ Г., Ивановская И. Структура поверхностных слоев Мак-Иннеса и Дола при его взаимодействии с растворами // Стеклообразное состояние. Л.: Наука, 1971. С. 310–313.
Sharagov V., Azarenko O. Analysis of surface layers of industrial glasses // Proc. of conf. “Glass in the New Millennium, Challenges and Break-through Technologies”. ICG Annual Meeting. Amsterdam, 2000. PS 4. P. 1–7.
Гороховский В.А., Щербакова В.П. Упрочнение и изменение структуры поверхности оконного стекла при обработке его сернистым газом // Механические и тепловые свойства и строение неорганических стекол. М., 1972. С. 225–230.
Шарагов В.А., Бурковский И.А. Критерии оценивания интенсивности выщелачивания промышленных стекол кислыми газами // Сборник тезисов Международной конференции “Стекло: наука и практика” GlasSP2017. С. 104–106.
Gorokhovsky A.V., Escalante-Garcia J.I. Ion mobility in the surface layers of soda-lime-silicate glass with different thermal history // International Congress on Glass. Extended Abstracts. 2001. V. 2. P. 14–15.
Бутаев А.М. Прочность стекла. Махачкала: Дагестанский гос. университет, 1997. 253 с.
Шарагов В.А., Курикеру Г.И. Особенности химического взаимодействия промышленных стекол с газообразными фторхлорсодержащими реагентами // Физика и химия стекла. 2018. Т. 44. № 4. С. 365–373.
Бабушкин В.И., Матвеев Г.М., Мчедлов–Петросян О.П. Термодинамика силикатов. 4-е изд., перераб. и доп. М.: Стройиздат, 1986. 406 с.
Поллер З. Химия на пути в третье тысячелетие. М.: Мир, 1982. 401 с.
Прангов Л.Г. Технолoгични особености на магнитната обработка на стъкло // Известия на ВМЕИ “Ленин”. 1988. Т. 43. Кн. 5. С. 73–82.
Шарагов В.А. Термомагнитная обработка промышленных стеклоизделий // Развитие технологий будущего: монография. Одесса, 2018. С. 44–54.
Дополнительные материалы отсутствуют.
Инструменты
Физика и химия стекла