Известия РАН. Энергетика, 2021, № 3, стр. 24-41
Обоснование режимов и условий организации процесса газификации твердого органического топлива на основе учета реакционной способности его взаимодействия с диоксидом углерода и водяным паром
Е. А. Бойко 1, *, А. В. Страшников 1, **
1 ФГАОУ ВО “Сибирский федеральный университет”
Красноярск, Россия
* E-mail: EBoiko@sfu-kras.ru
** E-mail: savtr@mail.ru
Поступила в редакцию 09.03.2021
После доработки 23.04.2021
Принята к публикации 26.04.2021
Аннотация
На основе комплексного термического анализа канско-ачинских и кузнецких углей экспериментально получены кинетические параметры процесса газификации коксового нелетучего остатка при взаимодействии с углекислым газом и водяным паром. Установлено, что наблюдается прямо пропорциональная зависимость между максимальной скоростью реагирования коксового остатка с СО2 и Н2О в исследованной температурной области 600–1300°С и максимальной скоростью выделения летучих веществ $\left( {W_{{\text{л}}}^{{\max }}} \right),$ а также повышенная склонность коксовых остатков канско-ачинских углей к участию в реакциях с СО2 и Н2О. Показано, что полученные характеристики реакционной способности коксовых остатков по отношению к углекислому газу и водяному пару могут быть использованы для расчетной оценки протекания процессов термохимического превращения топлива и научно-обоснованного определения оптимальных условий и режимов его газификации в реальных газогенерирующих установках. Предложена технология и техническое решение для многостадийной термохимической обработки твердого органического топлива, предусматривающие организацию трех последовательных стадий в рамках единой конструкции газогенератора с индивидуальными условиями газификации и подводом теплоты при температурах процесса 400, 600 и 800°С.
ВВЕДЕНИЕ
Совершенствованию технологии производства и потребления энергии, вырабатываемой на твердом органическом топливе (бурые и каменные угли, древесина, твердые бытовые отходы), уделяется значительное внимание в энергетической отрасли и жилищно-коммунальном хозяйстве. Существующие проблемы энергетического использования твердых органических топлив в значительной степени можно решить за счет их газификации для получения синтез-газа с последующей выработкой электрической и тепловой энергии в газопоршневых или газотурбинных установках. Хорошая воспламеняемость газообразных продуктов газификации, их удовлетворительная калорийность, высокая реакционная способность и экологическая безопасность открывают широкие возможности для применения данной технологии на электрогенерирующих установках небольшой мощности в системах малой распределенной энергетики при использовании твердых топлив местных месторождений. Однако, вопросы влияния режимов и способов реализации процесса газификации твердого органического топлива на показатели энергетической эффективности газогенерирующего оборудования, надежности его эксплуатации и экологической безопасности требуют дальнейших исследований.
Скорость термохимического превращения твердого органического топлива за счет его термической деструкции и газификации во многом зависит от средней температуры процесса, которая может быть повышена ступенчатым подводом продуктов сгорания к потоку угольной пыли. Экспериментально доказано [1], что достигается значительно более высокая скорость конверсии, если топливо в этом процессе продолжают нагревать. В [1] приведены данные, свидетельствующие о том, что топливо, нагреваемое в процессе газификации от 600 до 700°С, имеет в два раза более высокую реакционную способность, чем при поддержании постоянной температуры 700°С. Полагают, что при газификации топлива и активированном повышением температуры, образуются промежуточные соединения, которые существенно изменяют механизм реакции по сравнению с условиями, имеющимися при постоянной температуре.
В данной статье для практического обоснования эффективности организации ступенчатого подвода тепла в процессе газификации твердого органического топлива выполнено сравнение возможных вариантов реализации данного процесса в газогенерирующей установке на основе исследования и учета кинетики процесса взаимодействия топлива с диоксидом углерода и водяным паром. Для каждого варианта принято ограничение по максимальной температуре зоны газификации после смешения топлива с высокотемпературными газообразными продуктами.
Следует отметить, что при разработке научно-обоснованных рекомендаций по выбору наиболее оптимальных способов и режимов газификации твердых органических топлив необходимо установить связь между качеством исходного топлива и его реакционной способностью по отношению к СО2 и Н2О.
Помимо процессов испарения влаги, термического разложения твердого органического топлива, а также первичных реакций взаимодействия углерода коксовой основы и выделившихся летучих веществ с кислородом, которыми обусловлено образование СО, Н2О и СО2 в области высоких температур, например, при газификации топлива в газогенерирующих установках или в ядре пылеугольного факела, особенно в зоне активного горения камерных топок с жидким шлакоудалением, со значительными скоростями протекают и вторичные реакции восстановления СО2 и Н2О. Это – гетерогенные эндотермические многостадийные реакции, протекающие на поверхности [2]:
Вследствие соударения атомов и молекул с поверхностью нелетучих остатков и благодаря значительным валентным силам образуются промежуточные комплексы. Последние стимулируют электронный перенос, обеспечивая сильные связи между газом и нелетучим коксовым остатком, т.е. хемосорбцию [3]. Экспериментальные исследования реакций углерода с газами [4] свидетельствуют о том, что на поверхности нелетучих остатков диссоциируют и хемосорбируются атомы, а не молекулы. При этом можно говорить об аналогии между хемосорбированным комплексом в гетерогенной реакции и радикалом в гомогенной кинетике. В обоих случаях создаются промежуточные активные соединения. В связи с вышеизложенным эффективным инструментом для определения реакционной способности коксовой основы топлива по отношению к СО2 и Н2О может служить применение комплексного термического анализа [5].
Также, как и в случае использования О2 в качестве окислителя, неизотермическая кинетика взаимодействия коксовой основы с СО2 и Н2О позволяет обойти необходимость учета изменения поверхности реагирования по мере развития процесса [6]. Последнее обстоятельство, оказывающее решающее влияние на оценку константы скорости реагирования при T = const учитывается в неизотермических условиях осреднением кинетических параметров на всем температурном интервале взаимодействия окислителя с нелетучим остатком.
МЕТОДИКА ОПРЕДЕЛЕНИЯ РЕАКЦИОННОЙ СПОСОБНОСТИ
Для изотермического процесса реагирования СО2 и Н2О в объеме коксовой частицы, согласно [7], уравнения скорости реакции имеют соответствующий вид:
(1)
${{W}_{{{\text{C}}{{{\text{O}}}_{{\text{2}}}}}}} = \frac{{d{{C}_{{{\text{C}}{{{\text{O}}}_{{\text{2}}}}}}}}}{{d\tau }} = a{{k}_{{{\text{C}}{{{\text{O}}}_{2}}}}}{{({{P}_{{{\text{C}}{{{\text{O}}}_{{\text{2}}}}}}})}^{n}}(1 - {{C}_{{{\text{C}}{{{\text{O}}}_{2}}}}}),$(2)
${{W}_{{{{{\text{H}}}_{{\text{2}}}}{\text{O}}}}} = \frac{{d{{C}_{{{{{\text{H}}}_{{\text{2}}}}{\text{O}}}}}}}{{d\tau }} = a{{k}_{{{{{\text{H}}}_{{\text{2}}}}{\text{O}}}}}{{({{P}_{{{{{\text{H}}}_{{\text{2}}}}{\text{O}}}}})}^{n}}(1 - {{C}_{{{{{\text{H}}}_{{\text{2}}}}{\text{O}}}}}),$Пропорциональность скорости реагирования окислителя учитывается показателем степени n. Влияние концентрации на скорость процесса подробно исследовано в работе Г.Де Соэте [8]. Классическая работа Е.С. Головиной [9] также выполнялась при различных концентрациях СО2 и Н2О в потоке – 25, 50 и 100%. В работе [9] установлено, что влияние концентрации СО2 и Н2О существенно сказывается при температурах реагирования 1350°С и выше. Обработка К. Вином и сотрудниками [10] экспериментальных данных по газификации углей разных месторождений, полученных различными авторами, показала, что скорости реакции газификации коксовой основы углекислым газом и водяным паром в низкотемпературной области (до 1700°С) можно принимать по первому порядку реакции от концентрации СО2 и Н2О при давлениях ниже и в пределах атмосферного, и по нулевому – при давлениях больше 1.5 МПа.
Уравнения (1) и (2) применимы при отсутствии диффузионных осложнений в объеме коксовой частицы (чисто кинетический режим) [11] при температурах процесса газификации ниже 1350°С, присущих условиям большинства газогенерирующих установок. С увеличением температуры процесса (более 1700°С) они начинают сказываться существенно, что приводит к необходимости вводить дополнительную поправку (фактор эффективности, по [9]), учитывающий изменение концентрации СО2 и Н2О по глубине реагирования.
Использование комплексного термического анализа для оценки реакционной способности коксового остатка натуральных углей по отношению к СО2 и Н2О в неизотермических условиях позволяет на основе уравнений (1) и (2) без специальной оценки коэффициента α и, используя в низкотемпературной области первый порядок реагирования, оценить константу скорости процессов (см3/(моль ⋅ с)) по выражениям:
(3)
${{k}_{{{\text{C}}{{{\text{O}}}_{{\text{2}}}}}}} = \frac{{{{W}_{{{\text{C}}{{{\text{O}}}_{{\text{2}}}}}}}}}{{{{P}_{{{\text{C}}{{{\text{O}}}_{{\text{2}}}}}}}({{C}_{0}} - {{C}_{{{\text{C}}{{{\text{O}}}_{2}}}}})}},$(4)
${{k}_{{{{{\text{H}}}_{{\text{2}}}}{\text{O}}}}} = \frac{{{{W}_{{{{{\text{H}}}_{{\text{2}}}}{\text{O}}}}}}}{{{{P}_{{{{{\text{H}}}_{{\text{2}}}}{\text{O}}}}}({{C}_{0}} - {{C}_{{{{{\text{H}}}_{{\text{2}}}}{\text{O}}}}})}},$Уравнения (3) и (4) имеют вид, аналогичный уравнению, использованному ранее для оценки кинетических характеристик взаимодействия коксового остатка с кислородом воздуха (O2) [6]. Константа скорости k, также как и в случае реакции C + O2, учитывает изменение начальной концентрации реагирующих с СО2 и Н2О активных центров углеродной поверхности с увеличением температуры процесса, а также изменение площади поверхности реагирования коксовых частиц в процессе выгорания в неизотермических условиях [12].
Для определения реакционной способности нелетучего коксового остатка по отношению к углекислому газу и водяному пару использовались фракции бородинского, березовского и назаровского углей Канско-Ачинского и марок Г, СС и Т Кузнецкого бассейнов размером от 1 до 3 мм. Характеристика исследованных углей представлена в табл. 1. Предварительно исходные образцы угля подвергались термическому разложению на установке комплексного термического анализа с использованием термогравиметрического анализатора TGA-701 фирмы Leco в инертной среде (Ge) при скорости нагрева β = 10 град/мин. Непосредственно из термограмм рассчитывались: максимальная скорость выделения летучих веществ ($W_{{\text{л}}}^{{{\text{max}}}},$ мг/(г ⋅ град), соответствующая ей температура ($T_{{\text{л}}}^{{{\text{max}}}},$ °С). Аналогичные характеристики при термическом разложении бородинского угля составили $W_{{\text{л}}}^{{{\text{max}}}}$ = 1.672 мг/(г ⋅ град), $T_{{\text{л}}}^{{{\text{max}}}}$ = 440°С; березовского угля $W_{{\text{л}}}^{{{\text{max}}}}$ = 1.65 мг/(г ⋅ град), $T_{{\text{л}}}^{{{\text{max}}}}$ = 440°С; назаровского угля $W_{{\text{л}}}^{{{\text{max}}}}$ = 1.58 мг/(г ⋅ град), $T_{{\text{л}}}^{{{\text{max}}}}$ = 430°С; кузнецкого Г $W_{{\text{л}}}^{{{\text{max}}}}$ = 2.1 мг/(г ⋅ град), $T_{{\text{л}}}^{{{\text{max}}}}$ = 440°С; кузнецкого СС $W_{{\text{л}}}^{{{\text{max}}}}$ = 0.375 мг/(г ⋅ град), $T_{{\text{л}}}^{{{\text{max}}}}$ = 520°С; кузнецкого Т $W_{{\text{л}}}^{{{\text{max}}}}$ = 0.212 мг/(г ⋅ град), $T_{{\text{л}}}^{{{\text{max}}}}$ = 575°С. Эти результаты находятся в соответствии с данными, полученными при исследовании бурых и каменных углей других месторождений [6, 13].
Таблица 1.
Кинетические параметры процесса взаимодействия нелетучих остатков канско-ачинских и кузнецких углей с СО2
Марка угля | Температура максимума реакции, tmax, °С | Максимальная скорость реакции, Wmax, мг/(г ⋅ град) | Энергия активации, E, кДж ⋅ моль–1 |
Вероятностный фактор, k0, м ⋅ с–1 |
---|---|---|---|---|
Бородинский | 990 | 6.16 | 214.0 | 7.9 × 106 |
Назаровский | 1000 | 7.61 | 221.9 | 3.8 × 106 |
Березовский (рядовой) | 980 | 7.54 | 210.1 | 5.5 × 106 |
Березовский (окисленный) | 980 | 7.88 | 211.2 | 6.2 × 106 |
Березовский (сажистый) | 990 | 8.14 | 208.5 | 2.4 × 106 |
Кузнецкий Г | 1030 | 2.35 | 230.5 | 4.7 × 108 |
Кузнецкий СС | 1080 | 0.7 | 229.4 | 0.5 × 108 |
Кузнецкий Т | 1000 | 0.45 | 209.2 | 2.6 × 108 |
Нелетучие остатки канско-ачинских и кузнецких углей, полученные при термическом анализе в инертной среде с конечной температурой нагрева 900°С, затем подвергались на установке комплексного термического анализа обработке диоксидом углерода и водяным паром в условиях непрерывного подъема температуры. Скорость нагрева в опытах по определению реакционной способности коксовых остатков по отношению к СО2 и Н2О составляла 5 град/мин; концентрация СО2 = 100%, Н2О = = 100% (при атмосферном давлении); масса навески – 150 мг; расход СО2 в печь термогравиметрического анализатора составлял 220–240 см3/мин, расход Н2О = 250–290 см3/мин. В качестве объектодержателя использовались стандартные керамические тарельчатые тигли [11]. Определение оптимальных условий проведения комплексного термического анализа угольного вещества, минимизирующих влияние диффузионных процессов основано на выполнении расчетных и экспериментальных исследования влияния теплообмена на поверхности образца, скорости нагрева, массы навески и размера пылеугольных частиц на характер термогравиметрических кривых [6]. Анализ полученных результатов позволил установить минимальную чувствительность терморегистрирующего прибора (0.0625 см/град), линейную скорость движения тренда (0.01 см/с), минимальный угол наклона термической кривой $t = f(\tau )$ к оси абсцисс (1°), оптимальный диапазон темпа нагрева навески (${{\beta }_{{{\text{опт}}}}}$ = 0.018–20 град/мин, где нижний предел обусловлен ограничением совокупности технических характеристик, верхний – инерционностью установки). С уменьшением размера пылеугольных частиц при постоянной скорости нагрева, величине навески и прочих равных условиях ширина и высота пика теплового эффекта увеличиваются, а температура, соответствующая максимальной скорости реакции, сдвигается в область более высоких температур. Экспериментально подтверждено предположение о независимости значения температуры начала термохимической реакции от условий проведения термоаналитического эксперимента. Для контроля и прогноза области протекания исследуемых процессов при выполнении комплексного термического анализа угольного вещества, обеспечивающего получение объективных кинетических характеристик широкого класса термохимических реакций в зависимости от наиболее значимых режимных факторов, обоснован и применен критерий, характеризующий отношение количества прореагировавшего вещества на единице поверхности в единицу времени (“потока реакции”) к диффузионному потоку через слой продукта
(5)
$\frac{N}{q} = \frac{{\mu {{m}_{0}}}}{{4\pi {{D}_{{\text{c}}}}}}\frac{{\left( {{{r}_{0}} - {{r}_{{\text{п}}}}} \right)}}{{{{r}_{0}}{{r}_{{\text{п}}}}\left( {\mu \rho - \left[ {{{С}_{0}}} \right]} \right)}}\frac{{d\alpha }}{{d\tau }},$При ${N \mathord{\left/ {\vphantom {N q}} \right. \kern-0em} q} \ll 1$ обеспечивается кинетический режим протекания термохимической реакции; при ${N \mathord{\left/ {\vphantom {N q}} \right. \kern-0em} q} \approx 1$ реакция протекает в промежуточной области; при ${N \mathord{\left/ {\vphantom {N q}} \right. \kern-0em} q} \gg 1$ – в диффузионной области. Согласно уравнению (5), факторы, определяющие режимные условия проведения комплексного термического анализа пылевидного твердого топлива, подбираются таким образом, чтобы гарантировать протекание исследуемого процесса в строго кинетической области.
Термограммы процесса реагирования коксовой основы с СО2 и Н2О на примере бородинского угля представлены на рис. 1 и 2. Обработка ТГ-, ДТГ- и Т-кривых, полученных в опытах, осуществлялась по методике, изложенной в работе [6]. Для расчета кинетических параметров взаимодействия СО2 и Н2О с коксовым нелетучим остатком твердого органического топлива использовано уравнение (6):
где k – константа скорости реакции горения коксовых частиц, м/ч; W – скорость реагирования по коксу (скорость убыли массы коксовой навески, определяемая по ДТГ-кривой) в i-ый момент времени (при i-ой температуре), мг/мин.Рис. 1.
Термограмма взаимодействия нелетучего остатка бородинского угля с углекислым газом (СО2) при β = 5 град/мин.
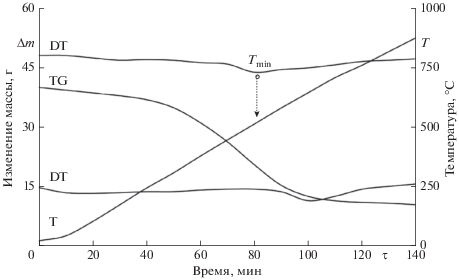
Рис. 2.
Термограмма взаимодействия нелетучего остатка бородинского угля с водяным паром (Н2О) при β = 5 град/мин.
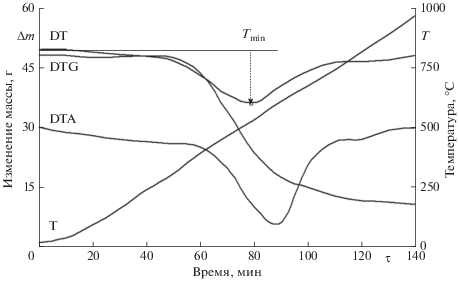
В связи с тем, что по мере газификации коксовых частиц изменяется размер частиц [14] в соответствии с формулой (7) площадь реагирования органической части с газифицирующим агентом, и, следовательно, при прочих равных условиях скорость реакции горения. Характер изменения размера реагирующей коксовой частицы от степени термохимического превращения нелетучего остатка в данной работе описывался зависимостью [6]:
где ${{d}_{i}}$ – текущий (по мере взаимодействия) размер коксовой частицы, м; ${{C}_{0}}$ – начальная масса нелетучего остатка, кг; C – текущая по мере термохимического превращения масса прореагировавшего кокса, кг.ОБСУЖДЕНИЕ РЕЗУЛЬТАТОВ ИССЛЕДОВАНИЯ
Полученные зависимости $W_{{{\text{C}}{{{\text{O}}}_{{\text{2}}}}}}^{{{\text{max}}}},$ $T_{{{\text{C}}{{{\text{O}}}_{{\text{2}}}}}}^{{{\text{max}}}},$ ${{E}_{{{\text{C}}{{{\text{O}}}_{{\text{2}}}}}}},$ ${{k}_{{{\text{0C}}{{{\text{O}}}_{{\text{2}}}}}}}$ и $W_{{{{{\text{H}}}_{{\text{2}}}}{\text{O}}}}^{{{\text{max}}}},$ $T_{{{{{\text{H}}}_{{\text{2}}}}{\text{O}}}}^{{{\text{max}}}},$ ${{E}_{{{{{\text{H}}}_{{\text{2}}}}{\text{O}}}}},$ ${{k}_{{{\text{0}}{{{\text{H}}}_{{\text{2}}}}{\text{O}}}}}$ от содержания углерода на горючую массу (${{C}^{{daf}}}$) дополненные данными других авторов [15, 16] представлены на рис. 3 и 4 и табл. 1 и 2. Как видно из рисунков, экстремальные значения этих величин приходятся на угли с ${{C}^{{daf}}}$ = 87–89%. Общий характер изменения кинетических параметров газификации коксовой основы согласуется с реакционной способностью при стандартном ее определении (рис. 5). На рисунке 5 в качестве показателя степени метаморфизма (ось абсцисс) использована средняя отражательная способность углей по витриниту ($R_{0}^{{{\text{ср}}}}$). Для исследованных топлив (бородинский, березовский, назаровский уголь) величина $R_{0}^{{{\text{ср}}}}$ соответственно равна: 0.87; 1.28; 1.84%. Кроме того, на рис. 3 и 4 представлены дополнительные данные о реакционной способности нелетучих остатков по отношению к СО2 и Н2О некоторых каменных углей [6].
Рис. 3.
Кинетические параметры взаимодействия СО2 с коксовыми остатками углей по данным комплексного термического анализа: ⚪ – соответственно Wmax (мг/(г ⋅ град)) и E (кДж/моль); △ – соответственно Tmax (°С) и k0 × 10–11 (см3/(с ⋅ моль)).
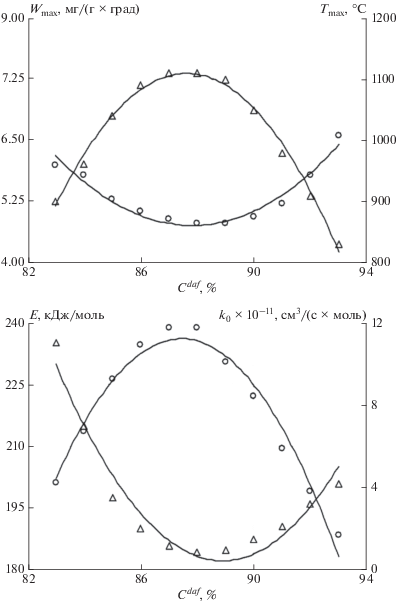
Рис. 4.
Кинетические параметры взаимодействия Н2О с коксовыми остатками углей по данным КТА: ⚪ – соответственно Wmax (мг/(г ⋅ град)) и E (кДж/моль); △ – соответственно Tmax (°С) и k0 × 10–11 (см3/(с ⋅ моль)).
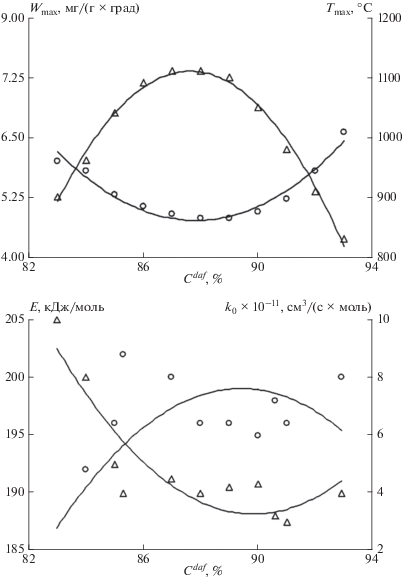
Таблица 2.
Кинетические параметры процесса взаимодействия нелетучих остатков канско-ачинских и кузнецких углей с Н2О
Марка угля | Температура
максимума реакции, tmax, °С |
Максимальная скорость реакции, Wmax, мг/(г ⋅ град) | Энергия активации E, кДж ⋅ моль–1 |
Вероятностный фактор, k0, м ⋅ с–1 |
---|---|---|---|---|
Бородинский | 700 | 1.25 | 191.4 | 2.6 × 105 |
Назаровский | 675 | 1.18 | 189.4 | 2.9 × 105 |
Березовский (рядовой) | 705 | 1.33 | 201.2 | 5.8 × 105 |
Березовский (окисленный) | 440 | 1.15 | 198.2 | 4.2 × 105 |
Березовский (сажистый) | 430 | 1.07 | 190.5 | 2.4 × 105 |
Кузнецкий Г | 530 | 0.32 | 276.3 | 1.7 × 107 |
Кузнецкий СС | 575 | 0.25 | 284.4 | 2.5 × 107 |
Кузнецкий Т | 560 | 0.27 | 286.2 | 2.6 × 107 |
Рис. 5.
Реакционная способность коксовых остатков канско-ачинских углей (стандартный метод): ⚪ – по отношению к СО2; △ – по отношению к Н2О.
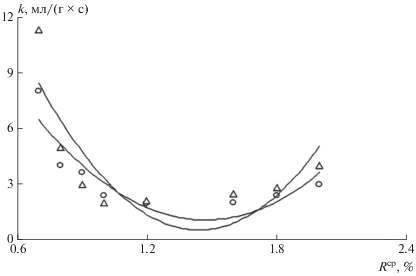
По данным С.П. Родькина [17], для предварительной оценки реакционной способности коксового остатка по отношению к СО2 и Н2О при использовании комплексного термического анализа в неизотермических условиях следует ориентироваться на величину максимальной скорости (Wmax, мг/(г ⋅ град)), оценка которой в данном случае не представляет затруднений. Значение Wmax чувствительно к свойствам исходного материала, из которого получен коксовый остаток, а также к условиям его получения; существует тесная связь между W max и показателем реакционной способности по ГОСТ 10089-62 (коэффициент корреляции составляет 0.84); наблюдается прямопропорциональная зависимость между максимальной скоростью реагирования коксового остатка с СО2 и Н2О в исследованной температурной области 600–1300°С и максимальной скоростью выделения летучих веществ $\left( {W_{{\text{л}}}^{{{\text{max}}}}} \right)$ [6]; коэффициент корреляции этой связи для СО2 составляет 0.78, для Н2О – 0.84.
Рис. 6.
Корреляционная зависимость между максимальными скоростями термического разложения $\left( {W_{{\text{л}}}^{{{\text{max}}}}} \right)$ и взаимодействия СО2 (⚪) и Н2О (Δ) с коксовыми остатками (Wmax) канско-ачинских углей (полифракция).
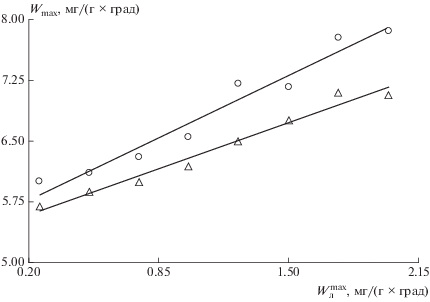
Подтверждение вышеизложенному получено в работе Г.П. Алаева [18] применительно к исследованию реакций газификации петрографических микрокомпонентов слабоспекающихся углей Кузбасса. Пользуясь этими выводами, можно отметить повышенную склонность коксовых остатков канско-ачинских углей к участию в реакциях с СО2 и Н2О. Этот вывод имеет важное значение при газификации и пылеугольном сжигании энергетических углей, в частности, канско-ачинских, и он полностью коррелирует с результатами комплексного термического анализа по отношению к кислороду и опытно-промышленных испытаний газогенерирующих установок при использовании бородинских, березовских и назаровских углей [18–20].
Практическая значимость полученных результатов заключается в научно-обоснованном подходе к учету протекания восстановительных реакций в зависимости от исходного качества топлива [20].
Полученные характеристики реакционной способности коксовых остатков по отношению углекислому газу и водяному пару используются в дальнейшем для научно-обоснованного выбора оптимальных условий и режимов газификации твердого органического топлива в реальных газогенерирующих установок. В частности, ключевым вопросом эффективности работы газогенерирующих установок является вопрос организации конкретного числа ступеней подвода тепла, температурного режима и динамики распределения процесса газификации топлива по времени.
ОБОСНОВАНИЕ РЕЖИМОВ И УСЛОВИЙ ОРГАНИЗАЦИИ ПРОЦЕССА ГАЗИФИКАЦИИ ТВЕРДОГО ОРГАНИЧЕСКОГО ТОПЛИВА
В первом традиционном варианте (рис. 7а) все топливо смешивается сразу с газифицирующим агентом (высокотемпературным газом) [19]. Для реализации процесса по формированию стадий газификации с индивидуальными температурными условиями (второй альтернативный вариант, рис. 7б) высокотемпературный газифицирующий агент делят на несколько частей, который последовательно и ступенчато подмешивают к топливу таким образом, чтобы температура на каждой стадии процесса газификации имела индивидуальный характер и не превышала заданного максимального значения [21].
Рис. 7.
Расчетные схемы разных способов организации процесса газификации твердого органического топлива: (а) с подводом всего количества теплоты в начале процесса; (б) со ступенчатым подводом теплоты; 1 – камера сгорания части топлива для получения высокотемпературных продуктов сгорания; 2 – смеситель; 3 – камера термообработки; 4 – подвод части топлива для получения высокотемпературных продуктов сгорания; 5 – подвод основной части топлива на термообработку; 6 – подвод газов рециркуляции; 7 – подвод воздуха; 8 – тракт продуктов сгорания для ступенчатого подвода теплоты; 9 – ступени термохимической обработки; 10 – отвод газообразных продуктов термохимического превращения угля.
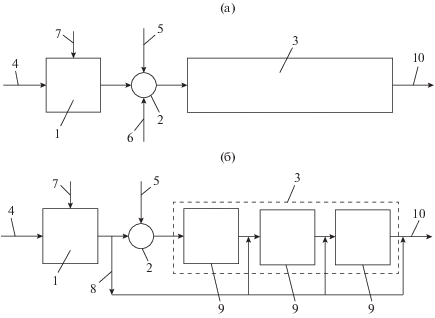
Скорости химических реакций при газификации твердого органического топлива (на примере бородинского угля) описываются следующими уравнениями:
(8)
${{W}_{{{{{\text{H}}}_{{\text{2}}}}{\text{O}}}}} = \frac{{3.44 \times {{{10}}^{5}}}}{{{{T}_{{{\text{тп}}}}}}}{{C}_{{{{{\text{H}}}_{{\text{2}}}}{\text{O}}}}}\exp \left( { - \frac{{16000}}{{{{T}_{{{\text{тп}}}}}}}} \right);\,\,\,\,{{W}_{{{\text{C}}{{{\text{O}}}_{{\text{2}}}}}}} = \frac{{9.0 \times {{{10}}^{5}}}}{{{{T}_{{{\text{тп}}}}}}}{{C}_{{{\text{C}}{{{\text{O}}}_{2}}}}}\exp \left( { - \frac{{17500}}{{{{T}_{{{\text{тп}}}}}}}} \right),$Эффективность сравниваемых вариантов определяется отношением скоростей реакций, протекающих при газификации топлива:
– для водяного пара
(9)
$\frac{{W_{{{{{\text{H}}}_{{\text{2}}}}{\text{O}}}}^{1}}}{{W_{{{{{\text{H}}}_{{\text{2}}}}{\text{O}}}}^{2}}} = \frac{{T_{{{\text{тп}}}}^{2}}}{{T_{{{\text{тп}}}}^{1}}}\exp \left[ { - \frac{{16{\kern 1pt} 000\left( {T_{{{\text{тп}}}}^{2} - T_{{{\text{тп}}}}^{1}} \right)}}{{T_{{{\text{тп}}}}^{1}T_{{{\text{тп}}}}^{2}}}} \right],$(10)
$\frac{{W_{{{\text{C}}{{{\text{O}}}_{{\text{2}}}}}}^{1}}}{{W_{{{\text{C}}{{{\text{O}}}_{{\text{2}}}}}}^{2}}} = \frac{{T_{{{\text{тп}}}}^{2}}}{{T_{{{\text{тп}}}}^{1}}}\exp \left[ { - \frac{{17{\kern 1pt} 500\left( {T_{{{\text{тп}}}}^{2} - T_{{{\text{тп}}}}^{1}} \right)}}{{T_{{{\text{тп}}}}^{1}T_{{{\text{тп}}}}^{2}}}} \right],$Температура процесса газификации твердого органического топлива определяется как среднеарифметическая величина температур смеси на входе и выходе из каждой расчетной стадии. Приняв температуру гетерогенной смеси на входе в устройство по газификации топлива (ступень, стадия) – t', определим температуру гетерогенной смеси на выходе из устройства (ступени, стадии) – t" путем составления теплового баланса установки по газификации топлива, с учетом термического разложения топлива и физико-химического механизма реагирования твердых нелетучих остатков с газифицирующим агентом (высокотемпературными газообразными продукты сгорания части топлива).
Определим температуру t" на выходе из ступени газификации твердого органического топлива высоковлажными газообразными продуктами:
где n – число ступеней предварительной термической обработки твердого органического топлива; k – индекс рассчитываемой ступени; Gy, Gk + 1, Gг, ${{G}_{{{\text{C}}{{{\text{O}}}_{{\text{2}}}}}}},$ GCO, Gгп – соответственно расход угля высокотемпературных газообразных продуктов для повышения температуры гетерогенной смеси перед (k + 1)-ой ступенью, первоначальный расход газифицирующего агента, диоксида углерода, оксида углерода и синтез-газа, кг/с; $с_{{\text{y}}}^{'},$ ${{с}_{{{\text{г,кс}}}}},$ $с_{{\text{г}}}^{'},$ $с_{{{\text{С}}{{{\text{О}}}_{2}}}}^{'},$ $с_{{{\text{СО}}}}^{'},$ $с_{{{\text{гп}}}}^{'}$ – соответственно теплоемкость угля газифицирующего агента, дымовых газов, диоксида углерода, оксида углерода и синтез-газа при температуре t', кДж/(кг ⋅ град);




На рисунке 8 показано изменение температуры процесса газификации твердого органического топлива в зависимости от величины изменения массы прореагировавшего топлива, при условии ограничения максимальной температуры гетерогенной смеси.
Рис. 8.
Зависимость температуры процесса газификации твердого органического топлива (Ттп, °С) от величины массы прореагировавшего вещества (m, доли) при максимальной температуре 1000°С: 1 – подвод всех продуктов сгорания в начале процесса; 2 – ступенчатый подвод газифицирующего агента в равном соотношении; 3 – ступенчатый подвод газифицирующего агента в неравном соотношении (по нарастающей).
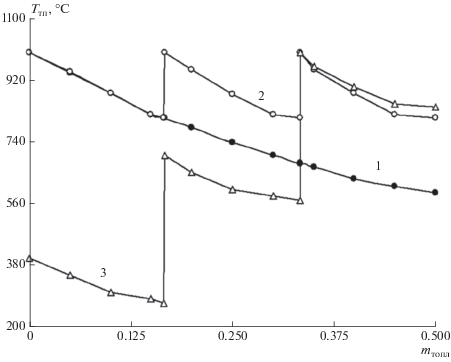
Необходимо отметить, что ступенчатый подвод теплоты в процессе термической обработки и газификации топлива повышает скорость процессов термического разложения и физико-химического реагирования нелетучего остатка с водяными парами и углекислым газом. Так, при трех ступенях подвода теплоты и термохимического превращения 50% органической массы топлива скорость процесса увеличивается в 2.5–2.8 раза для кузнецких и канско-ачинских углей. При этом эффективность ступенчатого подвода тепла будет еще выше, если температуру процесса на каждой ступени термообработки поддерживать не постоянную, а увеличивать ее по мере увеличения номера ступени (кривая 3 на рис. 8). Предлагается на первой ступени температуру процесса поддерживать на уровне 400°С, на второй – 600°С и на третьей – 800°С. Такая последовательная стадийная организация процесса газификации топлива обеспечивает наибольшую его неизотермичность, что позволяет повысить эффективность процесса еще на 15–20%, снизить затраты топлива на получение высокотемпературных продуктов сгорания, рационально реализовать схему и конструкцию устройства для практического осуществления процесса с учетом физико-химических свойств исходного топлива. Предполагается, что в первой ступени протекает процесс глубокой сушки топлива с выделением балластных летучих веществ (преимущественно углекислого газа). Во второй ступени осуществляется глубокая термическая деструкция топлива, сопровождаемая выделением низкокалорийных газообразных летучих веществ (оксида углерода, метана, водорода и т.д.). В третьей ступени осуществляется газификация топлива с выделением синтез-газа и основной массы высококалорийных парогазовых компонентов.
Для определения длительности процесса термохимической обработки и газификации топлива выражения (8) представим в следующем виде
(13)
${{W}_{{{{{\text{H}}}_{{\text{2}}}}{\text{O}}}}} = \frac{1}{{{{T}_{{{\text{тп}}}}}}}\frac{{d{{C}_{{{{{\text{H}}}_{{\text{2}}}}{\text{O}}}}}}}{{d\tau }};\,\,\,\,{{W}_{{{\text{C}}{{{\text{O}}}_{{\text{2}}}}}}} = \frac{1}{{{{T}_{{{\text{тп}}}}}}}\frac{{d{{C}_{{{\text{C}}{{{\text{O}}}_{2}}}}}}}{{d\tau }}.$Откуда находим время протекания процессов:
(14)
${{\tau }_{{{{{\text{H}}}_{{\text{2}}}}{\text{O}}}}} = - \frac{{\ln \left( {1 - \frac{{{{C}_{{{{{\text{H}}}_{{\text{2}}}}{\text{O}}}}}}}{{C_{{{{{\text{H}}}_{{\text{2}}}}{\text{O}}}}^{'}}}} \right)}}{{{\text{0}}{\text{.344}} \times {\text{1}}{{{\text{0}}}^{{\text{6}}}}\exp \left( { - \frac{{16{\kern 1pt} 000}}{{{{T}_{{{\text{тп}}}}}}}} \right)}},$(15)
${{\tau }_{{{\text{С}}{{{\text{O}}}_{{\text{2}}}}}}} = - \frac{{\ln \left( {1 - \frac{{{{C}_{{{\text{C}}{{{\text{O}}}_{{\text{2}}}}}}}}}{{C_{{{\text{C}}{{{\text{O}}}_{{\text{2}}}}}}^{'}}}} \right)}}{{{\text{0}}{\text{.9}} \times {\text{1}}{{{\text{0}}}^{{\text{6}}}}\exp \left( { - \frac{{17{\kern 1pt} 500}}{{{{T}_{{{\text{тп}}}}}}}} \right)}},$Выражения (11), (12), (14) и (15) позволяют рассчитать динамику процесса газификации твердого органического топлива при различном числе ступеней подвода теплоты. На рисунке 9 представлены результаты расчета динамики процесса термической подготовки бородинского угля при организации ступенчатой термохимической обработки и газификации твердого органического топлива.
Рис. 9.
Расчетная динамика процесса термохимической обработки и газификации твердого органического топлива при максимальной температуре 1000°С.
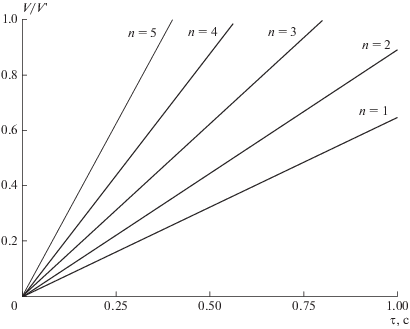
Расчеты показывают, что время пребывания твердого органического топлива в газогенераторе зависит от числа ступеней ni подвода продуктов сгорания. При этом получена следующая универсальная зависимость определения времени термообработки от количества ступеней подвода тепла
(16)
$\frac{{{{\tau }_{1}}{{n}_{2}}}}{{{{n}_{1}}{{\tau }_{2}}}} = \frac{{{{\tau }_{2}}{{n}_{3}}}}{{{{n}_{2}}{{\tau }_{3}}}} = ... = \frac{{{{\tau }_{i}}{{n}_{{i + 1}}}}}{{{{n}_{i}}{{\tau }_{{i + 1}}}}},$Необходимый температурный уровень процесса газификации топлива на каждой стадии достигается посредством сжигания части топлива с помощью воздуха, дозируемого индивидуально через регуляторы, режим работы которых задается устройством регулирования с учетом реакционной способности по отношению к СО2 и Н2О на основе данных комплексного термического анализа. Таким образом, организация многостадийной термохимической обработки и газификации топлива позволяет повысить эффективность процесса, повысить калорийность синтез-газа, обеспечить возможность регулирования условий и режима газификации в зависимости от качества исходного топлива.
Реализация вышеизложенного подхода к формированию условий и режимов газификации твердого органического топлива на основе учета реакционной способности его взаимодействия с диоксидом углерода и водяным паром позволяет не только выполнить оптимизацию конструктивных и режимных параметров перспективных газогенерирующих установок промышленного исполнения, но и сформировать систему автоматического контроля и управления процессом газификации с позиции обеспечения его максимальной энергетической эффективности.
ЗАКЛЮЧЕНИЕ
Исследованы процессы взаимодействия коксовой основы твердого органического топлива с углекислым газом и водяными парами. Экспериментально полученные на основе комплексного термического анализа канско-ачинских и кузнецких углей кинетические параметры процесса газификации коксового остатка. Установлено, что характер изменения показателей реакционной способности бурых и каменных углей носит экстремальный характер в зависимости от содержания углерода на горючую массу в исходном топливе с экстремумом при Cdaf = 87–89%.
Значения максимальной скорости реакции (Wmax, мг/(г ⋅ град)) чувствительны к свойствам исходного материала, из которого получен коксовый остаток, а также к условиям его получения. Наблюдается прямо пропорциональная зависимость между максимальной скоростью реагирования коксового остатка с СО2 и Н2О в исследованной температурной области 600–1300°С и максимальной скоростью выделения летучих веществ $\left( {W_{{\text{л}}}^{{{\text{max}}}}} \right).$ Следует отметить повышенную склонность коксовых остатков канско-ачинских углей к участию в реакциях с СО2 и Н2О.
Показано, что полученные характеристики реакционной способности коксовых остатков по отношению к углекислому газу и водяному пару могут быть использованы для расчетной оценки протекания процессов термохимического превращения топлива и научно-обоснованного определения оптимальных условий и режимов его газификации в реальных газогенерирующих установках.
Предложены технология и техническое решение для многостадийной термохимической обработки твердого органического топлива, предусматривающие организацию трех последовательных стадий в рамках единой конструкции газогенератора с индивидуальными условиями газификации и подводом теплоты при температурах процесса 400, 600 и 800°С.
Список литературы
Донской И.Г., Козлов А.Н., Свищев Д.А., Шаманский В.А. Расчетное исследование эффективности ступенчатого процесса газификации влажной древесины // Теплоэнергетика. 2017. № 4. С. 21–29.
Бойко Е.А., Страшников А.В. Когенерационная энергетическая установка на основе газификации твердого органического топлива для нужд малой распределенной энергетики // Промышленная энергетика. 2020. № 2. С. 34–43.
Donskoy I., Svishchev D., Ryzhkov A. Reduced-order modeling of pulverized coal stages gasification: influence of primary and secondary fuel proportion // Energy system research. 2018. T. 1. № 4. P. 27–35.
Астановский Д.Л., Астановский Л.З., Кустов П.В., Бурданов А.В. Переработка угля в местах его добычи по технологии фаст-инжиниринг // Кокс и химия. 2020. № 7. С. 8–13.
Сучков С.И., Сомов А.А. Разработка мер подавления образования оксидов азота в ПГУ с внутрицикловой газификацией угля // Известия РАН. Энергетика. 2015. № 4. С. 84–92.
Бойко Е.А. Реакционная способность энергетических углей // Красноярск: ИПЦ СФУ, 2011. С. 606.
Lopez F.C.R., Tannous K. Coconut fiber pyrolysis decomposition kinetics applying single- and multi-step reactions models // Thermochimica Acte. 2020. № 691. P. 1–12.
De Soete G.G. Aspects chimiques de la combustion du charbon pulverize. Part 1 // Revue de Insitut Francais du Petrole. 2002. № 3. P. 403–424.
Головина Е.С. Высокотемпературное горение и газификация углерода. М.: Энергоатомиздат, 1983. С. 176.
Win C.J. A kinetics study of reaction of coal char with hydrogen – steam mixtures; fuel gasification; advances in chemistry series // Am. Chem. Soc. Washington. 1997. № 9. P. 253–274.
Boiko E.A. Research on kinetics of the thermal processing of brown coals of various oxidative ageing degree using the non-isothermal methods // Thermochim. Acta. 2000. № 348. P. 97–104.
Бойко Е.А., Пачковский С.В., Дидичин Д.Г. Экспериментально-расчетная методика оценки кинетических процессов термохимического превращения твердых органических топлив // Физика горения и взрыва. 2005. № 1. С. 55–65.
Babiskiy P., Labojko G., Kotyczka-Moranska M., Shiazko M. Kinetics of pressurized oxy-combustion of coal chars // Thermochnica Acta. 2019. № 682. P. 569–588.
Досумов К., Ергазиева Г.В., Ермагамбет Г.Т., Нуралиев Н.У., Мироненко А.В. Получение синтез-газа газификацией угля и углекислотной конверсией метана // Горение и плазмохимия. 2019. Т. 17. № 2. С. 110–116.
Draiden S. The chemical Reactivity of Carbons // Carbon. 2008. V. 6. P. 213–221.
Peters A.A., Papavasiliou D., Batos K., Vasalos I. Product distribution and kinetic predictions of Greek lignite pyrolysis // Fuel. 2010. № 10. P. 1304–1308.
Родькин С.П., Зорин Т.А., Казачков А.И., Юсупова Е.А. Дериватографический метод исследования коксов в окислительной среде // Кокс и химия. 1984. № 8. С. 22–25.
Алаев Г.П., Федчишин В.В. Определение степени выгорания пылеугольного факела в вихревой камере горения котла Е-500-140ВЖ // Известия СО АН. Серия технические науки. 1990. Вып. № 6. С. 103–105.
Исламов С.Р. Частичная газификация угля // М: Горное дело, 2017. С. 384.
Rosdam-Abadi M., Debar J.A., Chen W.T. Combustion studies of coal derived solid fuels by thermogravimetric analysis. III. Correlation between burnout temperature and carbon combustion efficiency // Thermochimica Acta. 2017. № 4. P. 358–367.
Бойко Е.А., Страшников А.В., Охремчук А.Е., Казанцев В.П. Двухрежимный газогенератор // Патент на полезную модель RU 191623 U1. 2020.
Дополнительные материалы отсутствуют.
Инструменты
Известия РАН. Энергетика