Неорганические материалы, 2019, T. 55, № 7, стр. 702-704
Получение и свойства композиционных электрохимических покрытий на основе сплава никель–хром, модифицированных нитратом графита
В. Н. Целуйкин *
Энгельсский технологический институт (филиал) Саратовского государственного технического университета
им. Ю.А. Гагарина
413100 Саратовская обл, Энгельс, пл. Свободы, 17, Россия
* E-mail: tseluikin@mail.ru
Поступила в редакцию 18.04.2018
После доработки 05.12.2018
Принята к публикации 27.12.2018
Аннотация
Получены композиционные электрохимические покрытия (КЭП) на основе сплава никель–хром, модифицированные нитратом графита. В потенциодинамическом режиме исследован процесс электроосаждения указанных покрытий. Изучено влияние концентрации дисперсной фазы и катодной плотности тока на микротвердость КЭП никель–хром–нитрат графита.
ВВЕДЕНИЕ
Электрохимическое осаждение сплавов – более сложный процесс по сравнению с катодным выделением индивидуальных металлов: в данном случае требуется строгий контроль над составом электролита и режимом электролиза. Электроосаждение сплавов является одним из случаев протекания параллельных электрохимических процессов при их взаимном влиянии. Это проявляется в том, что поляризационные кривые, как правило, отличаются от соответствующих кривых, полученных при индивидуальном осаждении каждого компонента из электролита того же состава. Когда парциальная кривая смещена в отрицательную сторону по сравнению с индивидуальной, имеет место сверхполяризация при выделении этого компонента. В противоположном случае говорят о деполяризации [1].
Вместе с тем, электролитические сплавы зачастую имеют более высокие характеристики по сравнению с их чистыми компонентами. Одними из наиболее распространенных являются различные сплавы на основе никеля [1–7]. В частности, электрохимические сплавы никель–хром, которые используются в качестве твердых износостойких и коррозионностойких покрытий [1, 3, 7]. Функциональные свойства электролитических осадков можно улучшить, внедряя в их матрицу различные дисперсные частицы. Для этого используется метод осаждения композиционных электрохимических покрытий (КЭП) [8–10].
Эффективность применения КЭП во многом определяется природой и свойствами дисперсной фазы [10]. Интерес в качестве дисперсных материалов композиционных покрытий представляют графит и его производные. Графит обладает слоистой структурой. Внедрением различных молекул или ионов в межслоевое пространство его кристаллической решетки получают т.н. соединения внедрения графита [11]. При взаимодействии графита с азотной кислотой в присутствии сильных окислителей образуется нитрат графита.
Цель работы – получить КЭП на основе сплава никель–хром с нитратом графита в качестве дисперсной фазы и исследовать влияние различных факторов на их микротвердость.
ЭКСПЕРИМЕНТАЛЬНАЯ ЧАСТЬ
Осаждение КЭП никель–хром–нитрат графита проводилось из электролита следующего состава, г/л: NiSO4 ⋅ 7H2O – 28, Cr2(SO4)3 ⋅ 6H2O – 150, H3BO3 – 20, (NH4)2SO4 – 40; нитрат графита – 0.5–2.5. Размеры частиц дисперсной фазы не превышали 10 мкм. Электроосаждение КЭП осуществлялось на стальную основу (сталь 45) при температуре 50°С с постоянным перемешиванием электролита. Чистый сплав никель–хром осаждался из раствора приведенного состава без добавки нитрата графита.
В работе использовался нитрат графита, синтезированный анодным окислением дисперсного порошка графита ГСМ-1 в потенциостатическом режиме. Рабочим электродом служил дисперсный графит, противоэлектродом – платина. Частицы графита к токоотводу поджимались подвижным поршнем, который в процессе реакции внедрения перемещался.
Микротвердость осадков по Виккерсу (HV) измерялась с помощью прибора ПМТ-3. В электролитические осадки статически вдавливалась четырехгранная алмазная пирамида под нагрузкой 10 H. Расстояние между отпечатками составляло не менее двух диагоналей. Форма отпечатка – квадрат. На основании проведенных испытаний определялись величины обеих диагоналей отпечатка. Расчет HV проводился по данным пяти параллельных опытов. Погрешность измерений составляла 3%.
Состав композиционных покрытий исследовался методом лазерного микроспектрального анализа [12]. Использовался лазерный спектроаналитический комплекс, включающий в себя лазер на Nd:YAG (длина волны 1.06 мкм), работающий в режиме гигантского импульса (длительность импульса 9 нс). Частота следования импульсов 25 Гц. Система регистрации – дифракционный спектрограф ДФС-458С и ПЗС-приставка МИРС, включающая в себя блок из восьми ПЗС-приемников, плату сопряжения с компьютером и соответствующее программное обеспечение SPEKTRAN 8, позволяющее проводить качественный и количественный спектральный анализ, а также математическую обработку данных.
Электрохимические измерения проводились на импульсном потенциостате P-30S. Потенциалы задавались относительно насыщенного хлоридсеребряного электрода сравнения и пересчитывались по водородной шкале.
РЕЗУЛЬТАТЫ И ОБСУЖДЕНИЕ
На потенциодинамических поляризационных кривых наблюдается сдвиг потенциала в область более электроотрицательных значений при введении дисперсии нитрата графита в электролит осаждения сплава никель–хром (рис. 1). Данный эффект указывает на протекание катодного процесса со сверхполяризацией: токи при электроосаждении КЭП никель–хром–нитрат графита уменьшаются по сравнению с покрытиями без дисперсной фазы. Вероятно, уменьшение скорости процесса при введении в электролит нитрата графита связано с тем, что в составе дисперсной фазы и в объеме электролита находятся разноименные анионы (нитрат- и сульфат-ионы соответственно). Электростатическое взаимодействие дисперсной фазы с анионами электролита приводит к некоторому уменьшению скорости процесса осаждения композиционных покрытий по сравнению с чистыми сплавами никель–хром.
Рис. 1.
Потенциодинамические поляризационные кривые осаждения сплава никель–хром: 1 – без добавки; 2 – совместно с нитратом графита.
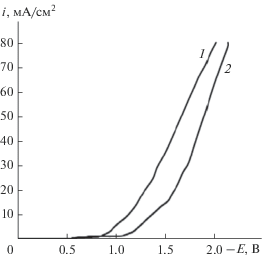
Перенос дисперсных частиц к катоду может осуществляться не только вследствие конвекции, но и за счет их адсорбционного взаимодействия с катионами осаждаемых металлов [9]. Ионы, адсорбированные на частицах, способствуют связыванию дисперсной фазы с поверхностью катода. Данное связывание способствует ослаблению давления жидкостной прослойки между частицей и катодом (расклинивающее давление). В результате усиливается адгезия. На катодной поверхности дисперсные частицы выступают в качестве центров кристаллизации, определяя дальнейший рост электролитического осадка.
Включение дисперсных частиц в покрытие приводит к структурным изменениям металлической матрицы [8–10]. Это в свою очередь должно сказываться на эксплуатационных свойствах покрытия. Существенный интерес в практическом отношении представляют физико-механические характеристики металлических поверхностей и, в частности, микротвердость.
Проведенные исследования показали, что микротвердость электролитических осадков никель–хром–нитрат графита возрастает как с увеличением содержания дисперсной фазы в электролите (табл. 1), так и с ростом катодной плотности тока (табл. 2). Можно предположить, что внедрение частиц нитрата графита в матрицу сплавов приводит к их уплотнению и формированию мелкокристаллических покрытий. А включение в осадки водорода и гидроксидов способствует деформированию и сжатию кристаллов покрытия [1]. Согласно данным лазерного микроспектрального анализа, содержание хрома в КЭП возрастает по мере продвижения от подложки к поверхностным слоям осадков (рис. 2). Кроме того, лазерный микроспектральный анализ показал, что обогащение КЭП хромом происходит при увеличении катодной плотности тока. Данные факторы также обусловливают рост микротвердости изученных покрытий.
Таблица 1.
Влияние концентрации нитрата графита в электролите на микротвердость HV КЭП никель–хром–нитрат графита, полученных при плотности катодного тока ik = 10 А/дм2
Концентрация нитрата графита, г/л | HV100, МПа |
---|---|
0 | 4423 |
1.0 | 4707 |
1.5 | 4933 |
2.0 | 5158 |
2.5 | 6149 |
ЗАКЛЮЧЕНИЕ
На основании проведенных исследований установлено, что при введении дисперсной фазы нитрата графита в электролит осаждения сплава никель–хром формируются композиционные покрытия. Значения микротвердости КЭП никель–хром–нитрат графита возрастают как с увеличением содержания дисперсной фазы в электролите, так и с ростом катодной плотности тока.
Список литературы
Гамбург Ю.Д. Электрохимическая кристаллизация металлов и сплавов. М.: Янус-К, 1997. 384 с.
Ваграмян А.Т., Жамагорцянц М.А. Электроосаждение металлов и ингибирующая адсорбция. Л.: Наука, 1981. 210 с.
Вячеславов П.М. Электролитическое осаждение сплавов. Л.: Машиностроение, 1986. 112 с.
Liquin Z., Quinpeng Z., Jianhua L. Amorphous Nickel–Tungsten–Boron Composite Electrodeposits With Zirconium Oxide Particles // Metal Finishing. 2001. V. 99. № 7. P. 28–30.
Meenu S., Grips V.K., Rajam K.S. Structure and Properties of Electrodeposited Ni–Co–YZA Composite Coatings // J. Appl. Electrochem. 2008. V. 38. № 5. P. 669–677.
Torabinejad V., Aliofkhazraei M., Assareh S., Allahyarzadeh M.H., Sabour Rouhaghdam A. Electrodeposition of Ni–Fe Alloys, Composites and Nano Coatings – A review // J. Alloys Compd. 2017. V. 691. P. 841–859.
Виноградов С.Н., Синенкова О.К. Электроосаждение и физико-механические свойства покрытия сплавом никель-хром // Журн. прикл. химии. 2007. Т. 80. № 10. С. 1638–1640.
Антропов Л.И., Лебединский Ю.Н. Композиционные электрохимические покрытия и материалы. Киев: Техника, 1986. 200 с.
Сайфуллин Р.С. Физикохимия неорганических полимерных и композиционных материалов. М.: Химия, 1990. 240 с.
Целуйкин В.Н. О структуре и свойствах композиционных электрохимических покрытий // Физикохимия поверхности и защита материалов. 2016. Т. 52. № 2. С. 171–184.
Фиалков А.С. Углерод, межслоевые соединения и композиты на его основе. М.: Аспект-пресс, 1997. 718 с.
Павлычева Н.К., Пеплов А.А., Демин А.П. Малогабаритный спектрометр широкого применения // Опт. журн. 2007. Т. 74. № 3. С. 29–32.
Дополнительные материалы отсутствуют.
Инструменты
Неорганические материалы