Неорганические материалы, 2022, T. 58, № 3, стр. 341-348
Керамика на основе фосфата NaRe2(PO4)3 со структурой коснарита как матрица для иммобилизации технеция
Л. С. Алексеева 1, *, А. В. Нохрин 1, А. И. Орлова 1, М. С. Болдин 1, Е. А. Ланцев 1, А. А. Мурашов 1, К. К. Корченкин 2, Д. В. Рябков 2, В. Н. Чувильдеев 1
1 Нижегородский государственный университет им. Н.И. Лобачевского
603022 Нижний Новгород, пр. Гагарина, 23, Россия
2 АО “Радиевый институт им. В.Г. Хлопина”
194021 Санкт-Петербург, 2-й Муринский пр., 28, Россия
* E-mail: golovkina_lyudmila@mail.ru
Поступила в редакцию 18.11.2021
После доработки 20.12.2021
Принята к публикации 22.12.2021
- EDN: FMXVQX
- DOI: 10.31857/S0002337X22030010
Аннотация
Методом электроимпульсного плазменного спекания получена керамика на основе фосфата NaRe2(PO4)3 со структурой минерала коснарита. Рений (Re) использовался в качестве химического и структурного аналога технеция. Относительная плотность керамики 85%. Изучен механизм выщелачивания Re из керамики NaRe2(PO4)3 в статическом режиме при комнатной температуре. Скорость выщелачивания рения составила 1.3 × 10–5 г/(см2 сут).
ВВЕДЕНИЕ
Технеций-99 (99Tc) является одним из наиболее распространенных и долгоживущих радиотоксичных изотопов в отработанном ядерном топливе (ОЯТ). Он является одним из ключевых элементов в стратегиях разделения ОЯТ, таких как UREX+, для изоляции и инкапсуляции в твердых формах отходов [1]. Иммобилизация 99Tc является сложной научной и практической задачей. К настоящему моменту исследована иммобилизация 99Tc в формах металлических сплавов [2–4], цементов [5–7] и стекол [2, 8, 9]. В наиболее широко применяемом процессе стеклования высокоактивных радиоактивных отходов (РАО) часть технеция окисляется или подвергается диспропорционированию и, следовательно, испаряется в виде гептаоксида, что приводит к загрязнению окружающей среды. Альтернативный подход к иммобилизации 99Tc заключается во введении катиона в минералоподобную матрицу [10–16], что потенциально позволит избежать образования высокомобильных пертехнетатных ионов ${\text{TcO}}_{4}^{ - }$ при переработке РАО.
В работах [13, 14] изучены Tc-содержащие соединения со структурами пирохлора (Nd2Tc2O7), перовскита (SrTcO3) и слоистого перовскита (Sr2TcO4). Проведенные в течение 28 дней гидролитические испытания керамики на основе пирохлора Nd2Tc2O7 позволили установить, что скорость выщелачивания Tc составляет 1.48 × × 10–7 г/(мм2 сут) и примерно в 4 раза ниже, чем скорость выщелачивания из боросиликатного стекла (~6.43 × 10–7 г/(мм2 сут)). Недостатком исследованных в [13, 14] соединений является большая продолжительность (2–10 сут) высокотемпературного отжига при твердофазном синтезе.
В работах [11, 16] изучена возможность включения технеция в шпинели – Mg2Ti1 –xTcxO4. Скорость выщелачивания таких соединений, процесс синтеза которых весьма сложен и трудоемок, составляла (3–7) × 10–3 г/(м2 сут) после испытания в течение 40 сут при комнатной температуре.
В работе [15] описаны соединения со структурой NZP вида ARe2(PO4)3 (где А – щелочной металл). Соединения были получены сплавлением концентрированной фосфорной кислоты, перрената аммония и хлоридов щелочных металлов с последующим отжигом при 400°C на воздухе и при 550°C в запаянной ампуле в инертной атмосфере. Химическая устойчивость синтезированных соединений не изучена.
В настоящей работе исследовали фосфат NaRe2(PO4)3 со структурой коснарита в качестве потенциальной керамической матрицы для иммобилизации 99Tc. Рений (Re) выступал в качестве химического и структурного аналога технеция. Для получения соединения NaRe2(PO4)3 использовали метод мокрой химии, для получения керамики – метод высокоскоростного электроимпульсного плазменного спекания (ЭИПС).
ЭКСПЕРИМЕНТАЛЬНАЯ ЧАСТЬ
Для получения порошков NaRe2(PO4)3 со структурой NZP к смеси растворов хлорида натрия и перрената аммония, взятых в стехиометрических количествах, при постоянном интенсивном перемешивании постепенно прибавляли раствор 1 М ортофосфорной кислоты. Полученный прозрачный раствор выпаривали при 80°С при постоянном перемешивании, сушили при 200 и 300°С до полного удаления влаги и частичного разложения промежуточных продуктов реакции. После отжига шихта приобрела черный цвет. Полученный порошок отжигали в запаянной кварцевой ампуле при температурах 600, 700 или 800°С в течение 12 ч.
Фазовый состав порошков и керамик определяли на рентгеновском дифрактометре Shimadzu LabX XRD-6000 (CuKα-фильтрованное излучение). Дифференциальный термический анализ проводили в аргоне с помощью анализатора DSC-204 F1 Phoenix в интервале температур 25–1200°С. Скорость нагрева составляла 10°C/мин. Функциональный состав соединений исследовали с помощью ИК-Фурье-спектрофотометра Shimadzu FTIR-8400S при комнатной температуре в интервале частот 400–4000 см–1.
Для получения керамик использовали установку Dr. Sinter model SPS-625. Порошки помещали в графитовую пресс-форму с внутренним диаметром 10 мм и нагревали за счет пропускания миллисекундных импульсов постоянного электрического тока большой мощности (до 3 кА) в условиях приложения одноосного давления. Температура спекания измерялась с помощью пирометра Chino IR-AH, сфокусированного на поверхности графитовой пресс-формы. Спекание осуществляли в вакууме (6 Па). Точность определения температуры составляла ±10°C, точность поддержания давления – 1 МПа. Усадка и скорость усадки порошков контролировали с помощью дилатометра, входящего в состав установки Dr. Sinter model SPS-625.
Плотность спеченных образцов измеряли методом гидростатического взвешивания в дистиллированной воде при помощи весов Sartorius CPA. Для оценки параметров микроструктуры образцов использовали растровый электронный микроскоп JEOL JSM-6490 с рентгеновским микроанализатором Oxford Instruments INCA-350.
Гидролитическую устойчивость керамик исследовали методом выщелачивания в статическом режиме в течение 28 сут. Испытания проводили при комнатной температуре в дистиллированной воде. Концентрацию Re в водных пробах определяли с помощью масс-спектрометра высокого разрешения с индуктивно связанной плазмой ELEMENT 2 по внешней градуировке. Градуировку проводили по растворам многоэлементного стандарта ICP-MS-68A-A High-Purity Standards и с помощью времяпролетного масс-спектрометра iDplus Perfomance.
В процессе эксперимента рассчитывали нормализованную потерю массы по формуле
(1)
$N{{L}_{i}} = {{{{a}_{{ki}}}} \mathord{\left/ {\vphantom {{{{a}_{{ki}}}} {({{M}_{{oi}}}S)}}} \right. \kern-0em} {({{M}_{{oi}}}S)}},$Расчет скорости выщелачивания Ri проводился по формуле
(2)
${{R}_{i}} = {{N{{L}_{i}}} \mathord{\left/ {\vphantom {{N{{L}_{i}}} {{{\tau }_{n}}}}} \right. \kern-0em} {{{\tau }_{n}}}},$Для определения механизма выщелачивания катионов из керамики использовали модель де Гроота–ван дер Слоота [17], которую можно представить в виде уравнения:
где Bi – общий выход Re из образца за время контакта с водой, мг/м2; τ – время контакта, сут. Величина Bi рассчитывалась по формуле(4)
${{B}_{i}} = {{C}_{i}}({L \mathord{\left/ {\vphantom {L S}} \right. \kern-0em} S}){{\surd {\kern 1pt} {{\tau }_{n}}} \mathord{\left/ {\vphantom {{\surd {\kern 1pt} {{\tau }_{n}}} {(\surd {\kern 1pt} {{\tau }_{n}}--\surd {\kern 1pt} {{\tau }_{n}}_{{--1}})}}} \right. \kern-0em} {(\surd {\kern 1pt} {{\tau }_{n}}--\surd {\kern 1pt} {{\tau }_{n}}_{{--1}})}},$Значениям коэффициента A в уравнении (3) соответствуют следующие механизмы выщелачивания элементов: <0.35 – вымывание с поверхности соединения; 0.35–0.65 – диффузия из внутренних слоев; >0.65 – растворение поверхностного слоя соединения [18, 19].
РЕЗУЛЬТАТЫ И ОБСУЖДЕНИЕ
По данным РФА (рис. 1), однофазный продукт получили после отжига при 700°C. После отжига при 600 и 800°C в порошке присутствовало незначительное количество примеси пирофосфата рения ReP2O7 и оксида рения ReO2 соответственно, что, вероятнее всего, связано с методикой синтеза. Полученные однофазные соединения кристаллизовались в ожидаемой структуре NZP и относились к пр. гр. $R\bar {3}c.$
Дальнейшие исследования проводили с использованием порошка, синтезированного при температуре 700°С.
Гранулометрический состав порошка был неоднороден. По данным растровой электронной микроскопии (РЭМ), синтезированный порошок содержал частицы двух типов: крупные ограненные частицы размером ~10 мкм, которые, вероятно, являются монокристаллами, и агломераты, состоявшие из частиц размером до 1 мкм (рис. 2а, 2б). Наличие рения в структуре синтезированного порошка подтверждено методом энергодисперсионного микроанализа (рис. 2в).
Рис. 2.
РЭМ-снимки (а, б) и результаты энергодисперсионного микроанализа (в) исходного порошка NaRe2(PO4)3.
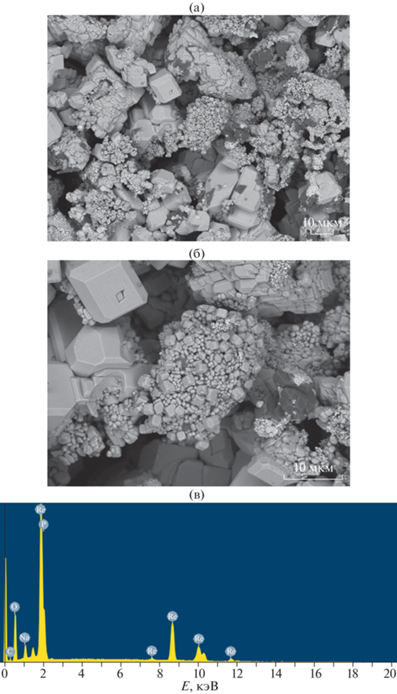
Анализ результатов дифференциальной сканирующей калориметрии (ДСК) (рис. 3) позволил обнаружить эндотермический эффект в интервале температур 970–1030°C, который соответствовал разложению NaRe2(PO4)3, что подтверждалось данными термогравитермического анализа (ТГА).
В ИК-спектре изучаемого образца (рис. 4) широкая полоса в области 980–1120 см–1 и высокочастотная полоса 1247 см–1 могут быть отнесены к асимметричным валентным колебаниям ν3${\text{PO}}_{4}^{{3 - }}$-иона. Малоинтенсивная высокочастотная полоса в районе 1247 см–1, не характерная для фосфатов, обусловлена, по нашему мнению, влиянием многозарядного иона Re4+, поляризующего связь P–O–Re. Полоса в области 883 см–1 соответствовала валентным симметричным ν1-колебаниям. Полосы в области 640–438 см–1 относились к деформационным колебаниям: полосы 650–540 см–1 отвечали асимметричным ν4-колебаниям, а полоса 445 см–1 – симметричным ν2-колебаниям.
ЭИПС порошка NaRe2(PO4)3 проводили в условиях постоянной скорости нагрева. Изотермическая выдержка при температуре спекания отсутствовала. Основные параметры спекания керамических образцов (скорость нагрева vh, средняя величина приложенного одноосного давления P, температура спекания ts и время изотермической выдержки τs при температуре спекания) представлены в табл. 1.
Таблица 1.
Основные параметры процесса ЭИПС порошков NaRe2(PO4)3, плотность и гидролитическая стойкость полученных образцов
Серия | ts, °С | vh, °С/мин | ρ, г/см3 | ρотн, % | NLRe, г/см2 | RRe, г/(см2 сут) |
---|---|---|---|---|---|---|
1 | 1100 | 50 | – | – | – | – |
2 | 800 | 50 | 4.154 | 84.9 | 4.4 × 10–4 | 1.3 × 10–5 |
3 | 800 | 100 | 4.174 | 85.3 | – | – |
4 | 800 | 200 | 4.168 | 85.2 | – | – |
Для определения оптимальных режимов ЭИПС было проведено предварительное спекание порошков NaRe2(PO4)3 путем нагрева до температуры 1100°С со скоростью 50°С/мин (серия 1). Режимы спекания в виде зависимостей температуры (t, °С), приложенного одноосного давления (Р, кН) и уровня вакуума (Vac, Па) от времени процесса ЭИПС представлены на рис. 5а. Зависимости усадки (L, мм) и скорости усадки (S, мм/с) от температуры нагрева представлены на рис. 5б. Как видно из рис. 5б, усадка порошка начинается при t = 600°С; скорость усадки мала и не превышает Smax ~ 4.5 × 10–3 мм/с (рис. 5б). При температуре 1000°С наблюдали пик усадки, вероятно, связанный с разложением порошка NaRe2(PO4)3. Это косвенно подтверждается тем, что при температурах более 850°С наблюдалось снижение уровня вакуума в камере спекания установки Dr. Sinter model SPS-625 (рис. 5а). Разложение образца в процессе ЭИПС при нагреве до 1100°С не позволило достоверно определить его плотность методом Архимеда.
Рис. 5.
Режимы спекания (а) и температурные зависимости усадки (L) и скорости усадки (S) порошка NaRe2(PO4)3 в условиях ЭИПС (образец 1) (б).
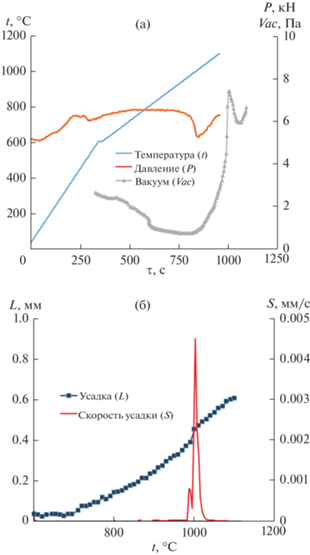
С целью минимизации или исключения процесса разложения порошкового образца дальнейшее спекание керамик проводили при температуре ts = 800°С с разными скоростями нагрева (серии 2–4). Интересно отметить, что максимальные значения скорости усадки Smax незначительно увеличивались от ~0.2 × 10–3 до ~1.5 × 10–3 мм/с при повышении скорости нагрева от 50 до 200°С/мин. Спеченные образцы представляли собой спрессованный до плотности ρотн ≈ 85% порошок с размером частиц, аналогичным размеру частиц исходного порошка d = 1–10 мкм (рис. 6). Многие частицы после спекания сохраняли свою ограненную форму, что свидетельствовало о низкой интенсивности процессов диффузии при ЭИПС. Достигнутая в процессе спекания плотность оказалась не достаточной для получения прочных керамик. Фазовый состав керамики после спекания не изменился (рис. 7).
Рис. 6.
Макро- (а, в, д) и микроструктура (б, г, е) образцов NaRe2(PO4)3, полученных методом ЭИПС при скорости нагрева vh = 50 (а, б), 100 (в, г), 200°С/мин (д, е) (см. табл. 1).
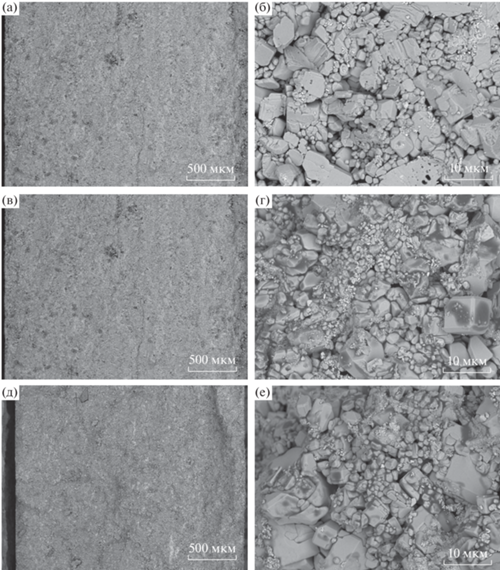
Зависимости нормализованной потери массы NL и скорости выщелачивания R от времени испытания τ приведены на рис. 8. Как видно из полученных данных, скорость выщелачивания рения на 28-е сутки составила R = 1.3 × 10–5 г/(см2 сут). Рассчитанное значение скорости выщелачивания оказалось несколько меньше, но сопоставимо со скоростью выщелачивания технеция из других минералоподобных соединений [11, 13, 14, 16]. Следует отметить, что реальная площадь поверхности S исследуемых керамических образцов больше, чем рассчитанная из геометрических размеров, из-за их повышенной пористости (рис. 6). Поэтому, по нашему мнению, полученные результаты характеризуют предельную величину R для данного соединения.
Рис. 8.
Результаты гидролитических испытаний керамики NaRe2(PO4)3: зависимости нормализованной потери массы (NL) и скорости выщелачивания (R) рения от времени испытания.
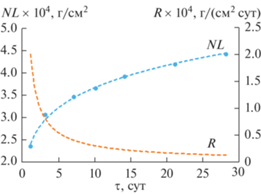
В соответствии с формулой (3), для определения механизма выщелачивания рения из керамики NaRe2(PO4)3 построили зависимость коэффициента В от времени эксперимента τ в логарифмических координатах (рис. 9). Из данных, представленных на рис. 9, видно, что величина коэффициента A составляет –0.38–0.3. Это позволяет сделать заключение о том, что выщелачивание рения происходит за счет вымывания с открытой поверхности керамики NaRe2(PO4)3.
ЗАКЛЮЧЕНИЕ
Однофазный фосфат NaRe2(PO4)3 со структурой минерала коснарита был синтезирован при температуре 700°C. Порошок NaRe2(PO4)3 имел неоднородный гранулометрический состав: присутствовали крупные монокристаллические частицы размером ~10 мкм и агломерированные частицы микронного размера.
Оптимальным режимом ЭИПС, с точки зрения достижения максимально возможной плотности керамики (ρотн = 85.3%) и сохранения фазового состава, является нагрев до температуры ts = 800°С со скоростью vh = 100°С/мин в условиях приложения одноосного давления р = 70 МПа.
Предельная скорость выщелачивания рения из керамики NaRe2(PO4)3 на 28-е сут составила 1.3 × 10–5 г/(см2 сут), что позволяет классифицировать исследуемый фосфат как обладающий высокой гидролитической устойчивостью. Установлено, что доминирующим механизмом выщелачивания рения в статическом режиме при комнатной температуре является вымывание катионов с поверхности керамики.
Список литературы
Paviet–Hartmann P., Lineberry M., Benedict R. Nuclear Fuel Reprocessing in Nuclear Engineering L.: CRS, Taylor and Francis. 2009. P. 315–366. https://doi.org/10.1201/9781420053913
Лаверов Н.П., Юдинцев С.В., Омельяненко Б.И. Об изоляции долгоживущего технеция-99 в консервирующих матрицах // Геология рудных месторождений. 2009. Т. 51. № 4. С. 291–307. https://doi.org/10.1134/S1075701509040011
Keiser D.D., Abraham D.P., Richardson J.W. Influence of Technetium on the Microstructure of a Stainless Steel–Zirconium Alloy // J. Nucl. Mater. 2000. V. 277. № 2–3. P. 333–338. https://doi.org/10.1016/S0022-3115(99)00158-0
Hartmann T. Synthesis and Properties of Metallic Technetium and Technetium–Zirconium Alloys as Transmutation Target and Radioactive waste storage form in the UREX + 1 Process. Atalante – 2008. Montpellier (19–23 May 2008). 2008. P. 3–13.
Попова Н.Н., Тананаев И.Г., Ровный С.И., Мясоедов Б.Ф. Технеций: поведение в процессах переработки облученного ядерного топлива и в объектах окружающей среды // Успехи химии. 2003. Т. 72. № 2. С. 115–137. https://doi.org/10.1070/RC2003v072n02ABEH000785
Mattigod S.V., Whyatt G.A., Serne J.R., Wood M.I. Diffusion of Iodine and Technetium-99 through Waste Encasement Concrete and Unsaturated Soil Fill Material // Proc. of Symp. “Sci. Bas. Nucl. Waste Management XXVIII”. Warrendale: MRS, 2004. V. 824. P. 391–398.
Aloy A., Kovarskaya E.N., Harbour J.R. et al. Pretreatment of Tc-Containing Waste and Its Effect on Tc-99 Leaching from Grouts // Proc. of Symp. “Sci. Bas. Nucl. Waste Management XXX”. Warrendale: MRS, 2007. V. 985. CD-version. Paper NN 10-02.
Ebert W.L., Wolf S.F., Bates J.K. The Release of Technetium from Defense Waste Processing Facility Glasses // Proc. of Symp. “Sci. Bas. Nucl. Waste Management XIX”. Pittsburgh: MRS, 1996. V. 412. P. 221–227.
McKeown D.A., Buechele A.C., Lukens W.W. et al. Raman Studies of Technetium in Borosilicate Waste Glass // Radiochim. Acta. 2007. V. 95 P. 275–280. https://doi.org/10.1524/ract.2007.95.5.275
Carter M.L., Stewart M.W.A., Vance E.R. et al. HIPed Tailored Ceramic Waste Forms for Immobilization of Cs, Sr, and Tc // Proc. of Symp. “Global 2007”. Idaho. 2007. P. 1022–1028.
Khalil M.Y., White W.B. Magnesium Titanate Spinel: a Ceramic Phase for Immobilization of Technetium-99 from Radioactive Waste // Commun. Am. Ceram. Soc. 1983. V. 66. № 10. P. 197–198. https://doi.org/10.1111/j.1151-2916.1983.tb10554.x
Юдинцев С.В., Коновалов Э.Е., Куприн А.В. и др. Иммобилизация технеция и редкоземельной актинидной фракции методом самораспространяющегося высокотемпературного синтеза // Геология. Инженерная геология. Гидрогеология. 2010. № 3. С. 232–242.
Hartmann T., Alaniz–Ortez I.J. Fabrication and Chemical Durability of Ceramic Technetium-Based Pyrochlores and Perovskites as Potential Waste Forms // Adv. Sci. Technol. 2014. V.94. P. 85–92. doi: 10.4028/www.scientific.net/AST.94.85
Hartmann T., Alaniz A.J., Antonio D.J. Fabrication and Properties of Technetium-Bearing Pyrochlores and Perovskites as Potential Waste Forms // Procedia Chem. 2012. V. 7. P. 622–628. https://doi.org/10.1016/j.proche.2012.10.095
Sukhanov M.V., Pet’kov V.I. Technetium and Rhenium Orthophosphates with Kosnarite-Type Structure // 7th Int. Symp. Technetium and Rhenium – Science and Utilization. M.: House GRANISTA, 2011. P. 75–78.
Exter M.J., Neumann S., Tomasberger T. Immobilization and Behavior of Technetium in a Magnesium Titanate Matrix for Final Disposal // Proc. of Symp. “Sci. Bas. Nucl. Waste Management XXIX”. Warrendale: MRS, 2006. V. 932. P. 567–574.
De Groot G.J., Van der Sloot H.A. Determination of Leaching Characteristics of Waste Minerals Leading to Environmental Product Certification / Eds. Gilliam T.M., Wiles C.C. Stabilization and Solidification of Hazardous, Radioactive and Mixed Wastes. V. 2. Philadelphia: ASTM, 1992. P. 149–170.
Torras J., Buj I., Rovira M., de Pablo J. Semi-Dynamic Leaching Tests of Nickel Containing Wastes Stabilized/Solidified with Magnesium Potassium Phosphate Cements // J. Hazard. Mater. 2011. V. 186. P. 1954–1960. https://doi.org/10.1016/j.jhazmat.2010.12.093
Xue Q., Wang P., Li J.-S. et al. Investigation of the Leaching Behavior of Lead in Stabilized/Solidified Waste Using a Two-Year Semi-Dynamic Leaching Test // Chemosphere. 2017. V. 166. P. 1–7. https://doi.org/10.1016/j.chemosphere.2016.09.059
Дополнительные материалы отсутствуют.
Инструменты
Неорганические материалы