Неорганические материалы, 2022, T. 58, № 6, стр. 606-614
Особенности нейтронно-физического и теплофизического расчетов ядерного топлива (Zr,U)N, полученного с применением подхода окислительного конструирования
Д. П. Шорников 1, 2, И. А. Ковалев 1, *, А. В. Тенишев 2, Б. А. Тарасов 1, 2, А. В. Шокодько 1, А. И. Огарков 1, С. С. Стрельникова 1, А. С. Чернявский 1, К. А. Солнцев 1
1 Институт металлургии и материаловедения им. А.А. Байкова Российской академии наук
119334 Москва, Ленинский пр., 49, Россия
2 Национальный исследовательский ядерный университет “МИФИ”
115409 Москва, Каширское ш., 31, Россия
* E-mail: vankovalskij@mail.ru
Поступила в редакцию 14.12.2021
После доработки 03.02.2022
Принята к публикации 04.02.2022
- EDN: JJOVAC
- DOI: 10.31857/S0002337X22050098
Аннотация
Нитридизацией твердых растворов урана в цирконии синтезированы нитриды Zr1 –хUхN. В ходе высокотемпературного насыщения твердых растворов азотом образуется керамика Zr1 –хUхN с повышенной концентрацией урана в центральной области образца. На основе Zr1 –хUхN представлена концепция нового вида топлива для высокотемпературных газоохлаждаемых реакторов. Проведен нейтронно-физический расчет активной зоны, показана возможность достижения критической массы при содержании урана 10 и 20 мас. %. Определены габариты активной зоны концептуального реактора. Проведен теплофизический расчет активной зоны реактора, показана возможность получения высокопотенциального тепла.
ВВЕДЕНИЕ
В настоящее время, согласно концепции Generation IV, основой ядерной энергетики будущего станут шесть реакторов. Особый интерес представляют быстрый газовый реактор (Gas-Cooled fast reactor) и высокотемпературный газовый реактор (Very-High Temperature reactor). В том или ином виде они представляют собой дальнейшее развитие газографитовых реакторов типа высокотемпературного газоохлаждаемого реактора (ВТГР) (США) и AVR (ФРГ). Эти реакторы представляют повышенный интерес как источник высокопотенциального тепла (до 1000°С) для металлургических и теплофизических производств. В отличие от водо-водяного энергетического реактора (ВВЭР) и реактора на быстрых нейронах (БН) такие реакторы имеют несколько упрощенную тепловую схему и обладают повышенным КПД. Основой газографитовых реакторов является микротвэльное топливо, которое представляет собой гранулы диоксида (реже карбида) урана с нанесенными на них покрытиями из пироуглерода и карбида кремния. Покрытия призваны исключить выход продуктов деления в газовый теплоноситель. Топливные гранулы размещены в графитовой матрице, из которой затем изготавливают стержни (концепция ВТГР) или шары (концепция AVR). Несмотря на уникальные характеристики, такой вид топлива обладает и рядом серьезных недостатков, в частности, за счет наличия неделящейся матрицы приходится повышать обогащение топлива, технология изготовления гранул и покрытий на них достаточно сложна и полностью не исключает выход продуктов деления. При повышенных выгораниях наблюдается “амебный” эффект, когда топливные гранулы мигрируют к поверхности топливного элемента. Попытка ухода от микроТВЭЛов и использование ТВЭЛов с развитой поверхностью теплосъема не позволяют достичь необходимых высоких температур [1–5].
Для решения некоторых из обозначенных проблем высокотемпературных реакторов предложена концепция ухода от дисперсного топлива и применения в качестве ТВЭЛов тонких пластин. Очевидно, что применение металлов и сплавов невозможно из-за высокой температуры, поэтому принято решение использовать тонкие керамические пластины. Чтобы достигнуть высокой температуры теплоносителя, увеличив поверхность теплопередачи, было предложено создать из керамического топлива структуру, через которую свободно проходит газовый теплоноситель. Схема активной зоны приведена на рис. 1 и 2.
Рис. 1.
Схематичный разрез активной зоны газового реактора: 1 – тепловыделяющая сборка (ТВС); 2 – ТВС с каналом для регулирующего стержня; 3 – биологическая защита; 4 – верхний свод, выход нагретого газа; 5 – опорная плита из жаропрочного сплава; 6 – стержни регулирования и аварийной защиты; 7 – вход теплоносителя из газодувки.
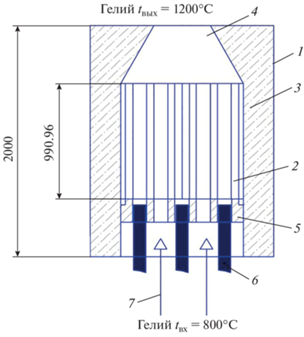
Рис. 2.
Вид сверху на активную зону реактора: 1 – отражатель, 2 – ТВС с отверстием под стержень системы управления и защиты (СУЗ), 3 – штатная ТВС.
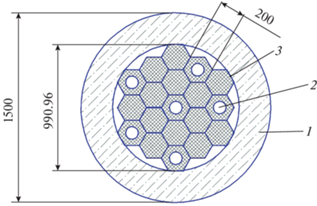
В качестве топливного материала предложено использование керамики на основе нитрида урана [6, 7]. Топливные элементы представляют собой тонкостенные сотовые керамические блоки, создать которые традиционными технологиями спекания порошков очень сложно, поэтому авторы использовали подход окислительного конструирования [8–13]. Нитридную керамику создавали нитридизацией твердых растворов урана в цирконии Zr〈U〉, где доля урана варьировалась в пределах 5–30 мас. %. Сплав прокатывали, гофрировали, изготавливали металлические заготовки, которые после диффузионного сваривания нитридизовали в атмосфере азота при высокой температуре. Керамика Zr1 –хUхN повторяла форму исходной металлической заготовки.
В основу концепции положен ВТГР с призматическими ТВЭЛами. ТВЭЛы представляют из себя полые шестигранные трубы с размером под “ключ” 200 мм, в которых размещены тепловыделяющие пластины. В качестве теплоносителя используется гелий, температура на входе 800–1000°С, на выходе – 1200–1500°С. Тепловая схема одноконтурная. Регулирование осуществляется стержнями из карбида бора или гафната диспрозия.
На рис. 3 приведен пример ТВС с пластинчатыми ТВЭЛами из твердого раствора Zr1 –хUхN с покрытием из ZrN.
Рис. 3.
Конструкция ТВС высокотемпературного реактора: 1 – кожух ТВС (молибден, ванадиевый сплав, нитрид титана или циркония), 2 – пластинчатый ТВЭЛ; А – поперечное сечение пластинчатого ТВЭЛа.
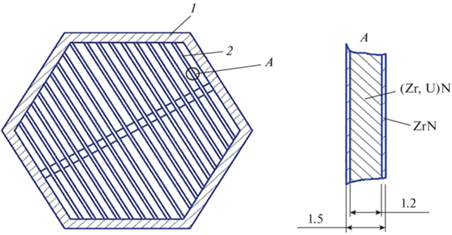
В шестигранной ТВС расположены пластинчатые ТВЭЛы в количестве от 17 штук, толщина до 1.5 мм. Пластина ТВЭЛ представляет из себя сердечник из композиции Zr1 –хUхN и оболочку ZrN. Сердечник и оболочка изготовлены из сплавов Zr–U и Zr соответственно, между ними достигается плотный диффузионный контакт, после чего осуществляется азотирование. Возможна любая геометрия расположения пластин, теплосъем осуществляется гелием или водородом.
ТЕОРЕТИЧЕСКИЙ АНАЛИЗ
Нейтронно-физический расчет концептуального реактора. Проведены предварительные исследования нейтронно-физических характеристик для ТВЭЛов из топливной композиции Zr1 – хUхN с помощью программы расчета методом Монте-Карло MCU-PTR. При расчетах было решено уйти от простой пластинчатой геометрии и провести оценку более сложной структуры, которая представляет из себя композицию из плоской и гофрированной лент. Профиль гофрированной ленты имеет вид равносторонних треугольников. Геометрия ТВЭЛов изображена на рис. 4а. Оболочка ТВЭЛов не учитывалась.
Рис. 4.
Геометрия ТВЭЛов с топливной композицией Zr1 – хUхN (горизонтальное сечение) (а); элементарная ячейка газового реактора (б).
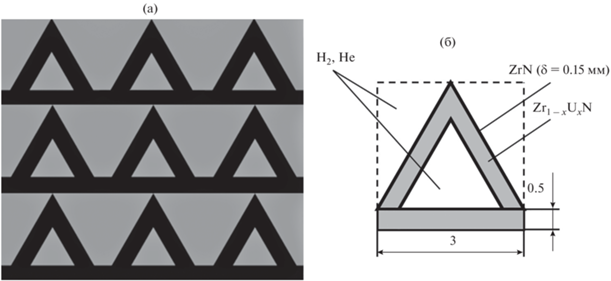
В табл. 1 приведены характеристики топливных композиций.
Таблица 1.
Характеристики топливных композиций
Содержание U в сплаве UZr, мас. % | 10 | 20 |
Плотность UZr, г/см3 | 8.3 | 7.8 |
Плотность U в UZr, г/см3 | 1.66 | 0.78 |
Обогащение по 235U, % | 90 | 90 |
Теплоноситель | H2 | H2 |
Ядерная концентрация*, ат./(барн см) | ||
235U | 3.828 × 10–3 | 1.7986 × 10–3 |
238U | 4.199 × 10–4 | 1.973 × 10–4 |
Zr | 4.3942 × 10–2 | 4.6456 × 10–2 |
N | 4.3942 × 10–2 | 4.6456 × 10–2 |
H | 5.412 × 10–5 | 5.4121 × 10–5 |
Рассчитаны коэффициенты размножения нейтронов для бесконечной среды из вышеописанных ТВЭЛов (табл. 2). Расчет проведен для температуры 300 К.
Таблица 2.
Результаты расчета по программе MCU-PTR
Состав композиции | Zr–20 мас. % U | Zr–10 мас. % U |
---|---|---|
kinf | 1.5776 | 1.3690 |
Δk/k, % | 27.0 | 36.6 |
Оценена чувствительность коэффициента размножения нейтронов в бесконечной среде kinf к концентрациям Zr и N (Δk/k – относительное изменение коэффициента размножения). Коэффициент чувствительности kinf к концентрации Zr составляет –8.19 × 101 (%Δk/k)/(ат./(барн см)). Коэффициент чувствительности kinf к концентрации N составляет –2.16 × 102 (%Δk/k)/(ат./(барн см)). То есть при изменении концентрации Zr и N на 10% коэффициент kinf изменится на 0.4%Δk/k и 1.0%Δk/k соответственно.
Для варианта Zr–10 мас. % U оценен коэффициент размножения для бесконечной в горизонтальной плоскости решетки ТВЭЛов при различной высоте активной зоны (без торцевых отражателей):
Следует отметить, что рассматриваемая система является практически гомогенной. Значение kinf с объемными долями Zr1 –хUхN 0.429, водорода 0.571 отличается от гетерогенного варианта менее чем на 0.1%Δk/k; keff – эффективный коэффициент размножения нейтронов.
На основании результатов расчета установлено, что предложенная конструкция реактора позволяет достичь реактивности при указанных геометрических размерах активной зоны реактора. При использовании боковых и торцевых отражателей удается снизить размер активной зоны примерно в два раза.
Теплофизический расчет канала газового реактора. Теплофизический расчет канала предложенного в данной работе реактора осуществлялся для определения максимальной температуры топливной композиции в элементарной ячейке, максимальной температуры оболочки и расхода охлаждающего газа. Элементарная ячейка реактора представляет из себя периодическую треугольную структуру (рис. 4б), охлаждаемую газообразным гелием или водородом. Топливо Zr1 –хUхN заключено в оболочку из ZrN. Размеры активной зоны взяты с учетом использования отражателя и составляют 0.5 × 0.5 м.
Исходные данные для проведения расчета представлены в табл. 3.
Таблица 3.
Исходные данные для расчета газового реактора
Температура газа на входе в активную зону, °C | tвх | 1000 |
Температура газа на выходе из активной зоны, °C | tвых | 1500 |
Давление в активной зоне, МПа | pа.з | 10 |
Тепловая мощность, кВт | Qтепл | 100 |
Высота активной зоны, м | Hа.з | 1.4 |
Диаметр активной зоны, м | Dа.з | 1.5 |
Шаг решетки, мм | a | 3 |
Толщина ТВЭЛа, мм | δ | 0.5 |
Толщина оболочки ТВЭЛа, мм | δоб | 0.15 |
Коэффициент неравномерности энерговыделения по высоте | Kz | 1.4 |
Коэффициент неравномерности энерговыделения по радиусу | Kr | 1.4 |
Число каналов в активной зоне определяли через отношение площади активной зоны к площади одной ячейки
где а = 3 мм – шаг решетки.Объемное энерговыделение в активной зоне определяли по формуле
(2)
${{q}_{V}} = \frac{{{{Q}_{{{\text{тепл}}}}}}}{{{{V}_{{{\text{тепл}}}}}}} = 3.58 \times {{10}^{6}}\,\,{\text{Вт/}}{{{\text{м}}}^{3}}.$Данное значение характерно для газоохлаждаемых реакторов.
Расход теплоносителя через активную зону рассчитывали по формуле
(3)
${{G}_{{{\text{а}}{\text{.з}}}}} = \frac{{{{Q}_{{{\text{тепл}}}}}}}{{{{c}_{{{\text{газ}}}}}({{t}_{{{\text{вых}}}}} - {{t}_{{{\text{вх}}}}})}},$Эффективная высота активной зоны представляет собой гипотетическую высоту, у которой на нижней и верхней границах тепловыделение в топливе обращается в ноль. Величину распределения энерговыделения по высоте определяли из уравнения
(4)
${{K}_{z}} = \frac{{{{H}_{{{\text{а}}{\text{.з}}}}}}}{{\int\limits_{ - {{H}_{{{\text{а}}{\text{.з/2}}}}}}^{{{H}_{{{\text{а}}{\text{.з/2}}}}}} {\cos \left( {\frac{{\pi z}}{{{{H}_{{{\text{эф}}}}}}}} \right)dz} }}.$Эффективная высота активной зоны Hэф = = 0.458 м. Распределение энерговыделения описывается тригонометрической зависимостью. Для наиболее энергонапряженного (центрального) канала справедлива запись
(5)
${{q}_{{l\,\,{\text{центр}}}}}(z) = \frac{{{{Q}_{{{\text{тепл}}}}}{{K}_{r}}{{K}_{z}}}}{{{{H}_{{{\text{а}}{\text{.з}}}}}{{N}_{{{\text{кан}}}}}}}\cos \left( {\frac{{\pi z}}{{{{H}_{{{\text{эф}}}}}}}} \right).$Распределение температуры теплоносителя (газа) по высоте наиболее энергонапряженного канала описывается уравнением
(6)
${{t}_{{{\text{газ}}}}}(z) = {{t}_{{{\text{вх}}}}} + \frac{{{{N}_{{{\text{яч}}}}}\int\limits_{ - {{H}_{{{\text{а}}{\text{.з/2}}}}}}^{{{H}_{{{\text{а}}{\text{.з/2}}}}}} {\frac{{{{Q}_{{{\text{тепл}}}}}{{K}_{r}}{{K}_{z}}}}{{{{H}_{{{\text{а}}{\text{.з}}}}}{{N}_{{{\text{кан}}}}}}}\cos \left( {\frac{{\pi z}}{{{{H}_{{{\text{эф}}}}}}}} \right)dz} }}{{{{G}_{{{\text{а}}{\text{.з}}}}}{{c}_{{{\text{газ}}}}}}}.$Наибольшая температура теплоносителя достигается на выходе из центрального канала и составляет ∼1700°С для водорода и для гелия. Совпадение значений объясняется близостью теплофизических свойств данных газов при расчетных температурах и давлениях.
При расчете температурного режима ТВЭЛа принято допущение, что в поперечном сечении канала температура газа остается постоянной. Коэффициент теплоотдачи определяли с помощью выражения
(7)
$\alpha = \frac{{(0.22R{{e}^{{0.8}}}P{{r}^{{0.6}}}){{\lambda }_{{{\text{газ}}}}}}}{{{{d}_{{{\text{гидр}}}}}}},$По результатам вычислений коэффициент теплоотдачи составил 18.7 Вт/(м2 К) для водорода и 19.5 Вт/(м2 К) для гелия.
Максимальная температура топлива достигается на равном удалении от обеих поверхностей оболочки внутри ТВЭЛа. Оценим термические сопротивления стенки ТВЭЛа (8) и половины толщины топливной части (9):
(8)
${{r}_{{{\text{об}}}}} = \frac{{{{\delta }_{{{\text{стенки}}}}}}}{{{{\lambda }_{{{\text{ZrN}}}}}}} = \frac{{0.15 \times {{{10}}^{{ - 3}}}}}{{27.2}} = 5.5 \times {{10}^{{ - 6}}}\,\,{{{\text{м}}}^{2}}\,\,{\text{К/Вт}},$(9)
${{r}_{{\text{т}}}} = \frac{{{{\delta }_{{\text{т}}}}}}{{{{\lambda }_{{({\text{UZr)N}}}}}}} = \frac{{0.1 \times {{{10}}^{{ - 3}}}}}{{25}} = 4 \times {{10}^{{ - 6}}}\,\,{{{\text{м}}}^{2}}\,\,{\text{К/Вт}}{\text{.}}$Наибольшие перепады температуры в оболочке и топливе могут быть достигнуты в местах наибольшего теплового потока. Перепады температур в оболочке и топливе в центральном сечении канала:
(10)
$\Delta {{t}_{{{\text{об}}}}} = \frac{{{{q}_{{l\,\,{\text{центр}}}}}(0)}}{a}{{r}_{{{\text{об}}}}} = 0.036^\circ {\text{C,}}$(11)
$\Delta {{t}_{{\text{т}}}} = \frac{{{{q}_{{l\,\,{\text{центр}}}}}(0)}}{a}{{r}_{{\text{т}}}} = 0.026^\circ {\text{C}}$пренебрежимо малы, и температура в центре топлива сопоставима с температурой теплоносителя. Таким образом, максимальная температура и топлива, и оболочки равна 1700°С. Результаты теплофизического расчета сведены в табл. 4.
Таблица 4.
Результаты теплофизического расчета
Теплоноситель | Водород | Гелий |
---|---|---|
Объемное энерговыделение, Вт/м3 | 3.58 × 106 | |
Число каналов, шт. | 25180 | |
Максимальная температура теплоносителя, °С | ∼1700 | |
Максимальная температура оболочки, °С | ∼1700 | |
Максимальная температура топлива, °С | ∼1700 | |
Расход теплоносителя через активную зону, кг/с (л/с) | 13 × 10–3 (7.06) | 38 × 10–3 (10.33) |
Скорость протекания теплоносителя, м/с | 0.04 | 0.05 |
Коэффициент теплоотдачи к теплоносителю, Вт/(м2 К) | 19.5 | 18.7 |
ЭКСПЕРИМЕНТАЛЬНАЯ ЧАСТЬ
Для проверки заявленной концепции ухода от дисперсного топлива и применения в качестве ТВЭЛов тонкостенных керамических блоков из тугоплавкой керамики с развитой поверхностью теплосъема были изготовлены модельные фрагменты керамических блоков. Керамику получали нитридизацией твердых растворов урана в цирконии с разным содержанием урана (5 и 10 мас. %). Методику нитридизации изучали на имитаторах – цирконии и титане, а затем использовали при синтезе нитридов твердых растворов циркония с 5 и 10 мас. % урана.
Шихту из 5 мас. % гранул обедненного металлического урана и 95 мас. % йодидного циркония плавили в дуговой печи МИФИ 9.3 в слиток длиной 49 и диаметром 8 мм. Для приготовления сплава брали 18.479 г циркония и 0.977 г урана, масса слитка после плавки составляла 19.439 г, потеря массы – менее 0.09%. Образец травили в растворе 50 об. % азотной и 50 об. % плавиковой кислот для удаления оксидного слоя и отжигали в вакуумной печи сопротивления при температуре 1000°С в течение 1 ч. Плотность сплава Zr–5 мас. % U, измеренная пикнометрическим методом, составила 6.214 г/см3. Анализ микроструктуры проводили на растровом электронном микроскопе (РЭМ) JEOL 6610 LV. Морфология поверхности литого и отожженного слитков представлена на рис. 5.
Рис. 5.
Морфология поверхности образца Zr–5 мас. % U: а – исходный литой сплав, б – прокатанный сплав, в – после нитридизации (отмечены участки спектрального анализа).
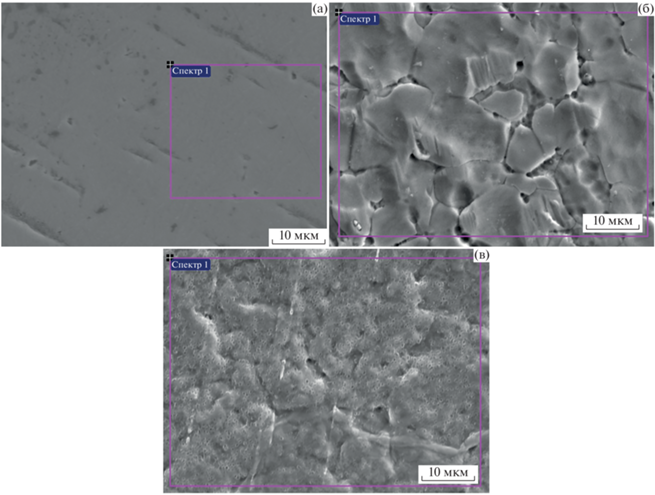
Слиток помещали в алюминиевую фольгу для исключения окисления, нагревали в индукторе до температуры 800–900°С и проковывали в пластину толщиной около 3 мм. После ковки образец прокатывали до толщины 1.76 мм, отжигали в процессе нагрева до 900°С (выше температуры фазового перехода циркония) без изотермической выдержки. После этого образец снова прокатывали до толщины 1.02 мм.
Из РЭМ-изображений видно, что в ходе плавки удается сохранить заданный состав, содержание циркония варьируется от 95.5 до 95.6, а содержание урана – от 4.35 до 4.45 мас. %.
Микрорентгеноспектральным анализом установлено равномерное распределение циркония и урана. Это связано с особенностями кристаллизации данного твердого раствора, который представляет собой перитектику, состоящую из матрицы чистого циркония и δ-фазы. Особенностью перитектики является равномерное распределение элементов в объеме материала.
На рис. 5б представлено РЭМ-изображение поверхности прокатанного твердого раствора. Элементным анализом установлено, что в ходе плавки содержание урана снижается от 4.35 до 3.58 мас. %.
Нитридизацию твердого раствора Zr–U проводили в атмосфере азота при температуре 1800°С. Морфология поверхности керамики представлена на рис. 5в. По результатам анализа установлено, что концентрация урана на поверхности образца несколько снижается и составляет около 1.6–3.0 мас. %. Снижение концентрации урана в приповерхностных областях можно объяснить его частичным испарением с поверхности за счет высокой упругости насыщенного пара при температуре нитридизации и одновременной миграцией урана в центр образца при образовании нитрида циркония.
Для исследования нитридизации твердых растворов на основе Zr изготавливали фольгу, содержащую 10 и 20 мас. % U. После плавки шихты в дуговой печи слиток проковывали и прокатывали в пластины толщиной 0.3–1.0 мм. Затем пластины сплава с двух сторон покрывали циркониевой фольгой толщиной 0.1 мм и прокатывали пакет, обеспечивая плотное диффузионное сцепление между цирконием и сплавом Zr〈U〉. Далее пластины гофрировали, собирали в форму ТВЭЛа, проводили диффузионное сваривание в вакуумной печи при температуре 0.85tпл и азотировали при 1700°С в атмосфере азота до образования твердого раствора Zr1–хUхN. Цирконий из покрытия образует нитрид ZrN, одновременно являющийся оболочкой. После азотирования пакет сохраняет первоначальную геометрию с развитой поверхностью. Фрагменты керамики представлены на рис. 6.
Для оценки состояния керамических блоков изучено качество сварных швов в местах контакта гофры с лентой. С учетом малого количества Zr1–хUхN исследование проводили на нитриде титана TiN. Точки контакта элементов керамического блока изображены на рис. 7. Видно, что критической зоной блока является участок диффузионной сварки. Так, в месте соединения пластин наблюдается только точечный контакт.
Рис. 7.
Морфология поверхности поперечного среза керамического блока TiN в месте контакта гофры и ленты.
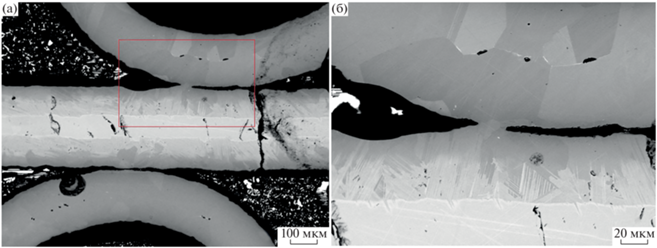
На поверхности поперечного среза различаются три слоя. Морфологические особенности поверхности связаны с образованием металлокерамического композита: наружный слой – стехиометрический нитрид титана, средний слой – нестехиометрический нитрид и в центре – твердый раствор азота в титане. Образование металлокерамического композита указывает на незавершенность процесса нитридизации.
РЕЗУЛЬТАТЫ И ОБСУЖДЕНИЕ
Для подтверждения концепции замены дисперсного топлива в ТВЭЛах на тонкостенное керамическое топливо были изготовлены модельные керамические пластины и фрагменты блоков. Керамику получали нитридизацией твердых растворов урана в цирконии с разным содержанием урана (5 и 10 мас. %) до образования Zr1 – хUхN. Установлено, что во время плавки слитка и нитридизации проката твердого раствора происходит незначительное испарение урана. В ходе высокотемпературного азотирования твердых растворов образуется керамика состава Zr1 – хUхN, в которой уран сосредоточен в центральной области образца. Концентрация урана в центральной области происходит во время формирования нитрида циркония.
Исследование морфологии поперечных срезов керамических имитаторов на основе нитридов ZrN и TiN показало, что основные дефекты материала сосредоточены в местах сварки и сгибов гофры. Низкая прочность сварного шва между структурными элементами керамического блока связана с не до конца отработанными режимами диффузионной сварки металла и незавершенностью процесса нитридизации. Для устранения дефектов необходим вакуумный отжиг заготовок для снятия напряжений с зоны сварных швов и сгибов.
Нейтронно-физическими расчетами показана возможность достижения критической массы в активной зоне, состоящей из пластин Zr1 – хUхN. При этом расчет проводили при содержании урана в композиции 10 и 20 мас. %. Консервативный расчет, не учитывающий наличие отражателя, показывает возможность достижения Keff = 1.15–1.25. Возрастание коэффициента связано с увеличением размеров активной зоны вплоть до 2 м. Оценка массы урана в активной зоне дает величину в пределах 400 кг, а масса самой активной зоны, без учета отражателя и стержней СУЗ, может достигать 4000 кг. Оценки показывают, что использование отражателя позволяет снизить размер активной зоны до значений менее 1 м, что соответствует размерам активных зон реакторов БН. Можно отметить некоторую неопределенность в функциональном назначении реактора, поскольку размеры активной зоны не позволяют использовать его в качестве транспортного реактора. Наличие азота в топливе в целом смещает спектр нейтронов в быструю область. Для более адекватной оценки необходимы дальнейшие расчеты.
Теплофизический расчет показал возможность получения температуры теплоносителя на выходе из активной зоны в пределах 1500°С. Расчеты были проведены для активной зоны размером 50 × 50 см, объемное энерговыделение которой составляет 3.58 × 106 Вт/м3. Увеличение размеров активной зоны до 1 м снижает объемное энерговыделение и температуру теплоносителя на выходе, однако она остается в пределах 1200°С.
ЗАКЛЮЧЕНИЕ
Нитридизацией твердых растворов урана в цирконии синтезированы нитриды твердых растворов Zr1 –хUхN. Керамика характеризуется повышенным содержанием урана в центре образца.
Представлена концепция газоохлаждаемого реактора с новым видом топлива на основе Zr1 –хUхN, синтезированного высокотемпературным насыщением в атмосфере азота металлических заготовок из твердых растворов урана в цирконии. Подтверждена возможность создания керамических изделий на основе нитридов твердых растворов урана в цирконии сложной формы с развитой поверхностью.
На основании нейтронно-физического расчета активной зоны показана возможность достижения критической массы при содержании урана 10 и 20 мас. %. Определены примерные габариты активной зоны концептуального реактора, которые находятся в пределах 1–2 м.
Проведен теплофизический расчет активной зоны реактора, показана возможность достижения на выходе температуры порядка 1200–1500°С при сохранении допустимого значения объемного энерговыделения.
Список литературы
Чиркин В.С. Теплофизические свойства материалов ядерной техники. Справочник. М.: Атомиздат, 1967. 484 с.
Бабичев А.П., Бабушкина Н.А., Братковский А.М. и др. Физические величины. Справочник / Под ред. Григорьева И.С., Мейлихова Е.З. М.: Энергоатомиздат, 1991. 1232 с.
Алексеев С.В., Зайцев В.А. Нитридное топливо для ядерной энергетики М.: Техносфера, 2013. 240 с.
Кириллов П.Л. Справочник по теплогидравлическим расчетам в ядерной энергетике. Т. 1. Теплогидравлические процессы в ЯЭУ. М.: ИздАт, 2010. 776 с.
Кириллов П.Л. Справочник по теплогидравлическим расчетам в ядерной энергетике. Т. 2. Ядерные реакторы, теплообменники, парогенераторы. М.: ИздАт, 2013. 688 с.
Streit M., Ingold F., Pouchon M., Gauckler L.J., Ottaviani J.P. Zirconium Nitride as Inert Matrix for Fast Systems // J. Nucl. Mater. 2003. V. 319. P. 51–58. https://doi.org/10.1016/S0022-3115(03)00133-8
Hollmer T. Manufacturing Methods for (U–Zr)N-Fuels: Student Thesis. Stockholm: AlbaNova University Centre, 2011. P. 80.
Кузнецов К.Б., Ковалев И.А., Нечаев А.Н., Огарков А.И., Шевцов С.В., Чернявский А.С., Солнцев К.А. Устойчивость структуры компактной керамики нитрида циркония к облучению высокоэнергетическими ионами ксенона // Неорган. материалы. 2016. Т. 52. № 12. С. 1311–1315.
Огарков А.И., Шевцов С.В., Кузнецов К.Б., Ковалев И.А., Чернявский А.С., Солнцев К.А. Эффект облучения нитридов титана, циркония и гафния высокоэнергетическими ионами // Неорган. материалы. 2016. Т. 52. № 6. С. 612–616.
Кузнецов К.Б., Ковалев И.А., Зуфман В.Ю., Огарков А.И., Шевцов С.В., Ашмарин А.А., Чернявский А.С., Солнцев К.А. Кинетика насыщения циркония азотом в процессе высокотемпературной нитридизации // Неорган. материалы. 2016. Т. 52. № 6. С. 609–611.
Shevtsov S.V., Ogarkov A.I., Kovalev I.A., Kuznetsov K.B., Prosvirnin D.V., Ashmarin A.A., Chernyavskii A.S., Solntsev K.A. Structural and Phase Transformations and Hardness of Ceramics Produced by High-Temperature Zirconium Nitriding // Russ. J. Inorg. Chem. 2016. V. 61. № 12. P. 1573–1577. https://doi.org/10.1134/S0036023616120160
Шевцов С.В., Огарков А.И., Ковалев И.А., Кузнецов К.Б., Ашмарин А.А., Чернявский А.С., Иевлев В.М., Солнцев К.А. Природа структурной неоднородности керамики, образующейся в процессе нитридизации циркония // Неорган. материалы. 2016. Т. 52. № 6. С. 651–655.
Шевцов С.В., Кузнецов К.Б., Ковалев И.А., Огарков А.И., Чернявский А.С., Солнцев К.А. Структура и микротвердость керамики, полученной в процессе высокотемпературной нитридизации циркониевой фольги // Неорган. материалы. 2015. Т. 51. № 8. C. 893–900.
Дополнительные материалы отсутствуют.
Инструменты
Неорганические материалы