Неорганические материалы, 2023, T. 59, № 2, стр. 202-207
Синтез тугоплавкой керамики на основе карбида циркония прямой карбидизацией циркония
Г. П. Кочанов 1, И. А. Костиков 1, 2, И. А. Ковалев 1, *, С. В. Канныкин 1, 3, С. В. Шевцов 1, А. А. Коновалов 1, П. А. Осипов 4, А. В. Костюченко 4, С. Н. Климаев 1, С. С. Стрельникова 1, А. С. Чернявский 1, К. А. Солнцев 1
1 Институт металлургии и материаловедения им. А.А. Байкова
Российской академии наук
119991 Москва, Ленинский пр., 49, Россия
2 Московский государственный университет им. М.В. Ломоносова
119991 Москва,
Ленинские горы, 1, Россия
3 Воронежский государственный университет
394006 Воронеж,
Университетская пл., 1, Россия
4 Воронежский государственный технический университет
394006 Воронеж,
ул. 20-летия Октября, 84, Россия
* E-mail: vankovalskij@mail.ru
Поступила в редакцию 21.10.2022
После доработки 15.12.2022
Принята к публикации 16.12.2022
- EDN: YDNHJU
- DOI: 10.31857/S0002337X23020094
Аннотация
Прямой карбидизацией циркониевого проката в атмосфере смеси газообразных аргона и этилена синтезирован компактный образец стехиометрического карбида циркония ZrC заданной формы. Формирование керамики происходит в результате взаимодействия металла с газообразным этиленом и при поглощении углерода, образующегося на реакционной поверхности при пиролизе С2Н6. Охарактеризована субструктура керамики, дана оценка механических и проводящих свойств ZrC.
ВВЕДЕНИЕ
Керамика на основе карбида циркония – функциональный материал, обладающий уникальным набором свойств. Карбид циркония характеризуется высокими температурой плавления, твердостью и теплопроводностью, низким электрическим сопротивлением, обладает высокой устойчивостью к абразивному износу и к воздействию различных агрессивных сред, как кислотно-щелочных так и окислительных [1, 2]. Более 95% изготавливаемого в мире карбида циркония идет на производство тугоплавких конструкционных и функциональных материалов [1–4], применяемых в металлургии, машиностроении, ядерной и аэрокосмической промышленностях. Традиционные способы получения [5–7] включают в себя 3 основные стадии: синтез порошков, формование и спекание.
В данной работе для синтеза керамики на основе карбида циркония использован способ окислительного конструирования, который позволяет создать керамические изделия в результате полной карбидизации металлических заготовок [8, 9]. Ранее этот метод был успешно использован при окислении и нитридизации металлов для получения керамических изделий сложной формы в одном технологическом процессе [10, 11]. Материалы на основе карбита циркония перспективны также в качестве нагревателей и термоэлектрических преобразователей [12].
Цель работы – синтез высокотемпературной тугоплавкой керамики на основе карбида циркония прямой карбидизацией циркониевого проката заданной формы.
ЭКСПЕРИМЕНТАЛЬНАЯ ЧАСТЬ
Синтез карбида циркония проводили резистивным нагревом металлической ленты длиной 60 мм, сечением 4.0 × 0.25 мм, изготовленной из проката фольги иодидного циркония (ТУ 95.46-97), в атмосфере контролируемого состава, представляющей смесь аргона высокой чистоты (ТУ 20.11.11-006-45905715-2017) и этилена (ГОСТ 20448-90), в интервале температур до 2100°C. В реакционную камеру, заполненную аргоном, пропущенным через нагретую до 450°C муфельную печь с циркониевой стружкой, подавали этилен с 25%-ным избытком от стехиометрии. Расчетный объем этилена подавали в реактор в течение 70 мин в процессе нагревания образца до заданной температуры. После достижения заданной температуры образец выдерживали 180 мин. Далее образец охлаждали 40 мин до комнатной температуры. В соответствии с фазовой диаграммой системы Zr–C [13, 14] при температуре 2100°C фаза состава ZrC1–x образуется уже при соотношении С/Zr > 0.65. Температуру контролировали оптическим пирометром LumaSense IMPAC ISR 50-LO.
Морфологию поверхности поперечных сколов и шлифов изучали на растровом электронном микроскопе (РЭМ) LEO 1420, Carl Zeiss и на оптическом инвертированном микроскопе Carl Zeiss Axio Observer 3 в поляризационном и дифференциально-интерференционном рельефном контрастах.
Фазовый состав приповерхностного слоя (глубиной ~7 мкм) и порошковых проб образцов определяли на вертикальном рентгеновском θ–2θ-дифрактометре XRD-6000 (Shimadzu) в монохроматизированном медном излучении. Кристаллические фазы идентифицировали по банку данных [15]. Параметр кристаллической решетки определяли методом экстраполяции к θ = 90° функцией Нельсона–Райли и аппроксимации их прямой по МНК; относительная погрешность в определении межплоскостных расстояний составляла 5 × 10–5 нм.
Механические свойства образцов исследовали методом измерительного наноиндентирования (Nano Hardness Tester фирмы CSM Instruments) поверхности скола. Максимальная величина нагрузки на индентор (алмазная пирамида Берковича) составляла 40 мН. Для всех измерений использовали линейный режим нагружения и разгрузки индентора; время нагружения составляло 45 с, выдержки при максимальной нагрузке – 1 с, разгрузки – 30 с. В каждой области проводили не менее 5 измерений. Значения твердости по Мейру, Виккерсу, модуль Юнга и долю упругой деформации в работе индентирования для образцов определяли по методу Оливера и Фара [16] согласно ГОСТ Р8.748-2011. Математическую обработку результатов проводили с помощью программы Indentation, прилагаемой к нанотвердомеру.
Температуру перехода в сверхпроводящее состояние компактного карбида циркония определяли на сверхпроводящем магните 16Т СFMS (Cryogenic LTD) по 4-точечной схеме, что дает возможность измерять сопротивление образца в температурном интервале от 1.6 до 290 К без учета сопротивления подводящих проводов. Характерные величины измерительного тока составляли от 1 мкА до 1 мА. В начале каждого измерения подбирали оптимальное для измерения вольтамперных характеристик значение измерительного тока, не приводящее к смещению сверхпроводящего перехода.
РЕЗУЛЬТАТЫ И ОБСУЖДЕНИЕ
На рис. 1 приведены дифрактограммы, отображающие фазовый состав синтезируемого образца и исходного металлического циркония. Исходный образец (рис. 1, дифрактограмма 3) имеет кристаллическую решетку α-Zr с параметром a = 3.2524 ± 0.008 Å. Поверхность карбидного образца двухфазная (рис. 1, дифрактограмма 2), основная фаза – монокарбид циркония ZrC (ГЦК, a = 4.6969 ± 0.0002 Å), вторая фаза – высокоориентированный графит (ГПУ, a = 2.482 Å, c = 6.840 Å). В объеме образца (рис. 1, дифрактограмма 1) основная фаза – монокарбид циркония ZrC с тем же параметром решетки (ГЦК, a = 4.6969 ± 0.0002 Å); кроме того, наблюдается диффузное рассеяние в области небольших углов 2θ (20°–30°), максимум которого совпадает с положением самого интенсивного рефлекса графита.
Рис. 1.
Рентгеновские дифрактограммы исследуемых образцов: 1 – порошковая проба карбида циркония, 2 – поверхность карбида циркония, 3 – исходный цирконий.

На поверхности образца обнаружен слой углерода толщиной до 20 мкм, отображающий пиролиз углеводорода в процессе нагрева образца, который имеет слоистую структуру (рис. 2). Адгезия углеродной пленки к поверхности карбида низкая, что приводит к отслоению.
На рис. 3 представлена морфология поверхности поперечного скола карбида циркония. Морфология поперечного скола образца не свойственна металлу или твердому раствору углерода. Материал однородный и без выраженной слоистости (рис. 3). В центральной области образца наблюдается граница встречи фронтов диффузии углерода внутрь образца, которая имеет вид ломаной линии (рис. 3б), очевидно, как следствие собирательной рекристаллизации, вследствие которой размер зерен кристаллитов карбида циркония достигает нескольких десятков микрон (70–90 мкм), но редко превышает полуширину образца. Это свидетельствует о незавершенности процесса рекристаллизации. Содержание пор в приповерхностных областях керамики низкое, однако в самом центре образца формируется пористая область шириной порядка 20 мкм с размером пор до ~0.5 мкм (рис. 4), а также на отдельных участках в центре образца встречаются полости размером до 10 мкм.
Рис. 3.
РЭМ-изображения морфологии поверхности поперечного скола карбида циркония: а – в приповерхностной области, б – в объеме образца.
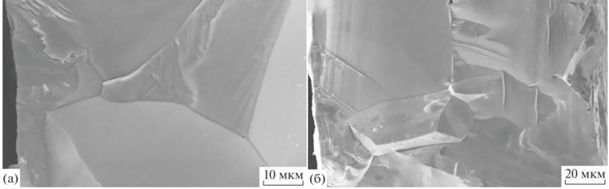
Рис. 4.
Поверхность поперечного шлифа образца карбида циркония в дифференциально-интерференционном рельефном контрасте.
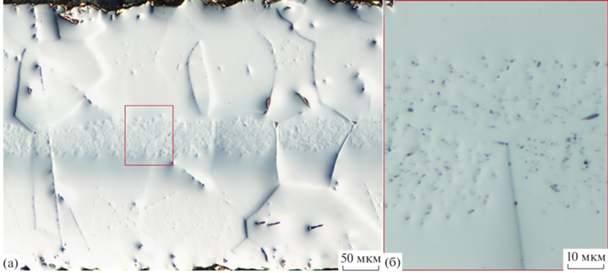
Наличие таких дефектов в центре керамического образца можно объяснить преобладанием диффузии металла из объема к поверхности над встречной диффузией углерода. Преобладание парциальной диффузии циркония из объема подтверждается большей величиной энергии активации процесса диффузии углерода в монокарбидных фазах [17]. Сопоставление величины коэффициентов самодиффузии в α- и β-фазах циркония [18] и коэффициентов диффузии углерода в цирконии также не противоречит предположению о преимущественной диффузии циркония на поверхность на стадии завершения карбидизации.
На рис. 5 приведены усредненные по результатам серии измерений диаграммы нагрузка (Р)–глубина отпечатка (h), которые характеризуют процесс деформации образца ZrC при наноиндентировании поперечного скола на расстоянии от поверхности 10 (кривая 1) и 110 мкм (кривая 2).
Рис. 5.
Диаграммы Р–h, построенные при индентировании поперечного скола образца ZrC на расстоянии от поверхности 10 (1) и 110 мкм (2).
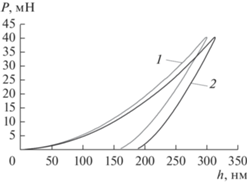
Диаграммы, полученные при индентировании на глубину от поверхности 20 и 40 мкм, практически совпадают с диаграммой 1 для глубины h = 10 мкм, а диаграмма, полученная на глубине 70 мкм, совпадает с диаграммой 2, полученной на глубине 110 мкм, поэтому на рис. 5 не представлены. Как показывает кривая разгрузки, деформация образцов имеет обратимую и необратимую компоненты. Их доли практически равны.
В табл. 1 представлены твердость по Мейру Н, твердость по Виккерсу HV, модуль Юнга Е, доля упругой деформации в работе индентирования η, глубина проникновения индентора hс, полученные при индентировании скола образца ZrC на расстоянии 10–110 мкм от поверхности образца. Из приведенных результатов следует, что различие величины модуля упругости Е по объему образца составляет ~5% (средняя величина по глубине ~390 ГПа), что соответствует известным данным для компактного ZrC [19, 20]. Этот результат подтверждает полную конверсию металла с образованием карбида циркония вследствие диффузии углерода. На глубине от 10 до 60 мкм прочностные характеристики Н, HV и η практически постоянны. Начиная с 60 мкм происходит плавное снижение величин Н, HV и η, которые достигают наименьших значений в центре образца (на глубине 110 мкм Н и HV ниже по сравнению с приповерхностной областью на ~15%, η – на 11%).
Таблица 1.
Результаты измерений прочностных характеристик керамики ZrC
Расстояние от поверхности образца, мкм | 10 | 20 | 40 | 70 | 110 |
---|---|---|---|---|---|
H, ГПа | 28.9 | 28.7 | 27.2 | 24.8 | 24.5 |
27.9 | 27.5 | 26.0 | 23.3 | 24.0 | |
31.4 | 30.5 | 28.7 | 25.6 | 25.2 | |
HV | 2674 | 2656 | 2517 | 2298 | 2268 |
2585 | 2545 | 2404 | 2155 | 2224 | |
2905 | 2821 | 2661 | 2368 | 2329 | |
E, ГПа | 390 | 392 | 406 | 395 | 378 |
379 | 384 | 381 | 377 | 355 | |
397 | 406 | 413 | 409 | 407 | |
η, % | 55 | 53 | 51 | 49 | 48 |
54 | 52 | 49 | 47 | 47 | |
57 | 55 | 55 | 50 | 49 | |
hc, нм | 225 | 226 | 232 | 243 | 245 |
216 | 219 | 226 | 239 | 242 | |
229 | 231 | 238 | 251 | 247 |
Величина Н образца ZrC на глубине более 60 мкм соответствует известным [19–21] значениям для крупнокристаллического ZrC, полученного спеканием порошков. Величина Н приповерхностного слоя толщиной до 60 мкм превышает Н в центре образца более чем на 10%, что соответствует данным для сплошных покрытий ZrC с субмикрокристаллической структурой, полученных в результате химической реакции из газовой среды [22, 23]. Повышенные значения твердости могут указывать на низкую подвижность дислокаций в синтезированном компактном карбиде. Снижение механических свойств керамики, наблюдаемое в центральной области на глубине больше 60 мкм, можно объяснить незначительным изменением состава карбида за счет дефицита углерода либо небольшой дефектностью микроструктуры керамики (пористости) (рис. 4).
На рис. 6 приведена температурная зависимость продольного удельного сопротивления R ZrC при нулевом магнитном поле в области температур 1.6–290 К. Образец показывает металлическое поведение во всем температурном диапазоне температур. Следует отметить, что результаты подтверждают отсутствие сверхпроводящих свойств у данного материала [24, 25].
ЗАКЛЮЧЕНИЕ
Предложен эффективный способ синтеза однофазной компактной керамики на основе карбида циркония. Синтезированный компактный карбид представлен единственной фазой – эквиатомным ZrC. Установлена двухстадийность процесса синтеза: на первой стадии на поверхности металла образуется углерод, вступающий в реакцию с металлом и диффундирующий в объем образца. На второй стадии происходит образование стехиометрического эквиатомного карбида во всем объеме образца. Двухстадийность процесса образования компактного карбида подтверждается различием величин нанотвердости в приповерхностном слое и в центре образца. Величина Н в приповерхностном слое соответствует нанотвердости покрытий, получаемых из газовой фазы, а нанотвердость в объеме образца сопоставима со значением для керамики, полученной спеканием порошков карбида циркония. Подтверждены известные данные об отсутствии в интервале температур 4.2–290 К перехода в сверхпроводящее состояние.
Список литературы
Сорокин О.Ю., Гращенков Д.В., Солнцев С.С., Евдокимов С.А. Керамические композиционные материалы с высокой окислительной стойкостью для перспективных летательных аппаратов // Тр. ВИАМ: электрон. науч.-техн. журн. 2014. № 6. С. 8.
Кириченко В.Г., Азаренков Н.А. Ядерно-физическое металловедение сплавов циркония. Харьков: ХНУ им. В. Н. Каразина, 2012. С. 405.
Yutai Katoh, Gokul Vasudevamurthy, Takashi Nozawa, Lance L. Snead. Properties of Zirconium Carbide for Nuclear Fuel Applications // J. Nucl. Mater. 2013. V. 441. № 1–3. P. 718–742.https://doi.org/10.1016/j.jnucmat.2013.05.037
Chunlei Yan, Rongjun Liun, Yingbin Cao, Changrui Zhang, Deke Zhang. Synthesis of Zirconium Carbide Powders Using Chitosan as Carbon Source // Ceram. Int. 2013. V. 39. № 3. P. 3409–3412. https://doi.org/10.1016/j.ceramint.2012.09.032
Кузнецова В.В., Крутский Ю.Л. Синтез карбида циркония карботермическим методом с использованием нановолокнистого углерода // Новосибирск: НГТУ, 2014. С. 248–251.
Tamoghna Chakrabarti, Lingappa Rangaraj, Vikram Jayaram. Computational Modeling of Reactive Hot Pressing of Zirconium Carbide // J. Mater. Res. 2015. V. 30. № 12. P. 1876–1886. https://doi.org/10.1557/jmr.2015.147
Wei X., Back C., Izhvanov O., Haines C., Olevsky E. Zirconium Carbide Produced by Spark Plasma Sintering and Hot Pressing: Densification Kinetics, Grain Growth, and Thermal Properties // Materials. 2016. V. 9. № 7. P. 577. https://doi.org/10.3390/ma9070577
Кочанов Г.П., Рогова А.Н., Ковалев И.А., Шевцов С.В., Ситников А.И., Костюченко А.В., Климаев С.Н., Ашмарин А.А., Стрельникова С.С., Чернявский А.С., Солнцев К.А. Синтез высокотемпературной керамики на основе карбида ниобия прямой карбидизацией ниобия // Неорган. материалы. 2021. Т. 57. № 10. С. 1138–1143. https://doi.org/10.31857/S0002337X21100055
Солнцев К.А., Шусторович Е.М., Буслаев Ю.А. Окислительное конструирование тонкостенной керамики // Докл. Академии наук. 2001. Т. 378. № 4. С. 492–499.
Шевцов С.В., Ковалев И.А., Огарков А.И., Канныкин С.В., Просвирнин Д.В., Чернявский А.С., Солнцев К.А. Cтруктура и твердость керамики, синтезируемой в процессе высокотемпературной нитридизации титановой фольги // Неорган. материалы. 2018. Т. 54. № 3. С. 311–316. https://doi.org/10.7868/S0002337X18030144
Ковалев И.А., Зуфман В.Ю., Шевцов С.В., Шашкеев К.А., Огарков А.И., Овсянников Н.А., Чернявский А.С., Солнцев К.А. Микроструктура рутильной керамики, полученной с применением подхода окислительного конструирования // Перспективные материалы. 2015. № 6. С. 57–65.
Ковалев И.А., Кочанов Г.П., Рубцов И.Д., Шокодько А.В., Чернявский А.С., Солнцев К.А. Способ получения высокотемпературных керамических термоэлектрических преобразователей для высокотемпературной термометрии из нитридов элементов подгрупп титана и ванадия методом окислительного конструирования: Патент RU 2759827 C1, МПК G01K7/02 C01B21/76, от 12.02.2021 г.
Лякишев Н.П. Диаграммы состояния двойных металлических систем: Справочник. В 3 т.: Т. 1. М.: Машиностроение, 1996. С. 992.
Sara R.V. The System Zirconium-Carbon // J. Am. Ceram. Soc. 1965. V. 48. № 5. P. 243–247. https://doi.org/10.1111/j.1151-2916.1965.tb14729.x
The International Centre for Diffraction Data. 2003.
Oliver W., Pharr G. An Improved Technique for Determining Hardness and Elastic Modulus Using Load and Displacement Sensing Indentation Experiments // J. Mater. Res. 1992. V. 7. № 6. P. 1564–1583. https://doi.org/10.1557/JMR.1992.1564
Вильк Ю.Н., Никольский С.С., Аварбэ Р.Г. Температурная зависимость коэффициента диффузии углерода в нестехиометрических карбидах циркония, ниобия и тантала // Теплофизика высоких температур. 1967. Т. 5. № 4. С. 607–611.
Чувильдеев В.Н., Семенычева А.В. Модель зернограничной самодиффузии в α- и β-фазах титана и циркония // Физика твердого тела. 2017. Т. 59. № 1. С. 5–12.
Harrison R.W., Lee W.E. Processing and Properties of ZrC, ZrN and ZrCN Ceramics: a Review // Adv. Appl. Ceram. 2016. V. 115. № 5. P. 294–307. https://doi.org/10.1179/1743676115y.000000006
Frank F., Tkadletz M., Czettl C., Schalk N. Microstructure and Mechanical Properties of ZrN, ZrCN and ZrC Coatings Grown by Chemical Vapor Deposition // Coatings. 2021. V. 11. № 5. P. 491. https://doi.org/10.3390/coatings11050491
Gridneva I.V., Mil’man Y.V., Rymashevskii G.A., Trefilov V.I., Chugunova S.I. Effect of Temperature on the Strength Characteristics of Zirconium Carbide // Sov. Powder Metall. Met. Ceram. 1976. V. 15. № 8. P. 638–645. https://doi.org/10.1007/bf01159455
He X.-M., Shu L., Li H.-B., Li H.-D., Lee S.-T. Structural Characteristics and Hardness of Zirconium Carbide Films Prepared by Tri-Ion Beam-Assisted Deposition // J. Vac. Sci. Technol., A. 1998. V. 16. № 4. P. 2337–2344. https://doi.org/10.1116/1.581349
Long Y., Javed A., Chen J., Chen Z., Xiong X. Phase Composition, Microstructure and Mechanical Properties of ZrC Coatings Produced by Chemical Vapor Deposition // Ceram. Int. 2014. V. 40. № 1. P. 707–713. https://doi.org/10.1016/j.ceramint.2013.06.05
Нешпор В.С., Никитин В.П., Новиков В.И., Попов В.В. Электрофизические свойства карбида циркония // Изв. АН СССР. Неорган. материалы. 1977. Т. 13. № 4. С. 654–657.
Allison C.Y., Finch C.B., Foegelle M.D., Modine F.A. Low-Temperature Electrical Resistivity of Transition-Metal Carbides // Solid State Commun. 1988. V. 68. № 4. P. 387–390.
Дополнительные материалы отсутствуют.
Инструменты
Неорганические материалы