Проблемы машиностроения и надежности машин, 2020, № 1, стр. 21-30
АНАЛИЗ ЖЕСТКОСТИ И ТОЧНОСТИ ПОЗИЦИОНИРОВАНИЯ РОБОТА-ТРИПОДА
Е. В. Гапоненко 1, *, Л. А. Рыбак 1, Л. Г. Вирабян 1
1 Белгородский государственный технологический университет им. В.Г. Шухова
г. Белгород, Россия
* E-mail: gaponenkobel@gmail.com
Поступила в редакцию 06.04.2018
Принята к публикации 25.10.2019
Аннотация
В статье представлена методика определения жесткости и смещения выходного звена робота-трипода, входящего в состав роботизированного комплекса с модулями относительного манипулирования, с использованием матрицы Якоби. Показано, что карты жесткости позволяют выявить максимальную и минимальную жесткость в рабочем пространстве робота. Приведен алгоритм расчета погрешности, вызываемой смещением выходного звена под действием силы резания. Представлены результаты моделирования.
При создании новых типов высокопроизводительного инновационного оборудования для различных применений (механической обработки, резки, сварки, сборки, окраски) возникают проблемы разработки новых схемно-технических решений, их компоновок, обеспечивающих сложные виды движений выходного звена в пространстве и высокую точность позиционирования. Одним из вариантов решения этих проблем является использование механизмов параллельной структуры для относительного манипулирования. В последнее время произошел значительный скачок в исследованиях механизмов параллельной структуры [1–7].
Одной из важных проблем при создании роботизированных комплексов на основе механизмов параллельной структуры является обеспечение требуемой точности механической обработки. В работах [8, 9], проведены экспериментальные исследования точности позиционирования, точности воспроизведения “эталонной” траектории, статической и динамической жесткости станка-гексапода “Гексамех-1”.
Для определения точности механизмов параллельной структуры-необходимо определить жесткость конструкции. Жесткость механизма во многом определяет его качество: производительность, надежность, долговечность и точность. Возрастающее значение высокой точности и динамических характеристик роботизированных систем параллельной структуры увеличило использование высокопрочных материалов и легких конструкций за счет значительного сокращения поперечных сечений звеньев и их массы. Но такие решения увеличивают структурные деформации и могут привести к интенсивным резонансным и самовозбуждающимся колебаниям высокой частоты. Поэтому исследование жесткости приобретает первостепенное значение при проектировании робототехнических систем параллельной структуры с целью правильного выбора материалов, геометрии, формы и размеров элементов конструкции, а также взаимодействия каждого элемента с другими.
Общая жесткость манипулятора зависит от нескольких факторов, включая размеры и материал звеньев. Для реализации механизма высокой жесткости многие элементы конструкции должны быть большими и тяжелыми. Однако для достижения высокоскоростного движения необходимо, чтобы они были небольшими и легкими.
Для получения модели жесткости механизмов параллельной структуры используются четыре основных метода, основанных: 1) на вычислении матрицы Якоби [10–13]; 2) на анализе конечных элементов [14]; 3) на матричном структурном анализе [15, 16], 4) на использовании набора виртуальных соединений, которые описывают упругие свойства звеньев, соединений и пружин [17, 18].
Однако работы, посвященные исследованию жесткости, не учитывают технологический процесс обработки, силу резания, оказывающую влияние на смещение выходного звена.
Рассмотрим использование метода на основе матрицы Якоби для нахождения жесткости и смещения выходного звена робота-трипода, входящего в состав роботизированного комплекса с модулями относительного манипулирования. Такой комплекс с шестью степенями свободы выполнен в виде соединения двух механизмов параллельной структуры с тремя степенями свободы каждый. На рис. 1 представлен макет манипулятора относительного манипулирования по патенту РФ [19], имеющегося в распоряжении Лаборатории мехатроники и робототехники БГТУ им. В.Г. Шухова.
На рис. 2 приведена 3D-модель роботизированного комплекса с модулями относительного манипулирования.
Рис. 2.
3D-модель роботизированного комплекса: 1 – модуль для установки инструмента; 2 – выходное звено; 3 – модуль для установки детали.
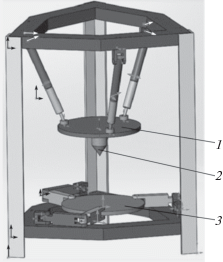
Механизм содержит модуль для установки инструмента и модуль для установки обрабатываемой детали на базе триподов. Использование таких механизмов позволит повысить техническую и эксплуатационную эффективность устройств манипулирования в пространстве по шести координатам. Важным преимуществом данного комплекса является отсутствие динамической связанности приводов, которая усложняет задачу моделирования и управления.
Верхний модуль для установки инструмента представляет собой трипод, который состоит из трех штанг переменной длины, соединенных вращательными шарнирами с основанием и рабочей платформой. Модуль может совершать вращение вокруг горизонтальных осей х и у, а также поступательное движение вдоль вертикальной оси z.
Нижний модуль для установки детали выполнен в виде плоского механизма параллельной структуры. Каждая кинематическая цепь имеет одну вращательную кинематическую пару, сопряженную с основанием, одну вращательную кинематическую пару, сопряженную с выходной платформой, и одну промежуточную вращательную кинематическую пару. Модуль имеет перемещения вдоль горизонтальных осей х и у, а также вращение вокруг вертикальной оси z.
Рассмотрим верхний модуль, выполненный в виде трипода. Основание и рабочая платформа верхнего модуля (рис. 3) представляют собой равносторонние треугольники, точки Ai, i = 1, 2, 3 и точек Bi, i = 1, 2, 3, соответственно расположены на вершинах равностороннего треугольника, минимальная и максимальная длины каждой штанги одинаковы. Поэтому механизм полностью симметричен.
Воспользуемся принципом виртуальной работы. В общем виде для трипода, представленного на рис. 2, работы, совершаемые силой резания и тремя силами, возникающими в штангах, можно выразить уравнением
(1)
${\mathbf{F}}_{{\text{p}}}^{T} \times \Delta {\mathbf{P}} = {{{\mathbf{f}}}^{T}} \times \Delta {\mathbf{q}},$Длины штанг трипода определим на основе соотношений
Из [21] эти смещения равны
Для преобразования уравнения (1) применим методику расчета, основанную на использование матрицы Якоби. Учитывая, что погрешность позиционирования центра подвижной платформы можно найти из уравнения
где J – прямая матрица Якоби, подставим выражение (2) в уравнение (1)После преобразований выразим силу резания через усилия, возникающие в штангах
Для данного механизма силы, возникающие в штангах под действием силы резания, являются осевыми. Согласно закону Гука, справедливо выражение
(4)
${\varepsilon } = \frac{{\Delta {{q}_{i}}}}{{{{q}_{i}}}} = \frac{\sigma }{E} = \frac{{{{f}_{i}}}}{{A \cdot E}},$Выразим из уравнения (4) силу, возникающую в штанге
Запишем уравнение (5) с учетом жесткости трипода
После преобразований получим
(6)
${{{\mathbf{F}}}_{p}} = {{{\mathbf{J}}}^{{ - T}}} \cdot {{{\mathbf{K}}}_{{\text{s}}}} \cdot {{{\mathbf{J}}}^{{ - 1}}} \cdot \Delta {\mathbf{P}} = {{{\mathbf{K}}}_{{\text{c}}}} \cdot \Delta {\mathbf{P}},$J–1 – обратный Якобиан
Выразим из уравнения (6) смещения центра платформы под действием силы резания
где ${\mathbf{K}}_{{\text{c}}}^{{ - 1}}$ – матрица статической жесткости параллельного робота; Fр – сила резания.Механизм может не соответствовать требуемой жесткости в некоторых точках и областях рабочего пространства. Поэтому для механизма параллельной структуры полезно иметь атлас матриц жесткости в зависимости от положения. Из такого атласа можно выбрать рабочую конфигурацию, матрица жесткости в которой наиболее полно соответствует требованиям поставленной задачи. Механизм можно спроектировать таким образом, чтобы его матрица жесткости была близка к желаемой, по крайней мере, в некоторых положениях. В этом случае может потребоваться изменение геометрии и/или топологии структуры механизма. Карты позволяют выявить наличие зон, где жесткость неприемлема, а также помогают проектировщику, обеспечивая более точное представление о свойствах данного механизма.
Построим карты жесткости для роботизированного комплекса (рис. 3) с геометрическими размерами: z = 200 мм, R = 200 мм, r = 100 мм, q1, q2, q3 ∈ [170 мм, 250 мм], модуль упругости для стержней из стали E = 2 × 105 МПа.
На рис. 4 приведены карты жесткости по оси z при изменении углов ϑ и φ как множество кривых жесткости для различных значений z в программной среде Matlab. В ходе вычислений производился циклический перебор значений углов поворота ϑ и φ от –45° до 45° с шагом 5°. Сетка строится по области рабочего пространства, а матрица жесткости вычисляется на каждом узле сетки. Карты показывают минимальную и максимальную жесткость в рабочем пространстве робота. Из таких графиков можно определить, какие области рабочего пространства удовлетворяют заданным критериям жесткости. Из рис. 4 видно, что жесткость по z выше вблизи центра рабочего пространства, что является наилучшим положением для поддержания вертикальных нагрузок (например, инструмента на рабочей платформе). Чем меньше z, тем выше жесткость, т.е. жесткость в верхней части механизма выше, т.к. рабочая платформа находится ближе к основанию.
Рис. 4.
Карта жесткости по координате z при изменении координат φ, ϑ: (а) z = 250 мм; (б) z = 200 мм; (в) z = = 180 мм.
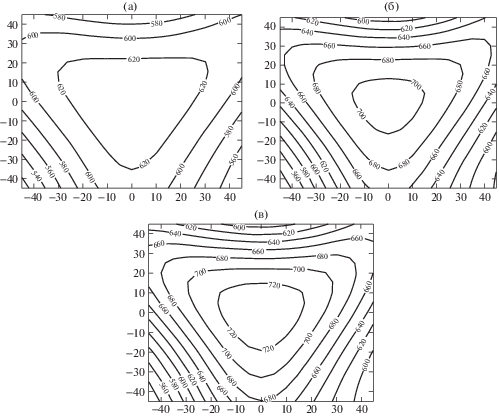
Такая оценка жесткости может использоваться как инструмент для проектировщика с целью выбора между различными вариантами конструкции механизма или для оценки существующей структуры.
На рис. 5 представлен алгоритм расчета погрешности (7), вызываемой смещением выходного звена под действием силы резания для трипода (рис. 3). Среди полученных значений координат рабочего органа исключены значения, не удовлетворяющие условиям
где qi – длина i-й штанги; qmin – минимальное значение длины штанги; qmax – максимальное значение длины штанги.Рис. 5.
Алгоритм расчета погрешности, вызываемой смещением выходного звена под действием силы резания.
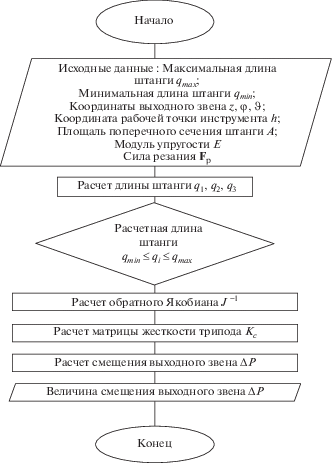
На основании предложенного алгоритма составлена программа в среде Matlab для нахождения жесткости и погрешности, вызываемой смещением выходного звена под действием силы резания для трипода (рис. 2).
По полученной программе в среде Matlab были построены зависимости смещения выходного звена по оси z от главной составляющей силы резания при чистовом фрезеровании Fz (рис. 6), которая изменялась в пределах от 10 до 150 Н, при трех различных конфигурациях механизма z = 180 мм, z = 200 мм, z = 250 мм и при, φ = 30°, ϑ = 0°. На рис. 6а приведены зависимости для случая, когда стержни переменной длины изготовлены из стали, на рис. 6б – из алюминия.
Рис. 6.
Зависимость линейных смещений выходного звена от составляющей силы резания Fz при 1 – z = 180 мм, 2 – z = 200 мм, 3 – z = 250 мм: (а) для стержней из стали; (б) для стержней из алюминия.
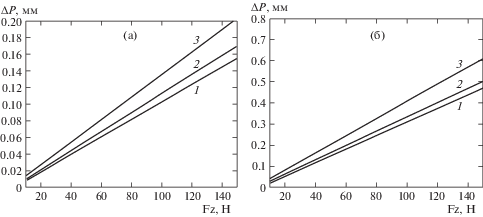
Из графиков видно, что с увеличением расстояния между платформой и основанием механизма, увеличивается смещение выходного звена под действием силы резания. Например, при силе Fz =70 Н, смещение выходного звена ΔP составляет 0.07 мм для z = 180 мм; ΔP = 0.076 мм для z = 200 мм; ΔP = 0.09 мм для z = 250 мм (рис. 6а). Из рис. 6б видно, что смещение выходного звена в случае использования штанг робота-трипода из алюминия выше, чем при использовании штанг из стали. При силе Fz = 70Н смещение выходного звена при z = 200 мм составляет ΔP = 0.076 мм (рис. 6а) против ΔP = 0.2 мм (рис. 6б). Целесообразно использовать данный механизм при небольших динамических нагрузках: для чистовой механической обработки, сварки, 3D-печати, покраски.
Предложенные алгоритмы позволяют на стадии проектирования выбрать геометрические параметры механизма параллельной структуры, материал штанг для обеспечения требуемой жесткости и точности обработки. Пользователь может задавать любые исходные параметры моделирования. Используемая методология может применяться для анализа жесткости и точности параллельных механизмов других кинематических структур.
Список литературы
Kong H., Gosselin C.M. Type Synthesis of Parallel Mechanisms. Springer. 2007. P. 275.
Merlet J.-P. Parallel Robots. Springer. 2006. P. 402.
Крайнев А.Ф., Глазунов В.А., Муницына Н.В. Механизмы перемещения заготовки и инструмента для станка нетрадиционной компоновки // Станки и инструмент. 1995. № 7. С. 10.
Глазунов В.А., Ласточкин А.Б., Терехова А.Н. Об особенностях устройств относительного манипулирования // Проблемы машиностроения и надежности машин. 2007. № 2. С. 77.
Глазунов В.А., Ласточкин А.Б., Шалюхин К.А. и др. К анализу и классификации устройств относительного манипулирования // Проблемы машиностроения и надежности машин. 2009. № 4. С. 81.
Рыбак Л.А., Мамаев Ю.А., Вирабян Л.Г. Синтез алгоритма коррекции траектории движения выходного звена робото-гексапода на основе теории искусственных нейронных сетей // Вестник Белгородского государственного технологического университа им. В.Г. Шухова. 2016. № 12. С. 142.
Рыбак Л.А., Ержуков В.В., Чичварин А.В. Эффективные методы решения задач кинематики и динамики робота-станка параллельной структуры. М.: ФИЗМАТЛИТ, 2011. С. 147.
Вайнштейн И.В., Серков Н.А., Сироткин Р.О. Экспериментальное исследование статической жесткости 5-координатного фрезерного станка с параллельной кинематикой // Проблемы машиностроения и надежности машин. 2007. № 5. С. 102.
Мерзляков А.А., Серков Н.А., Сироткин Р.О. Экспериментальные исследования динамических свойств станка с параллельной кинематикой // Проблемы машиностроения и надежности машин. 2008. № 1. С. 98.
Gosselin C.M. Stiffness mapping for parallel manipulator // IEEE Trans. On Robotics and Automation. 1990. V. 6. P. 377.
El-Khasawneh B.S., Ferreira P.M. Computation of stiffness and stiffness bounds for parallel link manipulato // Int. J. Machine Tools & Manufacture. 1999. V. 39. № 2. P. 321.
Company O., Pierrot F., Fauroux J.C. A method for modeling analytical stiffness of a lower mobility parallel manipulator // Proc. of IEEE ICRA: Int. Conf. On Robotic and Automation. 2010. V. 28. № 5. P. 719.
Qiang Zeng, Kornel F. Ehmann, Jian Cao. Tri-pyramid Robot: stiffness modeling of a 3-DOF translational parallel Manipulator // Robotica. 2016. V. 34. № 2. P. 383.
Corradini C., Fauroux J.C., Krut S., Company O. Evaluation of a 4 degree of freedom parallel manipulator stiffness // Proc. of the 11th Word Cong. In Mechanism & Machine Science, IFTOMM’2004. 2004.
Huang T., Zhao X., Whitehouse D.J. Stiffness estimation of a tripod-based parallel kinematic machine // IEEE Trans. on Robotics and Automation. 2002. V. 18. № 1.
Dong W., Du Z., Sun L. Stiffness influence atlases of a novel flexure hinge-based parallel mechanism with large workspace // Proc. of IEEE ICRA: Int. Conf. on Robotic and Automation. 2005.
Pashkevich A., Chablat D., Wenger P. Stiffness analysis of overconstrained parallel manipulators // Mechanism and Machine Theory. 2009. V. 44. № 5. P. 966.
Pashkevich A., Klimchik A., Caro S., Chablat D. Cartesian stiffness matrix of manipulators with passive joints: Analytical approach // in Proc. IEEE Int. Conf. Intell. Robots Syst. 2011. P. 4034.
Робототехническая установка для обработки деталей: пат. 2415744 Рос. Федерация: МПК B25J 9/00 / В.А. Глазунов, К.А. Шалюхин, С.В. Левин, С.Д. Костерева; заявитель и патентообладатель Учреждение Российской академии наук Институт машиноведения им. А.А. Благонравова РАН. № 2009112772/02; заявл. 06.04.2009; опубл. 10.04.2011, Бюл. № 10. 3 с.: ил.
Lee K.-M., Shan D.K. Kinematic Analysis of a Three-Degress-of-Freedom In-Parallel Actuated Manipulator // IEEE. J. of Robotics and. Automation. 1988. № 3.
Pundru Srinivasa Rao, Nalluri Mohan Rao. Position Analysis of Spatial 3-RPS Parallel Manipulator // International Journal of Mechanical Engineering and Robotics Research. 2013. V. 2. № 2. P. 80.
Дополнительные материалы отсутствуют.
Инструменты
Проблемы машиностроения и надежности машин