Приборы и техника эксперимента, 2022, № 6, стр. 53-60
КОМПРЕССИЯ ПУЧКА БЫСТРЫХ АТОМОВ АРГОНА ДЛЯ ПОЛИРОВАНИЯ ПОВЕРХНОСТИ
А. С. Метель a, *, С. Н. Григорьев a, М. А. Волосова a, Ю. А. Мельник a, Э. С. Мустафаев a
a Московский государственный технологический университет “СТАНКИН”
127994 Москва, Вадковский пер., 3а, Россия
* E-mail: a.metel@stankin.ru
Поступила в редакцию 20.05.2022
После доработки 17.06.2022
Принята к публикации 18.06.2022
- EDN: NMRRSM
- DOI: 10.31857/S0032816222060088
Аннотация
Приведены результаты исследования источника пучка быстрых атомов аргона, получаемых нейтрализацией зарядов ускоренных ионов при пролете через ускоряющую сетку в виде набора плоскопараллельных пластин. Ионы ускоряются из плазменного эмиттера напряжением отрицательной полярности на сетке, влетают в зазоры между ее пластинами и при приближении к их поверхностям вызывают эмиссию электронов, нейтрализующих их заряд. Эквивалентный ток пучка вылетающих из сетки быстрых атомов составляет до 90% тока в ее цепи, а их энергия равна энергии ионов, соответствующей ускоряющему напряжению между плазменным эмиттером и сеткой. Для увеличения плотности тока пучка быстрых атомов на обрабатываемой поверхности участки пластин сетки, обращенные к плазменному эмиттеру, выполнены в форме сегмента круга. Движение ионов и образованных внутри сетки быстрых атомов к центру этого круга позволяет на порядок снизить ширину пучка и увеличить плотность потока быстрых атомов без уменьшения угла их падения на обрабатываемую поверхность. Компрессия пучка значительно повышает эффективность полирования поверхности пучком быстрых нейтральных атомов аргона с углом падения на поверхность 80°.
ВВЕДЕНИЕ
Источники широких ионных пучков применяют для модификации поверхности изделий, в том числе для имплантации в нее необходимых химических элементов, травления поверхности, ее полирования и сопровождения синтеза различных функциональных покрытий. Каждый источник содержит газоразрядную камеру, в которой создается плазменный эмиттер, а также ионно-оптическую систему для ускорения ионов и формирования пучка. Основным недостатком многих ионных источников является применение для получения плазменного эмиттера термоэмиссионных катодов, которые выходят из строя в среде химически активных газов, например кислорода [1, 2]. Для получения ионов химически активных газов применяют источники с генерацией плазменного эмиттера в высокочастотном разряде или в тлеющем разряде с холодным катодом [3, 4].
При обработке ионными пучками диэлектрических изделий происходит накопление положительного заряда на поверхности и в объеме материала. Во многих случаях это ограничивает область применения ускоренных ионов. В связи с этим получили распространение источники пучков быстрых нейтральных атомов, получаемых нейтрализацией заряда ускоренных ионов. Например, в работе [5] описаны источники быстрых нейтральных атомов с генерацией плазменных эмиттеров в высокочастотном разряде. Их недостатками являются ограниченная энергия ускоренных частиц и, следовательно, скорость распыления материалов, а также необходимость согласования высокочастотных источников питания с плазменной нагрузкой и отрицательное влияние излучения высокой частоты на электронные приборы и здоровье персонала.
Энергия ускоренных частиц и скорость распыления ими материалов заметно выше в источниках быстрых нейтральных атомов с генерацией плазменного эмиттера тлеющим разрядом с удержанием электронов в электростатической ловушке [6–8]. Обычно ловушка образована полым катодом и отрицательной по отношению к нему эмиссионной сеткой. В работе [6] из заполняющей полый катод диаметром 21 см однородной плазмы через отверстия ускоряющей сетки влетают в вакуумную камеру ионы аргона с энергией до 3 кэВ. В результате столкновений с перезарядкой при давлении аргона 0.2 Па ионы превращаются в быстрые нейтральные атомы на расстоянии около 10 см от сетки. При меньших давлениях начинается рост разрядного напряжения и разряд погасает, а при давлении более 0.5 Па через отверстия сетки происходят пробои между плазменным эмиттером в полом катоде и вторичной плазмой в камере. В результате ускорение ионов между этими двумя плазмами прекращается. Таким образом, объем электростатической ловушки 3 л, обеспечивающий работоспособность источника [6] в диапазоне от 0.2 до 0.5 Па, является минимальным для рассматриваемых источников. Чтобы расширить диапазон давления, в котором данные источники устойчиво работают, нужно увеличивать объем полого катода. Такие источники можно использовать для модификации свойств покрытий на изделиях из металлов [9] и диэлектриков [10] в процессе их осаждения.
При использовании источника быстрых атомов аргона для травления или полирования поверхности небольших подложек, например, диаметром 2 см коэффициент использования пучка диаметром 20 см составляет около 1%. Для его увеличения необходимо осуществить компрессию пучка, чтобы на некотором расстоянии от сетки его диаметр лишь незначительно превышал диаметр подложки. Для этого плоскую эмиссионную сетку источника диаметром 20 см заменяют на вогнутую сетку с таким же диаметром и радиусом кривизны поверхности 20 см. В этом случае диаметр пучка быстрых нейтральных атомов с увеличением расстояния h от сетки снижается от 20 см до минимальной величины ~1 см при h = 20 см, а затем снова возрастает. Установив подложку диаметром 2 см на расстоянии 18 или 22 см от сетки, можно на два порядка повысить скорость травления подложки по сравнению с травлением широким пучком, формируемым плоской сеткой.
Однако использовать такой пучок для полирования поверхности нельзя. Дело в том, что полирование эффективно лишь при больших углах падения (α = 75°–85°) ускоренных частиц на обрабатываемую поверхность [11]. При компрессии пучка с помощью круглой вогнутой сетки с диаметром и радиусом кривизны поверхности, равными 20 см, угловой разброс атомов составляет 60°, и установить обрабатываемую подложку в пучке так, чтобы быстрые атомы бомбардировали ее поверхность под углом падения α = 75°–85°, невозможно. Целью настоящей работы является разработка источника быстрых атомов аргона с компрессией пучка, повышающей скорость полирования подложки атомами с большим углом падения (α = 80°) на ее поверхность.
ЭКСПЕРИМЕНТАЛЬНАЯ УСТАНОВКА
На рис. 1 представлена конструктивная схема установки для полирования подложек пучком быстрых атомов аргона. Она состоит из охлаждаемой водой газоразрядной камеры диаметром 50 см и длиной 21 см, в которой формируется плазменный эмиттер ионов, и охлаждаемого водой прямоугольного корпуса длиной 55 см, высотой 14 см и шириной 40 см со съемным фланцем. В центре съемного фланца установлен полый цилиндр диаметром 3 см и длиной 30 см с кварцевым окошком в конце. Через него с помощью инфракрасного пирометра IMPAC IP 140 фирмы LumaSense Technologies GmbH (Германия) измеряется температура устанавливаемых внутри корпуса подложек. Цилиндр предохраняет окошко от напыления металлических пленок. Корпус крепится на левой стенке камеры, которая откачивается через плоскую заземленную сетку до давления остаточного газа 0.001 Па турбомолекулярным и роторным насосами. Заземленная сетка не позволяет плазме проникать в систему вакуумной откачки.
Внутри корпуса размещена ускоряющая сетка, выполненная в виде набора из 11-ти плоскопараллельных титановых пластин толщиной 0.5 мм, шириной 300 мм и длиной 150 мм. Пластины со вставками толщиной 4.5 мм между ними скрепляются вместе стяжными шпильками. Ускоряющая сетка крепится к стенкам корпуса с помощью четырех керамических изоляторов, защищенных от осаждения металлических пленок полыми цилиндрическими экранами. Между камерой и корпусом имеется прямоугольное отверстие шириной 31 см и высотой 6 см, перекрытое ускоряющей сеткой. Сетка установлена так, что кромки ее пластин лежат в плоскости стенки камеры.
На верху корпуса смонтирован высоковольтный ввод. Он позволяет подключить сетку к источнику ускоряющего напряжения и изменять отрицательное напряжение на ней от нуля до 5 кВ. Снизу корпуса установлено устройство вращения, состоящее из стержня диаметром 10 мм с резьбовым гнездом М6 для соединения через отверстие в дне корпуса с держателем подложек. Вращающийся со скоростью 8 оборотов/мин стержень расположен немного ниже дна корпуса, а угол между дном и осью стержня равен 80°. Держатель подложек выполнен в виде стержня с резьбой М6 снизу и чашей глубиной 3 мм и внутренним диаметром 30 мм сверху. После соединения держателя со стержнем устройства вращения и установки в его чаше подложки диаметром 30 мм и толщиной 6 мм центр поверхности подложки оказывается на оси корпуса на расстоянии 25 см от плоскопараллельных пластин сетки.
На дне корпуса установлена также подставка для вертикальной мишени высотой 11 см и шириной 34 см из листа титана толщиной 1 мм, которую после удаления из корпуса держателя подложек можно перемещать от съемного фланца корпуса до плоскопараллельных пластин сетки. Для измерения плотности потока энергии быстрых атомов можно вместо мишени закрепить на подставке подложку диаметром 30 мм и толщиной 2 мм из нержавеющей стали, перемещать ее вдоль оси корпуса и измерять пирометром ее температуру.
Из устройства подачи газа в корпус поступает аргон. Он проходит в вакуумную камеру через зазоры между плоскопараллельными пластинами. Давление газа в камере измеряется датчиком Baratron и регулируется с пульта управления. Источник питания газового разряда и источник ускоряющего напряжения управляются с этого же пульта.
Включение источника питания между анодом и газоразрядной камерой при давлении газа 0.5 Па приводит к зажиганию тлеющего разряда с напряжением U ~ 400 В и заполнению камеры однородной плазмой. Поверхность камеры отделена от плазмы слоем положительного пространственного заряда. Ширина d этого слоя зависит от напряжения U и плотности ионного тока j из плазмы на камеру. Согласно закону Чайлда−Ленгмюра [12],
(1)
$j = (4{\text{/}}9){{\varepsilon }_{{\text{o}}}}{{(2e{\text{/}}M)}^{{1/2}}}{{U}^{{3/2}}}{\text{/}}{{d}^{2}},$При измерении массы иона M = AMo в атомных единицах массы A = 1.66 ⋅ 10– 27 кг
(2)
$j = 5.46 \cdot {{10}^{{--8}}}{{(1{\text{/}}{{M}_{{\text{o}}}})}^{{1/2}}}{{U}^{{3/2}}}{\text{/}}{{d}^{2}}.$Масса иона аргона составляет Mo = 40, и средняя ширина d слоя будет равна 5 мм при плотности ионного тока j = 2.76 А/м2 и ионном токе Ii = jS = = 2.76 ⋅ 0.72 = 2 А, где S = 0.72 м2 – площадь внутренней поверхности камеры. При энергии ионов не более 0.5 кэВ коэффициент вторичной ионно-электронной эмиссии равен γ ≈ 0.05 [13], а ионный ток практически равен току разряда I. Поэтому при токе разряда I до 2 А ширина слоя между плазмой и камерой превышает ширину зазоров между пластинами сетки, равную 4.5 мм, и равна ширине слоя между плазмой и ускоряющей сеткой.
Ионизацию газа в камере осуществляют в основном эмитированные ее стенками электроны. Они ускоряются в слое у стенки камеры, пролетают через плазму и отражаются обратно в плазму в слое у противоположной стенки. Эти электроны могут пролетать через плазму до ста раз, а длина их пути от стенки камеры до анода L = 4V/Sa, где V – объем камеры, а Sa – площадь поверхности анода [14], может превышать ширину камеры на два порядка. При постоянном токе, например I = = 2 А, разрядное напряжение U не зависит от давления p газа до тех пор, пока оно не уменьшится до критической величины po. При давлении po путь Λ, при прохождении которого эмитированные камерой электроны расходуют всю свою энергию eU на ионизацию газа, возрастает до L. Каждый из электронов образует N = eU/W ионов, где W – цена ионизации газа, для аргона равная W = 26 эВ [15]. Сопоставимый вклад в ионизацию газа вносят быстрые электроны, образованные в слое у стенки камеры.
При подаче на сетку ускоряющего напряжения Ua до 5 кВ ширина слоя объемного заряда между сеткой и плазмой увеличивается. Ионы из плазмы, ускоренные в этом слое, влетают в зазоры между пластинами сетки. Из-за неоднородности электрического поля на кромках пластин они рассеиваются на малые углы. Поэтому ионы касаются боковых поверхностей пластин и в результате превращаются в быстрые атомы инжектируемого в корпус пучка с прямоугольным поперечным сечением высотой ∼5 см и шириной ∼28 см.
Представленную на рис. 1 сетку из пластин с прямолинейными кромками, лежащими в плоскости внутренней поверхности камеры, можно заменить на сетку с криволинейными кромками, показанную на рис. 2. Участки пластин этой сетки, граничащие с плазменным эмиттером, имеют форму сегмента круга с радиусом 50 см. Поэтому траектории ускоряемых в слое между плазменным эмиттером и сеткой ионов, влетающих в зазоры между пластинами сетки, а также траектории быстрых атомов, вылетающих из сетки после нейтрализации зарядов ионов, направлены к центру этого круга.
Ширина сходящегося пучка ускоренных частиц, примерно равная 30 см вблизи плазменного эмиттера, должна снизиться в десять раз на расстоянии 5 см от центра круга, т.е. на расстоянии 30 см от плоскопараллельных пластин сетки и на расстоянии 10 см от съемного фланца. В результате на расстоянии 30 см от плоскопараллельных пластин сетки плотность потока быстрых атомов аргона в пучке возрастает в десять раз по сравнению с пучком без компрессии. Соответственно в десять раз увеличивается и скорость распыления ими подложки.
Учитывая повышение в десять раз плотности потока быстрых атомов, плотность мощности, переносимой ими на подложку, при плотности тока эмиссии j = 2.76 А/м2 ионов с энергией eU = = 400 эВ, влетающих в сетку с прозрачностью η = = 0.9, можно оценить как w = 10ηjU = 10 ⋅ 0.9 × × 2.76 ⋅ 400 ≈ 104 Вт/м2. Поверхностная плотность мощности теплового излучения подложки R* определяется ее температурой T:
где σC-Б = 5.7 ⋅ 10–8 Вт/(м2 · К4) – постоянная Стефана−Больцмана, β – коэффициент черноты подложки, а температура T измеряется в кельвинах. Учитывая, что подложка поглощает энергию одной стороной, а излучает в обе стороны, баланс поглощения и излучения можно представить в виде:Коэффициент черноты β подложки из нержавеющей стали определили с помощью пирометра IMPAC IP 140. Подложку нагрели до температуры 100°С, направили на нее пирометр и вращали регулятор коэффициента черноты до совпадения показания пирометра с температурой подложки. Величина коэффициента черноты составила β = = 0.8. При переносимой быстрыми атомами на подложку плотности мощности w = 104 Вт/м2 температура подложки, получаемая из выражения (4), равна T = (w/(2βσC-Б))1/4 = (104/(2 ⋅ 0.8 ⋅ 5.7 ⋅ 10−8))1/4 = = 575 K = 302°С.
Для получения распределения плотности потока быстрых атомов по ширине пучка на подставке внутри корпуса устанавливали титановую мишень в виде полосы толщиной 2 мм, длиной 340 мм и шириной 25 мм. Ее полированную поверхность, обращенную к ускоряющей сетке, перекрывали по всей длине маской из титановой полосы шириной 10 мм. После травления мишени пучком в течение 0.5–1 ч остывшую в вакууме подложку извлекали из корпуса, снимали с нее маску и с помощью стилусного профилометра Dektak XT производства фирмы Bruker Nano, Inc. (США) получали поперечные профилограммы поверхности подложки. Измерение высоты ступеньки между участками профилограммы, соответствующими открытой поверхности мишени, распылявшейся быстрыми атомами, и поверхности, закрытой маской, дает толщину слоя, удаляемого быстрыми атомами. Деление толщины удаленного слоя на время обработки дает скорость травления.
РЕЗУЛЬТАТЫ ЭКСПЕРИМЕНТОВ
Изучение отпечатков пучка, формируемого сеткой с прямолинейными кромками пластин (см. рис. 1), на установленной в корпусе мишени показало, что при давлении аргона p = 0.05 Па и токе I = 2 А в цепи газоразрядной камеры поперечное сечение пучка практически не изменяется с увеличением расстояния h между сеткой и мишенью. Ширина отпечатка пучка лишь немного увеличивается от 28 см при h = 2 см до 29 см при h = 40 см. Высота отпечатка также возрастает от 5 см при h = 2 см до 5.5 см при h = 40 см. При этом с ростом h границы отпечатков становятся размытыми. При подаче на сетку ускоряющего напряжения Ua = 5 кВ отпечатки становятся более четкими, а их ширина и высота при увеличении h сохраняют постоянные значения 28 и 5 см.
Измерения температуры T подложки из нержавеющей стали свидетельствуют о том, что температура слабо зависит от расстояния h до ускоряющей сетки, а при подаче на сетку ускоряющего напряжения Ua = 5 кВ возрастает от 55 до 350°С. Согласно выражению (4), это соответствует увеличению плотности потока энергии нагревающих подложку быстрых атомов аргона от 103 до 1.35 ⋅ 104 Вт/м2.
После установки сетки из пластин с криволинейными кромками температура T подложки из нержавеющей стали при давлении аргона p = 0.05 Па и токе I = 2 А в цепи камеры быстро возрастает с увеличением расстояния h до плоскопараллельных пластин сетки от T = 410°С при h = 2 см до T = 830°С при h = 30 см (рис. 3). Зависимость температуры T от расстояния h обусловлена компрессией пучка вылетающих из сетки быстрых нейтральных атомов аргона и увеличением плотности потока энергии нагревающих подложку быстрых атомов аргона.
Рис. 3.
Зависимость температуры T нагреваемой быстрыми атомами подложки от расстояния h до плоскопараллельных пластин сетки.
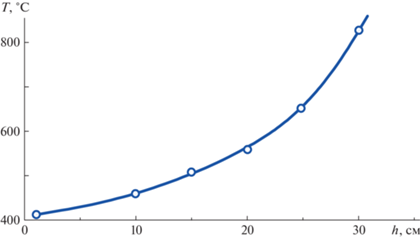
Отпечатки пучка на плоских мишенях показывают, что с увеличением расстояния h высота отпечатка сохраняет постоянное значение H = 5 см, а ширина отпечатка W снижается от W = 20 см при h = 2 см до W = 6 см при h = 25 см (рис. 4).
Рис. 4.
Зависимость ширины W отпечатка пучка быстрых атомов на плоской мишени от расстояния h до плоскопараллельных пластин сетки.
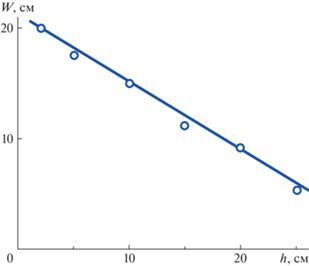
На рис. 5 представлена профилограмма поверхности титановой мишени в виде полосы длиной 34 см и шириной 25 мм, распылявшейся вместе с маской пучком, формируемым сеткой с прямолинейными кромками пластин. На ней видны два участка, соответствующие поверхности, которая была закрыта маской (слева), и открытой поверхности мишени, распылявшейся в течение 0.5 ч быстрыми атомами. Высота ступеньки между участками равна толщине удаляемого слоя титана 2.2 мкм. Эта величина сохраняет постоянное значение на участке титановой полосы длиной 28 см, что говорит об однородном распределении плотности потока быстрых атомов аргона по ширине пучка. Разделив толщину удаленного слоя титана на время его распыления быстрыми атомами аргона, получим скорость травления v = 4.4 мкм/ч.
Рис. 5.
Профилограмма поверхности мишени со ступенькой между поверхностью, закрытой маской (слева), и открытой поверхностью, распылявшейся быстрыми атомами (справа).
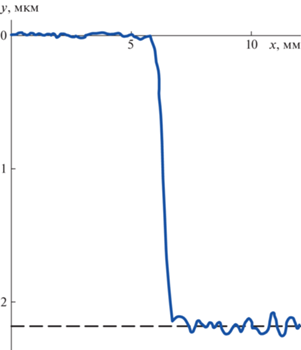
На рис. 6 представлено распределение скорости травления титановой полосы пучком, формируемым сеткой с криволинейными кромками пластин. Распределение получено при давлении аргона p = 0.05 Па, токе в цепи камеры I = 2 А и ускоряющем напряжении Ua = 5 кВ на расстоянии от плоскопараллельных пластин сетки h = 25 см. Скорость травления сохраняет постоянное значение ${v}$ = 23 мкм/ч по всей ширине пучка, равной 6 см.
Рис. 6.
Зависимость от расстояния R до оси пучка скорости травления v титановой полосы, удаленной от плоскопараллельных пластин сетки на расстояние h = 25 см.
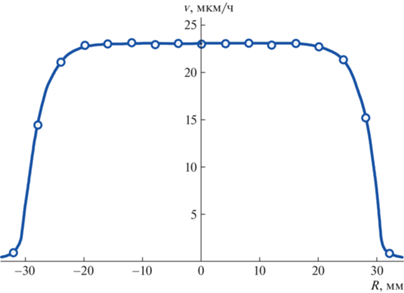
После распыления полированной титановой полосы быстрыми атомами аргона под близким к нулю углом падения шероховатость ее поверхности значительно возросла. Для исследования процесса полирования под большим углом падения, α = 80°, изготовленную из титана подложку диаметром 30 мм и толщиной 6 мм сначала закрепили на подставке, удаленной от ускоряющей сетки на расстояние h = 25 см, и в течение часа распыляли ее поверхность под нулевым углом падения атомов аргона при токе в цепи камеры I = 2 А, ускоряющем напряжении Ua = 5 кВ и давлении аргона p = 0.05 Па. Затем подставку с подложкой извлекли из корпуса и с помощью стилусного профилометра Dektak XT измерили шероховатость поверхности подложки, которая составила Ra = 0.42 мкм.
После установки на дне корпуса держателя подложек в его чашу вставили подложку с измеренной шероховатостью поверхности и в течение часа распыляли поверхность вращающейся со скоростью 8 оборотов/мин подложки под углом падения α = 80° быстрых атомов аргона при том же токе в цепи камеры I = 2 А, напряжении Ua = = 5 кВ и давлении p = 0.05 Па. Остывшую в вакууме подложку извлекли из чаши держателя и измерили шероховатость ее поверхности, которая составила Ra = 0.08 мкм. Затем подложку снова вставили в чашу держателя и распыляли еще два часа. В результате шероховатость уменьшилась до Ra = 0.01 мкм.
Чтобы изучить возможность полирования поверхности с более высокой исходной шероховатостью, были изготовлены методом аддитивной технологии подложки диаметром 30 мм и толщиной 6 мм. В качестве исходного материала для их изготовления был выбран мелкодисперсный порошок для аддитивного производства, полученный газовой атомизацией из жаропрочного сплава CoCrMo. Подложки изготавливались на промышленной установке EOS M 400 для аддитивного производства, использующей технологию селективного лазерного плавления. Измерения с помощью стилусного профилометра Dektak XT показали, что шероховатость поверхности изготовленной подложки равна Ra = 4.9 мкм. После распыления поверхности этой подложки в течение двух часов под углом падения α = 80° быстрых атомов аргона при той же скорости вращения, том же токе в цепи камеры I = 2 А и ускоряющем напряжении на сетке Ua = 5 кВ шероховатость уменьшилась до Ra = 1.6 мкм. В результате последующей обработки этой подложки в течение еще двух часов шероховатость снизилась до Ra = 0.5 мкм. После третьей обработки подложки в течение еще двух часов шероховатость уменьшилась до Ra = 0.1 мкм.
ОБСУЖДЕНИЕ РЕЗУЛЬТАТОВ
Полученные результаты подтвердили эффективность полирования металлической поверхности пучком быстрых нейтральных атомов аргона с углом падения на поверхность 80°. Шероховатость поверхности вращающейся титановой подложки была снижена от Ra = 0.42 мкм до Ra = 0.01 мкм, что соответствует четырнадцатому классу чистоты поверхности. Чтобы обеспечить такую шероховатость в течение приемлемого времени обработки, нужна плотность потока распыляющих поверхность атомов аргона, превышающая на порядок плотность тока ионов аргона из плазменного эмиттера. С этой целью осуществлена компрессия пучка ускоренных частиц с уменьшением на порядок ширины сечения пучка экстрагируемых из плазменного эмиттера ионов при неизменной высоте сечения пучка 5 см. Плазменный эмиттер создается тлеющим разрядом с электростатическим удержанием электронов в газоразрядной камере диаметром 50 см. Плотность тока ионов на ее стенку остается постоянной на расстоянии до 15 см от оси камеры и лишь затем начинает снижаться до минимальной величины на расстоянии 25 см от оси в углу между плоской и цилиндрической поверхностями камеры. Это обеспечивает высокую однородность плазмы вблизи отверстия в стенке шириной 31 см и высотой 6 см, перекрытого ускоряющей сеткой в виде набора плоскопараллельных пластин.
Ионы ускоряются из плазменного эмиттера напряжением отрицательной полярности на сетке, влетают в зазоры между ее пластинами, а при приближении к их поверхностям вызывают потенциальную эмиссию электронов, нейтрализующих их заряд. Прозрачность сетки из пластин толщиной 0.5 мм, отстоящих на расстоянии 4.5 мм друг от друга, равна 90%. Поэтому эквивалентный ток пучка вылетающих из сетки быстрых атомов составляет до 90% тока в ее цепи, а их энергия равна энергии ионов, соответствующей ускоряющему напряжению между плазменным эмиттером и сеткой.
Если участки пластин сетки, обращенные к плазменному эмиттеру, выполнены в форме сегмента круга, ионы и образованные внутри сетки быстрые атомы движутся к центру этого круга. Это позволяет на порядок уменьшить ширину пучка, увеличить плотность потока быстрых атомов и скорость распыления ими подложки. Скорость распыления возрастает также из-за повышения коэффициента распыления с увеличением энергии быстрых атомов до 5.5 кэВ. При этом скорость распыления плоской поверхности подложки в несколько раз выше скорости распыления ее цилиндрической поверхности, так как коэффициент распыления возрастает при увеличении угла падения быстрых атомов на распыляемую поверхность.
ЗАКЛЮЧЕНИЕ
1. Использование ускоряющей сетки в виде набора плоскопараллельных пластин под высоким отрицательным напряжением позволяет получать пучки быстрых нейтральных атомов с соответствующей приложенному напряжению энергией и малым угловым разбросом.
2. При выполнении участков пластин сетки, граничащих с плазменным эмиттером, в форме сегмента круга можно на порядок уменьшить ширину пучка, увеличить плотность потока быстрых атомов и скорость распыления ими подложки.
3. Компрессия пучка значительно повышает эффективность полирования поверхности пучком быстрых нейтральных атомов аргона с углом падения на поверхность 80° и позволяет снизить шероховатость поверхности титановой подложки от Ra ∼ 0.4 мкм до Ra ∼ 0.01 мкм, что соответствует четырнадцатому классу чистоты поверхности.
4. С увеличением исходной шероховатости поверхности подложки (из сплава CoCrMo) до Ra ∼ ∼ 5 мкм время, необходимое для ее полирования, возрастает до неприемлемой величины ∼10 ч.
Список литературы
Kaufman H.R. // Review of Scientific Instruments. 1990. V. 61. № 1. P. 230. https://doi.org/10.1063/1.1141883
Hayes A.V., Kanarov V., Vidinsky B. // Review of Scientific Instruments. 1996. V. 67. № 4. P. 1638. https://doi.org/10.1063/1.1146907
Gavrilov N.V., Mesyats G.A., Radkovskii G.V., Bersenev V.V. // Surface and Coatings Technology. 1997. V. 96. P. 81. https://doi.org/10.1016/S0257-8972(97)00096-0
Oks E.M., Vizir A.V., Yushkov G.Y. // Review of Scientific Instruments. 1998. V. 69. P. 853. https://doi.org/10.1063/1.1148580
Economou D.J. // Journal of Physics D: Applied physics. 2008. V. 41. 024001 https://doi.org/10.1088/0022-3727/41/2/024001
Григорьев С.Н., Мельник Ю.А., Метель А.С., Па-нин В.В. // ПТЭ. 2009. № 4. С. 166.
Grigoriev S., Metel A. // NATO Science Series II: Mathematics, Physics and Chemistry / eds. A.A. Voevodin, D.V. Shtansky, E.A. Levashov, J.J. Moore. Dordrecht: Springer, 2004. V. 155. P. 147−154. https://doi.org/10.1007/1-4020-2222-0_14
Метель А.С., Григорьев С.Н., Мельник Ю.А., Болбуков В.П. // ПТЭ. 2012. № 2. С. 149.
Григорьев С.Н., Метель А.С., Фёдоров С.В. // Металловедение и термическая обработка металлов. 2012. Т. 54. № 1. С. 9.
Volosova M., Grigoriev S., Metel A., Shein A. // Coatings. 2018. V. 8. P. 287. https://doi.org/10.3390/coatings8080287
Андрианова Н.Н., Борисов А.М., Боровская В.В., Машкова Е.С. // Прикладная физика. 2012. № 2. С. 36.
Langmuir I. // Phys. Rev. 1929. V. 33. P. 954. https://doi.org/10.1103/PhysRev.33.954
Kaminsky M. Atomic and Ionic Impact Phenomena on Metal Surfaces. Germany, Berlin, Heidelberg: Springer, 1965.
Метель А.С., Григорьев С.Н., Мельник Ю.А., Панин В.В. // Физика плазмы. 2009. Т. 35. № 12. С. 1140.
Далгарно А. Атомные и молекулярные процессы / Под ред. Д. Бейтса. М.: Мир, 1964. С. 540.
Дополнительные материалы отсутствуют.
Инструменты
Приборы и техника эксперимента