Радиотехника и электроника, 2021, T. 66, № 10, стр. 980-988
Защита цепей питания постоянного тока от короткого замыкания в нагрузке
Д. Н. Борисенко a, *, А. А. Жохов a, Б. С. Редькин a
a Институт физики твердого тела РАН
142432 Черноголовка, Московской обл., ул. Акад. Осипьяна, 2, Российская Федерация
* E-mail: bdn@issp.ac.ru
Поступила в редакцию 08.12.2020
После доработки 11.02.2021
Принята к публикации 25.02.2021
Аннотация
Рассмотрена защита цепей питания постоянного тока от короткого замыкания в нагрузке и показана принципиальная возможность предотвращения аварийных ситуаций при работе импульсных источников питания на электрическую дугу переменного тока, представляющую собой сложную нагрузку для выходных каскадов инвертора. Предложенная схема реализована и опробована при разработке источника питания дуги для развития способа 3D-печати по типу локальной гарнисажной электродуговой плавки.
1. ПОСТАНОВКА ЗАДАЧИ
При внимательном изучении всего многообразия предложенных схемотехнических решений в области защиты силовой электроники от короткого замыкания (КЗ) обращает на себя внимание тот факт, что использование современных импульсных источников питания со встроенной защитой от КЗ как в сварочной аппаратуре, так и в области индукционного нагрева, тем не менее непрерывно сопровождается аварийными режимами работы выходных каскадов DC/AC-преобразователей, приводящими к сквозным токам КЗ. Разработчики электронных схем и разработчики элементной базы (силовых транзисторов и микросхем драйверов) постоянно совершенствуют способы защиты от КЗ, однако реализация такой защиты далека от совершенства – отсутствует длительная гарантия на коммерчески доступные импульсные источники питания, а также растет объем продаж проверенных временем плавких предохранителей11. Лучшие представители плавких предохранителей (класс защиты aR, gR, gS) способны защитить силовые полупроводники только спустя 0.1…1 мс с момента возникновения аварийной ситуации22, 33 [1].
Чтобы оценить время, в течение которого транзистор еще способен сохранять свою работоспособность в случае возникновения сквозных токов КЗ (время до теплового пробоя p–n-перехода), воспользуемся тепловым расчетом времени нагрева кремниевого кристалла в адиабатическом приближении на примере n-канального MOSFET транзистора IRF840. Это время будет являться пороговым значением, относительно которого проводится оценка времени срабатывания защиты от КЗ или, другими словами, оценка запаса по устойчивости регулирования. Тепловой расчет проводили без рассмотрения причин, вызывающих токи КЗ, потому что разрабатываемая защита служит для отключения инвертора от источника питания постоянного тока, а не для устранения мгновенно или системно возникающих причин КЗ в процессе эксплуатации (токи утечки, паразитные индуктивности, выбросы электродвижущей силы самоиндукции, эффект Миллера, заводской брак при изготовлении транзисторов и микросхем драйверов). Комплексный подход к построению современных источников вторичного электропитания и расчету работы силовых транзисторов в ключевом режиме в выходных каскадах инверторов на смешанную активно-индуктивно-емкостную нагрузку с учетом всего многообразия ошибок проектирования подробно рассмотрен в [2] и представлен производителями транзисторов в специальной литературе44 ,55.
Цель данной работы – разработать схему защиты цепей питания постоянного тока от короткого замыкания в нагрузке, в частности, при возникновении сквозных токов в инверторах по причине наличия ошибок при проектировании полумостовых и мостовых схем либо их нецелевого использования.
В спецификации66 на MOSFET-транзистор IRF840 указано, что максимальная температура эксплуатации p–n-перехода равна Тmax = 150°C, рабочая температура T = 25°С, сопротивление перехода сток–исток Rс–и = 0.85 Ом, плотность кремния равна ρ = 2.33 г см–3, теплоемкость при нормальных условиях составляет CP = 710 Дж кг–1 град–1 [3]. При питании полумостовой или мостовой схемы инвертора постоянным напряжением U = 310 В в случае возникновения сквозных токов КЗ (в этом случае силовые транзисторы полумостовой или мостовой схемы включены последовательно) величина тока “мгновенно” вырастет до значения
Тепловая мощность, выделяемая на одном кристалле кремния, составит
Типовые размеры кристалла кремния, применяемые в MOSFET-транзисторах такой мощности как IRF840, в поперечном сечении составляют примерно 5 × 5 мм2 и толщина около 50 мкм [4]. Масса такого кристалла кремния равна
В адиабатическом приближении вся подводимая мощность W пойдет на разогрев кристалла с 25 до 150°С за время τ:
Таким образом, примерно через 10 мкс температура p–n-перехода достигнет максимальной температуры эксплуатации. При повышении температуры сопротивление p–n-перехода уменьшается, ток и выделяемая на кристалле мощность увеличиваются и (при сохранении аварийного режима работы) процесс развивается катастрофически. В системах автоматического регулирования оценку запаса по быстродействию управляющего воздействия определяют на основании опыта эксплуатации систем регулирования. В следящих системах, к которым относится защита от КЗ, при мгновенном изменении управляющего воздействия в большинстве случаев считается, что запас по устойчивости регулирования является достаточным, если величина перерегулирования (“время отключения” в случае электронного предохранителя) не превышает 10…30% основного установившегося значения регулируемой величины (время до теплового пробоя p–n-перехода с момента возникновения сквозных токов короткого замыкания) [5]. Таким образом, время отключения должно быть не более 1…3 мкс. Ниже приведены данные по времени отключения микросхем драйверов по разным каналам регулирования, которые хорошо согласуются с нашими расчетами.
Релейная защита, которую часто используют производители пусковых и зарядных устройств в автомобильной промышленности, в силу особенностей работы индукционных катушек, имеет среднее время срабатывания около 20 мс [6, 7]. То же самое касается и герконовых реле, время срабатывания которых лежит в интервале 0.3..1 мс [8].
Следует отметить, что в настоящее время большинство драйверов силовых IGBT/MOSFET-транзисторов проектируется со встроенной схемой защиты от КЗ. По данным, указанным производителями в спецификации на каждую модель, время срабатывания в среднем составляет:
1) ~0.3…2 мкс по каналу “CS” (Current Sense – сигнал с датчика тока),
2) ~0.1…0.3 мкс по каналу “SD” (Shutdown propagation – отключение передачи управляющих сигналов),
3) 0.5…12 мкс по каналам “FAULT” (авария) и “ERR” (ошибка).
Однако, как показала практика, даже такие малые времена срабатывания при неправильном подборе силовых транзисторов приводят к фатальным результатам как для транзисторов, так и для микросхемы драйвера, несмотря на наличие гальванической развязки и плавких предохранителей.
Важно отметить, что переменное напряжение на промышленной частоте 50 Гц за период длительностью 20 мс дважды проходит через ноль и, меняя свою полярность, нарастает и спадает по закону синуса. Поэтому автоматизированной системе времени для защиты от короткого замыкания в цепях переменного тока более чем достаточно, тем более что, пока система защиты формирует управляющий сигнал на отключение, напряжение через 5 мс с максимума само “упадет” до нуля. В цепях постоянного тока ситуация усугубляется стабильным уровнем напряжения как в процессе эксплуатации, так и при коротком замыкании, причем наличие сглаживающих фильтров с индуктивными элементами приводит в некоторых случаях после обрыва цепи к росту напряжения с последующим дуговым разрядом и термическим разрушением схемы. Поэтому защита цепей питания постоянного тока от КЗ в нагрузке является важной и актуальной задачей.
1. ЭКСПЕРИМЕНТАЛЬНАЯ ЧАСТЬ
Предложенные ранее схемотехнические решения электронных предохранителей на основе силовых транзисторов можно разделить на четыре группы:
1) схемы, которые способны надежно работать при низких напряжениях 12…36 В, но не могут быть масштабированы по напряжению до 310 В, так как при 36 В время достижения максимальной температуры эксплуатации транзистора согласно формуле
достигнет значения около 0.2 мс, что на два порядка больше того же значения для напряжения питания 310 В, при прочих равных условиях;
2) схемы, которые спроектированы с принципиальными нарушениями и могут работать только в качестве стабилизаторов тока и напряжения (в этом случае силовой транзистор работает в активном режиме усиления и сильно греется);
3) схемы с ошибками, в которых при подаче питания “триггерная защелка” сразу переводит транзистор в режим отсечки и напряжение на инвертор не подается ни при каких условиях;
4) рабочие схемы защиты цепей питания постоянного тока от короткого замыкания в нагрузке на основе драйверов силовых транзисторов, имеющие свои недостатки, с которыми пришлось столкнуться авторам при проектировании высоковольтного блока питания инверторного типа.
При проектировании высоковольтного источника питания (за основу была взята схема, предложенная С.В. Кухтецким77 (Институт химии и химической технологии СО РАН)), мы столкнулись с проблемой сквозных токов в силовых транзисторах при работе источника питания на индуктивную нагрузку, представляющую собой повышающий трансформатор 310/2000 В, высокое напряжение которого должно было обеспечить свободное горение электрической дуги переменного тока в атмосферах различных газов.
На рис. 1 представлена принципиальная схема полумостового инвертора. Отличие этой схемы от предложенной Кухтецким заключается в замене силовых транзисторов VT1 и VT2 на IRF840, который имеет низкие значения входной емкости Cвх = 1300 пФ, времени нарастания τн = 23 нс, времени задержки выключения τз выкл = 23 нс и времени спада τс = 20 нс по сравнению с теми же параметрами для транзистора IXFH30N50: Cвх = = 5200 пФ, τн = 42 нс, τз выкл = 110 нс и τс = 26 нс. Время задержки между сигналами открытия транзисторов для микросхемы полумостового драйвера IR2153D лежит в интервале τз = 0.75…1.65 мкс, поэтому мы решили использовать транзистор с меньшими временами переключения на случай возможных выбросов ЭДС-самоиндукции, вызывающими непреднамеренное переключение, приводящие к сквозным токам КЗ. В инверторе Кухтецкого в качестве нагрузки использовали индукционную печь, параметры которой были хорошо согласованы с DC/AC-преобразователем. В нашем случае использован повышающий трансформатор, вторичная обмотка которого обеспечивала технологический процесс электродуговой плавки напряжением 2000 В. В процессе электродуговой плавки выбросы ЭДС-самоиндукции не такое уж редкое явление в случае замыкания и размыкания электродов и других причин технологического характера. При таком режиме работы DC/AC-преобразователя мощный импульс тока короткого замыкания IКЗ (на рис. 1 показан стрелкой от источника питания G3 через транзистор VT1, трансформатор Т2 и конденсатор С7) в первом такте генератора импульсов IR2153D выводит из строя транзистор VT1, превратив его в проводник с “нулевым” сопротивлением, а во втором такте IR2153D открывает транзистор VT2, который также выходит из строя из-за сквозного тока КЗ. Но иногда транзистор VT1 на первом такте преобразования при КЗ разрушается, и его сопротивление становится бесконечно большим, и к моменту второго такта случайным образом электроды во вторичной обмотке трансформатора Т2 размыкаются и мощный импульс ЭДС-самоиндукции (см. рис. 1, направление тока самоиндукции IЭДС показано стрелкой) через емкость Миллера транзистора VT2 (который еще закрыт), резистор R4 и трансформатор гальванической развязки Т1 полностью разрушают микросхемы драйвера IR2153 и усилителей обоих каналов полумоста MAX4420 (резистор R4 сгорает тоже). Ни плавкие предохранители, ни трансформатор гальванической развязки не смогли обеспечить защиту цепи управления от аварийного режима работы выходного каскада инвертора. Электрическая дуга переменного тока – это сложная нагрузка для импульсных источников питания, так как выбросы ЭДС-самоиндукции два раза за период (при рабочей частоте 60 кГц и напряжении питания 310 В) представляют собой серьезное испытание для инвертора даже в отсутствие КЗ при случайном и хаотичном изменении сопротивления дугового разряда, вызванного рядом причин технологического характера. Для того чтобы согласовать такую нагрузку с источником питания, требовалась серия экспериментов, в каждом из которых с вероятностью 100% источник питания приходил бы в негодность и восстановлению не подлежал. Поэтому прежде всего было принято решение разработать электронный предохранитель, включенный в цепь с напряжением 310 В (см. рис. 1), с быстродействием, способным обеспечить безопасную работу как силовых транзисторов полумоста, так и цепи управления инвертора.
Рис. 1.
Схема полумостового инвертора с электронным предохранителем (неуказанные номиналы компонентов см. в тексте статьи и работе С.В. Кухтецкого).
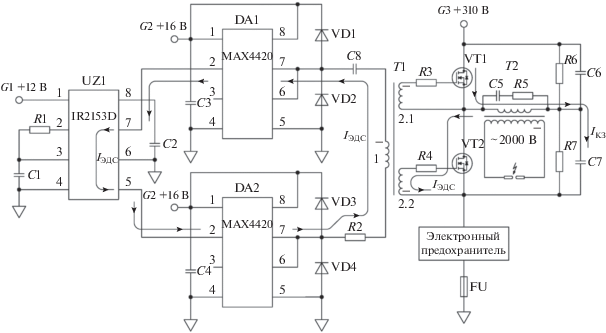
Для имитации токов КЗ в качестве нагрузки подключали лампу накаливания, что позволило избежать конфликтных ситуаций с электроснабжающими предприятиями. Блок-схема испытательного стенда для настройки и изучения работы электронного предохранителя представлена на рис. 2 (пунктирные прямоугольники). При включении холодная вольфрамовая нить лампы накаливания обладает примерно в 12 раз меньшим сопротивлением, чем разогретая до рабочих температур [9]. На переменном токе длительность прогрева для лампы мощностью 500 Вт составляет около 400 мс, а ток в холодном состоянии примерно 25 А. На постоянном токе время прогрева лампы уменьшается, но незначительно, и для имитации КЗ этого времени более чем достаточно.
Рис. 2.
Блок-схема испытательного стенда электронного предохранителя: а – ток управления идет по каналам 1–3, б – ток управления идет по каналам 2–3.
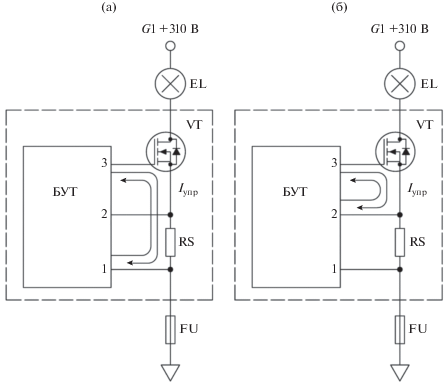
Рассмотрим работу электронного предохранителя на основе транзистора VT1 IRF840. На рис. 2 обозначены: 1–2 – канал блока управления транзистором (БУТ) для сигнала с датчика тока; 1–3 или 2–3 – каналы БУТ для сигнала управления транзистором. В качестве датчика тока RS здесь и далее использовали шунт из манганина марки 75ШИП1-50-0.5. В работе88 подробно рассмотрен вопрос проектирования блока управления транзистором для защиты от перегрузок и КЗ в цепи постоянного тока с напряжением 310 В. В итоге у автора получилась схема, в которой управляющие сигналы БУТ Iупр идут через шунт RS по каналу 1–3, как показано стрелками на рис. 2а. В этом случае импульсы тока при открытии и закрытии транзистора VT1 Iупр ≤ (±2) А соответственно складываются и вычитаются с рабочим током в шунте RS. Такая схема подключения имеет низкую помехозащищенность с гарантированным уровнем шумов на шунте ±2 А и не рекомендуется к использованию. Далее в нашей работе будем рассматривать схему электронного предохранителя, представленную на рис. 2б, где сигнал управления Iупр БУТ идет по каналу 2–3.
Первый вариант электронного предохранителя был собран на базе микросхемы драйвера “нижнего плеча” IR2121 (рис. 3). Сигнал с датчика тока RS подается на операционный усилитель (ОУ) DA3 с отрицательной обратной связью, подключенный по схеме “инвертирующего усилителя”, опорное напряжение которого на неинвертирующем входе равно нулю, а входной сигнал отрицательного значения подается на инвертирующий вход. Как следствие, на выходе ОУ DA3 имеем всегда положительное значение. Стоит отметить, что, регулируя коэффициент усиления резистором R7, мы можем не только устанавливать порог срабатывания электронного предохранителя, но и влиять на скорость его срабатывания. Дело в том, что важной характеристикой ОУ является скорость нарастания выходного напряжения, измеряемая в единицах В мкс–1. Для ОУ DA3 TL081 скорость нарастания выходного напряжения составляет 16 В мкс–1. Выставляя коэффициент усиления, равным Ку ≈ 102, получаем на выходе ОУ типовые значения напряжения ~1 В, на что ОУ потребуется около 1/16 мкс или ~60 нс. Чем выше коэффициент усиления, тем выше напряжение на выходе усилителя и тем больше времени требуется ОУ, чтобы достигнуть такого значения.
Таким образом, коэффициент усиления лучше настраивать в разумных пределах с учетом шумов в цепи 310 В, а порог срабатывания настраивать резистором R8 через величину опорного напряжения инвертирующего входа компаратора DA2, причем “дребезг” управляющего сигнала в цепи обратной связи при таком подходе будет меньше [10]. Для уменьшения “дребезга” выходного сигнала компаратор снабжен положительной обратной связью, величина гистерезиса регулируется резистором R3. В наших экспериментах величину резистора R3 изменяли в диапазоне 1..2 МОм. Выбор микросхемы LM393 в качестве компаратора DA2 был обусловлен следующими причинами: достаточно быстрым временем отклика 300 нс на большой дифференциальный сигнал на входе, защитой от статического электричества вплоть до ±1300 В, высоким напряжением питания 36 В и наличием открытого коллектора на выходе компаратора с возможностью подключать подтягивающий резистор к любому источнику напряжению отличному от питания компаратора, но не выше 36 В (в этой работе данная возможность не использовалась, так как для открытия транзисторов хватило напряжения питания компаратора 14 В).
Так как микросхема драйвера нижнего плеча IR2121 не рассчитана на работу с высоким напряжением, то для увеличения надежности работы электронного предохранителя была разработана схема испытательного стенда на высоковольтных MOSFET-транзисторах IRF840 (рис. 4). Сигнал с датчика тока RS после усиления операционным усилителем DA2 TL081 и однопороговой оцифровки компаратором DA1 LM393 подается на транзистор VT6 IRF840, который управляет в ключевом режиме симметричным триггером, собранным на транзисторах VT3 IRF840 и VT4 IRF840; бустер на транзисторах VT2 IRF840 и VT7 IRF840 ускоряет включение и выключение транзистора VT5 IRF840; с помощью кнопки SB и транзистора VT1 IRF840 осуществляют перезапуск триггера после срабатывания защиты в случае КЗ; световая индикация работы триггера обеспечивается светодиодами HL1 и HL2.
2. РЕЗУЛЬТАТЫ И ОБСУЖДЕНИЕ
Для проверки работоспособности схемы, представленной на рис. 3, и изучения ее быстродействия оцифрованный после компаратора сигнал подавался через переключатель SA на входы ERR и CS микросхемы DA1 IR2121. Кнопка SB служит для перезапуска микросхемы после устранения КЗ в цепи 310 В путем снятия и подачи напряжения питания +14 В на вход драйвера IN. При подаче управляющего напряжения на канал CS скорость срабатывания оказалась выше по сравнению с каналом ERR. Полученные экспериментальные данные хорошо согласуются с заявленными в спецификации параметрами. После проведения серии успешных экспериментов при разных установленных пороговых значениях тока было принято решение провести эксперимент, повторяющий условия работы транзистора VT1 IRF840 (см. рис. 3) в составе полумостовой схемы инвертора, т.е. был выставлен порог срабатывания по току 50 А, что выше допустимого предела, заявленного в спецификации на транзистор (максимальное значение тока в импульсном режиме для IRF840 равно 32 А). Как и прогнозировалось, транзистор сгорел и вывел из строя микросхему драйвера. Максимальный ущерб для источника питания постоянным напряжением 310 В (на схеме не показан) в целом удалось избежать благодаря плавкому предохранителю FU и двум лампам накаливания мощностью 500 Вт, включенным параллельно для достижения тока 50 А. Операционный усилитель DA3 и компаратор DA2 (см. рис. 3) не пострадали.
Таким образом, экспериментально было показано, что спасать силовой транзистор в составе инвертора за пределами его рабочих токовых характеристик с помощью сигнала с датчика тока по цепи обратной связи не имеет никакого смысла и противоречит принципу причинности, устанавливающему допустимые пределы влияния событий друг на друга. Другими словами, сигнал управления был подан на исполняющий элемент (транзистор), который уже сгорел, тем более что этот управляющий сигнал никак не устраняет причину аварийной ситуации, например выброс ЭДС-самоиндукции, возникающий в трансформаторе Т2 (см. рис. 1), причем снаббер C5-R5 (см. рис. 1) не всегда способен защитить силовые транзисторы инвертора, тем более при работе на такую сложную нагрузку как электрическая дуга. Зависимость номинала конденсатора снаббера от нагрузки значительно усложняет расчет схемы и снижает надежность работы этого демпфирующего устройства в случае, когда электродуговой разряд имеет различную длину, давление, потенциал ионизации и теплопроводность газа. Применение супрессоров тоже не всегда позволяет до конца решить проблему гашения импульсов ЭДС-самоиндукции: быстродействие супрессоров составляет не более десятков наносекунд, но и длительность работы супрессора редко превышает сотни наносекунд, т.е. импульсная мощность у них относительно небольшая [11]. Таким образом, даже если допустить, что управляющий сигнал защиты от КЗ успеет выключить силовой транзистор в составе полумостового инвертора, то мощный выброс ЭДС-самоиндукции все равно разрушит p‒n-переход импульсом высокого напряжения, и авария неизбежна. Исходя из этих рассуждений, мы пришли к простому выводу, что функция электронного предохранителя не может быть делегирована транзисторам полумостового инвертора, а должна быть исполнена отдельным модулем и не зависеть от работоспособности инвертора.
Электронный предохранитель, схема которого представлена на рис. 4, показал хорошие результаты работы как по скорости срабатывания, так и по степени защиты по напряжению управляющего канала 2–3 (см. рис. 2) по сравнению с микросхемой драйвера IR2121. После небольших изменений схема оказалась полезной для реализации простого способа измерения времени отключения электронного предохранителя. Если в схеме на рис. 4 транзистор VT6 IRF840 заменить комплиментарной парой транзисторов VT6 IRF630 и VT7 IRF9630, то бистабильный мультивибратор на транзисторах VT3 IRF840 и VT4 IRF840 будет выступать в роли генератора импульсов с внешней синхронизацией (рис. 5), период которых в среднем будет равен удвоенному времени отключения электронного предохранителя. В результате прямых измерений тестером частоты было определено, что время срабатывания рассматриваемой схемы лежит в интервале 2…5 мкс, что хорошо согласуется с данными, полученными из осциллограмм, изображенных на рис. 6а. На рис. 6а представлена осциллограмма управляющих импульсов на затворе VT5 IRF840 (см. рис. 5). Если транзистор VT8 IRF840 (см. рис. 5) в составе бустера заменить на резистор номиналом 1 кОм, то осциллограмма примет вид, представленный на рис. 6б.
Рис. 6.
Осциллограммы генератора импульсов (см. рис. 5) с бустером на транзисторах VT2 и VT8 (кривая 1) и без транзистора VT8 (кривая 2).
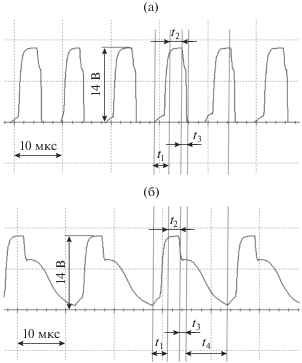
В соответствии с обозначениями транзисторов на рис. 5 принято на рис. 6:
– время t1 – это время, за которое транзистор VT5 IRF840 полностью открывается при подаче на него напряжения 14 В транзистором VT2 IRF840, а ток в цепи 310 В достигает установленной пороговой величины КЗ.
– время t2 – это время, в течение которого в цепи 310 В течет ток КЗ и одновременно в электронном предохранителе формируется сигнал управления на отключение транзистора на основе сигнала с датчика тока RS или, другими словами, время распространения сигнала по петле обратной связи RS-DA2-DA1-VT6-VT8-VT5 (закрыт).
– время t3 – это длительность переходных процессов в транзисторе VT5 IRF840 после получения сигнала на отключение при наличии бустера VT2 IRF840 и VT8 IRF840.
– время t3+ t4 – длительность переходных процессов в транзисторе VT5 IRF840 после получения сигнала на отключение при замене в бустере транзистора VT8 IRF840 на резистор номиналом 1 кОм.
Из представленных на рис. 6а и 6б данных наглядно видно преимущество бустерной схемы управления силовым транзистором VT5 IRF840, что неоднократно отмечалось многими авторами [12]. В представленном масштабе время t2 ≈ 2.5 мкс, время t3 ≈ 1.3 мкс. Таким образом, время отключения электронного предохранителя, схема которого представлена на рис. 4 и 5, составляет около 3.8 мкс. Эти данные хорошо согласуются с результатами прямых измерений тестером частоты следования импульсов.
ЗАКЛЮЧЕНИЕ
Рассмотрена защита цепей питания постоянного тока от короткого замыкания в нагрузке и показана принципиальная возможность предотвращения аварийных ситуаций при работе импульсных источников питания на электрическую дугу переменного тока, представляющую собой сложную нагрузку для выходных каскадов инвертора. Так как управляющий сигнал всегда запаздывает относительно причин, его вызывающих (в отсутствие предиктора, конечно), то защитить силовой транзистор от теплового пробоя возможно лишь в рамках его допустимых рабочих характеристик. Несмотря на то, что быстродействие схемы во много раз может превышать скорость нагрева кремниевого кристалла при КЗ, не будем забывать о деградации свойств p–n-перехода даже при его кратковременном аварийном нагреве при сохранении работоспособности. Поэтому если ток короткого замыкания будет превышать допустимый максимальный ток транзистора, то авария рано или поздно неизбежна. Сквозные токи короткого замыкания в инверторах могут быть вызваны различными причинами. На эти причины не оказывает никакого влияния сигнал на отключение силового транзистора, чаще всего уже сгоревшего к моменту аварийного отключения.
Таким образом, можно сделать вывод, что защита от КЗ должна быть выполнена отдельным модулем и никак не зависеть от работоспособности инвертора, а лишь отключать его от источника питания постоянного напряжения, причем силовой транзистор электронного предохранителя должен иметь запас по его рабочим характеристикам относительно режима КЗ. Предложенная схема реализована и опробована при разработке источника питания дуги для способа 3D-печати по типу локальной гарнисажной электродуговой плавки.
Список литературы
Blaabjerg F., Iov F., Ries K. // J. Power Electronics. 2002. V. 2. № 2. P. 88.
Битюков В.К., Симачков Д.С., Бабенко В.П. Источники вторичного электропитания. М.: Инфра-Инженерия, 2019.
Шелудяк Ю.Е., Кашпоров Л.Я., Малинин Л.А. и др. Теплофизические свойства компонентов горючих систем. Справочник / Под ред. Н. А. Силина. М.: НПО Информ ТЭИ, 1992.
Боднарь Д. // Компоненты и технологии. 2012. № 11. С. 116.
Бесекерский В.А., Попов Е.П. Теория систем автоматического регулирования. М.: Наука, 1972.
Степанов В.М., Казаков А.О. // Изв. ТулГУ. Технические науки. 2013. Вып. 12. Ч. 2. С. 95.
Гуревич В.И. // Проблемы энергетики. 2008. № 1–2. С. 11.
Карабанов С., Майзельс Р. // Компоненты и технологии. 2001. № 7. С. 28.
Савалёв А.С., Шайхеева Г.Р. // Тр. XI Всерос. научно-практич. конф. “Современные проблемы проектирования, производства и эксплуатации радиотехнических систем”. Ульяновск. 10–11 окт. 2019 г. Ульяновск: Изд-во УлГТУ, 2019. С. 251.
Хоровиц П., Хилл У. Искусство схемотехники. М.: БИНОМ, 2014.
Новиков П. // Силовая электроника. 2019. № 2. С. 4.
Семенов Б.Ю. Силовая электроника: от простого к сложному. М.: СОЛОН-Пресс, 2005.
Дополнительные материалы отсутствуют.
Инструменты
Радиотехника и электроника