Расплавы, 2022, № 4, стр. 384-394
Термодинамическое моделирование фьюмингования шлаков медной плавки
А. С. Вусихис a, *, Л. И. Леонтьев a, С. В. Сергеева a
a Институт металлургии УрО РАН
Екатеринбург, Россия
* E-mail: vas58@mail.ru
Поступила в редакцию 27.02.2022
После доработки 20.03.2022
Принята к публикации 23.03.2022
- EDN: KMEIWW
- DOI: 10.31857/S0235010622040120
Аннотация
Для описания процессов фьюмингования шлаков медной плавки продуктами конверсии метана кислородом при различном коэффициенте расхода кислорода (α), меняющемся от 0.25 до 0.75, в интервале температур 1473–1773 К применена методика термодинамического моделирования в приближении к открытым системам, с дробным введением исходного газа-восстановителя и периодическим выводом металлической фазы и отходящих газов из состава рабочего тела. Выявлены взаимосвязи содержаний оксидов железа и цинка в оксидном расплаве и степеней их восстановления от температуры и количества введенного восстановителя. Термодинамическое равновесие систем рассчитывалось при допущении идеальности растворов, т.е. при коэффициенте активности оксида цинка, равном 1. В реальных условиях шлакового расплава медной плавки aZnO близок к 3. Поэтому количественные показатели промышленной плавки отличаются от расчетных. В то же время изменение параметров плавки относительно друг друга будет одинаково. Основной результат работы – сравнительный анализ протекания процессов в зависимости от температуры и состава газа-восстановителя. Показано, что количество продуктов конверсии и соответственно природного газа, необходимого для их получения, необходимое для восстановления металлов до фиксированной степени извлечения цинка существенно зависит от температуры и состава газа. Полученные сведения полезны для прогнозирования термоэкстракционных процессов, протекающих при извлечении полезных компонентов из шлаков цветной металлургии.
ВВЕДЕНИЕ
Шлаки автогенной плавки медных сульфидных руд [1–7] могут содержать большое количество цинка. Одним из способов его извлечения является фьюмингование, в основе которого лежит барботаж оксидного расплава газом-восстановителем [7–9]. В связи с этим оценка влияния состава газа и температуры на ход процесса представляется важной задачей.
Для предварительного анализа параметров протекания различных металлургических процессов с целью решения задач совершенствования металлургических технологий широко используют термодинамическое моделирование (ТДМ) [10–13], в том числе при изучении восстановительной обработки шлаковых расплавов при их обеднении, обеспечивающих высокое извлечение из них цветных металлов. В результате проведенных расчетов получены данные о фазовом составе исходных и восстановленных шлаков, определены формы нахождения в них цветных металлов, закономерности распределения цветных металлов между сплавом и шлаком, влияние на него кислородного потенциала взаимодействующих с ними газов [14–18].
Однако, существующие методологии ТДМ предназначены для анализа равновесия в закрытых системах, что не отвечает реальным процессам в пирометаллургических агрегатах. Авторами данной работы разработана методика, позволяющая приблизить данные ТДМ к реальным процессам восстановления металлов из многокомпонентных оксидных расплавов [19]. Основное различие методик заключается в том, что в первом случае рассматривают равновесие в системе при одном и том же составе исходного расплава в зависимости от количества введенного в нее газа-восстановителя, а во втором, в проведении расчетных циклов с шаговым приближением к требуемой степени восстановления металлов, с одновременным выводом из состава рабочего тела образовавшихся газов и металлической фазы. Этот подход позволяет моделировать процессы и качественно оценить полноту протекания реакций в пирометаллургических агрегатах, использующих барботаж расплава газом-восстановителем.
При апробации метода ТДМ на процессах восстановления железа и никеля монооксидом углерода получено хорошее совпадение расчетных и экспериментальных данных [19]. Ранее указанная методика была применена для моделирования процессов восстановления железа и никеля из рудных и модельных расплавов различными газами-восстановителями [20–22].
В настоящей работе методами термодинамического моделирования проанализированы процессы барботажа оксидного расплава, близкого по составу шлаку медной плавки в печи Ванюкова СУМЗ [23]. В качестве газа-восстановителя, приняты продукты кислородной конверсии метана при различном коэффициенте расхода кислорода (α) по реакции
где α – коэффициент расхода, определяемый как отношение количества кислорода, поданного на окисление углеводородов, к его количеству, необходимому для полного окисления метана до СО2 и Н2О по реакции СН4 + 2О2 → СО2 + 2Н2, k, h, m и n – коэффициенты, определяющие количество образующихся газов при окислении СН4 для заданного α.МЕТОДИКА ТЕРМОДИНАМИЧЕСКИХ РАСЧЕТОВ
Математическая модель ТДМ предусматривает следующие допущения.
1. Скорость взаимодействия оксидов восстанавливаемых металлов с газом-восстановителем настолько велика, что при всплывании в оксидном расплаве пузыря газа в нем достигается равновесие.
2. После взаимодействия с очередной порцией газа концентрация оксидов меняется мгновенно и по всему объему расплава.
Расчет дробится на циклы, в каждом последующем из которых предусмотрено участие только оксидной фазы с достигнутым содержанием оксидов восстанавливаемых металлов и выводом из системы газа и металлической составляющей. Расчет проводится по (Z) последовательным циклам с введением восстановителя в количестве (n) молей в единичной порции.
Расчет ведут следующим образом:
Задаются исходные составы расплава и газа и их количество
(2)
$\sum\limits_{j{\kern 1pt} = {\kern 1pt} 1}^{j{\kern 1pt} = {\kern 1pt} n} {N_{{0,j}}^{{(s)}},} \,\,\,\,\sum\limits_{i{\kern 1pt} = {\kern 1pt} 1}^{i{\kern 1pt} = {\kern 1pt} m} {N_{i}^{{\{ g\} }},} $Производится расчет равновесия в системе
(3)
$\sum\limits_{j{\kern 1pt} = {\kern 1pt} 1}^{j{\kern 1pt} = {\kern 1pt} n} {N_{{0,j}}^{{(s)}}} + \sum\limits_{i{\kern 1pt} = {\kern 1pt} 1}^{i{\kern 1pt} = {\kern 1pt} m} {N_{i}^{{\{ g\} }}} \to \sum\limits_{j{\kern 1pt} = {\kern 1pt} 1}^{j{\kern 1pt} = {\kern 1pt} n} {N_{{1,j}}^{{(s)}}} + \sum\limits_{b{\kern 1pt} = {\kern 1pt} 1}^{b{\kern 1pt} = {\kern 1pt} c} {N_{{1,b}}^{{[s]}}} + \sum\limits_{i{\kern 1pt} = {\kern 1pt} 1}^{i{\kern 1pt} = {\kern 1pt} m} {N_{{i,1}}^{{\{ g\} }},} $Задается новый исходный состав оксидного расплава, количество оксидов в котором равно равновесному содержанию
(4)
$\sum\limits_{j{\kern 1pt} = {\kern 1pt} 1}^{j{\kern 1pt} = {\kern 1pt} n} {N_{{1,j}}^{{(s)}}.} $Повторяется расчет равновесия системы с новыми исходными данными (состав газа-восстановителя, подаваемого в систему, и его количество не меняются, а компоненты системы, находящиеся в металлическом состоянии, выводятся из системы и при расчете равновесия не учитываются).
(5)
$\sum\limits_{j{\kern 1pt} = {\kern 1pt} 1}^{j{\kern 1pt} = {\kern 1pt} n} {N_{{1,j}}^{{(s)}}} + \sum\limits_{i{\kern 1pt} = {\kern 1pt} 1}^{i{\kern 1pt} = {\kern 1pt} m} {N_{i}^{{\{ g\} }}} \to \sum\limits_{j{\kern 1pt} = {\kern 1pt} 1}^{j{\kern 1pt} = {\kern 1pt} n} {N_{{2,j}}^{{(s)}}} + \sum\limits_{b{\kern 1pt} = {\kern 1pt} 1}^{b{\kern 1pt} = {\kern 1pt} c} {N_{{2,b}}^{{[s]}}} + \sum\limits_{i{\kern 1pt} = {\kern 1pt} 1}^{i{\kern 1pt} = {\kern 1pt} m} {N_{{i,2}}^{{\{ g\} }},} $Цикл повторяется до тех пор, пока количество восстанавливаемых оксидов в расплаве не уменьшится до заданной величины.
Применение методики позволяет определять, в зависимости от количества введенного газа-восстановителя (Vg), следующие величины: содержание оксидов (CMeO) в шлаке и металлов (CMe) в сплавах, коэффициенты перехода компонентов в элементное состояние (φMe) и межфазное распределение элементов. Расчеты проведены с использованием программного комплекса и базы данных ИВТАНТЕРМО.
В качестве конденсированной фазы рабочего тела выбрана оксидная система массой 1.03 кг, близкая по составу шлакам медной плавки и содержащая, мас. %: 36.41 FeO, 15.79 Fe3O4, 31.51 SiO2, 7.88 ZnO, 3.97 Al2O3, 3.27 CaO, 1.17 MgO. Расчеты проведены при давлении 0.1 МПа и температурах 1473–1773 К. Единичный цикл расчетов соответствовал количеству конвертированного газа 21.87 дм3 на килограмм оксидов. В расчетах принято, что, исходя из диаграммы состояния Fe–Zn, металлические продукты восстановления взаимно нерастворимы [24]. Для рассматриваемого интервала температур цинк находится в газообразном состоянии. Термодинамическое равновесие систем рассчитывалось при допущении идеальности растворов, а основной результат – это сравнительный анализ протекания процессов в зависимости от температуры и состава газа-восстановителя.
В ходе расчетов вели оценку изменения содержания оксидов цинка (СZnO) и железа (${{С}_{{{\text{F}}{{{\text{e}}}_{{\text{3}}}}{{{\text{O}}}_{{\text{4}}}}}}},$ СFeO) в рабочем теле (РТ) от количества введенного газа (Vg). Степень восстановления цинка (φZn) и железа (φFe) до металлического состояния определяли по выражению:
где mМе – масса элемента в металлическом состоянии; mМеО – масса элемента в виде оксидов в исходном рабочем теле.РЕЗУЛЬТАТЫ И ИХ ОБСУЖДЕНИЕ
Предварительно были проведены термодинамические расчеты состава продуктов кислородной конверсии метана, используемых в качестве газа-восстановителя при термодинамическом моделировании барботажного восстановления металлов из оксидного расплава для температур 1473–1773 К. Соотношения объемов кислорода $\left( {{{V}_{{{{{\text{О}}}_{{\text{2}}}}}}}} \right)$ и метана $\left( {{{V}_{{{\text{С}}{{{\text{Н}}}_{{\text{4}}}}}}}} \right)$ в конвертируемой смеси $\left( {{{{{V}_{{{{{\text{О}}}_{{\text{2}}}}}}}} \mathord{\left/ {\vphantom {{{{V}_{{{{{\text{О}}}_{{\text{2}}}}}}}} {{{V}_{{{\text{С}}{{{\text{Н}}}_{{\text{4}}}}}}}}}} \right. \kern-0em} {{{V}_{{{\text{С}}{{{\text{Н}}}_{{\text{4}}}}}}}}}} \right)$ соответствуют уравнению (1) откуда рассчитан состав конвертированного газа (табл. 1).
Таблица 1.
Составы конвертированных газов, взятых для термодинамических расчетов
α | ${{{{V}_{{{{{\text{О}}}_{2}}}}}} \mathord{\left/ {\vphantom {{{{V}_{{{{{\text{О}}}_{2}}}}}} {{{V}_{{{\text{С}}{{{\text{Н}}}_{4}}}}}}}} \right. \kern-0em} {{{V}_{{{\text{С}}{{{\text{Н}}}_{4}}}}}}},$ моль/моль | Т, К | Состав газа, % | ||||
---|---|---|---|---|---|---|---|
Н2 | СО | СН4 | Н2О | СО2 | |||
0.25 | 0.5 | 1473 | 66.5 | 33.3 | 0.1 | 0.1 | 0.0 |
1573 | 66.6 | 33.3 | 0.0 | 0.0 | 0.0 | ||
1673 | 66.6 | 33.3 | 0.0 | 0.0 | 0.0 | ||
1773 | 66.6 | 33.3 | 0.0 | 0.0 | 0.0 | ||
0.33 | 0.7 | 1473 | 55.8 | 30.9 | 0.0 | 10.9 | 2.4 |
1573 | 55.5 | 31.2 | 0.0 | 11.2 | 2.2 | ||
1673 | 55.3 | 31.4 | 0.0 | 11.4 | 1.9 | ||
1773 | 55.1 | 31.6 | 0.0 | 11.6 | 1.8 | ||
0.5 | 1 | 1473 | 40.3 | 26.4 | 0.0 | 26.4 | 7.0 |
1573 | 39.7 | 27.0 | 0.0 | 27.0 | 6.3 | ||
1673 | 39.2 | 27.5 | 0.0 | 27.5 | 5.8 | ||
1773 | 38.7 | 27.9 | 0.0 | 27.9 | 5.4 | ||
0.75 | 1.5 | 1473 | 17.6 | 15.7 | 0.0 | 49.1 | 17.6 |
1573 | 16.8 | 16.5 | 0.0 | 49.8 | 16.8 | ||
1673 | 16.2 | 17.2 | 0.0 | 50.5 | 16.2 | ||
1773 | 15.6 | 17.7 | 0.0 | 51.1 | 15.6 |
При α = 0.25 температура слабо влияет на состав конвертированного газа. В остальных случаях с ростом температуры количество Н2 и СО2 в газе несколько снижается, а СО и Н2О повышается.
Анализ результатов термодинамического моделирования барботажного восстановления (рис. 1) показал следующее.
Рис. 1.
Изменение содержания оксидов железа (CFeO, ${{C}_{{{\text{F}}{{{\text{e}}}_{{\text{3}}}}{{{\text{O}}}_{{\text{4}}}}}}}$) и цинка (CZnO) (а) в расплаве, степени металлизации цинка (φZn) и железа (φFe) (б), содержания цинка в отходящем газе (CZn) (в) в зависимости от количества конвертированного газа (Vg), при температурах 1473–1773 K.
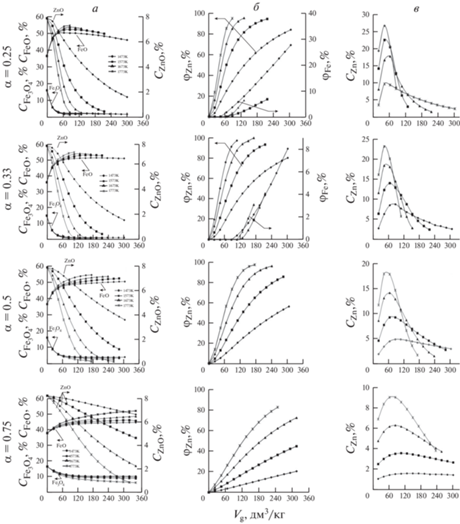
Процесс можно разделить на несколько этапов. На первом этапе происходит восстановление Fe3+ до Fe2+ и Zn2+ до Zn0. За счет этого содержание в оксидном расплаве Fe3O4 и ZnO снижается, а FeO – увеличивается. С ростом расхода газа количество цинка, восстановленного единичной порцией газа, увеличивается, что приводит к возрастанию его концентрации в отходящем газе до максимального значения, соответствующего окончанию этапа. Не зависимо от состава газа повышение температуры интенсифицирует восстановление, поэтому одному и тому же количеству введенного газа, соответствует более низкие содержания Fe3O4 и ZnO и более высокие – FeO, а окончание этапа наступает раньше. С увеличением α от 0.25 до 0.75 окончание первого этапа наступает при больших расходах газа.
На втором этапе продолжается снижение содержаний в оксидном расплаве Fe3O4 и ZnO и увеличение FeO. Такой ход процесса наблюдается при барботаже оксидного расплава продуктами кислородной конверсии метана при коэффициенте расхода α > 0.33 конвертированным газом независимо от его количества и состава в температурном интервале 1473–1773 К.
В случае использования конвертированного газа, полученного при α ≤ 0.33, можно выделить третий этап – наблюдается появление в системе металлического железа, что сопровождается снижением содержания FeO в расплаве. Аналогичные результаты достигнуты в ходе экспериментальных исследований [25, 26].
Для оценки возможности использования полученных результатов при описании процессов извлечения цинка из высокожелезистых оксидных расплавов путем барботажа продуктами конверсии природного газа, для пояснения механизма восстановления и кинетических особенностей, а также разработки методики ведения таких процессов в лабораторных и промышленных условиях, их сравнили с результатами фьюмингования шлаков, близких по составу к рассматриваемым в настоящей статье, в промышленных печах емкостью 30 и 75 т продуктами конверсии природного газа при коэффициенте расхода воздуха 0.75 до степени извлечения цинка 85% [8, 27]. Расход природного газа на промышленные плавки много меньше, чем это получилось при моделировании (170 против 450 дм3/кг). Это связано с тем, что при расчетах расплавы принимали как идеальные растворы с коэффициентами активности γ равными 1. В реальных шлаках, согласно данным различных авторов [28, 29], γ ~ 3, поэтому количество цинка, восстанавливаемое единичной порцией газа, реально будет больше, чем по расчетам, а значит общий расход газа – меньше. В то же время изменение параметров плавки относительно друг друга будет одинаково. Так интенсивность процесса восстановления при изменении температуры от 1473 до 1573 К в обоих случаях будет меняться в два раза.
Таким образом, количественно расчетные показатели, полученные в результате моделирования, будут отличаться от реальных, но для сопоставления влияния температуры и состава газа на ход процесса их вполне можно использовать.
Сопоставительный анализ показателей восстановления, достигнутых к конечному циклу (табл. 2), свидетельствует о следующем. Рост температуры интенсифицирует восстановление цинка и сокращает потребляемое количество газа-восстановителя. Минимальное количество газа, полученного в результате конверсии метана $\left( {{{V}_{{{\text{С}}{{{\text{Н}}}_{{\text{4}}}}}}}} \right)$ при α = 0.25, необходимое для восстановления цинка до степени извлечения (φZn) ~ 96%, расходуется при температуре 1773 К. При этом цинк на 2/3 восстанавливается водородом, доля использования которого (V1/V2), определяемая как отношение количества водорода, пошедшего в реакцию к его количеству, барботируемому в расплав, составляет более 50%, доля СО в два раза меньше (26.4%). При снижении температуры увеличивается количество конвертированного газа, участвующего в процессе барботажа, но снижается доля использования, как водорода, так и монооксида углерода. По мере увеличения α (при одинаковых температурах) количество водорода и СО в единичной порции газа уменьшается, поэтому общий расход газа увеличивается, но так же, как и при α = 0.25 с ростом температуры общий расход газа уменьшается.
Таблица 2.
Параметры, достигнутые в заключительном цикле расчетов по барботажному восстановлению цинка с использованием конвертированного газа (α = 0.25–0.75)
α | Т, К | Vg, дм3/кг | ${{V}_{{{\text{С}}{{{\text{Н}}}_{4}}}}},$ дм3/кг | φZn, % | φFe, % | СZnO мас. % | CFeO, мас. % | ${{C}_{{{\text{F}}{{{\text{e}}}_{3}}{{{\text{O}}}_{4}}}}},$ мас. % | V1/V2, % | |
---|---|---|---|---|---|---|---|---|---|---|
Н2 | СО | |||||||||
0.25 | 1473 | 304 | 101 | 85.2 | 28 | 1.6 | 46 | 1.3 | 30.5 | 15.3 |
1573 | 217 | 72 | 95.8 | 17.1 | 0.4 | 49.9 | 1.5 | 34.7 | 16.1 | |
1673 | 130 | 43 | 96.7 | 6.5 | 0.3 | 53.0 | 1.4 | 42.4 | 19.7 | |
1773 | 87 | 29 | 96.3 | 1.4 | 0.3 | 54.7 | 0.9 | 52.6 | 26.4 | |
0.33 | 1473 | 304 | 101 | 80.4 | 8 | 1.7 | 51.2 | 2.1 | 19.6 | 9.6 |
1573 | 217 | 72 | 93.4 | 4.1 | 0.6 | 53.0 | 1.9 | 25.8 | 13.7 | |
1673 | 152 | 51 | 96.9 | 1.9 | 0.3 | 54.1 | 1.5 | 32.9 | 16.3 | |
1773 | 109 | 36 | 97.4 | 0.0 | 0.2 | 55.1 | 1,0 | 46.0 | 25.4 | |
0.5 | 1473 | 304 | 101 | 57 | 0.0 | 3.6 | 50.5 | 3.8 | 14.0 | 8.6 |
1573 | 283 | 94 | 86.5 | 0.0 | 1.2 | 52.3 | 3.3 | 20.0 | 11.4 | |
1673 | 239 | 80 | 97.2 | 0.0 | 0.2 | 53.6 | 2.4 | 24.1 | 13.7 | |
1773 | 174 | 58 | 98.6 | 0.0 | 0.1 | 54.5 | 1.6 | 36.5 | 21.8 | |
0.75 | 1473 | 304 | 101 | 21 | 0.0 | 6.4 | 42.8 | 10.1 | 11.4 | 9.5 |
1573 | 304 | 101 | 45.9 | 0.0 | 4.4 | 43.8 | 9.1 | 17.8 | 13.0 | |
1673 | 304 | 101 | 74.2 | 0.0 | 2.2 | 46.1 | 8.7 | 27.0 | 19.7 | |
1773 | 304 | 101 | 92.5 | 0.0 | 0.6 | 49.0 | 6.1 | 30.8 | 27.8 |
ВЫВОДЫ
Сравнительный анализ полученных результатов позволяет сделать вывод о том, что процесс фьюмингования наиболее эффективно вести при температурах выше 1773 и коэффициенте расхода кислорода менее 0.33. В этих условиях восстанавливается только цинк. Снижение температуры приводит к увеличению расхода газа и появлению в расплаве металлического железа, что отрицательно сказывается на процессе в целом.
При коэффициенте расхода кислорода более 0.33 восстановление оксидов железа до металла не происходит, но при этом увеличивается расход газа для достижения фиксированной степени восстановления цинка.
Полученные результаты полезны для планирования экспериментальных работ как в лабораторных, так и в промышленных условиях. Их следует учитывать при моделировании процессов, интерпретации достигнутых результатов и использовании для оптимизации пирометаллургических процессов.
Работа выполнена по Государственному заданию ИМЕТ УрО РАН.
Список литературы
Ванюков A.B., Быстров В.П., Васкевич А.Д. и др. Плавка в жидкой ванне. М.: Металлургия, 1986.
Халемский А.М., Тарасов А.В., Казанцев А.Н., Кинев В.Д. Плавка в печи Ванюкова медно-цинкового сульфидного сырья. Екатеринбург: Кедр, 1993.
Schlesinger M.E., King M.J., Sole K.C., Davenport W.G. Extractive Metallurgy of Copper. Elsevier, Fifth Edition, 2011.
Moskalyk R.R., Alfantaz A.M. Review of copper pyrometallurgical practice: today and tomorrow // Minerals Engineering. 2003. № 16. P. 893–919.
Wang J.P., Erdenebold U. A Study on reduction of copper smelting slag by carbon for recycling into metal values and cement raw material // Sustainability. 2020. № 12. P. 1421–1430.
Prince S., Young J., Ma G., Young C. Characterization and recovery of valuables from waste copper smelting slag // In book: Advances in Molten Slags, Fluxes, and Salts: Proceedings of the 10th International Conference on Molten Slags, Fluxes and Salts, 2016.
Reddy R.G., Prabhu V.L., Mantha D. Zinc Fuming from lead blast furnace slag // High Temperature Materials and Processes. 2002. 21. № 6. P. 377–386.
Козырев В.В. Отгонка цинка из шлака при фьюминговании природным газом // Цветные металлы. 2009. № 2. С. 61–64.
Колобов Г.А., Грищенко С.Г., Пожуев В.И. Цветная металлургия. Физико-химические и технологические основы. Запорожье: Запорожская гос. инженерная академия, 2010.
Ватолин Н.А., Моисеев Г.К., Трусов Б.Г. Термодинамическое моделирование в высокотемпературных неорганических системах. М.: Металлургия. 1994.
Моисеев Г.К., Вяткин. Г.П. Термодинамическое моделирование в неорганических системах. Челябинск: ЮУрГУ. 1999.
Михайлов Г.Г., Леонович Б.И., Кузнецов Ю.С. Термодинамика металлургических процессов и систем. М.: МИСиС. 2009.
Boronenkov V., Zinigrad M., Leontiev L., Pastukhov E., Shalimov M., Shanchurov S. Phase interaction in the metal-oxide melts-gas system. The Modeling of Structure, Properties and Processes: Heidelberg, Springer-Verlag, Berlin, 2012.
Pickles C.A., Harris C.T., Peacey J., Forster J. Thermodynamic analysis of the Fe–Ni–Co–Mg–Si–O–H–S–C–Cl system for selective sulphidation of a nickeliferous limonitic laterite ore / Miner. Eng. // International J. Devoted to Innovation and Developments in Mineral Processing and Extractive Metallurgy. 2013. 54. P. 52–62.
Sohn H.Y. Process modeling in non-ferrous metallurgy // Treatise on Process Metallurgy: Industrial Processes, Oxford: Elsevier Ltd. 2014. Ch. 2.4. P. 701–838.
Комков A.A., Ладыго Е.А., Быстров В.П. Термодинамический анализ процесса восстановительного обеднения шлаков, богатых по меди и никелю // Изв. ВУЗов. Цветная металлургия. 2002. № 4. С. 7–14.
Кожахметов С.М., Квятковский С.А., Соколовская Л.В., Билялова С.М. Структура и фазовые превращения металлизированных продуктов процессов восстановления шлаков // Комплексное использование минерального сырья. 2008. № 1. С. 74–80.
Досмухамедов Н.К., Жолдасбай Е.Е., Нурлан Г.Б., Сейткулова Ж.Б. Исследование поведения цветных металлов, железа и мышьяка при восстановительном обеднении богатых по меди шлаков // Международный журн. прикладных и фундаментальных исследований. 2016. № 1. С. 486–491.
Вусихис А.С., Леонтьев Л.И., Селиванов Е.Н., Ченцов В.П. Моделирование процесса газового восстановления металлов из многокомпонентного оксидного расплава в барботируемом слое // Бутлеровские сообщения. 2018. 55. № 7. С. 58–63.
Dmitriev A.N., Vusikhis A.S., Sitnikov V.A., Leontiev L.I., Kudinov D.Z. Thermodynamic modeling of iron oxide reduction by hydrogen from the B2O3–CaO–FeO melt in bubbled layer // Israel J. Chemistry. 2007. 47. № 3–4. P. 299–302.
Вусихис А.С., Леонтьев Л.И., Кудинов Д.З., Селиванов Е.Н. Термодинамическое моделирование восстановления никеля и железа из многокомпонентного силикатного расплава в процессе барботажа. Сообщение 1. Восстановитель – смесь СО–СО2 // Известия ВУЗов. Черная металлургия. 2018. 61. № 9. С. 731–736.
Вусихис А.С., Леонтьев Л.И., Кудинов Д.З., Селиванов Е.Н. Термодинамическое моделирование восстановления никеля и железа из многокомпонентного силикатного расплава в процессе барботажа. Сообщение 2. Восстановитель – смесь Н2–Н2О // Известия ВУЗов. Черная Металлургия. 2018. 61. № 10. С. 794–800.
Selivanov E., Gulyaeva R., Istomin S., Tyushnyakov S., Bykov A., Belyaev V. Viscosity and thermal properties of slag in the process of autogenous smelting of copper-zinc concentrates // Transactions of the Institutions of Mining and Metallurgy, Section C: Mineral Processing and ExtrActive Metallurgy. 2015. 124. № 2. P. 88–95.
Банных О.А., Будберг П.Б., Алисова С. П. и др. Диаграммы состояния двойных и многокомпонентных систем на основе железа. М.: Металлургия, 1986.
Серегин П.С., Попов В.А., Цемехман Л.Щ. Новые методы переработки материалов, содержащих цинк олово и свинец // Цветные металлы. 2010. № 10. С. 27–33.
Комков А.А., Камкин Р.И. Поведение меди и примесей при продувке медеплавильных шлаков газовой смесью СО–СО2 // Цветные металлы. 2011. № 6. С. 26–31.
Козырев В.В., Бессер А.Д., Парецкий В.Н. К вопросу извлечения цинка из шлаков свинцовоq плавки // Электрометаллургия. 2013. № 6. С. 31–35.
Комков А.А., Камкин Р.И. Математическая модель поведения примесей в условиях восстановительной барботажной обработки медеплавильных шлаков // Изв. ВУЗов Цветная металлургия. 2010. № 1. С. 24–30.
Cockcroft S.L., Richard G.G., Brimacombe J.K. Mathematical model of lead behavior in zinc slag furning process // The Canadian J. Metallurgy and Materials Science 1988. 27. P. 27–40.
Дополнительные материалы отсутствуют.