Теплофизика высоких температур, 2022, T. 60, № 3, стр. 428-433
Исследование воздействия высокоэнтальпийного воздушного потока на эффективность защитного действия антиокислительного покрытия для углеродсодержащих композиционных материалов
С. А. Евдокимов 1, *, Г. В. Ермакова 1, А. Н. Гордеев 2, А. Ф. Колесников 2
1 ФГУП “Всероссийский институт авиационных материалов” ГНЦ РФ
Москва, Россия
2 ФГБУН Институт проблем механики им. А.Ю. Ишлинского РАН
Москва, Россия
* E-mail: sergei_evd@mail.ru
Поступила в редакцию 17.03.2021
После доработки 22.10.2021
Принята к публикации 23.11.2021
- EDN: WXMEVK
- DOI: 10.31857/S0040364422030073
Аннотация
С применением метода высокотемпературного химического синтеза изготовлены образцы материала с высокотемпературной системой защиты. Исследование термохимического воздействия высокоэнтальпийных воздушных потоков на углеродсодержащий композиционный материал с высокотемпературным антиокислительным покрытием на основе соединений гафния при температурах поверхности 1400–1600°С выполнено в свободной дозвуковой струе высокоэнтальпийного воздуха 100-киловаттного высокочастотного индукционного плазмотрона ВГУ-4. Эксперименты проведены при давлении 100 гПа в режиме ступенчатого нагрева и в режиме постоянной температуры поверхности 1400, 1500 и 1600°С. Продолжительность каждого цикла испытаний в режиме постоянной температуры составляла 1500 c.
ВВЕДЕНИЕ
На сегодняшний день развитие авиационной, ракетной и космической техники связано с созданием на основе жаропрочных сплавов изделий нового поколения, при изготовлении которых доля композиционных материалов значительно превышает долю традиционных материалов [1–3]. Для уменьшения аэродинамического сопротивления, увеличения подъемной силы и маневренности высокоскоростные летательные аппараты должны иметь профили с острыми передними кромками. При этом поверхность может подвергаться воздействию мощных тепловых потоков и предельно высоких механических нагрузок, что приводит к росту температуры поверхности вплоть до 2200–2600°C [4, 5]. Применение керамоматричных, углерод-углеродных и углеродкерамических композиционных материалов позволит качественно повысить рабочие характеристики изделий. Данный тип материалов обладает рядом уникальных свойств, таких как механическая прочность при высоких температурах, низкий коэффициент термического расширения, высокая термостабильность и теплопроводность, высокое сопротивление ползучести и стойкость к термическому удару. В свою очередь низкая окислительная стойкость выше 400°С представляет серьезную проблему при изготовлении деталей газотурбинных двигателей, передних кромок спускаемых аппаратов и сопел ракет. Для решения данной задачи целесообразно применение многослойной системы защиты, включающей в себя защитное антиокислительное покрытие и промежуточный слой, необходимый для согласования коэффициента термического расширения и снижения уровня взаимодействия покрытия с материалом подложки. В качестве основных компонентов антиокислительного покрытия следует выделить тугоплавкие соединения гафния, которые под действием высоких температур образуют соединения, позволяющие значительно снизить диффузионную способность кислорода воздуха, обеспечив при этом необходимый уровень свойств [6–11].
Основными методами нанесения антиокислительных покрытий на углеродсодержащие композиционные материалы являются:
– химическое осаждение из паровой фазы (метод CVD), в частности, с использованием металлорганических соединений (MOCVD);
– реакционное химическое осаждение из паровой фазы (метод RCVD);
– химическая пропитка в газовой фазе (CVI);
– плазменное напыление;
– пульверизация растворов;
– электролитическое и электрофорезное нанесение растворов.
Эффективное применение данных методов возможно при использовании направленного выбора и синтеза компонентов, к которым предъявляется ряд требований. При получении покрытий методом CVI возникают трудности, связанные в первую очередь с необходимостью обеспечить объемную однородность распределения дисперсного компонента. Для CVD-процесса выбираются соединения, обладающие летучестью в заданном интервале температур, в соответствии со степенью заполнения сферы центрального атома и в зависимости от типов и количества групп в молекуле, определяющих энтальпию парообразования вещества. Метод CVD позволяет получать, кроме оксидов, непосредственно бинарные соединения, при этом покрытия отличаются высокой химической чистотой. Основным недостатком рассмотренных методов является высокая трудоемкость и ресурсозатратность. Применение метода пульверизации раствора покрытия на поверхность углеродсодержащего композиционного материала с последующим высокотемпературным химическим синтезом позволило получить образцы комплексной системы защиты с равномерно нанесенным внешним слоем без видимых дефектов.
Работа выполнена в рамках реализации комплексных научных направлений 2.1 “Фундаментально-ориентированные исследования” и 14.1. “Конструкционные керамические композиционные материалы” (“Стратегические направления развития материалов и технологий их переработки на период до 2030 года”) [12].
МАТЕРИАЛЫ И МЕТОДИКА ЭКСПЕРИМЕНТА
Для изготовления образцов антиокислительного покрытия использовались следующие компоненты: оксид гафния марки ГФО-1, средний размер частиц – 11 мкм; борид гафния “Ч”, средний размер частиц – менее 40 мкм и основа стеклофазы для проведения процесса высокотемпературного химического синтеза. Нанесение покрытия проводилось методом пульверизации водного раствора шликера покрытия с последующей термообработкой в электропечи в атмосфере воздуха.
Съемка образцов проведена на дифрактометре D/MAX–2500, “RIGAKU” с монохроматическим CuKα-излучением. Диапазон сканирования в интервале углов 2θ 10°–90°. Рабочий режим дифрактометра: напряжение – 30 кВ, ток – 100 мА, время экспозиции – 1.5 с. Дифрактограммы расшифрованы с помощью специализированной программы Jade5 и базы данных PDF2.
Исследование термохимического воздействия высокоэнтальпийных воздушных потоков на углерод-углеродный композиционный материал (УКМ) с высокотемпературным антиокислительным покрытием на основе соединений гафния и бора при температурах поверхности 1400–1600°С выполнено в свободной дозвуковой струе высокоэнтальпийного воздуха 100-киловаттного высокочастотного индукционного плазмотрона ВГУ-4 (мощность анодного питания плазмотрона – 12–82 кВт, давление – 6–1000 гПа) [13–15]. Температура поверхности образца измерялась пирометром Mikron M_770S в режиме пирометра спектрального отношения (температурный интервал – 1000–3000°C, диаметр области измерения ~5 мм), для регистрации распределения температуры по лицевой поверхности образца использовался термовизор “Тандем VS_415U”.
В процессе испытания и после него определяются зависимость от времени температуры поверхности в окрестности критической точки, унос массы образцов, наличие или отсутствие на лицевой и тыльной стороне образцов очагов разрушения, трещин и оплавленных участков, а также изменений цвета и фактуры поверхности.
Термохимическая стойкость испытываемых образцов тепловой защиты определяется по наличию/отсутствию на поверхности образца после испытаний локальных очагов разрушения, проявляющихся в процессе испытаний в виде зон локального перегрева (пятен размерами 0.5–5 мм) с температурой, превышающей температуру остальной поверхности на 50–100°С и более.
Важным критерием стойкости к окислению в потоке диссоциированного воздуха также является ресурс покрытия при заданной температуре и давлении, т.е. время выдержки в струе диссоциированного воздуха до начала разрушения образца. Ресурс покрытия обычно определяется в циклических испытаниях, и только при температурах, близких к температуре начала разрушения, ресурс может определяться в одном эксперименте.
РЕЗУЛЬТАТЫ И ОБСУЖДЕНИЕ
Объектами испытаний являлись образцы из материала УКМ с высокотемпературным антиокислительным покрытием. Использовались образцы двух типов. Образцы первого типа представляют собой диски с конической боковой поверхностью. Диаметр лицевой поверхности – 26.5 мм, толщина – 5 мм, полуугол раствора конуса боковой поверхности – 30°. Эти образцы устанавливаются в так называемую евромодель (ESA standard model), имеющую форму цилиндра с плоским торцом диаметром 50 мм и радиусом скругления кромки торца 11.5 мм. Схематический чертеж евромодели с установленным в ней образцом показан на рис. 1.
Рис. 1.
Схематический чертеж евромодели с установленным в ней образцом: 1 – образец, 2 – прокладка, 3 – оснастка, 4 – теплоизолятор, 5 – калориметр, 6 – штифт, 7 – водоохлаждаемая державка.
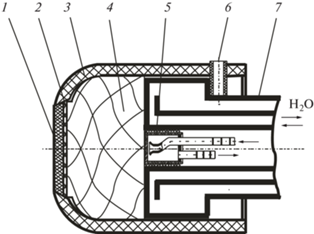
Важнейшим преимуществом евромодели является высокая однородность поля температур на лицевой поверхности образца, что позволяет проводить определение каталитичности и измерение интегральной и спектральной степеней черноты поверхности образца [16–19]. Однако при использовании евромодели для исследований при максимально возможных температурах термостойкость модели должна быть почти такой же высокой, как и у исследуемого образца, что делает изготовление модели еще более сложным, чем образца.
Второй тип образцов представляет собой диски диаметром 31.5 мм и толщиной 5 мм, устанавливаемые в водоохлаждаемую медную модель, схематический чертеж которой показан на рис. 2.
Испытания проводились в свободной дозвуковой струе воздушной плазмы плазмотрона ВГУ-4 при давлении 100 гПа и постоянном расходе воздуха 2.4 г/с, расстояние от выходного сечения разрядного канала до торца модели составляло 60 мм.
Испытания проводились в двух режимах.
Первый режим – это режим ступенчатого нагрева, который используется для экспресс-оценки свойств антиокислительного покрытия и представляет собой испытание при повышающихся мощностях анодного питания ВЧ-генератора: 27, 30, 32, 35, 37, 40, 42 кВт.
Измерение температуры поверхности Tw в критической точке модели, т.е. в центре лицевой поверхности образца, осуществлялось пирометром “Mikron M-770S”, работающим в режиме пирометра спектрального отношения, который определяет цветовую температуру образца. Точность измерений пирометра составляет ±15°С. Регистрация полей температуры на лицевой поверхности образца осуществляется с помощью термовизора “Тандем VS-415U”, прокалиброванного по модели абсолютно черного тела в диапазоне температур 700–2300°С. В настоящей работе используется калибровка для стандартной пирометрической длины волны 0.65 мкм, инструментальная погрешность измерений не превышает ±10°С. Результаты испытаний образцов УКМ с антиокислительным покрытием в режиме ступенчатого нагрева представлены в табл. 1.
Таблица 1.
Результаты испытаний образцов УКМ с антиокислительным покрытием в режиме ступенчатого нагрева
№ образца | t, c | N, кВт | Tw, °С | M0, г | ΔM, г | ΔM/М0, % |
---|---|---|---|---|---|---|
1 | 720 | 27.5 30.0 32.5 35.0 |
1475 1458 1560 1611 |
5.6981 | 0.0795 | 1.40 |
2 | 1260 | 27.5 30.0 32.5 35.0 37.5 40.0 42.5 |
1320 1260 1320 1400 1480 1550 1600 |
7.2925 | 0.0015 | 0.02 |
В ходе испытаний отработан режим нагрева образцов и получена зависимость температуры поверхности образца от мощности анодного питания ВЧ-генератора индукционного плазмотрона. Зависимости от времени основных рабочих параметров плазмотрона – мощности ВЧ-генератора по анодному питанию и давления в барокамере, а также средней температуры в окрестности критической точки, максимальной температуры по поверхности образца и цветовой температуры в критической точке исследуемого образца № 1 ‒ представлены на рис. 3. Небольшая разность между максимальной и средней температурой свидетельствует о хорошей однородности распределения температуры и об отсутствии на поверхности зон локального перегрева, что также подтверждают термоизображения (рис. 4) образца.
Рис. 3.
Зависимости от времени рабочих параметров плазмотрона: 1 – температура стенки, 2 – максимальная температура, 3 – температура , 4 – мощность, 5 – давление.
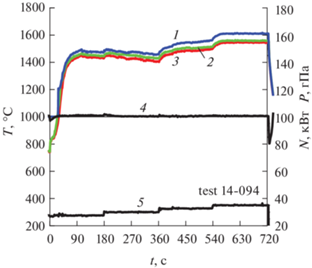
Увеличение температуры на 100-й с нагрева (рис. 4а) связано с протекающими процессами окисления поверхности покрытия с интенсивным образованием стеклофазы, которые в дальнейшем затрудняются и которые связаны с диффузией газов окислителей в объем покрытия через образующийся оксидный слой. Видно, что ступенчатое увеличение мощности анодного питания плазмотрона 30 → 32 → 35 кВт (рис. 4; временной интервал ≤3 мин) приводит также к ступенчатому росту температуры на 50–100°C.
Фотографии лицевой стороны образца № 1 до и после испытания представлены на рис. 5, из которого видно, что лицевая поверхность образца до испытаний была однотонной темно-серой, а после испытания стала более светлой. Это связано с изменением химического состава (образованием защитного стеклообразного слоя) поверхности, приводящим к падению интегральной степени черноты и росту каталитичности поверхности. При этом изменение масс образцов №№ 1, 2 относительно исходного состояния составило 1.4 и 0.02% соответственно. Следует отметить, что значительное изменение массы образца № 1 относительно образца № 2 связано с увеличением скорости нагрева. В результате чего интенсивность процесса окисления исходных компонентов с образованием стеклофазы возрастает.
Второй режим заключается в циклических испытаниях при постоянной температуре поверхности 1600°С, которым подвергались два образца в виде дисков. Каждый из образцов прошел по четыре цикла испытаний продолжительностью 1500 с каждый. Таким образом, суммарное время воздействия высокоэнтальпийного потока воздуха составило по 100 мин для каждого образца. Результаты испытаний приведены в табл. 2.
Таблица 2.
Основные результаты циклических испытаний образцов из УКМ с покрытием при температуре поверхности 1600°С
№ образца | № цикла | N, кВт | Tw, °С | t, c | M0, г | ΔM, г | ΔM/М0, % |
---|---|---|---|---|---|---|---|
3 | 1 | 42 | 1600 | 1500 | 7.2494 | 0.0035 | 0.48 |
2 | 38 | 1600 | 1500 | 7.2459 | 0.0034 | 0.05 | |
3 | 34 | 1600 | 1500 | 7.2425 | 0.0077 | 0.11 | |
4 | 34 | 1600 | 1500 | 7.2349 | 0.0132 | 0.18 | |
4 | 1 | 50 | 1600 | 1500 | 7.7164 | 0.0055 | 0.07 |
2 | 42 | 1600 | 1500 | 7.7109 | 0.0001 | 0.00 | |
3 | 39 | 1600 | 1500 | 7.7108 | 0.0030 | 0.04 | |
4 | 36 | 1600 | 1500 | 7.7078 | 0.0030 | 0.04 |
В ходе циклических испытаний выявлена разность между максимальной и средней температурой, которая свидетельствует о росте температуры в зонах локального перегрева. Уменьшение яркостной температуры в критической точке при постоянной цветовой температуре указывает на уменьшение спектральной излучательной способности покрытия в результате воздействия на него высокоэнтальпийным воздухом. Суммарное изменение массы образцов УКМ с антиокислительным покрытием при постоянной температуре поверхности 1600°С в течение 100 мин не превысило 1.00%.
В результате проведенного рентгеноструктурного анализа установлено, что в исходном состоянии основной фазой высокотемпературного антиокислительного покрытия является HfSiO4 с тетрагональной решеткой, второй фазой (менее интенсивной) ‒ моноклинный оксид HfO2. Дифрактограмма образца высокотемпературного антиокислительного покрытия в исходном состоянии представлена на рис. 6.
Рис. 6.
Дифрактограмма образца высокотемпературного антиокислительного покрытия в исходном состоянии.
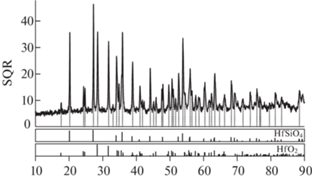
На рис. 7 приведена дифрактограмма образца высокотемпературного антиокислительного покрытия после испытаний при температуре 1600°С. В образцах после испытаний при 1600°С качественный фазовый состав остается стабильным, т.е. в покрытиях также присутствуют HfSiO4 и HfO2.
Рис. 7.
Дифрактограмма образца высокотемпературного антиокислительного покрытия после испытаний при температуре 1600°С.
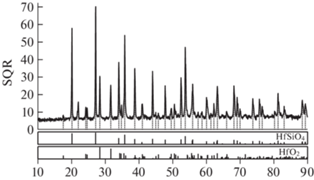
Однако при этом соотношение интенсивностей фаз в образцах после испытаний изменилось, интенсивность рентгеновских линий фазы HfSiO4 выросла, а фазы HfO2 уменьшилась, следовательно, изменилось количественное соотношение фаз, что является следствием химического взаимодействия исходных компонентов покрытия при воздействии высоких температур с образованием тугоплавких соединений, обеспечивающих защитное действие покрытия.
ЗАКЛЮЧЕНИЕ
Применение метода пульверизации водного раствора шликера покрытия с последующим высокотемпературным химическим синтезом позволяет получать образцы УКМ с антиокислительным покрытием с высокой устойчивостью к длительному воздействию дозвукового высокоэнтальпийного потока воздуха с постоянной температурой поверхности 1600°С. Защитное действие антиокислительного покрытия обусловлено образованием тугоплавких соединений, обеспечивающих снижение диффузии кислорода в объем материала. Рассмотренное покрытие может быть применено при изготовлении деталей газотурбинных двигателей, передних кромок спускаемых аппаратов и сопел ракет.
Список литературы
Каблов Е.Н., Оспенникова О.Г., Светлов И.Л. Высокоэффективное охлаждение лопаток горячего тракта ГТД // Авиационные материалы и технологии. 2017. № 2. С. 3.
Каблов Е.Н., Бондаренко Ю.А., Ечин А.Б. Развитие технологии направленной кристаллизации литейных высокожаропрочных сплавов с переменным управляемым температурным градиентом // Авиационные материалы и технологии. 2017. № S. С. 24.
Мубояджян С.А., Будиновский С.А. Ионно-плазменная технология: перспективные процессы, покрытия, оборудование // Авиационные материалы и технологии. 2017. № S. С. 39.
Севастьянов В.Г., Симоненко Е.П., Гордеев А.Н., Симоненко Н.П., Колесников А.Ф., Папынов Е.К., Шичалин О.О., Авраменко В.А., Кузнецов Н.Т. Получение сверхвысокотемпературных композиционных материалов HfB2–SiС и исследование их поведения под воздействием потока диссоциированного воздуха // Журн. неорг. химии. 2013. Т. 58. № 11. С. 1419.
Гращенков Д.В., Исаева Н.В., Солнцев С.С., Евдокимов С.А. Высокотемпературные антиокислительные покрытия для углеродкерамических композиционных материалов // Вопросы материаловедения. 2013. № 3(75). С. 76.
Солнцев С.С., Шалин Р.Е., Исаева Н.В. Реакционноспекаемые керамические покрытия // Сб. тр. 8-й Всемирн. конф. по керамике и новым материалам. 1995. Т. 9. С. 237.
Солнцев С.С., Исаева Н.В., Швагирева В.В., Максимов В.И. Высокотемпературные покрытия для защиты сплавов и углеродкерамических композиционных материалов от окисления // Конверсия в машиностроении. 2004. № 4. С. 77.
Yao X.Y., Li H.J., Zhang Y.L., Wu H., Qiang X.F. A SiC‒Si‒ZrB2 Multiphase Oxidation Protective Ceramic Coating for SiC-coated Carbon/Carbon Composites // Ceram. Int. 2012. V. 38. P. 2095.
Yang X., Huang Q.Z., Su Z.A., Chang X., Chai L.Y., Liu C.X., Xue L., Huang D. Resistance to Oxidation and Ablation of SiC Coating on Graphite Prepared by Chemical Vapor Reaction // Corros. Sci. 2013. V. 75. P. 16.
Saravanan S., Hari Srinivas G., Jayaram V., Paulraj M., Asokan S. Synthesis and Characterization of Y3Al5O12 and ZrO2–Y2O3 Thermal Barrier Coatings by Combustion Spray Pyrolysis // Surface Coat. Technol. 2008. V. 202. № 19. P. 4653.
Weyant C.M., Faber K.T. Processing–microstructure Relationships for Plasma-sprayed Yttrium Aluminum Garnet // Surface Coat. Technol. 2008. V. 202. № 24. P. 6081.
Каблов Е.Н. Инновационные разработки ФГУП “ВИАМ” ГНЦ РФ по реализации “Стратегических направлений развития материалов и технологий их переработки на период до 2030 года” // Авиационные материалы и технологии. 2015. № 1(34). С. 3.
Гордеев А.Н., Колесников А.Ф. Высокочастотные индукционные плазмотроны серии ВГУ. В cб.: Актуальные проблемы механики: Физико-химическая механика жидкостей и газов. М.: Наука, 2010. С. 151.
Терентьева В.С., Астапов А.Н., Еремина А.И. Анализ перспективных антиокислительных покрытий на жаропрочные углеродсодержащие композиционные материалы (обзор) // Коррозия: материалы, защита. 2014. № 1. С. 30.
Дорошенко В.М., Мысова В.М., Рулев Ю.К., Якушин М.И. Измерение энтальпии в дозвуковых высокотемпературных струях азота и воздуха на индукционном плазмотроне // ИФЖ. 1987. Т. 53. № 3. С. 492.
Гордеев А.Н., Колесников А.Ф., Якушин М.И. Исследование теплообмена на моделях в дозвуковых струях индукционного плазмотрона // Изв. АН СССР. МЖГ. 1983. № 6. С. 129.
Gordeev A.N., Kolesnikov A.F., Yakushin M.I. An Induction Plasma Application to “Buran’s” Heat Protection Tiles Ground Tests // SAMPE J. 1992. V. 28. № 3. P. 29.
Gordeev A.N., Yakushin M.I. The Thermochemical Stability of Carbon-Carbon Using an Antioxidation Coating for Buran, Part II // SAMPE J. 1993. V. 29. № 2. P. 27.
Жестков Б.Е., Терентьева В.С. Исследование многофункционального покрытия МАИ Д5, предназначенного для защиты особожаропрочных материалов // Металлы. 2010. № 1. С. 39.
Дополнительные материалы отсутствуют.
Инструменты
Теплофизика высоких температур