Теоретические основы химической технологии, 2022, T. 56, № 1, стр. 11-25
О влиянии гидродинамических условий на микросмешение в микрореакторах со сталкивающимися струями
Р. Ш. Абиев a, b, *, А. А. Сироткин a
a Санкт-Петербургский государственный технологический институт (технический университет)
Санкт Петербург, Россия
b Институт химии силикатов им. И.В. Гребенщикова РАН
Санкт Петербург, Россия
* E-mail: abiev.rufat@gmail.com
Поступила в редакцию 14.09.2021
После доработки 19.09.2021
Принята к публикации 23.09.2021
- EDN: ADHZCZ
- DOI: 10.31857/S0040357122010018
Аннотация
Выполнено экспериментальное исследование микросмешения (при помощи йодид-иодатной методики) в микрореакторе со свободно сталкивающимися струями (МРСС) с дифференцированным отбором проб, а также в лабораторном реакторе с магнитной мешалкой. В последнем случае качество микросмешения оказалось крайне низким (индекс сегрегации Xs = 0.52 ± 0.03). В МРСС проведены исследования микросмешения при различных диаметрах струй (dj = 0.55, 1.0 и 2.0 мм) и расстояниях от среза сопла до точки столкновения (L = 5, 20, 40 мм), для различных расходов жидкости. Диаметр струй и расстояние от среза сопла до точки столкновения оказывают существенное влияние на качество микросмешения. При относительно низких числах Вебера (We < 2000) и при L/dj ≈ 73 возникает так называемая “варикозная” неустойчивость струй, в результате чего происходит их распад на капли до момента столкновения. При We > 2000 за счет увеличения кинетической энергии струя стабилизируется, и при We = 6000 значение Xs для L = 40 мм становится таким же, как и для L = 5 мм. Для водных растворов оптимальным является диаметр 1 мм, поскольку он позволяет обеспечить относительно высокую производительность при высоком качестве микросмешения, при этом разлет капель и филаментов на периферию минимален (или почти отсутствует).
ВВЕДЕНИЕ
Микрореакторы в целом, и микрореакторы со сталкивающимися струями, в частности, стали предметом пристального внимания в последние десятилетия, поскольку они способны обеспечить интенсификацию различных гидродинамических, тепло- и массообменных процессов [1, 2]. Микрореакторы активно исследуются, в частности, как устройства для синтеза микронных, субмикронных и наноразмерных частиц в однофазных [3–5] и в двухфазных потоках [6, 7].
Известны микрореакторы с затопленными и со свободными сталкивающимися струями [8]. Нами разработан микрореактор со сталкивающимися струями, в котором возможно смешение двух и более растворов: при столкновении двух струй под углом формируется жидкостная пелена, имеющая форму, схожую с эллипсом в первом приближении. Еще две или более струй могут быть направлены непосредственно в сформированную пелену [9], например, для ввода допирующих элементов или иных целей.
В одной из недавних работ предложено смешение трех потоков, сталкивающихся под углом 120° в горизонтальной плоскости [10]. Здесь, по существу, реализован принцип, похожий на предложенный нами; отличие в том, что импульс третьей струи компенсирует проекции импульсов двух других струй.
Для микрореакторов, предназначенных для синтеза наноразмерных частиц, принципиальным является обеспечение высокого качества микросмешения [11–17]. В последние 3–4 г. в результате возросшего интереса к МРСС опубликовано несколько работ, в которых представлен синтез наноразмерных частиц сложных оксидов и других неорганических веществ [18–25].
В работе [26] исследованы четыре варианта синтеза нанокристаллического BiFeO3 методом соосаждения нитратов железа и висмута раствором NaOH, с последующей термообработкой аморфных продуктов: 1) в микрореакторе с двумя затопленными струями (МРЗС), подаваемыми под слой раствора NaOH; 2) в микрореакторе со свободно сталкивающимися струями (МРСС); 3) в микрореакторе со струей раствора нитратов, подаваемой на поверхность раствора NaOH под углом 30° к горизонту (МРПС); 4) с использованием ультразвукового диспергатора И100-6/1 (частота колебаний 23 кГц) при обратном соосаждении (УЗВ).
У образцов МРПС и УЗВ по данным рентгеновской дифрактометрии выявлена заметная доля аморфной фазы и следовые количества примесей кристаллических фаз (Bi2Fe4O9 и Bi25FeO39). Сделан вывод о том, что для быстрой дегидратации смеси гидроксидов и их последующей трансформации в кристаллический ортоферрит висмута целесообразно использовать методы свободно сталкивающихся струй или затопленных струй, которые обеспечивают высокое качество микросмешения, необходимое для получения наноразмерных частиц.
В работах [27–29] исследован синтез в МРСС феррита гадолиния GdFeO3, который представляет интерес как основа материалов для газовых сенсоров, устройств хранения данных, а также в качестве контрастного агента для магнитно-резонансной томографии. Полученные наночастицы ортоферрита гадолиния имеют изометрическую морфологию и средний размер кристаллитов 27 ± ± 3 нм с узким распределением по размерам. В работе [29] проанализировано влияние нескольких факторов на размер образующихся наночастиц ортоферрита гадолиния: температура растворов, концентрация нитратов в растворе, расход жидкостей, угол между струями. Оптимальными (для синтеза частиц с минимальным размером) оказались параметры: температура 0°С, концентрации 0.001 М–0.01 М, расход 200 мл/мин, угол между струями 2θ = 90°. Определены мессбауэровские спектры полученных образцов, ширина запрещенной зоны [29].
В публикации [28] проведено сравнение методов прямого и обратного осаждения с методом МРСС, с использованием масштабного исследования полученных продуктов. Показано, что порошки GdFeO3, полученные в микрореакторе со сталкивающимися струями, обладают наименьшими показателями коэрцитивной силы и остаточной намагниченности, а также наименьшей склонностью к образованию агрегатов (6 частиц на агрегат, тогда как для обратного и прямого осаждения это значение составляет 31 и 160 соответственно). Характерный размер агрегатов для метода МРСС составил 78.5 нм, что примерно в 2 и в 2.5 раза меньше, чем для частиц, полученных обратным и прямым осаждением. Удельная поверхность частиц (по БЭТ) и общий объем пор, полученных методом МРСС, оказались примерно в 2 и в 2.5 раза больше, чем для частиц, полученных обратным и прямым осаждением.
В экспериментальной части приведено описание установки, использованной в данном исследовании.
Иодид-йодатная методика определения качества микросмешения. Выбор оптимальных концентраций. Йодид-иодатная методика, предложенная в 1990-х [30], подробней описана в работах [31–35] и основана на параллельных конкурирующих реакциях Виллермо–Душмана – реакции нейтрализации (R1) и окислительно-восстановительной (R2):
(R1)
${{{\text{H}}}_{{\text{2}}}}{\text{BO}}_{3}^{ - } + {{{\text{H}}}^{ + }} \rightleftarrows {{{\text{H}}}_{{\text{3}}}}{\text{B}}{{{\text{O}}}_{3}},$(R2)
${\text{IO}}_{3}^{ - } + 5{{{\text{I}}}^{ - }} + 6{{{\text{H}}}^{ + }} \rightleftarrows 3{{{\text{I}}}_{2}} + 3{{{\text{H}}}_{{\text{2}}}}{\text{O}}.$Метод основан на измерении чувствительного к перемешиванию выхода йода, который зависит от конкуренции между нейтрализацией кислоты, и ее ролью в освобождении йода в реакции Душмана.
Реакция (R2) быстрая, имеет тот же порядок времени, что и микросмешение, но гораздо медленней реакции (R1).
Йодид-иодатная методика заключается в следующем [32, 34]:
Предварительно готовится смесь растворов йодида I– и иодата ${\text{IO}}_{3}^{ - }$ в буферном растворе ${{{{{\text{H}}}_{{\text{2}}}}{\text{BO}}_{3}^{ - }} \mathord{\left/ {\vphantom {{{{{\text{H}}}_{{\text{2}}}}{\text{BO}}_{3}^{ - }} {{{{\text{H}}}_{{\text{3}}}}{\text{B}}{{{\text{O}}}_{{\text{3}}}}}}} \right. \kern-0em} {{{{\text{H}}}_{{\text{3}}}}{\text{B}}{{{\text{O}}}_{{\text{3}}}}}},$ а также раствор серной кислоты, который является поставщиком протонов H+ в реакции (R1) и (R2). Концентрация кислоты должна быть фиксированной, чтобы обеспечить стехиометрический недостаток протонов по отношению к ионам бората.
В случае идеального перемешивания, кислота расходуется только первой реакцией (R1), которая протекает существенно быстрее окислительно-восстановительной реакцией (R2). Вторая реакция при этом не может протекать в силу стехиометрического недостатка серной кислоты.
В случае плохого перемешивания время распределения серной кислоты может оказаться больше характерного времени окислительно-восстановительной реакции. В результате возникает локальное пересыщение некоторых объемов реактора серной кислотой, которая, после участия в реакции (R1) с ионами бората, способна реагировать с ионами йодида и иодата, с образованием йода I2.
Таким образом, образование йода является мерой сегрегации жидкости. В этой системе йод может далее реагировать с иодидом, формируя ионы трийодида I3–:
Данные о скоростях реакций и другие подробности экспериментальной процедуры приведены в [32, 34, 35].
Концентрация трийодида может быть легко измерена при помощи UV/vis-спектрофотометрии на длине волны 353 нм и определена по закону Бугера–Ламберта–Бера:
(1)
$\left[ {{\text{I}}_{3}^{ - }} \right] = \frac{{OD}}{{{{\varepsilon }_{{353}}}{{L}_{{{\text{opt}}}}}}},$Одним из ограничений, связанных со спектрофотометрическими измерениями, является применимость (линейность) закона Бугера–Ламберта–Бера, который связывает измеренную оптическую плотность с концентрацией трииодида (см. уравнение (1)). Измеряемая оптическая плотность должна находиться в допускаемом интервале значений (для спектрофотометра СФ-2000 OD = = 0.3–3.15) для заданного диапазона режимов работы лабораторной установки.
Наиболее подходящий набор концентраций для использования зависит не только от ранее оцененного времени смешивания, но и от максимальной величины оптической плотности, полученной при минимальных режимах работы установки. В табл. 1 представлены шесть различных возможных наборов концентраций, которые должны использоваться для наиболее распространенных микросмесителей, работающих при эквимолярном расходе реагентов (растворов кислоты и бората, йодата калия, йодида калия), и не должны использоваться для других значений отношения потоков. Экспериментальным способом было определено, что для исследованного микрореактора со свободно сталкивающимися струями подходит набор концентраций № 2 из табл. 1.
Таблица 1.
Рекомендованные комбинации концентраций реагентов для экспериментального определения качества микросмешения в микрореакторах [34]
Номер комбинации концентраций реагентов | ||||||
---|---|---|---|---|---|---|
Концентрация, моль/л | 1 | 1b | 1c | 2 | 2b | 2c |
[H–] | 0.03 | 0.06 | 0.04 | 0.015 | 0.03 | 0.02 |
[KI] | 0.032 | 0.032 | 0.032 | 0.016 | 0.016 | 0.016 |
[KIO3] | 0.006 | 0.006 | 0.006 | 0.003 | 0.003 | 0.003 |
[NaOH] | 0.09 | 0.09 | 0.09 | 0.045 | 0.045 | 0.045 |
[H3BO3] | 0.09 | 0.09 | 0.09 | 0.045 | 0.045 | 0.045 |
В качестве показателя качества микроперемешивания используется индекс сегрегации XS [34], значения которого могут варьироваться от XS = 0 (идеальное микросмешение) до XS = 1 (полная сегрегация). В общем случае индекс сегрегации рассчитывают по формуле
где Y – селективность по определяемому веществу (в данному случае – йоду), индекс “ST” соответствует полной сегрегации.Для йодид-иодатной методики значения селективности определяют по следующим формулам:
(3)
$Y = \frac{{2({{n}_{{{{{\text{I}}}_{2}}}}} + {{n}_{{{\text{I}}_{3}^{ - }}}})}}{{{{n}_{{{\text{H}}_{0}^{ + }}}}}} = \frac{{2{{V}_{r}}([{{{\text{I}}}_{2}}] + [{\text{I}}_{3}^{ - }])}}{{{{V}_{{inj}}}[{\text{H}}_{0}^{ + }]}},$(4)
${{Y}_{{ST}}} = \frac{{6[{\text{IO}}_{3}^{ - }]}}{{6{{{[{\text{IO}}_{3}^{ - }]}}_{0}} + {{{[{{{\text{H}}}_{{\text{2}}}}{\text{BO}}_{3}^{ - }]}}_{0}}}},$Поскольку в данном случае процесс непрерывный, за время контакта Δt в зону смешения струй поступает раствор А (раствор серной кислоты) с расходом Q1 и раствор B (боратный буферный раствор) с расходом Q2. Поскольку во всех исследованиях Q1 = Q2 = Q, и при этом расход инжектируемой кислоты равен Q1, в формуле (3) отношение 2Vr/Vinj = 2(Q1 + Q2)/Q1 = 4.
В числителе формулы (3) – количество молей, соответствующее числу молей кислоты, потребленной в реакции (R2) (с учетом той части I2, которая преобразовалась в ${\text{I}}_{3}^{ - }$ в реакции (R3)), в знаменателе – общее число молей кислоты, инжектированной в аппарат.
В числителе формулы (4) – количество молей, соответствующее числу молей кислоты, потребленной в реакции (R2), в знаменателе – общее число молей кислоты, потребленных в реакциях (R2) и (R1).
По существу, индекс сегрегации XS отражает конверсию кислоты, инжектированной в реактор, с учетом ее участия в реакциях (R2) и (R3), выраженную через концентрацию йода и трийодида ${\text{I}}_{3}^{ - }.$
Иногда дополнительно используют показатель качества микросмешения – относительный объем идеального смешения [36]:
где VPM – объем зоны идеального смешения, м3; VST – объем зоны полной сегрегации, м3 (VPM + + VST = Vr).Очевидно, что по мере приближения к идеальному микросмешению α → ∞, для полной сегрегации α = 0.
Данная статья имеет следующую структуру: в теоретической части описана модель гидродинамики жидкостной пелены, образующейся в МРСС при столкновении вертикальных струй, позволяющая оценить основные параметры ее геометрии; далее описана экспериментальная установка и условия проведения экспериментов (включая фотографии и характеристики жидкостной пелены и йодид-иодатную методику). В частности, выполнены исследования по дифференциальному отбору проб в центральной зоне и на периферии аппарата. Далее приведены результаты экспериментов по микросмешению и их анализ на основе макрофотографий струй и пелены, сделанных с короткой выдержкой. Для всего исследованного диапазона расходов струй (от 100 до 400 мл/мин для всех диаметров струй, до 3200 мл/мин для dj = 2.0 мм) построены зависимости индекса сегрегации от струйного числа Вебера, полученные данные сопоставлены с результатами для реактора с магнитной мешалкой.
ТЕОРЕТИЧЕСКИЙ АНАЛИЗ
В работах Ашгрица [37, 38] представлен обзор современных методов расчета геометрии пелены. В недавних работах [2, 25] даны количественные оценки объема зоны столкновения, объема жидкостной пелены, а также удельной скорости диссипации.
Здесь важно напомнить о теоретических работах Дж. Тейлора [39, 40], а также о базирующихся на них количественных характеристиках горизонтальной (осесимметричной) жидкостной пелены, образующейся при столкновении двух струй. Ниже представлено развитие модели Тейлора, позволяющее связать размер и толщину пелены с числом Вебера.
В соответствии с моделью расширения плоской горизонтальной жидкостной пелены толщиной 2δ, описанной в [39, 40], по всему ее контуру образуется жидкостной валик. При движении валика с радиальной компонентой скорости wr баланс массы в пелене (рис. 1) представлен в форме
где Ls – длина контура пелены, м (для пелены круглой формы радиусом R периметр Ls = 2 πR); ρ – плотность жидкости, кг/м3.Рис. 1.
Схема к расчету предельного размера R и толщины жидкостной пелены. 1 – сталкивающиеся струи; 2 – жидкостная пелена; 3 – жидкостной валик на контуре пелены.
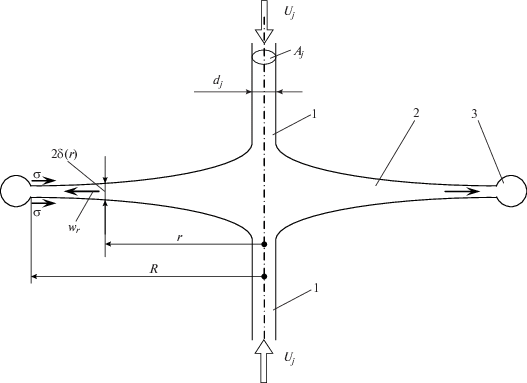
Для того же валика закон сохранения количества движения, с учетом действия поверхностного натяжения с двух сторон пелены:
(7)
$\frac{{d\left( {m{{w}_{r}}} \right)}}{{dt}} = m\frac{{d{{w}_{r}}}}{{dt}} + {{w}_{r}}\frac{{dm}}{{dt}} = 2{{L}_{s}}\sigma .$После подстановки (6) в (7) получим
Остановка расширения пелены, т.е. остановка жидкостного валика (и его последующее разрушение из-за роста “варикозной” неустойчивости) произойдет при dwr/dt = 0, откуда легко получить радиальную скорость в пелене в момент остановки и распада валика, т.е. при достижении им максимального радиуса пелены R (и минимальной толщины пелены):
(9)
${{w}_{{r.{\text{desint}}}}} = {{w}_{r}}\left( {r = R} \right) = \sqrt {\frac{\sigma }{{\rho {{\delta }_{{\min }}}}}} .$Баланс массы в струях и пелене:
Учитывая, что давление в любой точке жидкостной пелены (исключая зону столкновения струй) равно атмосферному, из теоремы Бернулли следует, что радиальная скорость в пелене будет равна скорости в струе, т.е.
что с достаточной степенью точности подтверждено экспериментально в работах [41, 42].
Исходя из закона сохранения массы, легко получить связь между толщиной пелены для произвольного радиуса r и площадью струй Aj:
Из уравнения (9) с учетом равенства скоростей (11) найдем минимальную толщину пелены по контуру пелены, при которой происходит распад валика:
Из уравнения (12) легко получить максимальный радиус пелены R
Для цилиндрической струи диаметром dj площадь струи Aj = π ${{d_{j}^{2}} \mathord{\left/ {\vphantom {{d_{j}^{2}} 4}} \right. \kern-0em} 4},$ тогда
Подставляя в (15) выражение (13), получим
(16а)
$R = \frac{{d_{j}^{2}\rho U_{j}^{2}}}{{8\sigma }} = {{d}_{j}}\frac{{{\text{W}}{{{\text{e}}}_{j}}}}{8},$или
Соотношение (16б) демонстрирует связь отношения радиуса пелены R и струи Rj со струйным числом Вебера
Отсюда следует (довольно очевидный) вывод о том, что струйное число Вебера является одним из определяющих критериев, характеризующих гидродинамику жидкостной пелены.
Интересно отметить связь струйного числа Вебера с диаметром струи dj при заданном расходе Qj = UjAj жидкости в струе:
(18)
${\text{W}}{{{\text{e}}}_{j}} = \frac{{{{d}_{j}}\rho U_{j}^{2}}}{\sigma } = \frac{\rho }{\sigma }\frac{{16Q_{j}^{2}}}{{\pi d_{j}^{3}}}.$Этим объясняется эффект снижения числа Вебера при фиксированном интервале расходов через сопла, обеспечиваемых имеющимся в распоряжении исследователей насосом, при увеличении диаметра сопла (см. графики ниже).
Еще одним ключевым гидродинамическим параметром является “струйное” число Рейнольдса
Поскольку при турбулентном режиме (а режим в большинстве рассмотренных случаев был турбулентным) роль вязкости снижается, основным определяющим критерием становится число Вебера.
Некоторые геометрические и гидродинамические параметры исследованных сопел микрореактора со сталкивающимися струями представлены в табл. 2.
Таблица 2.
Геометрические и гидродинамические характеристики исследованных сопел микрореактора со сталкивающимися струями
dj, мм | Qj, мл/мин | Uj, м/с | Wej | Rej |
---|---|---|---|---|
0.55 | 100–400 | 7.015–28.06 | 375–6000 | 3835–15340 |
1.0 | 100–400 | 2.12– 8.49 | 62.3–998 | 2109–8438 |
2.0 | 2800–3200 | 14.85–16.98 | 6114–7986 | 29530–33750 |
В последующем изложении для краткости записи индекс “j” у струйного числа Вебера опущен.
ЭКСПЕРИМЕНТАЛЬНАЯ ЧАСТЬ
Исследование микросмешения в емкости с магнитной мешалкой. Для проведения сравнительного анализа эффективности традиционных способов перемешивания были проведены опыты на магнитной мешалке ULAB, модель US-1500S с регулировкой частоты вращения. Исследование проводилось в конической колбе объемом 250 мл из стекла пирекс (размеры колбы: внутренний диаметр нижней части 82 мм, верхней части 47 мм, высота 147 мм), с магнитным якорем длиной 25 мм и диаметром 7 мм. Для определения качества микросмешения использована йодид-иодатная методика с концентрациями, описанными в [33].
Лабораторный стакан заполняли раствором боратного буфера с солями йодида калия KI и йодата калия KIO3. Над емкостью помещали сопло, выполненное из стекла марки пирекс длиной Ln = = 50 мм и внутренним диаметром dn = 1 мм, раствор серной кислоты подавался в центральную часть стакана с помощью перистальтического насоса Heidolph-5201, как показано на рис. 2. Подача раствора серной кислоты осуществлялась с постоянным расходом 100 мл/мин.
Рис. 2.
Схема лабораторной установки для исследования микроперемешивания в емкости с магнитной мешалкой: 1 – емкость с раствором серной кислоты; 2 – перистальтический насос Heidolph-5201; 3 –сопло для подачи раствора кислоты; 4 – стакан с раствором боратного буфера и солей йода; 5 – магнитный якорь, 6 – магнитная мешалка.
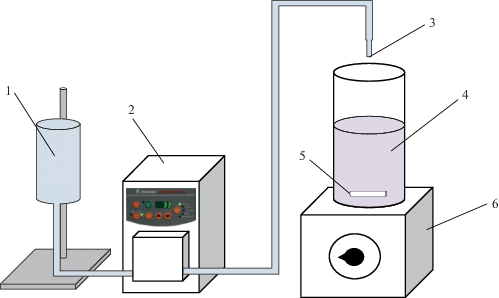
После окончания подачи раствора серной кислоты, отбирали пробу и анализировали на спектрофотометре СФ-2000. Процедура измерений на каждом режиме и анализ проб повторялись трижды.
Исследование микросмешения в микрореакторе со сталкивающимися струями. На кафедре оптимизации химической и биотехнологической аппаратуры СПбГТИ(ТУ) для изучения процессов микросмешения и синтеза наноразмерных частиц в микрореакторе со сталкивающимися струями (МРСС) разработана лабораторная установка [30], в составе которой использовались МРСС нескольких модификаций: 1) для проведения синтеза оксидных материалов [18–29] и параметров микросмешения – с цельным стеклянным корпусом; 2) для исследования геометрии и условий формирования и распада жидкостной пелены – “бескорпусной” МРСС (рис. 3), в котором сопла закреплялись с заданным углом 2θ на металлической рамке (рис. 4), или на рамке, оснащенной механическим угломером, для быстрого определения угла между соплами (рис. 5). Эксперименты по определению параметров микросмешения с использованием йодид-иодатной методики проводились с применением дифференциального отбора продуктов реакции: непосредственно под зоной столкновения струй и на периферии (рис. 3).
Рис. 3.
Лабораторная установка для исследования микроперемешивания с дифференциальным от бором продуктов реакции: непосредственно под зоной столкновения струй и на периферии: 1 – емкости для приема продуктов; 2 – сопла; 3 – шестеренчатые насосы TOPSFLO; 4 – расходомеры VISION® 1005 2F66 с блоком ILR750T 56704; 5 – зона столкновения струй; 6 – зона разлета филаментов и капель к стенкам реактора; 7 – жидкостная пелена; 8 – стакан для сбора жидкости из центральной зоны (зоны столкновения струй); 9 – кольцевая камера для сбора жидкости из зоны разлета филаментов и капель; 10, 11 – патрубки для отвода продуктов реакции; 12 – рамка для фиксации сопел.
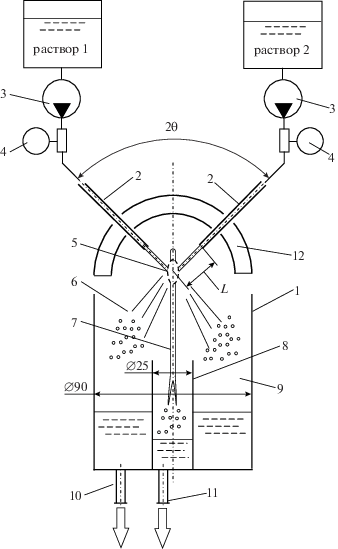
Рис. 4.
Фото зоны столкновения струй в микрореакторе со сталкивающимися струями, оснащенного металлической рамкой с дискретными значениями угла 2θ (на фото 2θ = 97.5°).
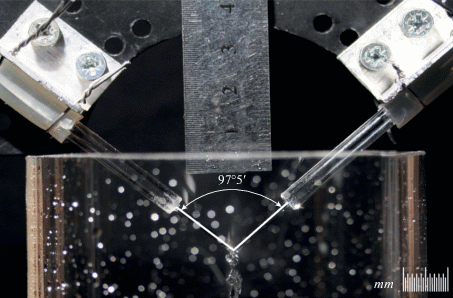
Рис. 5.
Фото верхней части лабораторной установки для исследования геометрии и условий формирования и распада жидкостной пелены с “бескорпусным” МРСС; 2θ = 100°, dj = 1.0 мм. Расстояние от выхода из сопла до точки столкновения L = 17 мм.
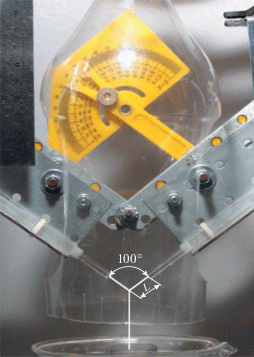
Подача растворов осуществляется двумя шестеренчатыми насосами фирмы TOPSFLO Micro Pump Technology (модель MG213XKDC24WI, КНР) с номинальной производительностью до 3500 мл/мин и рабочим давлением до 7 бар. Материал внутренней части корпуса – хромоникелевая сталь марки AISI 316L, шестерен – PEEK, уплотнений – PTFE.
Для определения объемных расходов растворов использовались турбинные расходомеры VISION® 1005 2F66 с диаметром проходного сечения 5 мм, пределами измерений расхода 100–2500 мл/мин, с погрешностью измерений ±3%, оборудованных электронными цифровыми показывающими блоками ILR750T 56704 с унифицированным токовым выходом.
Принцип действия МРСС (рис. 3) заключается в следующем: смешиваемые растворы подаются в виде тонких струй 5, вытекающих из сопел 2. Сопла расположены в вертикальной плоскости с углом между ними 2θ. Скорость струй должна быть достаточно высокой, чтобы обеспечить хорошее качество микросмешения, определяемое удельной скоростью диссипации энергии. При столкновении струй образуется зона 5 активного перемешивания растворов, которая при расширении формирует жидкостную пелену 7. Часть жидкости из пелены стекает вниз, в стакан 8 (центральная зона отбора проб), остальная жидкость разлетается в виде филаментов и капель на периферии пелены и собирается в кольцевой камере 9.
РЕЗУЛЬТАТЫ И ИХ ОБСУЖДЕНИЕ
Микросмешение в реакторе с магнитной мешалкой. Результаты исследования микросмешения в 250 мл колбе представлены на рис. 6. Как видно из графика, индекс сегрегации практически не зависит от частоты вращения якоря, и равен 0.52 ± 0.03. Напомним, что при Xs = 1 в аппарате имеет место полная сегрегация, т.е. проведенные эксперименты выявили крайне низкое качество микросмешения в данном устройстве.
Рис. 6.
Зависимость индекса сегрегации Xs от частоты вращения якоря магнитной мешалки n (об/мин). Реактор – коническая колба объемом 250 мл.
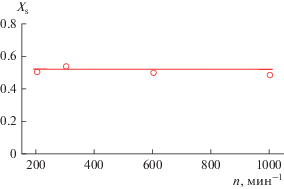
Таким образом, привычная для использования в лабораторных условиях магнитная мешалка, имеющая удовлетворительные показатели по макросмешению, совершенно непригодна для микросмешения. Этот результат может показаться неожиданным для многих исследователей, но он позволяет ответить на многие вопросы, связанные с широким распределением размеров наночастиц, синтезируемых прямым или обратным соосаждением, а также наличием больших концентраций побочных продуктов. Подробный анализ влияния условий гидродинамических условий синтеза неорганических наноразмерных материалов будет изложен в нашей следующей работе (направлена в журнал).
Дополнительно в той же конической колбе нами был проведен следующий эксперимент: в 0.05 М раствор щелочи (NaOH), подкрашенной фенолфталеином, при помощи шприца вводили концентрированный раствор HCl, при постоянном перемешивании магнитной мешалкой. Производилась видеозапись процесса, из которой хорошо видно, что изменение окраски раствора (с малиновой на бесцветную) происходило не мгновенно во всем объеме аппарата, а в течение 3–5 с, в крупных вихрях, масштаб которых сопоставим с линейными размерами аппарата. Очевидно, для процессов синтеза соосаждением, длительность которых оценивается миллисекундами, столь высокая неравномерность распределения реагентов в растворе неприемлема.
Характер течения жидкостной пелены при различных расстояниях до точки столкновения струй. В табл. 3 и 4 представлены фотографии жидкостной пелены, образованной при столкновении водяных струй при 24°C, при диаметре сопла dj = = 0.55 мм и 1.0 мм, и различных расстояниях L между срезом сопла и плоскостью столкновения струй (L = 5, 20, 40 мм), ось объектива нормальна к плоскости пелены; в табл. 5 – фотографии струй при диаметре сопла dj = 0.55 мм, ось объектива нормальна к плоскости струй. Снимки производились при помощи цифровой фотокамеры Canon EOS 40D со специализированным макрообъективом Canon EF-S 60 mm f/2.8 macro, с выдержкой 1.25 × 10–4 с и диафрагмой 4.5.
Таблица 3.
Фотографии жидкостной пелены при диаметре сопла dj = 0.55 мм. Жидкость – вода при 24°C. Ось объектива нормальна к плоскости пелены.
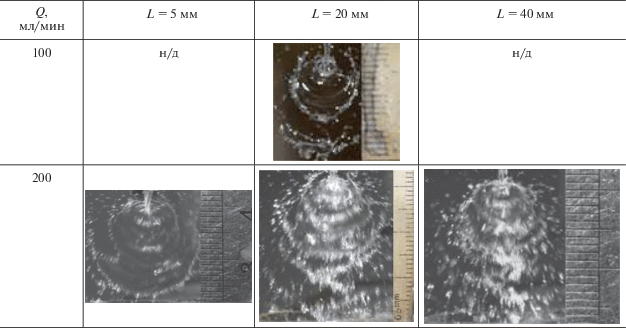
Таблица 4.
Фотографии жидкостной пелены при диаметре сопла dj = 1.0 мм. Жидкость – вода при 24°C. Ось объектива нормальна к плоскости пелены
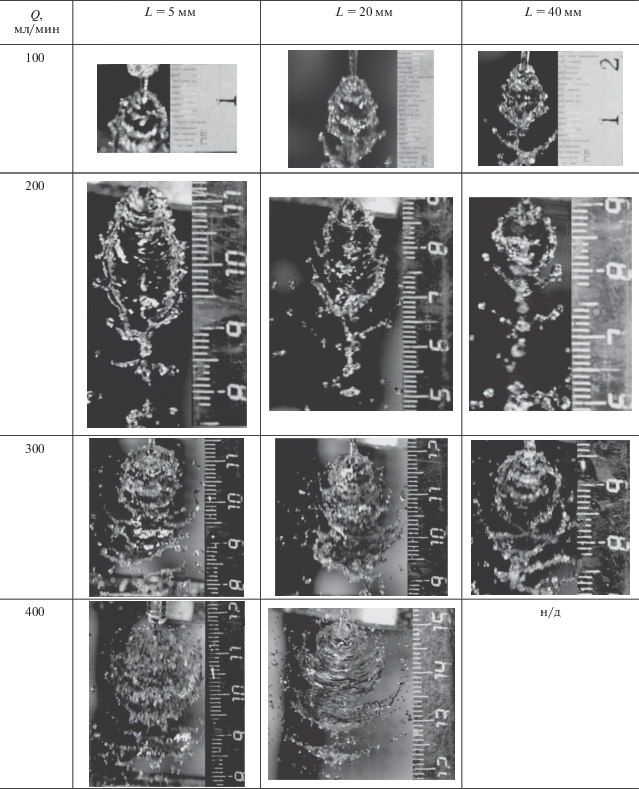
Таблица 5.
Фотографии струй и пелены при диаметре сопла dj = 0.55 мм. Жидкость – вода при 24°C. Ось объектива нормальна к плоскости струй

По фотографиям, представленным в табл. 3 и 4, виден ожидаемый результат: с увеличением расхода жидкости в струях (при прочих равных условиях) ускоряется распад пелены (см. формулу (16а)), что связано с увеличением кинетической энергии, вводимой пелену [2, 25, 37].
Влияние числа Вебера на качество микросмешения. На рис. 7 показаны зависимости индекса сегрегации Xs от струйного числа Вебера We для различных диаметров струй: dj = 0.55, 1.0 и 2.0 мм; и для различных расстояний от среза сопла до точки столкновения струй: L = 5, 20, 40 мм.
Рис. 7.
Зависимость индекса сегрегации от струйного числа Вебера для различных диаметров струй: а – dj = = 0.55 мм; б – dj = 1.0 мм; в – dj = 2.0 мм; Линии: 1 – L = 5 мм; 2 – L = 20 мм; 3 – L = 40 мм; заполненные точки (индекс “c”) – центральная зона отбора проб, контурные точки (индекс “p”) – периферийная зона отбора проб.
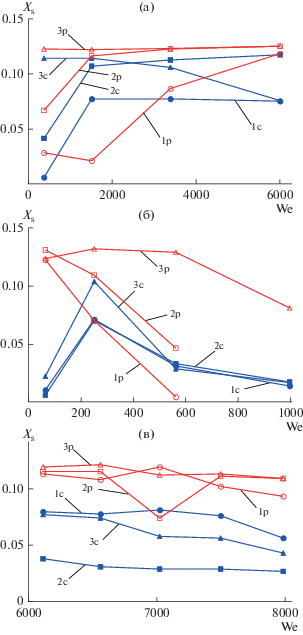
Проанализируем кривые, представленные на рис. 6, с учетом характера течения в пелене и формы струй, представленных в табл. 3–5.
1) Для dj = 0.55 мм анализ ситуации удобно проводить, ориентируясь на характер течения, представленный в табл. 3 и 5.
При We < 2000 наихудшее микросмешение оказалось для L = 40 мм. Это объясняется тем, что для струй столь малого диаметра при L/d = 40/0.55 = = 72.7 возникает капиллярная (так называемая “варикозная”) неустойчивость струй, в результате чего происходит их распад до момента столкновения (см. фото в табл. 5, правый столбец). При несинхронизированном столкновении капель микросмешение ухудшается.
При We > 2000 за счет увеличения кинетической энергии струя стабилизируется, и при We = 6000 значение Xs для L = 40 мм становится таким же, как и для L = 5 мм.
Ожидаемо наиболее высокое качество микросмешения для We < 2000 получено для L = 5 мм, несколько ниже для L = 20 мм. Как следует из фотографий в табл. 5, при L = 5 мм меньше разлет капель, пелена более компактная. При этом стоит отметить, что для L = 20 мм уже наблюдаются некоторые признаки варикозной неустойчивости, что также может являться причиной увеличения значения Xs по сравнению с L = 5 мм.
2) Для dj = 1.0 мм наилучшими являются расстояния L = 20 мм и L = 5 мм при We < 50. При We > 500 значение L практически не влияет – это связано с тем, что струя не распадается. А для L = = 40 мм струя успевает распасться на капли. Наличие максимума на кривой связано, по-видимому, с тем, что при малых числах Вебера (We ≈ 50) формируется стабильная жидкостная пелена, с незначительным разлетом капель на периферию, а при We ≈ 230 начинается распад пелены, при этом уровень кинетической энергии струй еще недостаточно высок для обеспечения высокого качества микросмешения. По мере дальнейшего увеличения скорости струй (We > 500) кинетическая энергия струй возрастает, а пелена (см. табл. 4) становится более компактной, т.е. растет и удельная скорость диссипации энергии ε, поскольку на меньший объем приходится больше энергии. В итоге при We ≈ 1000 (при отборе проб в центральной части аппарата) достигаются примерно такие же значения индекса сегрегации, как и при We ≈ 50 (Xs ≈ 0.01–0.02). Отметим, что для dj = 1.0 мм при L = 5 мм и L = 20 мм в исследованном диапазоне расходов (100–400 мл/мин) разлет капель и филаментов на периферию минимален (или почти отсутствует).
3) Для dj = 2.0 мм вариант L = 20 мм существенно лучше, чем L = 5 мм и L = 40 мм. При We < 6500 варианты L = 5 мм и L = 40 мм мало отличаются друг от друга, но по мере роста числа Вебера отличие между ними немного возрастает. Для всех случаев при увеличении числа Вебера качество микросмешения слабо, но монотонно снижается. Это связано с тем, что при большом диаметре струи расстояние, которое должны преодолеть ионы реагентов, увеличивается.
Резюме: наилучшее качество микросмешения достигается для dj = 0.55 мм, при L = 5 мм и We < 500. Сопоставимые результаты получены для dj = 1.0 мм, We ≈ 50, L = 20 мм и L = 5 мм.
При дальнейшем увеличении диаметра струй (более 1 мм) микросмешение ухудшается, даже при больших числах Вебера (см. рис. 6в).
Отсюда следует вывод об ограничениях на диаметр струй и скорость потока в них. А это ограничивает производительность аппарата в целом. Так, для dj = 0.55 мм оптимальной является производительность 100 мл/мин.
А для dj = 1.0 мм, вследствие того, что риск распада струй до момента их столкновения снижается (см. ниспадающую ветвь на рис. 6б), в лабораторной и промышленной практике целесообразно использовать большие расходы (We ≈ 1000), при этом расстояние L практически не влияет на индекс сегрегации.
ЗАКЛЮЧЕНИЕ
Теоретический анализ на основе модели Тейлора позволил выявить определяющее число для течения в жидкостной пелене – струйное число Вебера. С учетом турбулентного характера течения струйное число Рейнольдса перестает играть определяющую роль. Сделана оценка минимальной толщины пелены и ее размера, а также связь отношения радиуса пелены R и струи Rj со струйным числом Вебера Wej.
Экспериментально (при помощи йодид-иодатной методики) исследована эффективность микросмешения в лабораторном реакторе с магнитной мешалкой, а также в микрореакторе со сталкивающимися струями (МРСС), при различных диаметрах струй (dj = 0.55, 1.0 и 2.0 мм) и расстояниях от среза сопла до точки столкновения (L = 5, 20, 40 мм), для различных расходов жидкости. Качество микросмешения в реакторе с магнитной мешалкой оказалось крайне низким (индекс сегрегации Xs = 0.52 ± 0.03). Этим объясняется низкое качество получаемых продуктов при синтезе наноразмерных частиц при соосаждении в реакторе с магнитной мешалкой. Диаметр струй и расстояние от среза сопла до точки столкновения оказывают существенное влияние на качество микросмешения. Наилучшее качество микросмешения достигается для dj = 0.55 мм, при L = 5 мм и We < 500. Сопоставимые результаты получены для dj = 1.0 мм, We ≈ 50, L = 20 мм и L = 5 мм. Индекс сегрегации при этом в десятки раз ниже (Xs ≈ 0.01–0.02), чем в реакторе с магнитной мешалкой. Анализ макрофотографий струй и пелены, выполненных с короткой выдержкой (1.25 × 10–4 с) позволил выявить причины влияния расстояния L на индекс сегрегации: при относительно низких числах Вебера (We < 2000) и при L/dj ≈ 73 возникает капиллярная (так называемая “варикозная”) неустойчивость струй, в результате чего происходит их распад на капли до момента столкновения. При несинхронизированном столкновении капель микросмешение ухудшается. При We > 2000 за счет увеличения кинетической энергии струя стабилизируется, и при We = 6000 значение Xs для L = 40 мм становится таким же, как и для L = 5 мм.
Сделан вывод об ограничениях на диаметр струй и скорость потока в них. Для водных растворов оптимальным является диаметр 1 мм, поскольку он позволяет обеспечить относительно высокую производительность при высоком качестве микросмешения, при этом разлет капель и филаментов на периферию минимален (или почти отсутствует). При диаметре струй 0.55 мм хорошее качество микросмешения получено только при минимальном расходе (100 мл/мин), а для диаметра струй 2 мм минимальный индекс сегрегации (Xs ≈ 0.03) может быть достигнут при больших скоростях струй (15–17 м/с), но только в центральной зоне.
БЛАГОДАРНОСТИ
Исследование выполнено при финансовой поддержке РФФИ в рамках научного проекта № 19-33-90299 “Аспиранты”.
Авторы признательны И.В. Макушевой за помощь в проведении исследований микросмешения в лабораторном реакторе в виде конической колбы.
ОБОЗНАЧЕНИЯ
Aj | площадь поперечного сечения струи, м2 |
dj | диаметр струи, м |
Ls | длина контура пелены, м |
L | расстояние от среза сопла до точки столкновения струй, м |
Lopt | длина оптического пути измерительной ячейки, м |
m | масса, кг |
n | частота вращения якоря магнитной мешалки, об/мин |
OD | оптическая плотность, отн. ед. |
P | скорость диссипации механической энергии, Вт |
Qj | расход жидкости в струе, м3/с |
r | радиальная координата, м |
R | радиус жидкостной пелены, м |
Rj | радиус струи, м |
Uj | скорость жидкости в струе, м/с |
Vi | объем зоны столкновения струй, м3 |
Vinj | объем инжектируемого раствора кислоты, м3 |
Vr | объем реактора, м3 |
VPM | объем зоны идеального смешения, м3; |
VST | объем зоны полной сегрегации, м3 |
wr | радиальная компонента скорости в жидкостной пелене, м/с |
XS | индекс сегрегации |
Y | селективность по определяемому веществу |
α | относительный объем идеального смешения |
δ | полутолщина жидкостной пелены, м |
ε | удельная скорость диссипации энергии, Вт/кг |
ε353 | коэффициент затухания волн в трийодиде на длине волны 353 нм (ε353 = 26047 л/(моль см)) |
μ | вязкость жидкости, Па с |
ρ | плотность жидкости, кг/м3 |
σ | коэффициент поверхностного натяжения, Н/м |
Rej | струйное число Рейнольдса |
Wej | струйное число Вебера |
ИНДЕКСЫ:
Список литературы
Stankiewicz A.I., Moulijn J.A. Process intensification: Transforming chemical engineering. Chem. Eng. Progress. 2000. V. 96(1). P. 22–33.
Абиев Р.Ш. Микросмесители и микрореакторы со сталкивающимися струями: современное состояние и перспективы применения в химической технологии наноматериалов (обзор) // Теор. основы хим. технол. 2020. Т. 54. № 6. С. 668–686. https://doi.org/10.31857/S004035712006001910.31857/S0040357120060019 (Abiev R.S. Impinging-Jets Micromixers and Microreactors: State of Art and Prospects for Use in the Chemical Technology of Nanomaterials (Review)// Theor. Found. Chem. Eng. 2020. V. 54. № 6. P. 1131–1147. https://doi.org/10.1134/S0040579520060019)
Ravi Kumar D.V., Prasad B.L.V., Kulkarni A.A. Impinging Jet Micromixer for Flow Synthesis of Nanocrystalline MgO: Role of Mixing/Impingement Zone // Ind. Eng. Chem. Res. 2013. V. 52. P. 17376. https://doi.org/10.1021/ ie402012x
Liu Y., Cheng C., Liu Y., Prud’homme R.K., Fox R.O. Mixing in a multi-inlet vortex mixer (MIVM) for flash nano-precipitation, Chem Eng Sci. 2008. V. 63. P. 2829–2842. https://doi.org/10.1016/j.ces.2007.10.020
Pal S., Madane K., Kulkarni A.A. Antisolvent based precipitation: Batch, capillary flow reactor and impinging jet reactor. Chemical Engineering J. 2019. V. 369. P. 1161–1171. https://doi.org/10.1016/j.cej.2019.03.107
Nightingale A.M., deMello J.C. Segmented Flow Reactors for Nanocrystal Synthesis. Adv. Mater. 2013. V. 25. P. 1813–1821. https://doi.org/10.1002/adma.201203252
Kurt S.K., Akhtar M., Nigam K.D.P., Kockmann N. Continuous Reactive Precipitation in a Coiled Flow Inverter: Inert Particle Tracking, Modular Design, and Production of Uniform CaCO3 Particles. Ind. Eng. Chem. Res. 2017. V. 56. № 39. P. 11320–11335. https://doi.org/10.1021/acs.iecr.7b02240
Johnson B.K., Prud’homme R.K. Chemical Processing and Micromixing in Confined Impinging Jets, AIChE J. 2003. V. 49(9). P. 2264. https://doi.org/10.1002/aic.690490905
Патент РФ № 2625981, Б.И. 20, 2017. Способ получения нанопорошков феррита кобальта и микрореактор для его реализации.
Tacsi K., Joo A., Pusztai E., Domokos A., Nagy Z.K., Marosi G., Pataki H. Development of a triple impinging jet mixer for continuous antisolvent crystallization of acetylsalicylic acid reaction mixture. Chem. Eng. Proc.: Proc. Intens. 2021. V. 165. P. 108446. https://doi.org/10.1016/j.cep.2021.108446
Gavi E., Marchisio D., Barresi A. On the importance of mixing for the production of nanoparticles, J. Dispersion Sci. Technol. 2008. V. 29. P. 548–554.
Marchisio D.L., Rivautella L., Barresi A.A. Design and scale-up of chemical reactors for nanoparticle precipitation, AIChE J. 2006. V. 52. P. 1877–1887.
Krupa K., Nunes M.I., Santos R.J., Bourne J.R. Characterization of micromixing in T-jet mixers, Chem. Eng. Sci. 2014. V. 111. P. 48–55.
Metzger L., Kind M. On the transient flow characteristics in confined impinging jet mixers-CFD simulation and experimental validation, Chem. Eng. Sci. 2015. V. 133. P. 91–105.
Deshpande J.B., Chakrabarty S., Kulkarni A.A. Heterogeneous nucleation in citrate synthesis of AgNPs: Effect of mixing and solvation dynamics Chemical Engineering J. 2021. V. 421. P. 127753. https://doi.org/10.1016/j.cej.2020.127753
Teychené S., Rodríguez-Ruiz I., Ramamoorthy R.K. Reactive crystallization: From mixing to control of kinetics by additives. Current Opinion in Colloid & Interface Science. 2020. V. 46. P. 1–19. https://doi.org/10.1016/j.cocis.2020.01.003
Johnson B.K., Prud’homme R.K. Chemical processing and micromixing in confined impinging jets // AIChE J. 2003. V. 49. P. 2264–2282.
Proskurina O.V., Abiev R.S., Danilovich D.P., Panchuk V.V., Semenov V.G., Nevedomsky V.N., Gusarov V.V. Formation of nanocrystalline BiFeO3 during heat treatment of hydroxides co-precipitated in an impinging-jets microreactor. Chem. Eng. Proc. 2019. V. 143. P. 107598. https://doi.org/10.1016/j.cep.2019.107598
Проскурина О.В., Ноговицин И.В., Ильина Т.С., Данилович Д.П., Абиев Р.Ш., Гусаров В.В. Формирование наночастиц BiFeO3 с использованием струйного микрореактора // Журн. общей химии. 2018 Т. 88. № 10. С. 1699–1704. [Proskurina O.V., Nogovitsin I.V., Il’ina T.S., Danilovich D.P., Abiev R.Sh., Gusarov V.V. Formation of BiFeO3 Nanoparticles Using Impinging Jets Microreactor. Russian J. General Chemistry. 2018. V. 88. № 10. P. 2139–2143. https://doi.org/10.1134/S1070363218100183]
Proskurina O.V., Sivtsov E.V., Enikeeva M.O., Sirotkin A.A., Abiev R.Sh., Gusarov V.V. Formation of rhabdophane structured lanthanum orthophosphate nanoparticles in an impinging jets microreactor and rheological properties of sols based on them. Nanosystems: physics, chemistry, mathematics. 2019. V. 10(2). P. 206–214. https://doi.org/10.17586/222080542019102206214
Park J.I., Saffari A., Kumar S., Günther A., Kumacheva E. Microfluidic synthesis of polymer and inorganic particulate materials. Annu. Rev. Mater. Res. 2010. V. 40. P. 415–443.
Здравков А.В., Кудряшова Ю.С., Уголков В.Л., Абиев Р.Ш. Получение фотокатализаторов на основе диоксида титана, синтезированного с использованием микрореактора со сталкивающимися струями// Физика и Химия Стекла. 2020. Т. 46. № 4. С. 427–434. (Kudryashova Yu.S., Zdravkov A.V., Ugolkov V.L., Abiev R.Sh. Preparation of Photocatalizers Based on Titanium Dioxide Synthesized Using a Microreactor with Colliding Jets // Glass Physics and Chemistry. 2020. V. 46. № 4. P. 335–340. )https://doi.org/10.1134/S1087659620040082
Здравков А.В., Кудряшова Ю.С., Абиев Р.Ш. Фотокатализаторы на основе допированного неодимом диоксида титана, синтезированные в микрореакторе со сталкивающимися струями // Журн. общ. хим. 2020. Т. 90. № 9. 2020. С. 1422–1426. https://doi.org/10.31857/S0044460X2009014010.31857/S0044460X20090140 (Zdravkov A.V., Kudryashova Y.S., Abiev R.S. Synthesis of Titanium Oxide Doped with Neodymium Oxide in a Confined Impinging-Jets Reactor// Russian J. General Chemistry. 2020. V. 90(9). P. 1677–1680. https://doi.org/10.1134/S1070363220090145)
Кудряшова Ю.С., Здравков А.В., Абиев Р.Ш. Синтез иттрий-алюминиевого граната с использованием микрореактора со сталкивающимися струями // Физика и химия стекла. 2021. Т. 47. № 3. С. 330–336. https://doi.org/10.1134/S108765962103007X) (Kudryashova Yu.S., Zdravkov A.V., Abiev R.Sh. Synthesis of Yttrium-Aluminum Garnet Using a Microreactor with Impinging Jets // Glass Physics and Chemistry. 2021. V. 47. № 3. P. 260–264. 10.1134/S108765962103007X)
Абиев Р.Ш., Проскурина О.В., Еникеева М.О., Гусаров В.В. Влияние гидродинамических условий в микрореакторе со сталкивающимися струями на формирование наночастиц на основе сложных оксидов// Теор. основы хим. технол. 2021. Т. 55. № 1. С. 16–33. https://doi.org/10.31857/S004035712101001210.31857/S0040357121010012 (Abiev R.Sh., Proskurina O.V., Enikeeva M.O., Gusarov V.V. Effect of Hydrodynamic Conditions in an Impinging-Jet Microreactor on the Formation of Nanoparticles Based on Complex Oxides // Theor. Found. Chem. Eng. 2021. V. 55. № 1. P. 12–29. https://doi.org/10.1134/S0040579521010012)
Проскурина О.В., Соколова А.Н., Сироткин А.А., Абиев Р.Ш., Гусаров В.В. Роль условий соосаждения гидроксидов в формировании нанокристаллического BiFeO3 // Жур. Неорг. Хим. 2021. Т. 66. № 2. С. 160–167. https://doi.org/10.31857/S0044457X2102015X10.31857/S0044457X2102015X (Proskurina O.V., Sokolova A.N., Sirotkin A.A., Abiev R.Sh., Gusarov V.V. Role of Hydroxide Precipitation Conditions in the Formation of Nanocrystalline BiFeO3. Russ. J. Inorg. Chem. 2021. V. 66. № 2. P. 163–169. https://doi.org/10.1134/S0036023621020157).
Албади Я., Сироткин А.А., Семенов В.Г., Абиев Р.Ш., Попков В.И. Синтез суперпарамагнитных наночастиц GdFeO3 с использованием микрореактора со свободно сталкивающимися струями. Изв. Академии наук. Сер. хим. 2020. № 7. P. 1290–1295. (Albadi Y., Sirotkin A.A., Semenov V.G., Abiev R.S., Popkov V.I. Synthesis of superparamagnetic GdFeO3 nanoparticles using a free impinging-jets microreactor // Rus. Chem. Bull., Int. Ed. 2020. V. 69. № 7. P. 1290–1295. https://doi.org/10.1007/s11172-020-2900-x)
Albadi Y., Ivanova M.S., Grunin L.Y., Martinson K.D., Chebanenko M.I., Izotova S.G., Nevedomskiy V.N., Abiev R.S., Popkov V.I. The Influence of Co-Precipitation Technique on the Structure, Morphology and Dual-Modal Proton Relaxivity of GdFeO3 Nanoparticles // Inorganics. 2021. V. 9. P. 39. https://doi.org/10.3390/inorganics9050039
Albadi Y., Abiev R.S., Sirotkin A.A., Martinson K.D., Chebanenko M.I., Nevedomskyi V.N., Buryanenko I.V., Semenov V.G., Popkov V.I. Physicochemical and hydrodynamic aspects of GdFeO3 production using a free impinging-jets methods // Chem. Eng. and Proc. 2021. V. 166. P. 108473. https://doi.org/10.1016/j.cep.2021.108473
Fournier C., Falk L., Villermaux J. A new parallel competing reaction system for assessing micromixing efficiency – experimental approach. Chem. Eng. Sci. 1996. V. 22. P. 5053–5064.
Jasińska M. Test reactions to study efficiency of mixing // Chem. Process Eng. 2015. V. 36. № 2. P. 171–208.
Falk L., Commenge J.M. Performance comparison of micromixers, Chem. Eng. Sci. 2010. V. 65. P. 405–411. https://doi.org/10.1016/j.ces.2009.05.045
Commenge J.-M., Falk L. Villermaux–Dushman protocol for experimental characterization of micromixers. Chem Eng. Proc. 2011. V. 50. P. 979–990. https://doi.org/10.1016/j.cep.2011.06.006
Guichardon P., Falk L. Characterisation of micromixing efficiency by the iodide-iodate reaction system. Part I: experimental procedure // Chem. Eng. Sci. 2000. V. 55. P. 4233–4243. https://doi.org/10.1016/S0009-2509(00)00068-3
Guichardon P., Falk P., Villermaux J. Characterisation of mixing efficiency by the iodide/iodate reaction system. Part 2. Kinetic study // Chem. Eng. Sci. 2000. V. 55. P. 4243–4245. https://doi.org/10.1016/S0009-2509(00)00069-5
Villermaux J. Micromixing phenomena in stirred reactors. Encyclopedia of fluid mechanics. Houston: Gulf Publishing Company. 1986.
Li R., Ashgriz N. Characteristics of liquid sheets formed by two impinging jets. Physics Fluids. 2006. V. 18. P. 087104. https://doi.org/10.1063/1.2338064
Handbook of Atomization and Sprays / Ed. N. Ashgriz. Toronto: Springer Science + Business Media, LLC, 2011. Ch. 30. P. 685. https://doi.org/10.1007/978-1-4419-7264-4-30
Taylor G.I. The dynamics of thin sheets of fluid. III. Disintegration of fluid sheets. Proc. Roy. Soc. A. 1959. V. 253. P. 313. https://doi.org/10.1098/rspa.1959.0196
Фабер Т.Е. Гидроаэродинамика. М.: Постмаркет, 2001. 560 с.
Choo Y.-J., Kang B.-S. The velocity distribution of the liquid sheet formed by two low-speed impinging jets. Physics Fluids. 2002. V. 14(2). P. 622–627. https://doi.org/10.1063/1.1429250
Choo Y.J., Kang B.S. A study on the velocity characteristics of the liquid elements produced by two impinging jets. Experiments in Fluids. 2003. V. 34. P. 655–661. https://doi.org/10.1007/s00348-002-0554-0
Дополнительные материалы отсутствуют.
Инструменты
Теоретические основы химической технологии