Теоретические основы химической технологии, 2022, T. 56, № 2, стр. 209-218
Влияние структуры поверхности на смачиваемость полимерных насадочных элементов тепломассообменных аппаратов
П. Д. Васильев a, *, А. А. Сидягин a, А. В. Степыкин a, Д. М. Бухаров a, И. А. Балахнин a
a Нижегородский государственный технический университет им. Р.Е. Алексеева
г. Нижний Новгород, Россия
* E-mail: pvas-tech@yandex.ru
Поступила в редакцию 13.07.2021
После доработки 25.10.2021
Принята к публикации 09.11.2021
- EDN: AMJGLF
- DOI: 10.31857/S0040357122020166
Аннотация
Работа посвящена изучению методов улучшения смачиваемости полимерных насадочных элементов за счет нанесения на их рабочие поверхности различных геометрических структур. Авторами настоящей работы выполнен обзор последних научных исследований, в которых рассматривались явления смачивания на структурированных поверхностях. Разработан лабораторный стенд для изучения профиля и характера течения пленки жидкости по полимерным пластинам с различными структурами поверхностей. По результатам проведенных исследований было отмечено, что смачиваемость поверхности сильно зависит от ее структуры. Представлено качественное и количественное сравнение степени смачиваемости исследуемых пластин, в ходе которого было выявлено, что сетчатая конфигурация поверхности пластины является наиболее эффективной. На основании полученных данных указаны рекомендации по практическому применению результатов настоящей работы.
ВВЕДЕНИЕ
В химической, нефтехимической, нефтеперерабатывающей и других смежных отраслях промышленности широко используются тепломассообменные процессы, которые проводят в тарельчатых и насадочных аппаратах. В настоящее время активно применяются насадочные колонные аппараты, поскольку они обеспечивают, как правило, меньший перепад давления по высоте (особенно при использовании регулярных насадок), широкий диапазон устойчивой работы, достаточно высокий КПД и более высокую разделительную способность [1]. При этом разрабатывается большое количество новых конструкций промышленных насадочных контактных устройств, что повышает конкурентоспособность колонн с насадкой относительно тарельчатых аппаратов [2–4].
Насадочные колонны относятся к аппаратам поверхностного типа. Контакт фаз в них осуществляется на поверхности пленки жидкости, растекающейся по насадочным элементам. Эффективность работы такого аппарата зависит от множества факторов, таких как: равномерное орошение, перераспределение жидкости, ввод и распределение газовой фазы по сечению колонны. Однако в большей степени эффективность рассматриваемого оборудования зависит от типа применяемых контактных устройств (насадок). Так, конструкция насадки и материал, из которого она изготовлена, во многом определяют достигаемую в аппарате величину поверхности контакта фаз, которая, в свою очередь, оказывает сильное влияние на качество проведения того или иного технологического процесса [5].
Насадки изготавливают из различных материалов, применение которых обусловлено формовочными качествами, смачиваемостью, прочностью, термостойкостью и коррозионной стойкостью. Самыми распространенными материалами для изготовления насадок являются металл, полимеры, керамика и фарфор [6]. Последние тенденции в области материального исполнения насадочных контактных элементов направлены в сторону применения именно полимерных материалов. Главными достоинствами насадок из полимерных материалов являются: легкость придания им требуемой формы, малый вес, доступность и дешевизна пластмасс, что в совокупности позволяет организовать производство с меньшими капиталовложениями и низкой себестоимостью получаемого продукта. Помимо этого насадки из полимерных материалов долговечны и обладают оптимальными техническими характеристиками, подходящими под множество различных технологических процессов. Так, например, авторами монографий [7, 8] отмечается, что регулярные полимерные насадки получили широкое распространение в промышленных градирнях, а автором работы [9] отмечается увеличение эффективности абсорбционных аппаратов в результате замены керамических и металлических насадок на полимерные.
Тем не менее область применения полимерных насадок ограничивается их термостойкостью. Так, в зависимости от типа используемого полимера упомянутые насадки могут применяться в тепломассообменных аппаратах, работающих при температурах от минус 40 до плюс 80°С [6].
Также известно, что полимерные материалы обладают низкой поверхностной энергией, что определяет основной недостаток пластиковых насадок – плохую смачиваемость. Это обстоятельство значительно снижает эффективность протекания технологических процессов, поскольку оно требует увеличения энергозатрат на орошение насадки. В противном случае недостаточное орошение приведет к уменьшению величины активной поверхности контакта фаз. Следует отметить, что последняя характеристика во многом зависит от геометрической поверхности насадки. На данный момент разработано множество насадок, геометрические параметры и конструктивные особенности которых незначительно отличаются друг от друга. Каждое новое конструктивное решение дает меньший выигрыш в увеличении удельной поверхности контакта фаз. В соответствии с этим, более детальное внимание следует уделить методам улучшения смачиваемости поверхностей полимерных насадок.
ОБЗОРНАЯ ЧАСТЬ
Самым перспективным методом улучшения смачиваемости насадочных элементов промышленных аппаратов является формирование на их поверхностях искусственной шероховатости или заданной геометрической структуры [10]. Среди опубликованных исследований по данной тематике можно выделить работу [11], в которой выявлено, что наличие регулярной шероховатости в виде горизонтальных впадин (расположенных поперек движения потока) увеличивает равномерность распределения пленки жидкости по поверхности полимерного листа насадки. В представленном случае впадины выполняют роль накопителей и перераспределителей жидкости, и, тем самым, они повышают реальную величину смоченной поверхности [11].
Также представляют интерес работы [12, 13], в которых исследовался характер течения жидкости на различных структурированных поверхностях. Объектом исследования авторов работы [12] являлась пластина с горизонтальными треугольными гофрами высотой 0.6 мм, а авторов работы [13] – поверхность с вертикальными прямоугольными выступами высотой 0.2 мм. Результаты данных исследований идентичны, поскольку в обоих случаях доказано, что полное смачивание указанных структурированных поверхностей наступает при меньших расходах орошающей жидкости по сравнению с гладкой пластиной.
В работе [14] представлены экспериментальные исследования влияния горизонтальных и вертикальных микроструктур на зоны растекания пленки жидкости по профилированным поверхностям при различных значениях пленочного числа Рейнольдса. Угол наклона гофр к горизонтали составлял 47°. После получения результатов данных исследований было показано, что наличие микротекстуры и ее ориентация оказывают существенное влияние на характер пленочного течения жидкости, размер и форму зон ее растекания по поверхности пластин [14]. Наиболее эффективным оказалось вертикальное направление микротекстуры, которое обеспечивает значительный переток орошаемой жидкости через вершины крупных ребер [14], в результате чего смачивается вся поверхность пластины. Следует отметить, что на пластинах с горизонтальным направлением микротекстуры, а также на пластинах без какой-либо микротекстуры, подобный эффект не наблюдается.
Значительный объем исследований характеристик смачивания и гидродинамики течения жидкости по гофрированной поверхности регулярной насадки с просечными элементами представлен в работах [15–17]. Авторами представленных работ было выявлено, что горизонтальное расположение элементов приводит к лучшему растеканию жидкости по сравнению с их вертикальным расположением. В первом случае на поверхности насадки образуется пленочное течение жидкости, а во втором ее движение происходит лишь по отдельным впадинам гофр. Также в работе [15] отмечается, что с увеличением плотности орошения насадки с горизонтальным расположением элементов происходит более интенсивное увеличение ширины стекающей пленки жидкости при ее условно постоянной толщине. Данное наблюдение свидетельствует о том, что с помощью гофр и просечек можно добиться улучшения смачиваемости поверхности регулярной насадки.
Изучение влияния шероховатости на смачиваемость непрофилированных поверхностей обычно производят с помощью статических методов. Например, результаты исследований [18, 19] свидетельствуют о наличии критической высоты и шага микронеровностей, которые определяют максимальный краевой угол лежащей капли, что указывает на плохую смачиваемость поверхности. С другой стороны, авторами статьи [20] установлено, что существует определенная величина шероховатости, определяющая минимальное значение краевого угла и, соответственно, лучшую смачиваемость. Однако дальнейшее увеличение высоты микронеровностей приводит к резкому и значительному росту значения краевого угла, что подтверждает результаты вышеупомянутых исследований [18, 19].
В рамках настоящей работы изучено влияние различных структур поверхностей на смачиваемость пластин, изготовленных из полимерных материалов. Основной целью исследований является определение принципиальной структуры поверхности, которая в перспективе позволит улучшить смачиваемость полимерных насадочных элементов и, тем самым повысить эффективность промышленных колонных аппаратов с пластиковыми насадками.
ЭКСПЕРИМЕНТАЛЬНАЯ ЧАСТЬ
Известно, что в насадочных массообменных аппаратах реализуется непрерывное пленочное течение жидкости. На основании этого в настоящей работе было принято решение использовать динамический метод оценки смачиваемости исследуемых поверхностей. Данный метод заключается в определении геометрических параметров течения жидких пленок по наклонным поверхностям подготовленных образцов. Получаемые параметры являются косвенными величинами, характеризующими процесс смачивания. Несмотря на это, в рамках сравнительного эксперимента указанный метод позволяет определить наиболее эффективную структуру поверхности, которая отличается лучшей смачиваемостью. Следует отметить, что сравнительные результаты адекватны только при исследовании образцов, приведенных к одним и тем же условиям в части размеров, метода изготовления, материального исполнения, методики проведения эксперимента и обработки полученных данных.
С учетом этого для проведения исследований были разработаны образцы, представляющие собой пластины с длиной 120 мм и шириной 60 мм. Они изготовлены с помощью 3D-принтера с технологией печати FDM (метод послойного наплавления). Применение 3D-печати обосновано необходимостью быстрого и удобного получения готовых образцов с необходимой структурой поверхности. В качестве полимерного материала пластин использовался PLA-пластик.
В качестве базового образца была изготовлена полимерная пластина с условно гладкой поверхностью. При ее моделировании не задавались какие-либо микро- и макроструктуры. Однако с помощью микроскопа было выявлено, что в результате 3D-печати на поверхности этой пластины была сформирована микроструктура, которая характеризуется направленными под 45° ребрами с высотой 0.05 мм и шагом 0.75 мм. Профиль ребра – прямоугольный с шириной 0.5 мм.
На следующем шаге прорабатывались варианты различных структур поверхностей, которые могут оказать положительное влияние на смачиваемость изготавливаемых образцов. Как указывалось в обзорной части настоящей работы, некоторыми авторами уже изучено влияние вертикальных и горизонтальных гофр на смачиваемость исследуемых пластин. Следовательно, для дальнейшего расширения и систематизации научно-практических данных в рассматриваемой области было принято решение оценить влияние других примитивных форм поверхности пластин на степень их смачиваемости. Так, методом 3D-печати были изготовлены образцы с полусферическими выступами и впадинами, геометрические размеры которых идентичны (см. рис. 1а). В дальнейшем полученные структуры поверхностей образцов с нанесенными выступами и вырезанными впадинами будем соответственно называть точечной и пористой. Аналогичным образом была изготовлена пластина, на поверхность которой нанесены перпендикулярно пересекающиеся ребра (см. рис. 1б). Данные ребра образуют на поверхности образца структуру в виде искусственной сетки, вследствие чего полученную структуру в дальнейшем будем называть сетчатой. Последним изготовленным полимерным образцом является пластина с шевронной структурой поверхности (см. рис. 1в). Для каждого образца, кроме гладкого, высота (глубина) всех искусственных неровностей составляла 0.5 мм.
Рис. 1.
Структуры поверхностей образцов: (а) – точечная и пористая; (б) – сетчатая; (в) – шевронная.
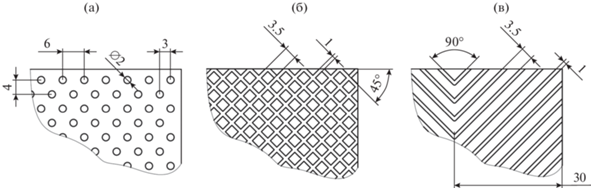
С целью последующего сравнения степени смачиваемости представленных полимерных пластин относительно других материалов, применяемых в производстве насадок, были подготовлены гладкие образцы из керамики и углеродистой стали. Керамический образец имел микропористую структуру поверхности, свойственную для промышленных нерегулярных керамических насадок. Состояние отделки рабочей поверхности стального образца характеризуется показателем шероховатости Ra не более 1.6 мкм.
Изучение профиля и характера течения пленки жидкости по наклонным поверхностям полученных образцов проводилось на лабораторном стенде, принципиальная схема которого представлена на рис. 2. Основным элементом стенда являлся лабораторный штатив 1 с двумя лапками. На конце нижней лапки была закреплена платформа 2, на которую устанавливались исследуемые образцы с предварительно обезжиренными и осушенными рабочими поверхностями. Угол наклона платформы относительно горизонтальной оси составлял не менее 80°. На конце верхней лапки располагалось сопло 3 для орошения рабочих поверхностей исследуемых образцов. Внутренний диаметр сопла имел величину 5 мм. Расстояние между соплом и исследуемыми образцами составляло не более 10 мм.
Рис. 2.
Схема лабораторного стенда: 1 – лабораторный штатив; 2 – платформа; 3 – сопло; 4 – мембранный насос; 5 – стеклянный сосуд; 6 – игольчатый вентиль; 7 – ротаметр; 8 – всасывающая линия насоса; 9 – нагнетательная линия насоса.
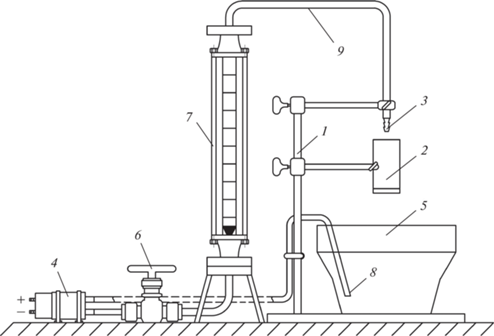
В качестве рабочей жидкости для проведения эксперимента использовалась вода с температурой 15°С. Данная температура контролировалась термометром (на рис. 2 не показан) и в ходе эксперимента не изменялась. Вода подавалась в сопло по системе гибких шлангов с помощью мембранного насоса 4. Забор жидкости во всасывающую линию насоса осуществлялся из стеклянного сосуда 5, куда также попадала вода, стекающая с поверхности исследуемого образца. Таким образом была организована циркуляция рабочей жидкости по замкнутому контуру лабораторного стенда. Для регулирования и измерения расхода воды, подаваемой в сопло для орошения образов, были предусмотрены игольчатый вентиль 6 и ротаметр 7.
Фиксация стационарного режима течения пленки жидкости по поверхностям исследуемых образцов производилась с помощью высококачественной видеосъемки с частотой 60 кадров в секунду. Вся поверхность пластины в это время подсвечивалась с помощью стробоскопа, рабочая частота которого настраивалась с целью получения более качественного изображения. Видеозаписи, полученные в ходе эксперимента, подвергались детальной раскадровке в видеоредакторе. Подготовленные кадры загружались в двухмерную систему автоматизированного проектирования, где с помощью меню диагностики определялась смоченная поверхность исследуемого образца Ft и начальная длина (от верхнего края пластины) стекающей пленки жидкости L0. Пример обработки профиля растекания пленки жидкости по поверхности гладкого полимерного образца представлен на рис. 3.
Рис. 3.
Пример обработки профиля растекания пленки жидкости: (а) – кадр эксперимента; (б) – получаемый профиль.
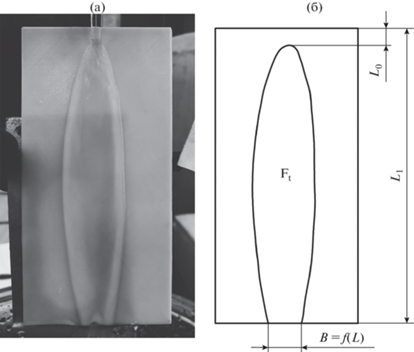
В научной практике для оценки смачиваемости твердых поверхностей в условиях динамического эксперимента применяются различные абсолютные и относительные величины. Например, в работе [21] абсолютные значения ширины стекающей пленки жидкости использовались при оценке характера растекания воды вдоль поверхности вертикальной перегородки исследуемого контактного устройства. Авторы статьи [15] изучали степень смачиваемости поверхности насадки путем определения угла растекания струи воды, подаваемой на орошение экспериментального образца. В работах [12, 13] для интерпретации результатов математического компьютерного моделирования течения пленки жидкости по гладким и гофрированным поверхностям использовалось отношение смоченной поверхности к общей поверхности пластины.
Принимая во внимание факт, что в настоящей работе эксперимент проводился при наличии только одной точки орошения в виде сопла, а также учитывая представленный выше опыт различных исследователей, в качестве показателя степени смачиваемости образцов было принято использовать такую абсолютную величину, как ширина стекающей пленки жидкости B. Однако в ходе эксперимента было выявлено, что ширина этой пленки значительно меняется по длине L вдоль фронта растекания жидкости. Таким образом, имеем функцию B = f(L), которая непрерывна на отрезке [L0; L1] и дифференцируема в интервале (L0; L1), где величина L1 – это конечная длина стекающей пленки жидкости, равная длине исследуемого образца. Следовательно, согласно формуле конечных приращений среднее значение функции B = f(L) может быть выражено следующим образом:
(1)
${{B}_{{\text{m}}}} = \frac{1}{{{{L}_{{\text{1}}}} - {{L}_{{\text{0}}}}}}\int\limits_{{{L}_{{\text{0}}}}}^{{{L}_{{\text{1}}}}} {f\left( L \right)dL} .$В свою очередь величина смоченной поверхности исследуемого образца определяется по формуле:
(2)
${{F}_{{\text{t}}}} = \int\limits_{{{L}_{{\text{0}}}}}^{{{L}_{{\text{1}}}}} {f\left( L \right)dL} .$Тогда выражение (1) можно преобразовать к следующему виду:
Таким образом, с помощью описанной выше методики обработки экспериментальных данных и выражения (3) были получены необходимые величины Bm для каждого образца.
Как правило, смачиваемость насадки оценивают в зависимости от плотности орошения. Однако в настоящей работе необходимо было использовать характеристики одиночного сопла, из которого осуществлялось орошение исследуемых образцов. В связи с этим было принято решение использовать такую безразмерную характеристику течения жидкости, выходящей из сопла, как число Рейнольдса. Подобный подход применен в работе [22], где число Рейнольдса использовалось для описания течения жидкости на выходе из сопла конической форсунки. Формула для расчета данного числа имеет следующий вид:
Исследования проводили при постепенном увеличении расхода в диапазоне чисел Рейнольдса от 1000 до 3500. Максимальная степень орошения для экспериментов была определена по эталонному керамическому образцу из условий достижения пленкой жидкости его боковых краев. Для полимерных образцов расход увеличивали до достижения величины Re = 4000 с целью более широкой визуализации характера растекания пленки жидкости по их рабочим поверхностям.
РЕЗУЛЬТАТЫ И ИХ ОБСУЖДЕНИЕ
Экспериментальные графики зависимостей средней ширины стекающей пленки жидкости от числа Рейнольдса для исследуемых образцов представлены на рис. 4. Как и следовало ожидать, для каждого образца с увеличением числа Re растет величина Bm, также как и площадь смоченной поверхности. При этом представленные графики показывают, что структура поверхности полимерных пластин оказывает значительное влияние на их смачиваемость.
Рис. 4.
Зависимость средней ширины стекающей пленки жидкости от числа Рейнольдса для полимерных образцов с шевронной (1), гладкой (2), точечной (3), пористой (4), сетчатой (5) структурами поверхностей и для керамического образца (6).
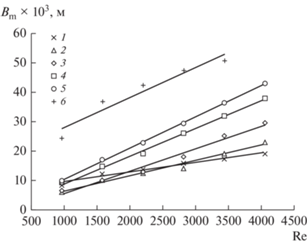
Рассматривая полученные данные, следует отметить, что пластина с шевронной структурой поверхности характеризуется наименьшим влиянием числа Рейнольдса на среднюю ширину растекающейся пленки жидкости. На рис. 4 видно, что прямая линия тренда зависимости величины Bm от числа Re для данного образца обладает малым углом наклона относительно оси абсцисс. Это объясняется следующими наблюдениями. Набегающая струя воды встречает резкое сопротивление в виде сходящихся ребер в относительной близости к точке орошения пластины, где наблюдается рост пятна пленки жидкости по ширине образца. Однако при дальнейшем растекании жидкость стремится к центру пластины, где ее пленочное движение переходит в ручейковое (см. рис. 5а). Данный характер течения жидкости по шевронной поверхности образца остается постоянным во всем диапазоне нагрузок по числу Рейнольдса, что является причиной незначительного роста величины Bm по мере увеличения степени орошения пластины.
Рис. 5.
Профиль растекания жидкости при Re = 3500 для полимерных образцов с шевронной (а), гладкой (б), точечной (в), пористой (г), сетчатой (д), структурами поверхностей и для керамического образца (е).
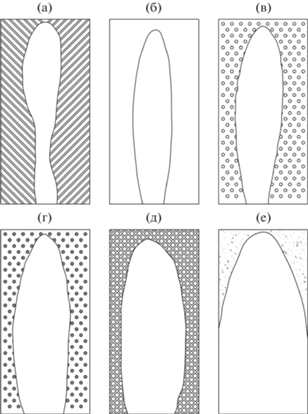
Шевронная поверхность показывает хорошую смачиваемость по сравнению с гладкой полимерной пластиной только в диапазоне чисел Рейнольдса от 1000 до 3000. При дальнейшем увеличении орошения гладкий образец лучше смачивается водой. На его поверхности образуется более равномерная по ширине пленка жидкости (см. рис. 5б), которая не встречает на своем пути значительного сопротивления. Однако по сравнению с другими образцами данная пленка остается достаточно узкой. Помимо этого, она характеризуется неравномерной толщиной в поперечном сечении. У боковых краев толщина пленки значительно больше, что объясняется пограничным эффектом, когда сила поверхностного натяжения частиц жидкости преобладает над силами их межмолекулярного взаимодействия с твердой поверхностью. В связи с этим жидкость скапливается у боковых краев пленки, но не растекается дальше по ширине.
Пластина с точечной структурой поверхности имеет аналогичный характер движения жидкости у пограничного слоя, но в тоже время этот образец лучше смачивается водой. Искусственные выступы создают сопротивление движению пленки жидкости. При этом визуально различимы линии тока воды, возникающие при обтекании отдельных выступов. Данные наблюдения указывают на возникающую поперечную турбулизацию частиц в стекающей пленке жидкости, что способствует увеличению ее ширины, а также приводит к интенсификации процессов тепло- и массопереноса.
Таблица 1.
Результаты численного сравнения исследуемых образцов по степени смачиваемости
№ п/п | Образец | ΨR.m |
---|---|---|
1 | Гладкий керамический (эталон) | 1.0 |
2 | Полимерный с сетчатой поверхностью | 0.551 |
3 | Гладкий металлический | 0.521 |
4 | Полимерный с пористой поверхностью | 0.484 |
5 | Полимерный с точечной поверхностью | 0.351 |
6 | Полимерный с шевронной поверхностью | 0.350 |
7 | Гладкий полимерный | 0.290 |
Среди полимерных образцов лучшими показателями смачиваемости обладают пластинки с пористой и сетчатой структурами поверхности. Искусственные впадины улучшают адгезию поверхности образца, вследствие чего смещается равновесие на линии раздела фаз в пользу сцепления частиц жидкости и твердого тела. Так, у боковых границ смоченной поверхности пористого образца с увеличением числа Рейнольдса наблюдается постепенное заполнение впадин водой. Вследствие этого значительно расширяется профиль растекания пленки жидкости по сравнению с гладким полимерным образцом (см. рис. 5г). Аналогичным образом происходит смачивание сетчатой поверхности, где впадины образованы ребрами сетки. Однако следует отметить, что структура поверхности сетчатого образца дополнительно создает значительное сопротивление движению пленки жидкости. Вблизи точки орошения пластины наблюдается диссипация энергии падающей струи, а в этом месте образуется широкое пятно жидкости. Здесь вода перетекает через ребра и заполняет пустые впадины, а затем стекает вниз сплошной по ширине пленкой (см. рис. 5д). При этом движение пленки жидкости по поверхности сетчатого образца характеризуется образованием волн, наличие которых существенно интенсифицирует тепломассоперенос [23].
Таким образом, по результатам анализа полученных данных было выявлено, что среди испытанных структур поверхностей именно сетчатая конфигурация оказывает наиболее положительное влияние на смачиваемость полимерных пластин. Как видно на рис. 4, пластина с сетчатой структурой поверхности характеризуется наибольшей шириной стекающей пленки жидкости по сравнению с другими полимерными образцами во всем диапазоне чисел Рейнольдса.
С помощью представленных на рис. 4 зависимостей была произведена качественная оценка смачиваемости исследуемых полимерных образцов. Для практического использования полученных результатов в области разработки насадочных контактных элементов для колонных аппаратов, данные результаты должны быть интерпретированы количественно. В связи с этим исследуемые полимерные образцы необходимо сравнить с эталоном. Для нашего случая эталоном будет являться керамическая поверхность. Среди множества материалов для насадочных элементов именно керамика характеризуется наилучшей смачиваемостью, на что также указано в работе [6]. Действительно, на рис. 4 можно заметить, что экспериментальные точки зависимости величины Bm от числа Re для керамического образца лежат гораздо выше, чем для пластиковых. При этом на рис. 5е видно, как при значении Re = 3500 пленка жидкости растекается по всей ширине керамической пластины, что не достигается на полимерных образцах.
На основании вышесказанного, для количественной оценки степени смачиваемости исследуемых образцов предлагается использовать следующую относительную величину:
В дальнейшем величину ΨR будем называть коэффициентом относительной смачиваемости. Согласно уравнению (5) данный коэффициент выражается отношением площадей смоченных поверхностей исследуемого и эталонного (керамического) образцов. В таком случае, значение ΨR = 1 отражает максимально достижимый (желаемый) результат, а значения ΨR < 1 показывают степень приближения к этому результату.
Графические зависимости коэффициента относительной смачиваемости от числа Рейнольдса, представленные на рис. 6, показывают, как с увеличением орошения меняется интенсивность роста смоченной поверхности полимерных образцов относительно керамического эталона. Здесь следует отметить, что в исследуемом диапазоне нагрузок по числу Рейнольдса величина ΨR для гладкого и шевронного образцов меняется незначительно. С другой стороны, пластины с сетчатой, пористой и точечной структурами отличаются более интенсивным ростом смоченной поверхности по сравнению с эталоном. Следовательно, при сохранении тенденции этого роста с увеличением числа Рейнольдса для представленных образцов теоретически может быть достигнуто значение ΨR = 1, что будет являться свидетельством достижения желаемого результата. Однако, на данном этапе не известен дальнейший характер представленных зависимостей при значениях Re > 3500, а его определение в рамках настоящей работы не представилось возможным ввиду наличия ограничений по геометрическим размерам изготовленных образцов. Таким образом, изучение возможности достижения эталонной смачиваемости структурированных полимерных поверхностей при больших числах Рейнольдса является одной из ключевых целей дальнейших исследований.
Рис. 6.
Зависимость коэффициента относительной смачиваемости от числа Рейнольдса для полимерных образцов с шевронной (1), гладкой (2), точечной (3), пористой (4) и сетчатой (5) структурами поверхностей.
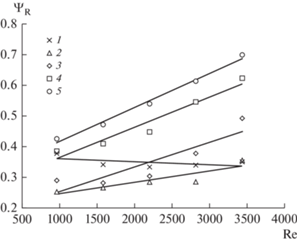
Ввиду того, что коэффициент относительной смачиваемости меняется в зависимости от числа Рейнольдса, то для итогового численного сравнения исследуемых образцов будем использовать среднее арифметическое значение этого коэффициента, определяемое по формуле:
(6)
${{\Psi }_{{{\text{R}}{\text{.m}}}}} = \frac{{\sum\limits_{i = 1}^n {{{\Psi }_{{{\text{R}}i}}}} }}{n}.$В таблице представлены результаты численного сравнения исследуемых образцов по степени смачиваемости. Полимерные образцы с наличием любой из представленных в настоящей работе конфигураций поверхностей обладают большими значениями ΨR.m по сравнению с их гладким аналогом в исследуемом диапазоне нагрузок по числу Рейнольдса. Данный факт подтверждает целесообразность применения метода структурирования поверхности с целью улучшения ее смачиваемости.
Также, с помощью таблицы дается количественная оценка эффективности нанесения различных структур на поверхности полимерных пластин. Критерием эффективности в представленном случае является безразмерная величина ΨR.m. Проанализировав имеющиеся данные, наиболее эффективной следует признать сетчатую структуру поверхности, для которой величина вышеуказанного критерия составляет 0.551. По величине этого критерия полимерная пластинка с нанесенной сеткой превосходит гладкий стальной образец. В применении к промышленной практике данное наблюдение показывает нам, что за счет структурирования поверхностей полимерных насадочных элементов, они могут смачиваться лучше, чем стальные, не смотря на то, что последние характеризуются большей поверхностной энергией.
ЗАКЛЮЧЕНИЕ
На основании проведенных исследований можно рекомендовать изготовление полимерных насадочных элементов с сетчатой структурой поверхности. Следует отметить, что применение данных насадок в промышленности несет в себе такие преимущества, как: снижение негативного влияния каналообразования в слое насадки ввиду улучшения смачиваемости ее отдельных элементов, интенсификация процессов тепло- и массопереноса за счет волнового режима движения пленки жидкости по сетчатой поверхности, минимизация числа точек орошения, которая, в свою очередь, позволяет упростить конструктивное исполнение оросительного устройства.
Кроме того, при использовании насадок с сетчатой структурой поверхности открывается возможность снижения величины плотности орошения для тех тепломассообменных аппаратов, в которых расход жидкой фазы выбирается исходя из условий полного смачивания слоя насадки. При организации рециркуляции жидкости данный факт также позволит снизить энергозатраты на ее перекачку. С другой стороны, если расход жидкости ограничивается условиями проведения конкретного технологического процесса или указывается в техническом задании на проектирование, то использование рассматриваемых насадок позволит увеличить значение их удельной смоченной поверхности при заданной плотности орошения.
Таким образом, можно сделать вывод, что дальнейшее изучение смачиваемости полимерных насадочных элементов с сетчатой структурой поверхности является перспективным направлением для будущих исследований, а их использование в промышленности позволит повысить эффективность тепломассообменных аппаратов.
ОБОЗНАЧЕНИЯ
B | ширина стекающей пленки жидкости, м |
d | диаметр сопла, м |
F | площадь смоченной поверхности, м2 |
ΨR | коэффициент относительной смачиваемости |
L | длина стекающей пленки жидкости, м |
n | количество экспериментальных точек |
w | скорость жидкости на выходе из сопла, м/с |
μ | коэффициент динамической вязкости жидкости, Па с |
ρ | плотность жидкости, кг/м3 |
Re | число Рейнольдса для сопла |
ИНДЕКСЫ
Список литературы
Марешова Л.А., Богатых К.Ф., Рольник Л.З., Ягафарова Г.Г. Результаты внедрения в промышленность разработок по регулярным перекрестноточным насадкам учеными уфимского государственного нефтяного технического университета // Электронный научный журн. нефтегазовое дело. 2007. № 1. С. 74.
Фарахов М.И., Лаптева Е.А. Энергосбережение на установке разделения этаноламинов // Известия высших учебных заведений. Проблемы энергетики. 2008. № 7–8. С. 133.
Леонтьев В.С. Инновации в области разработки высокоинтенсивных массообменных устройств для модернизации ректификационных комплексов // Электронный научный журн. нефтегазовое дело. 2012. № 1. С. 178.
Farakhov M.I., Laptev A.G., Basharov M.M. Modernization of mass-exchange equipment by new packings in chemical engineering // Theor. Found. Chem. Eng. 2015. V. 49. № 3. P. 233. [Фарахов М.И., Лаптев А.Г., Башаров М.М. Модернизация массообменных аппаратов новыми насадками в химической технологии // Теорет. основы хим. технологии. 2015. Т. 49. № 3. С. 247.]
Kagan A.M., Yudina L.A., Pushnov A.S. Active surface of the elements of irregular heat and mass transfer packings // Theor. Found. Chem. Eng. 2012. V. 46. № 2. P. 165. [Каган А.М., Юдина Л.А., Пушнов А.С. Активная поверхность элементов нерегулярных тепло- массообменных насадок // Теорет. основы хим. технологии. 2012. Т. 46. № 2. С. 199.]
Контактные насадки промышленных тепломассообменных аппаратов / Под ред. Лаптева А.Г. Казань: Отечество, 2013.
Иванов С.П. Полимерные оросители градирен. М.: Интер, 2009.
Лаптев А.Г., Ведьгаева И.А. Устройство и расчет промышленных градирен. Казань: КГЭУ, 2004.
Голованов И.Ю. Эффективность замены керамических и металлических элементов насадок полимерными на примере регулярной насадки из колец рашига // Роль инноваций в трансформации современной науки: сборник статей по итогам Международной научно-практической конференции. Магнитогорск, 2019. С. 80.
Князев С.Д. Перспективные методы улучшения смачиваемости поверхностей насадок из полимерных материалов // Научные перспективы – 2020: материалы региональной молодежной научно-технической конференции. Дзержинск, 2020. С. 56.
Дорошенко А.В., Васютинский С.Ю. Совершенствование тепломассообменной аппаратуры для энергетических систем // Проблемы региональной энергетики. 2008. № 2. С. 32.
Yoshiyuki I., Xi C. Development of numerical prediction of liquid film flows on packing elements in absorbers // Engineering review. 2011. V 11. № 2. P. 1.
Cooke J.J., Gu S., Armstrong L.M., Luo K.H. Gas-liquid flow on smooth and textured inclined planes // International Scholarly and Scientific Research & Innovation. 2012. V. 6. № 8. P. 1446.
Павленко А.Н., Володин О.А., Сердюков В.С. Особенности пленочного течения жидкого азота по структурированным поверхностям // Вестник Новосибирского государственного университета. Серия: Физика. 2015. Т. 10. № 1. С. 33.
Пушнов А.С., Городилов А.А., Беренгартен М.Г. Гидродинамика растекания струи жидкости по гофрированной поверхности регулярной насадки с просечными элементами // Химическая технология. 2014. Т. 15. № 6. С. 364.
Gorodilov A.A., Berengarten M.G., Pushnov A.S. Features of fluid film falling on the corrugated surface of structured packings with perforations // Theor. Found. Chem. Eng. 2016. V. 50. № 3. P. 325. [Городилов А.А., Беренгартен М.Г., Пушнов А.С. Особенности пленочного течения жидкости по гофрированной поверхности регулярных насадок с перфорацией // Теорет. основы хим. технологии. 2016. Т. 50. № 3. С. 334.]
Gorodilov A.A., Pushnov A.S., Berengarten M.G. Spreading of a fluid jet on the corrugated surface of the structured packing of wet scrubbers // Problems of the regional energetics. 2014. № 2. P. 57.
Nakae H., Yoshida M., Yokota M. Effects of roughness pitch of surfaces on their wettability // J. Mater. Sci. 2005. V. 40. P. 2287.
Junchao W., Yankun M., Yijun C., Guosheng L., Yinfei L. Influence of surface roughness on contact angle hysteresis and spreading // Colloid Polym. Sci. 2020. V. 298. P. 1107.
Kubiak K.J., Wilson M.C.T., Mathia T.G., Carval Ph. Wettability versus roughness of engineering surfaces // Wear. 2011. V. 271. № 3–4. P. 523.
Шарипов И.И., Круглов Л.В., Круглов В.И., Дмитриева О.С. Разработка конструкции струйно-пленочного контактного устройства с целью интенсификации тепломассобмена // Известия высших учебных заведений. Проблема энергетики. 2018. Т. 20. № 9–10. С. 146.
Наз М.Я., Сулейман Ш.А., Эриваджуди Б., Кузилати К. Визуализация распада струи горячего водного аэрозоля, инициированного коническими форсунками // Прикладная механика и техническая физика. 2015. Т. 56. № 2. С. 53.
Актершев С.П., Алексеенко С.В. Волновое течение испаряющейся пленки жидкости // Известия Томского политехнического университета. 2014. Т. 324. № 4. С. 6.
Дополнительные материалы отсутствуют.
Инструменты
Теоретические основы химической технологии