Теоретические основы химической технологии, 2022, T. 56, № 4, стр. 453-463
Очистка изопентановой фракции от изопентенов в производстве изопрена
Ф. Б. Шевляков a, *, Э. Р. Зайнутдинов a, Н. В. Терещенко a, Т. Г. Умергалин a
a Уфимский государственный нефтяной технический университет
Уфа, Россия
* E-mail: sfb1980@mail.ru
Поступила в редакцию 31.03.2021
После доработки 08.03.2022
Принята к публикации 10.03.2022
- EDN: WHRNVX
- DOI: 10.31857/S0040357122040066
Аннотация
На первой стадии дегидрирования изопентана производства изопрена образуется изопентан-изопентеновая фракция, которую после стабилизации от легких и отделения от тяжелых углеводородов разделяют в колонне экстрактивной ректификации. Традиционно использующиеся колонны с числом тарелок 140–150 и экстрагента на основе N,N-диметилформамида селективного по отношению к олефиновым и диеновым углеводородам обеспечивают получение изопентанановой фракции с остаточным содержанием изопентенов 5 мас. % и более. Более глубокой очистки в производстве изопрена не предусмотрено и остаточные изопентены в составе изопентановой фракции возвращаются на первую стадию дегидрирования с алюмохромовым катализатором, где преимущественно превращаются в углеводороды С1–С4 и закоксовывают катализатор. Результаты моделирования процесса экстрактивной ректификации изопентан-изопентеновой фракции с помощью среды Honeywell UniSim Desing показали возможность извлечения изопентенов до остаточного содержания 0.67 мас. % за счет возврата части изопентановой фракции на орошение колонны в смеси с N,N-диметилформамидом.
ВВЕДЕНИЕ
Изопрен нашел применение в производстве синтетического каучука, используемого для изготовления резинотехнических изделий электротехнической, авиационной и машиностроительной отраслей промышленности, для изготовления изделий пищевого и медицинского назначения [1].
В литературных источниках приводится большое число способов синтеза изопрена, однако в промышленном производстве их реализовано пять: синтез из 2-метилпропена и формальдегида, двухступенчатое дегидрирование изопентана, дегидрирование изопентенов, димеризацией пропилена, выделение из пиролизной фракции С5 [1, 2]. Итоговая стоимость синтетического полиизопренового каучука в большей степени определяется затратой на производство изопрена, которая в свою очередь складывается от стоимости исходного сырья, количества энергии, затраченной на стадии синтеза, стабилизации катализата от легких и тяжелых примесей, выделение целевого продукта из углеводородной смеси, и прочие стадии очистки мономера до полимеризационной чистоты. Среди промышленных способов получения изопрена наиболее энерго-ресурсозатратным является двухстадийное дегидрирование изопентана, по которому из 2 тонн изопентана получают 1 тонну изопрена.
В настоящее время на ОАО “Синтез-Каучук” г. Стерлитамак производят изопрен, получаемый двухстадийным дегидрированием изопентана, годовая выработка изопрена составляет сотни тысяч тонн. Полупродукт производства – изоамиленовая фракция может быть использована для синтеза третамиловый эфира, являющимся высокооктановым компонентом автомобильного бензина. Для дегидрирования изопентана используется алюмохромовый катализатор (ИМ-2204, ИМ-2206 и др. модификации), на котором образуются три изопентена – 2-метилбутена-1 (γ), 3-метилбутена-1 (α) и 2-метилбтена-2 (β) [3] и ряд продуктов побочных реакций, связанных со скелетной изомеризацией, крекингом, дегидроциклизацией, образованием ацетиленовых и кислородсодержащих соединений, коксообразованием.
Для производства конкурентноспособной продукции по данному способу продолжаются исследования, направленные на снижение потерь изопрена как при каталитических превращениях на первой и второй стадиях дегидрирования изопентана и изопентенов, так и при фракционировании смесей изопентан-изопентеновой и изопентен-изопреновых фракций.
Катализат первой стадии дегидрирования изопентана после стабилизации содержит смесь близкокипящих углеводородов С5. Для разделения фракции С5 используют метод экстрактивной ректификации, где в качестве разделяющих агентов используется ацетон, фурфурол, ацетонитрил, N,N-диметилформамид (ДМФА), диметилацетамид, N-метилпирролидон, β-метоксипропионитрил. Внедрение в производство селективных катализаторов дегидрирования изопентана позволило увеличить содержание изопентенов в катализате до 30 мас. % [4]. Режимные параметры экстрактивной ректификации не позволяют абсорбировать α-изопентен разделяющим агентом из-за его низкой температуры кипения (20.1°С).
Таким образом, в состав изопентановой фракции после экстракции переходит α-изопентен, количественно равным его содержанию в сырьевом потоке. Суммарное остаточное содержание изопентенов составляет 5 мас. % и более. Кроме энергозатрат на перекачивание изопентана в качестве рецикла на дегидрирование с остаточным количеством α-изопентена до 1.5 т/ч наблюдаются осложнения в виде протекания побочных процессов, связанных с крекингом α-изопентена на первой стадии дегидрирования до С1–С4 и закоксовываением катализатора.
С целью совершенствования технологической схемы разделения изопентан-изопентеновой фракции рассмотрена возможность доизвлечения изопентенов путем возврата части изопентановой фракции на орошение в колонну хемосорбции в смеси с ДМФА.
Для решения поставленной задачи рассмотрена возможность модернизации схемы колонны экстракции путем возврата части изопентановой фракции на орошение в смеси с ДМФА через аппарат-смеситель, обеспечивающую доизвлечение остаточных изопентенов из изопентановой фракции.
ЭКСПЕРИМЕНТАЛЬНАЯ ЧАСТЬ
В лабораторных условиях проведено смешение ДМФА с изопентановой фракцией, содержащей остаточное количество изопентенов 5.13 мас. %. Состав исходного ДМФА и изопентановой фракции представлен в табл. 1 и 2.
Таблица 1.
Результаты анализа состава ДМФА
Состав ДМФА | Н2О | ∑С5 | ДМФА |
---|---|---|---|
x мас. % | |||
Исходный | 0.10 | 0 | 99.90 |
Эксперимент 1 | 0.087 | 5.76 | 94.15 |
Эксперимент 2 | 0.052 | 13.05 | 86.90 |
Эксперимент 3 | 0.078 | 13.61 | 86.32 |
Таблица 2.
Состав изопентановой фракции
Компоненты, мас. % | Исходный | Эксперимент 1 | Эксперимент 2 | Эксперимент 3 |
---|---|---|---|---|
∑С4 | 0.04 | 0.05 | 0.02 | 0.02 |
неопентан | 0.04 | 0.05 | 0.04 | 0.06 |
изопентан | 90.20 | 90.20 | 90.66 | 90.91 |
н-пентан | 4.17 | 4.17 | 4.20 | 4.39 |
∑изопентенов, | 5.13 | 5.15 | 4.70 | 4.61 |
в том числе: | ||||
α-изопентен | 3.62 | 3.73 | 3.34 | 3.27 |
γ-изопентен | 1.36 | 1.28 | 1.22 | 1.21 |
β-изопентен | 0.16 | 0.14 | 0.14 | 0.13 |
∑н-пентенов | 0.39 | 0.36 | 0.36 | 0.35 |
Изопрен | 0.01 | 0.01 | 0.01 | 0.01 |
ДМФА | 0.022 | 0.011 | 0.017 | 0.014 |
Изопропиловый спирт | 0.00026 | 0.00019 | 0.00013 | 0.00021 |
Эксперименты по извлечению изопентенов проводили в объемном аппарате смешения и в статическом аппаратах смешения, результаты которых сравнивали с данными эксперимента, моделирующего расслоенное течение углеводородной фракции и экстрагента. Время контакта смешиваемых потоков в экспериментах было принято равным одной минуте.
Извлечение изопентенов оценивали по изменению их концентраций в изопентановой фракции и в ДМФА.
Компонентный состав углеводородов изопентановой фракции анализировали методом газожидкостной хроматографии на двух приборах с использованием пламенно-ионизационного детектора. Неподвижная фаза – 5% полиэтиленгликоль ПЭГ-1500 на цветохроме 1К фракции 0.15–0.25 мм, газ-носитель – гелий, температура колонки начальная 80°С, конечная 150°С, температура испарителя 160°С, длина колонки 3 м, диаметр 3 мм. Массовую долю ДМФА в изопентановой фракции определяли методом абсолютной калибровки. С использованием детектора по теплопроводности. Неподвижная фаза – 20% диэтиленгликольдибутират на диатомитовом кирпиче фракции 0.15–0.25 мм, газ-носитель – гелий, температура колонки 30°С, температура испарителя 75°С, длина колонки 7 м, диаметр 3 мм. Массовую долю углеводородов С4 и С5 в изопентановой фракции определяли методом внутренней нормализации с учетом концентрации ДМФА, определенной на приборе, описанном выше.
Компонентный состав ДМФА определяли методом газожидкостной хроматографии на приборе с детектором по теплопроводности. Условия хроматографирования: колонка с неподвижной фазой – полисорб, фракции 0.25–0.30 мм, неподвижная фаза – 10% полиэтиленгликоль ПЭГ-3000, длина колонки 6 м, диаметр 3 мм, газ-носитель–гелий; температура испарителя 225°С, термостата колонки начальная 120°С, конечная 200°С. Массовую долю компонентов определяли методом внутренней нормализации.
В ДМФА объемом 30 мл и температурой плюс 23°С, вводили изопентановую фракцию объемом 45 мл с температурой плюс 10°С. Выдерживали смесь без перемешивания в течение одной минуты (эксперимент 1).
В эксперименте 2 данную смесь в течение 30 с перемешивали лопастной мешалкой в круглодонной колбе, далее выдержали без перемешивания 30 с и проводили анализ (эксперимент 2).
При температуре и объемных соотношениях перемешиваемых сред, соответствующим условиям экспериментов 1 и 2, смешивание проводили в трубчатом турбулентном аппарате (эксперимент 3). Схема экспериментальной установки представлена на рис. 1.
Рис. 1.
Установка смешения раствора ДМФА и изопентановой фракции. 1 – емкость с ДМФА; 2 – емкость с изопентановой фракцией; 3 – трубчатый турбулентный аппарат.
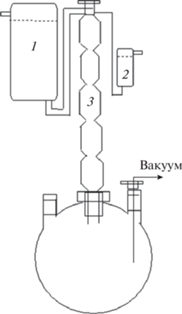
После экстракции, проведенной по экспериментам 1–3, ДМФА из изопентановой фракции отделяли перегонкой при 80°С и анализировали углеводородный состав.
РЕЗУЛЬТАТЫ И ИХ ОБСУЖДЕНИЯ
Анализ смешения потоков. Низкое содержание изопентенов в изопентановой фракции потребовало проведение эксперимента с полуторакратным превышением объема изопентановой фракции над ДМФА. Образовавшаяся двухслойная система позволила анализировать каждый слой. Состав ДМФА и изопентановой фракции приведены соответственно в табл. 1 и 2.
При условиях эксперимента 1 содержание углеводородов С5 в ДМФА возросло с отсутствия до 5.76 мас. %, в изопентановой фракции перераспределения содержаний компонентов не произошло, что свидетельствует о высокой растворяющей способности экстрагента и неравновесии изучаемой среды.
Проведение экстракции при увеличении контакта смешиваемых сред за счет использования перемешивающего устройства привело к интенсификации растворения углеводородов С5 в ДМФА. Перераспределению углеводородных компонентов в изопентановой фракции произошло в сторону уменьшения содержания изопентенов, которое снизилось на 0.43 мас. % (табл. 1 и 2). Интенсификация экстракции с использованием объемного аппарата смешения может быть рассмотрена как параметр, влияющий на смещение к равновесию.
Разница плотностей ДМФА и изопентановой фракции более чем на 30% требует при работе перемешивающего устройства больших затрат энергии для создания однородной смеси. В этой связи решение по организации перемешивания может быть достигнуто за счет движения потока при использования статического аппарата смешения. Результаты работ по смешиванию двухфазных потоков, приведенные в литературных источниках [5–11], показали эффективность использования трубчатого турбулентного аппарата диффузор-конфузорной конструкции. Следует ожидать устранения недостатков объемного аппарата смешения в следующем испытании с использованием трубчатого турбулентного аппарата. Интенсивное перемешивание в канале аппарата, создающее развитую поверхность смешиваемых сред, и избыточное давление во входном канале аппарата должны способствовать успешной экстракции олефиновых углеводородов.
Экстракция изопентановой фракции в ДМФА в потоке канала трубчатого турбулентного аппарата позволила снизить остаточное содержание изопентенов в углеводородной фракции на 0.52 мас. % (табл. 2), а эффективность данного способа составила 10% в расчете на изопентены. Экстрагирование в аппарате смесителе происходит за короткий промежуток времени, что недостаточно для наступления фазового равновесия компонентов в дисперсной системе. Частично извлеченные таким образом изопентены предлагается направлять в колонну экстракции на тарелки, расположенные ниже, чем поток флегмы изопентановой фракции, вводимой на орошение колонны экстракции. Изопентены более растворимы в ДМФА, чем изопентан, и увеличение их концентрации в колонне будет способствовать вытеснению изопентана из экстрагента.
Смешение изопентановой фракции и ДМФА может быть использовано при совершенствовании экстрактивной ректификации изопентан-изопентеновой фракции. Эффективность извлечения изопентенов может быть увеличена путем перераспределения точек ввода экстрагента и рециклового потока – изопентановой фракции в колонну экстракции, что требует проведения расчета их соотношения и выбора точки ввода при совместной подаче в колонну.
Моделирование объекта исследования. При моделировании аналогичных систем используется различное программное обеспечение [12–20]. Моделирование колонны экстрактивной ректификации проводилось в среде Honeywell UniSim Desing.
Экспериментальная часть работы смешивания изопентановой фракции с ДМФА проведена с целью установления влияния степени перемешивания на эффективность извлечения остаточных изопентенов, установления принципиальной возможности и целесообразности применения данного способа на установке экстрактивной ректификации. Полученные результаты экспериментальной части при дальнейшем моделировании экстрактивной ректификации не использовались.
При составлении модели экстрактивной ректификации значения параметров модели уточнялись по данным составов компонентов технологических потоков и режимных значений, полученных с промышленной установки. Для метода NRTL используя внутренние алгоритмы для оценки коэффициентов бинарного взаимодействия компонентов были рассчитаны коэффициенты Aij, которые представлены в табл. 3. Коэффициенты Bij и Cij для всех пар компонентов были приняты равными 0.0 и 0.3 соответственно.
Таблица 3.
Коэффициенты бинарного взаимодействия
Aij | Н-пентан | γ-изоамилен | α-изоамилен | β-изоамилен | Изопрен | Транс-пиперилен | Цис-пиперилен | Изобутан | Бутан | Изобутилен | Пентен-1 | Изопентан | Неопентан | ДМФА |
---|---|---|---|---|---|---|---|---|---|---|---|---|---|---|
Н-пентан | – | 32.95 | 28.69 | 99.02 | 114.78 | 83.42 | 83.42 | –33.59 | 12.61 | –65.22 | 29.51 | 56.86 | 66.78 | 634.11 |
γ-изоамилен | 3.79 | – | 33.11 | 50.26 | 25.89 | –26.27 | –26.27 | 25.77 | 25.76 | –45.97 | 31.83 | 0.22 | –15.78 | 692.64 |
α-изоамилен | 17.20 | –23.92 | – | 102.69 | 28.67 | 9.42 | 9.42 | –88.79 | –87.85 | 59.25 | 48.72 | –14.64 | 24.93 | 697.43 |
β-изоамилен | –74.77 | –47.99 | –82.59 | – | 55.54 | 20.84 | 20.84 | 110.97 | 97.47 | 6.79 | 100.23 | 97.96 | 98.21 | 622.60 |
Изопрен | 44.83 | 15.93 | 5.63 | 14.00 | – | 25.78 | 25.78 | 687.68 | 268.79 | 29.91 | 1.41 | 43.99 | 53.60 | 950.74 |
Транс-пиперилен | 62.46 | 75.89 | 15.56 | 51.44 | –18.47 | – | 48.73 | 224.63 | 242.10 | –58.79 | 9.76 | 59.92 | 81.19 | 882.75 |
Цис-пиперилен | 62.46 | 75.89 | 15.56 | 51.44 | –18.47 | 48.73 | – | 224.63 | 242.10 | –58.79 | 9.76 | 59.92 | 81.19 | 882.75 |
Изобутан | 87.34 | 1.04 | 138.88 | –94.20 | –486.94 | –75.11 | –75.11 | – | 91.47 | 38.22 | 148.24 | 87.41 | 53.90 | 423.81 |
Бутан | –5.26 | 0.73 | 138.00 | –82.71 | –106.72 | –90.16 | –90.16 | –68.77 | – | 37.62 | 147.14 | 50.48 | 137.31 | 425.46 |
Изобутилен | 104.31 | 39.22 | –52.66 | –10.20 | –3.60 | 101.05 | 101.05 | 6.03 | 6.18 | – | –45.33 | 113.69 | 124.20 | 490.07 |
Пентен-1 | 16.33 | –22.75 | –48.41 | –80.49 | 30.16 | 15.79 | 15.79 | –98.69 | –97.39 | 46.84 | – | –16.10 | 23.61 | 698.72 |
Изопентан | –51.48 | 34.89 | 63.10 | –73.49 | 116.50 | 86.11 | 86.11 | –59.88 | –49.53 | –71.62 | 64.19 | – | 40.02 | 632.77 |
Неопентан | 5.14 | 49.26 | 25.16 | –78.48 | 103.06 | 71.03 | 71.03 | –51.68 | –100.93 | –95.07 | 26.00 | –3.42 | – | 662.92 |
ДМФА | 1985.23 | 708.19 | 564.65 | 990.22 | 78.76 | 113.66 | 11.66 | 2113.28 | 2112.17 | 700.06 | 564.60 | 1986.09 | 1969.36 | – |
Анализ состава смеси (табл. 4), поступающей на разделение, значений температур и давлений, при которых происходит процесс разделения изопентана и изопентенов методом экстрактивной дистилляции с ДМФА, показал, что наиболее подходящей моделью расчета констант фазового равновесия является модель NRTL [21, 22].
Таблица 4.
Состав сырьевых потоков, подаваемых в колонну экстракции
Параметр | Содержание, мас. % |
---|---|
Изо-бутан | 0.02 |
Н-бутан | 0.02 |
Неопентан | 0.27 |
Изопентан | 61.15 |
Н-пентан | 2.09 |
∑ изопентенов, в т.ч. | 31.3 |
α-изоамилен | 1.75 |
γ-изоамилен | 9.88 |
β-изоамилен | 19.67 |
∑н-пентенов | 2.63 |
Изопрен | 2.03 |
Транс-пиперилен | 0.24 |
Цис-пиперилен | 0.24 |
Модели колонн были реализованы с учетом геометрических размеров и внутренних массообменных устройств, применяемых на производстве. Десорбер представляет из себя аппарат колонного типа с 57 тарелкой клапанного типа, конденсатором и ребойлером. Колонна экстракции является аппаратом со 116 клапанными тарелками и также с конденсатором и ребойлером. На реальном производстве колонна экстракции разделена на две колонны, расположенные рядом. Сходимость рециклов при расчете колонн обеспечивалась алгоритмом Вегстейна и 30 итерациями. Расчет парожидкостного равновесия компонентов был проведен с использованием метода NRTL. Значения остальных физико-химических параметров веществ и компонентов рассматриваемой системы были приняты по умолчанию в соответствии с установками программы.
Технологическая схема процесса с орошением колонны экстракции смесью изопентановой фракции с ДМФА представлена на рис. 2.
Рис. 2.
Схема разделения изопентан-изоамиленовой фракции. 1, 2 – колонны экстрактивной ректификации; 3 – колонна десорбции; 4, 5 – конденсатор; 6, 7, 8 – тройник; 9 – смеситель; 10, 11 – ребойлер. I – ДМФА; II – сырье; III – ДМФА основной поток; IV – смесь ДМФА с изопентаном; V – рецикл изоамиленовой фракции; VI – рецикл изопентановой фракции; VII – изопентановая фракция в парк; VIII – изоамиленовая фракция в парк; IX – отработанный ДМФА. Сплошными линиями обозначено движение потоков по действующей схеме, пунктирными линиями – поток орошения по предлагаемой схеме.
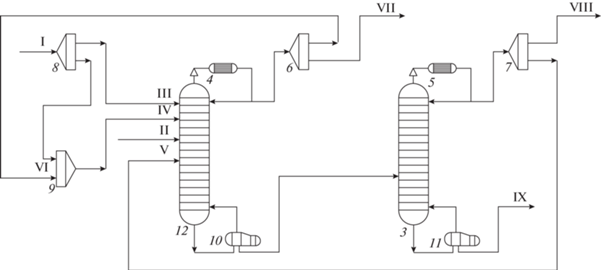
Моделирование начали с сопоставления расчетных данных с данными по содержанию углеводородных компонентов в выделяемых фракциях и основными технологическими режимами действующей установки экстрактивной ректификации и десорбции. Сопоставительный анализ данных табл. 5–8 показывает удовлетворительное совпадение рассчитанных данных промышленным.
Таблица 5.
Результаты моделирования состава изопентановой фракции
Компонент | Исходные значения, мас. % | Результаты расчета, мас. % |
---|---|---|
Н-пентан | 3.29 | 3.15 |
Σ изопентенов | 4.47 | 4.06 |
α-изопентен | 0.63 | 1.32 |
γ-изопентен | 3.82 | 2.64 |
β-изопентен | 0.02 | 0.10 |
Изопрен | 0.006 | 0 |
Транс-пиперилен | 0.00015 | 0 |
Цис-пиперилен | 0.00015 | 0 |
Изо-бутан | 0.02 | 0.02 |
Н-бутан | 0.02 | 0.02 |
ΣC4 | 0.04 | 0.03 |
∑н-пентенов | 0.12 | 0.07 |
Изопентан | 91.65 | 92.19 |
Неопентан | 0.35 | 0.41 |
ЦПД | 0 | 0 |
ДМФА | 0.01 | 0.07 |
Таблица 6.
Результаты моделирования параметров колонны К-1,2
Параметр | Исходные значения |
Результаты расчета |
---|---|---|
Tверх К-1,2, °С | 44 | 43.8 |
Tкуб К-1,2, °С | 123 | 117 |
Pверх К-1,2, кгс/см2 | 0.7 | 0.7 |
Pкуб К-1,2, кгс/см2 | 1.3 | 1.7 |
Флегмовое число К-1,2 | 3.1 | 3.1 |
Таблица 7.
Результаты моделирования состава изопентеновой фракции
Компонент | Исходные значения, мас. % |
Результаты расчета, мас. % |
---|---|---|
Н-пентан | 0.66 | 0 |
Σ изопентенов | 84.35 | 84.90 |
α-изопентен | 27.91 | 26.73 |
γ-изопентен | 0.02 | 0 |
β-изопентен | 56.42 | 58.17 |
Изопрен | 6.42 | 6.02 |
Транс-пиперилен | 0.76 | 0.71 |
Цис-пиперилен | 0.76 | 0.71 |
Изо-бутан | 0 | 0 |
Н-бутан | 0 | 0 |
ΣC4 | 0 | 0 |
∑н-пентенов | 6.91 | 7.66 |
Изопентан | 0.07 | 0 |
Неопентан | 0 | 0 |
ЦПД | 0.1 | 0 |
ДМФА | 0 | 0 |
Таблица 8.
Результаты моделирования параметров колонны десорбции К-3
Параметр | Исходные значения |
Результаты расчета |
---|---|---|
Tверх К-3, °С | 40 | 38 |
Tкуб К-3, °С | 161 | 157 |
Pверх К-3, кгс/см2 | 0.05 | 0.05 |
Pкуб К-3, кгс/см2 | 0.5 | 0.5 |
Флегмовое число К-3 | 2.5 | 2.1 |
Первым этапом исследований явилось установление влияния расхода изопентановой фракции, подаваемой на орошение от 4 до 15 т/ч в смеси с ДМФА и их отношение на эффективность извлечения изопентенов. Диапазон соотношений расходов выбран от 1 : 1 до преобладания ДМФА к изопентановой фракции 9 : 1. Точка ввода смеси по рассматриваемой схеме располагалась на пять тарелок ниже (108 тарелка) от точки ввода ДМФА (113 тарелка), при этом нагрузка по сырью (40 т/ч), общий расход ДМФА (220 т/ч), расход флегмы колонны экстракции и десорбции, а также точки их ввода оставались неизменными. При моделировании технологической схемы с целью смешения компонентов перед вводом в колонну был выбран смеситель, предлагаемый программным обеспечением.
Из представленных данных по содержанию компонентов в изопентановой фракции (табл. 9) видно, что содержание изопентенов во всем представленном интервале расхода и соотношения компонентов смеси, подаваемой на орошение, находится на сопоставимом уровне. Увеличение расхода изопентановой фракции до 15 т/ч позволяет незначительно снизить содержание изопентенов в изопентановой фракции.
Таблица 9.
Эффективность разделения изопентан-изопентеновой фракции в колоннах экстракции–десорбции при смесевом орошении
Компонент/Параметр | Размерность | Значения | |
---|---|---|---|
Изопентановая фракция | Изопентеновая фракция | ||
GDMF(mix) : GMR | – | 1 : 1–9 : 1 | |
Nmix | – | 108–93 | |
GMR | т/ч | 4–15 | |
Изопентан | мас. % | 93.25–93.40 | 0 |
Σ изопентенов | мас. % | 2.83–3.13 | 84.62–84.97 |
Проведен расчет процесса разделения изопентан-изопентеновой фракции с увеличением потока флегмы на 10 т/ч (с 75 до 85 т/ч) в колонне экстракции при неизменных остальных режимных параметрах работы блока. Увеличение расхода изопентановой фракции в виде флегмы на 10 т/ч выбрано из соображений, что это значение сопоставимо с расходом изопентановой фракции, подаваемой на орошение в смеси с ДМФА 4–15 т/ч по предлагаемому решению. При этом содержание изопентенов в изопентановой фракции осталось на соизмеримом уровне с результатами действующей установки. Аналогичные результаты были получены и по содержанию изопентановой фракции.
Вторым этапом исследования явилось определения эффективности извлечения изопентенов при снижении точки ввода смеси в колонну с шагом 5 тарелок от начальной точки ввода (108, 103, 98, 93 тарелки).
Наибольшая степень извлечения изопентенов происходит при подаче смеси на 108 тарелку колонны (остаточное содержание изопентенов 2.83–2.86 мас. %), что позволяет увеличивать выход изопентеновой фракции до 15.3 т/ч. Увеличение содержания изопентенов в изопентановой фракции при подаче смеси на 98 и 93 тарелки колонны было связано с подачей рециклового потока обогащенного изопентенами с колонны десорбции на 98 тарелку колонны экстракции (внутренний рецикл) для обогащения ДМФА изопентенами.
На третьем этапе исследования расход внутреннего рецикла с колонны десорбции был снижен с 2.8 до 0.5 т/ч, а точка ввода перенесена с 98 на 85 тарелку колонны экстракции. Расчеты по оценке степени извлечения изопентенов были повторно воспроизведены при подаче смеси на 93 тарелку колонны (таблица 10). В этом случае остаточное содержание изопентенов составило 0.49–0.67 мас. %.
Таблица 10.
Эффективность разделения изопентан-изопентеновой фракции при смесевом орошении после совершенствования схемы потоков
Компонент/параметр | Размерность | Значения (изопентановая/изопентеновая фракция) | |||
---|---|---|---|---|---|
GDMF | т/ч | 220 | 215 | 210 | 200 |
Nmix | – | 93 | |||
GMR | т/ч | 4 | |||
Изопентан | мас. % | 97.85/0.70 | 97.79/0 | 96.83/0 | 94.90/0 |
Σ изопентенов | 0.67/81.46 | 0.71/82.24 | 1.03/83.06 | 1.87/84.52 | |
Q | ГДж/ч | 56.6 | 55.8 | 55.1 | 53.6 |
GMR | т/ч | 8 | |||
Изопентан | мас. % | 98.01/0.74 | 97.82/0 | 96.83/0 | 94.89/0 |
Σ изопентенов | 0.60/81.29 | 0.67/82.25 | 1.01/83.23 | 1.88/84.51 | |
Q | ГДж/ч | 57.9 | 57.1 | 56.4 | 54.9 |
GMR | т/ч | 15 | |||
Изопентан | мас. % | 98.25/0.49 | 97.84/0 | 96.81/0 | 94.88/0 |
Σ изопентенов | 0.49/78.38 | 0.62/82.34 | 0.99/83.11 | 1.90/84.46 | |
Q | ГДж/ч | 60.2 | 59.5 | 58.7 | 57.3 |
Оптимальной точкой подачи смеси принята тарелка 93, т.к. в этом случае с одной стороны существенно снижается содержание изопентенов, с другой, происходит попадание изопентана до 0.74 мас. % в изопентеновую фракцию. Исключить вероятность проскока изопентана и обеспечить содержание изопентенов на минимальном уровне возможно снижением расхода ДМФА до 215 т/ч, дальнейшее снижение расхода ДМФА позволяет снизить энергопотребление ребойлера, но в этом случае возрастает остаточное содержание изопентенов. Очевидно, что увеличить степень разделения изопенан-изопентеновой фракции до следовых количеств изопентенов в изопентановой фракции возможно при увеличении расхода изопентановой фракции в смеси с ДМФА, что повлечет существенный рост энергозатрат.
Извлечение изопентенов при экстрактивной ректификации путем орошения колонны экстракции изопентановой фракцией 8 т/ч на тарелку 93 с предварительным смешением с ДМФА позволяет увеличить отбор изопентенов на 0.8–0.9 т/ч, являющимся дополнительным сырьем второй стадии дегидрирования для получения изопрена.
Потребление тепла на обогрев ребойлера колонны экстракции по предлагаемому способу показали сопоставимые энергозатраты (по исходной схеме – 56.0 ГДж/ч, рецикл 4 т/ч изопентановой фракции – 55.8 ГДж/ч, 8 т/ч изопентановой фракции – 57.1 ГДж/ч), соответственно затраты по совершенствованию установки разделения изопентан-изопентеновой фракции будут связаны с капитальными затратами на монтаж линии орошения и на установку смесителя.
В табл. 11 приведены сравнительные результаты по содержанию выделяемых фракций по действующей технологической схеме, полученной расчетным методом и по предлагаемому варианту. В результате совершенствования изопентановая фракция обогащается основным компонентом на 5.6 мас. % и снижается содержание изопентенов на 3.35 мас. %. Это позволяет увеличить выход изопентеновой фракции на 1.4 т/ч (табл. 12). Технологические параметры по колонне экстракции остались на сопоставимом уровне, но в колонне десорбции увеличилось энергопотребление на 12.5% на обогрев ребойлера и на 29.5% на охлаждение дистиллята.
Таблица 11.
Результаты моделирования состава выделяемых фракций
Компонент | Изопентановая фракция | Изопентеновая фракция | ||
---|---|---|---|---|
Исходные значения по расчету, мас. % |
Результаты расчета по предлагаемому решению, мас. % |
Исходные значения по расчету, мас. % |
Результаты расчета по предлагаемому решению, мас. % |
|
Н-пентан | 3.15 | 0.92 | 0 | 4.04 |
Σ изопентенов | 4.06 | 0.71 | 84.90 | 82.24 |
α-изопентен | 1.32 | 0.70 | 26.73 | 3.49 |
γ-изопентен | 2.64 | 0.01 | 0 | 26.33 |
β-изопентен | 0.10 | 0 | 58.17 | 52.42 |
Изопрен | 0 | 0 | 6.02 | 5.41 |
Транс-пиперилен | 0 | 0 | 0.71 | 0.64 |
Цис-пиперилен | 0 | 0 | 0.71 | 0.64 |
Изо-бутан | 0.02 | 0.02 | 0 | 0 |
Н-бутан | 0.02 | 0.02 | 0 | 0 |
∑н-пентенов | 0.07 | 0 | 7.66 | 7.01 |
Изопентан | 92.19 | 97.79 | 0 | 0 |
Неопентан | 0.41 | 0.43 | 0 | 0 |
ДМФА | 0.07 | 0.09 | 0 | 0 |
Таблица 12.
Результаты моделирования режимных параметров колонн К-1,2 и К-3
Режимный параметр | Колонна экстракции | Колонна десорбция | ||
---|---|---|---|---|
Исходные значения по расчету |
Результаты расчета по предлагаемому решению | Исходные значения по расчету |
Результаты расчета по предлагаемому решению | |
Флегмовое число | 3.10 | 2.80 | 2.02 | 1.73 |
Gорошение, т/ч | 75 | 75 | 32 | 32 |
Gдистиллята, т/ч | 24.2 | 22.8 | 15.8 | 17.2 |
Gкуб, т/ч | 236 | 232 | 220 | 215 |
Pверх, кгс/см2 | 0.72 | 0.72 | 0.05 | 0.05 |
Pкуб, кгс/см2 | 1.7 | 1.7 | 0.1 | 0.1 |
Tверх, °С | 43.8 | 43.9 | 38 | 40 |
Tкуб, °С | 117 | 117 | 157 | 157 |
Qdef, ГДж/ч | 33.1 | 33.9 | 21.0 | 27.2 |
Qreb, ГДж/ч | 56.0 | 55.8 | 39.3 | 44.2 |
Nсырье | 74 | 74 | 12 | 12 |
NDNF/NDMF(mix) | 113/– | 113/93 | – | – |
ЗАКЛЮЧЕНИЕ
В результате исследования показана возможность доизвлечения изопентенов из изопентановой фракции путем организации орошения колонны экстракции смесью изопентановой фракцией с ДМФА с применением аппарата-смесителя.
На основе расчетных исследований Honeywell UniSim Desing определена оптимальная схема подачи смеси для очистки изопентановой фракции, при которой остаточное содержание изопентенов составит 0.67 мас. %.
ОБОЗНАЧЕНИЯ
K | колонна экстрактивной ректификации и десорбции |
N | номер тарелки ввода потоков |
Q | потребление и расход энергии, ГДж/ч |
P | давление, кгс/см2 |
T | температура, °C |
G | расход, т/ч |
x | содержание компонентов, мас. % |
ИНДЕКСЫ
Список литературы
Тухватшин В.С., Насыров И.Ш., Беланогов И.А., Талипов Р.Ф. Синтез изопрена: монография. Уфа: РИЦ БашГУ. 2017.
Петрова Е.М., Юнусова Л.М., Богачева Т.М., Касьянова Л.З., Ахмедьянова Р.А., Лиакумович А.Ч. Влияние основного компонента и промоторов железооксидного катализатора на показатели процесса второй стадии дегидрирования изопентана // Вестн. Казан. технол. унив. 2013. Т. 16. № 22. С. 191.
Платэ Н.А., Сливинский Е.В. Основы химии и технологии мономеров. М.: “Наука/Интерпериодика”, 2002.
Касьянова Л.З., Даминев Р.Р., Исламутдинова А.А. Синтез изопрена-мономера методом двухстадийного дегидрирования изопентана // Башк. хим. журн. 2012. Т. 19. № 4. С. 205.
Shevlyakov F.B., Umergalin T.G., Shurupov O.K., Zakharov V.P., Nasyrov I.S. Improving the technological scheme of isolation of butane-butylene fraction by chemisorption using tubular turbulent apparatus. Theor. Found. Chem. Eng. 2019. V. 53. № 5. P. 517. [Шевляков Ф.Б., Умергалин Т.Г., Шурупов О.К., Захаров В.П., Насыров И.Ш. Совершенствование технологической схемы выделения бутан-бутиленовой фракции методом хемосорбции с использованием трубчатого турбулентного аппарата // Теор. осн. хим. технол. 2019. Т. 53. № 5. С. 517].
Каеем Д.Х., Умергалин Т.Г., Шевляков Ф.Б., Захаров В.П. К уменьшению потерь углеводородных компонентов попутных нефтяных газов // Изв. высш. учебн. завед., хим. хим. технол. 2009. Т. 52. Вып. 12. С. 129.
Данилов Ю.М., Мухаметзянова А.Г., Дьяконов Г.С. Интенсификация процесса перемешивания в малогабаритных трубчатых турбулентных аппаратах // Хим. пром-сть. сегодня. 2010. № 9. С. 50.
Захаров В.П., Минскер К.С., Шевляков Ф.Б., Берлин А.А., Алексанян Г.Г., Рытов Б.Л., Коноплев А.А. Интенсификация газожидкостных процессов в трубчатых турбулентных аппаратах // Журн. прикл. хим. 2004. Т. 77. № 11. С. 1822.
Tsadkin M.A., Badikova A.D. Industrial trials of a new-generation contactor for the process of the sulfuric-acid alkylation of isobutane with olefins // Theor. Found. Chem. Eng. 2018. Т. 52. № 2. P. 246 [Цадкин М.А., Бадикова А.Д. Промышленные испытания контактора нового поколения для процесса сернокислотного алкилирования изобутана олефинами // Теор. осн. хим. технол. 2018. Т. 52. № 2. С. 225].
Шевляков Ф.Б., Умергалин Т.Г., Захаров В.П. Использование трубчатого турбулентного аппарата в нефтегазовых и химических процессах. Уфа: Башкирский государственный университет, 2018.
Шевляков Ф.Б., Насыров И.Ш., Умергалин Т.Г. Влияние гидродинамического режима на восстановление компонентов медно-аммиачного раствора // Сетевое издание “Нефтегазов. дело”. 2020. № 5. С. 107.
Шевляков Ф.Б., Насыров И.Ш., Умергалин Т.Г. Смешение медно-аммиачного и водно-аммиачного раствора в производстве бутадиена-1,3 // Сетевое издание “Нефтегазов. дело”. 2020. № 6. С. 186.
Sanjay Pralhad Shirsat. Separation of isobutyl alcohol and isobutyl acetate by extractive distillation and pressure-swing distillation: Simulation and optimization // Separat. and Purif. Technol. 2015. V. 154. P. 366.
Onkar A. Deorukhkar, Amit Katariya, Yogesh S. Mahajan. Purification of tetrahydrofuran from its aqueous azeotrope by extractive distillation: Validation of model and simulation. Separat // Sci. and Technol. 2018. V. 54. P. 1.
Yang Xiaojian, YIN Xuan, Ouyang Pingkai. Simulation of 1,3-Butadiene Production Process by Dimethylfomamide Extractive Distillation // Chinese J. Chem. Eng. 2009. V. 17(1). P. 27.
Honghai Wang, Xiaoying Cui, Chunli Li, Jing Fang. Separation of Ethyl Acetate-Dichloromethane-Ethanol by Extractive Distillation: Simulation and Optimization // Chem. Eng. Technol. 2013. V. 36. № 4. P. 627.
Xiao-Ling Yang, Jeffrey D. Ward. Extractive Distillation Optimization using Simulated Annealing and a Process Simulation Automation Server // Ind. & Eng. Chem. Res. 2018. V. 57(32). P. 1.
Brondani L.B., Flores G.B., Soares R.P. Modeling and simulation of a benzene recovery process by extractive distillation // Braz. J. Chem. Eng. 2015. V. 32. № 1. P. 283.
Jun Qi, Qingjun Zhang, Xiaoyan Han, QingpengWu, Yafang Li, Qunsheng Li. Vapor-liquid equilibrium experiment and process simulation of extractive distillation for separating diisopropyl ether-isopropyl alcohol using ionic liquid. J. Molecular Liquids. 2019. V. 293. P. 1.
Hee Chul Woo, Young Han Kim. Solvent selection for extractive distillation using molecular simulation. American Institute of Chemical Engineers. 2019. V. 65. № 9. P. 1.
Luana Ferreira da Silva, Rafael da Silva Eustácio, Miguel Rascado Fraguas Neto, Camila de Souza Silva, Marisa Fernandes Mendes, Cristiane de Souza Siqueira Pereira. Simulation of the Extractive Distillation Process of Ethanol-Water- Propylene Glycol System. Journal of Thermodynamics & Catalysis. 2017. V. 8. № 3. P. 1.
Зиятдинов Н.Н., Рыжов Д.А., Лаптева Т.В., Курбатов В.А. Поиск энергосберегающих режимов работы установки разделения изоамилен-изопреновой фракции производства изопрена // Вестник Казан. Технолог. унив-та. 2009. № 6. С. 249.
Белов Г.В., Воронин Г.Ф., Куценок И.Б. Программа расчета фазовых диаграмм бинарных систем. Свид. о гос. регистрации программ для ЭВМ 2014617822. РФ. 2014.
Дополнительные материалы отсутствуют.
Инструменты
Теоретические основы химической технологии