Теоретические основы химической технологии, 2022, T. 56, № 5, стр. 518-523
Технологическая схема переработки литий-марганцевого элемента питания с использованием HDES Aliquat 336/ментол
А. В. Кожевникова a, Н. А. Милевский a, И. В. Зиновьева a, Ю. А. Заходяева a, *, А. А. Вошкин a
a Институт общей и неорганической химии им. Н.С. Курнакова РАН
Москва, Россия
* E-mail: yz@igic.ras.ru
Поступила в редакцию 10.06.2022
После доработки 11.06.2022
Принята к публикации 14.06.2022
- EDN: WLEYLX
- DOI: 10.31857/S0040357122050086
Аннотация
Впервые предложен гидрометаллургический метод выделения и разделения Li(I), Mn(II), Al(III) и Fe(III) из катодного материала литий-марганцевого элемента питания, основанный на сочетании процессов выщелачивания и жидкостной экстракции с использованием глубокого эвтектического растворителя. Экстракционная система на основе глубокого эвтектического растворителя Aliquat 336/ментол (1 : 1) была использована в процессе извлечения ионов металлов из солянокислого раствора выщелачивания катодного материала. Предложенная технологическая схема переработки литий-марганцевого элемента питания представляет возможность достаточно полного разделения Li, Mn, Al и Fe.
ВВЕДЕНИЕ
Запасы мирового литийсодержащего сырья, пригодного для переработки, сконцентрированы в нескольких месторождениях, что осложняет логистику поставок и возможности увеличения объемов производства [1]. Данная проблема находит различные пути решения. Одновременно с развитием технологий переработки природного сырья важным направлением является разработка технологий замкнутого цикла, предполагающая переработку отработанного сырья [2] с целью возврата ресурсов в цикл производства. В случае литийсодержащего вторсырья одной из основных групп отходов, подлежащих переработке, являются литийсодержащие химические источники тока, на производство которых поступает около 40% всего оборота лития [3]. При этом, переработка такого типа отходов важна не только по причине возобновления ценного сырья, но и для минимизации образования самих отходов, разгрузке мусорных полигонов.
Литийсодержащие химические источники тока представлены в широком диапазоне составов катодов и анодов, что увеличивает требования к сортировке отходов [4]. В случае литий-ионных батарей уже имеются успехи в создании схем экстракционного разделения растворов выщелачивания, содержащих практически все возможные элементы из состава катодов (Li, Co, Mn, Fe, Ni) [5, 6]. В том числе ранее для осуществления одной из таких схем разделения нашей группой был применен гидрофобный глубокий эвтектический растворитель (HDES) на основе Aliquat 336/ментол [7]. Однако существуют другие типы литийсодержащих батарей, в состав которых входит металлический литий. К таким батареям относятся неперезаряжаемые литиевые элементы питания. Среди литиевых элементов питания наиболее распространены литий-марганцевые батареи по причине их отличных эксплуатационных свойств [8]. После отработки такие батареи не могут быть перезаряжены и использованы повторно, что обуславливает необходимость их переработки.
Экстракция уже успешно применяется в области разделения растворов выщелачивания литий-ионных аккумуляторов различных составов [9]. Обширные исследования в области глубоких эвтектических растворителей позволяют использовать данный тип систем не только для выщелачивания твердых отходов [10–12], но и применять в качестве экстрагентов их гидрофобный подкласс [13]. Ранее предложенный нами HDES на основе Aliquat 336/ментол отвечает всем требованиям промышленного экстрагента, и имеет ряд конкретных преимуществ, одним из которых является отсутствие летучего органического растворителя, что дополнительно снижает экологическую нагрузку на окружающую среду и повышает безопасность на производстве.
Таким образом, целью данной работы является разработка и реализация технологической схемы переработки литий-марганцевого элемента питания с последующим выделением элементов состава в индивидуальном виде.
ЭКСПЕРИМЕНТАЛЬНАЯ ЧАСТЬ
Образцы катода, используемые в данном исследовании, были взяты из отработанной неперезаряжаемой литиевой батареи CR123A торговой марки WINPOWA (Китай). Перед началом работы батарея была разряжена, затем разобрана на составляющие: катод, сепаратор и металлический корпус.
В данном типе батарей катод состоит из порошка и сетки, которые были механически отделены друг от друга. Их состав был определен методом рентгенофлуоресцентного анализа (РФА) с помощью вакуумного волнодисперсионного рентгенофлуоресцентного спектрометра СПЕКТРОСКАН-МАКС GVM (Спектрон, Россия).
Для проведения экспериментов по выщелачиванию катод был измельчен и растворен при 80°С в соляной кислоте (Aldosa, “х. ч.”) с концентрацией 2 и 6 моль/л при массовом соотношении твердое : жидкость = 1 : 25 в течение 1 и 6 ч.
В качестве экстрагента для разделения ионов металлов в выщелачивающем растворе был использован HDES на основе Aliquat 336 (Acros Organics, чистота 99%) и L-ментола квалификации “х. ч.” в мольном соотношении 1 : 1. Взвешенные на аналитических весах AND HR-100AZ (Япония) реагенты помещали в пластиковые пробирки объемом 50 мл. Для образования глубокого эвтектического растворителя пробирки помещали в термостатированный шейкер Enviro-Genie SI-1202 (США) при температуре 70°C и перемешивали при 35 об/мин в течение 30 мин до образования жидкой смеси.
Все эксперименты по изучению экстракции проводили при 25°С в градуированных центрифужных пробирках в термостатируемом шейкере Scientific Industries Enviro-Genie при скорости вращения 35 об/мин до достижения термодинамического равновесия (30 мин). Объемное соотношение водной фазы и фазы HDES составило 5 : 1, соответственно. Для приготовления модельного раствора хлорида алюминия(III) (чистота >99%) его точную навеску растворяли в дистиллированной воде.
После перемешивания образцы центрифугировали при 2500 об/мин в течение 10 мин до полного разделения фаз на центрифуге SIA ELMI CM-6MT (Латвия). Затем фазы разделяли в делительных воронках. Концентрацию ионов металлов в растворе выщелачивания до и после экстракции определяли методом оптической эмиссионной спектроскопии с индуктивно-связанной плазмой (ICP-OES) на приборе Thermo Scientific ICAP PRO XP (США). Концентрации ионов металлов в фазе HDES были рассчитаны по математическому балансу.
Представленные экспериментальные данные являются результатом серии экспериментов и обработаны методами математической статистики.
ОБСУЖДЕНИЕ РЕЗУЛЬТАТОВ
Характеризация катодного материала отработанной литиевой батареи
В качестве катодного материала в литиевых элементах питания наиболее распространенным является MnO2, однако, могут быть использованы FeS2, CuS, (CF)n, FeF3 и др. В качестве анода в данном типе батарей содержится металлический литий, который при разрядке полностью переходит в катод [14].
На рис. 1 показан внешний вид поверхности катодной сетки и катодного порошка.
Состав поверхности данных материалов определяли методом РФА (табл. 1). Данный метод не позволяет анализировать атомы лития и кислорода, поэтому массовые проценты в таблице указаны без их учета. Исходя из полученных результатов, можно сказать, что основными элементами, содержащимися в данных материалах, являются Li, Mn, Al и Fe, а также следовые количества Si, K и Cu. Их содержание крайне мало, поэтому их извлечение нецелесообразно и в дальнейшем рассматриваться не будет.
Выщелачивание металлов из катода литиевой батареи и состав растворов выщелачивания
Выщелачивание металлов из катода раствором соляной кислоты проводили при условиях, представленных в табл. 2. В табл. 2 также приведены концентрации металлов и соляной кислоты в растворах выщелачивания.
Таблица 2.
Условия выщелачивания и состав растворов после растворения катода литиевой батареи в соляной кислоте
Условия выщелачивания | С, моль/л | |||||
---|---|---|---|---|---|---|
Li | Al | Mn | Fe | HCl | ||
1 ч | 2 моль/л HCl | 0.2835 | 0.1436 | 0.2093 | 0.0002 | 1.25 |
6 моль/л HCl | 0.2918 | 0.1323 | 0.2924 | 0.0002 | 5.00 | |
6 ч | 2 моль/л HCl | 0.2565 | 0.1194 | 0.2752 | 0.0003 | 1.25 |
6 моль/л HCl | 0.2802 | 0.1245 | 0.2391 | 0.0002 | 5.00 |
Как показано в табл. 2, влияние времени и концентрации соляной кислоты на выщелачивание Li, Mn, Al и Fe оказалось незначительным. Следует отметить, что во всех случаях сетка растворялась полностью. Неоднозначное поведение металлов при выщелачивании, а именно некоторое различие их концентраций в растворах, вероятно, связано с неоднородностью распределения элементов в образцах твердой фазы. Целесообразно использовать менее концентрированную соляную кислоту, при этом увеличение времени выщелачивания до 6 ч не является необходимым. Таким образом, наиболее благоприятными условиями выщелачивания являются: С(HCl) = 2 моль/л; Т = = 80°С; твердое : жидкость = 1 : 25, 1 ч (табл. 2). Дальнейшие исследования по разделению ионов Li(I), Mn(II), Al(III) и Fe(III) проводили из раствора выщелачивания, содержащего (моль/л): Li(I) 0.2835; Mn(II) 0.2093; Al(III) 0.1436; Fe(III) 0.0002; HCl 1.25.
Экстракция Li(I), Mn(II), Al(III) и Fe(III) в системе с HDES Aliquat 336/ментол
Одним из основных параметров, влияющих на эффективность экстракции ионов металлов, является концентрация HCl. Ранее в работе [7] была представлена зависимость степени извлечения индивидуальных ионов металлов от концентрации соляной кислоты в диапазоне от 0.01 до 6 моль/л. Как было показано, степень извлечения железа не зависит от концентрации соляной кислоты и составляет 99% во всем исследованном диапазоне, поэтому выделение ионов Fe(III) из раствора выщелачивания проводили без введения в смесь дополнительных компонентов. Степень извлечения Fe(III) составила 97.92%, при этом остальные металлы не извлекаются в фазу HDES при заданных условиях.
Увеличение эффективности извлечения ионов Mn(II) происходит при повышении концентрации кислоты до 3 моль/л и снижении исходной концентрации металла до 0.01 моль/л [7]. На второй стадии экстракции концентрация соляной кислоты в растворе выщелачивания была доведена до 3 моль/л. Степень извлечения ионов Mn(II) составила 27.04%, остальные металлы при этом не извлекаются в фазу HDES. Остаточная концентрация соляной кислоты составляет 2.4760 моль/л.
После селективного извлечения ионов Mn(II) в растворе выщелачивания содержатся ионы Li(I) и Al(III). Ранее было установлено, что ионы Li(I) не экстрагируются в фазу HDES даже при увеличении концентрации соляной кислоты до 6 моль/л. Для того, чтобы установить поведение ионов Al(III) в зависимости от концентрации HCl, нами была проведена серия экспериментов на модельных растворах, содержащих 0.005 моль/л ионов Al(III) (рис. 2).
Согласно рисунку 2, видно, что увеличение содержания HCl приводит к увеличению степени извлечения ионов Al(III). Таким образом, для эффективного выделения ионов Al(III) необходимо повышение концентрации соляной кислоты до 5 моль/л. При проведении экстракции на реальном растворе выщелачивания степень извлечения алюминия составила 88.53%. При этом остаточная концентрация HCl составила 3.1 моль/л.
На основании вышеприведенных данных может быть предложена схема переработки литиевых батарей, содержащих ионы Li(I), Mn(II), Al(III) и Fe(III) (рис. 3). Катод растворяли в 2 М растворе HCl при 80°С в течение 1 ч. Экстракционное разделение металлов осуществляли с использованием HDES Aliquat 336/ментол. Процесс реализован в экстракционном каскаде смесителей-отстойников в противоточном режиме.
Рис. 3.
Схема переработки литий-марганцевых элементов питания, содержащих ионы Li(I), Mn(II), Al(III) и Fe(III) на каскаде смесителей-отстойников в режиме противоточной экстракции.
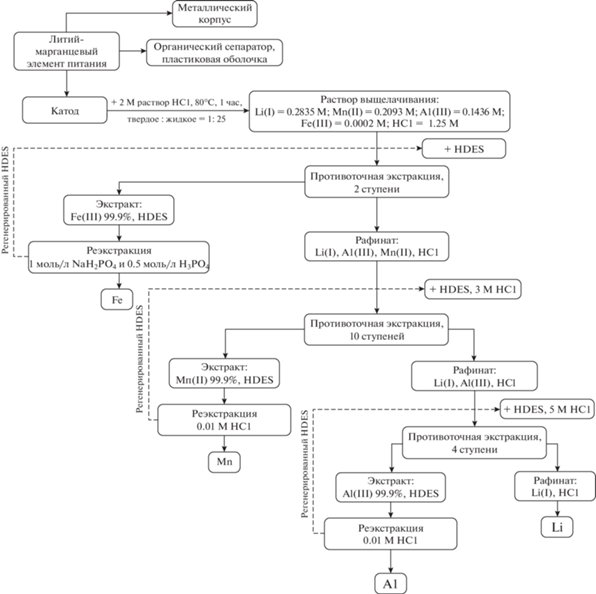
Раствор выщелачивания подается на первую ступень каскада, состоящую из 2 экстракторов. После экстракции фаза HDES содержит Fe(III) чистотой 99.9%, водная фаза – ионы Li(I), Mn(II), Al(III). Извлечение ионов Fe(III) из органической фазы может быть достигнуто за одну стадию реэкстракции в условиях: 1 моль/л NaH2PO4 и 0.5 моль/л H3PO4, О/В = 1, Т = 25°С, время контакта фаз = 30 мин. После очистки HDES может быть повторно использован в качестве экстрагента, а железо может быть повторно использовано после регенерации путем осаждения [15] или электролиза [16].
Концентрацию HCl в рафинате после первой ступени экстракции увеличивают до 3 М. Раствор подается на разделение во вторую часть каскада, состоящую из 10 ступеней, что приводит к выделению марганца в фазу HDES с чистотой 99.9%. После экстракции полученный рафинат содержит ионы Li(I) и Al(III). Далее концентрацию HCl в водной фазе увеличивают до 5 М добавлением концентрированной HCl и подают на третью часть каскада, состоящую из 4 ступеней. После экстракции водная фаза содержит только ионы Li(I), при этом фаза HDES насыщена ионами Al(III) с чистотой 99.9%. Извлечение марганца и алюминия из органической фазы можно провести в одну стадию реэкстракции 0.01 М раствором HCl с эффективностью примерно 99%. В дальнейшем металлы могут быть выделены простым осаждением, а регенерированные фазы повторно направлены в экстракционный каскад.
На основании полученных данных можно сделать вывод о возможности достаточного полного разделения Li, Mn, Al и Fe гидрометаллургическим методом.
ЗАКЛЮЧЕНИЕ
В настоящей работе предложен гидрометаллургический метод на основе выщелачивания и жидкостной экстракции для разделения ионов Li, Mn, Al и Fe. Выбраны оптимальные условия выщелачивания катодного материала: С(HCl) = = 2 моль/л; Т = 80°С; твердое : жидкость = 1 : 25, 1 ч. Применение глубокого эвтектического растворителя на основе Aliquat 336 и ментола позволило достаточно полно разделить основные ионы металлов из солянокислого раствора выщелачивания без введения дополнительных реагентов.
Таким образом, предложенный гидрометаллургический метод переработки катодного материала потенциально может быть использован не только для решения проблем утилизации литийсодержащих отходов, но и для возврата в производственный цикл основных компонентов катодов элементов питания. Предложенная схема позволяет выделить все металлы с высокой чистотой на каскаде смесителей-отстойников, работающем в режиме противоточной экстракции.
Исследование выполнено за счет гранта Российского научного фонда (проект № 20-13-00387). Исследования проводились с использованием оборудования ЦКП ФМИ ИОНХ РАН.
Список литературы
Tarascon J.-M. Is lithium the new gold? // Nature Chemistry. 2010. V. 2(6). P. 510–510. https://doi.org/10.1038/nchem.680
Yelatontsev D., Mukhachev A. Processing of lithium ores: Industrial technologies and case studies – A review // Hydrometallurgy. 2021. V. 201. P. 105578. https://doi.org/10.1016/j.hydromet.2021.105578
Gil-Alana L.A., Monge M. Lithium: Production and estimated consumption. Evidence of persistence // Resources Policy. 2019. V. 60. P. 198–202. https://doi.org/10.1016/j.resourpol.2019.01.006
Jung J.C.-Y., Sui P.-C., Zhang J. A review of recycling spent lithium-ion battery cathode materials using hydrometallurgical treatments // J. Energy Storage. 2021. V. 35. P. 102217. https://doi.org/10.1016/j.est.2020.102217
Chen X., Xu B., Zhou T., Liu D., Hu H., Fan S. Separation and recovery of metal values from leaching liquor of mixed-type of spent lithium-ion batteries // Separation and Purification Technology. 2015. V. 144. P. 197–205. https://doi.org/10.1016/j.seppur.2015.02.006
Shen X., Li B., Hu X., Sun C.-F., Hu Y.-S., Yang C., Liu H., Zhao J. Recycling Cathodes from Spent Lithium-Ion Batteries Based on the Selective Extraction of Lithium // ACS Sustainable Chemistry & Engineering. 2021. V. 9(30). P. 10196–10204. https://doi.org/10.1021/acssuschemeng.1c02493
Milevskii N.A., Zinov’eva I.V., Zakhodyaeva Yu.A., Voshkin A.A. Separation of Li(I), Co(II), Ni(II), Mn(II), and Fe(III) from hydrochloric acid solution using a menthol-based hydrophobic deep eutectic solvent // Hydrometallurgy. 2022. V. 207. P. 105777. https://doi.org/10.1016/j.hydromet.2021.105777
Park M.S., Yoon W.Y. Characteristics of a Li/MnO2 battery using a lithium powder anode at high-rate discharge // J. Power Sources. 2003. V. 114(2). P. 237–243. https://doi.org/10.1016/S0378-7753(02)00581-5
Jung J.C.-Y., Sui P.-C., Zhang, J. A review of recycling spent lithium-ion battery cathode materials using hydrometallurgical treatments // J. Energy Storage. 2021. V. 35. P. 102217. https://doi.org/10.1016/j.est.2020.102217
Zinov’eva I.v., Fedorov A.Ya., Milevskii N.A., Zakhodyaeva Yu.A., Voshkin A.A. Dissolution of Metal Oxides in a Choline Chloride–Sulphosalicylic Acid Deep Eutectic Solvent // Theoretical Foundations of Chemical Engineering. 2021. V. 55(4). P. 663–670. https://doi.org/10.1134/S0040579521040370
Peeters N., Binnemans K., Riaño S. Solvometallurgical recovery of cobalt from lithium-ion battery cathode materials using deep-eutectic solvents // Green Chemistry. 2020. V. 22(13). P. 4210–4221. https://doi.org/10.1039/D0GC00940G
Schiavi P.G., Altimari P., Branchi M., Zanoni R., Simonetti G., Navarra M.A., Pagnanelli F. Selective recovery of cobalt from mixed lithium ion battery wastes using deep eutectic solvent // Chemical Engineering J. 2021. V. 417. P. 129249. https://doi.org/10.1016/j.cej.2021.129249
Dwamena A. Recent Advances in Hydrophobic Deep Eutectic Solvents for Extraction // Separations. 2019. V. 6(1). P. 9. https://doi.org/10.3390/separations6010009
Wang L., Wu Z., Zou J., Gao P., Niu X., Li H., Chen L. Li-free Cathode Materials for High Energy Density Lithium Batteries // J. 2019. V. 3. P. 2086–2102. https://doi.org/10.1016/j.joule.2019.07.011
Fernandes A., Afonso J.C., Dutra A.J.B. Separation of nickel(II), cobalt(II) and lanthanides from spent Ni-MH batteries by hydrochloric acid leaching, solvent extraction and precipitation // Hydrometallurgy. 2013. V. 133. P. 37–43. https://doi.org/10.1016/j.hydromet.2012.11.017
Lupi C., Pasquali M. Electrolytic nickel recovery from lithium-ion batteries // Minerals Engineering. 2003. V. 16(6). P. 537–542. https://doi.org/10.1016/S0892-6875(03)00080-3
Дополнительные материалы отсутствуют.
Инструменты
Теоретические основы химической технологии