Теоретические основы химической технологии, 2023, T. 57, № 1, стр. 98-108
Анализ вариантов риформинга части топлива (на примере пропана) в смеси с отработавшим газом ДВС с целью добавки риформата в камеру сгорания
А. Б. Шигаров *
Институт катализа им Г.К. Борескова СО РАН
Новосибирск, Россия
* E-mail: shigarov@catalysis.ru
Поступила в редакцию 20.10.2022
После доработки 17.11.2022
Принята к публикации 17.11.2022
- EDN: BPEKAL
- DOI: 10.31857/S0040357123010128
Аннотация
Термохимическая рекуперация (ТХР) теплоты отработавших газов автомобильных двигателей внутреннего сгорания (ДВС) способствует экономии топлива и уменьшению вредных выбросов. Проведен численный анализ двух схем ТХР для ДВС на пропане. Обе схемы базируются на каталитическом риформинге 0.1–0.2 доли пропана с частью отработавших газов ДВС и последующей добавке водородсодержащих продуктов риформинга вместе с пропаном в камеру сгорания. В первой схеме риформинг проводится в адиабатическом реакторе, во второй – в трубчатом. При анализе варьировалась доля рецикла отработавшего газа 0.1–0.5 и его температура 470–690°С. Показаны преимущества второй схемы, которая позволяет достигать увеличения химической энтальпии топливной смеси на 1.9–3.6% при массовой доле водорода 0.3–0.9%. Для режима работы ДВС эффективной мощностью 30 кВт приводится расчет адиабатического и трубчатого риформера с катализатором Ni/Cr2O3/Al2O3.
ВВЕДЕНИЕ
Принцип термохимической рекуперации (ТХР) для двигателей состоит в том, что тепло отработавших газов, используется на эндотермическую конверсию основного либо дополнительного топлива в продукты с более высокой химической энтальпией, благодаря чему можно повысить эффективность использования исходного топлива [1–3]. Наиболее энергоемким вариантом в случае углеводородных топлив является их паровая конверсия в синтез–газ. Применительно к автомобильным двигателям внутреннего сгорания (ДВС) можно выделить два типа ТХР. Первый тип основан на использовании независимого источника водяного пара для проведения паровой конверсии. При втором типе ТХР используют рецикл горячего отработавшего газа, который смешивается с топливом и подается в каталитический риформер. В этом случае на катализаторе протекает паро-углекислотная конверсия топлива. В работах [1, 2] рассматривались вопросы технической реализации первого типа ТХР с использованием паровой конверсии метанола и этанола. В работе [3] было теоретически показано, что при втором типе ТХР для ДВС на природном газе при избытке воздуха 1.1–1.4 существует оптимальная доля рецикла отработавшего газа, которая зависит от ряда параметров.
Следует заметить, что даже без увеличения химической энтальпии топлива сами по себе небольшие добавки водорода или синтез-газа в камеру сгорания ДВС интенсифицируют процесс горения и позволяют стабильно работать при увеличении коэффициента избытка воздуха до 1.5–1.8. Это положительно сказывается на вредных выбросах и даже может приводить к экономии топлива на режимах малой мощности и холостом ходу (городской цикл). При этом для получения синтез-газа можно использовать метод воздушной конверсии топлива (экзотермический процесс) в адиабатическом реакторе. Этот подход был разработан и реализован на практике в работах [4, 5]. Однако при этом подходе не происходит рекуперации тепла, что ограничивает его эффективность.
Исследованием ТХР в автомобильных двигателях за счет риформинга топлива в смеси с отработавшим газом более 30 лет занимается группа Бирмингемского университета в Великобритании [6–8]. Было экспериментально показано, что ТХР позволяет снижать расход топлива и вредные выбросы на примере одноцилиндрового бензинового двигателя [6], двигателя с воспламенением однородной горючей смеси от сжатия, работающего на природном газе [7] и бензинового двигателя с прямым впрыском топлива [8]. В последние годы экспериментальными исследованиями ТХР с рециклом отработавшего газа применительно к судовому двигателю, работающему на сжиженном природном газе, занимается группа Уханьского университета в КНР [9, 10].
Пропан-бутан (сжиженный углеводородный газ) является в настоящее время широко используемым топливом для легковых автомобилей, микроавтобусов и малотоннажных грузовых автомобилей. Однако исследования по теме ТХР для автомобильных двигателей на пропан-бутане сравнительно малочисленны. В работе [11] представлен термодинамический анализ пароуглекислотной конверсии пропана применительно к ТХР тепла отработавших газов энергетического оборудования широкого профиля. Цикл экспериментальных исследований по влиянию добавок синтез-газа к пропан-бутану на работу автомобильных двигателей в условиях стендовых испытаний был выполнен группой Волгоградского государственного технического университета [12–14]. С целью определения области возможной термохимической рекуперации с применением катализаторов в работе [12] проводились измерения температуры отработавших газов на экспериментальном стенде с роторно-поршневым двигателем ВАЗ-311 и поршневым двигателем ВАЗ-11194 работающими на бензине и пропан-бутане. В работе [13] экспериментально показано, что для двигателя с искровым зажиганием происходит снижение межцикловой неидентичности рабочего процесса при замене бензина на пропан-бутан, а при добавке к пропан-бутановоздушной смеси синтез-газа этот положительный эффект проявляется еще сильнее. В работе [14] приводятся результаты стендовых испытаний двигателя ВАЗ-11194 на бензине, на пропан-бутане и на пропан-бутане с добавкой заранее приготовленного синтез–газа 5, 7 и 10% от массы топлива, что соответствовало массовой концентрации водорода 0.55, 0.77 и 1.1%. Измерение индикаторной работы проводилось при частоте вращения вала 2800 мин–1, степени открытия дроссельной заслонки 73% и стехиометрическом расходе воздуха. Авторами был сделан вывод о существовании оптимальной величины добавки 5–7% по массе синтез–газа (т.е. 0.55–0.77% по массе водорода) к пропан-бутану с точки зрения снижения вредных выбросов и увеличения мощности двигателя.
Итак, несмотря на полученные экспериментальные результаты о перспективности небольших добавок синтез-газа для автомобильных двигателей на пропан-бутане, пока еще не реализована на практике схема ТХР с рециклом отработавшего газа ДВС на пропан-бутане. Это частично объясняется недостатком теоретических исследований в данной области.
Цель данной работы состоит в анализе двух схем термохимической рекуперации с адиабатическим и трубчатым каталитическим генератором водородсодержащей смеси применительно к автомобильному двигателю, работающему на пропане. Обосновывается выбор таких параметров схемы как доля риформируемого пропана, доля отработавшего газа, посылаемого на риформинг, температура отработавшего газа. В качестве критериев выбора приемлемых параметров взяты доля водорода в топливной смеси, возможность выпадения углерода на катализаторе и выигрыш в химической энтальпии топлива. В заключении приводятся результаты расчета адиабатического и трубчатого каталитического риформера пропана для одного из режимов работы двигателя.
ТЕОРИЯ И МЕТОД РАСЧЕТА
Схемы частичного риформинга модельного топлива (пропана) в смеси с отработавшим газом двигателя. Поскольку в современных ДВС 4-го поколения автоматически поддерживается близкое к стехиометрическому соотношение расходов топлива и воздуха в камеру сгорания двигателя, то все расчеты были сделаны при коэффициенте избытка воздуха ${{\alpha }_{{air}}}$ = 1.01 (т.е. незначительном избытке кислорода). В таком случае процесс риформинга пропана с компонентами отработавшего газа (водяным паром и двуокисью углерода) при температуре 500–700°С на никелевом катализаторе будет протекать преимущественно с образованием синтез-газа (с небольшой добавкой метана) и иметь эндотермический характер. В зависимости от типа риформера можно предложить разные схемы интеграции риформера с камерой сгорания ДВС. Далее будут рассмотрены два варианта такой схемы для случаев адиабатического и трубчатого риформера соответственно.
Схема с адиабатическим риформером (рис. 1а). Входной поток пропана 1 делится на две части 2 и 3. Поток горячего отработавшего газа после камеры сгорания 6 также делится на две части 7 и 8. Поток пропана 2 смешивается с потоком 8 отработавшего газа и подается в адиабатический риформер 9. Выходящая из риформера смесь охлаждается в теплообменнике 10 с отводом водяного конденсата 11. Оставшийся поток пропана 3 смешивается с охлажденными продуктами его риформинга 12 и воздухом 4 и подается в камеру сгорания двигателя 5. Оставшаяся часть горячего отработавшего газа 7 в рамках этой схемы не используется и идет на выхлоп.
Рис. 1.
Схемы ТХР ДВС для адиабатического (a) и трубчатого (б) риформера. 1 – вход пропана; 2 – пропан на конверсию; 3 – пропан в камеру сгорания; 4 – вход воздуха; 5 – камера сгорания; 6 – выход отработавших газов; 7 – выхлопной газ; 8 – отработавший газ, забираемая на риформинг; 9 – объем риформера с катализатором; 10 – теплообменник для охлаждения риформата; 11 – выход водяного конденсата; 12 – вход охлажденных сухих продуктов риформинга в камеру сгорания ДВС; 13 – отработавший газ, используемый как теплоноситель; 14 – межтрубный объем риформера с теплоносителем.
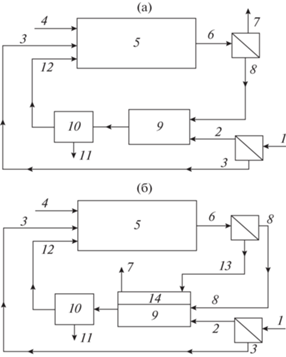
Следует отметить, что с учетом близкого к атмосферному давлению в основных узлах схемы, рецикл всего потока отработавшего газа практически невозможен из гидравлических ограничений для каталитического слоя и энергетических потерь при подаче смеси в камеру сгорания ДВС. Последний фактор объясняет необходимость охлаждения смеси после риформера. Однако использование не идущей на риформинг части отработавшего газа все же возможно через рекуперацию его теплоты посредством трубчатого риформера в рамках второй схемы ниже.
Схема с трубчатым риформером (рис. 1б). Как и в рассмотренной выше схеме входной поток пропана 1 делится на две части 2 и 3. Поток горячего отработавшего газа после камеры сгорания 6 также делится на две части 8 и 13. Но в отличие от первой схемы в трубчатый риформер подается оба потока отработавшего газа. Риформер представляет из себя трубчатый реактор со спутным направлением потоков. Внутреннее пространство труб 9 заполнено катализатором. Поток пропана 2 смешивается с потоком 8 отработавшего газа и подается внутрь труб с катализатором 9. Выходящая из риформера смесь охлаждается в теплообменнике 10 с отводом водяного конденсата 11. Оставшийся поток пропана 3 смешивается с охлажденными продуктами его риформинга 12 и воздухом 4 и подается в камеру сгорания двигателя 5. В межтрубное пространство риформера 14 подается теплоноситель – оставшаяся часть отработавшего газа 13, которая передает тепло катализатору внутрь труб для поддержания эндотермического процесса конверсии пропана. Далее отдавший часть тепла газ 7 выбрасывается в атмосферу.
Математическая модель и метод расчета риформера и схем ТХР. Известно [15], что процесс парового риформинга пропана на высокодисперсном Ni/Cr2O3/Al2O3 катализаторе протекает с большой скоростью уже при температурах 280–320°С через следующие реакционные стадии:
(1)
$\begin{gathered} {{{\text{С}}}_{3}}{{{\text{Н}}}_{8}} + 6{{{\text{Н}}}_{2}}{\text{О}} \Rightarrow 3{\text{С}}{{{\text{О}}}_{2}} + 10{{{\text{Н}}}_{2}}~ \\ \Delta H_{{298}}^{0} = 385{\text{ }}{{{\text{кДж}}} \mathord{\left/ {\vphantom {{{\text{кДж}}} {{\text{моль}}}}} \right. \kern-0em} {{\text{моль}}}}, \\ \end{gathered} $(2)
$\begin{gathered} {\text{С}}{{{\text{О}}}_{2}} + 4{{{\text{Н}}}_{2}} \Leftrightarrow {\text{С}}{{{\text{Н}}}_{4}} + 2{{{\text{Н}}}_{2}}{\text{О}} \\ \Delta H_{{298}}^{0} = - 165{\text{ }}{{{\text{кДж}}} \mathord{\left/ {\vphantom {{{\text{кДж}}} {{\text{моль}}}}} \right. \kern-0em} {{\text{моль}}}}, \\ \end{gathered} $(3)
$\begin{gathered} {\text{С}}{{{\text{О}}}_{2}} + {{{\text{Н}}}_{2}} \Leftrightarrow {\text{СО}} + {{{\text{Н}}}_{2}}{\text{О}} \\ \Delta H_{{298}}^{0} = 41{\text{ }}{{{\text{кДж}}} \mathord{\left/ {\vphantom {{{\text{кДж}}} {{\text{моль}}}}} \right. \kern-0em} {{\text{моль}}}}.~ \\ \end{gathered} $Расчеты сделаны для одномерной 2-х фазной математической модели риформера с зернистым катализатором внутри труб и течением теплоносителя в межтрубном пространстве. Расчет тепловых процессов делали по 3-х температурной модели с использованием эффективных радиальных коэффициентов теплообмена. В качестве независимых переменных были взяты температура теплоносителя, реакционного газа и средняя температура катализатора по радиусу трубы. Уравнения математической модели риформера, константы термодинамического равновесия, кинетические параметры и формулы для расчета коэффициентов тепломассопереноса приведены в работе [16]. Кинетическое выражение для стадии парового риформинга пропана (1) на Ni/Cr2O3/Al2O3 задавали в виде:
(4)
${{W}_{{ref}}} = {{k}_{{ref}}}\exp \left( {{{ - {{E}_{{ref}}}} \mathord{\left/ {\vphantom {{ - {{E}_{{ref}}}} {RT}}} \right. \kern-0em} {RT}}} \right){{P}_{{{{{\text{C}}}_{{\text{3}}}}{{{\text{H}}}_{{\text{8}}}}}}}.$Учет внутридиффузионного торможения по пропану основывался на результатах работы [17]. Реакционные стадии метанирования (2) и шифт-реакции (3) рассматривались достаточно быстрыми (квазиравновесными) по отношению к стадии парового риформинга (1). Скорость этих стадий задавали формальными выражениями с учетом обратимости реакций:
(5)
$\begin{gathered} {{W}_{{met}}} = {{k}_{{met}}}P_{{{{{\text{H}}}_{{\text{2}}}}}}^{{}}\left[ {1 - \frac{{{{P}_{{{\text{C}}{{{\text{H}}}_{{\text{4}}}}}}}P_{{{{{\text{H}}}_{{\text{2}}}}{\text{O}}}}^{2}}}{{K_{{eq}}^{{met}}{{{\left( {{{P}_{{{{{\text{H}}}_{{\text{2}}}}}}}} \right)}}^{4}}{{P}_{{{\text{С}}{{{\text{O}}}_{{\text{2}}}}}}}}}} \right], \\ {{W}_{{sh}}} = {{k}_{{sh}}}P_{{{{{\text{H}}}_{{\text{2}}}}}}^{{}}\left[ {1 - \frac{{{{P}_{{{\text{CO}}}}}{{P}_{{{{{\text{H}}}_{{\text{2}}}}{\text{O}}}}}}}{{K_{{eq}}^{{sh}}{{P}_{{{{{\text{H}}}_{{\text{2}}}}}}}{{P}_{{{\text{С}}{{{\text{O}}}_{{\text{2}}}}}}}}}} \right]. \\ \end{gathered} $Метод расчета. При численном расчете тепловых и материальных балансов двух схем, приведенных на рис. 1 и уравнений математической модели каталитического риформера (адиабатического и трубчатого) применяли программный пакет на языке СИ собственной разработки в некоммерческой программной среде CodeBlocks. Для расчета риформеров применялся конечно-разностный метод с переменным шагом по длине для решения уравнений переноса в рамках модели реактора идеального вытеснения. Также был использован ряд итерационных процедур по составу потоков с учетом рецикла, а также по температуре катализатора (в случае трубчатого реактора). Расчеты термодинамического равновесия сделаны методом численного решения уравнений математической модели в риформере достаточно большой длины, чтобы на выходе практически достигалось тепловое равновесие между обоими потоками и термодинамическое равновесие по составу смеси при температуре выхода.
Критерии количественной оценки схем с риформингом части топлива (пропана). Для оценки термодинамической возможности образования углерода из равновесной газовой смеси использовали величину ${{\chi }_{C}}$, определяемую по формуле (6), в которую подставляли температуру и парциальные давления компонент на выходе риформера:
(6)
${{\chi }_{C}} = 10\ln \left( {\frac{{{{P}_{{{\text{CO}}}}}{{P}_{{{\text{CO}}}}}}}{{{{K}_{{eq}}}\left( T \right){{P}_{{{\text{C}}{{{\text{O}}}_{{\text{2}}}}}}}}}} \right),$При величине ${{\chi }_{C}}$ < 0 образование углерода с термодинамической точки зрения невозможно, при ${{\chi }_{C}}$ > 0 возможно.
Для оценки эффективности термохимической рекуперации использовали коэффициент, определяемый как относительное изменение полной химической энтальпии топливной смеси после ее частичного риформинга по отношению к исходному топливу (пропану).
(8)
${{\mu }_{{rec}}} = \left( {\frac{{V_{{{{{\text{H}}}_{{\text{2}}}}}}^{{{\text{out}}}}{{Q}_{{{{{\text{H}}}_{{\text{2}}}}}}} + V_{{{\text{CO}}}}^{{{\text{out}}}}{{Q}_{{{\text{CO}}}}} + V_{{{\text{C}}{{{\text{H}}}_{{\text{4}}}}}}^{{{\text{out}}}}{{Q}_{{{\text{C}}{{{\text{H}}}_{{\text{4}}}}}}} + V_{{{{{\text{C}}}_{{\text{3}}}}{{{\text{H}}}_{{\text{8}}}}}}^{{{\text{out}}}}{{Q}_{{{{{\text{C}}}_{{\text{3}}}}{{{\text{H}}}_{{\text{8}}}}}}} + (1 - {{\psi }_{{fuel}}})V_{{{{{\text{C}}}_{{\text{3}}}}{{{\text{H}}}_{{\text{8}}}}}}^{{{\text{in}}}}{{Q}_{{{{{\text{C}}}_{{\text{3}}}}{{{\text{H}}}_{{\text{8}}}}}}}}}{{V_{{{{{\text{C}}}_{{\text{3}}}}{{{\text{H}}}_{{\text{8}}}}}}^{{{\text{in}}}}{{Q}_{{{{{\text{C}}}_{{\text{3}}}}{{{\text{H}}}_{{\text{8}}}}}}}}} - 1} \right) \times 100\% .$РЕЗУЛЬТАТЫ РАСЧЕТОВ И ИХ ОБСУЖДЕНИЕ
Стендовые испытания ДВС на пропан-бутане показали [14], что максимальный положительный эффект наблюдается при массовой доле водорода по отношению к исходному топливу 0.55–0.77%. В соответствии со сделанными нами оценками этого показателя можно достичь при риформинге 10–20% исходного пропана, поэтому расчеты сделаны при двух значениях ${{\psi }_{f}}$ = 0.1 и 0.2. Анализ представленных выше схем ТХР основывался на двух сценариях расчета. В первом случае при фиксированной температуре отработавшего газа 640°С и постоянной доле конвертируемого пропана ${{\psi }_{f}}$ варьировали долю отработавшего газа ${{\varphi }_{{eg}}}$, возвращаемого на риформинг пропана. Во втором случае при фиксированной доле конвертируемого пропана ${{\psi }_{f}}$ и доле отработавшего газа, возвращаемого на риформинг ${{\varphi }_{{eg}}}$, варьировали температуру отработавшего газа в интервале 460–700°С. Оба сценария расчетов были сделаны отдельно для схемы с адиабатическим и трубчатым риформером. Все результаты расчетов на рис. 2–3 и в табл. 1–2 соответствуют термодинамическому равновесию смеси при температуре выхода из риформера с одним замечанием: в области возможного образования углерода по термодинамике (${{\chi }_{С}}$ > 0) предполагалось, что углерод в любом случае не образуется по кинетическим причинам, обусловленным свойствами катализатора. Также при расчете схем было принято упрощающее допущение, что температура смеси пропана с отработавшим газом ДВС на входе в риформер равна температуре отработавшего газа. Это является хорошим приближением (с точностью до нескольких градусов) с учетом того, что объемный расход пропана на входе в риформер не превышает 1–2% от общего расхода смеси.
Рис. 2.
Влияние доли ${{\varphi }_{{eg}}}$ возвращаемых на риформинг отработавших газов ДВС на температуру выхода из риформера ${{T}_{{{\text{out}}}}}$ и термодинамической критерий образования углерода ${{\chi }_{{\text{С}}}}$ (a); на коэффициент эффективности термохимической рекуперации ${{\mu }_{{{\text{rec}}}}}$ и массовую долю водорода в топливной смеси ${{x}_{{{{{\text{H}}}_{{\text{2}}}}}}}$ (б). Левее точки С термодинамически возможно образование углерода. Расчет схемы с адиабатическим риформером при температуре отработавшего газа 640°С и доле конвертируемого пропана ${{\psi }_{f}}$ = 0.1.
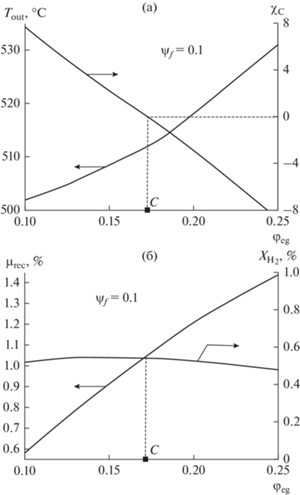
Рис. 3.
Влияние доли ${{\varphi }_{{eg}}}$ возвращаемых на риформинг отработавших газов ДВС на температуру выхода из риформера ${{T}_{{{\text{out}}}}}$ и термодинамической критерий образования углерода ${{\chi }_{{\text{С}}}}$ (a); на коэффициент эффективности термохимической рекуперации ${{\mu }_{{{\text{rec}}}}}$ и массовую долю водорода в топливной смеси ${{x}_{{{{{\text{H}}}_{{\text{2}}}}}}}$ (б). Левее точки С термодинамически возможно образование углерода. Расчет схемы с адиабатическим риформером при температуре отработавшего газа 640°С и доле конвертируемого пропана ${{\psi }_{f}}$ = 0.2.
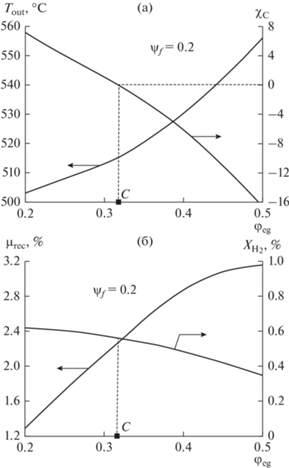
Таблица 1.
Результаты расчетов схемы с адиабатическим риформером. Доля конвертируемого пропана ${{\psi }_{f}}$ = 0.1, доля отработавшего газа, возвращаемого на риформинг ${{\varphi }_{{{\text{eg}}}}}$ = 0.18
№ | Tin, °C | Tout,°C | ΔТ,°C | ${{x}_{{{{{\text{H}}}_{{\text{2}}}}}}}$,% | ${{y}_{{{{{\text{H}}}_{{\text{2}}}}}}}$, % | ${{\chi }_{{\text{C}}}}$ | ${{\mu }_{{{\text{rec}}}}}$, % |
---|---|---|---|---|---|---|---|
1 | 464 | 435 | –34 | 0.29 | 4.5 | 3.9 | 0.14 |
2 | 502 | 450 | –52 | 0.35 | 5.3 | 3.2 | 0.33 |
3 | 555 | 475 | –80 | 0.42 | 6.4 | 2.1 | 0.61 |
4 | 587 | 490 | –97 | 0.47 | 7.0 | 1.2 | 0.79 |
5 | 640 | 509 | –131 | 0.54 | 8.0 | –0.7 | 1.09 |
6 | 698 | 550 | –148 | 0.62 | 9.1 | –1.1 | 1.30 |
Таблица 2.
Результаты расчетов схемы с трубчатым риформером. Доля конвертируемого пропана ${{\psi }_{f}}$ = 0.10, доля отработавшего газа, возвращаемого на риформинг ${{\varphi }_{{{\text{eg}}}}}$ = 0.16
№ | Tin, °C | Tout,°C | ΔТ,°C | ${{x}_{{{{{\text{H}}}_{{\text{2}}}}}}}$,% | ${{y}_{{{{{\text{H}}}_{{\text{2}}}}}}}$, % | ${{\chi }_{{\text{C}}}}$ | ${{\mu }_{{{\text{rec}}}}}$, % |
---|---|---|---|---|---|---|---|
1 | 465 | 455 | –10 | 0.37 | 5.6 | 4.2 | 0.33 |
2 | 508 | 490 | –18 | 0.48 | 7.2 | 2.6 | 0.72 |
3 | 570 | 540 | –30 | 0.63 | 9.3 | –1.6 | 1.37 |
4 | 606 | 570 | –36 | 0.69 | 10.1 | –5.7 | 1.69 |
5 | 640 | 600 | –40 | 0.71 | 10.4 | –10.9 | 1.89 |
6 | 692 | 650 | –42 | 0.71 | 10.4 | –20.4 | 2.05 |
Анализ схемы с адиабатическим риформером. На Рис. 2 показаны результаты расчета схемы с адиабатическим риформером при температуре смеси на входе в риформер (т.е. температуре отработавшего газа ДВС) 640°С и доле конвертируемого пропана 0.1. Доля рецикла отработавшего газа ${{\varphi }_{{eg}}}$ варьировалась в интервале 0.10–0.25. С увеличением величины ${{\varphi }_{{eg}}}$ адиабатическое охлаждение риформера ΔТ ожидаемо уменьшается, а температура выхода растет (рис. 2а) вместе с коэффициентом эффективности термохимической рекуперации ${{\mu }_{{rec}}}$ (рис. 2б). Термодинамическая возможность образования углерода ${{\chi }_{С}}$ > 0 сохраняется до тех пор, пока величина ${{\varphi }_{{eg}}}$ не достигнет 0.17 (точка С на рис. 2а). Итак, при риформинге 10% топлива (пропана) в смеси с 17–25% отработавшего газа с температурой 640°С расчетный выигрыш в химической энтальпии топлива равен 1.0–1.4%, причем образование углерода по термодинамике невозможно. Важно отметить, что при этих условиях массовая доля водорода в топливной смеси ${{x}_{{{{{\text{H}}}_{{\text{2}}}}}}}$ лежит в диапазоне 0.48–0.54% (рис. 2б), что близко к оптимальному интервалу 0.55–0.77% по данным стендовых испытаний автомобильного двигателя на пропан-бутановом топливе [14].
На рис. 3 показаны аналогичные результаты расчетов при увеличенной в два раза доле реформируемого пропана ${{\psi }_{f}}$ = 0.2. Доля ${{\varphi }_{{eg}}}$ отработавшего газа ДВС, возвращаемого в цикл (на риформинг пропана) была также пропорционально увеличена и варьировалась в интервале 0.2–0.5. Область свободная от углерода (${{\chi }_{C}}$ < 0) расположена правее точки С при ${{\varphi }_{{eg}}}$ > 0.32 (рис. 3а). В этой области по мере увеличения температуры на выходе риформера от 515 до 555°С выигрыш в химической энтальпии топливной смеси составляет от 2.3 до 3.2% (рис. 3б). На первый взгляд результаты анализа схемы с адиабатическим риформером на рис. 2–3 указывают на пользу дальнейшего увеличения рецикла отработавшего газа ${{\varphi }_{{eg}}}$. Однако на рис. 3б можно отметить, что увеличение параметра ${{\varphi }_{{eg}}}$ до 0.5 уже снижает массовую долю водорода от оптимальных 0.55–0.77 до 0.35% (за счет разбавления избыточным отработавшим газом) и, соответственно, может снижать промотирующий эффект водорода в камере сгорания двигателя. Кроме того, рост эффективности термохимической рекуперации ${{\mu }_{{rec}}}$ при увеличении параметра ${{\varphi }_{{eg}}}$ также замедляется, и кривая роста величины ${{\mu }_{{rec}}}$ выходит на плато (рис. 3б). Если добавить к этим нежелательным факторам уменьшение массы горючих компонент в камере сгорания за счет уменьшения плотности разбавленной смеси, а также рост гидравлического сопротивления на каталитическом слое риформера, то разумным выбором для практической реализации схемы с адиабатическим риформером является доля отработавшего газа ${{\varphi }_{{eg}}}$ вблизи точки С и справа от нее (в области свободной от углерода).
Если исходить из этих соображений, то при доле конвертируемого пропана ${{\psi }_{f}}$ = 0.1 следует выбрать долю возвращаемого на риформинг отработавшего газа (в соответствии с рис. 2а) ${{\varphi }_{{eg}}}$ = 0.18. Эти два параметра были выбраны и зафиксированы при дальнейших расчетах с варьированием температуры отработавшего газа для схемы с адиабатическим риформером. В работе [12] приводятся результаты замера температуры отработавшего газа при стендовых испытаниях автомобильных двигателей на пропан-бутане. В случае роторно-поршневого двигателя ВАЗ-311 и поршневого двигателя ВАЗ-11194 на режимах холостого хода, малых и средних нагрузок такая температура находилась в диапазоне 330–730°С. При расчетах (табл. 1) варьировали температуру отработавшего газа, т.е. температуру смеси на входе в риформер в немного более узком интервале 460–700°С. Рост входной температуры приводит к росту температуры на выходе риформера, но в меньшей степени чем на ходе, поскольку это компенсируется увеличением адиабатического охлаждения ΔТ. Последний фактор объясняется тем, что в соответствии с термодинамикой эндотермика процесса риформинга пропана усиливается с ростом температуры, а в составе продуктов (при 100% конверсии пропана) снижается доля метана и повышается доля водорода. При увеличении температуры термодинамическая склонность к образованию углерода ${{\chi }_{C}}$ снижается (табл. 1), а эффективность термохимической рекуперации ${{\mu }_{{rec}}}$ растет от 0.14 до 1.3%. Теоретически наилучшим вариантом для схемы с адиабатическим риформером следует назвать вариант № 5 из табл. 1. Для него достигается близкая к оптимальной массовая доля водорода в топливной смеси 0.54% (соответствует мольной доле 8.0%) и отсутствие образования углерода согласно термодинамике (${{\chi }_{C}}$ = –0.7) при выигрыше в химической энтальпии топливной смеси (${{\mu }_{{rec}}}$ = 1.09%). Пример расчета адиабатического риформера для этого варианта будет рассмотрен в конце статьи.
Очевидным недостатком рассмотренного варианта № 5 (табл. 1) является требование сравнительно высокой величины Tin = 640°С, что обусловлено адиабатическим типом риформера и рекуперацией теплоты только 0.18 доли от всего потока отработавшего газа. Далее будет проанализирована более эффективная в смысле химической рекуперации тепла схема с трубчатым риформером.
Анализ схемы с трубчатым риформером. На рис. 4 приводятся результаты расчета схемы с трубчатым риформером при фиксированной температуре входной смеси (равной температуре отработавшего газа ДВС) ${{T}_{{{\text{in}}}}} = {{T}_{{eg}}} = $ 640°С и доле конвертируемого пропана ${{\psi }_{f}}$ = 0.1 (рис. 4а) и 0.2 (рис. 4б). Следует напомнить, что в рамках данной схемы весь отработавший газ возвращается в риформер. При этом доля отработавшего газа ${{\varphi }_{{eg}}}$, которая смешивается с пропаном и подается в трубы с катализатором, при расчете увеличивалась в интервале 0.08–0.25. Оставшаяся доля отработавшего газа (1 – ${{\varphi }_{{eg}}}$), которая подается в качестве теплоносителя в межтрубное пространство риформера, соответственно уменьшалась от 0.92 до 0.75. Важное отличие от схемы с адиабатическим риформером состоит в том, что температура выхода из риформера (на рис. 4 не приводится) меняется сравнительно слабо: 600–60°С (для рис. 4а) и 576–594°С (для рис. 4б). Такой более высокий уровень температуры на выходе по сравнению с адиабатическим риформером (рис. 2а, 3а) приводит к положительному эффекту в виде термодинамической невозможности образования углерода (параметр ${{\chi }_{C}}$ < 0) во всем интервале изменения ${{\varphi }_{{eg}}}$ для расчетов на рис. 4. При этом массовая доля водорода в топливной смеси ${{x}_{{{{{\text{H}}}_{{\text{2}}}}}}}$ меняется в более широком диапазоне от 0.90 до 0.48 (при ${{\psi }_{f}}$ = 0.1) и от 0.90 до 0.35 (при ${{\psi }_{f}}$ = 0.2) по сравнению с адиабатическим вариантом (рис. 2б, 3б), что также может рассматриваться как преимущество в плане регулирования процесса термохимической рекуперации.
Рис. 4.
Влияние доли отработавших газов, возвращаемых на риформинг ${{\varphi }_{{{\text{eg}}}}}$ на коэффициент эффективности термохимической рекуперации ${{\mu }_{{{\text{rec}}}}}$ и массовую долю водорода в топливной смеси ${{x}_{{{{{\text{H}}}_{{\text{2}}}}}}}$ при доле конвертируемого пропана ${{\psi }_{f}}$ = 0.1 (а) и 0.2 (б). Расчет для схемы с трубчатым риформером при температуре отработавшего газа 640оС.
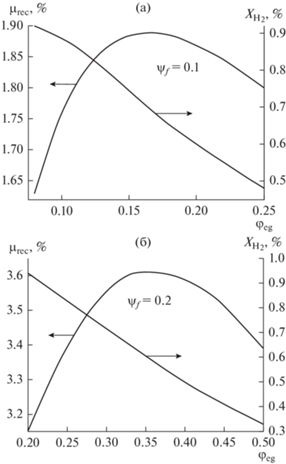
Также более высокий уровень температуры на выходе трубчатого риформера по сравнению с адиабатическим приводит к более высоким коэффициентам термохимической рекуперации ${{\mu }_{{rec}}}$ = = 1.65–1.90 вместо 0.60–1.45 (при ${{\psi }_{f}}$ = 0.1), и ${{\mu }_{{rec}}}$ = 3.1–3.6 вместо 1.2–3.2 (при ${{\psi }_{f}}$ = 0.2). Однако наиболее интересный эффект, который обнаружен в рамках схемы с трубчатым риформером – это существование максимума величины ${{\mu }_{{rec}}}$ при изменении ${{\varphi }_{{eg}}}$. В случае ${{\psi }_{f}}$ = 0.1 (конверсия 10% пропана) такой максимум достигается при величине ${{\varphi }_{{eg}}}$ ~ 0.18 (рецикл 18% отработавшего газа) и равняется ${{\mu }_{{rec}}}$ ~ 1.9%. В случае ${{\psi }_{f}}$ = 0.2 (конверсия 20% пропана) максимум достигается при ${{\varphi }_{{eg}}}$ ~ 0.36 (рецикл 36% отработавшего газа) и равняется ${{\mu }_{{rec}}}$ ~ 3.6%. Здесь можно отметить определенную закономерность в том, что максимальная эффективность термохимической рекуперации в обоих случаях достигается при одинаковом соотношении между долей отработавшего газа и долей пропана, которые образуют реакционную смесь, т.е. при ${{\varphi }_{{eg}}}$/${{\psi }_{f}}$ = 0.18. Заметим, что этот вывод получен при расчетах для случая температуры отработавшего газа ДВС 640°С.
Расчеты с варьированием температуры отработавшего газа для схемы с трубчатым риформером были сделаны при фиксированных параметрах ${{\psi }_{f}}$ = 0.1 и ${{\varphi }_{{eg}}}$ = 0.16, которые, как было показано ранее, максимизировали выигрыш в химической энтальпии топливной смеси ${{\mu }_{{rec}}}$ при ${{T}_{{{\text{in}}}}} = {{T}_{{eg}}} = $ = 640°С. Результаты расчетов приводятся в табл. 2. Можно отметить, что падение температуры по длине трубчатого риформера ΔТ = 10–4°оС при том же самом интервале изменения входной температуры (т.е. температуры отработавшего газа Tin ~ 460–690°С) в 3–4 раза меньше по абсолютной величине чем аналогичное падение ΔТ = 34–148°С для адиабатического риформера (табл. 1). Это объясняется более полной рекуперацией теплоты отработавшего газа ДВС для схемы с трубчатым риформером и приводит к более высокой температуре на выходе, увеличению доли водорода и выигрыша в химической энтальпии топливной смеси ${{\mu }_{{rec}}}$. Также стоит отметить расширение температурного интервала, внутри которого в соответствии с термодинамикой не образуется углерод (${{\chi }_{C}}$ < 0). Для схемы с трубчатым риформером для этого достаточно, чтобы температура отработавшего газа Tin была не менее ~570°С (табл. 2), в то время как для схемы с адиабатическим риформером при всех прочих одинаковых условиях минимальная температура Tin заметно выше, а именно 640°С (табл. 1).
Пример расчета адиабатического и трубчатого риформера. С целью оценки возможности практической реализации рассмотренных схем термохимической рекуперации на борту автомобиля были сделаны расчеты каталитического риформера адиабатического и трубчатого типа. Рассматривался один из возможных режимов работы ДВС на пропане с эффективной мощностью ~30 кВт и расходами пропана и воздуха из табл. 3. В качестве катализатора риформинга пропана, как было указано выше при описании математической модели, рассматривался катализатор Ni/Cr2O3/Al2O3. Данный катализатор позиционируется как катализатор метанирования СО, но результаты исследований [14, 15] указывают на его высокую активность в реакции паровой конверсии легких алканов и, в частности, пропана уже при температурах 260–320°С. Особенно ценным свойством этого катализатора является возможность работы без сажеобразования при низком отношении Н2О/С ~ 0.5–0.7, что может оказаться крайне важным при риформинге пропана-бутана в смеси с отработавшим газом ДВС. Кроме того, катализатор не содержит драгоценных металлов, что положительно сказывается на его цене. Данный катализатор выпускается в форме цилиндрических гранул размером 5 мм. Давление внутри обоих типов риформера при расчете предполагалось близким к атмосферному.
Таблица 3.
Основные параметры ДВС при расчете адиабатического и трубчатого риформера
$V_{{{{{\text{C}}}_{{\text{3}}}}{{{\text{H}}}_{{\text{8}}}}}}^{{{\text{in}}}}$, нм3/ч | $V_{{air}}^{{{\text{in}}}}$, нм3/ч | Ntot, кВт | Neff, кВт |
---|---|---|---|
3.4 | 82.0 | 88.3 | ~30 |
Для расчета адиабатического риформера был выбран режим № 5 из табл. 1, параметры риформера приводятся в табл. 4, результаты расчета в виде профилей температуры и конверсии пропана по длине риформера показаны на рис. 5. Следует отметить, что на входе температура катализатора 570°С заметно ниже температуры потока 640°С, затем обе температуры резко снижаются и сближаясь и выходят на свой адиабатический уровень ~509°С, определяемый термодинамическим равновесием. При этом достигается полная конверсия пропана при небольшом гидравлическом сопротивлении каталитического слоя 3 кПа.
Таблица 4.
Параметры адиабатического риформера
nt | Dt, м | L, м | Vcat, м3 | ΔPcat,кПа |
---|---|---|---|---|
1 | 0.08 | 0.16 | 8×10-4 | 3.0 |
Рис. 5.
Профили температуры реакционного газа (1), катализатора (2) и конверсии пропана (3) по длине адиабатического риформера. Расчет при ${{T}_{{{\text{in}}}}}$ = 640°С, ${{\psi }_{f}}$ = 0.1, ${{\varphi }_{{eg}}}$ = 0.18 (вариант № 5 в табл. 1). Другие параметры приведены в табл. 3 и 4.
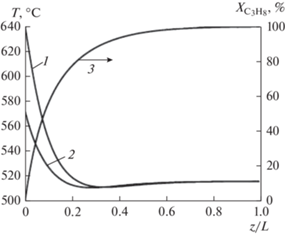
Для расчета трубчатого риформера был выбран режим № 5 табл. 2. Внутри труб размещается катализатор, трубный пучок имеет гексагональную упаковку в поперечнике. Межтрубное пространство для течения теплоносителя (отработавшего газа) разделено поперечными перегородками, частично перекрывающими поперечное сечение пучка, на четыре секции. Это обеспечивает продольно-поперечное обтекание трубного пучка теплоносителем. Предполагается спутное направление потоков реакционной смеси и теплоносителя. Размеры трубчатого риформера приводятся в табл. 5, результаты расчета в виде профилей температуры и конверсии пропана по длине риформера показаны на рис. 6. Мольные составы всех потоков в рамках второй схемы (рис. 2б) для данного варианта расчета приводятся в табл. 6.
Таблица 5.
Параметры трубчатого риформера
nt | Dt,м | S, м | L, м | msec | Vcat, м3 | ΔPcat,кПа | ΔPt, кПа |
---|---|---|---|---|---|---|---|
7 | 0.018 | 0.025 | 0.24 | 4 | 10–3 | 5.6 | 6.4 |
Рис. 6.
Профили температуры реакционного газа (1), катализатора (2), стенки труб (3), межтрубного газа-теплоносителя (4) и конверсии пропана (5) по длине трубчатого риформера. Расчет при ${{T}_{{{\text{in}}}}}$ = 640°С, ${{\psi }_{f}}$ = 0.1, ${{\varphi }_{{{\text{eg}}}}}$ = 0.16 (вариант № 5 в табл. 2). Другие параметры приведены в табл. 3, 5 и 6.
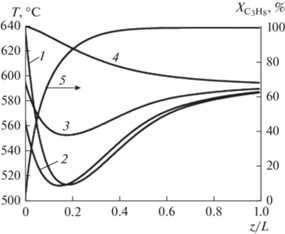
Таблица 6.
Составы потоков (мол. %) для схемы с трубчатым риформером: I – отработавший газ; II – вход в риформер; III – выход из риформера (соответствует варианту № 5 из табл. 2)
C3H8 | CH4 | H2 | CO | H2O | CO2 | O2 | N2 | |
---|---|---|---|---|---|---|---|---|
I | 0 | 0 | 0 | 0 | 13.9 | 11.7 | 0.2 | 74.2 |
II | 2.0 | 0 | 0 | 0 | 13.7 | 11.5 | 0.2 | 72.6 |
III | 0 | 0.2 | 11.3 | 5.6 | 7.8 | 9.9 | 0 | 65.2 |
В целом расчетные параметры двух типов риформера являются вполне приемлемыми для их размещения на борту автомобиля как по объему катализатора и риформера в целом (0.8 л для адиабатического, 1.0 и 1.2 л для трубчатого варианта), так и по гидравлическому сопротивлению (3 кПа и ~6 кПа). Но здесь не учитывается дополнительное оборудование (теплообменник, смесители и разделители потоков).
ЗАКЛЮЧЕНИЕ
Полученные результаты могут служить ориентиром при дальнейшей разработке и экспериментальном испытании блока ТХР для автомобильного двигателя на пропан-бутановом топливе с рециклом отработавшего газа через каталитический риформер. При учете известного ограничения на массовую долю водорода в топливной смеси в диапазоне 0.5–0.7% схема с адиабатическим риформером теоретически увеличивает химическую энтальпию топлива на 1.4–3.2% при доле конвертируемого пропана 0.1–0.2 и температуре отработавшего газа 470–694оС. Для второй более сложной схемы с трубчатым риформером увеличение химической энтальпии топлива может составить 1.9–3.6%, причем для такой схемы найдено оптимальное соотношение между долей отработавшего газа и долей конвертируемого пропана. Преимущество второй схемы также состоит в более широком температурном интервале отработавшего газа, в котором образование углерода термодинамически невозможно.
Полученные результаты могут найти применение при экспериментальной реализации рассмотренных схем ТХР на автомобилях. В связи с этим в настоящее время в Институте катализа СО РАН ведется разработка порометаллических блочных катализаторов, которые не уступали бы по объемной активности гранулированному катализатору Ni/Cr2O3/Al2O3.
Работа выполнена при финансовой поддержке Министерства науки и высшего образования РФ в рамках государственного задания Института катализа СО РАН (проект AAAA-A21-121011390009-1).
ОБОЗНАЧЕНИЯ
Dt | диаметр трубы/труб риформера, м |
kref | константа скорости парового риформинга, моль(С3Н8)/(м3 с атм) |
kmet, ksh | константы скорости метанирования, шифт-реакции, моль(СО2)/(м3 с атм) |
$K_{{eg}}^{{met}}$ | константа термодинамического равновесия метанирования, атм2 |
$K_{{eg}}^{{sh}}$ | константа термодинамического равновесия для шифт-реакции |
L | длина адиабатического или трубчатого риформера, м |
msec | число секций для продольно-поперечного обтекания труб в пучке |
nt | количество труб в риформере |
Ntot | общая тепловая мощность двигателя, кВт |
Neff | эффективная мощность двигателя, кВт |
${{Q}_{{{{{\text{C}}}_{{\text{3}}}}{{{\text{H}}}_{{\text{8}}}}}}}$, ${{Q}_{{{\text{C}}{{{\text{H}}}_{{\text{4}}}}}}}$, ${{Q}_{{{{{\text{H}}}_{{\text{2}}}}}}}$, ${{Q}_{{{\text{CO}}}}}$ | низшая теплота сгорания газов, МДж/нм3 |
Pi | парциальное давление компонент реакционного газа, атм |
Rg | газовая постоянная, Дж/(моль K) |
S | шаг трубного пучка, м |
Т | температура катализатора, K или оС |
Tin | температура потоков на входе в риформер, оС |
Teg | температура отработавшего газа двигателя, оС |
Tout | температура потоков на выходе из риформера, оС |
$V_{{air}}^{{{\text{in}}}}$ | расход воздуха на входе в двигатель, нм3/ч |
$V_{{{{{\text{C}}}_{{\text{3}}}}{{{\text{H}}}_{{\text{8}}}}}}^{{{\text{in}}}}$ | расход пропана на входе в двигатель, нм3/ч |
$V_{{{{{\text{C}}}_{{\text{3}}}}{{{\text{H}}}_{{\text{8}}}}}}^{{{\text{out}}}}$, $V_{{{\text{C}}{{{\text{H}}}_{{\text{4}}}}}}^{{{\text{out}}}}$, $V_{{{{{\text{H}}}_{{\text{2}}}}}}^{{{\text{out}}}}$, $V_{{{\text{CO}}}}^{{{\text{out}}}}$ | расходы горючих газов на выходе риформера, нм3/ч |
Vcat | насыпной объем катализатора, м3 |
$W_{{ref}}^{{}}$ | скорость реакции парового риформинга пропана, моль(С3Н8)/(м3 с) |
Wmet, Wsh | скорости метанирования и шифт-реакции, моль(СО2)/(м3 с) |
${{x}_{{{{{\text{H}}}_{{\text{2}}}}}}}$, ${{y}_{{{{{\text{H}}}_{{\text{2}}}}}}}$ | массовая и мольная доля водорода в топливной смеси на входе в камеру сгорания ДВС (после смешения продуктов риформинга с пропаном) |
${{X}_{{{{{\text{C}}}_{{\text{3}}}}{{{\text{H}}}_{{\text{8}}}}}}}$ | конверсия пропана на выходе риформера, % |
z | координата по длине риформера, м |
ΔPcat | перепад давления внутри трубы с катализатором, кПа |
ΔPt | перепад давления в межтрубном пространстве риформера, кПа |
ΔТ | разность температур потоков между выходом и входом риформера, оС |
${{\mu }_{{rec}}}$ | коэффициент эффективности термохимической рекуперации (выигрыш в химической энтальпии топливной смеси) |
${{\psi }_{f}}$ | доля топлива (пропана), отводимого на риформинг |
${{\varphi }_{{eg}}}$ | доля отработавшего газа двигателя, возвращаемая на риформинг |
${{\chi }_{C}}$ | термодинамический критерий образования углерода |
ИНДЕКСЫ
Список литературы
Ипатов А.А., Каменев В.Ф., Хрипач Н.А., Лежнев Л.Ю. Разработка и исследования транспортных средств с различными типами водородных и комбинированных энергоустановок // Журн. автомобил. инженеров. 2007. № 5 (46). С. 18–27.
Фомин В.М., Макунин А.В. Термохимическая регенерация теплоты отработавших газов двигателей внутреннего сгорания (общий подход к проблеме утилизации теплоты выпускных газов) // Хим. технология. 2008. Т. 9. № 10. С. 539–544.
Кириллов В.А., Шигаров А.Б., Кузин Н.А., Киреенков В.В., Амосов Ю.И., Самойлов А.В., Бурцев В.А. Термохимическое преобразование топлив в водородсодержащий газ за счет рекуперированного тепла двигателей внутреннего сгорания // Теорет. основы хим. технологии. 2013. Т. 47. № 5. С. 503–517. https://doi.org/10.7868/S0040357113050059
Перетрухин С.Ф., Бризицкий О.Ф., Кириллов В.А., Кузин Н.А., Козлов С.И. Бортовой генератор синтез-газа для ДВС с искровым зажиганием // Транспорт на альтернативном топливе. 2010. № 5(17). С. 68–74.
Певнев Н.Г., Кириллов В.А., Бризицкий О.Ф., Бурцев В.А. Перспективы использования газобаллонных автомобилей с бортовым генератором синтез-газа // Транспорт на альтернативном топливе. 2010 № 3(15). С. 40–45.
Jamal Y., Wagner T., Wyszynski M.L. Exhaust gas reforming of gasoline at moderate temperatures // Int. J. Hydrogen Energy. 1996. V. 21 № 6. P. 507–519.
Yap D., Peucheret S.M., Megaritis A., Wyszynski M.L., Xu H. Natural gas HCCI engine operation with exhaust gas fuel reforming // Int. J. Hydrogen Energy. 2006. V. 31. P. 587–595. https://doi.org/10.1016/j.ijhydene.2005.06.002
Bogarra M., Herreros J.M., Tsolakis A., York A.P.E., Millington P.J. Study of particulate matter and gaseous emissions in gasoline direct injection engine using on-board exhaust gas fuel reforming // Appl. Energy. 2016. V. 180. P. 245–255. https://doi.org/10.1016/j.apenergy.2016.07.100
Li G., Long Y., Zhang Z. et al. Performance and emissions characteristics of a lean-burn marine natural gas engine with the addition of hydrogen-rich reformate // Int. J. Hydrogen Energy. 2019. 44. P. 31544–31556. https://doi.org/10.1016/j.ijhydene.2019.10.007
Long Y., Li G., Zhang Z., Liang J. Application of reformed exhaust gas recirculation on marine LNG engines for NOx emission control // Fuel. 2021. V. 291. 120114. https://doi.org/10.1016/j.fuel.2020.120114
Pashchenko D. Thermodynamic equilibrium analysis of combined dry and steam reforming of propane for thermochemical waste-heat recuperation // Int. J. Hydrogen Energy. 2017. V. 42. № 22. P. 14926–14935. https://doi.org/10.1016/j.ijhydene.2017.04.284
Алимов В.А., Захаров Е.А., Федянов Е.А., Гаврилов Д.С., Сафаров Э.Г.. Улучшение процесса сгорания сжиженного углеводородного газа добавками водорода и водородсодержащего синтез-газа // Молодой ученый. 2017. № 27(161). С. 24–27.
Алимов В.А., Захаров Е.А., Приходьков К.В., Сафаров Э.Г., Федянов Е.А. Влияние добавок синтез-газа на межцикловую неидентичность рабочего процесса двигателя с искровым зажиганием // Энерго- и ресурсосбережение: промышленность и транспорт. 2019. № 3(28). С. 22-24.
Алимов В.А., Захаров Е.А., Сафаров Э.Г., Федянов Е.А. Влияние добавок синтез-газа к пропан-бутану на процесс сгорания в автомобильном двигателе // Двигателестроение. 2020. № 3(281). С. 17–20.
Zyryanova M.M., Snytnikov P.V., Shigarov A.B., Belyaev V.D., Kirillov V.A., Sobyanin V.A. Low temperature catalytic steam reforming of propane-methane mixture into methane-rich gas: experiment and macrokinetic modeling // Fuel. 2014. V. 135. P. 76–82. https://doi.org/10.1016/j.fuel.2014.06.032
Shigarov A.B. Modeling of low temperature steam reforming of flare gas to methane-rich fuel gas on Ni catalyst in different types of reactors // Chem. Eng. J. 2020. V. 397. 125313. https://doi.org/10.1016/j.cej.2020.125313
Shigarov A.B., Uskov S.I., Potemkin D.I., Snytnikov P.V. Experimental verification of kinetics and internal diffusion impact on low temperature steam reforming of a propane-methane mixture over Ni-based catalyst // Chem. Eng. J. 2022. V. 429. 132205. https://doi.org/10.1016/j.cej.2021.132205
Дополнительные материалы отсутствуют.
Инструменты
Теоретические основы химической технологии