Физика Земли, 2023, № 3, стр. 148-157
Совместный акустический и деформационный мониторинг трещины гидроразрыва в лабораторном эксперименте
Е. В. Зенченко 1, *, П. Е. Зенченко 1, В. А. Начев 1, С. Б. Турунтаев 1, 2, Т. К. Чумаков 1, 2
1 Институт динамики геосфер имени академика М. А. Садовского РАН
г. Москва, Россия
2 Московский физико-технический институт (национальный исследовательский университет)
г. Москва, Россия
* E-mail: zenchevj@gmail.com
Поступила в редакцию 20.09.2022
После доработки 22.11.2022
Принята к публикации 09.12.2022
- EDN: KBGNNF
- DOI: 10.31857/S0002333723030134
Аннотация
Приведены результаты лабораторных экспериментов по совместному активному акустическому и деформационному мониторингу трещины гидроразрыва. Эксперименты проводились в модельном материале на основе гипса. Для сравнения были проведены эталонные эксперименты по исследованию прохождения ультразвуковых волн через заполненную жидкостью щель контролируемой ширины между двумя прецизионными стеклянными пластинами. Целью экспериментов было исследование зависимости амплитуды ультразвуковой волны, прошедшей через трещину от величины ее раскрытия. В этих экспериментах создавалась круговая трещина гидроразрыва, плоскость которой была перпендикулярна оси цилиндрического образца. Вдоль этой же оси располагалась обсаженная нагнетательная скважина, заканчивающаяся на середине его высоты. Образец располагался между двумя дисками из алюминиевого сплава, оснащенных вмонтированными в них пьезокерамическими преобразователями, работающими как в режиме излучателя, так и режиме приемника. Через канал в нижнем диске осуществлялась подача рабочей жидкости в трещину. Через верхний диск производилось насыщение образца поровым флюидом. Вся сборка помещалась в гидравлический пресс, обеспечивающий постоянное сжимающее усилие. Величина раскрытия трещины изменялась в зависимости от расхода жидкости, подаваемой в центр трещины, и измерялась по относительному изменению расстояния между дисками сборки при помощи индукционных преобразователей перемещения. Также были проведены эксперименты, моделирующие трещину, заполненную проппантом. В этом случае апертура трещины изменялась в зависимости от приложенного вертикального давления на образец. По результатам экспериментов, проведенных в различных условиях, были построены зависимости амплитуды ультразвуковой волны, прошедшей через трещину. Экспериментально установлено, что поглощение звука в трещине гидроразрыва, обладающей естественной шероховатостью, вдвое ниже, чем в зазоре между прецизионными стеклянными пластинами. Полученные результаты позволят оценить величину раскрытия трещины гидроразрыва в лабораторных экспериментах, проводимых на образцах большего размера с использованием активного акустического мониторинга.
1. ВВЕДЕНИЕ
Метод активного акустического мониторинга трещины гидроразрыва является одним из методов исследования трещины гидроразрыва преимущественно в лабораторных экспериментах, поскольку методы активной акустики в полевых условиях применять значительно сложнее, чем в лаборатории. Помимо получения информации о скорости распространении трещины гидроразрыва, метод активного акустического мониторинга позволяет получить данные о величине ее раскрытия. Однако для этого необходимо знать связь между параметрами регистрируемого акустического сигнала и апертурой трещины. В нашей работе приводятся результаты исследований, устанавливающие связь между этими величинами.
В работе [Medlin, Massé, 1984] показана возможность измерения параметров трещины по регистрации ослабления волн сжатия. В этой работе величина раскрытия трещины измерялась непосредственно у стенки скважины. Эти исследования получили дальнейшее развитие в работах [Groenenboom, 1998; 2001], где использовалась дифракция акустических волн на кончике трещины, а также применялись излучатели и приемники поперечных волн, что позволило получить информацию о закрытии и повторном открытии трещины гидроразрыва. Для оценки величины апертуры трещины использовалась модель, основанная на прохождении звуковой волны через слой жидкости между гладкими параллельными поверхностями. Дальнейшее развитие этот метод получил в работе [Liu, 2020], где для исследования распространения трещины гидроразрыва использовался массив из 32 ультразвуковых приемников и 32 излучателей, однако оценок величины раскрытия трещины в этой работе не проводилось. Используя методы акустического мониторинга авторы работ [Stanchits и др., 2012; 2014; 2015] установили, что зарождение и распространение трещины ГРП происходит до достижения максимума давления в скважине, подтвердив ранее полученные результаты в работе [Zoback и др., 1977].
Аналогичные результаты по исследованию распространения трещины гидроразрыва, выполненные на установке трехосного нагружения были получены авторами работ [Зенченко и др., 2019; Турунтаев и др., 2021]. Для их дальнейшей интерпретации проведены эксперименты по совместному деформационному и акустическому мониторингу трещины гидроразрыва, результаты которых приводятся в данной работе. Преимуществом такого экспериментального подхода является непосредственное измерение величины раскрытия трещины, сопоставляемое с изменением амплитуды ультразвукового импульса, прошедшего через трещину гидроразрыва, полученную в модельном материале. Для сравнения приводятся результаты экспериментов по поглощению ультразвука в щели между двумя прецизионными стеклянными пластинами, заполненной той же жидкостью, что и в эксперименте по гидроразрыву.
2. ОПИСАНИЕ ЭКСПЕРИМЕНТАЛЬНЫХ УСТАНОВОК
2.1. Образец на основе гипса
Для изготовления образцов использовалась смесь из гипса и портландцемента в соотношении 10 : 1. Образцы отливались в форму, изготовленную из отрезка полипропиленовой трубы наружным диаметром 110 мм и высотой 60 мм. В основание формы для отливки вставлялась латунная трубка с наружным диаметром 12 мм с заглушенным концом, имитирующая обсаженную скважину. На заглушенном конце трубки, на середине высоты образца располагалась затравка будущей трещины гидроразрыва в виде диска диаметром 25 мм, изготовленного из двух слоев латунной сетки с размером ячейки 0.3 мм, имеющая гидравлическую связь с внутренним отверстием латунной трубки. Образец высушивался не менее 10 сут при температуре около 30°C. Критерием окончания сушки служила стабилизация массы образца. Нижняя поверхность высушенного образца не требовала дополнительной обработки, а верхняя выравнивалась на токарном станке, чем также достигалась параллельность обеих поверхностей. Высота обработанного образца составляла 60 мм при наружном диаметре 104 мм. Также в процессе обработки в центре верхнего основания образца просверливалось технологическое углубление диаметром и глубиной 15 мм.
Подготовленный образец помещался между двух круглых алюминиевых оснований в углублениях рабочих поверхностей, в которых были смонтированы пьезоэлектрические преобразователи, представляющие собой диски из пьезокерамики ЦТС-19 диаметром 8 мм и толщиной 1 мм, залитые эпоксидной смолой. Резонансная частота пьезопреобразователей составляла примерно 250 кГц. При сборке трубка с затравкой насаживалась на патрубок с кольцевым резиновым уплотнением, расположенный в нижнем основании, в то время как патрубок в центре верхнего основания входил в технологическое углубление в верхней части образца. Перед сборкой на поверхность нижнего основания наносился слой силиконового компаунда и на него помещался образец. После полимеризации компаунда таким же способом обрабатывалось и верхнее основание. Основания ориентировались таким образом, чтобы верхние и нижние пьезопреобразователи находились на одной вертикальной линии. Силиконовый компаунд обеспечивал отсутствие протекания по примыкающим поверхностям образца и оснований, а также создавал надежный акустический контакт между образцом и пьезоэлектрическими преобразователями.
Схема экспериментальной сборки показана на рис. 1. Кроме описанных выше элементов, на нижнем основании располагались четыре стойки, на которые крепились индукционные измерители перемещений, рабочий шток которых находился в контакте с внешней поверхностью верхнего основания. Благодаря тому, что на боковой поверхности верхнего основания имелись вертикальные углубления, в которые входили стойки, обеспечивалось правильное взаимное расположение оснований. Жидкость для проведения гидроразрыва и заполнения уже образовавшейся трещины подавалась через канал в нижнем основании, связанный через патрубок с центральной трубкой с затравкой. После выхода трещины гидроразрыва на боковую поверхность образца жидкость свободно вытекала через нее. Сборка помещалась в цилиндрический сосуд и устанавливалась в гидравлический пресс 2ПГ-10 с максимальным усилием 100 кН с возможностью нагружения винтовой парой и фиксировалась в нем. Нижняя плита пресса была установлена на шаровой опоре, обеспечивая компенсацию возможной непараллельности оснований экспериментальной сборки с образцом, а также непараллельность, возникающую из-за неравномерного раскрытия трещины гидроразрыва. Затем, через штуцер в верхнем основании и технологическое углубление, образец начинал вакуумироваться, после чего в емкость с образцом заливалась силиконовая жидкость ПМС‑5 с кинематической вязкостью 5 сСт, которая его насыщала. После того, как жидкость начинала поступать в буферную вакуумную емкость без вспенивания, насыщение считалось завершенным. Это происходило примерно в течение одних суток.
Рис. 1.
Схема экспериментальной сборки для исследования прохождения ультразвука через трещину гидроразрыва. Чтобы не загромождать рисунок, показана только одна стойка с измерителем перемещения.
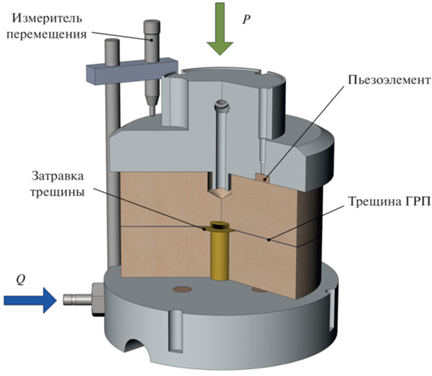
Для проведения гидроразрыва и обеспечения различных значений величины раскрытия трещины ГРП, а также для поддержания заданного постоянного давления в гидравлическом прессе использовалась насосная система СМП‑НС‑40‑250 производства ООО “Кортех”. При проведении гидроразрыва и для последующего изменения величины раскрытия трещины использовалась силиконовая жидкость ПМС‑500 вязкостью 500 сСт. Для поддержания давления в прессе применялось более вязкое силиконовое масло ПМС‑1000, что, учитывая конструкцию пресса, минимизировало утечку рабочей жидкости. Важной особенностью силиконовых жидкостей, используемых в эксперименте, является сравнительно невысокая зависимость их вязкости от температуры. Изменение вязкости при изменении температуры на 1°C не превышает 2% в интервале температур 20…50°C. Окружающая температура во время проведения описываемых экспериментов находилась в диапазоне 20…21°C, что не могло оказать существенного влияния на их результаты. Во время проведения экспериментов относительные перемещения верхнего и нижнего оснований измерялись индукционными датчиками и через интерфейсное устройство БИН‑8 в оцифрованном виде передавались на персональный компьютер, где записывались с интервалом около 0.35 с. Шаг измерения величины перемещения составлял 0.2 мкм.
Для возбуждения ультразвуковых импульсов, посылаемых через трещину гидроразрыва, использовался двухканальный генератор сигналов специальной формы АКИП 3418/1, каждый канал которого управлял схемой на основе MOSFET транзистора. В качестве управляющего использовался синусоидальный сигнал длительностью в один период, причем транзистором управлял только положительный полупериод сигнала. Частота и амплитуда синусоиды варьировались, чтобы получить с приемника приемлемую величину сигнала, особо обращая внимание на то, чтобы она не превышала динамический диапазон регистрирующего АЦП. Максимальная амплитуда возбуждающего импульса на выходе с MOSFET транзистора достигала 200 В. Период повторения возбуждающих импульсов изменялся в зависимости от решаемых экспериментальных задач, но обычно составлял 20 мс. В этом случае импульс со второго канала посылался с задержкой 8 мс относительно первого, что позволяло разделить их во времени и облегчить идентификацию принятых сигналов в процессе дальнейшей обработки.
Импульс, принятый приемником, передавался на предусилитель на основе инструментального усилителя Analog Devices AD621 и далее на вход четырехканального АЦП E20‑10 производства ООО “L-CARD”. Частота дискретизации составляла 2.5 МГц на канал. Оцифрованные сигналы непрерывно записывались на жесткий диск персонального компьютера в несколько последовательных по времени файлов в течение всего времени проведения эксперимента, которое достигало 10 минут.
Давление в рабочей скважине измерялось при помощи преобразователя давления NAT 8252 производства Trafag AG с нормированным токовым выходом. Преобразователь располагался на минимально возможном расстоянии от скважины и был соединен с ней трубкой с внутренним диаметром 4 мм, чтобы минимизировать потерю давления. Такие же преобразователи использовались для измерения давления в технологическом углублении образца для контроля вакуумирования и насыщения, а также на входной магистрали гидравлического пресса. Сигналы с преобразователей давления регистрировались с помощью АЦП Е14-440 производства Л-Кард с частотой дискретизации 100 Гц с непрерывной записью на жесткий диск персонального компьютера.
Для синхронизации записей давления и ультразвуковых импульсов использовался прямоугольный импульс длительностью 100 мс, подаваемый с генератора импульсов Г5-75. При этом в первую очередь программно вручную включалась запись давления. Затем, при подаче импульса с генератора, запускался сбор данных с АЦП Е20‑10 и этот же импульс записывался на один из каналов АЦП Е14-440. Также, перед проведением эксперимента, под один из измерителей перемещения подкладывалась полоска медной фольги толщиной 0.25 мм, которая выдергивалась одновременно с нажатием кнопки подачи импульса на генераторе. Таким образом, записи давления, ультразвуковых импульсов и перемещений оказывались синхронизированными.
2.2. Образец из стеклянных пластин
Для сравнения результатов экспериментов по исследованию прохождения ультразвука через естественную трещину был проведен эксперимент, в котором трещина имитировалась щелью контролируемой ширины между двумя плоскими прецизионными стеклянными пластинами. Пластины имели толщину 20 мм при диаметре 60 мм. Стекла помещались в чашки из оргстекла, в которых располагались излучатель и приемник, рабочий элемент которых также был изготовлен из пьезокерамики ЦТС-19 и имел форму диска диаметром 8 мм при толщине 1 мм. В верхнюю чашку стеклянная пластина вклеивалась на силиконовом герметике, а из нижней могла свободно выниматься. Объем, образуемый внутренней поверхностью чашек и поверхностью стекол заполнялся кремнийорганической жидкостью ПМС-500, обеспечивая тем самым неизменный акустический контакт между пьезоэлементами и стеклом независимо от величины сжимающего усилия, фиксирующего чашки, которое в эксперименте не контролировалось. Зазор между стеклами задавался при помощи двух параллельных отрезков проволок. Диаметр проволок предварительно измерялся при помощи вышеописанной измерительной системы БИН‑8 и индукционного датчика. Для этого на поверхность стеклянной пластины помещались две одинаковые измеряемые проволочки, на которые сверху накладывалась концевая мера длины толщиной около 1.5 мм, которая предварительно находилась в контакте со стеклянной пластиной. По изменению показаний индукционного датчика находился диаметр проволочки. Диапазон диаметров проволочек составлял от 14 до 380 мкм. Схема установки для исследования прохождения ультразвука через щель, образованную стеклянными пластинами, показана на рис. 2. Сборка помещалась в ручной винтовой пресс, фиксируя, таким образом, зазор между пластинами.
Рис. 2.
Схема сборки для исследования прохождения ультразвука через щель между стеклянными пластинами.
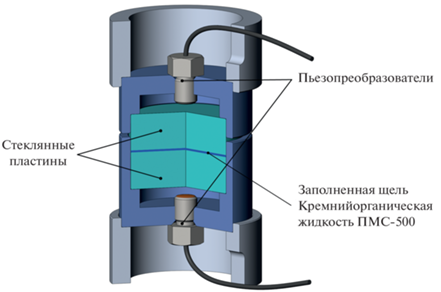
В этой серии экспериментов для возбуждения ультразвуковых зондирующих импульсов использовалась та же схема, что и в эксперименте по исследованию трещины гидроразрыва, но при этом использовался только один канал. Регистрация импульсов с приемника производилась непосредственно цифровым осциллографом GDS-72072 с разверткой 5 мкс/деление, что соответствовало частоте дискретизации 100 МГц.
3. МЕТОДИКА ПРОВЕДЕНИЯ ЭКСПЕРИМЕНТОВ И ОБРАБОТКИ ДАННЫХ
3.1. Образец на основе гипса
Для гарантированного получения горизонтальной трещины гидроразрыва, то есть такой, чтобы геометрическая вертикальная ось образца была перпендикулярна плоскости трещины, необходимо было выполнить условие превышения радиального сжимающего напряжения над вертикальным. Чтобы задать необходимую величину радиального напряжения, использовались четыре червячных хомута, расположенные так, чтобы не перекрывалась область в середине образца размером примерно 1/5 его высоты, через которую, как предполагалось, должна была пройти трещина гидроразрыва. Радиальное напряжение оценивалось на основе измерения диаметра свободной части образца до и после стяжки хомутами, которое также измерялось индукционными датчиками перемещений БИН-8. Для этой оценки использовалась величина модуля упругости модельного материала 2 ГПа, предварительно измеренная на основе специально проведенных деформационных испытаний. Изменение диаметра образца при его стяжке составило ≈20 мкм. Расчеты, выполненные в стандартном пакете методом конечных элементов, дали величину радиального напряжения ≈0.5 МПа, что превышало вертикальное сжимающее напряжение 0.37 МПа, соответствующее минимально возможному давлению 0.3 МПа, поддерживаемому насосной установкой в гидравлическом прессе. Таким образом, условие превышения горизонтальных напряжений над вертикальным было выполнено, что позволило получить в эксперименте горизонтальную трещину гидроразрыва, начальная геометрия которой обеспечивалась горизонтальным расположением затравки.
При проведении эксперимента образец сначала нагружался вертикальным давлением. Затем, после того как достигался постоянный уровень вертикальной нагрузки, с помощью импульса синхронизации запускался сбор данных на АЦП Е20‑10 и одновременно выдергивалась полоска фольги из под датчика перемещения. Примерно через 5 с после этого включалась подача жидкости ПМС-500 в рабочую скважину с заданным постоянным расходом 5 см3/мин. После этого давление в рабочей скважине начинало расти вплоть до момента образования трещины гидроразрыва. После образования трещины давление в скважине резко падало до определенного уровня и затем начинало медленно возрастать. Затем, не останавливая подачи рабочей жидкости в скважину, ступенчато увеличивался ее расход. Значения расхода последовательно составляли 5, 7.5, 12, 18, 24, 30, 40, 50 см3/мин. На каждой новой ступени расхода устанавливалось новое равновесное значение раскрытия трещины, поскольку вертикальное давление поддерживалось постоянным. Непрерывное проведение эксперимента не позволяло берегам трещины смыкаться, что в противном случае могло бы привести к нарушению поверхностей образовавшейся трещины при ее закрытии, обусловленном сбросом давления.
Образование и рост трещины гидроразрыва происходят неравномерно в разных направлениях в силу разных случайных факторов, например, вариаций прочности и проницаемости образца, поэтому величина раскрытия трещины оказывается неодинаковой в разных точках ее поверхности. Пренебрегая деформациями образца, можно считать, что значения относительных перемещений берегов трещины лежат в плоскости, наклонной по отношению к базовому горизонту. Поскольку координаты излучателей и приемников ультразвука не совпадали с координатами измерителей перемещения, то для расчета перемещений в местах расположения акустических преобразователей методом наименьших квадратов находилось уравнение плоскости, по которому эти перемещения вычислялись.
Для выделения зондирующих ультразвуковых импульсов применялся пороговый критерий с учетом заданного периода их повторения, что позволяло компенсировать погрешности частот дискретизации АЦП и периода следования импульсов. После этого, используя преобразование Гильберта, строилась огибающая каждого выделенного импульса. За амплитуду импульса принималось максимальное значение огибающей первых 4…5 периодов импульса, поскольку в дальнейшем в импульс вносились интерференционные искажения, обусловленные отражениями от элементов экспериментальной сборки. В результате такой обработки получалась зависимость амплитуды импульсов от времени с шагом, равным периоду повторения импульсов.
Чтобы сопоставить амплитуду ультразвуковых импульсов с величиной раскрытия трещины проводилась кусочно-линейная интерполяция зависимости перемещений от времени с последующим их пересчетом на моменты времени, соответствующие периоду повторения импульсов. Затем, по полученным значениям строилась зависимость амплитуды ультразвуковых импульсов, прошедших через трещину гидроразрыва от величины раскрытия трещины.
3.2. Трещина гидроразрыва, заполненная песком
Для имитации трещины, закрепленной проппантом, был проведен эксперимент, в котором образец после образования трещины гидроразрыва был разделен на две части по этой трещине. Затем на поверхность трещины нижней части образца была нанесена кремнийорганическая жидкость ПМС‑500, также использовавшаяся для создания трещины гидроразрыва. После этого на смоченную поверхность трещины был насыпан сухой кварцевый песок узкой фракции со средним размером частиц 0.3 мм. Чтобы убрать несмоченный песок, половинка образца была перевернута, после чего на поверхности трещины остался тонкий слой прилипшего песка визуально толщиной в одну песчинку. Далее нижняя часть образца была накрыта верхней в соответствии с их исходным взаимным расположением, после чего сборка была помещена в пресс и поджата давлением в прессе 0.2 МПа. Расстояния между алюминиевыми основаниями экспериментальной сборки вблизи точек установки датчиков перемещения были измерены при помощи набора концевых мер с точностью 0.01 мм как до заполнения трещины песком, так и после этого, что позволило зафиксировать исходную величину раскрытия трещины.
В отличие от эксперимента с незакрепленной трещиной, в этом эксперименте раскрытие трещины изменялось за счет увеличения вертикального давления на образец. Сначала был проведен эксперимент с сухой трещиной. Давление в прессе в этом случае составляло 0.2, 0.3, 0.4, 0.5, 0.7 МПа. Затем, для насыщения трещины, через нее прокачивалась рабочая жидкость с расходом 0.1 см3/мин, который был от одного до двух порядков ниже, чем в экспериментах с незакрепленной трещиной. Такой низкий расход обеспечивал отсутствие выноса песчинок из трещины, но не влиял при этом на величину ее раскрытия. Эксперимент с насыщенной закрепленной трещиной проводился при давлениях в прессе 0.15, 0.3, 0.5, 0.7, 0.9, 1.2, 1.6, 2, 2.5, 3 МПа.
3.3. Эксперимент со стеклянными пластинами
В отличие от ультразвуковых измерений в случае трещины гидроразрыва, в эксперименте со стеклянными пластинами уровень помех в измерительной системе был значительно ниже. Кроме того, при регистрации прошедшего ультразвукового сигнала осциллографом, использовался режим усреднения по 8 измерениям, что дополнительно снижало уровень шумов принятого сигнала. Поэтому, каждому значению размера щели между пластинами соответствовало одно значение амплитуды ультразвукового сигнала. Так же как и в случае трещины гидроразрыва, это значение находилось из максимума огибающей 4…5 периодов сигнала Вместе с тем, в ходе измерений диаметров проволочек отмечалась некоторая нестабильность их величин при смещениях концевой меры относительно измерительной головки индукционного датчика. Было установлено, что это отклонение могло достигать до 3 мкм в каждую сторону. Исходя из этого, на основе нормального распределения, был смоделирован набор случайных данных для каждого диаметра проволочки, учитывающий дискретность измерительного устройства. Используя этот смоделированный набор, строилась зависимость амплитуды ультразвукового сигнала от расстояния между стеклянными пластинами.
Для сравнения результатов экспериментов между собой, учитывая экспоненциальную аппроксимацию экспериментальных данных, все значения амплитуды были нормированы на амплитуду импульса, соответствующую величине раскрытия трещины 20 мкм. Такой выбор сравнительной базы обусловлен размером щели, близким к минимальному в эксперименте со стеклянными пластинами.
3.4. Результаты экспериментов и их обсуждение
Как было описано выше, эксперимент по образованию трещины гидроразрыва и последующему увеличению величины ее раскрытия проводился непрерывно. Раскрытие трещины увеличивалось за счет ступенчатого увеличения расхода жидкости, подаваемой в рабочую скважину. На рис. 3 представлены синхронизированные зависимости давления в рабочей скважине, гидравлическом прессе, создающем вертикальное давление с величиной раскрытия трещины гидроразрыва и с амплитудой прошедшего ультразвукового импульса от времени.
Рис. 3.
Синхронизированные по времени записи давления в рабочей скважине, гидравлическом прессе, создающем вертикальное давление, с величиной раскрытия трещины гидроразрыва и с амплитудой прошедшего ультразвукового импульса, нормированной на его амплитуду до возникновения трещины гидроразрыва. Числа над последовательными участками кривой давления в скважине показывают величину расхода рабочей жидкости на каждой ступени увеличения расхода в см3/мин.
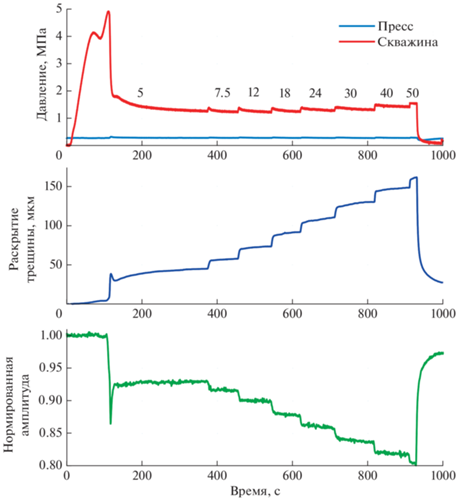
Момент образования трещины гидроразрыва, примерно совпадающий по времени с максимальным давлением в скважине, отмечается резким уменьшением амплитуды ультразвукового импульса. Что касается величины раскрытия трещины, то она изменяется не так заметно, что обусловлено низкой частотой опроса индукционного измерителя перемещения, вследствие чего момент максимального раскрытия трещины при гидроразрыве мог быть пропущен. Каждая ступень увеличения расхода отчетливо видна на зависимости давления в скважине от времени в виде небольшого скачка с последующим спадом. Используя построенные зависимости, можно оценить раскрытие трещины гидроразрыва в момент времени, когда она пересекала линию “излучатель–приемник”. Величина этого раскрытия составила ≈110 мкм. Для дальнейшей обработки использовался участок записи примерно с 300-й секунды, когда стабилизировалось давление в скважине, и до момента остановки насоса, после которой давление в скважине быстро упало.
Непосредственно после проведения первого эксперимента был проведен эксперимент по повторному раскрытию трещины гидроразрыва. В целом он продемонстрировал те же результаты, за исключением подъема давления, связанного с первичным образованием трещины. На рис. 4 показана зависимость нормированной амплитуды ультразвукового импульса от величины раскрытия трещины в первичном эксперименте по созданию трещины гидроразрыва. Напомним, что нормировка проводилась на значение амплитуды при раскрытии трещины 20 мкм.
Рис. 4.
Зависимость амплитуды ультразвукового импульса, прошедшего через трещину гидроразрыва от величины ее раскрытия в эксперименте с образованием трещины гидроразрыва в исходном образце. Амплитуда нормирована на ее значение при раскрытии, равном 20 мкм.
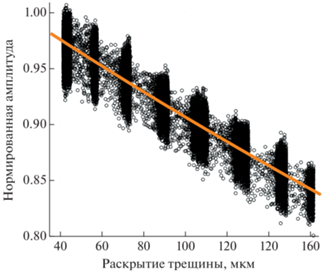
Аналогичная зависимость для эксперимента по прохождению ультразвука через заполненную щель между стеклянными пластинами показана на рис. 5.
Рис. 5.
Зависимость амплитуды ультразвукового импульса, прошедшего через щель между стеклянными пластинами от ее ширины.
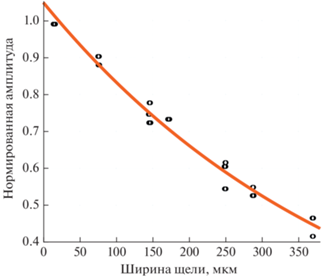
Результаты измерений аппроксимировались зависимостью вида A = ae–γx методом наименьших квадратов, где: А – амплитуда волны; а – безразмерный множитель; γ – коэффициент ослабления ультразвука; х – величина раскрытия трещины. Таким же способом обрабатывались результаты для экспериментов по повторному раскрытию трещины гидроразрыва, а также для сухой и насыщенной закрепленной трещины. В эксперименте по образованию первичной трещины гидроразрыва использовались результаты измерений только с одной пары излучатель—приемник. В остальных экспериментах использовались данные, полученные с обеих рабочих пар. Результаты всех проведенных экспериментов приведены в табл. 1.
Таблица 1
a | Δa | γ, см–1 | Δγ, см–1 | R2 | |
---|---|---|---|---|---|
ГРП | 1.025 | 0.001 | 12.27 | 0.04 | 0.9 |
ГРП (повтор) | 1.025 | 0.001 | 12.45 | 0.03 | 0.94 |
1.027 | 0.001 | 13.5 | 0.05 | 0.9 | |
Стекло | 1.049 | 0.007 | 23.0 | 0.4 | 0.98 |
Песок сухой | 3.5E + 08 | 1E + 08 | 560 | 10 | 0.98 |
1.2E + 04 | 1000 | 269 | 3 | 0.97 | |
Песок насыщенный | 1.09 | 0.02 | 42.5 | 0.5 | 0.97 |
1.07 | 0.02 | 31.5 | 0.4 | 0.96 |
Как видно из таблицы, коэффициент ослабления γ как для первичной трещины гидроразрыва, так и при повторном ее раскрытии имеет близкие значения. При этом значение коэффициента ослабления в стекле почти вдвое больше, чем для трещины в модельном материале. Результаты измерений для случая сухой или насыщенной трещины, заполненной песком, обработанные указанным выше способом, следует рассматривать как справочные, поскольку прохождение звука через сухую трещину с заполнителем обусловлено взаимодействием берегов трещины с его частицами. Насыщение сухой трещины жидкостью приводит к уменьшению коэффициента ослабления на порядок, но он оказывается примерно втрое больше, чем для трещины без песка. Таким образом, трещина становится более “похожей” на заполненную жидкостью, но наличие песка также продолжает влиять на прохождение звука через нее, увеличивая поглощение.
Существенное различие коэффициентов поглощения звука при прохождении через естественную трещину и через щель, образованную плоскими стеклянными пластинами, можно объяснить, если рассмотреть схематическую трещину, изображенную на рис. 6.
Можно предположить, что при гидроразрыве образуются две идентичные поверхности трещины, разделенные промежутком жидкости. Также очевидно, что при заданном (измеренном) вертикальном смещении, на наклонных участках величина кратчайшего расстояния между берегами трещины будет меньше этого смещения, что приведет к меньшему затуханию звуковой волны при прохождении через наклонные участки. Также, при возможном тангенциальном смещении берегов трещины, возможно дополнительное уменьшение локальных зазоров между ними, вплоть до их взаимного контакта. В итоге можно говорить об эффективной величине раскрытия трещины, которая оказывается меньше, чем если бы трещина была образована плоскими параллельными поверхностями.
ЗАКЛЮЧЕНИЕ
Использование в лабораторном эксперименте метода активного акустического мониторинга совместно с деформационными измерениями при образовании и дальнейшем раскрытии трещины гидроразрыва позволило выявить существенное отличие коэффициента ослабления звука в трещине гидроразрыва по сравнению с плоскопараллельной щелью между стеклянными пластинами, заполненной жидкостью. Для трещины гидроразрыва его значение лежит в диапазоне 12.3…13.5, в то время как для щели между стеклянными пластинами составляет величину 23.0. Причиной этого отличия может служить меньшее эффективное раскрытие естественной трещины по сравнению с измеренным, обусловленное ее шероховатостью.
Эксперименты, моделирующие заполнение трещины проппантом, в качестве которого использовался кварцевый песок, показали, что сухая трещина, заполненная песком, имеет наибольший эффективный коэффициент ослабления ультразвука из измеренных в экспериментах. Заполнение такой закрепленной трещины жидкостью уменьшает коэффициент ослабления на порядок, но он все равно остается примерно втрое большим, чем у трещины без песка.
По зависимостям, полученным в проведенных экспериментах можно оценивать величину раскрытия трещины гидроразрыва, основываясь на результатах акустического мониторинга трещины гидроразрыва.
Список литературы
Зенченко Е.В., Зенченко П.Е., Лукина А.А., Турунтаев С.Б. Исследование динамики распространения и раскрытия трещин гидроразрыва в лабораторном эксперименте акустическими методами // Динамические процессы в геосферах. 2019. № 11. С. 26–34.
Турунтаев С.Б., Зенченко Е.В., Зенченко П.Е., Тримонова М.А., Барышников Н.А., Новикова Е.В. Динамика роста трещины гидроразрыва по данным ультразвукового просвечивания в лабораторных экспериментах // Физика Земли. 2021. № 5. С. 104–119.
Groenenboom J., Fokkema J.T. Monitoring the width of hydraulic fractures, Geophysics, January–February. 1998. V. 63. № 1. P. 139–140.
Groenenboom J., van Dam D.B., de Pater C.J. Time-Lapse Ultrasonic Measurements of Laboratory Hydraulic-Fracture Growth: Tip Behavior and Width Profile // SPE J. 2001. V. 3. P. 14–24.
Liu D., Lecampion B., Blum T. Time-lapse reconstruction of the fracture front from diffracted waves arrivals in laboratory hydraulic fracture experiments // Geophysical J. International. 2020. https://doi.org/10.1093/gji/ggaa310
Medlin W.L., Massé L. Laboratory Experiments in Fracture Propagation // SPE. 1984. V. 6. P. 256–268.
Stanchits S., Surdi A., Edelman E., Suarez-Rivera R. Acoustic Emission and Ultrasonic Transmission Monitoring of Hydraulic Fracture Initiation and Growth in Rock Samples. 30th European Conference on Acoustic Emission Testing & 7th International Conference on Acoustic Emission. University of Granada. 12–15 September 2012.
Stanchits S., Surdi A., Gathogo P., Edelman E., Suarez-Rivera R. Onset of Hydraulic Fracture Initiation Monitored by Acoustic Emission and Volumetric Deformation Measurements // Rock Mech Rock Eng. 2014. V. 47. P. 1521–1532. https://doi.org/10.1007/s00603-014-0584-y
Stanchits S., Burghard J., Surdi A. Hydraulic Fracturing of Heterogeneous Rock Monitored by Acoustic Emission // Rock Mech Rock Eng. 2015. V. 48. P. 2513–2527. https://doi.org/10.1007/s00603-015-0848-1
Zoback M.D., Rummel F., Jung R., Raleigh C.B. Laboratory Hydraulic Fracturing Experiments in Intact and Pre-fractured Rock // Int. J. Rock Mech. Min. Sci. & Geomech. Abstr. 1977. V. 14. P. 49–58.
Дополнительные материалы отсутствуют.