Проблемы машиностроения и надежности машин, 2021, № 1, стр. 51-56
Исследование транспортирования порошковых присадочных материалов в зону лазерного нагрева при металлической 3D-печати
А. Ю. Албагачиев 1, *, Н. Н. Чунихин 2, Н. И. Минаева 2
1 Институт машиноведения им. А.А. Благонравова РАН
Москва, Россия
2 Российский технологический университет (МИРЭА)
Москва, Россия
* E-mail: albagachiev@yandex.ru
Поступила в редакцию 05.03.2020
Принята к публикации 22.10.2020
Аннотация
Разработана схема взаимодействия частицы порошка с парами металла. Для обеспечения гарантированного введения ППМ в область нагрева при использовании лазерного излучения, предложена модель теоретического анализа траекторий движения частиц ППМ при их транспортировании в зону построения струей газа в условиях металлической 3D-печати. Приведен сравнительный анализ расчетных данных с экспериментальными.
В настоящее время получили распространение технологические процессы металлической 3D-печати на базе селективного спекания или сплавления (SLS/DMLS/DMP/IMLS/SLM), позволяющие производить аддитивным методом различные изделия из металлов и сплавов. Аддитивные технологии с успехом можно использовать при ремонте и восстановлении различного инструмента, деталей машин и приборов [1–9].
Перспективными источниками нагрева порошковых присадочных материалов (ППМ) в таких аддитивных технологиях являются лучевые источники – лазерное излучение и электронный луч, обеспечивающие локальность воздействия при высокой концентрации энергии [1, 5–9].
Наиболее технологично ППМ транспортировать в зону построения струей газа. Способ позволяет гарантированно вводить в зону нагрева дозированное количество ППМ во всех пространственных положениях строящегося изделия [3].
Основным условием, обеспечения гарантированного введения ППМ в область нагрева, при использовании лазерного излучения, является ускорение частиц ППМ до скорости, необходимой для преодоления встречного потока паров металла (факела), формирующегося над поверхностью нагрева и, которое, согласно основному закону динамики, представляет собой силу лобового сопротивления.
На рис. 1 представлена схема взаимодействия частицы ППМ с потоком паров металла (факелом) при ее транспортировании в зону построения.
Рис. 1.
Схема взаимодействия частицы ППМ с потоком паров металла (факелом): 1 – сопло, формирующее газопорошковую струю; 2 – струя транспортирующего газа; 3 – поток паров металла (факел над поверхностью нагрева); 4 – частица ППМ; 5 – поверхность нагрева; 6 – многослойный наплавленный металл.

Принимая во внимание, изложенное можно записать
где mч – масса частицы; $\ddot {\vec {r}}$ – радиус-вектор; $\vec {F}$ – результирующая сил, действующих на частицу во встречном потоке паров металла (факеле).Проектируя равенство (1) на оси координат получим
(2)
$\left\{ {\begin{array}{*{20}{c}} {{{m}_{{{\text{ч\;}}}}}\ddot {x} = {{F}_{{\left( x \right)}}},} \\ {{{m}_{{\text{ч}}}}\ddot {z} = {{F}_{{\left( z \right)}}}.} \end{array}} \right.$Учитывая, что воздействие потока паров металла в факеле на сферическую частицу представляет собой силу лобового сопротивления, которая направлена по потоку и может быть определена по формуле F = Схωчρ1(u1 – uч0)2/2, где Сх – безразмерный коэффициент лобового сопротивления частицы; ωч – площадь поперечного сечения частицы, м2; (u1 – uч0) – относительная скорость движения паров металла в факеле; u1 – около частицы; uч0 – скорость частицы, м/с; ρ1 – плотность паров, кг/м3 можем записать
(3)
$\left\{ {\begin{array}{*{20}{c}} {{{m}_{{{\text{ч\;}}}}}\ddot {x} = \frac{{{{C}_{x}}{{{\omega }}_{{\text{ч}}}}{{{\rho }}_{1}}}}{2}{{{\left[ {{{u}_{1}} - \left( {{{{\dot {x}}}_{0}}\sin {\delta } - {\text{\;}}{{{\dot {z}}}_{0}}\cos {\delta }} \right)} \right]}}^{2}}\sin {\delta },~~~} \\ {{{m}_{{{\text{ч\;}}}}}\ddot {z} = - \frac{{{{C}_{x}}{{{\omega }}_{{\text{ч}}}}{{{\rho }}_{1}}}}{2}{{{\left[ {{{u}_{1}} - \left( {{{{\dot {x}}}_{0}}\sin {\delta } - {{{\dot {z}}}_{0}}\cos {\delta }} \right)} \right]}}^{2}}\cos {\delta }.} \end{array}} \right.$Введя обозначения: $\frac{{{{C}_{x}}{{{\omega }}_{{\text{ч}}}}{{{\rho }}_{1}}}}{2} = {\gamma }$; ${{u}_{1}} - \left( {{{{\dot {x}}}_{0}}\sin \delta - {{{\dot {z}}}_{0}}\cos \delta } \right)$ = k, получим
(4)
$\left\{ {\begin{array}{*{20}{c}} {{{m}_{{{\text{ч\;}}}}}\ddot {x} = \gamma {{k}^{2}}\sin {\delta },} \\ {{{m}_{{\text{ч}}}}\ddot {z} = - \gamma {{k}^{2}}\cos {\delta }.} \end{array}} \right.$Дифференциальные уравнения (4) записаны в терминах скорости
Однако, для нахождения уравнений движения частицы ППМ, описывающих ее взаимодействие с потоком паров металла в факеле, необходимо (4) представить в терминах времени $\ddot {x} = {{f}_{{\left( {\tau } \right)}}}$; $\ddot {z} = {{f}_{{\left( {\tau } \right)}}}$.
После решения системы уравнений (4) получим уравнения движения частицы ППМ в потоке паров металла в виде
(5)
$\left\{ {\begin{array}{*{20}{c}} {{{x}_{{\left( {\tau } \right)}}} = {{x}_{0}} + {{{\dot {x}}}_{0}}{\tau } - \sin {\delta }\frac{m}{{\gamma }}\ln \left( {\frac{{\gamma }}{m}k{\tau } + 1} \right) + \sin {\delta }k{\tau },} \\ {{{z}_{{\left( \tau \right)}}} = {{z}_{0}} + {{{\dot {z}}}_{0}}{\tau } + \cos {\delta }\frac{m}{{\gamma }}\ln \left( {\frac{{\gamma }}{m}k{\tau } + 1} \right) - \cos {\delta }k{\tau },} \end{array}} \right.$Произведя необходимые преобразования и вычисления времени взаимодействия частицы с потоком паров металла, координат точки вхождения частицы ППМ в поток паров металла, а также учитывая, что ${{\dot {x}}_{0}} = {{u}_{{{{{\text{ч}}}_{{\text{0}}}}}}}\sin {{\alpha }_{0}}$; ${{\dot {z}}_{0}} = {{u}_{{{{{\text{ч}}}_{{\text{0}}}}}}}\cos {{\alpha }_{0}}$; масса частицы ППМ ${{m}_{{\text{ч}}}} = \frac{1}{6}\pi d_{{\text{ч}}}^{{\text{3}}}{{\rho }_{{\text{ч}}}}$, а ее площадь поперечного сечения $\omega = \frac{{\pi d_{{\text{ч}}}^{{\text{2}}}}}{4}$, получим
(6)
$\begin{gathered} + \;\sin \delta ({{u}_{1}} + {{u}_{{{{{\text{ч}}}_{0}}}}}\cos ({{\alpha }_{0}} + \delta ))\tau , \\ {{z}_{{(\tau )}}} = \frac{{H\sin \delta \cos {{\alpha }_{0}}}}{{\sin ({{\alpha }_{0}} + \delta )}} + {{u}_{{{{{\text{ч}}}_{0}}}}}\cos {{\alpha }_{0}}\tau - \\ \end{gathered} $Экспериментальная проверка уравнений (6) затруднительна, поскольку яркость паров металла в факеле выше, чем яркость свечения транспортируемых в зону построения частиц ППМ. Поэтому проверку производили на модели при исследовании траекторий движения частиц в струе прозрачного газа – аргона, имитирующего поток паров металла в факеле, по фотографиям треков частиц ППМ.
На рис. 2 приведены фотографии траекторий движения частиц ППМ (железа) при различных скоростях истечения газа, имитирующего поток паров металла в факеле. Скорость движения частиц ППМ составляет uч0 = 2.7 м/с.
Рис. 2.
Внешний вид траекторий движения частиц ППМ при разных скоростях истечения газа – u1, имитирующего поток паров металла в факеле (а) – скорость газа u1 = 0; (б) – скорость газа u1 = 28 м/с; (в) – скорость газа u1 = 45 м/с.
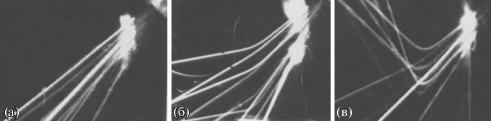
Оценку применимости уравнений (6) в реальных условиях многослойной наплавки производили путем сравнения теоретических и экспериментальных углов вылета частиц ППМ на участке, примыкающем к светящейся части потока паров металла в факеле.
Теоретический угол вылета частиц β определяем по формуле
(7)
$\beta = \operatorname{arctg} \frac{{{{{\dot {z}}}_{{\left( \tau \right)}}}}}{{{{{\dot {x}}}_{{\left( \tau \right)}}}}},$Принимая во внимание вышеизложенное, и производя соответствующие преобразования, получим расчетную формулу для определения угла вылета частицы ППМ из потока паров металла в факеле в виде
(8)
$\begin{gathered} \beta = \operatorname{arctg} \frac{{{{u}_{{{{{\text{ч}}}_{0}}}}}\cos {{\alpha }_{0}} + \frac{{3{{C}_{x}}{{\rho }_{1}}}}{{4{{d}_{{\text{ч}}}}{{\rho }_{{\text{ч}}}}}}}}{{{{u}_{{{{{\text{ч}}}_{0}}}}}\sin {{\alpha }_{0}} + \frac{{3{{C}_{x}}{{\rho }_{1}}}}{{4{{d}_{{\text{ч}}}}{{\rho }_{{\text{ч}}}}}}}} \times \\ \times \;\frac{{[{{u}_{1}} + {{u}_{{{{{\text{ч}}}_{0}}}}}\cos ({{\alpha }_{0}} + \delta )][{{u}_{{{{{\text{ч}}}_{0}}}}}\cos {{\alpha }_{0}} - \cos \delta ({{u}_{1}} + {{u}_{{{{{\text{ч}}}_{0}}}}}\cos ({{\alpha }_{0}} + \delta ))]\tau }}{{[{{u}_{1}} + {{u}_{{{{{\text{ч}}}_{0}}}}}\cos ({{\alpha }_{0}} + \delta )][{{u}_{{{{{\text{ч}}}_{0}}}}}\sin {{\alpha }_{0}} - \sin \delta ({{u}_{1}} + {{u}_{{{{{\text{ч}}}_{0}}}}}\cos ({{\alpha }_{0}} + \delta ))]\tau }}. \\ \end{gathered} $Экспериментально угол вылета частиц ППМ из потока паров металла β определяли фотографированием траекторий движения частиц. С целью исключения искажения процесса взаимодействия частиц ППМ с потоком паров металла в факеле, частицами, отраженными от нагреваемой поверхности, струю транспортирующего газа с частицами ППМ направляли параллельно этой поверхности. Фотографии траекторий движения частиц ППМ, нагретых лазерным излучением, представлены на рис. 3.
Рис. 3.
Внешний вид траекторий движения частиц ППМ, нагретых излучением лазера; (а) – без взаимодействия с потоком паров металла в факеле (мишень – кварцевое стекло); (б) – прошедших сквозь поток паров металла в факеле (мишень – технически чистое железо)).
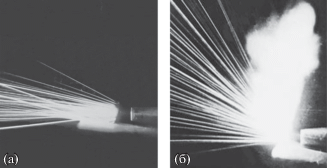
На рис. 4 представлены расчетно-экспериментальные зависимости угла вылета частиц ППМ из потока паров металла β от их начальной скорости ${{u}_{{{{{\text{ч}}}_{0}}}}}$.
Рис. 4.
Зависимость угла вылета частицы от начальной скорости 1 – экспериментальная; 2 – расчетная по уравнению (8).
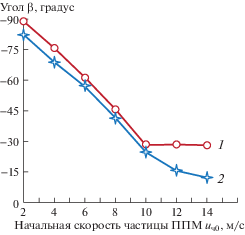
Результаты экспериментальных исследований и полученные расчетом (рис. 4) показывают, что минимальное отклонение траекторий движения частиц ППМ из технического железа диаметром 0.03–0.05 мм достигается в диапазоне их скоростей 9‒10 м/с. Нагрев осуществлялся лазерным излучением ОКГ специализированной установки LRS-50 на режиме: энергия в импульсе 10–12 Дж; дефокусировка 3 мм; длительность импульса 4 × 10–3 c; форма импульса прямоугольная, расход транспортирующего газа – аргона (8.0–8.1) × 10–5 м3/с; диаметр сопла, формирующий газопорошковую струю 1.5 мм, срез сопла расположен на расстоянии 4 мм от центра поверхности нагрева.
Данные экспериментальных исследований и результаты, полученные расчетом, показывают, что расхождение экспериментальных данных и теоретических расчетов составляют 10–15%. Это дает основание полагать, что уравнение (8) приемлемо для теоретического анализа траекторий движения частиц ППМ при их транспортировании в зону построения струей газа в условиях металлической 3D-печати.
Важным обстоятельством, следующим из решения этой задачи, является то, что производительность процесса металлической 3D-печати зависит от начальной скорости движения ППМ, транспортируемого в зону получения изделия, что должно учитываться при выборе режимов аддитивного процесса.
Проведенный анализ и полученное решение задачи о взаимодействии частиц порошковых материалов, с потоком паров металла в условиях лазерного нагрева, позволяет определять расчетным методом один из основных технологических параметров аддитивного процесса – производительность процесса транспортирования присадочного материала в зону построения при металлической 3D-печати.
Список литературы
Гибсон Я., Розен Д., Стакер Б. Технологии аддитивного производства. Трехмерная печать, быстрое прототипирование и прямое цифровое производство. 2-е изд. М.: Техносфера, 2016. 656 с.
Зубков А. Технологии DMT для 3D-печати металлических изделий. Control Engineering Россия, Август 2017. № 4 (70).
Чунихин Н.Н. Восстановление прецизионного инструмента 3D-печатью с использованием импульсного лазерного нагрева. Научные труды VI Международной научной конференции “Фундаментальные исследования и инновационные технологии в машиностроении”. М.: ИМАШ РАН, 2019. С. 446.
Springer H., Raabe D. Rapid alloy prototyping: Compositional and thermomechanical high throughput bulk combinatorial design of structural materials based on the example of 30Mn1.2CxAl triplex steels // Acta Materialia. 2012. V. 60. P. 4950.
Jagle E.A., Choi P.P., Humbeeck J., Raabe D. Precipitation and austenite reversion behavior of a maraging steel produced by selective laser melting // J. Mater. Res. 2014. V. 29. № 17. P. 2072.
Albagachiev A.Yu., Privezentsev V.I., Mamedova I.Yu. Pulse Laser Welding in the Assembly of Nonferrous and Mineral Components // Russian Engineering Research, 2019. V. 39. № 1. P. 22.
Shishkovsky I.V., Nazarov A.P., Kotoban D.V., Kakovkina N.G. Comparison of additive technologies for gradient aerospace part fabrication from nickel based superalloys. P. 221245. Book Chapter in: M. Aliofkhazraei (Ed.) Superalloys, InTech Publ. 2015. 344 p. https://doi.org/10.5772/61121.
Raabe D., Springer H., Gutierrez Urrutia I. et al. Alloy Design, Combinatorial Synthesis, and Microstructure Property Relations for Low Density FeMnAlC Austenitic Steels // JOM. 2014. V. 66. P. 1845.
Knoll H., Ocylok S., Weisheit A. et al. Combinatorial Alloy Design by Laser Additive Manufacturing // Steel research international. 2017. https://doi.org/10.1002/srin.201600416
Дополнительные материалы отсутствуют.
Инструменты
Проблемы машиностроения и надежности машин