Проблемы машиностроения и надежности машин, 2023, № 3, стр. 89-99
Обоснование и результаты численного моделирования струйного маслоснабжения сопряжения “цилиндр–поршень” в быстроходном четырехтактном двигателе внутреннего сгорания
С. В. Путинцев 1, С. А. Аникин 2, С. С. Стрельникова 3, *
1 Московский государственный технический университет им. Н.Э. Баумана
Москва, Россия
2 Военная академия воздушно-космической обороны им. Г.К. Жукова
Тверь, Россия
3 Институт машиноведения им. А.А. Благонравова РАН
Москва, Россия
* E-mail: sofya.s.strelnikova@yandex.ru
Поступила в редакцию 09.11.2022
После доработки 08.02.2023
Принята к публикации 20.02.2023
- EDN: PQUTRI
- DOI: 10.31857/S023571192303015X
Аннотация
В статье дано научное обоснование метода расчета и моделирования одного из малоизученных аспектов маслоснабжения, а именно: струйной подачи моторного масла из зазоров вращающегося шатунного подшипника коленчатого вала в сопряжение “цилиндр–поршень” быстроходного четырехтактного дизеля универсального назначения. Результатом моделирования явились представленные в настоящей статье визуализация траектории и зон попадания масла на поверхности трения деталей цилиндропоршневой группы, а также количественная оценка объемов масла в этих зонах и пространстве картера. Метод моделирования и результаты его применения могут представлять как научный, так и практический интерес для специалистов в области проектирования систем смазки и обеспечения надежности поршневых машин.
Гарантированное и рационально организованное маслоснабжение, рассматриваемое как совокупность способов и технических решений, обеспечивающих подвод смазочного материала к зонам трения и изнашивания деталей, является непременным условием энергоэкономичной и надежной работы машин, принцип действия которых не основан на трении. Сказанное в полной мере относится к двигателям внутреннего сгорания (ДВС), наиболее энергоемким сопряжением которых является цилиндропоршневая группа (ЦПГ) вообще и сопряжение “цилиндр–поршень”, в особенности. Известно, что потери на трение в ЦПГ вносят наибольший вклад в общие механические потери быстроходных поршневых двигателей [1, 2]. Причиной количественного преобладания механических потерь в этой группе деталей является несовершенство маслоснабжения последних, осуществляемое в меньшей степени за счет масляного тумана, а в большей степени путем выброса масла из зазоров вращающегося шатунного подшипника [3, 4]. Несовершенство подачи масла за счет разбрызгивания связано со спецификой конструкции и кинематики традиционного кривошипно-шатунного механизма (КШМ). Даже визуально прогнозируемая траектория полета единичной масляной струи под действием давления масла в зазоре шатунного подшипника и центробежных сил инерции при вращения кривошипа показывает, что масляные струи должны попадать в основном на одну из двух противолежащих в плоскости качания шатуна сторон внутренней поверхности цилиндра (так называемую ненагруженную сторону) цилиндра, оставляя другую (нагруженную) сторону в состоянии дефицита смазки. Эта аномалия подачи масла была обнаружена путем прямых измерений количества масла, удаляемого поршневыми кольцами со стенок цилиндра в режиме прокручивания поршневого двигателя от внешнего источника, т.е. в условиях равной нагрузки на левую и правую стороны стенки цилиндра в плоскости качания шатуна [5]. Косвенное свидетельство такого несовершенства маслоснабжения деталей ЦПГ, проявляющееся в асимметрии, или, точнее, в несоответствии количества подаваемого в цилиндр масла характеру и уровню нагружения сторон цилиндра боковой силой поршня, часто наблюдается в эксплуатации поршневых двигателей в виде разницы интенсивности износа противоположных стороны цилиндра и юбки поршня в плоскости качания шатуна [6–8].
Случаи повреждения от износа и заедания юбок поршней, “сухая” поверхность трения цилиндров, появление цвета побежалости на поршневом пальце, обнаруживаемые после разборки и осмотра вышедших из строя деталей ЦПГ [9], указывают на нерешенную проблему масляного голодания и необходимость более пристального изучения процесса подачи масла на трущиеся поверхности деталей. После выявления ограничений экспериментальных методов визуализации подачи масла к деталям ЦПГ в условиях высокой скорости вращения [5] выбор был сделан в пользу метода математического моделирования рассматриваемого процесса.
Из всех источников (или способов) подачи моторного масла на поверхности трения деталей ЦПГ в быстроходных четырехтактных поршневых двигателях [2], а именно: 1 – конденсации капель масла из масляного тумана; 2 – разбрызгивания масла с помощью ковша, расположенного на крышке шатунного подшипника; 3 – инерционного сброса масла с внутренней поверхности днища поршня, когда последний останавливается в нижней мертвой точке (НМТ); 4 – подачи масляной струи из специального канала в стержне шатуна; 5 – разбрызгивания масла из зазоров неподвижного коренного подшипника вращающимися поверхностями щек и противовесов кривошипа коленчатого вала и, наконец; 6 – выброса масла из зазоров вращающегося шатунного подшипника, в этой статье рассматривается только последний из шести вышеперечисленных источников маслоснабжения ЦПГ. Такой выбор обусловлен, во-первых, гарантированным наличием этого источника подачи масла в любой конструкции поршневого двигателя с традиционным КШМ, чего нельзя сказать, например, об источниках 2–4; во-вторых, этот выбор оправдан наибольшим (особенно по сравнению с первым источником) вкладом выброса масляных струй из зазора вращающегося шатунного подшипника в подачу масла к основным трущимся поверхностям деталей ЦПГ, что непосредственно следует из простого анализа геометрических соотношений в КШМ, указывающего на: 1) максимальную близость верхнего полукруга орбиты центральной оси шатунной шейки к поверхностям трения цилиндра и поршня; 2) пересечение траекториями масляных струй в плоскости качания шатуна зоны внутренней поверхности цилиндра, воспринимающей боковую силу поршня, что не очевидно в случае источника 5.
В результате экспериментов на макетной установке, созданной на базе малоразмерного быстроходного дизеля с оптически прозрачным цилиндром и позволяющей за счет этого визуально наблюдать образование струи в зазорах и специальных каналах подачи масла системы смазки, обнаружено, что одиночная струя масла выбрасывается из точки максимального зазора, возникающего в результате смещения шейки вала под действием приложенной внешней нагрузки.
Задача расчетного определения координаты этой точки поставлена и решена в настоящей статье в первом приближении на основе применения положений механики твердого тела, а во втором приближении – путем уточнения полученного решения с использованием положений гидродинамической теории смазки. Найденный таким образом массив координат точки выброса масляной струи для рабочего цикла четырехтактного поршневого двигателя позволил на основе использования разработанных математических моделей рассчитать не только траекторию, но и количество масла, попадающего со струей в характерные зоны трения ЦПГ, включая области, нуждающиеся в смазке для минимизации трения, износа и снижения риска задира. Результаты численного моделирования процесса струйной подачи масла, полученные для входных данных одноцилиндрового быстроходного четырехтактного дизеля, подтвердили экспериментально наблюдаемую аномалию подачи масла в цилиндр, которая заключается в том, что на нагруженную внутреннюю сторону (полуповерхность) цилиндра поступает значимо меньше масла, чем на противолежащую ненагруженную сторону. Исследование дало возможность впервые оценить c помощью расчета количественные соотношения объемов масла, попадающего в основные зоны трения и изнашивания деталей ЦПГ. Применение разработанной компьютерной программы моделирования процесса струйной подачи масла к деталям ЦПГ позволяет получать информацию о влиянии на этот процесс большого числа факторов, включая вязкость и температуру масла, скоростной и нагрузочный режимы работы двигателя, конструкцию его ЦПГ и КШМ, что открывает дополнительные возможности повышения топливной экономичности и надежности двигателя.
Цель настоящего исследования состояла в определении количества (объема) масла, попавшего за время рабочего цикла в основные зоны трения и изнашивания деталей ЦПГ за счет доминирующего источника маслоснабжения этой группы деталей – выброса масла из зазоров вращающегося шатунного подшипника.
Задачи, решаемые для достижения поставленной цели: 1. Составление и решение уравнений механики твердого тела для определения угловой координаты точки выброса струи масла из зазора вращающегося шатунного подшипника; 2. Разработка математической модели, описывающей траекторию полета струи масла от точки выброса до точки омывания поверхности трения детали; 3. Создание компьютерной программы, реализующей математическую модель по п. 2 и проведение с ее помощью моделирования процесса струйного маслоснабжения деталей ЦПГ быстроходного ДВС.
Методы решения задач. Решение задачи 1 было разделено на два этапа (или два приближения): этап 1 – получение математического выражения для угловой координаты точки выброса масляной струи из зазора вращающегося шатунного подшипника без учета влияния гидродинамических сил на положение вала относительно опоры в шатунном подшипнике; этап 2 – корректировка решения, полученного на этапе 1, на основе учета влияния гидродинамической реакции слоя масла в зазоре на положение вала в шатунном подшипнике.
Этап 1. Решение было получено в результате применения положений механики твердого тела к расчетной схеме традиционного КШМ (рис. 1)
где γ – угловая координата точки выброса струи масла из зазора вращающегося шатунного подшипника; Qx, Qy – проекции действующей на шатунную шейку силы Q на соответствующие оси координатной системы XOY.Рис. 1.
Угловая координата точки выброса струи масла из зазора вращающегося шатунного подшипника: (a) – без учета (угол γ); (б) – с учетом (угол φ) гидродинамики.
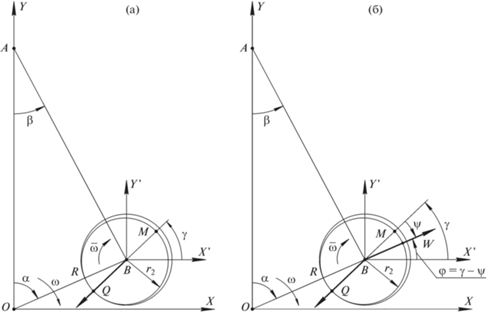
Этап 2. На этом этапе были уточнены значения угловой координаты (1), с помощью учета влияния гидродинамической реакции W, приложенной к шейке вала со стороны масляного слоя в зазоре шатунного подшипника и уравновешивающей внешнюю нагрузку Q (рис. 1). Влияние гидродинамической реакции W заключается в том, что она вызывает дополнительное угловое смещение точки максимального зазора в направлении вращения вала на угол ψ, называемый углом нагрузки (рис. 1). В результате этого углового смещения место истечения масляной струи переходит из точки M в точку N, которая характеризуется угловой координатой ${{\varphi }} = {{\gamma }} - {{\psi }}$.
Расчетное определение угла нагрузки ψ было получено на основе использования готовых выражений для тангенса этого угла, представленных в главе “Радиальные подшипники” работы [10] отдельно для решения Рейнольдса (модель бесконечно длинного подшипника) и решения Мичелла (модель бесконечно короткого подшипника) – выражения (2) и (3) соответственно
(2)
$\operatorname{tg} \psi = \frac{{2{{{\left( {1 - {{\varepsilon }^{2}}} \right)}}^{{\frac{1}{2}}}}\left[ {\sin \xi - \left( {\pi + \xi } \right)\cos \xi } \right]}}{{\varepsilon {{{\left( {1 + \cos \xi } \right)}}^{2}}}};$(3)
$\operatorname{tg} \psi = \frac{\pi }{4}\frac{{{{{\left( {1 - {{\varepsilon }^{2}}} \right)}}^{{\frac{1}{2}}}}}}{\varepsilon },$Численные выражения величин ε и ξ находили из представленных в работе [10] табличных массивов этих параметров на основе известных, определенных в ходе динамического расчета значений внешней нагрузки Q, а также решения уравнений гидродинамического равновесия шатунной шейки на слое масла в зазоре шатунного подшипника согласно первой и второй модели – выражения (4) и (5) соответственно
где μ – динамическая вязкость моторного масла; ${v}$ – линейная скорость вращения шатунной шейки; l, r – осевая длина и радиус шатунной шейки соответственно; с – радиальный зазор сопряжения “шатунная шейка–вкладыши кривошипной головки шатуна”; W* – относительная (безразмерная) функция гидродинамической реакции слоя масла в зазоре шатунного подшипника, определяемая согласно [10] для моделей бесконечно длинного и узкого подшипников зависимостями (6) и (7) соответственно(6)
$W* = \frac{{\varepsilon {{{\left( {1 + \cos \xi } \right)}}^{2}}}}{{2\left( {1 - {{\varepsilon }^{2}}} \right)\left( {1 + \varepsilon \cos \xi } \right)}}\sqrt {1 + {{{\operatorname{tg} }}^{2}}\psi } ;$(7)
$W* = \frac{\pi }{4}\frac{\varepsilon }{{{{{\left( {1 - {{\varepsilon }^{2}}} \right)}}^{2}}}}{{\left[ {\left( {\frac{{16}}{\pi } - 1} \right){{\varepsilon }^{2}} + 1} \right]}^{{\frac{1}{2}}}}.$Линейная скорость вращения шатунной шейки относительно кривошипной головки шатуна ${v}$, входящая в числитель правых частей уравнений равновесия (4) и (5), отличается от таковой для кривошипа и зависит от угловой скорости вращения коленчатого вала двигателя ω, радиуса шатунной шейки r, угла поворота коленчатого вала (ПКВ) α и постоянной КШМ λ, равной отношению радиуса кривошипа R к длине шатуна L (рис. 1), определяясь формулой
Решение задачи 2 базировали на расчетной схеме (рис. 2), позволяющей определять вектор скорости движения струи масла ${{{v}}_{o}}$, выбрасываемой из зазора вращающегося шатунного подшипника, с помощью выражений для компонентов (векторов) скорости ${{{v}}_{p}}$ и ${{{v}}_{c}}$, обусловленных соответственно давлением масла и вращением шатунной шейки
Для решения задачи 3 струя моторного масла, выбрасываемая из точки максимального зазора вращающегося шатунного подшипника М, была представлена набором математических точек, совершающих сложное движение в плоскости, касательной к торцовой поверхности кривошипной головки шатуна и параллельной плоскости его качания (рис. 3).
Рис. 3.
Модель набора математических точек, используемая для оценки количественных (а) и визуальных (б) характеристик струи масла.
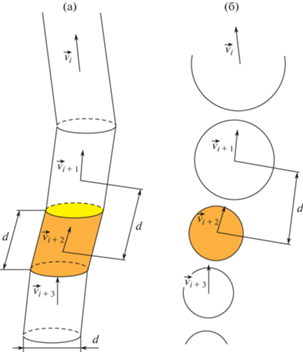
В рамках этой модели струя была разделена на условные порции в соответствии с шагом расчета по времени (углу α ПКВ). Каждая математическая точка в наборе представляла собой элементарную часть струи, соизмеримую по размеру с диаметром отверстия d, вписываемого в максимальный зазор шатунного подшипника (рис. 3).
Объем элементарной порции масла, образовавшейся за период времени ΔT, определялся как
где S – площадь сечения, через которое вытекает масляная струя.Общий объем масла в струе V находили путем умножения объема элементарной порции масла на количество порций в струе. Поскольку на каждом шаге расчета объем элементарной порции масла мог быть разным, постольку для наглядности и дополнительной информации было решено визуализировать масляную струю в виде кругов разного диаметра, размер которых пропорционален объему масляной порции (рис. 3).
Поверхности трения ЦПГ и КШМ, на которые потенциально могла попадать масляная струя, были разделены на восемь характерных зон: 1 – нагруженная сторона цилиндра (H); 2 – ненагруженная сторона цилиндра (НН); 3 – внутренняя поверхность юбки поршня на нагруженной стороне цилиндра; 4 – внутренняя поверхность юбки поршня на ненагруженной стороне цилиндра; 5 – внутренняя поверхность головки поршня; 6 – поршневой палец; 7 – картер; 8 – внутреннее пространство картера. Объем масла, попавшего в каждую из этих зон, определялся отдельно для каждого такта и в целом для полного рабочего цикла четырехтактного ДВС.
Описанные положения и расчетные модели составили математическую основу разработанной и отлаженной в ходе настоящего исследования компьютерной программы CSJet (Crank Shaft Jet – струя масла из коленчатого вала), которая позволяет выполнять численное моделирование процесса струйной подачи масла из зазоров вращающегося шатунного подшипника к деталям ЦПГ.
Результаты моделирования. Обсуждение. Задача моделирования состояла в определении количества (объема) моторного масла, попавшего в восемь характерных зон трения, износа и охлаждения ЦПГ за счет выброса струй масла из зазоров вращающегося шатунного подшипника. Объектом исследования выступал быстроходный четырехтактный дизель универсального назначения 1Ч 8.5/8.0, основные технические характеристики и показатели которого даны в табл. 1.
Таблица 1.
Технические характеристики (входные данные) к расчету процесса струйной подачи масла в ЦПГ дизеля 1Ч 8.5/8.0
Наименование | Значение |
---|---|
Частота вращения коленчатого вала, мин–1 | 3000 |
Давление масла, бар | 4 |
Температура масла, °С | 80 |
Плотность масла при 20°С, кг/м3 | 890 |
Кинематическая вязкость масла при 100°С, сСт | 10 |
Масса поршня, кг | 0.813 |
Масса шатуна, кг | 0.987 |
Радиус кривошипа, мм | 40 |
Длина шатуна, мм | 136 |
Диаметр поршня, мм | 85 |
Ход поршня, мм | 80 |
Длина цилиндра, мм | 153 |
Диаметр шатунной шейки, мм | 50 |
Длина шатунной шейки, мм | 21 |
Диаметральный зазор сопряжения “шатунная шейка–вкладыши”, мм | 0.025 |
В качестве расчетного режима была выбрана работа дизеля на постоянных мощности и частоте вращения (7 кВт и 3000 мин–1 соответственно) при использовании последнего в качестве силового агрегата электрогенератора переменного тока.
Результаты моделирования показали, что подавляющая часть (до 86%) общего объема масла, выброшенного за время рабочего цикла из зазоров вращающегося шатунного подшипника (рис. 4), попадает на внутреннюю поверхность стенок картера двигателя и, таким образом, напрямую в маслоснабжении трущихся деталей ЦПГ не участвует.
Рис. 4.
Распределение объема масла, выброшенного из зазоров вращающегося шатунного подшипника за рабочий цикл дизеля 1Ч 8.5/8.0, по характерным зонам 1–8 ЦПГ и КШМ.
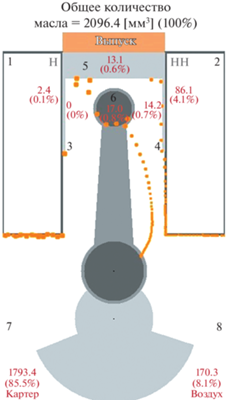
Косвенное участие этого объема масла, а также объема масла, не успевшего достичь поверхностей деталей ЦПГ и КШМ (округленно 8%), в смазывании движущихся сопряжений может проявляться лишь в формировании масляного тумана после факта соударения струй масла о неподвижную поверхность той или иной детали. Непосредственно в зоны трущихся сопряжений ЦПГ “юбка поршня–цилиндр” и “поршневой палец–втулка поршневой головки шатуна” поступает весьма незначительная доля (около 5%) общего объема вылетающих из вращающегося шатунного подшипника струй масла. Немногим более 1% масла достигает со струей внутренних поверхностей стенок головки и юбки поршня, участвуя в его охлаждении.
Результаты расчета в режиме “Такт за тактом” показали, что масло, выбрасываемое из зазоров вращающегося шатунного подшипника, попадает в зоны деталей ЦПГ только в течение двух тактов рабочего цикла, а именно: на такте “Выпуск” и такте “Впуск”, когда сектор окружности шатунной шейки, охватывающий точки выброса струи масла из шатунного подшипника, направлен на ненагруженную сторону (НН) стенки цилиндра по ходу вращения кривошипа (рис. 5), (табл. 2).
Рис. 5.
Визуализация процесса струйной подачи масла из зазоров шатунного подшипника к деталям ЦПГ в течение (по тактам) рабочего цикла дизеля 1Ч 8.5/8.0.
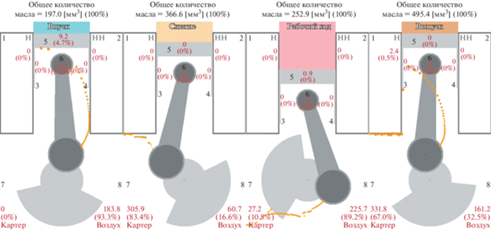
Таблица 2.
Результат расчета объемов масла в зонах 1–8 ЦПГ и КШМ в конце каждого из четырех тактов рабочего цикла дизеля 1Ч 8.5/8.0
Номер и название такта | Всего за время такта | Абсолютное мм3 и относительное (%) количество масла, попавшее в зону ЦПГ и КШМ со струей | |||||||
---|---|---|---|---|---|---|---|---|---|
зона | |||||||||
1 | 2 | 3 | 4 | 5 | 6 | 7 | 8 | ||
1 Впуск | 668.6 (100) | 0.0 (0.0) | 86.1 (12.9) | 0.0 (0.0) | 14.2 (2.1) | 13.1 (2.0) | 4.0 (0.6) | 463.0 (69.3) | 88.1 (13.2) |
2 Сжатие | 483.6 (100) | 0.0 (0.0) | 0.0 (0.0) | 0.0 (0.0) | 0.0 (0.0) | 0.0 (0.0) | 0.0 (0.0) | 385.0 (79.6) | 98.6 (20.4) |
3 Расширение | 426.8 (100) | 0.0 (0.0) | 0.0 (0.0) | 0.0 (0.0) | 0.0 (0.0) | 0.0 (0.0) | 0.0 (0.0) | 335.3 (78.6) | 91.4 (21.4) |
4 Выпуск | 517.4 (100) | 2.4 (0.5) | 0.0 (0.0) | 0.0 (0.0) | 0.0 (0.0) | 0.0 (0.0) | 13.0 (2.5) | 331.8 (64.1) | 170.3 (32.9) |
Сопоставление количества смазочного материала, попавшего за время рабочего цикла на нагруженную (Н) и ненагруженную (НН) стороны стенки цилиндра (рис. 4), с результатами выполненных оценок минимально необходимого для предотвращения масляного голодания объема моторного масла в этой зоне смазывания для данного дизеля показало, что объема смазочного материала на нагруженной стороне стенки цилиндра (2.4 мм3) явно недостаточно для обеспечения благоприятного гидродинамического режима смазки в сопряжении “цилиндр–юбка поршня”.
С учетом актуальности тренда, связанного с переходом на применение в современных поршневых и гибридных двигателях маловязких моторных масел [11], особый интерес представляло получение информации о влиянии высокотемпературной (при 100°С) кинематической вязкости масла ν100 на процесс струйного маслоснабжения деталей ЦПГ. Изменение указанной вязкости задавали в широком диапазоне ее значений, а именно: от 2 до 14 сСт. Контрольными выходными величинами были взяты: 1) абсолютное (в мм3) общее количество масла, выброшенного со струей в течение рабочего цикла q0; 2) количество масла, попавшего за это время в зоны трения деталей ЦПГ (т.е. в зоны 1–6) q1–6.
По мере линейного уменьшения вязкости моторного масла общее количество масла, выбрасываемого струей, и количество масла, подаваемого струей к частям ЦПГ, нелинейно возрастают (рис. 6). Анализ показал, что такое изменение q0 и q1–6 объясняется влиянием вязкости масла, как меры внутреннего трения слоев жидкости, на обусловленную вращением шатунной шейки составляющую скорости струи ${{{v}}_{{\text{c}}}}$: при уменьшении трения внутри масла среднее значение компоненты скорости струи масла ${{{v}}_{{\text{c}}}}$ увеличивается.
Рис. 6.
Влияние изменения высокотемпературной вязкости моторного масла ν100 на общее количество масла q0, выбрасываемого струей в течение рабочего цикла дизельного двигателя, и количество масла q1–6, подаваемого за то же время струей на поверхности трения ЦПГ.
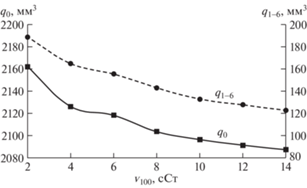
Заключение. Численное моделирование процесса маслоснабжения деталей ЦПГ, осуществляемого за счет выброса струи масла из зазоров вращающегося шатунного подшипника быстроходного четырехтактного дизельного двигателя, показалo, что в течение его рабочего цикла: 1) из общего объема масла, подаваемого со струей (100%), на поверхности трения деталей ЦПГ поступает только около 15% этого количества; 2) существует аномалия маслоснабжения деталей ЦПГ, при которой на нагруженную сторону стенки цилиндра подается значительно меньше смазки, чем на нагруженную сторону: в частности, 0.1% против 4.1% от общего количества масла, выбрасываемого струей, соответственно; 3) масло подается в зоны трения и охлаждения деталей ЦПГ только во время двух тактов рабочего цикла, когда точка выброса струи ориентирована при вращении коленчатого вала на ненагруженную сторону стенки цилиндра.
Исследование показало, что снижение вязкости моторного масла приводит к увеличению количества смазки, подаваемой в зоны трения деталей ЦПГ, что можно рассматривать как один из аспектов обоснования целесообразности перехода со средневязких на мало- и сверхмаловязкие моторные масла для современных быстроходных поршневых и гибридных двигателей.
Логическим продолжением исследований в этой области могут быть разработка и проверка эффективности технических решений, направленных на устранение аномалий маслоснабжения деталей ЦПГ. Кроме того, представляет практический интерес разработка метода количественного определения предельно малой вязкости моторного масла, обеспечивающей снижение потерь на трение при условии сохранения надежности работы поршневого двигателя.
Список литературы
Bedajangam S.K., Jadhav N.P. Friction losses between piston ring-liner assembly of internal combustion engine: A review // Int. J. of Scientific and Research Publications. 2013. V. 3. № 6. C. 1.
Heywood J.B. Internal combustion engine fundamentals, Second Edition. New York: McGraw-Hill Education, 2018. 1056 p.
Ganesan V. Internal combustion engines. New York: McGraw Hill Education, 2012. 573 p.
Coy R.C. Practical applications of lubrication models in engines // Tribology Int. 1998. V. 31. № 10. P. 563.
Путинцев С.В., Агеев А.Г. Экспериментальное исследование условий маслоснабжения цилиндра быстроходного четырехтактного двигателя внутреннего сгорания // Тракторы и сельхозмашины. 2016. Т. 83. № 10. С. 45.
Pulkrabek W.W. Engineering fundamentals of the internal combustion engine // J. Eng. Gas Turbines Power. 2004. V. 126. № 1. P. 198.
Xiaohua X. Influence of piston-bore clearance on second motion characteristics of piston and skirt wear // Mechanics and Industry. 2019. V. 20. № 2. P. 205.
Delprete C., Razavykia A. Piston dynamics, lubrication and tribological performance evaluation: A review // Int. J. of Engine Research. 2020. V. 21. № 5. P. 725.
Damaged pistons. How to identify and eliminate them [Электронный ресурс] // Technical brochure MS Motor Service International GmbH [2006] URL: https://www.ms-motorservice.com/en/technical-know-how/technical-information/ (дата обращения: 21.07.2022)
Cameron A. Basic Lubrication Theory. London: Ellis Horwood Ltd., 1981. 256 p.
Singh S.K., Singh S., Sehgal A.K. Impact of low viscosity engine oil on performance, fuel economy and emissions of light duty diesel engine // Conference: SAE 2016 Int. Powertrains, Fuels & Lubricants Meeting. October 17, 2016. Technical Paper, 2016-01-2316. https://doi.org/10.4271/2016-01-2316
Дополнительные материалы отсутствуют.
Инструменты
Проблемы машиностроения и надежности машин