Поверхность. Рентгеновские, синхротронные и нейтронные исследования, 2021, № 1, стр. 102-106
Карбонизация рабочих поверхностей шашек импульсного источника плазмы
А. В. Богатый a, С. А. Семенихин a, *
a Научно-исследовательский институт прикладной механики и электродинамики Московского авиационного института (национального исследовательского университета) (НИИ ПМЭ МАИ)
125080 Москва, Россия
* E-mail: riame3@sokol.ru
Поступила в редакцию 19.02.2020
После доработки 20.03.2020
Принята к публикации 27.03.2020
Аннотация
Проведено экспериментальное исследование процесса карбонизации рабочих поверхностей шашек абляционного импульсного источника плазмы с боковой подачей твердого рабочего тела. В процессе исследования рассмотрены факторы, влияющие на возникновение устойчивых углеродных образований в процессе работы источника в различных режимах. Показано, что температура шашек рабочего тела не влияет на процесс формирования устойчивых углеродных образований на их рабочих поверхностях.
ВВЕДЕНИЕ
В процессе проведения (как в России, так и за рубежом) экспериментальных исследований абляционных импульсных источников плазмы с твердым рабочим телом, в качестве которого используется политетрафторэтилен (фоторопласт-4) [1–3], было установлено, что в отдельных режимах функционирования или при некоторых размерах разрядного канала на поверхностях шашек рабочего тела появляется углеродный налет. Происходит так называемая карбонизация [4–6], которая может носить локальный характер (первый тип, рис. 1) либо занимать большую часть рабочей поверхности шашек (второй тип, рис. 2). При локальном расположении углеродной пленки источник плазмы некоторое время сохраняет свою работоспособность. Однако, поскольку данный участок шашки практически перестает вырабатываться, это приводит к изменению контуров разрядного канала, затруднению подачи шашек в канал, ухудшению характеристик и невыполнению источником плазмы своего целевого назначения.
Если же углеродный налет появился на большей части поверхности шашек, характеристики источника плазмы быстро деградируют, по истечении некоторого времени происходит фактически короткое замыкание электродов, и он прекращает функционировать (рис. 1).
Следует заметить, что после появления углеродная пленка не может быть полностью удалена с поверхности шашки при изменении режима работы источника плазмы (увеличении энергии разряда) или уменьшении объема разрядного канала за счет уменьшения расстояния между шашками (рис. 2). Для того чтобы повторно использовать такие шашки, необходимо удалить углеродный налет механическим способом.
ЭКСПЕРИМЕНТАЛЬНОЕ ИССЛЕДОВАНИЕ ПРОЦЕССА КАРБОНИЗАЦИИ ПОВЕРХНОСТИ ШАШЕК ИМПУЛЬСНОГО ИСТОЧНИКА ПЛАЗМЫ
Ускорительный канал импульсного источника плазмы с боковой подачей рабочего тела (рис. 3) образован поверхностями электродов – катода 1 и анода 2, шашек рабочего тела 3, 4 и торцевой поверхностью керамического изолятора 5. Его основные, наиболее важные размеры это: расстояние между электродами (высота канала) H, расстояние между шашками рабочего тела на входе в канал (начальная ширина канала) a, длина шашек (длина закрытой части канала) L. Эти размеры определяют начальную индуктивность ускорительного канала и его объем, от которого зависит плотность плазмы.
Рис. 3.
Ускорительный канал абляционного импульсного источника плазмы с боковой подачей рабочего тела и его основные геометрические размеры: 1 – катод; 2 – анод; 3, 4 – шашки рабочего тела; 5 – торцевая поверхность керамического изолятора; H – высота канала; a – начальная ширина канала; L – длина закрытой части канала; α – угол раскрытия шашек рабочего тела.
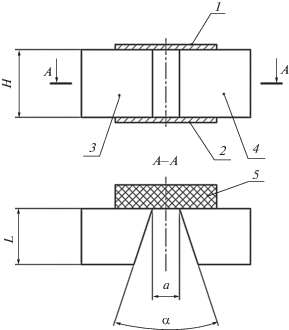
Карбонизация шашек первого типа (с локализацией зоны) – наиболее часто встречающийся тип карбонизации. Он в основном зависит от плотности энергии, выделяющейся в канале, а расположение зоны на поверхности шашки рабочего тела определяется процессами, проходящими на начальной стадии разряда [7]. Карбонизация второго типа встречается реже и обусловлена ошибками в разработке конструкции разрядного канала, вызывающими нестабильность разрядного процесса и его асимметричность. Также карбонизация этого типа наблюдается при работе источника плазмы с большой скважностью, фактически в режиме единичных импульсов, причем величина энергии разряда практически не влияет на данный процесс.
В процессе экспериментальной доводки источника изменение его интегральных характеристик наиболее легко достигается путем регулировки основных геометрических размеров ускорительного канала. Наиболее просто регулируется расстояние a между шашками рабочего тела. На рис. 4 представлены типичные зависимости единичного импульса тяги Ред, удельного импульса тяги J и тяговой эффективности от начальной ширины канала а. Видно, что больший единичный импульс тяги достигается при меньшей ширине канала, а большие удельный импульс тяги и тяговая эффективность – при большей ширине.
Рис. 4.
Зависимость характеристик источника плазмы от начальной ширины канала а [мм]: единичного импульса тяги Ред [мН · с]; удельного импульса тяги J [м/с]; тяговой эффективности η [%].
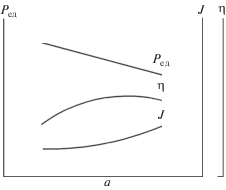
При оптимизации источника плазмы по удельному импульсу тяги путем увеличения параметра а увеличивается объем разрядного канала – снижается плотность плазмы и плотность теплового потока на шашки. Поэтому при некотором значении а возможно появление углеродной пленки на их рабочих поверхностях. В настоящей работе исследование зависимости процесса карбонизации шашек от расстояния между ними проводили на моделях источников плазмы с энергией разряда 70 и 155 Дж. Для изменения расстояния между шашками в разрядном канале был смонтирован дистанционно управляемый механизм их перемещения.
Предварительно перед исследованиями процесса карбонизации шашки проходили приработку в течение ~105 импульсов до стабилизации геометрической формы разрядного канала. Процесс карбонизации изучали при следующих режимах работы: энергия разряда 70 Дж, частота f = = 0.5, 1.0 и 1.5 Гц. Суммарная наработка источника плазмы в каждом эксперименте составляла 5000–6000 импульсов. Исследовали диапазон расстояний между шашками от 10 до 22 мм с шагом 2 мм. В результате было установлено, что при частоте работы 0.5 Гц следы карбонизации первого типа появляются при параметре а = 20 мм – так называемая “точка карбонизации” (рис. 5), а при 22 мм и более они увеличиваются в размерах. На частотах 1.0 и 1.5 Гц наблюдается та же картина. При пересчете на единицу объема разрядного канала, ограниченного рабочими поверхностями шашек, при параметре а = 20 мм средняя плотность энергии составила ≈2.7 Дж/см3.
Масса плазменного сгустка в разрядном канале пополняется за счет абляции фторопласта с рабочих поверхностей шашек рабочего тела в результате ударной ионизации, поглощения фторопластом энергии излучения плазмы и конвективного теплообмена с плазмой [8]. Имеет место как “горячая” абляция фторопласта, когда температура поверхности больше температуры абляции, так и “холодная”, с меньшей интенсивностью, когда температура поверхности меньше температуры абляции. Характерной особенностью рабочего процесса является малая длительность разрядного импульса и, соответственно, процесса ускорения, и сравнительно большая длительность паузы [9–12]. Расчеты показали, что за время разрядного импульса поток тепла от плазмы к фторопластовым шашкам проникает на очень малую глубину. На глубине 0.015 мм прирост температуры шашки составляет величину меньше 0.5% от разности температуры абляции и начальной температуры шашки. Кроме того, на протяжении длительности разрядного импульса (значительной ее части) и процесса ускорения температура поверхности шашек, соприкасающихся с плазмой, равна температуре абляции. Эти обстоятельства позволяют считать, что процесс подвода тепла носит импульсный характер [10, 11]. Единственным существенным фактором можно считать суммарную подведенную энергию, вследствие которого было сделано предположение, что процесс карбонизации шашек также зависит от начальной температуры (Тш0) шашек рабочего тела. Для проверки этой версии на электроды источника плазмы были установлены плоские нагреватели, позволяющие изменять Тш0. Контроль температуры шашек осуществляли с погрешностью ~2% в диапазоне температур 20–140°С с помощью датчиков температуры – термисторов, установленных внутри шашек рабочего тела на расстоянии ~1 мм от их рабочих поверхностей. Цель экспериментов состояла в том, чтобы с помощью предварительного нагрева шашек сдвинуть точку карбонизации в сторону больших значений объема разрядного канала. Для этого было выбрано такое расстояние между рабочими поверхностями шашек, при котором начинает проявляться карбонизация первого типа при работе источника плазмы без предварительного нагрева шашек.
На рис. 6 приведен внешний вид рабочих поверхностей шашек после работы с их предварительным нагревом до 110°С. Видно, что, как и в случае без предварительного нагрева, на рабочих поверхностях шашек присутствует углеродный налет. Аналогичные исследования процесса карбонизации шашек (без изменения их начальной температуры) были проведены на модели c энергией разряда 155 Дж (рис. 7). Исследовали диапазон расстояний между шашками от 16 до 26 мм с шагом 2 мм при постоянной энергии разряда. Измерения величины а, так же как в источнике плазмы с энергией разряда 70 Дж, проводили по средней линии.
Рис. 6.
Внешний вид шашек после работы и предварительного нагрева до 80°С при расстоянии между ними 20 мм.
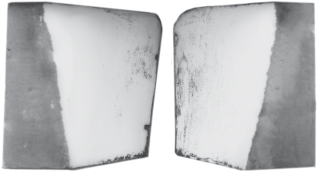
В результате проведенных экспериментов было установлено, что следы карбонизации появляются при расстоянии между шашками порядка 26 мм и, как в случае источника плазмы с энергией разряда 70 Дж, не устраняются при увеличении мощности разряда (рис. 8). При пересчете на единицу объема разрядного канала, ограниченного рабочими поверхностями шашек, при параметре а = 26 мм средняя плотность энергии составила ≈2.5 Дж/см3.
ЗАКЛЮЧЕНИЕ
Таким образом, в результате проведенных исследований процесса карбонизации рабочих поверхностей шашек было установлено, что при постоянном значении энергии разряда положение точки науглероживания определяется только расстоянием между шашками и не зависит от мощности и начальной температуры шашек рабочего тела. Можно заключить, что существует некая критическая плотность энергии, в среднем составляющая 2.6 Дж/см3 для энергии разряда в диапазоне от 70 до 155 Дж, при снижении которой начинается формирование устойчивых поверхностных углеродных пленок. Так называемая “точка карбонизации” – предельное расстояние между рабочими поверхностями шашек рабочего тела, превышение которого в краткосрочной перспективе приводит к выходу из строя абляционного импульсного плазменного источника. Полученные в результате исследований научные знания об условиях возникновения карбонизации необходимо учитывать при разработке абляционных импульсных источников плазмы, при выборе геометрических параметров разрядных каналов для обеспечения их стабильной работы.
Список литературы
Burton R.L. // Encycl. Aerospace Engin. 2010. https://doi.org/10.1002/9780470686652.eae120
Rayburn C.D., Campbell M.E., Mattick T.A. // J. Spacecraft and Rockets. 2012. V. 42. № 1. P. 161. https://doi.org/10.2514/1.15422
Wu Z., Sun G., Huang T. et al. // AIAA J. 2018. V. 56. № 8. P. 3024. https://doi.org/10.2514/1.J056272
Keidar M., Boyd I.D., Antonsen E.L. et al. // J. Propuls. Power. 2004. V. 20. № 6. P. 978. https://doi.org/10.2514/1.2471
Spanjers G.G., Bromaghim D.R., Lake L. et al. AFRL MicroPPT Development for the Small Spacecraft Propulsion // Proc. 38th AIAA/ASME/SAE/ASEE Joint Propulsion Conf. and Exhibit. Induanaopolis, 2002. AIAA 2002-3974. https://doi.org/10.2514/6.2002-3974
Gulczinski F.S., Dulligan M.J., Lake J.P., Spanjers G.G. Micropropulsion Research at AFRL // Proc. 36th AIAA/ASME/SAE/ASEE Joint Propulsion Conf. and Exhibit. Las Vegas, 2000. AIAA 2000-3255. https://doi.org/10.2514/6.2000-3255.
Antipov A.A., Bogatyy A.V., Semenov A.A. // J. Surf. Invest.: X-ray, Synchrotron Neutron Tech. 2018. V. 12. № 5. P. 1037. https://doi.org/10.1134/S1027451018050208
Богатый А.В., Дьяконов Г.А., Семенихин С.А. // Космические исследования. 2019. Т. 57. № 5. С. 332. https://doi.org/10.1134/S0023420619050017
Антропов Н.Н., Богатый А.В., Дьяконов Г.А. и др. // Вестн. ФГУП НПО им. С.А. Лавочкина. 2011. № 5. С. 30.
Антипов А.А., Богатый А.В. // Изв. РАН. Энергетика. 2017. № 3. С. 42.
Antipov A.A., Bogatyy A.V. // Procedia Engin. 2017. V. 185. P. 61.
Keidar M., Boyd I.D., Antosen E., Spanjers G.G. // J. Propuls. Power. 2004. V. 20. № 6. P. 961. https://doi.org/10.2514/1.8985
Дополнительные материалы отсутствуют.
Инструменты
Поверхность. Рентгеновские, синхротронные и нейтронные исследования