Поверхность. Рентгеновские, синхротронные и нейтронные исследования, 2021, № 2, стр. 102-112
Исследование структуры поверхностного слоя стали 40Х после черновой и получистовой механической обработки резанием
М. В. Пимонов a, *, Д. А. Романов b, c, **, Х. Чен c, ***
a Кузбасский государственный технический университет им. Т.Ф. Горбачева
650000 Кемерово, Россия
b Сибирский государственный индустриальный университет
654006 Новокузнецк, Россия
c Wenzhou University Institute of Laser and Optoelectronic Intelligent Manufacturing
325024 Wenzhou, China
* E-mail: pimonovmv@kuzstu.ru
** E-mail: romanov_da@physics.sibsiu.ru
*** E-mail: chenxizhang@wzu.edu.cn
Поступила в редакцию 12.01.2020
После доработки 17.02.2020
Принята к публикации 20.02.2020
Аннотация
Приведены результаты исследований микроструктуры, локальных полей внутренних напряжений, возникающих в поверхностном слое образцов, стали 40Х, механически обработанных в двух режимах: черновом и получистовом (снятие стружки на глубину 1.0 и 0.5 мм соответственно). Изучена внутренняя структура всех морфологических составляющих стали. Измерены и рассчитаны скалярная плотность дислокаций, ширина изгибных экстинкционных контуров, по которым затем определены амплитуда кривизны–кручения кристаллической решетки формирующихся фаз, избыточная плотность дислокаций и амплитуда внутренних напряжений на различных участках материала. В исходном состоянии матрица стали 40Х представляет собой α-фазу – твердый раствор углерода и легирующих элементов в α-Fe с ОЦК-решеткой. Морфологическими составляющими α-фазы являются пластинчатый перлит и феррит. Черновая обработка привела к образованию вторично фрагментированного перлита. После получистовой обработки образуется пластинчатый перлит с искривленными пластинами цементита.
ВВЕДЕНИЕ
В настоящее время развиваются различные технологии изготовления объемных материалов и формирования покрытий [1, 2]. Несмотря на их возможности, на финальной стадии внедрения в производство для получения поверхности определенной формы приходится использовать методы механической обработки [3, 4]. К ним относят точение [5], фрезерование [6], сверление [7], строгание [8], долбление [9], шлифование [10], протягивание [11] и другие. Кроме широко известных и часто используемых материалов возникает необходимость обработки композиционных материалов и материалов со специальными свойствами [12]. В [13] рассмотрена эффективность резки армированного волокном композиционного материала методом абразивно-водоструйной обработки. Такая контролируемая обработка гибридных полимерных композитов может быть использована для получения качественных пропилов [14]. Повышению эффективности резки нержавеющей стали при добавлении криолита посвящена работа [15]. Авторами [16] с использованием комбинационного и просвечивающего электронного микроскопа было исследовано влияние при резании флуенса на микроструктуру CVD-алмаза. Механизм движения материала, вопросы тепловыделения вблизи фаски, а также высокопроизводительное резание со скошенными вставками изучены в [17]. Процессы, протекающие при механической обработке, как правило, подвергаются математическому моделированию. Так, авторы [18] проводили моделирование эволюции износа одного абразивного зерна оксида алюминия и анализ влияния кристаллической структуры. Немногие модели механистического прогнозирования силы резания включают особенности случайного распределения абразивного зерна, что ограничивает существующие методы оптимизации для уменьшения силы резания [19]. Микроструктурная деформация на уровне зерен оказывает большое влияние на достижимую предельную точность обработки поликристаллических материалов. В [20] проведены численное моделирование и эксперименты по алмазной резке поликристаллической меди для исследования образования структур на границах зерен, формирующихся на обработанной поверхности. Обработка резанием используется для формирования правильной геометрии деталей с целью обеспечения их максимальной производительности. Однако в зависимости от используемого метода обработки резанием свойства поверхности деталей и их структура изменяются. Большая часть опубликованных к настоящему времени работ ограничивается описанием геометрии поверхности и определением ее свойств. Однако тонкая структура и морфологические составляющие материалов изучены слабо. Целью настоящей работы было исследование тонкой структуры стали 40Х после черновой и получистовой обработки методом просвечивающей электронной микроскопии.
МАТЕРИАЛ И МЕТОДИКИ ИССЛЕДОВАНИЯ
Объектом исследований была сталь 40Х после рекристаллизационного отжига при температуре 600°C в течение 60 мин. Затем образцы стали подвергали черновому и получистовому точению. Обработку осуществляли на токарном станке 16К20Ф3 с системой числового программного управления NC-210. Использовали резец фирмы Korloy с режущей пластиной марки CNMG120408-VM. Черновое точение проводили при диаметре 34 мм, глубине резания 1 мм, подаче 0.4 мм/об., количестве оборотов 650 об.–1 Получистовое точение проводили при диаметре 35 мм, глубине резания 0.5 мм, подаче 0.25 мм/об., количестве оборотов 900 об.–1 Структуру тонких фольг исследовали методом просвечивающей электронной микроскопии. Использовали электронный микроскоп ЭМ-125. Ускоряющее напряжение составляло 125 кВ. Фольги вырезали на электроискровом станке, методом электролитического утонения толщину вырезанных пластинок доводили до 0.25–0.30 мм.
РЕЗУЛЬТАТЫ ИССЛЕДОВАНИЯ И ИХ ОБСУЖДЕНИЕ
Сталь 40Х в исходном состоянии
Проведенные исследования показали, что в исходном состоянии матрица стали 40Х представляет собой α-фазу – твердый раствор углерода и легирующих элементов в α-Fe с ОЦК-решеткой. Морфологическими составляющими α-фазы являются пластинчатый перлит, объемная доля которого ~80% от объемной доли материала, и феррит, доля которого в материале ~20%. Типичные изображения феррито-перлитной структуры стали 40Х в исходном состоянии представлены на рис. 1, 2. Известно, что пластинчатый перлит часто бывает дефектным. Схемы образования дефектных структур и причины их появления обобщены и подробно рассмотрены в [21, 22]. Как видно из рисунков, в исходном состоянии стали 40Х наряду с бездефектным (идеальным) пластинчатым перлитом (рис. 1), объемная доля которого составляет 50% от объемной доли материала, присутствуют зерна с дефектными пластинами цементита. Это пластинчатый перлит с изогнутыми пластинами цементита. Одна из причин появления изогнутых карбидов цементита в пластинчатом перлите – воздействие напряжений и рост пластин цементита по механизму ветвления [23]. В феррито-перлитных сталях пластины цементита формируются преимущественно вследствие нестационарных процессов роста. Поэтому в феррито-перлитных сталях структура перлита более дефектная, чем в перлитных. Объемная доля такого типа пластинчатого перлита невелика и составляет не более 1% от объемной доли всего материала.
Рис. 1.
Электронно-микроскопическое изображение тонкой феррито-перлитной структуры стали 40Х в исходном состоянии: Ф – зерна фрагментированного феррита; П – зерно пластинчатого перлита. На вставке НФ – зерно фрагментированного феррита.
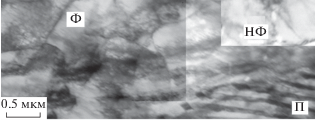
Рис. 2.
Электронно-микроскопическое изображение тонкой структуры стали 40Х в исходном состоянии: Ф – фрагментированный феррит; П – пластинчатый бездефектный перлит; ПД – пластинчатый дефектный перлит.
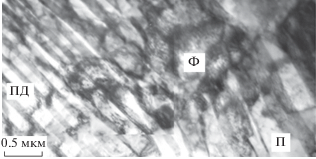
В дефектном пластинчатом перлите второго типа явно выражена дефектная субструктура пластин цементита (рис. 2). В относительно широких цементитных пластинах либо видна слоистая структура, состоящая из чередующихся полос различного контраста, либо дислокации, располагающиеся хаотически или в виде плотных дислокационных сеток. Полосчатый контраст не связан с эффектами, вызванными расслоением областей примесных атомов в кристаллической решетке цементита, и может быть обусловлен наличием планарных дефектов [24–26]. Микродифракционная картина подтверждает наличие карбидной фазы – цементита. Поскольку по виду светлопольных изображений дефектный перлит (рис. 2) мало отличается, в настоящей работе эти два типа пластинчатых перлитов объединены в один тип, названный “дефектным пластинчатым перлитом”. Объемная доля его в исходном состоянии стали 40Х составляет 20%.
К пластинчатому перлиту может быть причислен перлит, светлопольное изображение которого приведено на рис. 3. Такая картина относится либо к псевдоглобулярному перлиту [22], либо к пластинчатому перлиту, когда изображение представляет собой сечение перлитной колонии в направлении, перпендикулярном пластинам цементита. Выполненные измерения показали, что скалярная плотность дислокаций в такой структуре равна 1.88 × 1010 см–2, избыточная плотность дислокаций 1.80 × 1010 см–2, амплитуда внутренних напряжений 275 МПа. Точно такими же количественными параметрами характеризуется структура бездефектного пластинчатого перлита. Поэтому структура на рис. 3 отнесена к структуре бездефектного пластинчатого перлита. Ее объемная доля составляет 10%.
Рис. 3.
Электронно-микроскопическое изображение тонкой структуры стали 40Х в исходном состоянии, пластинчатый перлит: сечение перлитной колонии перпендикулярно пластинам цементита.
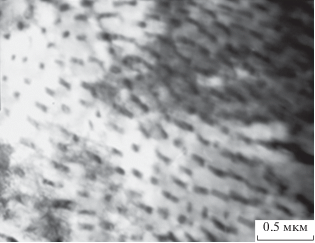
Дислокационная структура всех морфологических составляющих пластинчатого перлита представлена в основном плотными дислокационными сетками. Средняя скалярная плотность дислокаций ρ в пластинах α-фазы каждой составляющей перлита приведена в табл. 1. Как видно из таблицы, величины ρ в бездефектном и дефектном перлите близки по своим значениям, тем не менее, средняя величина ρ в бездефектном перлите несколько выше. Дислокационная структура в перлите поляризована, на что указывают изгибные экстинкционные контуры на электронно-микроскопических изображениях тонкой фольги [27, 28]. Как правило, эти контуры начинаются от границ зерен перлита, которые и являются основными причинами кривизны–кручения кристаллической решетки стали. Определены амплитуда кривизны–кручения кристаллической решетки χ и избыточная плотность дислокаций ρ± в пластинах α-фазы (феррита). Эти данные также приведены в табл. 1. В исходном состоянии в стали 40Х во всех морфологических составляющих пластинчатого перлита дислокационная структура значительно поляризована, тем не менее, везде выполняются условия: χ = χпл, ρ > ρ±, σЛ > σд (σЛ – напряжение сдвига (или “леса” дислокаций), поля напряжений, создаваемые дислокационной структурой; σд – дальнодействующие напряжения (или локальные), возникающие там, где присутствует избыточная плотность дислокаций). Как отмечалось выше, в исходном состоянии стали 40Х наряду с зернами пластинчатого перлита присутствуют зерна феррита, которые в своем объеме не содержат частиц цементита. Поэтому в феррито-перлитных сталях зерна такого феррита часто называют зернами структурно-свободного феррита [22] (рис. 1, 2). В исследуемой стали фрагменты содержат сетчатую дислокационную структуру.
Таблица 1.
Количественные параметры тонкой структуры образцов стали 40Х в исходном состоянии
Морфологическая составляющая матрицы стали | Скалярная плотность дислокаций | Избыточная плотность дислокаций | Кривизна–кручение кристаллической решетки | Амплитуда внутренних напряжений | |
---|---|---|---|---|---|
напряжения сдвига | локальные напряжения | ||||
ρ, 1010 см–2 | ρ±, 1010 см–2 | χ, см–1 | σЛ, МПа | σд, МПа | |
Пластинчатый перлит | |||||
Бездефектный | 1.88 | 1.80 | 450 | 275 | 275 |
Дефектный | 1.69 | 1.56 | 390 | 260 | 250 |
В перлите | 1.83 | 1.74 | 435 | 270 | 265 |
Феррит | |||||
Нефрагментированный | 2.43 | 2.43 | 620 | 310 | 310 |
Фрагментированный | 2.79 | 2.79 | 730 (695 – пл. 35 – упр.) |
335 | 380 (335 – пл. 45 – упр.) |
В феррите | 2.61 | 2.61 | 675 (655 – пл. 20 – упр.) |
320 | 345 (320 – пл. 25 – упр.) |
Средние в материале | 1.99 | 1.91 | 485 (480 – пл. 5 – упр.) |
289 | 285 (280 – пл. 5 – упр.) |
Исследования показали, что скалярная плотность дислокаций в феррите выше, чем в пластинчатом перлите (табл. 1). Кроме того, величина ρ в нефрагментированном феррите, хотя и незначительно, но ниже, чем во фрагментированном. Дислокационная структура, как и в пластинчатом перлите, поляризована (внутри ферритных зерен присутствуют изгибные экстинкционные контуры), однако поляризована полностью. Тем не менее, в нефрагментированном феррите выполняются условия: χ = χпл, ρ = ρ± и σЛ = σд. Это означает, что изгиб–кручение кристаллической решетки нефрагментированного феррита носит пластический характер. Иная картина складывается во фрагментированном феррите. Расчеты показали, что во фрагментах ρ < ρ±. Это означает, что во фрагментированном феррите имеет место упруго-пластический изгиб, т.е. выполняются условия: χ = χпл + χупр, а σд = $\sigma _{{\text{д}}}^{{{\text{пл}}}}$ + + $\sigma _{{\text{д}}}^{{{\text{упр}}}}.$
“Черновая” обработка
Первой отличительной особенностью структуры пластинчатого перлита является наличие в материале зерен с разрушенным перлитом. В таких зернах пластины цементита разрушены и представляют собой отдельные осколки разного размера. Один из таких примеров приведен на рис. 4. На этом же рисунке приведены дифракционная картина и ее индицированная схема. Темнопольное изображение, полученное для близко расположенных рефлексов α-фазы и цементита, подтверждает наличие частиц цементита. Фактически такая структура является ферритокарбидной смесью, но здесь и в дальнейшем будем называть ее “разрушенным перлитом”. Объемная доля такой структуры составляет 10% от материала в целом. По границам зерен разрушенного перлита, как правило, находятся частицы цементита пластинчатой формы.
Рис. 4.
Электронно-микроскопическое изображение структуры разрушенного пластинчатого перлита в стали 40Х после черновой обработки: а – светлопольное изображение; б – темнопольное изображение, полученное для близко расположенных рефлексов 10$\bar {1}$ α-фазы и 211 цементита; в – дифракционная картина, полученная с участка (а); г – ее индицированная схема (присутствуют рефлексы 111 и 113 α-фазы и $\bar {2}$31 цементита).
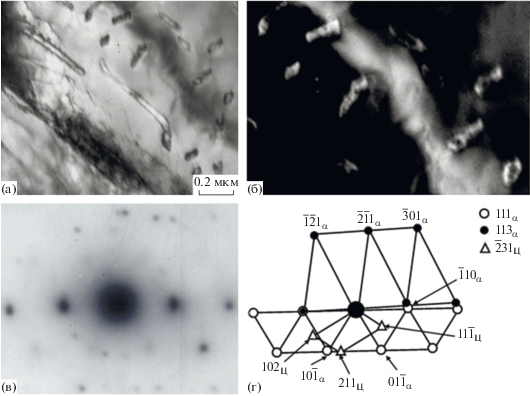
Второй отличительной особенностью структуры пластинчатого перлита в стали после “черновой” обработки является наличие фрагментированного перлита (рис. 5). Известно, что под влиянием какого-либо воздействия на материал внутри цементитных пластин вследствие перестройки дислокационной структуры могут образовываться малоугловые границы, что приводит к возникновению фрагментированного [22, 29] или, как его еще называют [21], субзеренного перлита. Формирование субзеренных границ и скоплений дислокаций отмечалось ранее в отожженной перлитной стали [30, 31], а также в отпущенных сталях [32]. Известно, что накопление дислокаций влечет за собой фрагментацию материала [33] – образование разориентированных объемов, разделенных границами дислокационного типа. Известно также, что в ОЦК-металлах и сплавах формируется фрагментированная субструктура на заключительной стадии активной деформации, предшествующей разрушению [34, 35]. Образование фрагментов в пластинчатом перлите было отмечено неоднократно [21, 22, 36–38]. Фрагментированная субструктура представляет тип субструктуры, в которой при определенной степени ее совершенства по границам фрагментов начинают зарождаться и развиваться микротрещины [35, 39], после слияния которых может образоваться магистральная разрушающая трещина. Совершенствование фрагментированной субструктуры уменьшает пластичность материала, а ее разрушение – увеличивает [34, 35].
Рис. 5.
Электронно-микроскопическое изображение фрагментированного перлита в стали 40Х после черновой обработки: а – светлопольное изображение; б – дифракционная картина, полученная с участка, отмеченного на (а) окружностью, кружками выделены рефлексы кристаллической решетки цементита; в – темнопольное изображение, полученное для близко расположенных рефлексов 110 α-фазы и 122 цементита, белыми стрелками отмечены частицы цементита, расположенные внутри и на границах фрагментов.
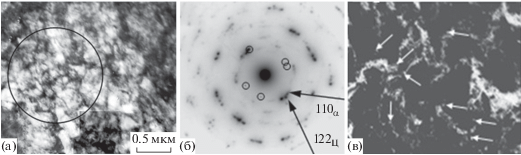
В перлитной стали может наблюдаться фрагментация двух типов – первичная и вторичная [22, 29]. Первичная фрагментация сохраняет (слегка искаженной) структуру пластин цементита, которые разделены малоугловыми границами, расположенными в плоскостях, перпендикулярных главной оси цементитной пластины. С боковых сторон фрагменты (субзерна) ограничены пластинами цементита и обладают анизотропной формой. Особенностью первичных фрагментов является то, что их поперечный размер соответствует толщине ферритных пластин. При вторичной фрагментации образуются дислокационные стенки как поперек, так и вдоль пластин α-фазы. Она разрушает перлитные колонии, создавая в структуре хаос. Образуются изотропные фрагменты α-фазы, границы которых частично окаймлены цементитом. Такие участки представляют собой смесь зерен α-фазы и цементита (рис. 5). Различные отклонения от нормального строения феррито-цементитной смеси обуславливают неоднородность механических свойств в локальных участках колоний перлита. Характер расположения дефектов строения перлита определяет места зарождения зон локализации течения, образования трещин. Таким образом, “черновая” обработка материала привела к образованию вторично фрагментированного перлита. Доказательством того, что эта структура образовалась из пластинчатого перлита, являются дифракционная картина (рис. 5б), на которой отмечены рефлексы, принадлежащие кристаллической решетке цементита, и темнопольное изображение (рис. 5в), полученное в случае близко расположенных рефлексов α-фазы и цементита. На темнопольном изображении отчетливо видны частицы цементита округлой формы, находящиеся внутри и на границах фрагментов α-фазы бывшего перлита. Объемная доля такой структуры составляет 10% от объема материала в целом. В стали после черновой обработки встречаются лишь единичные микротрещины, но опасность разрушения все-таки присутствует.
Изучена внутренняя структура всех морфологических составляющих стали. Были измерены и рассчитаны скалярная плотность дислокаций, ширина изгибных экстинкционных контуров, по которым затем определены амплитуда кривизны–кручения кристаллической решетки α-фазы, избыточная плотность дислокаций и амплитуда внутренних напряжений на различных участках материала. Полученные данные приведены в табл. 2. Как видно из таблицы, во всех морфологических составляющих пластинчатого перлита скалярная плотность дислокаций существенно возросла. Возросла она и в феррите, хотя и не столь значительно. По-прежнему величина скалярной плотности дислокаций в феррите больше, чем в перлите. Как и в исходном состоянии, во всех морфологических составляющих как перлита, так и феррита присутствуют изгибные экстинкционные контуры, что свидетельствует об изгибе–кручении кристаллической решетки. Были определены средние ширины изгибных экстинкционных контуров отдельно в каждой морфологической составляющей перлита и феррита. Из средней ширины изгибного экстинкционного контура, как и прежде, были определены следующие параметры структуры: амплитуда кривизны–кручения кристаллической решетки χ, избыточная плотность дислокаций ρ± и амплитуда внутренних локальных напряжений. Полученные параметры также приведены в табл. 2. Изгиб–кручение кристаллической решетки в нефрагментированной структуре перлита и феррита носит чисто пластический характер, во фрагментированной – упруго-пластический, т.е. в нефрагментированной структуре ρ ≥ ρ±, во фрагментированной ρ < ρ± и χ = χпл + χупр. Видно также, что величины χупр во фрагментах и перлита, и феррита меньше χпл. В перлите эта разница в ~3.5 раза, в феррите – в ~1.5 раза и, тем не менее, существует вероятность возникновения микротрещин именно в этих местах. Но так как объемная доля фрагментированного перлита в материале составляет 10%, а феррита 5%, то даже возникшие микротрещины не смогут привести к разрушению материала. Отметим, что микротрещин после черновой обработки материала ни в одной морфологической структуре обнаружено не было.
Таблица 2.
Количественные параметры тонкой структуры образцов стали 40Х после черновой обработки
Морфологическая составляющая матрицы стали | Скалярная плотность дислокаций | Избыточная плотность дислокаций | Кривизна–кручение кристаллической решетки | Амплитуда внутренних напряжений | |
---|---|---|---|---|---|
напряжения сдвига | локальные напряжения | ||||
ρ, 1010 см–2 | ρ±, 1010 см–2 | χ, см–1 | σЛ, МПа | σд, МПа | |
Пластинчатый перлит | |||||
Бездефектный | 2.16 | 2.12 | 530 | 290 | 290 |
Дефектный | 2.50 | 2.50 | 690 | 315 | 315 |
Разрушенный | 2.89 | 1.44 | 360 | 340 | 240 |
Вторично фрагментированный | 3.14 | 3.14 | 1010 (785 – пл. 225 – упр.) |
355 | 660 (355 – пл. 305 – упр.) |
В перлите | 2.46 | 2.26 | 610 (580 – пл. 30 – упр.) |
310 | 335 (300 – пл. 35 – упр.) |
Феррит | |||||
Нефрагментированный | 3.04 | 2.36 | 590 | 350 | 305 |
Фрагментированный | 2.06 | 2.06 | 870 (515 – пл. 355 – упр.) |
290 | 770 (290 – пл. 480 – упр.) |
В феррите | 2.80 | 2.80 | 660 (570 – пл. 90 – упр.) |
335 | 420 (300 – пл. 120 – упр.) |
Средние в материале | 2.83 | 2.36 | 620 (580 – пл. 40 – упр.) |
315 | 350 (300 – пл. 50 – упр.) |
Во всех морфологических составляющих структуры была определена амплитуда внутренних напряжений: локальных σд и напряжений сдвига σЛ. Полученные данные также представлены в табл. 2. Из сравнения данных следует, что в нефрагментированной структуре и перлита, и феррита всегда выполняется условие σЛ > σд, во фрагментированной – σЛ < σд. Если во фрагментированном перлите упругая составляющая внутренних локальных напряжений все-таки меньше упругой составляющей, то во фрагментированном феррите $\sigma _{{\text{д}}}^{{{\text{упр}}}}$ превышает $\sigma _{{\text{д}}}^{{{\text{пл}}}}$ в 1.7 раза. Это означает, что наиболее вероятно образование микротрещин именно во фрагментированном феррите.
“Получистовая” обработка
Объемная доля пластинчатого перлита с искривленными пластинами цементита в исходном состоянии стали и в состоянии после черновой обработки образцов в целом по материалу составляла менее 1%, поэтому при обработке количественных параметров ее не принимали во внимание. Теперь объемная доля этой структуры составляет 15% от общего объема материала (рис. 6в, 7б, 8). Дефектный перлит оказался частично фрагментирован – в отдельных пластинах α-фазы появились первичные фрагменты (рис. 6г). Первичная фрагментация встречается и в бездефектном пластинчатом перлите с изогнутыми пластинами цементита (рис. 7б). В пластинчатом разрушенном перлите сохранились отдельные пластины цементита в виде кусков, осколков. Это хорошо видно на темнопольном изображении (рис. 8б), полученном в случае близко расположенных рефлексов α-фазы и цементита (рис. 8в, 8г). Другой пример пластинчатого разрушенного перлита представлен на рис. 9. Зерна разрушенного перлита находятся между зернами бездефектного пластинчатого перлита с искривленными пластинами цементита и фрагментированного феррита. Пластины цементита разрушены настолько, что сохранились лишь отдельные короткие цементитные пластинки, смещенные относительно друг друга. Направленность перлитной колонии сохраняется.
Рис. 6.
Типы пластинчатого перлита после получистовой обработки стали 40Х: а – бездефектный; б – дефектный; в – бездефектный с искривленными пластинами цементита; г – первично фрагментированный дефектный.
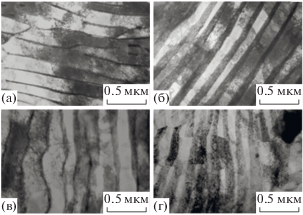
Рис. 7.
Электронно-микроскопическое изображение тонкой структуры стали 40Х после получистовой обработки; стык двух зерен: а – дефектного пластинчатого перлита; б – бездефектного пластинчатого перлита с изогнутыми пластинами цементита и первичными фрагментами α-фазы.
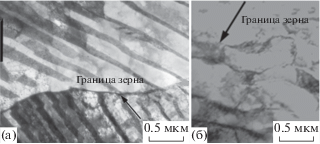
Рис. 8.
Электронно-микроскопическое изображение тонкой структуры стали 40Х после получистовой обработки, зерно с практически полностью разрушенным пластинчатым перлитом, в котором сохранились отдельные пластины цементита (отмечены стрелками): а – светлопольное изображение; б – темнопольное изображение, полученное для близко расположенных рефлексов $\bar {1}$10 α-фазы и 0$\bar {2}$3 цементита (Ц); в – микродифракционная картина; г – ее индицированная схема (присутствуют рефлексы 331 α-фазы и $\bar {4}$32 цементита).
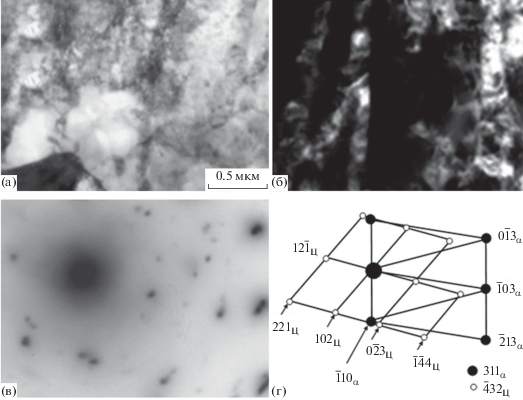
Рис. 9.
Электронно-микроскопическое изображение тонкой структуры стали 40Х после получистовой обработки: П – бездефектный пластинчатый перлит с изогнутыми пластинами цементита; ПР – разрушенный пластинчатый перлит; Ф – фрагментированный феррит.
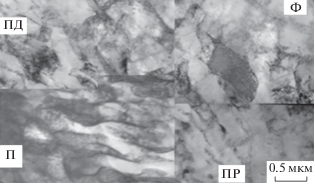
Как и в описанных выше образцах, была детально изучена структура всех морфологических составляющих стали, измерены и рассчитаны скалярная плотность дислокаций, ширина изгибных экстинкционных контуров, по которым затем определены амплитуда кривизны–кручения кристаллической решетки α-фазы, избыточная плотность дислокаций и амплитуда внутренних напряжений на различных участках материала (табл. 3). “Получистовая” обработка образца привела к изменениям количественных параметров. Во-первых, скалярная плотность дислокаций существенно увеличилась во всех морфологических составляющих стали и в целом по образцу, но вид дислокационной структуры не изменился. Во-вторых, если в разрушенном пластинчатом перлите в образцах после черновой обработки изгиб–кручение кристаллической решетки α-фазы носит только пластический характер и χ = χпл, то после получистовой обработки χ = χпл + χупр, т.е. характер изгиба–кручения кристаллической решетки α-фазы упруго-пластический и σд = $\sigma _{{\text{д}}}^{{{\text{пл}}}}$ + + $\sigma _{{\text{д}}}^{{{\text{упр}}}}.$ По-видимому, это связано с тем, что “черновая” обработка образцов приводит лишь к начальной стадии разрушения пластин цементита – скользящие дислокации разрезают пластины, они начинают делиться на части, образуются разориентированные объемы, разделенные малоугловыми границами дислокационного типа, что в дальнейшем должно привести к фрагментации материала. Но пока разориентация небольшая, изгибные экстинкционные контуры относительно широкие, что свидетельствует о слабом изгибе–кручении кристаллической решетки α-фазы. Получистовая обработка образцов привела к большему разрушению цементита (рис. 8, 9). Это подтверждается и тем, что величина ρ в α-фазе в среднем в разрушенном перлите возросла в 1.2 раза. Накопление дислокаций повлекло за собой их перераспределение и, как следствие, образование объемов с большой разориентацией. На электронно-микроскопических изображениях это проявляется в уменьшении ширины изгибных экстинкционных контуров, иначе говоря, увеличении χ и σд.
Таблица 3.
Количественные параметры тонкой структуры образцов стали 40Х после получистовой обработки
Морфологическая составляющая матрицы стали | Скалярная плотность дислокаций | Избыточная плотность дислокаций | Кривизна–кручение кристаллической решетки | Амплитуда внутренних напряжений | |
---|---|---|---|---|---|
напряжения сдвига | локальные напряжения | ||||
ρ, 1010 см–2 | ρ±, 1010 см–2 | χ, см–1 | σЛ, МПа | σд, МПа | |
Пластинчатый перлит | |||||
Бездефектный | 2.65 | 2.0 | 500 | 325 | 280 |
Бездефектный с изогнутыми пластинами | 2.55 | 1.72 | 430 | 320 | 260 |
Дефектный | 3.64 | 1.52 | 380 | 380 | 245 |
Разрушенный | 3.29 | 3.29 | 990 (820 – пл. 170 – упр.) |
360 | 590 (360 – пл. 230 – упр.) |
В перлите | 3.0 | 2.07 | 550 (520 – пл. 30 – упр.) |
310 | 325 (280 – пл. 45 – упр.) |
Феррит | |||||
Фрагментированный | 3.83 | 3.72 | 930 | 390 | 385 |
В феррите | 3.83 | 3.72 | 930 | 390 | 385 |
Средние в материале | 3.17 | 2.40 | 625 (600 – пл. 25 – упр.) |
355 | 335 (300 – пл. 35 – упр.) |
В-третьих, получистовая обработка изменила характер изгиба–кручения в ферритной составляющей стали – он стал исключительно пластическим. Это объясняется тем, что такая обработка привела к полной фрагментации феррита. Границы фрагментов стали более четкими, дислокационная структура внутри фрагментов – более совершенной. Это хорошо видно из сравнения рис. 9, 10 (получистовая обработка) с рис. 4, 5 (черновая обработка). Величина ρ ферритной составляющей в случае второго режима по сравнению с первым увеличилась практически в два раза, χ – лишь в 1.1 раза. Локальные внутренние напряжения (дальнодействующие) представлены по-прежнему пластической и упругой составляющими. Пластическая составляющая не изменилась, а упругая уменьшилась. В целом величина локальных напряжений даже несколько уменьшилась.
ЗАКЛЮЧЕНИЕ
В исходном состоянии сталь 40Х представляет собой α-фазу, образованную пластинчатым перлитом и ферритом в отношении 4 : 1. Пластинчатый перлит состоит из бездефектных (идеальных) областей, зерен с изогнутыми пластинами цементита и пластин цементита с явно выраженной дефектной субструктурой. Фрагменты феррита имеют сетчатую дислокационную структуру. Феррит включает нефрагментированные и фрагментированные области.
После черновой обработки в структуре пластинчатого перлита выявлены зерна с разрушенным и вторичным фрагментированным перлитом. В разрушенном перлите пластины цементита представляют собой отдельные осколки различных размеров. Объемная доля такой структуры составляет 10% от материала в целом. По границам зерен разрушенного перлита находятся частицы цементита. Вторичный фрагментированный перлит образовался из пластинчатого перлита. В структуре стали 40Х после черновой обработки выявлены единичные микротрещины. Во всех морфологических составляющих пластинчатого перлита скалярная плотность дислокаций возросла, присутствуют изгибные экстинкционные контуры. Изгиб–кручение кристаллической решетки в нефрагментированной структуре как перлита, так и феррита носит чисто пластический характер, во фрагментированной – упруго-пластический.
После получистовой обработки образуется перлит с искривленными пластинами цементита, его объемная доля увеличилась до 15% от общего объема материала. В бездефектном перлите с изогнутыми пластинами цементита происходит первичная фрагментация. Зерна пластинчатого разрушенного перлита находятся между зернами бездефектного перлита с искривленными пластинами цементита и фрагментированного феррита. Направленность перлитной колонии сохраняется. После получистовой обработки скалярная плотность дислокаций существенно увеличилась во всех морфологических составляющих стали и в целом по образцу, вид дислокационной структуры не изменился. Изгиб–кручение кристаллической решетки α-фазы является упруго-пластическим. В ферритной составляющей стали изгиб–кручение носит исключительно пластический характер.
Список литературы
Reich M.J., Woer A.L., Tanikella N.G., Pearce J.M. // Materials. 2019. V. 12. P. 1642. https://doi.org/10.3390/ma12101642
Romanov D.A., Moskovskii S.V., Sosnin K.V. et al. // Mater. Res. Express. 2019. V. 6. P. 055042. https://doi.org/10.1088/2053-1591/ab0672
Wang H., Chi G., Jia Y. et al. // Appl. Surf. Sci. 2020. V. 504. P. 144 285. https://doi.org/10.1016/j.apsusc.2019.144285
Chen X.L., Fan G.C., Lin C.H. et al. // J. Mater. Process. Technol. 2020. V. 276. P. 116406. https://doi.org/10.1016/j.jmatprotec.2019.116406
Song B., Luo L., Wang Y.-F. // Guangxue Jishu/Opt. Tech. 2008. V. 34. P. 278.
Wang H., Yang J., Sun F. // J. Mater. Process. Technol. 2020. V. 276. P. 116401. https://doi.org/10.1016/j.jmatprotec.2019.116401
Uthayakumar M., Kumaran T.S., Khan A.M. et al. // J. Testing Evaluation. 2020. V. 48. https://doi.org/10.1520/JTE20180216
Ancuta P.N., Manescu H., Vasile I. // Roman. Rev. Precision Mechan. Opt. Mechatronics. 2018. V. 2015. P. 37.
Yin J., Wen J.-J. // Yantu Gongcheng Xuebao/Chinese J. Geotech. Eng. 2012. V. 34. P. 98.
Zhou K., Ding H., Wang R. et al. // Tribol. Int. 2020. V. 143. P. 106 040. https://doi.org/10.1016/j.triboint.2019.106040
Fiza M., Ullah H., Islam S., Chohan F. // J. Math. Comput. Sci. 2020. V. 20. P. 43. https://doi.org/10.22436/jmcs.020.01.05
Romanov D.A., Moskovskii S.V., Martusevich E.A. et al. // Metalurgija. 2018. V. 57. P. 299.
Kalusuraman G., Thirumalai Kumaran S., Siva I., Anand Kumar S. // J. Testing Evaluation. 2020. V. 48. https://doi.org/10.1520/JTE20180330
Vigneshwaran S., Uthayakumar M., Arumugaprabu V. // J. Testing Evaluation. 2020. V. 48. P. JTE20180593. https://doi.org/10.1520/JTE20180593
Dellen J., Lynen L., Schwedt A. et al. // Tribol. Int. 2020. V. 143. P. 106021. https://doi.org/10.1016/j.triboint.2019.106021
Mouhamadali F., Equis S., Saeidi F. et al. // Opt. Las. Eng. 2020. V. 126. P. 105917. https://doi.org/10.1016/j.optlaseng.2019.105917
Hu C., Zhuang K., Weng J. et al. // Int. J. Mech. Sci. 2020. V. 167. P. 105273. https://doi.org/10.1016/j.ijmecsci.2019.105273
Godino L., Pombo I., Girardot J. et al. // J. Mater. Process. Technol. 2020. V. 277. P. 116464. https://doi.org/10.1016/j.jmatprotec.2019.116464
Lv D., Yan C., Chen G. et al. // Ultrasonics. 2020. V. 101. P. 106 006. https://doi.org/10.1016/j.ultras.2019.106006
Wang Z., Zhang J., Zhang J. et al. // J. Mater. Process. Technol. 2020. V. 276. P. 116400. https://doi.org/10.1016/j.jmatprotec.2019.116400
Тушинский Л.И., Батаев А.А., Тихомирова Л.Б. Структура и конструктивная прочность стали. Новосибирск: Наука, 1993. 280 с.
Иванов Ю.Ф., Громов В.Е., Попова Н.А. и др. Структурно-фазовые состояния и механизмы упрочнения деформированной стали. Новокузнецк: Полиграфист, 2016. 510 с.
Бернштейн М.Л., Владимирская Т.К., Займовский В.А. и др. // Изв. АН СССР. Металлы. 1979. № 2. С. 130.
Счастливцев В.М., Табачникова Т.И., Яковлева И.Л. // Физика металлов и металловедение. 1997. Т. 84. Вып. 4. С. 61.
Окишев К.Ю., Мирзаев Д.А., Счастливцев В.М., Яковлева И.Л. // Физика металлов и металловедение. 1998. Т.85. Вып. 2. С. 145.
Яковлева И.Л., Карькина Л.Е., Хлебникова Ю.В., Счастливцев В.М. // Физика металлов и металловедение. 2001. Т. 92. № 3. С. 77.
Утевский Л.М. Дифракционная электронная микроскопия в металловедении. М.: Металлургия, 1973. 584 с.
Хирш П., Хови А., Николсон Р. и др. Электронная микроскопия тонких кристаллов. М.: Мир, 1968. 574 с.
Ветер В.В., Попова Н.А., Игнатенко Л.Н., Козлов Э.В. // Изв. вузов. Черная металлургия. 1994. № 10. С. 44.
Долженков В.И., Лоцманова И.Н. // Металловедение и термическая обработка металлов. 1972. № 7. С. 67.
Сухомлин Г.Д. // Физика металлов и металловедение. 1974. Т. 38. № 4. С. 878.
Счастливцев В.М., Яковлева И.Л., Заваров А.С. // Физика металлов и металловедение. 1980. Т. 49. № 1. С. 138.
Конева Н.А., Козлов Э.В. // Изв. вузов. Физика. 1990. № 2. С. 89.
Рыбин В.В. Большие пластические деформации и разрушение металлов. М.: Металлургия, 1986. 224 с.
Трефилов В.И., Моисеев В.Ф., Печковский Э.П. и др. Деформационное упрочнение и разрушение поликристаллических материалов. Киев: Наук. думка, 1989. 256 с.
Гриднев В.Н., Гаврилюк В.Г. // Металлофизика. 1982. Т. 4. № 3. С. 74.
Громов В.Е., Козлов Э.В., Базайкин В.И. Физика и механика волочения и объемной штамповки. М.: Недра, 1997. 293 с.
Нестерова Е.В., Рыбин В.В., Золоторевский Н.Ю. // Физика металлов и металловедение. 2000. Т. 89. № 1. С. 47.
Козлов Э.В., Теплякова Л.А., Тришкина Л.И. и др. // Прочность и разрушение гетерогенных материалов. Л.: ФТИ им. А.Ф. Иоффе, 1990. С. 3.
Дополнительные материалы отсутствуют.
Инструменты
Поверхность. Рентгеновские, синхротронные и нейтронные исследования