Поверхность. Рентгеновские, синхротронные и нейтронные исследования, 2023, № 6, стр. 39-44
Влияние текстуры молибдена на стойкость к высокотемпературному окислению сплава Zr–1Nb с покрытием Cr/Mo
А. В. Абдульменова a, *, М. С. Сыртанов a, **, Е. Б. Кашкаров a, Д. В. Сиделев a
a Национальный исследовательский Томский политехнический университет
634050 Томск, Россия
* E-mail: ava75@tpu.ru
** E-mail: maxim-syrtanov@mail.ru
Поступила в редакцию 14.11.2022
После доработки 11.01.2023
Принята к публикации 11.01.2023
- EDN: DHMMDZ
- DOI: 10.31857/S102809602306002X
Аннотация
Исследовано влияние кристаллической структуры подслоя Mo на стойкость циркониевого сплава Zr–1Nb с покрытием Cr/Mo к высокотемпературному окислению на воздухе. Методом магнетронного распыления были нанесены покрытия трех видов: однослойное Cr покрытие толщиной 8 мкм, двухслойные покрытия с подслоем из Mo (3 мкм) различной текстуры и внешним защитным слоем из Cr (8 мкм). Различную текстуру пленок молибдена формировали путем изменения конфигурации системы магнетронного распыления. Образцы с покрытиями окисляли в атмосферной печи при 1100°C в течение 15, 30, 45 и 60 мин. Результаты рентгеновской дифракции и растровой электронной микроскопии показали, что применение подслоя Mo ограничивает взаимную диффузию системы Cr–Zr. Диффузия Mo приводит к образованию междиффузионных слоев Cr–Mo и Mo–Zr. Более быстрая диффузия наблюдается на границе раздела Cr–Mo. Толщина остаточного слоя Cr в двухслойных покрытиях больше, чем в однослойном при аналогичных условиях окисления.
ВВЕДЕНИЕ
Разработка циркониевых оболочек тепловыделяющих элементов, обеспечивающих безопасность при авариях с потерей теплоносителя, является крайне важной задачей на сегодняшний день [1–3]. Предлагается множество материалов в качестве защитных покрытий, которые будут способны предотвращать окисление циркониевых сплавов и впоследствии предотвращать или замедлять разрушение оболочек с ядерным топливом [4–7]. Большинство научных коллективов рассматривают хром в качестве основного защитного покрытия, поскольку образующийся во время высокотемпературного окисления оксидный слой (Cr2O3) препятствует проникновению кислорода в циркониевый сплав [8–11]. Тем не менее при высоких температурах значительно возрастает взаимная диффузия Cr и Zr с последующим образованием эвтектики с температурой плавления 1332°C [12]. Перспективным решением для предотвращения взаимной диффузии хрома и циркония является нанесение промежуточного слоя между защитным хромовым покрытием и циркониевым сплавом [13, 14]. Одним из материалов барьерного слоя можно считать молибден, который может образовывать эвтектику с хромом при температуре значительно выше, чем в системе Cr–Zr (1550°C) [15]. Кроме этого, он обладает высокой теплопроводностью (139 Вт/(м · К)) и температурой плавления (2623°C), а также приемлемым сечением захвата тепловых нейтронов [16]. В предыдущей работе коллектива и в работах других авторов была показана эффективность применения двухслойного покрытия из Cr/Mo для подавления диффузии хрома в циркониевый сплав и повышения стойкости к высокотемпературному окислению [16–18]. Однако нет данных о том, как кристаллографическая ориентация слоя молибдена может влиять на кинетику окисления циркониевого сплава с покрытием из Cr/Mo.
Таким образом, целью настоящей работы было исследование барьерных свойств и коррозионной стойкости покрытий из Cr/Mo с различной текстурой молибдена, полученных с помощью магнетронного распыления на циркониевом сплаве Zr–1Nb.
МАТЕРИАЛЫ И МЕТОДЫ
Образцы циркониевого сплава Zr–1Nb (15 × × 15 × 2 мм) использовали в качестве подложек. Двухслойные Cr(8 мкм)/Mo(3 мкм) и однослойное Cr (8 мкм) покрытия были нанесены методом магнетронного распыления с использованием ионно-плазменной установки, разработанной в Томском политехническом университете [19]. Следует отметить, что вследствие крепления образцов в держателе при нанесении на них покрытий часть поверхности образцов циркониевого сплава не имела защитного покрытия (площадь непокрытой области составляла ~5–10 мм2). Для измерения температуры образцов в процессе осаждения покрытий использовали инфракрасный пирометр Optris CTlaser 3MH1CF4.
Покрытия из Cr осаждали с помощью мультикатодного магнетронного распыления с источником питания постоянного тока. Для формирования пленок молибдена с различной кристаллической структурой использовали одиночное и дуальное магнетронное распыление с источником постоянного тока. В работе образец с молибденовым подслоем, полученным в процессе одиночного распыления, и защитным покрытием из хрома обозначен как Cr/Mo–1, а образец с молибденовым подслоем, полученным с помощью дуального магнетронного распыления, и защитным покрытием из хрома – Cr/Mo–2. Режимы осаждения покрытий представлены в табл. 1.
Таблица 1.
Параметры осаждения Cr и Mo пленок
Покрытие | Q, Вт/см2 | Uсм, В | jп, мА/ см2 | t, ч | Тмакс, °С | h, мкм |
---|---|---|---|---|---|---|
Сr | 39 | –50 | 65 | 2.5 | 320 | 8 |
Mo–1 | 39 | –50 | 18 | 2.8 | 190 | 3 |
Mo–2 | 39 | –50 | 55 | 1.6 | 320 | 3 |
Высокотемпературные испытания на воздухе проводили в атмосферной печи (ATS 3210, Applied Test Systems Inc.) при нагреве от 500 до 1100°С со скоростью нагрева ~20°С/мин и с последующим изотермическим выдерживанием в течение 15, 30, 45 и 60 мин. После окисления образцы охлаждались до комнатной температуры естественным образом.
Прирост массы образцов измеряли на аналитических весах Sartorius CP 124S с точностью 10–4 г с учетом непокрытой части (без защитного покрытия в месте крепления). Таким образом, расчет происходил следующим образом:
где S – площадь части образца с покрытием [см2], Δm – прирост массы части образца с покрытием [мг], m – прирост массы всего образца [мг], Sнеп – площадь непокрытой части образца [см2], WZr – прирост массы непокрытого циркониевого сплава [мг].Микроструктуру образцов исследовали с помощью растрового электронного микроскопа (РЭМ) Tescan MIRA3. Текстуру и фазовый состав образцов изучали методом рентгенофазового анализа с использованием дифрактометра Shimadzu XRD-7000S в конфигурации Брэгга–Брентано (CuKα-излучение, λ = 1.54 Å) при 40 кВ и 30 мА. Для идентификации фаз использовали базу данных PDF4+ 2021 и программу SIeve. Расчет коэффициентов текстуры проводили по дифрактограммам образцов с молибденовыми слоями, нанесенными на циркониевый сплав Zr–1Nb по следующей формуле [20]:
где N – количество отражений, I – интенсивность рентгеновского излучения, нанесенного покрытия, I0 – интенсивность излучения эталонного материала.РЕЗУЛЬТАТЫ И ИХ ОБСУЖДЕНИЕ
На первом этапе был проведен расчет текстурных коэффициентов, сформированных молибденовых подслоев, дифрактограммы которых представлены на рис. 1. По данным рентгенофазового анализа видно, что оба образца содержат фазу β-Mo с объемно-центрированной кубической решеткой. Параметры решеток образцов Mo–1 и Mo–2 значительно отличаются и составляют 0.3179 и 0.3158 нм соответственно. Различие в параметрах пленок обусловлено разными условиями осаждения покрытий. Анализ дифрактограмм показал, что в образце Mo–2 наблюдаются отражения 110, 200, 211 и 220, в то время как в образце Mo–1 отражение 200 не наблюдается. Необходимо отметить, что сформированные слои имеют преимущественную ориентацию кристаллитов в направлении [110]. Однако расчет, представленный в табл. 2, показал, что в покрытии Mo–1 коэффициент текстуры в направлении [110] превышает коэффициент в покрытии Mo–2. Текстурные коэффициенты в направлениях [211] и [220] сопоставимы.
Рис. 1.
Дифрактограммы тонких (1 мкм) пленок молибдена Mo–1 (1) и Mo–2 (2) с различной текстурой, нанесенных на циркониевый сплав Zr–1Nb.
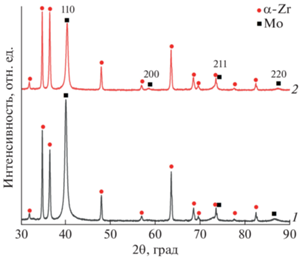
Таблица 2.
Коэффициенты текстуры тонких (1 мкм) пленок молибдена
Покрытие | Tc(110) | Tc(200) | Tc(211) | Tc(220) |
---|---|---|---|---|
Mo–1 | 2.5 | 0 | 0.7 | 0.8 |
Mo–2 | 2 | 0.3 | 0.9 | 0.8 |
На следующем этапе оценивали прирост массы образцов на воздухе при температуре 1100°С без покрытия, с однослойным хромовым покрытием и покрытиями из Cr/Mo различной текстуры (рис. 2). Образцы с покрытиями характеризуются значительно меньшим приростом массы в отличие от непокрытого циркониевого сплава, который имеет наибольший прирост. Прирост массы образца Cr/Mo–1 составляет ~3 (15 мин) и 14 мг/см2 (60 мин), а образца Cr/Mo–2 ~5 (15 мин) и 15 мг/см2 (60 мин). Результаты испытаний показывают, что независимо от текстуры молибденового подслоя в образцах наблюдается практически соизмеримый прирост массы на протяжении всего времени окисления. Осаждение хромового покрытия приводит к снижению прироста массы в ~три–четыре раза в сравнении с покрытиями из Cr/Mo и более чем на один порядок в сравнении с непокрытым сплавом Zr–1Nb. Разница в приросте массы образцов с покрытиями из Cr и Cr/Mo вызвана интенсивным окислением на границе, покрытой и непокрытой частей циркониевого сплава [16].
Рис. 2.
График прироста массы окисленных образцов циркониевого сплава без покрытия и с покрытиями при температуре 1100°C.
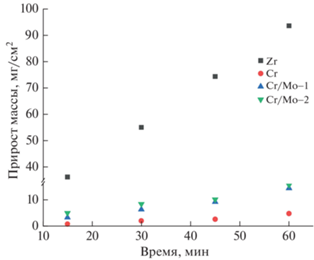
Анализ РЭМ-изображений поперечного сечения образцов после окисления (рис. 3) показал, что сплав Zr–1Nb с однослойным хромовым покрытием имеет микроструктуру, состоящую из четырех основных слоев: внешнего оксидного слоя Cr2O3, остаточного слоя α-Cr, междиффузионного слоя Cr–Zr, слоя циркониевого сплава с выпадениями Cr-обогащенной фазы β-Zr. Увеличение времени окисления от 15 до 45 мин приводит к росту толщины внешнего оксидного слоя от 4.5 до 5 мкм, а также увеличению толщины междиффузионного слоя от 0.5 до 1 мкм (рис. 3а, 3б). Поэтому толщина остаточного слоя хрома уменьшается за счет окисления хрома и его диффузии вглубь сплава. В случае покрытий Cr/Mo–1 и Cr/Mo–2 толщина внешнего оксидного слоя Cr2O3 после 15 мин окисления составляет 2.5 и 4 мкм соответственно. После 45 мин окисления толщины оксидных слоев примерно соответствуют толщине образца с покрытием из Cr без барьерного слоя (5 мкм), что указывает на активный процесс окисления внешнего защитного слоя при длительном окислении. Важно отметить, что толщина остаточного слоя хрома в случае двухслойных покрытий значительно больше в сравнении с однослойным покрытием. Это обусловлено более быстрой диффузией в системе Cr–Zr, чем в системе Cr–Mo. Тенденция роста внешнего оксидного слоя и, соответственно, уменьшение толщины остаточного слоя хрома с увеличением длительности окисления сохраняется, как и в случае однослойных покрытий. В обоих образцах после окисления наблюдается взаимная диффузия между хромом и молибденом, а также молибденом и цирконием (рис. 3в–3е). Междиффузионный слой Cr–Mo после 45 мин окисления в покрытии Cr/Mo–2 больше, чем в Cr/Mo–1, что указывает на более активную диффузию при данной текстуре молибдена. Диффузия молибдена в цирконий протекает по схожему механизму, что и в случае с хромовым покрытием: происходит формирование и рост междиффузионного слоя Mo–Zr.
Рис. 3.
РЭМ-изображения образцов Cr (а, б), Cr/Mo–1 (в, г), Cr/Mo–2 (д, е) после окисления в течение 15 (а, в, д) и 45 мин (б, г, е).
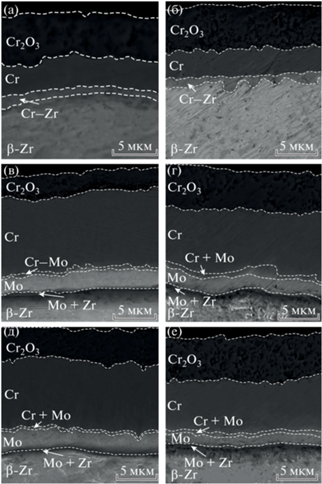
Анализ дифрактограмм показал, что окисление однослойного хромового покрытия приводит к формированию фазы Cr2O3 наряду с α-Cr (рис. 4). Увеличение времени окисления сопровождается перераспределением интенсивности рефлексов, которое указывает на увеличение содержания оксидной фазы. Фазовый состав образцов с покрытиями из Cr/Mo аналогичен покрытию из Cr, за исключением того, что помимо фаз Cr2O3 и α-Cr была идентифицирована фаза Cr3Mo (рис. 4б, 4в). Появление этой интерметаллической фазы связано с активным процессом диффузии молибдена в хром при высокой температуре. Увеличение длительности окисления до 45 мин приводит к перераспределению интенсивностей отражений фаз α-Cr и Cr2O3, что указывает на увеличение содержания оксидной фазы по аналогии с однослойным покрытием из Cr.
ЗАКЛЮЧЕНИЕ
В ходе работы были исследованы барьерные свойства и стойкость к окислению защитного покрытия из Cr/Mo с различной текстурой молибдена. Покрытия состояли из барьерного молибденового слоя толщиной 3 мкм и защитного хромового покрытия толщиной 8 мкм, полученных методом магнетронного распыления. В результате комплексного анализа структурно-фазового состояния циркониевого сплава с покрытиями из Cr/Mo при высокотемпературном окислении можно сделать следующие выводы.
Молибден ограничивает взаимную диффузию хрома и циркония при высокотемпературном окислении, обеспечивая большую толщину остаточного слоя хрома в отличие от однослойного хромового покрытия. Диффузия молибдена при высоких температурах приводит к формированию междиффузионных слоев Cr–Mo и Mo–Zr на границах их раздела. Толщина диффузионного слоя Cr–Mo больше в случае покрытия из Cr/Mo–2, что указывает на более активную взаимную диффузию Cr и Mo. Толщины оксидных слоев Cr2O3 при окислении однослойного Cr покрытия и покрытий из Cr/Mo с различной текстурой схожи, что указывает на несущественное влияние подслоя Mo и его текстуры на стойкость к окислению циркониевого сплава.
Список литературы
Terrani K.A. // J. Nucl. Mater. 2018. V. 501. P. 13. https://doi.org/10.1016/j.jnucmat.2017.12.043
Bragg-Sitton S. // Nucl. News. 2014. V. 57. № 3. P. 83.
Bischoff J., Delafoy C., Vauglin C., Barberis P., Roubeyrie C., Perche D., Duthoo D., Schuster F., Brachet J.C., Schweitzer E.W., Nimishakavi K. // Nucl. Engin. Technol. 2018. V. 50. P. 223. https://doi.org/10.1016/j.net.2017.12.004
Khatkhatay F., Jiao L., Jian J., Zhang W., Jiao Z., Gan J., Zhang H., Zhang X., Wang H. // J. Nucl. Mater. 2014. V. 451. Iss. 1–3. P. 346. https://doi.org/10.1016/j.jnucmat.2014.04.010
Li W., Wang Z., Shuai J., Xu B., Wang A., Ke P. // Ceram. Intern. 2019. V. 45. Iss. 11. P. 13912. https://doi.org/10.1016/j.ceramint.2019.04.089
Tang C., Stueber M., Seifert H.J., Steinbrueck M. // Corrosion Rev. 2017. V. 35. Iss. 3. P. 141. https://doi.org/10.1515/corrrev-2017-0010
Tallman D., Anasori B., Barsoum M.A. // Mater. Res. Lett. 2013. V. 1. Iss. 3. P. 115. https://doi.org/10.1080/21663831.2013.806364
Park D.J., Kim H.G., Jung Y., Park J.H., Yang J.H., Koo Y.H. // J. Nucl. Mater. 2016. V. 482. P. 75. https://doi.org/10.1016/j.jnucmat.2016.10.021
Brachet J.C., Le Saux M., Le Flem M., Urvoy S., Rouesne E., Guilbert T., Cobac C., Lahogue F., Rousselot J., Tupin M., Billaud P., Hossepied C., Schuster F., Lomello F., Billard A., Velisa G., Monsifrot E., Bischoff J., Ambard A. // Proc. TopFuel. 2015. P. 1.
Yang J., Steinbrück M., Tang C., Große M., Liu J., Zhang J., Yun D., Wang S. // J. Alloys Compd. 2022. V. 895. P. 162450. https://doi.org/10.1016/j.jallcom.2021.162450
Chen H., Wang X., Zhang R. // Coatings. 2020. V. 10 P. 808. https://doi.org/10.3390/coatings10090808
Jiang J., Du M., Pan Z., Yuan M., Ma X., Wang B. // Mater. Design. 2021. V. 212. № 110168. P. 1. https://doi.org/10.1016/j.matdes.2021.110168
Wang X., Liao Y., Xu C., Guan H., Zhu M., Gao C., Jin X., Pang P., Du J., Liao B., Xue W. // J. Alloys Compd. 2021. V. 883. № 160798. P. 1. https://doi.org/10.1016/j.jallcom.2021.160798
Krejčí J., Ševeček M., Kabátová J., Manoch F., Kočí J., Cvrček L., Málek J., Krum S., Šutta P., Bublíková P., Halodová P., Namburi H.K. // Proc. TopFuel. 2018. P. 1.
Kashkarov E., Afornu B., Sidelev D., Krinitcyn M., Gouws V., Lider A. // Coatings. 2021. V. 11. № 5. P. 1. https://doi.org/10.3390/coatings11050557
Wei T., Zhang R., Yang H., Liu H., Qiu S., Wang Y., Du P., He K., Hu X., Dong C. // Corros. Sci. 2019. V. 158. № 108077. P. 1. https://doi.org/10.1016/j.corsci.2019.06.029
Syrtanov M.S., Kashkarov E.B., Abdulmenova A.V., Sidelev D.V. // Surf. Coat. Technol. 2022. V. 439. № 128459. P. 1. https://doi.org/10.1016/j.surfcoat.2022.128459
Yeom H., Maier B., Johnson G., Dabney T., Walters J., Sridharan K. // J. Nucl. Mater. 2018. V. 507. P. 306. https://doi.org/10.1016/j.jnucmat.2018.05.014
Sidelev D.V., Kashkarov E.B., Syrtanov M.S., Krivo- bokov V.P. // Surf. Coat. Technol. 2019. V. 369. P. 69. https://doi.org/10.1016/j.surfcoat.2019.04.057
Stylianou R., Stylianoua R., Tkadletza M., Schalka N., Penoyb M., Czettlc C., Mitterera C. // Surf. Coat. Technol. 2019. V. 359. P. 314. http://doi.org/10.1016/j.surfcoat.2018.12.095
Дополнительные материалы отсутствуют.
Инструменты
Поверхность. Рентгеновские, синхротронные и нейтронные исследования