Расплавы, 2021, № 6, стр. 582-591
Электролизное борирование коррозионностойкого чугуна “нирезист” в расплавленных солях
К. Р. Каримов a, Е. С. Филатов a, b, Н. И. Шуров a, *
a Институт высокотемпературной электрохимии УрО РАН
Екатеринбург, Россия
b Уральский федеральный университет им. Б.Н. Ельцина
Екатеринбург, Россия
* E-mail: n.shurov@ihte.uran.ru
Поступила в редакцию 07.07.2021
После доработки 12.07.2021
Принята к публикации 21.07.2021
Аннотация
Исследован процесс термодиффузионного электролизного борирования поверхности образцов высокопрочного коррозионностойкого чугуна “Ni-Resist”, допированного никелем и медью, в боратном расплаве. Установлена зависимость толщины боридного покрытия от температуры, плотности катодного тока и времени обработки. Боридное покрытие нанесено на детали нефтяного насоса из чугуна “Ni-Resist” согласно установленному оптимальному режиму. Эти детали испытаны на устойчивость к абразивному износу и к коррозии в условиях практической работы насоса. Их износостойкость увеличилась в 5–6 раза.
ВВЕДЕНИЕ
Легированный никелем и медью жаропрочный аустенитный чугун “нирезист” (Ni-Resist) разработан в средине 20 века, и в настоящее время известны более 30 марок этого вида чугуна [1]. Его главные качества – износостойкость, формоустойчивость при повышенных температурах, коррозионно- и хладостойкость. С равным основанием “нирезист” иногда называют специальным сплавом. В частности, из этого чугуна производят крыльчатки насосов для откачки агрессивных жидкостей и суспензий из нефтяных скважин, поэтому основной причиной выхода из строя этих деталей (ресурс работы 10–15 дней) является абразивный износ.
Несмотря на заявляемую износостойкость этого чугуна, ее можно значительно увеличить различными видами обработки поверхности, например, лазерным оплавлением с аморфизацией или нанесением тонкого покрытия из нитрида титана. Конкурирующим методом поверхностного упрочнения деталей машин, работающих при повышенных статических и динамических нагрузках, является термодиффузионное борирование, значительно увеличивающее износостойкость, поверхностную твердость и усталостную прочность деталей. Разработке различных вариантов технологии борирования посвящены работы [2–8], исследованию химических и электрохимических процессов борирования – [8, 9], исследованию функциональных свойств и износостойкости боридных покрытий посвящены работы [10–15].
ЭКСПЕРИМЕНТАЛЬНАЯ ЧАСТЬ
Было проведено исследование борирования чугуна “нирезист” с содержанием легирующих компонентов (мас. %), установленным химическим анализом: С – 3.0; Ni – 15.2; Cu – 7.6; Si – 2.0; Cr – 1.0; Mn – 1.0. Микрофотография шлифа образца этого чугуна представлена на рис. 1.
Графит в этом чугуне находится в микропластинчатой форме хаотичной ориентации, никель – в твердом растворе с железом, весь хром находится в мелкодисперсных включениях легированного цементита [Fe(Cr)]3C.
Целями настоящей работы являются:
– определение оптимальных режимов процесса электролизного борирования чугуна “нирезист”, обеспечивающих получение наиболее качественного неотслаивающегося покрытия;
– исследование структуры, микротвердости и фазового состава боридного слоя;
– борирование крыльчатки нефтяного насоса по оптимальному режиму.
Работа состояла из следующих этапов:
1. Изучение кинетики электролизного насыщения поверхности бором при 800, 850, 900°C и временах выдержки 2 и 3 часа.
2. Металлографические исследования: измерение толщины, структуры и микро-твердости покрытия.
3. Микрорентгеноспектральный анализ покрытия для определения распределения легирующих элементов в покрытии и прилегающем к нему объеме.
4. Борирование крыльчатки нефтяного насоса по оптимальному режиму.
Техника экспериментов
Ранее в монографии [8] систематизированы мировые данные по разработке различных вариантов технологии термодиффузионного борирования сталей и сплавов до 2000 г., в том числе результаты авторов монографии. В данной работе использована усовершенствованная технология термодиффузионного электролизного борирования в расплаве CaCl2 + 3 мас. % B2O3, описанная в работах [16, 17]. Лабораторная установка состояла из шахтной печи с терморегулятором, в которой по центру помещен корундовый тигель на 400 см3 расплава. В тигель наплавляли хлоридно-оксидный расплав вышеуказанного состава, погружали в него графитовый анод в трубчатом корундовом чехле с открытым нижним торцом и по два взвешенных образца чугуна на катодной подвеске из нихромовой проволоки, затем включали постоянный ток. Все эксперименты вели в открытой ванне на воздухе. Температуру процесса контролировали Ni–NiCr термопарой. После борирования образцы вынимали из расплава на воздух и после охлаждения отмывали в кипящей воде. Поверхность деталей после отмывки была ровной, светло-серой и матовой.
РЕЗУЛЬТАТЫ И ИХ ОБСУЖДЕНИЕ
В начале работы была изучена зависимость толщины боридного слоя (Ɩ, мкм) на чугуне “нирезист” от температуры, времени выдержки 2 и 3 ч при плотности тока 40 мА/см2. Эти результаты представлены в графической форме на рис. 2.
Рис. 2.
Зависимость толщины боридного слоя (Ɩ) на чугуне “нирезист” от температуры и времени: 1 – 2 часа; 2 – 3 часа.
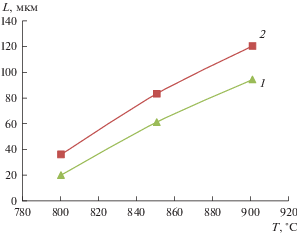
Из этих экспериментальных данных и микроскопического осмотра поверхности борированных образцов мы установили, что наилучшие результаты по качеству покрытия обеспечивает оптимальный режим борирования при температуре 850°С, плотности тока 40 мА/см2, режимы реверсирования – катодный импульс 1.5 с, анодный 0.4 с, время электролиза – 2 ч, что подтверждает результаты работ [16, 17]. При 800°С толщина покрытия слишком мала, а при 900°С покрытие слишком толстое и отслаивается от основы, что также согласуется с данными работ [16, 17] по другим маркам сталей.
Методы анализа борированных образцов
Для проведения металлографического анализа борированные образцы запрессовывали в пластмассу по технологии фирмы “Struers” на термопрессе “LaboPress-1”, отрезали на алмазном станке”Minosecar2”, шлифы полировали по технологии фирмы “Struers” на станке “LaboPol-4”, травление полированных образцов проводили в 5–8% растворе азотной кислоты в спирте. Шлифы исследовали на металлографическом микроскопе “Reichert”, микротвердость (HV) измерялась на микротвердомере ПМТ-3 при нагрузке 50 г.
Рентгеноструктурный анализ покрытий производился на рентгеновском дифрактометре Rigaku DMAX-D1200. Микрорентгеноспектральный анализ покрытий производился на рентгеновском микроанализаторе Jeol.
Результаты металлографического исследования борированных образцов
На рис. 3 представлена фотография поперечного шлифа образца чугуна “нирезист”, борированного при 850°C, 2 ч. Покрытие толщиной 60 ± 5 мкм сплошное, микротвердость внешнего слоя 16.2 ГПа, что меньше справочной величины для борида FeB (19.2 ± 0.5). Микротвердость промежуточного слоя 12.4 ГПа, что также меньше справочной величины для борида Fe2B (17.0 ± 0.5) [7, 9]. Микротвердость основы 2.2 ГПа. Из представленных данных металлографического анализа невозможно уверенно идентифицировать фазовый состав боридного покрытия, поэтому мы продолжили исследовать покрытия другими методами.
Рис. 3.
Структура боридного покрытия на чугуне “Ni-Resist”: микротвердость HV50, ГПа: внешний слой – 16.2; промежуточный слой – 12.4; основа – 2.2.
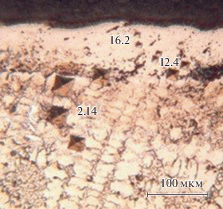
Рентгенофазовый (XRD) анализ
Дифрактограмма образца боридного покрытия на чугуне “нирезист” приведена на рис. 4.
Из анализа дифрактограммы следует, что внешний слой покрытия состоит из фазы FeB, с мелкими включениями меди, углерода и карбида Fe3C. Состав фаз промежуточного слоя остается неопределенным.
Поэтому мы предприняли дальнейшее исследование структуры боридного покрытия более информативным методом сканирующего микрорентгеновского анализа (SEM).
На рис. 5 представлены SEM-карты распределения элементов по площади шлифа.
Рис. 5.
Карты распределения элементов по поверхности шлифа борированного образца из чугуна “нирезист”.
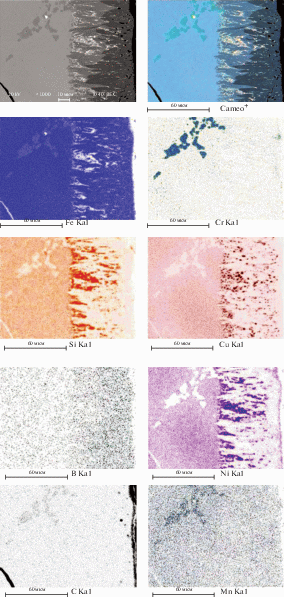
Из анализа карт распределения элементов можно утверждать:
а) темные совпадающие пятна на картах распределения хрома, железа и марганца в объеме чугуна можно идентифицировать как включения феррохрома с примесью марганца, не полностью растворившегося в объеме чугуна во время его плавления;
б) хром и марганец в боридном покрытии присутствуют как малые примеси в составе боридных фаз;
в) в процессе диффузии бор оттесняет кремний, никель и медь перед собой вглубь основы, в результате чего они локализованы в промежуточном слое покрытия.
На рис. 6 представлены точки в области внешнего слоя покрытия, среднего слоя и включений, в которых выполнен количественный анализ концентраций наиболее значимых компонентов чугуна.
Рис. 6.
Карты распределения элементов по поверхности шлифа борированного образца. Номера указывают места точечного элементного анализа.
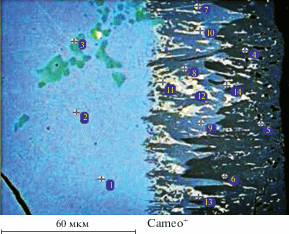
В таблице 1 представлены концентрации элементов (мас. %) в точках, обозначенных на рис. 6.
Таблица 1.
Результаты качественного анализа шлифа борированного образца из высоконикелевого чугуна, (мас. %)
Основа | |||||||||||
---|---|---|---|---|---|---|---|---|---|---|---|
№ точки | B | Si | Cr | Mn | Fe | Ni | Cu | C | Σ проч. примеси |
фаза | x в MexEl |
1 | 0.00 | 1.87 | 1.17 | 1.16 | 68.58 | 17.09 | 8.12 | 1.55 | 0.46 | Основа | – |
2 | 0.00 | 1.99 | 1.60 | 1.24 | 71.22 | 15.51 | 6.59 | 1.38 | 0.51 | Основа | – |
3 | 0.00 | 1.90 | 21.38 | 2.75 | 65.08 | 1.52 | 0.17 | 6.70 | 0.50 | [Fe(Cr,Mn)]3C | 2.9 |
Внешний слой | |||||||||||
4 | 16.2 | 0.09 | 1.56 | 1.14 | 74.37 | 5.95 | 0.19 | 0.00 | 0.50 | [Fe(Ni)]B | 0.99 |
5 | 16.5 | 0.11 | 1.60 | 1.10 | 73.95 | 6.02 | 0.20 | 0.00 | 0.49 | [Fe(Ni)]B | 0.97 |
6 | 16.3 | 0.08 | 1.55 | 1.09 | 74.15 | 6.10 | 0.21 | 0.00 | 0.52 | [Fe(Ni)]B | 0.98 |
Промежуточный слой | |||||||||||
7 | 8.84 | 0.09 | 1.80 | 1.35 | 80.62 | 6.27 | 0.45 | 0.00 | 0.58 | [Fe(Ni)]2B | 1.97 |
8 | 9.01 | 0.13 | 1.82 | 1.40 | 80.03 | 6.51 | 0.50 | 0.00 | 0.60 | [Fe(Ni)]2B | 1.93 |
9 | 8.85 | 0.10 | 1.78 | 1.34 | 80.86 | 6.06 | 0.42 | 0.00 | 0.59 | [Fe(Ni)]2B | 1.97 |
Включения в промежуточный слой | |||||||||||
10 | 0.00 | 12.48 | 0.24 | 0.61 | 15.20 | 58.29 | 12.63 | 0.00 | 0.55 | [Ni(Fe)]xSiy | – |
11 | 0.00 | 12.69 | 0.25 | 0.71 | 16.50 | 57.90 | 11.36 | 0.00 | 0.59 | [Ni(Fe)]xSiy | – |
12 | 0.00 | 12.55 | 0.22 | 0.68 | 16.38 | 58.61 | 10.96 | 0.00 | 0.60 | [Ni(Fe)]xSiy | – |
13 | 0.00 | 13.37 | 0.25 | 0.36 | 14.95 | 60.04 | 10.45 | 0.00 | 0.58 | [Ni(Fe)]xSiy | – |
14 | 0.00 | 2.68 | 0.25 | 0.23 | 6.20 | 14.18 | 75.86 | 0.00 | 0.60 | Cu(Ni) | – |
По совокупности результатов исследований структуры и состава боридного покрытия на чугуне “нирезист” можно сделать следующие выводы:
а) оптимальная толщина покрытия во избежание сколов не должна превышать 65 ± ± 5 мкм;
б) покрытие состоит из двух фазовых слоев столбчатой структуры, что типично для боридных покрытий на сталях [6, 8, 16, 17];
в) пониженная микротвердость фазовых слоев FeB и Fe2B, указанная в подписи к рис. 3 и тексте комментария, связана с легированием этих боридов никелем;
г) редкие включения графита микронных размеров распределяются в наружном фазовом слое FeB покрытия между клиньями боридов, соответственно не происходит концентрирование углерода между покрытием и основой в виде отдельного фазового слоя, что является причиной сколов покрытия при механических нагрузках борированной детали в процессе эксплуатации [6, 8];
д) светлые включения в промежуточном слое между основой и покрытием вероятно являются легированными силицидами [Ni(Fe,Cu)]xSiy и твердым раствором кремния в сплаве CuNi (точка 14 на рис. 6). Эти включения не ухудшают качество сцепления покрытия с основой.
Борирование опытных деталей
Детали нефтяного насоса из нирезистного чугуна борировали по установленному оптимальному режиму при температуре 850°C в течение 2 ч. Фотография образцов представлена на рис. 7. Получено равномерное покрытие без сколов.
Поскольку состав и вязкость суспензии, вызывающей абразивный износ, переменны и неизвестны точно, было невозможно моделировать условия работы деталей, соответственно мы не могли исследовать износостойкость покрытий в лабораторных условиях. Поэтому испытания борированных деталей нефтяного насоса были проведены в реальных условиях эксплуатации в серийной нефтяной скважине. К сожалению, испытания были прерваны после 4 суток работы из-за аварии на скважине, поэтому мы не смогли извлечь опытные детали и изучить состояние покрытий и степень их износа. Однако известно, что по величине микротвердости покрытия можно в первом приближении судить о его износостойкости [6, 9, 11–15]. Поскольку микротвердость боридного покрытия на чугуне “нирезист” почти в 8 раз выше, чем микротвердость его основы, можно предполагать повышение абразивной стойкости детали как минимум в 5–6 раз.
ЗАКЛЮЧЕНИЕ
Изучена кинетика формирования электролизных боридных покрытий на чугуне “нирезист” состава (С – 3.0; Ni – 15.2; Cu – 7.6; Si – 2.0; Cr – 1.0; Mn – 1.0) в расплаве CaCl2 + 3 мас. % B2O3, при температурах 800, 850 и 900°C и времени выдержки 2 и 3 часа. Установлено, что оптимальная толщина покрытия 65 ± 5 мкм (без сколов) получается при 850оС, плотности тока 40 мА/см2 и времени экспозиции 2 часа.
Проведены металлографические, рентгенофазовые (XRD), микрорентгено-спектральные (SEM) исследования полученных покрытий. Определены их микротвердость, фазовый состав и оптимальная толщина. Установлено, что микротвердость поверхностного боридного слоя в 6 раз выше, чем у основы.
По установленному оптимальному режиму (850°С, 2 ч) выполнено борирование реальных деталей нефтяного насоса из чугуна “нирезист”. Их испытания в реальных условиях эксплуатации показали, что стойкость к абразивному износу увеличилась, а коррозионная стойкость нет. Коррозионную стойкость боридного покрытия можно улучшить при помощи физических методов аморфизации поверхности.
Исследование выполнено с использованием приборных возможностей ЦКП “Состав вещества” ИВТЭ УрО РАН. Авторы благодарны Б.Д. Антонову за рентгенофазовый анализ покрытий, и А.А. Панкратову за проведение микрорентгеноспектрального (SEM) анализа.
Список литературы
Covert R., Morrison J., Roehrig K. Properties and Applications of Ni-Resist and Ductile Ni-Resist Alloys. Nickel Development Institute, Reference Book, Series № 11 018; 1998.
Hill V.L., Stapleton T.F. Method of Boronizing. United States patent US 3 201 286 CI. 148-6.11. Appl. 15.03.62; Publ.17.08.65.
Илющенко Н.Г., Плотникова А.Ф., Анфиногенов А.И., Беляева Г.И., Кожевников Г.Н., Ефремкин В.В., Плышевский Ю.С., Халиков Р.С., Кнышев Е.А. Расплав для борирования. Авторское свидетельство 533671 (СССР).
Tohri A., Masayoshi M., Noboru K. Diffusion Layers of Steel Surfaces Immersed in Fused Borax Baths Containing Various Kinds of Additives // J. Japan Inst. Metals. 1975. 39. P. 247–255.
Fichtl W. Boronizing and its Practical Applications // Materials in Engineering. 1981. 2. P. 276–286.
Ворошнин Л.Г. Борирование промышленных сталей и чугунов. Справочное пособие. Минск, 1981.
Matiasovsky K., Chrenkova-Paneirova M., Fellner P. Electrochemical and Thermochemical Boriding in Molten Salts // Surface and Coatings Technology 1988. 35. P. 133–149.
Чернов Я.Б., Анфиногенов А.И., Шуров Н.И. Борирование сталей в ионных расплавах, Екатеринбург, 2001.
Shurov N.I., Anfinogenov A.I., Chebykin V.V. et al. Transport Reactions in Salt Melts and their Applied Aspects // High Temperature Material Processes: An International Journal. 2002. 6. P. 101–108.
Dearnley P.A., Bell T. Engineering the Surface with Boron based Materials // Surface Engineering. 1985. 3. P. 203–217.
Крукович М.Г., Прусаков Б.А., Сизов И.Г. Пластичность борированных слоев. М.: Физматлит, 2010.
Litoria A.K., Joshi A.A., Joshi M.D. Wearbehaviour of boronized and duplex-treated AISI 4140 steel against DLC-coated boronized AISI 4140 disc // Surface Engineering. 2019. 35. № 4. P. 370–377.
Hunger H.J., Trute G. Boronizing to Produce Wear-Resistant Surface Layers // Heat Treatment of Metals. 1994. 21. P. 31–39.
Gaona-Martínez M.J., Alonso-Saavedra O.F., Ramírez-Ramírez J.H. Mechanical stability of boron-based coatings grown on Incoloy 909 superalloy by thermochemical diffusion // Surface Engineering. 2018. 34. № 7. P. 527–535.
Chernega S., Poliakov I., Krasovsky M. Wear Resistant Coatings On Based Boride Phases Formed In The Magnetic Field On Alloys // Machines. Technologies. Materials. 2017.11. № 2. P. 91–94.
Чернов Я.Б., Филатов Е.С., Каримов К.Р. Термодиффузионное борирование в расплаве на основе хлорида кальция с добавкой оксида бора с применением реверсированного тока // Расплавы. 2016. № 4. С. 307–315.
Филатов Е.С., Шуров Н.И., Каримов К.Р., Никитина Е.В., Чухванцев Д.О. Исследование продуктов электролизного борирования поверхности инструментальных сталей с реверсированием тока в борсодержащем оксихлоридном расплаве на основе CaCl2 // Расплавы. 2021. № 4. С. 338–353.
Дополнительные материалы отсутствуют.