Расплавы, 2022, № 3, стр. 301-313
Исследование металлургических свойств материалов, полученных при совместной утилизации красных шламов и прокатной окалины
Л. И. Леонтьев a, Ю. А. Чесноков a, *, И. Н. Танутров a, М. Н. Свиридова a, Л. А. Маршук a
a Институт металлургии Уральского отделения РАН
Екатеринбург, Россия
* E-mail: garlics@list.ru
Поступила в редакцию 23.01.2022
После доработки 28.01.2022
Принята к публикации 03.02.2022
- EDN: FYMOAQ
- DOI: 10.31857/S0235010622030069
Аннотация
В результате проведенных экспериментальных исследований получены пробы окускованных продуктов методами окислительного обжига, глубокой металлизации и прессования. Изучены физико-химические и металлургические свойства объектов исследования, существенно влияющих на технико-экономические показатели последующей технологии промышленной переработки. Исходные материалы получены гидрометаллургическим способом при совместном выщелачивании отходов производства алюминия (красные шламы) и трубопрокатного производства (замасленной окалины). В лабораторных условиях из наработанной опытной партии железорудного концентрата получены различные типы окускованных продуктов, в том числе окисленные и рудоугольные окатыши, брикеты с различными химическим составом и заданным соотношением основности CaO/SiO2. Определены основные технологические параметры окускования и термообработки для получения заданных характеристик для данного типа железорудного сырья. Исследованы основные стандартизированные металлургические характеристики полученных материалов, такие как восстановимость по ГОСТ 17 212–84, прочность при высокотемпературной обработке по ISO 13 930–1998, а также температуры начала и конца размягчения материалов по ГОСТ 26 517–85 с целью дальнейшего математического моделирования и сравнительного анализа технико-экономических показателей в различных металлургических агрегатах при обосновании выбора оптимальных параметров для различных технологических схем переработки данного типа железорудного сырья. Изучен рентгенофазовый состав исходного сырья и продуктов переработки, а также выявлены основные структурные составляющие исследуемых материалов, полученных при совместной утилизации красных шламов и прокатной окалины. Разработана методика расчета температуры кристаллизации и вязкости шлаков на основе тройных и четверных диаграмм состояния CaO–SiO2–MgO–Al2O3 для оперативного анализа и контроля структурно-чувствительных свойств оксидных систем. Выполнена программная реализация расчета по предложенным методикам в электронных таблицах MS Excel.
ВВЕДЕНИЕ
Одним из существенных направлений решения вопросов охраны окружающей среды от вредного воздействия промышленных отходов является разработка и внедрение в практику комплексных и безотходных технологических схем. С этой точки зрения совместное использование отходов алюминиевой промышленности и прокатного производства – красных шламов (КШ) и замасленной прокатной окалины (ЗПО) можно рассматривать как дополнительный источник железорудного сырья в черной металлургии. Настоящая статья является продолжением исследований, в которых рассматривались вопросы получения гидрометаллургическим способом коллективного железорудного концентрата из отходов глиноземного и прокатного производств [1, 2]. В данной работе рассматриваются варианты получения окускованного сырья с заданными по составу характеристиками и сравнительная оценка их металлургических свойств применительно к пирометаллургической переработке в области черной металлургии.
Согласно предварительной оценке [2] в лабораторных условиях из замасленной прокатной окалины и концентрата смеси красных шламов, были получены окатыши естественной основности и офлюсованные известняком, химический состав которого приведен в табл. 1. В состав связки окатышей входил бентонит (0.7% от общей массы), обжиг проводили при температуре 1200°С. Для обеспечения офлюсования окатышей до степени CaO/SiO2 ≈ 2.10 использовался обычный известняк подготовленной крупности, влажность концентрата – 9%. Режим окомкования и термообработки (сушка, нагрев, обжиг и охлаждение) исходных проб соответствовал типичным условиям промышленного производства на обжиговых машинах. Химический состав полученных окатышей представлен в табл. 2.
Таблица 1.
Исходный химический состав концентрата (КШ + ЗПО), мас. %
Feобщ | Fe2O3 | FeO | CaO | MgO | SiO2 | TiO2 | Al2O3 | MnO |
---|---|---|---|---|---|---|---|---|
56.74 | 54.06 | 24.29 | 5.74 | 0.74 | 3.65 | 1.47 | 5.61 | 0.46 |
V2O5 | NiO | Cr2O3 | Na2O | K2O | CuO | CoO | P2O5 | SO3 |
0.04 | 0.12 | 0.00 | 1.45 | 0.09 | 0.11 | 0.10 | 1.46 | 0.61 |
Таблица 2.
Химический состав неофлюсованных (ОНФ) и офлюсованных (ОФ) окатышей, мас. %
Окатыши | Feобщ | Fe2O3 | FeO | CaO | MgO | SiO2 | TiO2 | Al2O3 | MnO |
---|---|---|---|---|---|---|---|---|---|
ОНФ | 55.31 | 76.24 | 2.5 | 5.61 | 0.75 | 3.95 | 1.44 | 5.61 | 0.30 |
ОФ | 53.85 | 74.15 | 2.5 | 8.09 | 0.75 | 3.85 | 1.40 | 5.47 | 0.29 |
Окатыши | V2O5 | NiO | Cr2O3 | Na2O | K2O | CuO | CoO | P2O5 | SO3 |
ОНФ | 0.04 | 0.10 | 0.11 | 1.46 | 0.04 | 0.11 | 0.10 | 1.32 | 0.12 |
ОФ | 0.03 | 0.09 | 0.10 | 1.16 | 0.03 | 0.08 | 0.08 | 1.26 | 0.11 |
Анализ показывает, что в результате окислительного обжига в полученном окускованном сырье существенно снизилось содержание вредных примесей, в том числе серы (с 0.61 до 0.11–0.12%). Тем не менее, содержание пентаоксида фосфора, осталось на достаточно высоком уровне – 1.26–1.32%.
Также для исследования процесса переработки металлизованного сырья из исследуемого концентрата были получены рудоугольные окатыши (ОМ) естественной основности. Окомкованные рудоугольные гранулы, влажностью 8.5% обжигали в окислительной атмосфере при 1200–1220°С. В качестве связки использовали бентонит (0.7% по массе). Заданная конечная основность окатышей колебалась в пределах CaO/SiO2 ≈ 1.12–1.15. Исходный и конечный состав полученных окатышей приведен в табл. 3.
Таблица 3.
Химический состав исходных и обожженных рудоугольных окатышей, мас. %
Окатыши | Feобщ | Fe2O3 | FeO | CaO | MgO | SiO2 | TiO2 | Al2O3 | MnO |
---|---|---|---|---|---|---|---|---|---|
Исх. | 46.45 | 45.45 | 18.81 | 7.95 | 0.75 | 7.07 | 1.71 | 7.14 | 0.57 |
Обож. | 49.83 | 32.24 | 35.04 | 9.31 | 0.75 | 8.12 | 2.07 | 8.58 | 0.68 |
Окатыши | V2O5 | NiO | Cr2O3 | Na2O | K2O | CuO | CoO | P2O5 | SO3 |
Исх. | 0.03 | 0.08 | 0.12 | 1.41 | 0.10 | 0.11 | 0.90 | 1.73 | 0.56 |
Обож. | 0.05 | 0.00 | 0.11 | 1.46 | 0.06 | 0.10 | 0.10 | 2.06 | 0.68 |
Исследование восстановимости железорудного сырья
Методика исследования по ГОСТ 17 212-84 заключается в восстановлении пробы восстановительным газом (CO + H2) при заданных температурных условиях (до 1100°С) и определении степени восстановления по результатам химического анализа исходной и восстановленной пробы или потере массы кислорода при восстановлении. Результаты определения восстановимости неофлюсованных (ОНФ) и офлюсованных (ОФ) окатышей приведены в табл. 4 и 5. На рис. 1 приведены кинетические кривые восстановления исследуемых окатышей и окатышей Михайловского ГОКа (МГОК), сравнительный анализ которых показывает, что восстановительный процесс опытных офлюсованных окатышей протекает более полно в сравнении с неофлюсованными и практически идентичен промышленным окатышам МГОКа.
Таблица 4.
Условия проведения опытов по восстановимости
Опыт | ОНФ | ОФ |
---|---|---|
Класс крупности, мм | –12.5 + 10 | –12.5 + 10 |
Масса перед восстановлением, г | 500 | 500 |
Масса после восстановления, г | 446.5 | 439.5 |
Восстановимость | 57.46 | 67.94 |
Состав газа, % | 100 | 100 |
СО | 35 | 35 |
N2 | 65 | 65 |
Расход газа, дм3/мин | 30 | 30 |
Температура нагрева, °С | ||
первые 40 мин | 600 | |
послед. 175 мин | 1100 |
Таблица 5.
Химический состав исходных и восстановленных образцов и экспериментальные значения восстановимости по ГОСТ 17 212-84
Химический состав | ||||||
---|---|---|---|---|---|---|
исходная проба | восстановленная проба | |||||
Fеобщ | Feмет | FeO | Fеобщ | Feмет | FeO | |
ОНФ | 55.31 | 0.00 | 2.50 | 58.73 | 25.26 | 34.00 |
ОФ | 53.85 | 0.00 | 2.50 | 63.63 | 37.57 | 22.88 |
восстановимость | ||||||
абс-1 | абс-2 | факт | абс' | |||
ОНФ | 57.95 | 45.88 | 57.46 | 1.16 | ||
ОФ | 68.33 | 53.45 | 67.94 | 1.20 |
Исследование индекса низкотемпературного разрушения при нагревании (LTD)
Сущность методики заключается в восстановлении пробы газообразным восстановителем во вращающемся барабане при заданном температурном режиме и последующем рассеве испытуемого материала на классы крупности, характеризующие его прочностные свойства. Исследование прочности при низкотемпературном восстановлении проводили на установке в соответствии с требованиями ISO 13 930-1998. Результаты исследований прочности исследуемых материалов приведены в табл. 6. Анализ полученных результатов показывает, что “горячая” прочность у окатышей ОНФ, ОФ находится на уровне 81–97%, что обеспечивает высокую газопроницаемость слоя при использовании в агрегатах шахтного типа (доменная печь, вагранка, Мидрекс). Металлизованные рудоугольные окатыши (ОМ) с индексом +6.3 мм LTD = 66% имеют достаточную прочность для использования в электропечах (ДСП, руднотермическая печь).
Таблица 6.
Прочность материалов LTD (+6.3 мм) по ISO 13 930
Окатыши | ОНФ | ОФ | ОМ |
---|---|---|---|
Класс крупности, мм | –12.5 + 10 | –12.5 + 10 | –12.5 + 10 |
Масса перед восстановлением, г | 500.00 | 500.00 | 500.00 |
Масса после восстановления, г | 494.20 | 496.60 | 311.80 |
Класс крупности после опыта, мм | |||
6.3 | 400.00 | 482.20 | 203.50 |
3.15 | 8.20 | 4.10 | 17.00 |
0.5 | 10.10 | 2.30 | 1.00 |
–0.5 | 75.90 | 8.00 | 90.30 |
LTD +6.3 | 80.94 | 97.10 | 65.27 |
LTD –3.15 | 17.40 | 2.07 | 29.28 |
LTD –0.5 | 15.36 | 1.61 | 28.96 |
Состав газа, % | 100 | ||
СО | 20 | ||
СО2 | 20 | ||
Н2 | 2 | ||
N2 | 58 | ||
Расход газа, дм3/мин | |||
СО | 4 | ||
СО2 | 4 | ||
Н2 | 0.4 | ||
N2 | 11.6 |
Исследование температур начала размягчения и температурного интервала размягчения (ТиРП)
Проведение этой методики заключается в нагреве пробы испытуемого материала в инертном газе и определении температуры начала размягчения по началу погружения жесткого штока в пробу под действием внешнего давления, а также температурного интервала размягчения (40% усадки от исходной высоты навески). Исследование температурного интервала размягчения проводили в соответствии с ГОСТ 26 517–85. Результаты исследований температурного интервала исследуемых проб материалов приведены в табл. 7.
Таблица 7.
ТиРП по ГОСТ 26 517–85
Проба | ОНФ | ОФ | ОМ |
---|---|---|---|
Класс крупности, мм | –12 + 10 | –12 + 10 | –12 + 10 |
Температура начала размягчения, °С | 1220 | 950 | 1020 |
Температура конца размягчения, °С | 1430 | 1150 | 1160 |
Интервал размягчения, °С | 210 | 200 | 140 |
По результатам проведенных опытов офлюсованные и металлизованные окатыши наиболее полно отвечают требованиям к интервалу размягчения–плавления для условий доменной плавки, а именно: чем меньше ТИРП, тем уже зона когезии и лучше газо- и гидродинамика в печах шахтного типа.
Исследование рентгенофазового состава исследуемых материалов
Методом рентгенофазового анализа проведено исследование исходного концентрата, а также окатышей (неофлюсованных и офлюсованных), полученных этого концентрата. Съемка образцов проводилась на рентгеновском дифрактометре марки XRD 7000С (фирма SHIMADZU) с автоматическим программным управлением, с использованием CuKα-излучения (напряжение на трубке 40 кВ, ток на трубке 30 мА) и графитового монохроматора. Идентификацию фаз осуществляли, используя базу данных PDF2 (ICDD) (2018 г.).
Исследуемый исходный концентат характеризуется (рис. 2) сложным фазовым составом. Основу концентрата составляет гематит (Fe2O3). Другие железосодержащие фазы представлены магнетитом (Fe3O4), вюститом (FeO), в небольшом количестве железо может присутствовать в Mn, Al, Mg-содержащем силикате. В табл. 8 приведен фазовый состав исходного концентрата по данным рентгенофазового анализа.
Рис. 2.
Дифрактограмма исходного концентрата. Условные обозначения: v – Fe2O3; o – Fe3O4; w – FeO; + – CaCO3; x – Mg0.24Mn1.82Al1.86Fe0.09Si0.98O5(OH)4; s – SiO2 (кварц); u – Na2Ca(CO3)2; z – Na2(CO3)·H2O.
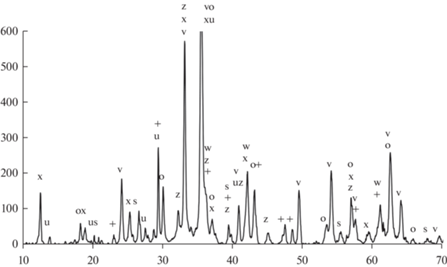
Таблица 8.
Фазовый состав исходного концентрата
Фазы, обнаруженные рентгенофазовым методом | Исходный концентрат |
---|---|
Fe2O3 (гематит) | Основная фаза |
Fe3O4 (магнетит) | |
FeO (вюстит) | |
(Mn1.82Al0.84Mg0.24Fe0.09)(Si0.98Al1.02O5)(OH)4 | |
CaCO3 – гидрокарбонат кальция | |
Na2Ca(CO3)2 – ньеререит | |
Na2(CO3)⋅H2O – моногидрат карбоната натрия | |
NaHCO3 – гидрокарбонат натрия | Возможно присутствует |
3CaOAl2O3 – трехкальциевый алюминат | Возможно присутствует |
SiO2 – (кварц) | Основная фаза |
Исходный концентрат использовали для получения неофлюсованных и офлюсованых окатышей, окислительный обжиг которых осуществляли при температуре 1200°С. В окисленных и восстановленных окатышах железосодержащие фазы представлены магнетитом (Fe3O4 – является основной фазой), гематитом (Fe2O3 – его количество значительно меньше) и вюститом (FeO – в данной фазе может присутствовать MnO в виде твердого раствора, так как ионный радиус марганца больше чем у двухвалентного железа, что способствует увеличению параметра кристаллической решетки “d”). Силикатная часть в основном состоит из магнезиального геленита (в исходном) и акерманита алюминиевого (после восстановления). Это проявляется в различии содержания Al и Mg: больше алюминия и меньше магния в исходном обожженном неофлюсованном окатыше и наоборот в пробе подвергнутому нагреву до 500°С восстановительным газом по ISO 13 930-1998.
Восстановление по ГОСТ 17 212–84 обожженных неофлюсованных окатышей приводит к образованию металлического железа в форме α-Fe. При восстановлении растет содержание FeO, в небольших количествах остается Fe3O4 и Fe2O3. Силикатная часть состоит в основном из геленита (Ca2Al2SiO7) и небольшого количества нефелина Na⋅(AlSiO4).
Восстановление по ГОСТ 17 212-84 офлюсованных обожженных окатышей приводит к образованию тех же фаз, что и без добавки флюса. Однако наблюдается наиболее четкое формирование структуры силикатной составляющей. Это можно объяснить присутствием дополнительного количества кальция, взятого в качестве флюса. Особенно это заметно при восстановлении офлюсованных окатышей. Количественная оценка фаз, образующихся в офлюсованных и неофлюсованных обожженных окатышах (исходных, частично восстановленных по ISO 13 930–1998 и восстановленных по ГОСТ 17 212–84) сведена в табл. 9.
Таблица 9.
Фазовый состав исследуемых окатышей, мас. %
Проба | Фазы, обнаруженные рентгенографическим методом | ||||||
---|---|---|---|---|---|---|---|
α-Fe | Fe3O4 | Fe2O3 | FeO | геленит магнез. Сa2(Mg0.25 Al0.75) (Si1.25Al0.75O7) |
акерманит алюмин. Сa2Mg0.75Al0.5Si1.75O7) |
нефелин Na(Al⋅SiO4) |
|
Окатыш неофлюсов. (исх.) | 63.85 | 20.83 | 1.27 | 14.05 | |||
Окатыш неофлюсов (ISO 13 930–1998) |
62.69 | 10.95 | 3.24 | 23.12 | |||
Окатыш неофлюсов (ГОСТ 17 212–84) |
30.05 | 7.52 | 8.19 | 22.74 | 18.75 | 12.75 | |
Окатыш офлюсов. (исх.) | 59.82 | 13.66 | 6.30 | 20.23 | |||
Окатыш офлюсов (ISO 13 930–1998) | 60.55 | 11.96 | 4.40 | 23.09 | |||
Окатыш офлюсов (ГОСТ 17 212–84) | 35.57 | Не опр. | 7.72 | 21.48 | 29.4 | 5.30 |
На следующем этапе исследований были изучены возможности практического использования полученных окускованных железорудных материалов. Вопрос применимости офлюсованных и нефлюсованных окатышей в аглодоменном производстве был подробно рассмотрен ранее в [3], поэтому для оценки возможного использования опытных рудоугольных окатышей, последние были проплавлены в лабораторной печи с получением металла и шлака, химический состав которых приведен в табл. 10. Плавка проводилась в обычных условиях характерных для электропечи, без добавок, с выдержкой после расплавления 30 мин для лучшего разделения металла и шлака.
Таблица 10.
Химический состав металла и шлака, мас. %
Металл | |||||||
---|---|---|---|---|---|---|---|
[C] | [Si] | [Ti] | [P] | [S] | [Mn] | [Cr] | [V] |
4.85 | 2.40 | 0.25 | 1.18 | 0.057 | 0.69 | 0.05 | 0.11 |
Шлаковая часть | |||||||
CaO | MgO | SiO2 | TiO2 | Al2O3 | MnO | K2O + Na2O | SO3 |
44.40 | 4.16 | 17.20 | 1.76 | 25.14 | 0.18 | 1.85 | 5.20 |
Выход металла составил около 62% от исходной массы загруженных окатышей. Состав полученного металла соответствует высокопрочному аустенитно-бейнитного класса литейному чугуну марки ПЛ-4. Полученный шлак содержит компоненты CaO и Al2O3, в количестве, которое позволяет рассматривать его как ценную добавку для получения либо глиноземсодержащих цементов либо, после предварительных подготовительных операций, последующий возврат в схему переработки бокситового сырья.
Термодинамические свойства шлака
Высокоглиноземистые шлаки c содержанием Al2O3 более 20 мас. % характеризуются повышенными значениями вязкости и низкой жидкотекучестью, что предопределяет значительные затруднения с отработкой такого шлака при пирометаллургическом переделе в доменном процессе или электроплавке. В связи с этим актуальной задачей становится предварительный оперативный контроль структурно-чувствительных свойств такого шлака с помощью тройных диаграмм состояния CaO–SiO2–MgO наиболее полно представленных в [9]. Для удобства была разработана методика расчета фигуративных точек температур кристаллизации в составе пакета электронных таблиц MS EXCEL для исследуемого состава оксидной системы в интервале содержания глинозема от 5 до 35% (мас.). На рис. 3 представлена программная реализация такой расчетной методики для расчета геометрического местоположения точки кристаллизации. Для полученного опытного шлака (25% Al2O3) температура кристаллизации лежит в диапазоне 1480–1485°С.
Рис. 3.
Расчетная фигуративная точка (красный цвет) кристаллизации шлака электроплавки рудоугольных окатышей ОМ.
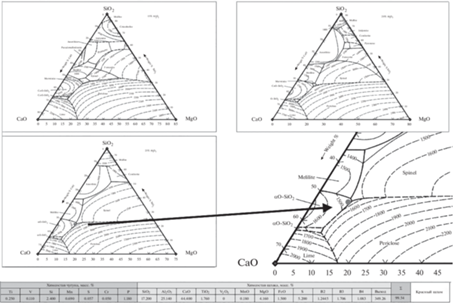
Для разработки модели расчета вязкости оксидных шлаковых систем, в качестве базовой, использовали методику определения вязкости шлака, представленную в [10] и позволяющую учитывать влияние максимально широкого спектра составов реальных шлаков в рабочем интервале температур. Дополнительно ввели в расчетную методику влияние соотношения в расплаве кислых, основных и амфотерных оксидов и влияние массовой доли каждого оксида в расплаве, а также влияние температуры расплава.
Уравнение для расчета вязкости имеет следующий вид:
(1)
$\eta = A \cdot {{\eta }_{{\text{o}}}} \cdot {{e}^{{\left( {{\text{\;}}\frac{C}{{B{\kern 1pt} '}}{\text{\;}}} \right)}}},$Эмпирические коэффициенты в уравнениях для расчета температурных коэффициентов А и С были подобраны с таким расчетом, чтобы как можно точнее подходить к экспериментальным данным, полученным для промышленных и полусинтетических шлаковых расплавов, а также соответствовать стандартному описанию измерений вязкости расплавов для различных температур. Параметр основности $B{\kern 1pt} '$ рассчитывается по формуле:
(2)
$B{\kern 1pt} {\text{'}} = \frac{{\sum {\text{(}}{{a}_{i}} \cdot {{X}_{O}}{\text{)}}}}{{\sum \left( {{{c}_{i}} \cdot {{X}_{K}}} \right) + \sum {\text{(}}{{d}_{i}} \cdot {{X}_{А}}{\text{)}}}},$Коэффициент ${{\eta }_{{\text{o}}}}$ предполагается рассматривать функционально зависящим от состава и температуры расплава, т.е. ${{\eta }_{{\text{o}}}} = f\left( T \right)$ и, например, для оксида алюминия принимается ${{\eta }_{{{\text{oA}}{{{\text{l}}}_{{\text{2}}}}{{{\text{O}}}_{{\text{3}}}}}}} = - {\kern 1pt} {\text{0}}{\text{.02}}3 \cdot {\text{ln}}\left( T \right) + {\text{0}}{\text{.1753}}{\text{.}}$
Адекватность предложенной методики проверили по экспериментальным данным вязкости шлаков, полученных в условиях работы доменного цеха НТМК и ОХМК.
На рис. 4 представлены результаты расчетных и фактических значений вязкости различных шлаков по предложенной методике в интервале температур 1200–1550°С. Из анализа представленных данных можно сделать вывод о том, что разработанная методика определения вязкости шлака дает достаточно близкие значения вязкости к определенным экспериментальным путем данным. При вязкости менее 8 Пз жидкоподвижность шлака достаточна для его отработки и выпуска из печи, поэтому его температура должна быть не менее 1450–1500°С, что достаточно хорошо согласуется с найденным ранее значением температуры кристаллизации шлака – 1480–1485°С.
ЗАКЛЮЧЕНИЕ
В результате проведенных исследований предложены технические решения, позволяющие комплексно утилизировать отходы, образующиеся при производстве алюминия (красные шламы) и прокатной окалины:
• разработаны оптимальные технологические режимы для получения коллективного железорудного концентрата гидрометаллургическим способом, соответствующего основным требованиям по химическому и гранулометрическому составу компонентов в области черной металлургии;
• получены в лабораторных условиях окускованный материал (окатыши) различной основности и степени металлизации, определены основные технологические параметры окускования и термообработки для получения заданных характеристик окатышей;
• проведены исследования по определению основных металлургических свойств (восстановимость, горячая прочность, интервалы размягчения и плавления) окатышей различного типа;
• с помощью методов математического моделирования определены технико-экономические показатели вариантов пирометаллургической схемы переработки исследуемых материалов с получением товарных продуктов различного назначения.
На основании проведенных исследований рекомендован вариант технологической схемы переработки железорудного концентрата с получением офлюсованных окатышей, используемых в качестве железосодержащей добавки для аглококодоменного производства или металлизованных окатышей для руднотермической плавки с получением товарного металла и глиноземсодержащего шлака, пригодного для последующего использования в качестве добавки к бокситовому сырью для процесса Байера либо для получения цемента в строительной индустрии.
Список литературы
Танутров И.Н., Свиридова М.Н., Чесноков Ю.А., Маршук Л.А. // Изв. вузов. Черная Металлургия. 2020. 63. № 11–12. Р. 891–898. https://doi.org/10.17073/0368-0797-2020-11-12-891-898
Танутров И.Н., Свиридова М.Н., Лямкин С.А., Чесноков Ю.А., Овчинникова Л.А., Маршук Л.А. // Бутлеровские сообщения. 2019. 58. № 6. С. 97–103. https://butlerov.com/stat/reports/details.asp?lang=ru&id=32432
Чесноков Ю.А., Маршук Л.А., Танутров И.Н., Свиридова М.Н. // Черная металлургия. Бюллетень научно-технической и экономической информации. 2020. 76. № 1. Р. 68–73. https://doi.org/10.32339/0135-5910-2020-1-68-73
Распопов Н.А., Корнеев В.П., Аверин В.В. Восстановление оксидов железа при пирометаллургической переработке красных шламов // Металлы. 2013. № 1. С. 41–45.
Корнеев В.И., Сусс А.Г., Цеховой А.И. Красные шламы: свойства, складирование, применение. М.: Металлургия, 1991.
Деревянкин В.А., Кузнецов С.И., Чупраков В.Я., Леонтьев Л.И. Комплексное использование низкокачественных бокситов. М.: Металлургия, 1972.
Мушкетов А.А., Газалеева Г.И., Сопина Н.А., Власов И.А. Выбор схемы обогащения красных шламов // Цветные металлы. 2013. № 7. С. 46–50.
Яценко С.П., Пягай И.Н., Пасечник Л.А., Суриков В.Т., Анашкин В.С., Климентенок Г.Н. Комплексная переработка и обезвреживание отхода глиноземного производства -красных шламов // Третий международный конгресс “Цветные металлы-2011", г. Красноярск. 2011. С. 123–126.
Allibert M., Gaye H. Slag Atlas. Dusseldorf: Stahleisen, 1995.
Iida T., Sakai H., Kawasima T., Kurihara Y.: Proc. 5th Int. Conf. on Molten Slags, Fluxes and Salts’97, Sydney, Australia, Iron & Steel Society, 1997.
Смирнов Д.И., Молчанова Т.В., Водолазов Л.И., Пеганов В.И. Методы переработки красных шламов // Цветные металлы. 2002. № 8. С. 64–69.
Леонтьев Л.И., Дюбанов В.Г., Зиновьев Д.В., Грудинский Д.И. Обзор мировой практики переработки красных шламов. Часть 1. Пирометаллургические способы // Изв. вузов. Черная металлургия. 2018. № 11. С. 843–858.
Можаренко Н.М., Носков В.А., Нестеров А.С. Влияние красных шламов на металлургические свойства агломерата // Фундаментальные и прикладные проблемы черной металлургии: Сб. научн. трудов. Днепропетровск. 2004. № 3. С. 62–70.
Чесноков Ю.А., Леонтьев Л.И., Дмитриев А.Н. Пирометаллургическая переработка отходов алюминиевого производства // Вестник МГТУ им. Г.И. Носова. 2013. № 3. С. 19–22.
Чесноков Ю.А. Информационная система “Интерактивные расчеты в черной металлургии” // Черная металлургия. Бюллетень научно-технической и экономической информации. 2015. № 12. С. 63–67.
Братыгин Е.В., Газалеева Г.И., Дмитриева Е.Г., Калугин Я.И. Использование обогащенных красных шламов при производстве высокоофлюсованного агломерата с целью дальнейшей их переработки в доменных печах // Черная металлургия. Бюллетень научно-технической и экономической информации. 2013. № 1. С. 30–34.
Роменец В.А., Валавин В.С., Похвиснев Ю.В. Утилизация красных шламов алюминиевой промышленности процессом Ромелт // Цветные металлы. 2011. № 7. С. 39–44.
Коршунов Е.А., Буркин С.П., Логинов Ю.Н. Патент № 2245371 C2 РФ, МПК C21B 3/04, C21B 13/00, C22B 34/12. Способ переработки красного шлама глиноземного производства: № 2003103262/02. Опубл. 27.01.2005.
Жумашев К.Ж., Торговец А.К., Кутжанова А.М. Изучение способов переработки красного шлама и оценка возможности развития нового направления исследований // Инновации в материаловедении и металлургии: материалы IV Междунар. Интеракт. научно-практич. Конф. Екатеринбург, 2015. С. 122–126.
Столяревский А.Я. Патент № 2542177 C1 РФ, МПК C22B 7/00, C22B 1/24, C22B 1/02. Способ переработки красного шлама: № 2013147294/02. Опубл. 20.02.2015.
Ни Л.П., Пономарев В.Д., Сажин В.С. Авторское свидетельство № 117646 A1 СССР, МПК C22B 7/00, C01F 7/38. Способ переработки красного шлама, содержащего титан: № 598 559. Опубл. 01.01.1958.
Дополнительные материалы отсутствуют.