Расплавы, 2022, № 5, стр. 477-484
Влияние кобальта на коррозионную стойкость аморфных сплавов Al–Ni–Co–R
Э. А. Карфидов a, Е. В. Никитина a, Б. А. Русанов b, *, В. Е. Сидоров b, c
a Институт высокотемпературной электрохимии УрО РАН
Екатеринбург, Россия
b Уральский государственный педагогический университет
Екатеринбург, Россия
c Уральский федеральный университет
Екатеринбург, Россия
* E-mail: rusfive@mail.ru
Поступила в редакцию 07.05.2022
После доработки 03.06.2022
Принята к публикации 10.06.2022
- EDN: NIDBXW
- DOI: 10.31857/S0235010622050048
Аннотация
Аморфные и нанокристаллические сплавы алюминий–переходный металл–редкоземельный металл активно исследуются в последние годы, благодаря повышенным значениям коррозионных и механических свойств по сравнению с кристаллическими аналогами. Для более широкого промышленного использования аморфных сплавов Al–ПМ–РЗМ необходимо повышение их термической стабильности и стеклообразующей способности. Использование одновременно двух переходных металлов – никеля и кобальта в различных соотношениях, и, соответственно, создание композиций Al–Ni–Co–РЗМ, позволяет получать аморфные сплавы с большей GFA и термической стабильностью по сравнению с тройными составами. В настоящей работе исследовано влияние содержания кобальта на коррозионное поведение аморфных лент Al-Ni–Co–Gd(Yb), полученных методом спиннингования из металлических расплавов. Чем выше растворимость гидроксида РЗМ, тем меньше коррозионная стойкость и, соответственно, выше скорость коррозии материала. По данным гравиметрического и химического анализов показано, что составы с большим содержанием кобальта (4 ат. %) имеют большую коррозионную стойкость в исследуемых условиях, чем составы, содержащие 2 ат. % кобальта. Сплавы состава Al86Ni4Co4R6 оказались более стойкими, чем сплавы Al86Ni6Co2R6, несмотря на несколько большую электроотрицательность кобальта по сравнению с никелем, что может быть связано с меньшей растворимостью гидроксида кобальта(II). Изученные композиции имеют высокие показатели коррозионной стойкости и могут рассматриваться в качестве перспективных при разработке защитных покрытий на основе алюминия.
ВВЕДЕНИЕ
Аморфные и нанокристаллические алюминиевые сплавы с переходными (ПМ) и редкоземельными металлами (РЗМ) характеризуются высокими показателями эксплуатационных характеристик [1–4]. В частности, композиции Al–Ni–РЗМ обладают хорошими механическими свойствами – их предел прочности на разрыв составляет 1560 МПа, что в три раза превышает соответствующее значение для традиционных высокопрочных кристаллических сплавов на основе алюминия [1]. Аморфные же сплавы составов Al—Co–РЗМ демонстрируют высокую коррозионную стойкость в растворах NaCl [5–9]. Некоторые из этих сплавов в настоящее время рассматриваются как перспективные защитные покрытия для различных материалов [5, 10].
Для более широкого промышленного использования аморфных сплавов Al–ПМ–РЗМ необходимо повышение их термической стабильности и стеклообразующей способности (glass forming ability – GFA) [2]. В наших недавних работах [11, 12] мы показали, что использование одновременно двух переходных металлов – никеля и кобальта в различных соотношениях, и, соответственно, создание композиций Al–Ni—Co–РЗМ, позволяет получать аморфные сплавы с большей GFA и термической стабильностью по сравнению с тройными составами. Кроме того, эти сплавы обладают как отличными механическими свойствами, так и повышенной антикоррозионной стойкостью. Среди добавляемых редкоземельных металлов предпочтительными являются неодим, гадолиний и иттербий, т.к. они лучше других редкоземельных металлов повышают GFA сплавов [13].
В настоящей работе изучены коррозионные свойства аморфных сплавов Al–Ni—Co–Gd и Al–Ni–Co–Yb с различным соотношением переходных металлов. Анализ результатов представлен с точки зрения влияния содержания кобальта на коррозионную стойкость аморфных сплавов. Результаты исследования сплавов с неодимом представлены в [14].
МАТЕРИАЛЫ И МЕТОДЫ
Сплавы составов Al86Ni6Co2R6 и Al86Ni4Co4R6 (R = Gd, Yb) (здесь и далее приведены атомные проценты) получены электродуговой плавкой чистых компонентов Al (99.999%), Ni (99.9%), Co (99.9%), Gd (99.8%) и Yb (99.8%) в атмосфере аргона. Для гомогенизации сплавов переплав проводили 4 раза.
Металлические ленты (ширина 4 мм, толщина 35–40 мкм) получены методом спиннингования в контролируемой атмосфере аргона. Подробное описание метода приведено в работе [11]. Структура исходных лент изучена методом рентгеновской дифракции на дифрактометре D8 Advance (Bruker AXS) (CuKα). Установлено, что все ленты являются рентгеноаморфными. Типичная рентгенограмма (на примере сплава Al86Ni6Co2Gd6) показана на рис. 1.
Оптическая и электронная микроскопии показали, что полученные аморфные металлические ленты однородны по своей структуре и соответствуют заявленному составу, а поверхность не содержит следов разрушения или локальных коррозионных очагов.
Коррозионные свойства сплавов исследованы в 5 мас. % водном растворе NaCl при 27°С в течение 1500 ч в термостате Tagler. Испытания проводились параллельно на трех образцах одинакового состава. Перед опытами образцы промывали дистиллированной водой и этаноло-ацетоновой смесью, сушили и взвешивали. Массовый и глубинный показатель скорости коррозии определяли по данным гравиметрических измерений и химического анализа. Морфология поверхности образцов исследовалась на электронном микроскопе GEOL SM-5900 LV до и после эксперимента для определения характера коррозионного разрушения сплава. Элементный анализ растворов, в которых осуществлялась выдержка образцов, проводили на оптическом эмиссионном спектрометре с индуктивно связанной плазмой OPTIMA 4300 DV (Perkin Elmer, USA).
РЕЗУЛЬТАТЫ И ОБСУЖДЕНИЕ
Скорости коррозии, рассчитанные по данным гравиметрического и химического анализов, представлены в табл. 1. Процесс и скорость коррозии металлических материалов оценивают следующими методами:
Таблица 1.
Скорости коррозии аморфных сплавов Аl–Ni–Co–R (R = Gd, Yb)
Сплав | Гравиметрический анализ | Химический анализ | |
---|---|---|---|
скорость коррозии, мг/м2 · ч | показатель глубины коррозии, мм/год | скорость коррозии, мг/м2 · ч | |
Al86Ni6Co2Gd6 | 5.21 ± 0.25 | 0.0162 ± 0.0008 | 5.25 |
Al86Ni4Co4Gd6 | 0.60 ± 0.03 | 0.0019 ± 0.0001 | 0.65 |
Al86Ni6Co2Yb6 | 1.83 ± 0.09 | 0.0059 ± 0.0003 | 2.19 |
Al86Ni4Co4Yb6 | 0.43 ± 0.02 | 0.0014 ± 0.0001 | 0.67 |
1) Гравиметрический метод (весовой показатель). Средняя скорость коррозии – коррозионные потери массы металла с единицы поверхности металла в единицу времени:
где m0, m1 – масса образца исходного и после коррозионного испытания, кг.2) Гравиметрический метод (глубинный показатель). Используя весовой метод, невозможно сравнить между собой коррозионную стойкость металлов, сталей и сплавов с различной плотностью. Учитывают это, применяя глубинный показатель коррозии П –глубину коррозионного разрушения металла в единицу времени:
где ρ – плотность металла, кг/м3.Испытания образцов исследуемых материалов осуществляли в параллели по 5 образцов. Предварительно материалы нарезали на образцы, равные по размерам и обрабатывались шлифовальной бумагой различной зернистости для удаления неровностей и заусенцев после резки. Далее образцы промывали, обезжиривали, сушили. После стадии сушки образцы незамедлительно отправлялись в бокс на хранение, для избегания формирования на поверхности оксидного слоя под действием окислительной атмосферы воздуха. Также производили замер габаритных размеров цифровым штангенциркулем для последующего расчета площади контакта материала с солевым электролитом, и многократное взвешивание образцов для определения скорости коррозии весовым методом.
Установлено, что скорости коррозии, рассчитанные по гравиметрическим измерениям несколько ниже, чем скорости коррозии, полученные с помощью элементного химического анализа растворов после испытаний. Это можно объяснить образованием кислородсодержащих слоев с хорошими адгезивными свойствами на поверхности образцов, что приводит к занижению реальных показателей коррозионных потерь материала. Установлено, что аморфные сплавы с одинаковым соотношением Ni/Co имеют большую коррозионную стойкость среди исследованных образцов.
Элементный анализ растворов, контактировавших с образцами в течение 1500 часов, показал, что доля перехода алюминия в раствор составляла в среднем 73–80%, РЗМ – 17–23%, кобальта и никеля менее 2.5%. Данные элементного анализа растворов после экспериментов представлены в табл. 2.
Таблица 2.
Данные элементного анализа коррозионных растворов после испытаний
Сплав | Среднее содержание элемента в пробе, ат. % | |||
---|---|---|---|---|
Al | Ni | Co | Yb или Gd | |
Al86Ni6Co2Gd6 | 92.86 | 1.46 | 0.71 | 4.97 |
Al86Ni4Co4Gd6 | 93.39 | 1.35 | 0.21 | 5.05 |
Al86Ni6Co2Yb6 | 93.45 | 1.34 | 0.89 | 4.32 |
Al86Ni4Co4Yb6 | 95.25 | 1.25 | 0.32 | 3.18 |
Полученные результаты могут указывать на то, что Al, Gd и Yb активно взаимодействуют с агрессивной средой, в отличии от переходных металлов. В свою очередь никель переходит в раствор в большем количестве, чем кобальт. Установлено, что наименьшие значения кобальта в растворах соответствуют составам, имеющим равное соотношение никеля и кобальта.
На рис. 2 показана морфология поверхности образцов после коррозионных испытаний, а в табл. 3 представлены данные рентгеноспектрального анализа поверхности аморфных сплавов Al–Ni–Co–Gd.
Рис. 2.
Морфология аморфных лент Al86Ni6Co2Gd6 (а) and Al86Ni4Co4Gd6 (б) после 1500 ч в водном растворе 5 мас. % NaCl.
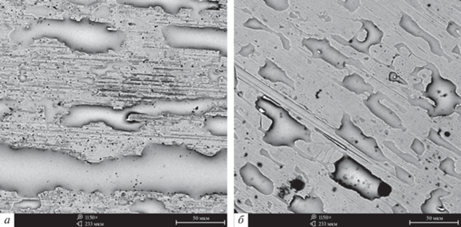
Таблица 3.
Данные рентгеноспектрального анализа аморфных сплавов Al–Ni–Co–Gd
Элемент | Среднее содержание элемента, мас. % | |||
---|---|---|---|---|
Al86Ni6Co2Gd6 | Al86Ni4Co4Gd6 | |||
до испытаний | после испытаний | до испытаний | после испытаний | |
O | 2.83 | 14.79 | 8.16 | 14.95 |
Al | 65.99 | 57.06 | 60.21 | 59.51 |
Gd | 19.64 | 19.28 | 21.24 | 20.51 |
Ni | 8.57 | 7.52 | 4.99 | 1.13 |
Co | 2.97 | 1.35 | 5.40 | 3.90 |
Точечная коррозия, при которой диаметр коррозионного поражения меньше, чем глубина очага, характерна для образцов, содержащих Gd. С увеличением концентрации никеля отмечается более интенсивное протекание локальных коррозионных процессов, в частности, увеличивается диаметр локальных коррозионных поражений.
Аналогичные данные для образцов с иттербием представлены на рис. 3 и в табл. 4.
Рис. 3.
Морфология аморфных лент Al86Ni6Co2Yb6 (а) и Al86Ni4Co4Yb6 (б) после 1500 ч в водном растворе 5 мас. % NaCl.
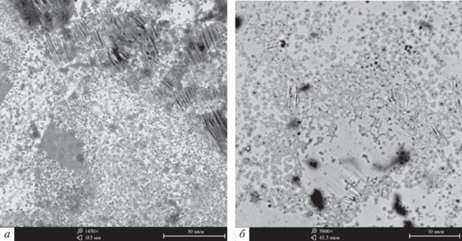
Таблица 4.
Данные рентгеноспектрального анализа аморфных сплавов Al–Ni–Co–Yb
Элемент | Среднее содержание элемента, мас. % | |||
---|---|---|---|---|
Al86Ni6Co2Yb6 | Al86Ni4Co4Yb6 | |||
до испытаний | после испытаний | до испытаний | после испытаний | |
O | 3.55 | 14.34 | 2.74 | 8.12 |
Al | 67.24 | 66.76 | 69.84 | 66.64 |
Yb | 16.27 | 11.54 | 15.65 | 13.99 |
Ni | 9.90 | 5.72 | 6.20 | 6.10 |
Co | 3.04 | 1.64 | 5.57 | 5.15 |
В отличии от сплавов с гадолинием, аморфные сплавы Al–Ni–Co–Yb с различным содержанием кобальта подвержены локальной язвенной коррозии, при которой диаметр очага больше, чем глубина. Установлено, что обширные очаги коррозионных поражений равномерно распределены по поверхности аморфной ленты. Следует отметить, что в образцах с высоким содержанием никеля размер коррозионных поражений возрастает.
Установлено, что на всех образцах образуется устойчивый слой гидроксида алюминия из-за взаимодействия с агрессивной средой.
Для конкретизации механизма коррозионного процесса аморфных лент сложного состава был произведен расчет изобарно-изотермического потенциала взаимодействия компонентов сплава с реакционной средой с образованием гидроксидов металлов. Для расчетов использован пакет HSC Chemistry 9, диапазон температур для расчета энергии Гиббса был выбран от 10 до 50°С.
Редкоземельные металлы, особенно гадолиний, склонны к образованию гидроксидов в большей степени, чем алюминий [15]. Никель и кобальт практически нерастворимы в электролите. Согласно термодинамическим расчетам, любой РЗМ является более электроотрицательным компонентом исследуемых сплавов по сравнению с Ni, Co и Al. Как правило, коррозионная стойкость материала обусловлена растворимостью гидроксида наиболее электроотрицательного компонента сплава [15]. Чем выше растворимость гидроксида РЗМ, тем меньше коррозионная стойкость и соответственно выше скорость коррозии материала.
Кроме того, сплавы состава Al86Ni4Co4R6 оказались более стойкими, чем сплавы Al86Ni6Co2R6, несмотря на несколько большую электроотрицательность кобальта по сравнению с никелем, что может быть связано с меньшей растворимостью гидроксида кобальта(II).
В работах [15, 16] показано, что произведение растворимости гидроксида никеля(II) на несколько порядков выше, чем для гидроксида кобальта(II), что обуславливает стойкость исследуемых сплавов с большим количеством кобальта. Наряду с этим, для алюминия произведение растворимости на несколько порядков меньше, чем для РЗМ, что вызывает точечную и язвенную коррозию аморфных лент из-за растворения образовавшихся слоев R(OH)3, что подтверждается результатами термодинамического анализа. Таким образом можно заключить, что на поверхности исследованных аморфных лент наблюдается локальное растворение образовавшихся слоев R(OH)3, что обуславливает тип и характер коррозионных поражений.
ЗАКЛЮЧЕНИЕ
В настоящей работе изучены коррозионные свойства аморфных сплавов Al–Ni–Co–R (R = Gd, Yb) с различным соотношением никеля и кобальта. Показано, что сплавы с гадолинием подвержены точечной коррозии. Аморфные сплавы с иттербием подвержены локальной коррозии с равномерно распределенными обширными очагами. Установлено, что интенсивность коррозионного процесса увеличивается с уменьшением концентрации кобальта в составе сплавов. Показано, что механизм коррозии во многом определяется разной реакционной способностью компонентов материала и принципиально разной растворимостью образующихся гидроксидных слоев компонентов материала, что объясняет локализацию коррозионного процесса материалов и преобладание точечной и язвенной коррозии, наблюдаемой на поверхности образцов.
Исследование выполнено при финансовой поддержке РФФИ в рамках научного проекта № 20-32-90 015.
Список литературы
Inoue A., Kimura H. // Journal of Light Metals. 2001. 1. P. 31–41. https://doi.org/10.1016/S1471-5317(00)00004-3
Li F.C., Liu T., Zhang J.Y., Shuang S., Wang Q., Wang A.D., Wang J.G., Yang Y. // Materials Today Advances. 2019. 4. 100027. https://doi.org/10.1016/j.mtadv.2019.100027
Zhang L.M., Zhang S.D., Ma A.L., Hu H.X., Zheng Y.G., Yang B.J., Wang J.Q. // Corrosion Science. 2018. 144. P. 172–183. https://doi.org/10.1016/j.corsci.2018.08.046
Sweitzer J.E., Shiflet G.J., Scully J.R. // Electrochimica Acta. 2003. 48. P. 1223–1234. https://doi.org/10.1016/S0013-4686(02)00830-7
Jin L., Zhang L., Liu K., Che Z., Li K., Zhang M., Zhang B. // Journal of Rare Earths. 2021. 39. № 3. P. 340–347. https://doi.org/10.1016/j.jre.2020.04.018
Zhang L.M., Zhang S.D., Ma A.L., Umoh A.J., Hu H.X., Zheng Y.G., Yang B.J., Wang J.Q. // Journal of Materials Science & Technology. 2019. 35. P. 1378–1387. https://doi.org/10.1016/j.jmst.2019.03.014
Tailleart N.R., Huang R., Aburada T., Horton D.J., Scully J.R. // Corrosion Science. 2012. 59. P. 238–248. https://doi.org/10.1016/j.corsci.2012.03.012
Lucente A.M., Scully J.R. Localized corrosion of Al-based amorphous-nanocrystalline alloys with solute-lean nanocrystals: pit stabilization // Journal of The Electrochemical Society. 2008. 155. № 5. P. 234–243.
Gao M.H., Zhang S.D., Yang B.J., Qiu S., Wang H.W., Wang J.Q. // Applied Surface Science. 2020. 530. 147211. https://doi.org/10.1016/j.apsusc.2020.147211
Zhang L.M., Zhang S.D., Ma A.L., Hu H.X., Zheng Y.G., Yang B.J., Wang J.Q. // Surface and Coatings Technology. 2018. 353. P. 263–273. https://doi.org/10.1016/j.surfcoat.2018.08.086
Svec P., Rusanov B., Moroz A., Petrova S., Janickovic D., Sidorov V., Svec Sr.P. // Journal of Alloys and Compounds. 2021. 876. 160109. https://doi.org/10.1016/j.jallcom.2021.160109
Rusanov B., Sidorov V., Svec Sr.P., Svec P., Janickovic D., Moroz A., Son L. // Journal of Alloys and Compounds. 2019. 787. P. 448–451. https://doi.org/10.1016/j.jallcom.2019.02.058
Rusanov B.A., Sidorov V.E., Svec Sr.P., Svec P., Janickovic D. // Russ. J. Inorg. Chem. 2020. 65. P. 663–667. https://doi.org/10.1134/S0036023620050198
Карфидов Э.А., Русанов Б.А., Сидоров В.Е., Никитина Е.В., Швец П., Яничкович Д. // Расплавы. 2022. № 2. С. 189–195. https://doi.org/10.31857/S0235010622010054
Лурье Ю.Ю. Справочник по аналитической химии. М., 1979.
Аксельруд Н.В. Произведения активностей и изобарные потенциалы образования основных хлоридов и гидроокисей редкоземельных элементов // ЖПХ. 1961. 34. С. 776.
Дополнительные материалы отсутствуют.