Расплавы, 2022, № 5, стр. 537-550
Влияние состава газовой и солевой фазы на коррозию металлических материалов на основе никеля в расплавленных хлоридах щелочных металлов
Э. А. Карфидов a, b, Е. В. Никитина a, b, *
a Институт высокотемпературной электрохимии УрО РАН
Екатеринбург, Россия
b Уральский федеральный университет
Екатеринбург, Россия
* E-mail: neekeetina@mail.ru
Поступила в редакцию 07.04.2022
После доработки 12.05.2022
Принята к публикации 14.06.2022
- EDN: FARPKW
- DOI: 10.31857/S023501062205005X
Аннотация
С учетом электрохимической активности хлоридных солевых расплавов проанализированы имеющиеся экспериментальные данные и выявлены фундаментальные закономерности коррозионно-электрохимического поведения металлических материалов на основе никеля в расплавленных галогенидных солевых электролитах, особое внимание уделено взаимосвязи между составом материалов, их свойствами, качеством межфазной границы, составом расплавленного электролита и коррозионными характеристиками и возможными способами защиты от коррозии. При переработке отработавшего ядерного топлива реактора на быстрых нейтронах (ОЯТ РБН) используется расплав LiCl–KCl (0.49 : 0.51) в инертной атмосфере, все металлические материалы в данном солевом расплаве крайне подвержены коррозии, к тому же в процессе переработки ОЯТ как жидкая (расплав), так и газовая фаза насыщаются продуктами деления, которые могут выступать в качестве дополнительных окислителей, усиливая агрессивность среды. Исследовано коррозионное поведение никеля, а также сплавов на его основе (Ni–Cr и Ni–Ti) в солевом расплаве хлорида лития и калия, содержащем в качестве добавки от 0 до 5 мас. % оксида лития Li2O и трихлорида церия CeCl3. Эксперименты были проведены при температуре 500–700°С в инертной атмосфере аргона в течение 24 ч. Было установлено, что скорость коррозии увеличивается в следующем ряду: Ni < NiCr < NiTi. С увеличением температуры скорость коррозии материала значительно возрастает для каждого исследованного материала. По совокупным данным гравиметрического, микрорентгеноспектрального, атомно-эмиссионного спектрального анализа установлено, что основной причиной коррозии является наличие кислородосодержащих примесей (О2) в газовой атмосфере над расплавом и/или в солевом электролите. Данные примеси вступают преимущественно в реакции с электроотрицательными компонентами сплава – Ti, Cr, с образованием их оксидов нестехиометрического состава, что усиливается при введении в расплав оксида лития за счет увеличения концентрации аниона О2–. Введение в расплав трихлорида церия приводит к образованию на поверхности слоя оксихлорида церия стехиометрического состава, что в свою очередь снижает скорость коррозии, за счет пассивации поверхности и экранирующего эффекта, при повышении температуры данный эффект наблюдается в значительно меньшей степени.
ВВЕДЕНИЕ
Солевые расплавы используются в ряде современных пирохимических и электрохимических технологий [1], таких как переработка ядерных материалов, включая отработавшее ядерное топливо (расплавы хлоридов щелочных металлов). Расплавленные галогениды щелочных металлов, используемые как среды для различных высокотемпературных электрохимических технологий, в том числе для переработки отработавшего ядерного топлива, по своей природе являются очень агрессивной средой.
При переработке отработавшего ядерного топлива реактора на быстрых нейтронах (ОЯТ РБН) используется расплав LiCl–KCl (0.49 : 0.51) в инертной атмосфере, все металлические материалы в данном солевом расплаве крайне подвержены коррозии, к тому же в процессе переработки ОЯТ как жидкая (расплав), так и газовая фаза насыщаются продуктами распада, которые могут выступать в качестве дополнительных окислителей, усиливая агрессивность среды. В солевых расплавах высокая температура и концентрация агрессивных веществ, высокая интенсивность протекания процесса делают неприменимыми многие классические методы снижения коррозионных потерь, применяющиеся в низкотемпературных средах. При этом принципиально изменяется механизм коррозии металлических материалов, резко возрастает ее скорость, изменяется характер коррозионных поражений, и разрушения зачастую приобретают катастрофический характер.
Природа процесса, механизм коррозии, характер возникающих коррозионных поражений, термодинамические и кинетические аспекты происходящего взаимодействия металлического материала с расплавленным солевым электролитом процесса по-разному оцениваются различными исследователями, до сих пор не предложено приемлемого механизма протекания коррозионных процессов при высоких температурах в расплавленных солях. При этом чрезвычайно важны конструкционные характеристики – материалы, помимо прочности, также должны легко обрабатываться и подвергаться сварке для получения изделий достаточно сложной конфигурации и быть устойчивыми в широком температурном диапазоне и при радиационном воздействии.
Механизм коррозии в расплавленных солях принципиально иной в сравнении с процессами в водных и других низкотемпературных средах, при этом использование многих коррозионностойких сплавов ограничено [2]. В области ядерной энергетики чаще всего рассматривается коррозия никель-молибденовых сплавов. Существуют работы, посвященные исследованию коррозии сталей в расплавленных солях, много работ по исследованию сталей в водных средах с различными агрессивными добавками [3, 4]. Практически отсутствуют исследовательские работы по коррозии металлов в расплавах хлоридов с добавками ионов редкоземельных металлов. Есть ряд работ по исследованию коррозии с добавками редкоземельных металлов в водной среде [5, 6], в исследованиях показано, что ионы РЗМ при определенных условиях могут являться ингибиторами питтинговой коррозии.
Экспериментальные данные по коррозии металлических материалов в расплавленных солях содержат ограниченное количество коррозионных характеристик для анализа, к тому же стандарты экспериментальных условий недостаточны или отсутствуют [7].
Таким образом предлагаемое исследование не имеет аналогов, обладает фундаментальным характером и практической значимостью.
Целью работы является определение коррозионных характеристик процесса взаимодействия в системе металл–расплав солей хлоридов лития и калия, содержащий добавки имитаторов продуктов деления ОЯТ (трихлоридов f-элементов церия и неодима) или кислородсодержащих соединений и установление механизма коррозии металлических материалов на основе никеля (никель, никель–хром, никель–титан) в расплаве хлоридов лития и калия при температурах 500–700°C. Комплексное использование экспериментальных данных, результатов термодинамического моделирования возможных коррозионных процессов и квантово-механических расчетов позволяет установить механизм коррозионного взаимодействия металлических материалов с расплавом хлоридов щелочных металлов, содержащем добавки хлоридов f-элементов.
ЭКСПЕРИМЕНТАЛЬНАЯ ЧАСТЬ
Установка для проведения высокотемпературных испытаний
Основным фактором, оказывающим негативное влияние на достоверность получаемых данных при проведении высокотемпературных коррозионных экспериментов, является наличие различных примесей в газовой и в солевой фазе.
Для проведения высокотемпературных коррозионных испытаний была использована установка, представленная на рис. 1.
Рис. 1.
Схема установки для проведения высокотемпературных коррозионных испытаний. 1 – Терморегулятор Варта; 2 – прибор комбинированный Щ 300-1; 3 – манометр; 4 – исследуемый образец; 5 – баллон с аргоном; 6 – печь сопротивления; 7 – алундовый тигель с исследуемым хлоридным расплавом; 8 – кварцевая пробирка; 9 – силитовый нагреватель; 10, 11 – термопары; 12 – фторопластовая пробка с экранами; 13 – кварцевая трубка подачи газа в систему; 14 – цеолитная ловушка; 15 – печь очистки аргона на титановой губке, 16 – регулятор расхода газа РРГ-12.
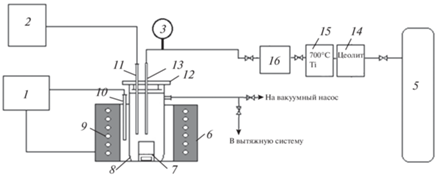
Подобная система позволяет исключить водо- и кислородосодержащие примеси в инертной газовой атмосфере, а также предотвратить их накопление в ячейке. Высокое качество очистки достигается за счет:
1) откачки газовой атмосферы вакуумным насосом и выдержке в течении часа при температуре 300°С. Из-за разрежения воздуха и температуры остаточные следы влаги в используемых солевых электролитах выделяются в газовое пространство ячейки (8) и удаляются из системы. После чего система трехкратно продувается инертным газом;
2) в систему непрерывно со скоростью 9 л/ч подается аргон, предотвращая возможное накопление в атмосфере над расплавом газообразных продуктов коррозии. Скорость подачи фиксируется с помощью регулятора расхода газа РРГ-12 (16) в совокупности с блоками управления БУИП-1M;
3) включения в систему дополнительной “ловушки”, заполненной цеолитом (14), который адсорбирует минорные водяные примеси (H2O) в подаваемом инертном газе;
4) Включения в систему очистки газа “ловушки” (15), заполненной титановой губкой, работающей при температуре 700°С, адсорбирующей кислородосодержащие примеси (O2) примеси в подаваемом инертном газе.
Подготовка исходных солей
В качестве исследуемого солевого электролита применялась эвтектика хлорида лития и калия (59.2 и 40.8 мол. % соответственно), содержащая в качестве добавки от 0 до 5% хлорида церия и оксида лития.
Хлорид церия и оксид лития, используемые в качестве добавок в расплав, имели чистоту более 99.9% (х.ч.) и хранились в перчаточном боксе для предотвращения абсорбирования кислородосодержащих примесей из атмосферы.
Исходный хлорид лития и калия марок ч.д.а. раздельно, просушивали в кварцевой ячейке в токе аргона при температуре 200°С. После чего индивидуальные соли были подвергнуты трехкратной зонной плавке в токе аргона со скоростью 1.5 см/ч. Для хлорида лития температура, используемая в зонной плавке, составляла 650°С, для хлорида калия – 850°С.
Полученные солевые слитки были перенесены в перчаточный бокс СПЕКС ГБ-02М, где осуществлялось отделение от хвостовой (примесной) части. Затем соли дробились и готовились навески по 25 г.
Непосредственно перед испытанием, уже загруженные солью алундовые тигли извлекались из бокса и незамедлительно размещались в рабочей кварцевой ячейке для проведения высокотемпературных коррозионных испытаний.
Подготовка образцов
В данной работе исследовалось коррозионное поведение образцов никеля (НП1) марки и сплавов на его основе, а именно никель-хромового (Х20Н80) и никель-титанового сплав (ТН-1К). В табл. 1 представлены составы исследуемых образцов согласно их торговой марке.
Таблица 1.
Состав исследуемых материалов
Исследуемый материал (марка) | Элемент, мас. % | ||||||
---|---|---|---|---|---|---|---|
Ni | Cr | Ti | Si | Mn | Fe | остальное | |
Никель (НП1) | 99.9 | – | – | <0.03 | – | <0.04 | <0.05 |
“Нихром” (Х20Н80) | 73–78 | 19–21 | <0.03 | 0.9–1.5 | <0.7 | <1.5 | <0.35 |
“Нитинол” (ТН-1К) | 50.5–53.5 | – | 42–47 | <0.15 | – | <4.5 | <0.6 |
Испытания образцов исследуемых материалов осуществляли в параллели по 3 образца, для большей достоверности получаемых данных. Предварительно материалы нарезали на образцы, равные по размерам, обрабатывались шлифовальной бумагой различной зернистости.
После этого образцы промывали в дистиллированной воде, обезжиривали спиртово-ацетоновой смесью и сушили в термошкафу. После стадии сушки образцы незамедлительно отправлялись в бокс на хранение для избегания формирования на поверхности оксидного слоя под действием окислительной атмосферы воздуха.
Также производили замер габаритных размеров для последующего расчета площади контакта материала с расплавленным солевым электролитом цифровым штангенциркулем, производилось многократное взвешивание образцов, для осуществления в дальнейшем гравиметрического анализа.
Исследуемые образцы были аттестованы на соответствие структуры и состава материалов заявленному согласно марке с помощью микрорентгеноспектрального и рентгенофазового методов.
По завершении испытаний, образцы отмывали при кипячении в дистиллированной воде, сушились и повторно взвешивались.
Приборы и методы анализа
Элементный анализ расплава выполнялся с использованием оптического эмиссионного спектрометра с индуктивно-связанной плазмой OPTIMA 4300 DV.
Поверхность образцов, а также их поперечный разрез исследовался при помощи сканирующего электронного микроскопа GEOL SM-5900 LV с возможностью энергодисперсионного рентгеновского анализа поверхности изучаемого образца. Данный растровый электронный микроскоп – система для микроанализа с безазотным энергодисперсионным детектором X-Act ADD + JSM-5900LV (Jeol, Япония), оснащен системой волнодисперсионного микроанализатора, устройством для подавления электромагнитных помех INCA Energy 250 и INCA Wave и шлюзовой камерой.
Растровые электронно-микроскопические (РЭМ) исследования и микрозондовый рентгеноспектральный анализ (МРСА) проводился на сканирующем электронном микроскопе TESCAN Mira3 LMU, оснащенном системой энергодисперсионного анализа характеристического рентгеновского излучения (ХРИ) x-Act 6 фирмы Oxford Instruments. Состояние поверхности образцов исследуется с использованием детекторов как вторичных (SE), так и отраженных (BSE) электронов.
Гравиметрическое взвешивание исследуемых образцов осуществляется на аналитических весах с точностью до пятого знака после запятой марки MSA 225P. Измерение размеров образцов осуществлялось с помощью цифрового штангенциркуля.
Результаты и обсуждение
Коррозионное поведение никеля, а также сплавов никель–титан и никель–хром было исследовано при температуре 500–700°С, в расплаве KCl–LiCl, содержащем добавки до 5 мас. % хлорида церия и оксида лития при коррозионной выдержке в течение 24 ч в инертной атмосфере аргона. Скоростей коррозии, рассчитанные по данным гравиметрического анализа представлены в табл. 2.
Таблица 2.
Скорости коррозии, рассчитанные по данным гравиметрического анализа образцов, выдержанных в течение 48 ч в исследуемых солевых расплавах
Образец | Расплав | Скорость коррозии, г/м2 · ч | ||
---|---|---|---|---|
температура, °С | ||||
500 | 600 | 700 | ||
NiTi | LiCl–KCl | 0.896 ± 0.045 | 1.182 ± 0.059 | 1.739 ± 0.087 |
LiCl–KCl + 1% СeCl3 | 0.500 ± 0.025 | – | – | |
LiCl–KCl + 5% СeCl3 | 0.024 ± 0.001 | 0.903 ± 0.045 | 2.146 ± 0.107 | |
LiCl–KCl + 1% Li2O | 0.955 ± 0.048 | – | – | |
LiCl–KCl + 5% Li2O | 1.333 ± 0.067 | 2.907 ± 0.145 | 6.150 ± 0.308 | |
NiCr | LiCl–KCl | 0.149 ± 0.007 | 0.429 ± 0.021 | 0.808 ± 0.040 |
LiCl–KCl + 1% СeCl3 | 0.110 ± 0.006 | – | – | |
LiCl–KCl + 5% СeCl3 | 0.025 ± 0.001 | 0.211 ± 0.011 | 0.444 ± 0.022 | |
LiCl–KCl + 1% Li2O | 0.122 ± 0.006 | – | – | |
LiCl–KCl + 5% Li2O | 0.176 ± 0.009 | 0.645 ± 0.032 | 1.262 ± 0.063 | |
Ni | LiCl–KCl | 0.064 ± 0.003 | 0.102 ± 0.005 | 0.164 ± 0.008 |
LiCl–KCl + 1% СeCl3 | 0.060 ± 0.003 | – | – | |
LiCl–KCl + 5% СeCl3 | 0.069 ± 0.003 | 0.080 ± 0.004 | 0.145 ± 0.007 | |
LiCl–KCl + 1% Li2O | 0.077 ± 0.004 | – | – | |
LiCl–KCl + 5% Li2O | 0.080 ± 0.004 | 0.106 ± 0.005 | 0.202 ± 0.010 |
Можно отметить, что скорость коррозии металлических материалов на основе никеля при температуре 500°С снижается при введении в расплав трихлорида церия и увеличивается при добавлении оксида лития. С ростом температуры данная тенденция становится менее выраженной. Также с ростом температуры скорость коррозии значительно возрастает для всех изучаемых материалов.
Металлический никель показал высокую коррозионную стойкость по сравнению с исследуемыми его сплавами. Следует отметить, что никель-титановый сплав подвергся наибольшей деградации, исходя из данных гравиметрического анализа.
По результатам данных атомно-абсорбционного анализа (элементного анализ) отвердевшего расплава после эксперимента, выполненного с помощью оптического эмиссионного спектрометра с индуктивно-связанной плазмой Perkin Elmer OPTIMA 4300 DV составлена табл. 3 скоростей по выходу компонентов в расплав.
Таблица 3.
Скорости коррозии и селективность выхода компонентов в расплав, рассчитанные по данным химического анализа
Исследуемый материал | Температура, °С | Солевой электролит | |||||
---|---|---|---|---|---|---|---|
500 | 700 | ||||||
скорость коррозии, г/м2 · ч | выход компонента мас. % | скорость коррозии, г/м2 ·ч | выход компонента мас. % | ||||
NiTi | 0.746 | Ni – 20.5 | Ti – 79.5 | 1.734 | Ni – 28.0 | Ti – 72.0 | LiCl–KCl |
0.334 | Ni – 28.1 | Ti – 71.9 | 2.246 | Ni – 30.2 | Ti – 69.8 | LiCl–KCl + + 5% СeCl3 | |
0.833 | Ni – 21.7 | Ti – 78.3 | 5.750 | Ni – 31.6 | Ti – 68.7 | LiCl–KCl + + 5% Li2O | |
NiCr | 0.249 | Ni – 28.1 | Сr – 71.9 | 0.828 | Ni – 30.6 | Сr – 69.4 | LiCl–KCl |
0.125 | Ni – 22.1 | Сr – 77.9 | 0.478 | Ni – 29.4 | Сr – 70.6 | LiCl–KCl + + 5% СeCl3 | |
0.286 | Ni – 29.0 | Сr – 71.0 | 1.662 | Ni – 29.9 | Сr – 77.1 | LiCl–KCl + + 5% Li2O | |
Ni | 0.066 | Ni – 100 | 0.161 | Ni – 100 | LiCl–KCl | ||
0.063 | 0.165 | LiCl–KCl + + 5% СeCl3 | |||||
0.078 | 0.212 | LiCl–KCl + + 5% Li2O |
Можно отметить, что скорости коррозии, полученные на основе расчета по данным атомно-абсорбционного анализа, удовлетворительно соответствуют аналогичным значениям скорости коррозии, полученным по данным гравиметрического анализа (табл. 1). Незначительная разность в значениях обуславливается наличием остатков солей на поверхности и/или в приповерхностном объеме образца.
По данным о селективности выхода компонентов, которые получены атомно-абсорбционным анализом, установлено, что для сплавов характерен выход в расплав электроотрицательного компонента. В результате высокотемпературной коррозионной выдержки никель-титанового сплава в электролите преимущественно растворяется титан, для никель-хромового сплава – хром.
На рис. 2–5 приведены данные SEM для образцов Ni, NiTi и NiCr после коррозионной выдержки, выполненные с помощью микроскопа TESCAN MIRA 3 LMU как с поверхности, так и со шлифа поперечного сечения металлического материала, провзаимодействовавшего с расплавленным солевым электролитом. В поперечном сечении представлено элементное картирование для анализа изменения морфологии приповерхностного слоя.
Рис. 2.
Морфология поверхностного слоя сплава NiTi после коррозионного испытания при температуре 500°С в течение 24 ч в расплаве: (а) LiCl–KCl; (б) LiCl–KCl + 5% СeCl3; (в) LiCl–KCl + 5% Li2O.
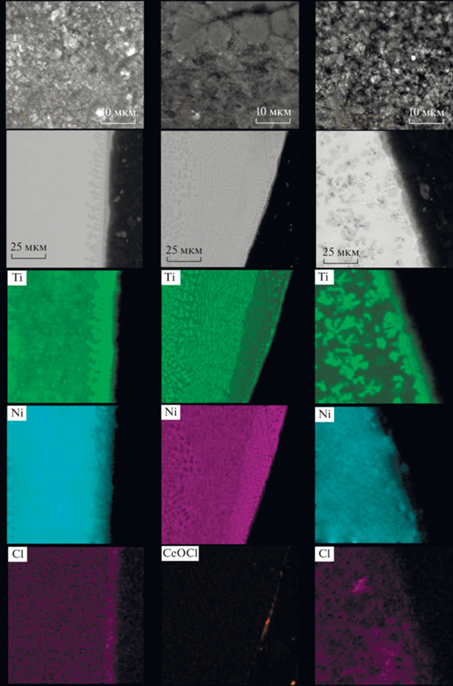
Рис. 3.
Морфология поверхностного слоя сплава NiСr после коррозионного испытания при температуре 500°С в течение 24 ч в расплаве: (а) LiCl–KCl; (б) LiCl–KCl + 5% СeCl3; (в) LiCl–KCl + 5% Li2O.
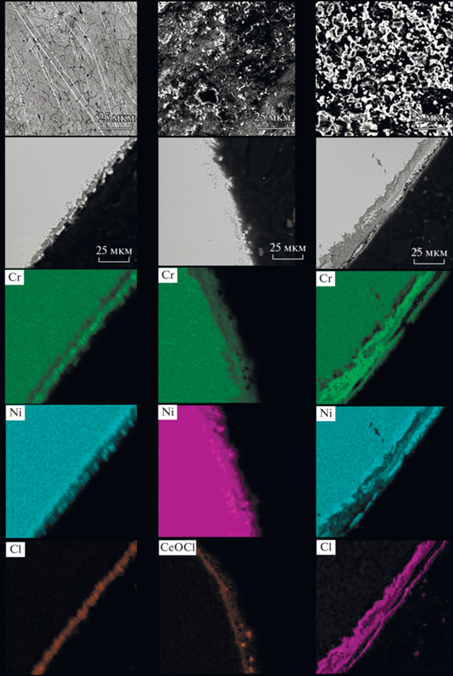
Рис. 5.
Морфология поверхностного слоя Ni после коррозионного испытания при температуре 500°С в течение 24 ч в расплаве: (а) LiCl–KCl; (б) LiCl–KCl + 5% СeCl3; (в) LiCl–KCl + 5% Li2O.
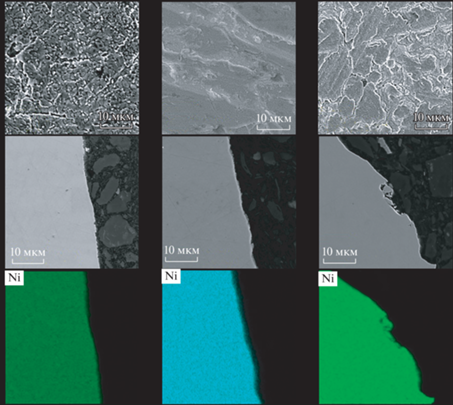
Из анализа морфологии поверхности (рис. 2) можно сделать вывод, что на никель-титановом сплаве происходит обеднение приповерхностного слоя по титану, с увеличением его концентрации у границы внешнего слоя. В свою очередь, перераспределение концентрации никеля вдоль фронта коррозионной атаки и в глубину образца не происходит.
При введении в расплав трихлорида церия, на поверхности образца формируется тонкая пленка стехиометрического состава оксихлорида церия, которая вызывает пассивирующий эффект за счет экранирования поверхности, тем самым снижая скорость коррозии. При введении в расплав оксида лития поверхность сплава по структуре подвергается более значительному коррозионному воздействию.
Анализ морфологии поверхности показал (рис. 3), что для никель-хромового сплава происходит увеличение концентрации хрома в поверхностном слое материала. Концентрация никеля у поверхности неравномерна, однако, подобное его распределение в составе поверхностного слоя связано с диффузионным перераспределением компонентов материала и последующим выделением из сплава хрома. Наблюдается склонность NiCr сплава к язвенной/подповерхностной коррозии.
При введении в расплав трихлорида церия, на поверхности образца формируется тонкая пленка стехиометрического состава оксихлорида церия, которая вызывает пассивирующий эффект за счет экранирования поверхности, тем самым снижая скорость коррозии, аналогично как для сплава NiTi. При введении в расплав оксида лития структура поверхности сплава претерпевает значительную деградацию, на поверхности наблюдается толстый слой продукта коррозии – оксида хрома (+3).
На рис. 4 представлен более подробный анализ формируемого данного оксихлоридного слоя на никель-титановом сплаве в ходе 24 часовой выдержке при температуре 500°С методом SEM.
На рис. 5, представляющем составы поверхности образца сплава Ni–Ti после коррозии в различных точка, наблюдается преимущественно массовое соотношение элементов приблизительно 79% Сe, 10% O и 18% Сl, что в перерасчете на мольное соотношения, учитывая молярные массы элементов дает стехиометрический Ce–O–Cl (32—36–32 мол. % соответственно). Кроме того, результаты данных рентгенофазового анализа подтверждают наличие сформированного оксихлоридного слоя.
Морфология образцов металлического никеля (рис. 5), выдержанного в эвтектическом расплаве хлоридов лития и калия, а также в расплаве, содержащем добавки хлорида церия и оксида лития, практически не претерпевает каких-либо изменений. На изображениях поверхности наблюдаются незначительные участки питтинговой коррозии, однако, в структуре поперечного сечения они отсутствуют. Т.е. введение в расплав добавок практически не влияет на деградацию никеля.
ВЫВОДЫ
1) Было исследовано коррозионное поведение никеля, а также сплавов на его основе (Ni–Cr и Ni–Ti) в солевом расплаве хлорида лития и калия, содержащем в качестве добавки от 0 до 5 мас. % оксида лития Li2O и трихлорида церия CeCl3 при температуре 500–700°С.
Установлено, что скорость коррозии увеличивается в следующем ряду: Ni < NiCr < < NiTi.
2) Основной причиной коррозии является наличие минорных кислородосодержащих примесей (О2) в газовой атмосфере над расплавом и/или в солевом электролите. Примеси вступают преимущественно в реакции с электроотрицательным компонентом сплава – Ti, Cr, с образованием их оксидов.
3) Введение в расплав трихлорида церия приводит к образованию на поверхности стехиометричного оксихлоридного слоя церия, что в свою очередь снижает скорость коррозии, за счет пассивации поверхности и экранирующего эффекта. При повышении температуры данный эффект наблюдается в значительно меньшей степени, что подтверждается термодинамическими расчетами.
4) Введение в расплав оксида лития с концентрацией 1 мас. % и более усиливает деградацию материала, за счет аниона О2–.
5) С ростом температуры скорость коррозии значительно увеличивается, а также практически нивелируется пассирующее влияние в системе хлорида церия.
Исследование выполнено при финансовой поддержке РФФИ в рамках научного проекта № 20-33-90082.
Список литературы
LeBlanc D. // Nucl. Eng. 2010. 240. № 6. P. 1644–1656. https://doi.org/10.1016/j.nucengdes.2009.12.033
Guo Sh., Zhang J., Wu W., Zhou W. // Progress in Materials Science. 2018. 97. P. 448–487. https://doi.org/10.1016/j.pmatsci.2018.05.003
Stephen S., Bartels D.M., Was G.S. // Journal of Nuclear Materials. 2017. 493. P. 40–52. https://doi.org/10.1016/j.jnucmat.2017.05.042
Xie Y., Zhang J. Chloride-induced stress corrosion cracking of used nuclear fuel welded stainless steel canisters: A review // Journal of Nuclear Materials. 2015. 466. P. 85–93.
Kim S.-T., Jeon S.-H., Lee I.-S., Park Y.-S. Effects of rare earth metals addition on the resistance to pitting corrosion of super duplex stainless steel // Corrosion Science. 2010. 52. № 6. P. 1897–1904.
Gou J., Wang Y., Li X., Zhou F. // Applied Surface Science. 2018. 431. P. 143–151. https://doi.org/10.1016/j.apsusc.2017.06.203
Raiman S.S., Lee S. // Journal of Nuclear Materials. 2018. 511. P. 523–535. https://doi.org/10.1016/j.jnucmat.2018.07.036
Sridharan K., Allen T.R. // Molten Salts Chemistry. 2013. P. 241–267. https://doi.org/10.1016/B978-0-12-398538-5.00012-3
Gomez-Vidal J.C., Tirawat R. // Sol. Energy Mater. Sol. Cells. 2016. 157. P. 234–244. https://doi.org/10.1016/j.solmat.2016.05.052
Ambrosek J. Molten chloride salts for heat transfer in nuclear systems. University of Wisconsin, 2011.
Feng X.K., Melendres C.A. Anodic corrosion and passivation behavior of some metals in molten LiCl–KCl containing oxide ions // J. Electrochem. Soc. 1982. 129. P. 1245–1249.
Vignarooban K., Pugazhendhi P., Tucker C., Gervasio D., Kannan A.M. Corrosion resistance of Hastelloys in molten metal-chloride heat-transfer fluids for concentrating solar power applications // Sol. Energy. 2014. 103. P. 62–69.
Vignarooban K., Xu X., Wang K., Molina E.E., Li P., Gervasio D., Kannan A.M. // Appl. Energy. 2015. 159. P. 206–213. https://doi.org/10.1016/j.apenergy.2015.08.131
Gomez-Vidal J.C.C., Fernandez A.G.G., Tirawat R., Turchi C., Huddleston W. // Sol. Energy Mater. Sol. Cells. 2017. 166. P. 222–233. https://doi.org/10.1016/j.solmat.2017.02.019
Johnson T.R., Teats F.G., Pierce R.D. A method for the purification of molten chloride salts. Argonne National Laboratory. Lemont, IL. ANL-7603, 1969.
Janz G.J. // Molten Salts Handb. 1967. P. 383–387. https://doi.org/10.1016/B978-0-12-395642-2.50032-0
Shaffer J.H. Preparation and handling of salt mixtures for the molten salt reactor experiment, ORNL-4616, 1971.
Edeleanu C.J., Gibson J.G., Meredith E. Effects of diffusion on corrosion of metals by fused salts // Journal of the iron- and steel institute. 1960. 196. № 1. P. 59–61.
Кочергин В.П. Защита металлов от коррозии в ионных расплавах и растворах электролитов: монография. Екатеринбург: УрГУ, 1991.
Смирнов М.В., Озеряная И.Н. Коррозия металлов в расплавленных солевых средах и защита от коррозии // Итоги науки и техники. Коррозия и защита от коррозии. 1987. 1. С. 142–143.
Улиг Г.Г., Реви Р.У. Коррозия и борьба с ней. Введение в коррозионную науку и технику. Л.: Химия, 1989.
Озеряная И.H. Коррозия металлов в расплавленных солях при термической обработке // Металловедение и термическая обработка металлов. 1985. № 3. С. 14–17.
Yamamura T., Mehmood M., Maekawa H., Sato Y. Electrochemical processing of rare-earth and rare metals by using molten salts // Chemistry for Sustainable Development. 2004. № 12. P. 105–111.
Пенягина O.П. Коррозионное поведение стали 12Х18Н10Т в хлоридных и карбонатных расплавах в условиях термоциклирования // Расплавы. 1994. № 3. С. 71–76.
Смирнов М.В., Володин В.П., Озеряная И.Н. Стационарный потенциал и коррозия металлов в расплавленных солях // Докл. АН СССР. Сер. 155. 1964. № 2. С. 418–421.
Смирнов М.В. Электродные потенциалы в расплавленных хлоридах: монография. М.: Наука, 1973.
Кочергин В.П. Растворение железа в расплавленных хлоридах щелочных и щелочноземельных металлов // Журнал прикладной химии. Сер. 29. 1956. № 4. С. 566–569.
Mohanty B.P. Role of chlorides in hot corrosion of a cast Fe–Cr–Ni alloy. Part II: Thermochemical model studies // Corrosion Science. 2004. 46. № 12. P. 2909–2924.
Devine T.M. Mechanism of intergranular corrosion and pitting corrosion of austenitic and duplex 308 stainless steel // J. Electrochem. Soc. 1979. 126. № 3. P. 374–385.
Озеряная И.Н., Смирнов М.В. Особенности коррозии металлов в расплавленных галогенидах и карбонатах // Высокотемпературная коррозия и методы защиты от нее. 1973. № 1. С. 76–83.
Дополнительные материалы отсутствуют.