Расплавы, 2022, № 5, стр. 469-476
Термодинамическое моделирование фьюмингования шлака медной плавки продуктами конверсии метана кислородом, водяным паром и углекислым газом
А. С. Вусихис a, *, Л. И. Леонтьев a, С. В. Сергеева a
a Институт металлургии УрО РАН
Екатеринбург, Россия
* E-mail: vas58@mail.ru
Поступила в редакцию 14.05.2022
После доработки 25.05.2022
Принята к публикации 16.06.2022
- EDN: MAGAPA
- DOI: 10.31857/S0235010622050103
Аннотация
В работе представлены результаты термодинамического моделирования фьюмингования шлака медной плавки в печи Ванюкова продуктами конверсии метана кислородом, водяным паром и углекислым газом в интервале температур 1473–1773 К. Для этого использована методика, позволяющая описать изменения в составах фаз исследуемых систем при их барботаже в зависимости от количества введенного газа-восстановителя, и отличающаяся цикличностью проведенных расчетов с выводом из состава рабочего тела образовавшихся газов и металлической фазы. В результате проведенных расчетов установлено, что, процесс взаимодействия газа с оксидами расплава протекает в два этапа независимо от его состава. На первом этапе происходит восстановление Fe3O4 до FeO, а ZnO до Zn. В связи с этим содержание в расплаве Fe3O4 и ZnO уменьшается, а FeO увеличивается. На втором этапе появляется металлическое железо, а содержание оксидов железа и цинка уменьшается. Показано значительное влияние температуры на фьюмингование. С ростом температуры от 1473 до 1773 К процесс значительно интенсифицируется, что сопровождается снижением количества газа-восстановителя необходимого для достижения близких значений степени извлечения цинка, в 4 раза. Состав газа слабо влияет на процесс. Показано, что наиболее эффективным восстановителем является газ полученный методом паровой конверсии метана, что обусловлено минимальными затратами на его получение. Полученные результаты позволяют прогнозировать показатели процесса фьюмингования продуктами конверсии метана и будут полезны для создания новых технологий.
ВВЕДЕНИЕ
Автогенные процессы широко используются в цветной металлургии для переработки сульфидных руд, к ним относятся: кислородно-факельная плавка, взвешенная плавка, плавка в жидкой ванне [1–6]. К недостаткам таких технологий можно отнести высокое содержание полезных компонентов, остающихся в шлаке [7–9]. Для их извлечения разработаны различные методы [10–16]. Большинство из них реализовано в процессе лабораторных исследований, а часть применяется в промышленных условиях. К таким методам относится фьюмингование. Процесс заключается в барботаже расплавленного шлака газом – восстановителем. В результате оксиды цинка, свинца и других летучих металлов восстанавливаются, и в виде пара переходят в газовую фазу. Процесс осуществляется в гарнисажных шахтных печах с выносными топками при температурах 1473–1573 К продуктами конверсии природного газа с коэффициентом расхода воздуха около 0.75 [17, 18]. В связи с этим вызывает интерес оценка влияния повышения температуры до 1773 К при фьюминговании расплава продуктами конверсии природного газа, полученными различными способами.
Одну из возможностей предварительного анализа предоставляет термодинамическое моделирование (ТДМ) изменения фазовых составов многокомпонентных и многофазных систем в процессе взаимодействия, широко используемое для совершенствования металлургических технологий [19–21]. Однако, предлагаемые методологии ТДМ предназначены для анализа равновесия в замкнутых системах, что не отвечает реальным процессам в пирометаллургических агрегатах. Авторами представленной работы разработана методика, позволяющая приблизить данные ТДМ к результатам, полученным в ходе барботажа многокомпонентных оксидных расплавов [22]. Особенности методики заключаются в том, что выполняют цикл последовательных расчетов с изменяющимся составом оксидного расплава, постоянным составом, и количеством восстановителя, выводом газа и металла из рабочего тела. В каждом цикле количество и состав равновесных оксидных и металлических фаз определяют для единичной порции газа постоянного состава, вводимой в рабочее тело, а содержание оксидов восстанавливаемых металлов в каждом последующем цикле принимают из предшествующих данных. Это позволяет моделировать процессы и качественно оценить полноту протекания реакций восстановления в пирометаллургических агрегатах барботажного типа.
В результате проведенных расчетов получают зависимости от общего количества введенного восстановителя таких величин, как составы отходящего газа, оксидного и металлического расплавов, соотношение этих продуктов, коэффициент перехода (извлечение) элементов в металлическое состояние. Ранее указанная методика была применена для моделирования различных процессов барботажного восстановления, в том числе совместного восстановления железа и цветных металлов (никеля, меди, свинца и цинка) из оксидных расплавов продуктами конверсии метана [23].
МЕТОДИКА МОДЕЛИРОВАНИЯ ПРОЦЕССА ВОССТАНОВЛЕНИЯ
В качестве конденсированной фазы рабочего тела выбрана оксидная система, близкая по составу шлакам медной плавки в печи Ванюкова и содержащая, мас. %: 36.41 FeO, 15.79 Fe3O4, 31.51 SiO2, 7.88 ZnO, 3.97 Al2O3, 3.27 CaO, 1.17 MgO. Расчеты проведены при давлении 0.1 МПа и температурах 1473–1773 К. В качестве газа-восстановителя взяты продукты конверсии метана, составы которых определены путем термодинамических расчетов (табл. 1) по уравнениям (1)−(3)
(1)
${\text{С}}{{{\text{Н}}}_{{\text{4}}}}{\text{ + 0}}{\text{.5}}{{{\text{О}}}_{2}} \to {\text{СО + 2}}{{{\text{Н}}}_{2}}\left( {\Delta H = - 35.6{\text{ }}{{{\text{кДж}}} \mathord{\left/ {\vphantom {{{\text{кДж}}} {{\text{моль}}}}} \right. \kern-0em} {{\text{моль}}}}} \right),$(2)
${\text{С}}{{{\text{Н}}}_{{\text{4}}}}{\text{ + }}{{{\text{Н}}}_{{\text{2}}}}{\text{O}} \to {\text{СО + 3}}{{{\text{Н}}}_{2}}\left( {\Delta H = + 206.4{\text{ }}{{{\text{кДж}}} \mathord{\left/ {\vphantom {{{\text{кДж}}} {{\text{моль}}}}} \right. \kern-0em} {{\text{моль}}}}} \right),$(3)
${\text{С}}{{{\text{Н}}}_{{\text{4}}}} + {\text{С}}{{{\text{O}}}_{2}} \to {\text{2СО + 2}}{{{\text{Н}}}_{2}}\left( {\Delta H = + 248.4{\text{ }}{{{\text{кДж}}} \mathord{\left/ {\vphantom {{{\text{кДж}}} {{\text{моль}}}}} \right. \kern-0em} {{\text{моль}}}}} \right).$Таблица 1.
Составы продуктов конверсии, взятых для термодинамических расчетов
Метод конверсии |
Т, К | Состав газа, % | ||||
---|---|---|---|---|---|---|
Н2 | СО | СН4 | Н2О | СО2 | ||
O2 | 1473 | 66.54 | 33.29 | 0.09 | 0.07 | 0.01 |
1573 | 66.59 | 33.31 | 0.05 | 0.04 | 0.01 | |
1673 | 66.63 | 33.31 | 0.03 | 0.03 | 0.00 | |
1773 | 66.64 | 33.33 | 0.02 | 0.02 | 0.00 | |
H2O | 1473 | 73.73 | 24.45 | 0.84 | 0.74 | 0.24 |
1573 | 74.32 | 24.71 | 0.46 | 0.42 | 0.10 | |
1673 | 74.59 | 24.83 | 0.30 | 0.26 | 0.03 | |
1773 | 74.75 | 24.90 | 0.18 | 0.17 | 0.01 | |
CO2 | 1473 | 49.87 | 49.98 | 0.07 | 0.05 | 0.02 |
1573 | 49.93 | 49.99 | 0.04 | 0.03 | 0.01 | |
1673 | 49.97 | 50.00 | 0.02 | 0.02 | 0.01 | |
1773 | 49.97 | 50.00 | 0.01 | 0.01 | 0.00 |
Единичный цикл расчетов соответствовал количеству конвертированного газа 21.87 дм3 на 1 кг оксидов. В расчетах принято, что, исходя из диаграммы состояния Fe–Zn, металлические продукты восстановления взаимно нерастворимы [24]. Для рассматриваемого интервала температур цинк находится в газообразном состоянии. Термодинамическое равновесие систем рассчитывалось при допущении идеальности растворов, а основной результат – это сравнительный анализ протекания процессов в зависимости от температуры и состава газа-восстановителя.
РЕЗУЛЬТАТЫ И ИХ ОБСУЖДЕНИЕ
Анализ результатов термодинамического моделирования барботажного восстановления (рис. 1) показал следующее. Процесс можно разделить на два этапа.
Рис. 1.
Зависимость изменения содержаний оксидов железа и цинка в расплаве (CFeO, ${{C}_{{{\text{F}}{{{\text{e}}}_{{\text{3}}}}{{{\text{O}}}_{{\text{4}}}}}}}$, CZnO) (a), степеней металлизации цинка и железа (φZn, φFe) (б) и цинка (CZn) в отходящем газе (в) от общего расхода газа-восстановителя при 1473–1773 К (метод конверсии: 1 – О2, 2 – Н2О, 3 – СО2).
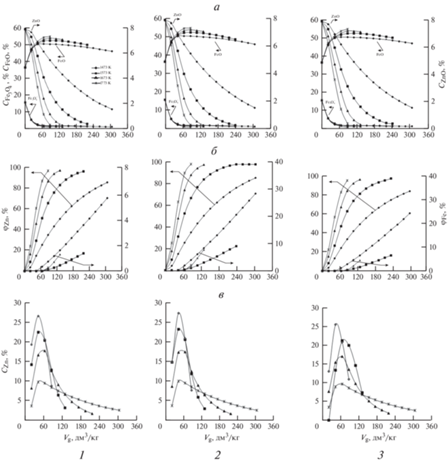
На первом этапе происходит восстановление Fe3+ до Fe2+ и Zn2+ до Znо. За счет этого при увеличении количества введенного газа-восстановителя содержание в оксидном расплаве Fe3O4 и ZnO снижается, а FeO – увеличивается до максимума. Одновременно, с ростом расхода газа количество цинка, восстановленного его единичной порцией увеличивается, что приводит к возрастанию его концентрации в отходящем газе до максимального значения. Дальнейшее уменьшение содержания оксида цинка в расплаве сопровождается снижением количества цинка, восстановленного единичной порцией газа и, соответственно, концентрации цинка в отходящем газе. Не зависимо от состава газа повышение температуры интенсифицирует восстановление, поэтому одному и тому же количеству введенного газа, соответствует более низкие содержания Fe3O4 и ZnO и более высокие – FeO.
На втором этапе продолжается снижение содержаний в оксидном расплаве Fe3O4 и ZnO, в системе появляется металлическое железо, что сопровождается уменьшением содержания FeO. Аналогичные результаты достигнуты в ходе экспериментальных исследований [25]. С ростом температуры процесс восстановления цинка интенсифицируется, поэтому для его извлечения в газовую фазу требуется меньшее количество восстановителя. При изменении температуры расплава от 1473 до 1573 К расход газа для восстановления цинка на 80% уменьшается в 2 раза, от 1573 до 1673 К в 1.5 раза, от 1673 до 1773 К в 1.2 раза, а от 1473 до 1773 К в 4 раза. Рост температуры замедляет металлизацию железа. При 1473 К металлическое железо появляется при наименьшем расходе газа, а доля железа, восстанавливаемая до металла к концу процесса, максимальна. Чем выше температура, тем больше расход газа, при котором появляется металлическое железо, и меньше степень металлизации к концу процесса. Метод конверсии слабо влияет на ход процесса, поэтому одинаковым количествам продуктов конверсии, принимающим участие в барботаже характерны близкие параметры процесса восстановления (табл. 2). Тем не менее, чем больше в газе водорода, тем выше степень восстановления цинка и железа.
Таблица 2.
Параметры, соответствующие заключительному циклу расчетов по восстановлению железа и цинка из оксидного расплава продуктами конверсии метана
Метод конверсии |
Т, К | Vg, дм3/кг | ${{V}_{{{\text{С}}{{{\text{Н}}}_{{\text{4}}}}}}}$, дм3/кг | φZn, % | φFe, % | СZnO мас. % | CFeO, мас. % | ${{C}_{{{\text{F}}{{{\text{e}}}_{{\text{3}}}}{{{\text{O}}}_{{\text{4}}}}}}}$ , мас. % |
---|---|---|---|---|---|---|---|---|
О2 | 1473 | 304 | 101 | 85.2 | 28 | 1.6 | 46 | 1.3 |
1573 | 217 | 72 | 95.8 | 17.1 | 0.4 | 49.9 | 1.5 | |
1673 | 130 | 43 | 96.7 | 6.5 | 0.3 | 53.0 | 1.4 | |
1773 | 87 | 29 | 96.3 | 1.4 | 0.3 | 54.7 | 0.9 | |
Н2О | 1473 | 304 | 76.1 | 84.9 | 28.2 | 1.5 | 46.0 | 1.3 |
1573 | 217 | 54.4 | 96.1 | 19.0 | 0.4 | 49.4 | 1.4 | |
1673 | 130 | 32.6 | 97.0 | 7.5 | 0.3 | 52.9 | 1.4 | |
1773 | 87 | 21.7 | 97.7 | 1.8 | 0.3 | 54.6 | 0.9 | |
СО2 | 1473 | 304 | 76.1 | 84.1 | 24.3 | 1.6 | 47.1 | 1.4 |
1573 | 217 | 54.4 | 95.4 | 14.0 | 0.4 | 50.7 | 1.6 | |
1673 | 130 | 32.6 | 96.2 | 4.6 | 0.3 | 53.4 | 1.4 | |
1773 | 87 | 21.7 | 95.3 | 0.6 | 0.4 | 54.9 | 0.9 |
Полученных данные показывают, что максимальная производительность процесса фьюмингования достигается при 1773 К.
Для определения наиболее эффективного способа конверсии, продукты которого используются в качестве газа-восстановителя необходимо учитывать следующие факты. С одной стороны, согласно уравнениям (1)–(3) кислородная конверсия сопровождается небольшим экзоэффектом, тогда как для осуществления паровой и углекислотной конверсии необходимы затраты тепла. С другой стороны, для получения единицы объема продуктов паровой и углекислотной конверсии необходимо на четверть меньше метана, чем кислородной. Излишек может быть использован для подогрева Н2О и СО2, что компенсирует затраты тепла. Кроме того, для получения чистого кислорода необходимы дополнительные затраты на строительство кислородной станции, а при реализации кислородной конверсии требуется принять меры предосторожности для предотвращения возможных взрывов. Определенные затраты необходимы и для получения чистого СО2. Отсюда можно сделать вывод о том, что для получения газа-восстановителя наиболее эффективен метод паровой конверсии.
ЗАКЛЮЧЕНИЕ
Методами термодинамического моделирования проведено описание процесса фьюмингования оксидного расплава, близкого по составу к шлакам медной плавки в печи Ванюкова, продуктами различных типов конверсии метана в интервале температур 1473–1773 К. Показано значительное влияние температуры на эффективность извлечения цинка и металлизацию железа. Состав газа-восстановителя, полученного различными методами слабо влияет на ход процесса, поэтому выбор метода конверсии связан с минимизацией затрат на его реализацию.
Работа выполнена по Государственному заданию ИМЕТ УрО РАН (№ госрегистрации темы: 122020100404-2).
Список литературы
Халемский А.М., Тарасов А.В., Казанцев А.Н., Кинев В.Д. Плавка в печи Ванюкова медно-цинкового сульфидного сырья. Екатеринбург: Кедр, 1993.
Мечев В.В., Быстров В.П., Тарасов А.В. и др. Автогенные процессы в цветной металлургии. М.: Металлургия, 1999.
Imris I., Sanchez M., Achurra G. Copper losses to slags obtained from the El Teniente process // VII International Conference on Molten Slags Fluxes and Salts, The South African Institute of Mining and Metallurgy. 2004. P. 177–182.
Комков А.А., Быстров В.П., Федоров А.Н. и др. Плавка медно-никелевой руды на штейн в печи Ванюкова // Цветные металлы. 2006. № 1. С. 7–11.
Hughes S., Reuter M.A., Baxter R., Kaye A. Ausmelt technology for lead and zinc processing // Lead and Zinc. 2008. P. 147–162.
Bakker M.L., Nikolic S., Burrows A.S., Alvear G.R. ISACONVERT – continuous converting of nickel/PGM mattes // J.S. Afr. Inst. Mining and Met. 2011. 111. № 10. P. 285–294.
Кайтмазов А.В., Пыхтин Б.С., Фомичев В.Б. и др. Вовлечение в переработку сырья техногенного происхождения // Цветные металлы. 2001. № 6. С. 41–42.
Vitkova M., Ettler V., Johan Z., Kribek B., Sebek O., Mihaljevic M. Primary and secondary phases in copper-cobalt smelting slags from the Copperbelt Province, Zambia // Mineralogical Magazine. 2010. 74. № 4. P. 581–600.
Starodub K., Kuminova Y., Dinsdale A., Cheverikin V., Filichkina V., Saynazarov A., Khvan A., Kondratiev A. Experimental investigation and modeling of copper smelting slags // Metallurgical and Materials Transactions B. 2016. 47. P. 2904–2918.
Мамонов С.В., Газалеева Г.И., Дресвянкина Т.П., Волкова С.В. Cовершенствование технологии переработки отвальных шлаков медеплавильного производства // Обогащение руд. 2018. № 1. С. 38–42.
Селиванов Е.Н., Беляев В.В., Гуляева Р.И., Копылов А.С., Сельменских Н.И. Фазовый состав продуктов и распределение металлов при флотации конвертерных шлаков Среднеуральского медеплавильного завода // Цветные металлы. 2008. № 12. С. 23–27.
Юсупходжаев А.А., Хасанов А.С., Худояров С.Р., Валиев Х.Р., Маткаримов С.Т. Переработка шлаков медного производства с использованием аппаратов идеального перемешивания // Горный вестник Узбекистана. 2017. 71. № 4. С. 67–72.
Topçu M.A., Rüşen A., Derin B. Minimizing of copper losses to converter slag by a boron compound addition // Journal of Materials Research and Technology. 2019. 8. № 6. P. 6244–6252.
Каряев В.И., Комков А.А., Кузнецов А.В., Плотников И.П. Извлечение меди и цинка из медеплавильных шлаков при восстановительно-сульфидирующей обработке // Вестник Магнитогорского государственного технического университета им. Г.И. Носова. 2020. 18. № 2. С. 4–12.
Alamova G.Kh., Khojiev S.T., Okhunova R.Kh. Current state of copper smelting slags and their processing: a review // Central Asian Journal of Literature, Philosophy and Culture. 2021. 2. № 2. P. 49–55.
Zhanga H., Bao L., Chen Y., Xuanb W., Yuan Y. Efficiency improvements of the CO-H2 mixed gas utilization related to the molten copper slag reducing modification // Process Safety and Environmental Protection. 2021. 146. № 2. P. 292–299.
Козырев В.В. Отгонка цинка из шлака при фьюминговании природным газом // Цветные металлы. 2009. № 2. С. 61–64.
Козырев В.В., Бессер А.Д., Парецкий В.М. К вопросу извлечения цинка из шлаков свинцовой плавки // Электрометаллургия. 2013. № 6. С. 31–35.
Ватолин Н.А., Моисеев Г.К., Трусов Б.Г. Термодинамическое моделирование в высокотемпературных неорганических системах. М.: Металлургия. 1994.
Sohn H.Y. Process Modeling in Non-Ferrous Metallurgy // In: Treatise on Process Metallurgy: Industrial Processes. Oxford: Elsevier Ltd. 2014. Ch. 2.4. P. 701–838.
Boronenkov V., Zinigrad M., Leontiev L, Pastukhov E, Shalimov M, Shanchurov S. Phase interaction in the metal–oxide melts–gas system // The Modeling of Structure, Properties and Processes, 2012.
Вусихис А.С., Леонтьев Л.И., Селиванов Е.Н., Ченцов В.П. Mоделирование процесса газового восстановления металлов из многокомпонентного оксидного расплава в барботируемом слое // Бутлеровские сообщения. 2018. 55. № 7. С. 58–63.
Вусихис А.С., Леонтьев Л.И., Селиванов Е.Н., Ченцов В.П. Моделирование совместного восстановления железа и цветных металлов (никеля, меди, свинца и цинка) из оксидных расплавов конвертированным метаном // Вестник Иркутского государственного технического университета. 2020. 5. № 24. С. 1113–1125.
Банных О.А., Будберг П.Б., Алисова С.П. Диаграммы состояния двойных и многокомпонентных систем на основе железа. М.: Металлургия, 1986.
Серегин П.С., Попов В.А., Цемехман Л.Ш. Новые методы переработки материалов, содержащих цинк, олово и свинец // Цветные металлы. 2010. № 10. С. 27–33.
Дополнительные материалы отсутствуют.