Акустический журнал, 2019, T. 65, № 3, стр. 372-381
Лазерно-ультразвуковое исследование остаточных напряжений в трубах из аустенитной стали
А. Н. Жаринов c, А. А. Карабутов a, b, c, Е. А. Миронова b, *, С. Н. Пичков d, Е. В. Саватеева a, В. А. Симонова a, Д. Н. Шишулин d, Е. Б. Черепецкая b
a ИПЛИТ РАН – филиал ФНИЦ “Кристаллография и фотоника” РАН
117342 Москва, ул. Бутлерова, 17А, Россия
b НИТУ “МИСиС”
119049 Москва, Ленинский проспект, 4, Россия
c МЛЦ МГУ имени М.В. Ломоносова
119991 Москва, Ленинские горы, 1, стр.62, Россия
d АО “ОКБМ Африкантов”
603074 Нижний Новгород, Бурнаковский проезд, 15, Россия
* E-mail: mea@optoacoustic.ru
Поступила в редакцию 27.12.2018
После доработки 27.12.2018
Принята к публикации 29.12.2018
Аннотация
Статья посвящена исследованию методом акустоупругости остаточных напряжений и связанных с ними структурных изменений в тонкостенных трубах из аустенитной стали. Пробный ультразвуковой пучок формируется за счет термоупругого эффекта при поглощении лазерного импульса в оптико-акустическом преобразователе. Использовалось нормальное и наклонное (с углом, близким к критическому) падение УЗ‑пучка на контролируемый объект. Построены карты распределения вариаций скорости УЗ по поверхности объекта и распределения неоднородностей структуры металла в его объеме. Даны оценки остаточных напряжений в образце при его нестационарном термическом нагружении. Показано соответствие распределения остаточных напряжений, неоднородностей структуры металла и распределения нагружающих термических источников. В работе обсуждается возможность оценки остаточного ресурса и определения зон зарождения макротрещин.
Проблема измерения остаточных напряжений возникает практически всегда при контроле поврежденности металла и оценке остаточного ресурса объекта критической инфраструктуры. Решение этой задачи может быть определяющим для принятия решения о продлении эксплуатации, что позволяет сэкономить значительные материальные средства и ресурсы, а также сократить время простоя. Очевидно, что приемлемое решение должно обеспечивать неразрушающий контроль без демонтажа конструкции. Из большого набора методов неразрушающего контроля остаточных напряжений (оптических, рентгеновских, электромагнитных, тепловых, акустических и пр. [1, 2]) в наибольшей мере этим условиям удовлетворяет ультразвуковой метод, основанный на эффекте акустоупругости.
Акустоупругий эффект (см., например, [3]) проявляется в зависимости скоростей упругих волн в среде от действующих или остаточных напряжений в ней [4]. Он подробно исследован и в различных вариантах использовался для контроля остаточных и действующих напряжений (см., например, [5, 6]). С практической точки зрения достаточно ограничиться линейной зависимостью скорости ультразвука V в деформированной среде от действующих в ней напряжений ${\sigma }$:
(1)
$\frac{{{{V}_{{x1}}} - {{V}_{0}}}}{{{{V}_{0}}}} = A{{\sigma }_{{11}}} + B\left( {{{\sigma }_{{22}}} + {{\sigma }_{{33}}}} \right),$Относительное изменение скорости продольной ультразвуковой волны, распространяющейся вдоль оси x1, определяется как компонентой напряжений в том же направлении, так и суммой напряжений вдоль осей x2 и x3, перпендикулярных оси x1. Соотношение вкладов этих составляющих близко к коэффициенту Пуассона среды [8], поэтому основное влияние на скорость продольной ультразвуковой волны оказывает компонента напряжений, ориентированная вдоль направления распространения волны.
В случае изотропного однородного твердого тела напряженные состояния не влияют на скорость сдвиговых волн (нелинейные модули упругости в этом случае обращаются в ноль [9]). Практически, однако, конструкционные материалы всегда анизотропны, а при наличии остаточных напряжений – еще и неоднородны. Поэтому использование сдвиговых волн для измерения напряженных состояний также возможно [10]. При этом относительные вариации скоростей сдвиговых волн в напряженных средах в несколько раз меньше, чем для продольных волн. Такие исследования проводились с использованием как пьезоэлектрических, так и электромагнитных преобразователей [5, 6].
Относительные вариации скоростей ультразвука под действием механических напряжений остаются малыми вплоть до порога пластичности металла: как правило, они не превышают 1–2%. Поэтому для определения действующих или остаточных напряжений измерения скоростей ультразвука должны осуществляться с неопределенностью выше 10–3, а учитывая неоднородность распределения напряжений, и с высоким (~ 1 мм) пространственным разрешением. Поэтому необходимо использование как излучателей, так и приемников ультразвуковых импульсов с максимально широкой полосой рабочих частот и минимальным временем установления сигнала. Этим требованиям удовлетворяет система контактной лазерно-ультразвуковой структуроскопии с лазерными термооптическими источниками зондирующих ультразвуковых импульсов и сверхширокополосной пьезорегистрацией сигналов [11].
МЕТОД ИССЛЕДОВАНИЯ
Метод лазерно-ультразвуковой структуроскопии основан на возбуждении акустических волн при поглощении лазерного излучения. Теоретическое описание этого процесса при различных условиях поглощения света (жесткая или свободная граница, объемное или поверхностное поглощение, конечная длительность лазерного импульса) подробно рассмотрены в [12]. Схема широкополосного лазерно-ультразвукового преобразователя ПЛУ-6П-02 (ООО “ЛИНКС 2000”, г. Москва) приведена на рис. 1а. Лазерный пучок 0 через оптически прозрачную призму 2 направляется на внутреннюю поверхность светопоглощающего слоя 1. Наружная поверхность оптико-акустического генератора 1 находится в акустическом контакте с объектом исследования 5 (используется та или иная контактная жидкость или гель). Прием акустического излучения производится с помощью демпфированного 4 пьезоприемника 3, расположенного на верхней поверхности призмы 2, обеспечивающего широкую полосу рабочих частот. Поглощение лазерного импульса приводит к быстрому нагреву светопоглощающего слоя 1, который, расширяясь, излучает акустические волны как в контролируемый объект 5, так и в призму 2. Рассеянные назад от неоднородностей структуры объекта волны распространяются обратно в сторону генератора, проходят через весь преобразователь и также регистрируются приемником 3. Сигнал с пьезоприемника оцифровывается скоростным прецизионным аналого-цифровым преобразователем, а затем передается в персональный компьютер для обработки и отображения в реальном времени.
Рис. 1.
(а) Схема лазерно-ультразвукового контроля: 0 – лазерный пучок, 1 – оптико-акустический генератор, 2 – оптико-акустическая призма, 3 – пьезоприемник, 4 – демпфер, 5 – исследуемый объект; (б) временная форма и спектр (на врезке) зондирующего акустического импульса.
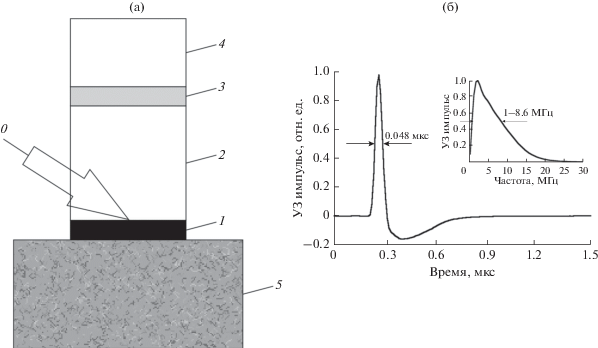
Зондирующий акустический сигнал (рис. 1б) имеет гладкую апериодическую форму, которая обеспечивает практическое отсутствие “мертвой зоны”. Короткая длительность импульса (порядка 50 нс по полувысоте) обеспечивает высокое пространственное разрешение, при этом спектр сигнала по уровню 0.5 от максимума занимает полосу 1–8.6 МГц. Частотная характеристика в высокочастотной области гладкая и обеспечивает возможность работы в полосе практически до 20–25 МГц. Малый диаметр зондирующего ультразвукового пучка (порядка 3 мм) обеспечивает высокую чувствительность при обнаружении дефектов малых размеров. Поскольку поглощение оптического излучения происходит в плоском тонком слое генератора 1, то возбуждаемые акустические волны имеют плоский фазовый фронт. Такие преобразователи использовались ранее для контроля напряженного состояния различных металлов [7, 13–15].
Как видно, описанная схема полностью соответствует традиционной схеме ультразвукового контроля в эхо-режиме. Отличие заключается только в лазерном излучателе ультразвуковых импульсов и сверхширокополосной пьезорегистрации акустических сигналов. Глубины залегания неоднородностей структуры определяются по временной задержке приходов сигналов от них и от поверхности раздела. Для получения двумерной картины распределения особенностей структуры оптико-акустический преобразователь перемещается вдоль поверхности исследуемой среды. Использование управляемых систем сканирования позволяет производить исследование в автоматизированном режиме.
Малая длительность и гладкая, хорошо повторяющаяся форма зондирующего импульса (рис. 1б) позволяют измерять время распространения ультразвука по контролируемому объекту с высокой точностью (δt ~ 1 нс) [13, 14] даже при малой толщине объекта (начиная с десятых долей миллиметра). Для определения с высокой точностью скорости ультразвука при этом необходимо также знать с высокой точностью толщину среды в пределах диаметра ультразвукового пучка (δh ~ ~ δtV0/2 ~ 1…2 мкм). Очевидно, что выполнение этого условия далеко не всегда возможно, что связано с неидеальным качеством и непараллельностью поверхностей объекта. Поэтому прецизионное измерение скорости ультразвука (и, соответственно, определение напряжений) в эхо-режиме возможно только при специальной подготовке поверхностей образца.
В силу вышесказанного целесообразно использование таких типов волн, измерение скоростей которых не требует отражения от тыльной поверхности. В первую очередь речь идет о рэлеевских волнах. Этот тип волн использовался для измерения дисперсии скорости ультразвука в микроэлектронике при полностью бесконтактном лазерном возбуждении и интерферометрической регистрации колебаний поверхности [15–17]. Прецизионное измерение скорости рэлеевских волн также требует тщательной подготовки поверхности ввиду сильного рассеяния этих волн на шероховатостях. Кроме того, проблематична адекватная трактовка результатов при измерениях на криволинейных поверхностях.
Другая возможность – использование головных (вытекающих) волн (в первую очередь продольных). Такое решение неоднократно обсуждалось в литературе (см., например, [18–20]). Использование традиционных пьезоэлектрических преобразователей, однако, во многих практически важных случаях не обеспечивает необходимой точности и локальности для эффективного контроля напряженных состояний в образце. В то же время малая длительность акустических импульсов и малый диаметр ультразвукового пучка делают перспективным использование термооптических источников для исследования напряженных состояний конструкционных материалов.
Схема измерения скорости ультразвука вытекающей волны приведена на рис. 2. Раздельно-совмещенный лазерно-ультразвуковой преобразователь 1 размещается на поверхности контролируемого объекта 2 с использованием контактной жидкости или геля [18]. Лазерно-ультразвуковой преобразователь 1 содержит две одинаковые наклонные акустические призмы 3 и 5, выходные поверхности которых прижимаются к поверхности исследуемой среды. На наклонной поверхности призмы 3 располагается термооптический излучатель 4, а на наклонной поверхности призмы 5 – широкополосный пьезоприемник 6.
Рис. 2.
(а) Схема измерения скорости ультразвука вытекающей волны и (б) характерный сигнал лазерно-ультразвукового преобразователя ПЛУ-6Н-02 от дюралюминия Д16Т.
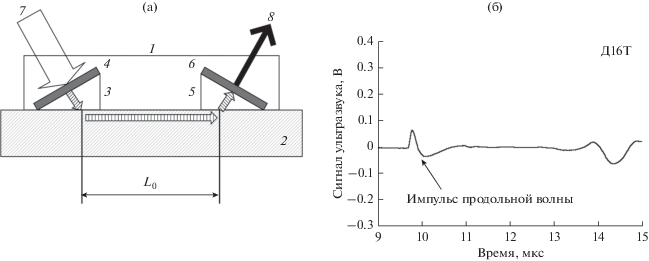
Для измерения скорости вытекающей продольной волны импульсный лазерный пучок 8 направляется на термооптический преобразователь 4, в котором полностью поглощается. Возбуждаемый при нестационарном тепловом расширении преобразователя (рис. 1б) импульсный акустический пучок (штрихованная стрелка на рис. 2а) через призму 3 направляется на поверхность исследуемой среды 2 под углом, близким к первому критическому. Преломленная продольная волна распространяется вдоль поверхности исследуемого объекта и, проходя по границе призмы 5, преломляется и попадает на широкополосный пьезоприемник 6. Электрический сигнал 8 пьезоприемника 6 после предусиления направляется на систему цифровой обработки.
Характерный вид сигнала раздельно-совмещенного преобразователя ПЛУ-6Н-02 (ООО “ЛИНКС 2000”, г. Москва) представлен на рис. 2б. Первый приходящий импульс соответствует сигналу продольной подповерхностной волны. Скорость этой волны определяется по измеренному времени прихода импульса δt, базой пробега L0 и временем пробега волны δt0 по наклонным призмам 3 и 5:
База и время пробега по призмам являются паспортными характеристиками преобразователя.
ОБЪЕКТЫ КОНТРОЛЯ
Объектами контроля являлись образцы трубопровода из высоколегированной аустенитной стали 12Х18Н10Т (AISI 321) с внешним диаметром в тестируемой области 59.5–59.8 мм, толщиной 4.8–5.0 мм и длиной 250 мм в количестве двух штук. Вначале исследовались образцы в состоянии поставки. Затем эти же образцы подвергались термическому нагружению, которое обеспечивалось впрыскиванием холодной струи в поток горячей воды, текущей внутри образца (рис. 3). После этого снова исследовалась внутренняя структура образцов (процедура аналогична использовавшейся в [21, 22]).
Рис. 3.
Схема термонагружения: 1 – образец трубопровода, 2 – патрубок для впрыска холодной воды, 3 – поток горячей воды, 4 – поток холодной воды.

Нерасчетный режим работы образца моделировался следующим образом (рис. 3). Через образец 1 пропускался поток 3 дистиллированной воды при температуре 300°C и давлении 14 МПа, расход составлял 3 м3/час. Нерасчетный нестационарный режим течения обеспечивался впрыском через патрубок 2 потока воды 4 при температуре 65°C. Таким образом формировался неоднородный турбулентный поток, приводящий к нестационарному неоднородному температурному полю в стенке образца 1. Время экспозиции составляло 20 часов. Уровень возникавших при этом температурных напряжений в образце локально мог превышать порог пластичности, что приводило к появлению остаточных напряжений. Исследование их распределения в образце и оценка величины напряжений являлись целью исследования.
ПРОЦЕДУРА ИЗМЕРЕНИЙ
Структуроскопия образцов производилась на автоматизированной установке, которая обеспечивала достаточную точность и воспроизводимость позиционирования датчика на поверхности образца и достижение необходимой стабильности измерений. На рис. 4а показано расположение широкополосного датчика модели ПЛУ-6П-02 на объекте контроля при тестировании. Вдоль оси образца расположена координата Y, поворот образца происходил по координате Х от 0° до 360° с шагом 1.8° (200 измерений). Запись акустических сигналов проводилась вдоль оси Y от 0 до 160 мм с шагом 2 мм, точность позиционирования составляет ~0.5 мм.
Рис. 4.
(а) Фотография образца трубопровода и расположение широкополосного оптико-акустического преобразователя при автоматическом контроле; (б) расположение преобразователя при измерении скорости вытекающей волны.
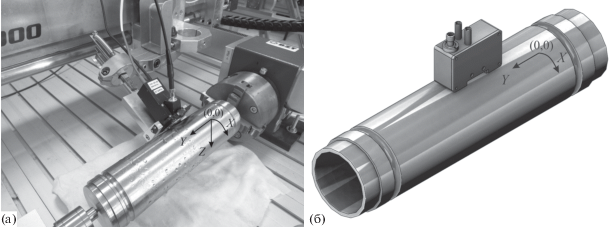
При лазерно-ультразвуковой структуроскопии образец фиксировался на поворотной оси в начальной точке О (0;0) (рис. 4а), где происходило считывание и запись акустического сигнала. Затем образец поворачивался на 1.8° вокруг оси Y (смещение на ~1.5 мм по оси X) и снова происходило считывание и запись акустического сигнала. Данная операция повторялась, пока не происходил полный оборот в 360° вокруг оси Y. Затем датчик автоматически перемещался вдоль оси Y в точку (0;2), где возобновлялось считывание по оси X (по окружности) и т.д. Ось Z направлена вглубь образца перпендикулярно к поверхности в каждой точке тестирования.
Исследованные образцы механически обрабатывались только с наружной стороны. Поэтому толщина стенки существенно (относительные вариации толщины составляли 2%) изменялась вдоль оси X, и измерение ее локального значения было затруднительно. В силу этого измерение скорости ультразвука по радиусу трубы (вдоль оси Z) с необходимой точностью ~0.1% было невозможно. Это не позволяло адекватно измерить распределение и величины остаточных напряжений в стенке трубы. Для использованных образцов (как и указывалось выше) исследования в эхо-режиме дают только картину пространственного распределения структурных неоднородностей среды. Для исследования распределения остаточных напряжений необходимо измерение скорости ультразвука с применением других схем.
В данной работе использовались вытекающие продольные волны (рис. 2). Схема расположения лазерно-ультразвукового преобразователя ПЛУ-6Н-02 на контролируемом образце приведена на рис. 4б. Измерялась скорость продольной волны вдоль оси трубы Y. База измерений L0 составляла ~30 мм, ширина ультразвукового пучка ~3 мм. Процедура измерений в целом соответствовала описанной выше, отличаясь только шагами по координатам. Шаг по углу составлял 18° (20 точек на оборот) и 15 мм вдоль оси трубы (Y). В каждой точке записывалось измеренное значение скорости продольной волны, распространяющейся вдоль оси трубы (Y), и формировалась карта распределения скорости по поверхности образца. Это позволяло определить распределение остаточных напряжений по поверхности образца в приповерхностном слое с толщиной ~0.5 мм (определяется длительностью акустического импульса).
ОБСУЖДЕНИЕ РЕЗУЛЬТАТОВ ЭКСПЕРИМЕНТОВ
Структуроскопия образцов дала идентичные результаты, поэтому далее будут приведены результаты тестирования образца № 1. На рис. 5 представлено изображение сечения образца № 1 плоскостью XZ, перпендикулярной оси образца (Y = 4 мм), в состоянии поставки (рис. 5а) и после тепловой нагрузки (рис. 5б). Горизонтальная ось X показывает развертку полного оборота по азимутальному углу вокруг оси образца (рис. 4). Соответственно, левая и правая стороны картины продолжают одна другую. Ось Z направлена от внешней поверхности в глубь цилиндра по радиусу.
Рис. 5.
Лазерно-ультразвуковое изображение структуры металла образца № 1 (а) до и (б) после тепловой нагрузки в сечении Y = 4 мм.
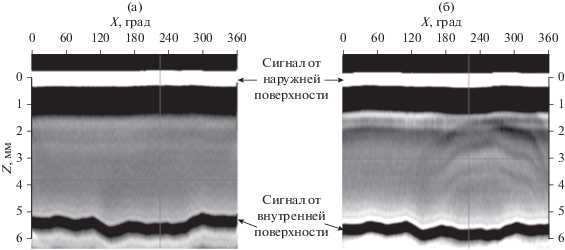
Амплитуда ультразвукового сигнала на рисунках изображена в градациях серого цвета. Лицевая поверхность образца отображается в виде белой полосы, т.к. зондирующий импульс отражается от границы среды (оптико-акустический преобразователь) с меньшим импедансом и среды с большим импедансом (сталь) в фазе с зондирующим импульсом. Внутренняя поверхность образца (так же, как и любые несплошности) отображается в виде темной полосы, т.к. сигнал отражается от границы среды с большим импедансом (сталь) и среды с меньшим импедансом (воздух) в противофазе. Видно, что внутренняя структура образца в состоянии поставки достаточно однородна. Относительный уровень акустических шумов, отраженных от структурных неоднородностей объекта, не превышает 3 × 10–3. По этому уровню глубина “мертвой зоны” составляет менее 1.5 мм и определяется в значительной мере рабочей полосой частот (1–12 МГц), установленной цифровым фильтром. При расширении рабочей полосы в высокочастотную область глубина “мертвой зоны” будет уменьшаться.
Внутренняя структура образца в состоянии поставки (рис. 5а) достаточно однородна. Относительно слабые неоднородности (скорее всего, зоны пониженной плотности) наблюдаются на глубинах ~2 мм в зоне Y = 20…76 мм в диапазоне углов X = 180°…300°. Эти неоднородности могут быть связаны как с пластическими изменениями при вытяжке трубы, так и при токарной обработке внешней поверхности – после этих операций нормализация образца не производилась. Извилистая линия внутренней поверхности подтверждает существенные вариации толщины стенки трубы по сечению XZ.
На рис. 5б представлено изображение сечения образца № 1 после термического нагружения; плоскость сечения XZ перпендикулярна оси образца и расположена там же (Y = 4 мм), что и сечение на рис. 5а. В отличие от структуры образца в состоянии поставки во внутренней структуре образца после термонагружения наблюдаются неоднородности, что проявляется визуально в появлении дугообразных полос на срезах. Эти неоднородности наиболее развиты в зоне Y = (4–30) мм на азимутах X = (150°–330°). В этой зоне тепловое влияние впрыска холодной воды наиболее сильное. Рассеяние на этих неоднородностях происходит в противофазе, поскольку дуга, отображающая границу зоны неоднородностей, имеет более темный оттенок, нежели ее окружение. Соответственно, эти неоднородности представляют собой разуплотнение среды (пористость, микроповрежденность, остаточные растягивающие напряжения и т.п.), возникшее за счет растягивающих напряжений при термической нагрузке образца.
Из сравнения структуры сечений до и после тепловой нагрузки (рис. 5а и 5б соответственно) видно, что линии внутренней поверхности трубы схожи. Однако изображение внутренней поверхности в образце после термического воздействия лежит ниже, чем до нагрузки. Это говорит о снижении скорости ультразвука Vz после теплового воздействия и появлении растягивающих остаточных напряжений в сечении Y = 4 мм. Этот эффект особенно заметен на азимутах X = = 150°…330°, соответствующих зоне впрыска холодной воды. Изображения сечений при Y = 4…30 мм в целом аналогичны представленным на рис. 5, отличаясь размерами и уровнем “серости” границ зоны разуплотнения.
Неравномерность толщины стенки образца не позволяет измерить скорость ультразвука Vz с точностью, необходимой для адекватной оценки остаточных напряжений. Поэтому те же образцы исследовались вытекающими волнами, использование которых не требует знания толщины образца (рис. 2). Соответствующие распределения по поверхности трубы скоростей продольных волн, распространяющихся вдоль оси трубопровода, представлены на рис. 6 в состоянии поставки (рис. 6а) и после тепловой нагрузки (рис. 6б).
Рис. 6.
Распределение относительной скорости продольной волны, распространяющейся вдоль оси образца № 1 по его поверхности (а) в состоянии поставки и (б) после тепловой нагрузки.
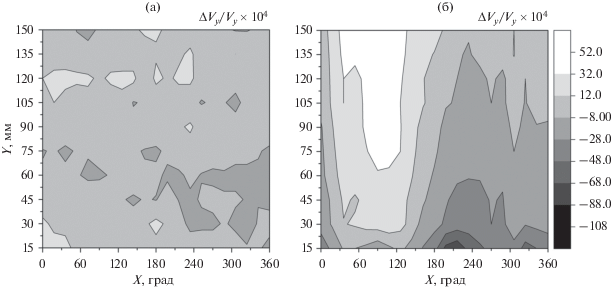
Относительная скорость, отображаемая на рис. 6, вычислялась как отклонение локального значения скорости Vy от ее значения 〈Vy〉, усредненного по всей контролируемой поверхности:
Образец в свободном состоянии считался механически разгруженным. На диаграммах вариация относительной скорости изображена в градациях серого цвета. Как видно, вариации скорости ультразвука по поверхности образца в состоянии поставки лежат в пределах –0.3…0.2%. Поэтому в исходном состоянии металл образца практически свободен от механических напряжений.
После теплового нагружения (рис. 6б) на углах 210°–270° у края образца появляется зона значительного снижения скорости ультразвука (относительная вариация достигает 1%), что соответствует появлению остаточных растягивающих напряжений в зоне впрыска хладагента. В свою очередь, на противоположном конце образца (углы 30°−150°) вариации скорости положительны, но в два раза меньше по максимальной величине.
В силу условий нагружения избыточное внутреннее давление и большие градиенты теплового потока в азимутальной плоскости по сравнению с их величиной в осевом направлении приводят к тому, что основным компонентом механических напряжений будут тангенциальные σxx. Поэтому для пересчета вариаций скорости ультразвука в величину механических напряжений (1) необходимо знать величину коэффициента B.
Измерение коэффициента акустоупругой связи B проводилось на традиционной нагрузочной машине на нормализованном образце стандартного размера аустенитной стали 12Х18Н10Т (рис. 7а) с одновременным измерением скорости ультразвука лазерно-ультразвуковым дефектоскопом УДЛ-2М (ООО “ЛИНКС 2000”, г. Москва). На рис. 7б показаны результаты измерений: поведение скорости ультразвука, распространяющегося по толщине образца (ось Y, кружки), и деформации длины образца εxx (квадраты) в зависимости от растягивающего напряжения σxx. Для данного типа стали порог текучести составляет 200–240 МПа в зависимости от способа обработки [ГОСТ 7350-77], что соответствует полученной зависимости (рис. 7б). До порога текучести сохраняется линейная зависимость скорости ультразвука от приложенного напряжения (прямая на рис. 7б). Наклон этой прямой дает коэффициент B акустоупругой связи для данного типа стали:
(2)
$B = --\left( {2.0{\text{ }} \pm {\text{ }}0.2} \right) \times {{10}^{{--5}}}\,\,{1 \mathord{\left/ {\vphantom {1 {{\text{М П а }}}}} \right. \kern-0em} {{\text{М П а }}}}.$Используя полученное значение коэффициента акустоупругой связи B, становится возможным перестроить полученные диаграммы вариации скорости ультразвука в распределения остаточных напряжений по поверхности образца. На рис. 8 приведены распределения остаточных напряжений для двух исследованных образцов. Как видно, качественный характер распределения остаточных напряжений сохраняется. Однако для образца № 2 их уровень выше, чем в образце № 1, на ~15%. Это связано, скорее всего, с некоторыми различиями в процессе теплового нагружения образцов.
Рис. 8.
Распределение остаточных напряжений (а) образца № 1 и (б) образца № 2 по их поверхности после тепловой нагрузки.
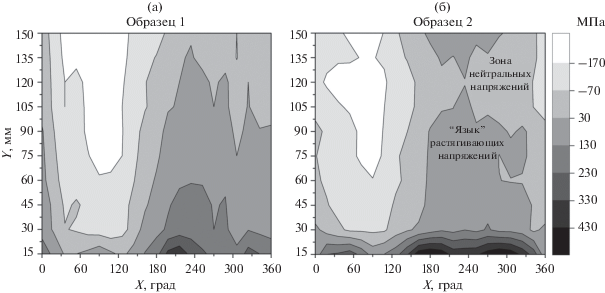
Зона значительных растягивающих напряжений (~400 МПа) во втором образце занимает значительно более широкую область по азимуту, нежели в первом. По-видимому, это также связано с некоторыми различиями в условиях теплового нагружения образцов. При этом продольные градиенты (вдоль оси образцов Y) во втором образце существенно больше, нежели в первом (размеры переходных зон средних уровней напряжений уже). Это может свидетельствовать о проявлении эффекта ползучести и развитии процесса старения материала.
Можно также отметить отличия в распределении напряжений в области 200°–300° по азимуту X и 105–135 мм по оси образца Y между первым и вторым образцом. Во втором образце появляется “язык” растягивающих напряжений (вытянутая зона на краю области сканирования Y = (135–150) мм), и сужается зона нейтральных напряжений, образуя как бы перемычку между зонами растяжения. Такое поведение можно трактовать как проявление микротрещиноватости в зоне (105–120 мм, 210°–300°). Предложенная трактовка, безусловно, требует подтверждения металлографическими исследованиями, что, однако, выходит за рамки настоящей статьи.
Исследованные в работе напряженные состояния были близки к одноосным. Поэтому удалось получить распределение напряжений достаточно простыми средствами. В общем случае многоосевого нагружения для его исследования с использованием эффекта акустоупругости требуются средства ультразвуковой томографии [23, 24]. Использование для этого лазерных термооптических источников ультразвука также представляется перспективным.
ВЫВОДЫ
Представленные исследования показали, что контактная лазерно-ультразвуковая структуроскопия может быть эффективно использована для количественной оценки напряженного состояния металла в конструкциях.
Для плоскопараллельных образцов измерение напряженных состояний возможно в эхо-режиме при нормальном вводе акустического пучка. При этом измеряются усредненные по толщине действующие или остаточные напряжения.
Использование головных волн позволяет исследовать распределения напряжений в поверхностных (толщиной ~1 мм) слоях и в образцах, для которых отражение от тыльной поверхности не дает информацию о скорости ультразвука с достаточной точностью.
Контактная лазерно-ультразвуковая структуроскопия позволяет рассчитывать на возможность выявления очагов концентрации напряжений, которые являются зародышами трещинообразования и формирования макротрещин.
Авторы благодарны АО “ОКБМ Африкантов” за предоставленные образцы. Исследования проводились в МЛЦ МГУ имени М.В. Ломоносова при поддержке НИТУ “МИСиС” с использованием оборудования, предоставленного ИПЛИТ РАН.
Список литературы
Hauk V. Structural and residual stress analysis by nondestructive methods. Amsterdam: Elsevier, 1997. 640 p.
Practical Residual Stress Measurement Methods. Ed. by Schajer G.S. New York: John Wiley & Sons, 2013. 320 p.
Гузь А.Н., Махорт Ф.Г., Гуща О.И., Лебедев В.К. Основы ультразвукового неразрушающего метода определения напряжений в твердых телах. Киев: Наукова Думка, 1974. 106 с.
Пуро А.Э. Акустическая томография поверхностных напряжений // Акуст. журн. 1996. Т. 42. № 1. С. 112–115.
Никитина Н.Е. Акустоупругость. Опыт практического применения. Нижний Новгород: ТАЛАМ, 2005. 208 с.
Углов А.Л., Ерофеев В.И., Смирнов А.Н. Акустический контроль оборудования при производстве и эксплуатации. Москва: Наука, 2009. 280 с.
Карабутов А.А., Кошкин В.В., Подольский А.С., Филатов А.А., Хижняк С.А. Исследование акустоупругого эффекта в металлах лазерно-ультразвуковым методом // Контроль. Диагностика. 2008. Т. 12. С. 22–27.
Hughes D.S., Kelly J.L. Second-order elastic deformation of solids // Phys. Rev. 1953. V. 92. № 5. P. 1145–1149.
Физическая акустика. Под ред. Мэзона. Т. 2Б. Свойства полимеров и нелинейная акустика. Москва: Мир, 1966.
ГОСТ Р 56664-2015 Контроль неразрушающий. Определение напряженного состояния материала изделий машиностроения методами акустоупругости. Общие требования. М.: Стандартинформ, 2016.
Карабутов А.А. Лазерно-ультразвуковой дефектоскоп. Патент РФ №2381496 от 29.05.2008.
Гусев В.Э., Карабутов А.А. Лазерная оптоакустика. Москва: Наука, 1991. 304 с.
Ивочкин А.Ю., Карабутов А.А., Лямшев М.Л., Пеливанов И.М., Рохатги У., Субудхи М. Измерение распределения скорости продольных акустических волн в сварных соединениях лазерным оптико-акустическим методом // Акуст. журн. 2007. Т. 53. С. 540–547.
Karabutov A., Devichensky A., Ivochkin A., Lyamshev M., Pelivanov I., Ruhadgi U., Solomatin V., Subudhi M. Laser ultrasonic diagnostics of residual stress // Ultrasonics. 2008. V. 48. P. 631–635.
Коробов А.И., Изосимова М.Ю., Одина Н.И. Диагностика металлических пластин с остаточными напряжениями и дефектами методами нелинейной лазерной сканирующей виброметрии // Акуст. журн. 2015. Т. 61. С. 317–324.
Lomonosov A.M., Mayer A.P., Hess P. Laser-based surface acoustic waves in material science // Exp. Methods Phys. Sci. 2001. V. 39. P. 65–134.
Девиченский А.Ю., Ломоносов А.М., Жаринов С.Е., Михалевич В.Г., Лямшев М.Л., Иванова Т.О., Меркулова Н.С. Диагностика остаточных напряжений в металлах с помощью широкополосных поверхностных акустических импульсов // Акуст. журн. 2009. Т. 55. С. 39–46.
Карабутов А.А., Шипша В.Г., Карабутов А.А. (мл.), Жаринов А.Н., Кудинов И.А. Лазерный ультразвуковой дефектоскоп. Патент РФ № 2544257. 2015.
Karabutov A.A., Podymova N.B., Simonova V.A. Use of acoustoelasticity effect with application of laser sources of the ultrasound for control of the stress state of railbars of the continuous welded rails // Int. J. App. Eng. Res. 2015. V. 10 (20). P. 41121–41128.
Карабутов А.А., Подымова Н.Б., Черепецкая Е.Б. Определение одноосных напряжений в стальных конструкциях лазерно-ультразвуковым методом // Прикладная механика и техническая физика. 2017. Т. 58. № 3. С. 146–155.
Углов А.Л., Хлыбов А.А., Пичков С.Н., Шишулин Д.Н. Акустический метод оценки поврежденности аустенитной стали при термопульсациях // Дефектоскопия. 2016. № 2. С. 3–10.
Коробов А.И., Ширгина Н.В., Кокшайский А.И., Прохоров В.М. Влияние статической реверсивной нагрузки на механические и упругие свойства поликристаллического сплава алюминия АMГ6 // Акуст. журн. 2018. Т. 64. № 4. С. 424–431.
Бычков А.С., Черепецкая Е.Б., Карабутов А.А., Макаров В.А. Улучшение пространственного разрешения изображения в оптоакустической томографии с помощью конфокальной антенны // Акуст. журн. 2018. Т. 64. № 1. С. 71–77.
Зарубин В.П., Бычков А.С., Карабутов А.А., Симонова В.А., Кудинов И.А., Черепецкая Е.Б. Профилометрия твердых тел с помощью лазерной ультразвуковой томографии в реальном масштабе времени // Вестник Московского университета. Серия 3: Физика, астрономия. Москва: Изд-во Моск. ун-та, 2018. № 1. С. 76–83.
Дополнительные материалы отсутствуют.
Инструменты
Акустический журнал