Доклады Российской академии наук. Химия, науки о материалах , 2022, T. 502, № 1, стр. 41-49
Исследование структуры, механических и антибактериальных свойств коррозионностойкой стали, легированной серебром и титаном
М. А. Каплан 1, *, А. Ю. Иванников 1, С. В. Конушкин 1, Е. О. Насакина 1, 2, А. С. Баикин 1, Б. Б. Картабаева 2, А. Д. Горбенко 1, 2, 3, член-корреспондент РАН А. Г. Колмаков 1, М. А. Севостьянов 1, 2
1 Институт металлургии и материаловедения
им. А.А. Байкова Российской академии наук (ИМЕТ РАН)
119334 Москва, Россия
2 Всероссийский научно-исследовательский институт фитопатологии (ФГБНУ ВНИИФ)
143050 Московская область, Большие Вяземы, Россия
3 Московский государственный технический университет имени Н.Э. Баумана
(Национальный исследовательский университет)
105005 Москва, Россия
* E-mail: mishakaplan@yandex.ru
Поступила в редакцию 05.09.2021
После доработки 22.01.2022
Принята к публикации 25.01.2022
- EDN: IMUMOJ
- DOI: 10.31857/S268695352201006X
Аннотация
Выплавлена новая медицинская антибактериальная коррозионностойкая сталь, легированная серебром и титаном. Подобран режим гомогенизирующего отжига для выравнивания структуры и образования равноосных зерен. Изучены механические свойства, микроструктура и фазовый состав. Рентгенофазовый анализ показал, что сталь после прокатки без легирующих элементов имеет аустенитную структуру. Легирование привело к появлению в структуре стали небольшого количества феррита. Спектральный анализ показал равномерное распределение серебра по всему объему сплава. Установлено, что образец стали, содержащий серебро и титан, обладает антибактериальным эффектом относительно штамма бактерий Pseudomonas marginalis.
ВВЕДЕНИЕ
На сегодняшний день среди материалов коррозионностойкие стали занимают одно из главных мест в мире. Состав стали многократно модифицируется и усовершенствуется, приобретая все новые и улучшенные свойства. Одной из самых популярных и применяемых марок среди коррозионностойких сталей является аустенитная сталь 316L. Она обладает высокой коррозионной стойкостью, механической прочностью и пластичностью, которые могут гарантировать длительную эксплуатацию изделий. Коррозионностойкая сталь 316L применяется во многих отраслях промышленности, например, в медицинской, пищевой, сельскохозяйственной, нефтехимической, горнодобывающей, автомобильной, аэрокосмической. Область применения коррозионностойкой стали 316L постоянно расширяется в новых отраслях экономики, таких как биотехнологии и другие [1–5].
За счет своих высоких эксплуатационных свойств коррозионностойкая аустенитная сталь давно применяется для изготовления различных медицинских изделий, таких как ортопедические протезы, зубные имплантаты, сердечно-сосудистые стенты/клапаны и т.д. [6]. Однако биологическая окружающая среда в человеческом теле очень агрессивна для металлов и может привести к адсорбции протеина, образованию биопленки (прикрепление микроорганизмов/бактерий к поверхности материала), коррозии и стать источником бактериального заражения [7].
Для повышения биохимической совместимости коррозионностойкой стали проводят специальное легирование, наносят покрытие, создают композиционные материалы и многое другое. Исследования показали, что легирование серебром коррозионностойких сталей может придать им антибактериальные свойства без необходимости модификации поверхности [8, 9].
В данной работе была получена коррозионностойкая сталь, легированная 0.2 мас. % Ag и 0.5 мас. % Ti, и исследованы ее механические и антибактериальные свойства.
МЕТОДЫ ИССЛЕДОВАНИЯ
Получены 2 образца коррозионностойкой стали. Образец № 1 (содержание углерода менее 0.3%, хрома 17%, никеля 10%, марганца 2%, молибдена 2%, кремния менее 0.5%, фосфора менее 0.05%, серы менее 0.01%, азота менее 0.08%) по составу аналогичен медицинской стали марки 316L. Образец № 2 дополнительно к вышеописанному составу содержал серебро (0.2%) и титан (0.5%) (табл. 1).
Таблица 1.
Содержание легирующих элементов в образцах сталей
Образец | Содержание легирующих элементов, % | ||||||||
---|---|---|---|---|---|---|---|---|---|
C | Cr | Ni | Ag | Si | Mn | Mo | Si | Ti | |
№ 1 | 0.023 | 17 | 10 | 0 | 0.5 | 1.5 | 2 | 0.5 | 0 |
№ 2 | 0.023 | 17 | 10 | 0.2 | 0.5 | 1.5 | 2 | 0.5 | 0.5 |
Образцы сталей получали следующим образом: плавку навесок компонентов стали проводили в аргонодуговой печи с нерасходуемым вольфрамовым электродом LK200DI фирмы Leybold-Heraeus (Германия). Навески помещали в медный водоохлаждаемый кристаллизатор, после чего рабочую камеру герметично закрывали и вакуумировали до давления 1 × 10–2 мм. рт. ст. После этого в камеру закачивали аргон до давления 0.4 атм.
В результате первого переплава получали слиток массой 45–50 г в форме двояковыпуклой линзы: диаметр 30–35 мм, высота 10–15 мм (рис. 1а). Последующие 2 переплава были направлены на получение равномерного химического состава по всему объему слитка. Длительность каждой плавки одного слитка 1–1.5 мин. Перед плавкой слитка расплавлялся геттер. В качестве геттера использовался слиток йодидного титана массой 15–20 г.
Рис. 1.
Внешний вид: (а) слитков после плавки навесок компонентов стали (масса 45–50 г, диаметр 30–35 см, высота 10–15 см); (б) слитка массой 180–200 г.
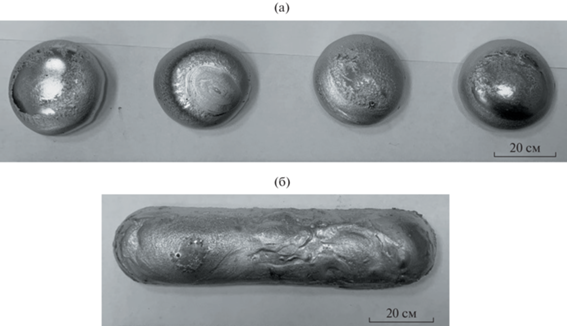
Далее в тех же условиях, в которых были получены слитки массой 45-50 г, сплавляли эти слитки в один массой 180–200 г за 2 переплава. Конечный слиток имел длину 90–100 мм, ширину 20–25 мм, высоту 10–15 мм (рис. 1б).
Для гомогенизирующего отжига слитков использовалась вакуумная печь ЭСКВЭ-1,7.2,5/ 21 ШМ13. Гомогенизацию проводили в вакууме 2 × 10–5 мм рт. ст. при температурах 900–1050°С в течение 9 ч.
Первичную деформацию (прокатку) литых заготовок толщиной 10–15 мм, диаметром 30–35 мм проводили методом горячей прокатки на двухвалковом стане ДУО-300 с частными абсолютными обжатиями за проход: 2 мм до толщины заготовки 4 мм (13–20% за проход), затем 1.0 мм до толщины заготовки 2.0 мм (6–10% за проход), далее 0.5 мм до конечной толщины заготовки 1–1.2 мм (3–5% за проход). Внешний вид получаемых пластин представлен на рис. 2. Нагрев заготовок перед каждой деформацией осуществляли в муфельной печи KYLS 20.18.40/10 фирмы HANS BEIMLER в течение 20–25 мин до температуры 1100°С перед первой прокаткой и в течение 5 мин при промежуточном нагреве. После нагрева заготовка прокатывалась холодными валками, что способствовало резкому охлаждению.
Исследование прочности при растяжении проводили на универсальной испытательной машине INSTRON 3382 со скоростью растяжения 1 мм мин–1. Плоские образцы с головками изготавливали с помощью электроэрозионной резки вдоль и поперек пластины (рис. 3). Такая форма необходима для минимизации влияния захватов на результаты исследования образцов.
Для исследования микротвердости методом Виккерса использовали микротвердомер 402-МVD фирмы Instron Wolpert Wilson Instruments. Нагрузка составляла 100 г при выдержке 10 c.
Структуру образцов слитков после выплавки и пластин после пластической деформации изучали при помощи оптического и сканирующего электронного микроскопов. Подготовку образцов проводили следующим образом. Образцы запрессовывали на пневмогидравлическом прессе IPA 40 при температуре 170°С и выдерживали 20 мин при давлении 4 атм. Затем шлифовали на установке Buehler Phoenix 4000 последовательно на шлифовальных кругах P120 (3 мин), Р320 (5 мин), P600 (5 мин), на алмазном диске тонкого шлифования Aka-Alegran-3 c алмазной суспензией зернистостью 6 мкм (5 мин). Последующую полировку проводили с помощью полировального вискозного круга (Aka-Napal) с применением алмазной суспензии (размер частиц 3 и 1 мкм) на протяжении 5 мин. При изготовлении шлифов применялась электропроводящая смола.
Травление поверхности образцов проводили смесью кислот для высоколегированных сталей, состоящей из 20% азотной кислоты, 10% серной кислоты, 5% плавиковой кислоты и 65% воды. Длительность травления составляла от 10 до 20 мин. После травления шлифы промывали дистиллированной водой и этиловым спиртом.
Световая оптическая микроскопия проведена на микроскопе Альтами МЕТ 5С с использованием видеокамеры высокого разрешения (14 мегапикселей), встроенной в прибор, и специального ПО Altami Studio.
Исследование микроструктуры и картирование (определение распределения концентраций химических элементов) проводили на сканирующем электронном микроскопе JEOL JSM-IT500 с приставкой энергодисперсионного микроанализа INCA ENERGY. Во время исследования произведен анализ изображений поверхности образца с высоким пространственным разрешением, полученным в режиме вторичных электронов.
Рентгеновские дифрактограммы получены на приборе ARL X`TRA в излучении CuKα в геометрии параллельного пучка. Параметр кристаллической решетки уточняли экстраполяцией на θ = = 90° по методу Нельсона–Райли в программе “Origin-2017”, величину микродеформации кристаллической решетки основной фазы определяли по методу Вильямсона–Холла в программе “HighScore Plus” (PanAnalytical). Количественное содержание кристаллических фаз оценивали по методу корундовых чисел.
Для определения антибактериальной активности образцов стали использовали трехсуточную бактерию рода Pseudomonas. Выросшие в пробирке колонии бактерии переносили в пробирку со стерильной дистиллированной водой для создания бактериальной суспензии. Затем на поверхность посева помещали образцы сталей. Оценивали антибактериальную активность сталей на посев по феномену задержки роста бактерий вокруг пластин.
РЕЗУЛЬТАТЫ
Для определения оптимальных условий, при которых происходит выравнивание структуры и образование равноосных зерен в образцах слитков, были изучены микроснимки шлифов после выплавки и отжига в течение 9 ч при температурах в интервале от 900 до 1050°С (рис. 4а–д).
Рис. 4.
Микроструктура слитков образцов № 1 и № 2 после выплавки (а); после выплавки и последующего отжига при 900°С (б), 950°С (в), 1000°С (г), 1050°С (д).
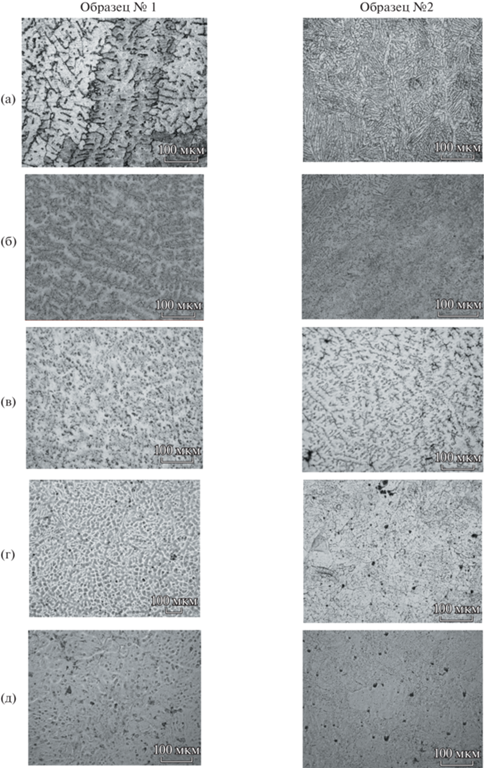
В слитках после выплавки наблюдается преобладание дендритной структуры. После гомогенизирующих отжигов при температурах 900°С, 950°С дендритная структура сохранялась. Гомогенизирующий отжиг при температуре 1000°С приводил к частичной рекристаллизации сплава № 2, в сплаве № 1 сохранялась дендритная структура. Полная рекристаллизация исследуемых сплавов наступала при гомогенизирующем отжиге при температуре 1050°С. Такой отжиг приводил к выравниванию структуры и образованию равноосных зерен размером ~50 мкм. Дальнейшее повышение температуры нецелесообразно из-за увеличения размеров зерен.
Исследование микроструктуры сплавов на световом оптическом и сканирующем микроскопах показало, что пластины обладают зеренной структурой без текстуры (рис. 5а,б), что может свидетельствовать о том, что рекристаллизация происходит после выхода пластины из валков.
Рис. 5.
Снимки микроструктуры пластин сплавов № 1 и № 2, полученных на оптическом (а) и сканирующем электронном (б) микроскопах.
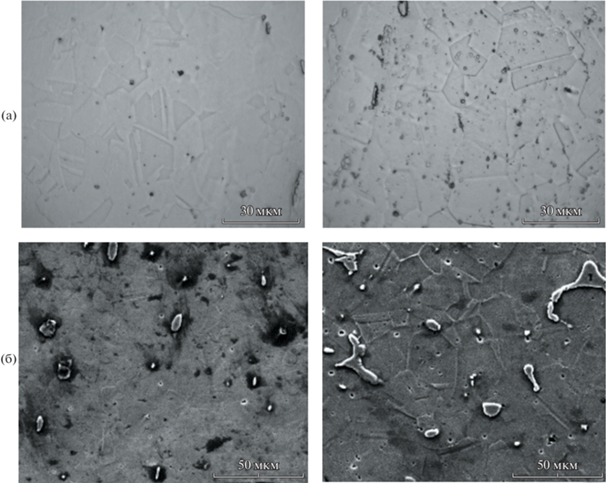
Равномерность распределения Ag и Ti в сплаве № 2 устанавливали на основании спектрального анализа (картирование) (рис. 6а–к).
Рис. 6.
Микроструктура поверхности образца № 2 (а) и распределение элементов по площади прокатанной пластины (б–к).
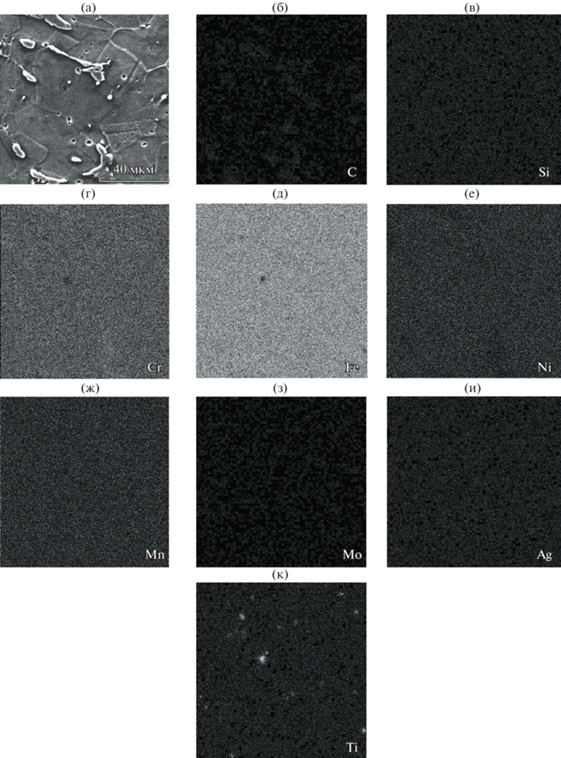
Картирование показало равномерное распределение серебра, что должно способствовать лучшему проявлению антибактериальных свойств сплава и может повысить стойкость к питинговой и межкристаллитной коррозии.
Рентгеновское исследование фазового состава показало, что на дифрактограммах образца № 1 наблюдаются только линии аустенита (γ-Fe). Легирование коррозионностойкой стали 0.2% Ag и 0.5% Ti привело к появлению небольшого количества феррита (α-Fe) (сплав № 2) (табл. 2, рис. 7).
Таблица 2.
Фазовый состав и периоды кристаллической решетки фаз горячекатаных пластин образцов № 1и № 2
Образец | Фазовый состав | Объемная доля, % | Весовая доля, % | Периоды кристаллической решетки А, Å |
---|---|---|---|---|
№ 1 | γ-Fe | 100.0 ± 0.1 | 100.0 ± 0.1 | 3.5934 ± 0.0004 |
№ 2 | γ-Fe | 97.7 ± 0.1 | 97.8 ± 0.1 | 3.5984 ± 0.0002 |
α-Fe | 2.3 ± 0.1 | 2.2 ± 0.1 | 2.8790 |
Рис. 7.
Дифрактограммы пластин образцов № 1 и № 2. На вставке – увеличенная дифрактограмма образца № 2.
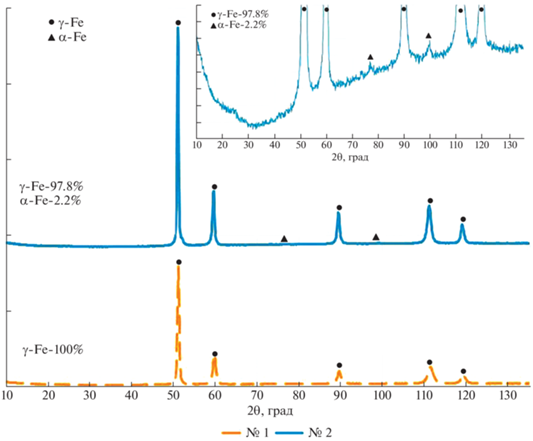
Механические испытания сплавов после прокатки показали, что все образцы обладают хорошей пластичностью (относительное удлинение δ находится в пределах 41–54%) и прочностью (предел прочности σв находится в пределах 626–690 МПа) (табл. 3). Условный предел текучести σ0.2 изменялся в зависимости от химического и фазового состава сплава, а также от ориентировки образцов относительно направления прокатки в пределах от 376 до 492 МПа. Присутствие небольшого количества серебра и титана (0.2% Ag и 0.5% Ti) привело к снижению механических свойств стали. Относительное удлинение δ составило 41 и 47%, а показатель прочности σв – 629 и 626 МПа – соответственно для поперечных и продольных образцов. Более высокие значения наблюдались у образцов сплава № 1: относительное удлинение составило 48 и 54% и предел прочности σв составил 682 и 690 МПа соответственно для поперечных и продольных образцов. Кроме того, для каждого из исследованных сплавов характерно то, что относительное удлинение немного выше у образцов, вырезанных вдоль направления прокатки, а предел текучести ниже, чем у образцов, вырезанных поперек направления прокатки. На предел прочности σв направление прокатки практически не влияет. Анизотропия свойств может быть связана с кристаллографической текстурой и ориентированностью структурных элементов.
Таблица 3.
Механические характеристики горячекатаных пластин образцов относительно ориентировки направления прокатки образцов
Образец | Отн. удл. δ, % | Предел текучести σ0.2, МПа | Предел прочности σв, МПа |
---|---|---|---|
№ 1 (вдоль направления прокатки) | 54 ± 3 | 456 ± 15 | 690 ± 16 |
№ 1 (поперек направления прокатки) | 48 ± 2 | 492 ± 20 | 682 ± 15 |
№ 2 (вдоль направления прокатки) | 47 ± 2 | 376 ± 10 | 626 ± 10 |
№ 2 (поперек направления прокатки) | 41 ± 2 | 453 ± 16 | 629 ± 10 |
Испытания на микротвердость показали также практически одинаковые значения для обоих сплавов (табл. 4).
Таблица 4.
Микротвердость горячекатаных пластин образцов по Виккерсу
Образец | Микротвердость, HV |
---|---|
№ 1 | 280 ± 5 |
№ 2 | 294 ± 6 |
Исследование антибактериальных свойств показало наличие явного антибактериального эффекта у образца № 2. На рис. 8в видно стерильную зону вокруг изучаемого образца, т.е. подавление роста и развития данного штамма бактерий Pseudomonas marginalis. На рис. 8б происходит агломерация бактерий при контакте с образцом № 1.
ЗАКЛЮЧЕНИЕ
Путем дополнительного легирования серебром и титаном получена антибактериальная коррозионностойкая сталь. Исследованы структура, механические и антибактериальные свойства. Для образцов подобраны оптимальные условия гомогенизирующего отжига, который в результате приводит к выравниванию структуры и образованию равноосных зерен размером ~50 мкм. Спектральным анализом показано равномерное распределение серебра по всему объему сплава. Легирование коррозионностойкой аустенитной стали 0.2% Ag и 0.5% Ti привело к появлению в структуре небольшого (2.2 ± 0.1%) количества феррита (α-Fe). Результаты механических испытаний на растяжение прокатанных пластин показали, что при добавлении небольшого количества серебра и титана (0.2% Ag и 0.5% Ti) показатели прочности и пластичности снижаются. Исследование антибактериальных свойств показало наличие явного антибактериального эффекта против штамма бактерий Pseudomonas marginalis у сплава с добавлением серебра и титана.
Список литературы
Grabco D., Shikimaka O., Pyrtsac C., Prisacaru A., Barbos Z., Bivol M., Alexandrov S., Vilotic D., Vilotic M. // Mater. Sci. Eng., A. 2020. V. 805. Article no. 140597. https://doi.org/10.1016/j.msea.2020.140597
Virtanen S., Milošev I., Gomez-Barrena E., Trebše R., Salo J., Konttinen Y.T. // Acta Biomater. 2008. V. 4. № 3. P. 468–476. https://doi.org/10.1016/j.actbio.2007.12.003
Brooks E.K., Brooks R.P., Ehrensberger M.T. // Mater. Sci. Eng. C. 2017. V. 71. P. 200–205. https://doi.org/10.1016/j.msec.2016.10.012
Kirsankin A.A., Kalaida T.A., Kaplan M.A., Smirnov M.A., Ivannikov A.Y., Sevostyanov M.A. // IOP Conf. Ser.: Mater. Sci. Eng. 2020. V. 848. Article no. 012033. https://doi.org/10.1088/1757-899X/848/1/012033
Kaplan M.A., Kirsankin A.A., Smirnov M.A., Kalaida T.A., Baranov E.E., Ustinova Yo.O., Sevostyanov M.A. // IOP Conf. Ser.: Mater. Sci. Eng. 2019. V. 525. Article no. 012075. https://doi.org/10.1088/1757-899X/525/1/012075
Chen Q., Thouas G.A. // Mater. Sci. Eng., R. 2015. V. 87. P. 1–57. https://doi.org/10.1016/j.mser.2014.10.001
Sreekumari K.R., Nandakumar K., Takao K., Kikuchi Y. // ISIJ Int. 2003. V. 43. № 11. P. 1799–1806. https://doi.org/10.2355/isijinternational.43.1799
Yang S.-M., Chen Y.-C., Pan Y.-T., Lin D.-Y. // Mater. Sci. Eng., C. 2016. V. 63. P. 376–383. https://doi.org/10.1016/j.msec.2016.03.014
Du J.K., Chao C.Y., Wei L.L., Wang C.H., Chen J.H., Chen K.K., Huang R.B. // Metals. 2021. V. 11. P. 23. https://doi.org/10.3390/met11010023
Дополнительные материалы отсутствуют.
Инструменты
Доклады Российской академии наук. Химия, науки о материалах