Электрохимия, 2020, T. 56, № 4, стр. 385-394
Влияние электролитно-плазменного полирования на коррозионную стойкость конструкционных сталей после их анодного насыщения азотом, бором и углеродом
С. А. Кусманов a, *, С. А. Силкин a, П. Н. Белкин a
a Костромской государственный университет
156005 Кострома, ул. Дзержинского, 17, Россия
* E-mail: sakusmanov@yandex.ru
Поступила в редакцию 25.02.2019
После доработки 30.03.2019
Принята к публикации 24.07.2019
Аннотация
В статье рассматриваются результаты электролитно-плазменного полирования стальных образцов после их анодного диффузионного насыщения элементами, образующими растворы внедрения. Структура и фазовый состав модифицированных слоев изучены с помощью рентгеновского анализа и электронной микроскопии. Измерена шероховатость поверхности и коррозионная стойкость образцов в 3.5%-ном растворе хлорида натрия. Обнаружена различная морфология оксидного слоя после нитроцементации, азотирования, борирования и бороцементации углеродистых конструкционных сталей 20 и 45. Выявлены варианты обработки и составы электролитов, обеспечивающие снижение поверхностной шероховатости от 1.00 мкм у контрольного образца до 0.23 мкм после бороцементации в растворе борной кислоты, глицерина и хлорида аммония с последующим полированием в сульфатном электролите и до 0.40–0.42 мкм после азотирования в растворе аммиака и хлорида аммония с последующим полированием в сульфатном или хлоридном электролитах. Показана возможность снижения плотности тока коррозии стали 45 почти в 4 раза после азотирования и полирования в сульфатном или хлоридном электролитах.
ВВЕДЕНИЕ
Современная терминология относит к электролитно-плазменным (ЭП) технологиям широкий класс процессов в электролизере, вызванных локализацией выделения тепла у электрода с меньшей площадью поверхности. В этих случаях образуется трехфазная система, содержащая электролит, парогазовую оболочку (ПГО) и металлический электрод. Совокупность тепловых, электрохимических и электроразрядных процессов обнаружила новые технологические возможности обработки металлов и сплавов. Разработанные технологии классифицируются по базовым признакам, которыми могут быть элементарные процессы окисления, насыщения, растворения, диффузии и др. [1]. В других классификациях учитываются процессы создания нанокристаллических покрытий [2] или технологические признаки, включающие полярность обрабатываемой детали, тип используемого напряжения, процедуру создания контакта детали с электролитом [3]. С практической точки зрения методы ЭП-обработки можно классифицировать по их воздействию на материал и разделить на четыре группы. Первой из них будет термическая обработка, включающая отжиг и закалку с использованием постоянного или импульсного тока, а также термоциклирования. Ко второй группе относится химикотермическая обработка (азотирование, нитроцементация, цементация, борирование, бороцементация и бороазотирование). Третью группу составляют покрытия, полученные осаждением металлов или оксидированием. Четвертая группа связана с удалением материала с поверхности детали, куда входят полирование, очистка или диспергирование [4]. В данной работе изучаются ЭП-процессы диффузионного насыщения (ЭПН) и полирования (ЭПП), способствующие повышению коррозионной стойкости конструкционных сталей.
Катодный вариант ЭП-азотирования в водных электролитах повышает сопротивление коррозии благодаря образованию нитрида железа Fe2–3N. Установлено, что обработка нержавеющих сталей 304, 316L и 430 в растворе нитрита натрия тормозит развитие питтинговой коррозии в насыщенном растворе хлорида натрия [5], причем оптимальные режимы обработки зависят от структурных особенностей указанных сталей. Положительные результаты получены после азотирования стали 12Х18Н10Т в электролите, содержащем 20% карбамида и 10% карбоната натрия [6], когда скорость коррозии азотированных образцов снизилась более чем в 2 раза после испытаний в 20%‑ном водном растворе хлорида железа.
Анодное ЭП-азотирование отличается параллельным протеканием высокотемпературного окисления в ПГО и анодного растворения наряду с диффузионным насыщением [7]. Испытания в 1 М растворе сульфата аммония показали, что поверхностный оксидный слой на стали 40Х, азотированной в электролитах, содержащих аммиак или нитрат аммония, обладает защитными свойствами вместе с нитридной зоной [8]. Потенциал коррозии образцов после азотирования сдвигается в положительном направлении, а плотности анодного тока уменьшаются на 2–3 порядка. Аналогичные результаты получены после испытаний азотированной стали 45 в растворе сульфата натрия [7], а также азотированных малоуглеродистой стали SA 106, аустенитной нержавеющей 304 и мартенситной нержавеющей после испытаний в растворах тетрабората натрия и борной кислоты [9]. Также установлено, что охлаждение образцов после азотирования на воздухе, сопровождающееся дополнительным окислением кислородом воздуха, способствует дальнейшему повышению коррозионной стойкости [10]. Механическое удаление оксидного слоя приводит к возрастанию плотности тока коррозии.
Катодная ЭП-цементация в глицериновом электролите улучшает коррозионную стойкость стали Т8 [11]. Потенциал коррозии в 3.5%-ном растворе хлорида натрия после цементации почти не изменяется, но плотность тока коррозии снижается. Также показано, что повышение коррозионной стойкости достигается при образовании оксидного слоя [10]. Анодная ЭП-цементация малоуглеродистых сталей сопровождается более выраженным окислением поверхности по сравнению с катодным вариантом. Наименьшая скорость коррозии образцов в 1 М растворе хлорида натрия 0.14 мг см–2 сут–1 достигается после цементации стали в глицериновом электролите при 900°С, что в 1.5 раза ниже, чем у контрольных образцов [12]. При температуре обработки 1000°С окисление возрастает, но скорость коррозии увеличивается. Предполагается, что качество оксидного слоя ухудшается из-за повышения его пористости. Электрохимическая импедансная спектроскопия показала, что процесс коррозии проходит под смешанным диффузионным и кинетическим контролем.
Катодное борирование стали St14 в растворе, содержащем тетраборат натрия, приводит к сдвигу потенциала коррозии в водопроводной воде в положительном направлении при уменьшении плотности тока коррозии в 23 раза по сравнению с контрольным образцом [13]. Результат объясняется действием защитного слоя боридов железа. Аналогично облагораживается потенциал коррозии стали Н13 в растворе хлорида натрия [14]. Импедансная спектроскопия подтвердила увеличение сопротивления переносу заряда и снижение емкостей двойного слоя и нанокристаллического покрытия. Сопротивление коррозии стали Н13 может быть дополнительно повышено с помощью импульсного борирования в том же электролите. Обнаружено, что увеличение частоты тока снижает плотность тока коррозии, минимальное значение которой достигается при напряжении ЭП-обработки 25 В, частоте 10 кГц и коэффициенте заполнения 40% [15].
Аналогичные результаты получены при одновременном насыщении стали бором и углеродом. Катодная бороцементация стали Q235 в растворе тетрабората натрия с глицерином уменьшает плотность тока коррозии в растворе хлорида натрия (3.5%) и повышает поляризационное сопротивление [16].
Анодная бороцементация в водном растворе, содержащем борную кислоту и глицерин, также повышает коррозионную стойкость стали 20 в децинормальном растворе сульфата натрия [17]. Наибольшее снижение скорости коррозии от 0.38 г/(м2 ч) у контрольного образца до 0.15 г/(м2 ч) наблюдается после бороцементации при 900°С, когда образуется наиболее толстый слой.
Положительные результаты ЭПН сталей элементами, образующими растворы внедрения, не дают достаточной информации о влиянии оксидов железа на коррозионные свойства обработанных сплавов. В еще большей степени это относится к износостойкости сталей, где оксидный слой после анодного ЭПН определяет прирабатываемость пары трения. Анодное растворение, как правило, сглаживает поверхность, но закономерности образования оксидного слоя не выяснены. Имеется предположение [7, с. 43] об отрицательной роли рыхлой части оксидного слоя (преимущественно FeO). Кроме того, обнаружено неконтролируемое отслаивание части оксидного слоя по мере его роста [18], особенно при высоких температурах, что не только может снижать качество слоя, но и, несомненно, ухудшать воспроизводимость результатов измерений. Образуемый на поверхности пористый, и в ряде случаев рыхлый, оксидный слой, приводит не только к повышению шероховатости поверхности, но и при достаточно пористой структуре к увеличению скорости коррозии.
Целью данной работы является изыскание возможности дальнейшего повышения коррозионной стойкости углеродистых сталей после их насыщения азотом, углеродом и бором дополнительным полированием для удаления рыхлой части оксидного слоя. Наиболее подходящим представляется ЭПП, реализуемое в том же электролизере. Технология характеризуется применением безопасных и дешевых нейтральных растворов, высоким качеством и скоростью обработки. Имеется также опыт повышения коррозионной стойкости изделий после снижения их шероховатости путем ЭПП [19].
ЭКСПЕРИМЕНТАЛЬНАЯ ЧАСТЬ
В работе проводилось исследование поверхности стали после ее анодного ЭПН углеродом, азотом и бором, а также последующего ЭПП. Обработке подвергались цилиндрические образцы из стали 20 и стали 45 высотой 15 мм и диаметром 8–10 мм. Перед обработкой образцы зачищались наждачной бумагой до поверхностной шероховатости Ra = 1.00 ± 0.10 мкм и очищались ацетоном в ультразвуковой ванне.
ЭПН осуществлялось в различных по составу электролитах и условиях насыщения, указанных в табл. 1, что позволяло проводить нитроцементацию, бороцементацию, азотирование и борирование. Выбраны составы электролитов и режимы диффузионного насыщения, которые обеспечивали наилучшие характеристики износостойкости без снижения коррозионной стойкости.
Таблица 1.
Составы электролитов и температура ЭПН стальных образцов
Обозначение способа ЭПН | Материал образца | Состав электролита | Температура, °С |
---|---|---|---|
Нитроцементация-1 | Сталь 20 | Карбамид (15%*)–хлорид аммония (10%) | 850 |
Нитроцементация-2 | Сталь 20 | Нитрат аммония (5%)–глицерин (8%)–хлорид аммония (15%) | 850 |
Бороцементация | Сталь 20 | Борная кислота (3%)–глицерин (8%)–хлорид аммония (15%) | 850 |
Азотирование | Сталь 45 | Аммиак (5%)–хлорид аммония (10%) | 750 |
Борирование | Сталь 45 | Борная кислота (3%)–хлорид аммония (10%) | 850 |
Для реализации ЭПН использовался цилиндрический электролизер с продольным обтеканием образцов-анодов электролитом [20]. В верхней части камеры-катода электролит переливался через край в поддон, откуда далее прокачивался через теплообменник при величине расхода 2.6 л/мин. Охлаждение электролита осуществлялось водопроводной водой, температура электролита поддерживалась равной (25 ± 2)°С на входе в электролизер. После подачи напряжения 180 В от источника постоянного тока образцы погружались в электролит с последующей коррекцией напряжения для достижения заданной температуры образца. Температура образцов измерялась мультиметром MS-8221 (Россия) и хромель-алюмелевой термопарой М89-К1 с точностью 2% в диапазоне от 400 до 1000°С. Термопара устанавливалась в отверстии на оси образца на расстоянии 2 мм от нагреваемой поверхности. Диффузионное насыщение осуществлялось в течение 5 мин, после чего образцы охлаждались в электролите (закаливались) от температуры насыщения отключением напряжения, промывались водой и сушились.
После ЭПН стальные образцы подвергались ЭПП в течение 1 мин при напряжении 300 В в водных электролитах хлорида аммония (3%) или сульфата аммония (5%). Образцы при ЭПП, как и при ЭПН, подключались к положительному выходу источника постоянного тока. Температура электролита составляла 80 ± 2°C. Компоненты электролита для ЭПП, их концентрации и режимы выбраны с учетом опубликованных рекомендаций [21].
Рентгеновский анализ фазового состава модифицированных образцов выполнялся на рентгеновском дифрактометре ARL X’tra (Швейцария) (излучение CuKα). Микроструктура поверхностного слоя стали изучалась с помощью сканирующего электронного микроскопа Quanta 3D 200i (Нидерланды). Образцы для электронно-микроскопических исследований подвергались предварительному шлифованию, полированию и травлению в 4%-ном растворе азотной кислоты в этиловом спирте. Шероховатость поверхности измерялась профилометром TR-200. Для изучения морфологии поверхности использовался оптический металлографический микроскоп Микромед МЕТ (Россия) с цифровой визуализацией изображения.
Поляризационные кривые образцов получены с помощью потенциостата-гальваностата Biologic SP-150 (Франция) (в трехэлектродной ячейке при скорости сканирования 1 мВ/с. В качестве противоэлектрода использовался графитовый, а электрода сравнения – хлоридсеребряный. Площадь контакта образца с коррозионной средой (3.5%-ный раствор хлорида натрия) составляла 0.312 см2. Непосредственно перед коррозионными испытаниями образцы выдерживались в электролите в течение 2 ч для установления постоянного значения коррозионного потенциала. Параллельные испытания проводились на трех образцах, разброс результатов измерений плотности тока коррозии не превышал 1.5 мкА/см2.
РЕЗУЛЬТАТЫ И ОБСУЖДЕНИЕ
В результате анодного ЭПН в водных электролитах происходит окисление поверхности стали и диффузия атомов легких элементов в структуру поверхностного слоя с образованием оксидных и диффузионных слоев (рис. 1). Оксидный слой содержит оксиды различного состава и структуры FeO, α-Fe2O3, γ-Fe2O3, ζ-Fe2O3 и Fe3O4 в зависимости от состава электролита и температуры обработки [7]. Диффузионные слои представляют собой твердые растворы атомов диффузантов в железе с дисперсными нитридами, карбидами или боридами в зависимости от вида диффузионного насыщения. Под оксидным слоем стали 20 после ее нитроцементации в указанных выше электролитах наблюдается наружный нитроцементованный слой, содержащий мартенсит, остаточный аустенит и нитриды Fe4N и Fe2–3N, и внутренний диффузионный слой, представляющий собой твердый раствор азота и углерода (рис. 1а и 1б). После бороцементации стали 20 на поверхности под оксидным слоем обнаружены боридный слой, содержащий бориды FeB, и далее вглубь образца диффузионный подслой, содержащий мартенсит и остаточный аустенит (рис. 1в). Азотирование стали 45 приводит к формированию структуры, состоящей из нитридно-мартенситного слоя (мартенсит, остаточный аустенит, нитриды Fe4N и Fe2–3N), и мартенситно-ферритного слоя (мартенсит, остаточный аустенит и твердый раствор азота в стали) (рис. 1г). После борирования стали 45 под оксидным слоем образуется боридно-мартенситный слой, содержащий бориды Fe2B и FeB, мартенсит и остаточный аустенит (рис. 1д).
Рис. 1.
Микроструктура поверхностного слоя стали после ЭПН в водных электролитах и при температурах, соответствующих данным табл. 1: а – нитроцементация-1, б – нитроцементация-2, в – бороцементация, г – азотирование, д – борирование. Обозначения: 1 – оксидный слой, 2 – диффузионный слой, 3 – исходная структура.
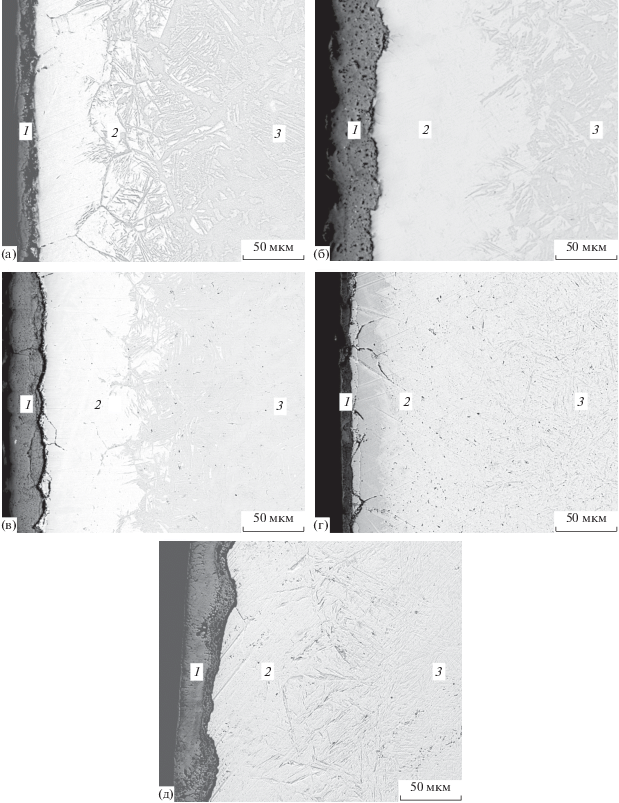
Коррозионное поведение обработанной поверхности определяется в первую очередь составом, структурой и толщиной оксидного слоя [10, 12, 17]. Изучение морфологии поверхности показало различие оксидных покрытий в зависимости от вида ЭПН (рис. 2), что связано с различной интенсивностью процессов окисления и анодного растворения металлической поверхности.
Рис. 2.
Изображение поверхности стали после ЭПН в водных электролитах и при температурах, соответствующих данным табл. 1: а – нитроцементация-1, б – нитроцементация-2, в – бороцементация, г – азотирование, д – борирование, а также после ЭПП в различных электролитах. Обозначения: 1 –образец после ЭПН, 2 – образец после ЭПП в сульфате аммония, 3 – образец после ЭПП в хлориде аммония.
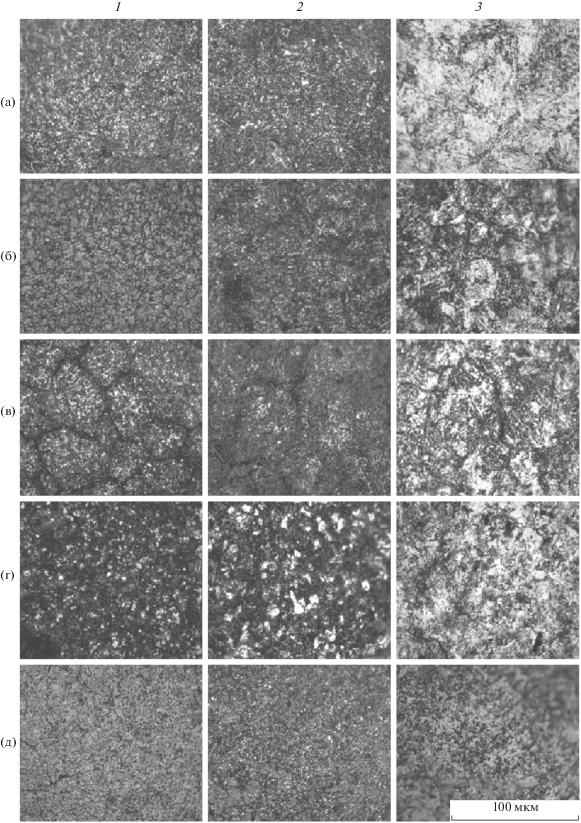
На рис. 2 показаны изображения наружного оксидного слоя, образующегося после различных вариантов ЭПН. Наибольшие поры наблюдаются после бороцементации, наименьшие – после нитроцементации в карбамидном электролите или борирования. Полирование в сульфатном электролите характеризуется относительно слабым травлением поверхности почти без изменения ее морфологии, что связано с пассивирующим действием сульфат-ионов. Очевидно, что удалению подвергалась лишь часть оксидного слоя. Значительно интенсивнее травление после полирования в хлоридном электролите. Некоторое осветление поверхности указывает на частичное удаление сплошного оксидного слоя и обнажение диффузионного слоя, обогащенного оксидами железа.
Удаление наружной части оксидного слоя отражается в убыли массы образцов (табл. 2). Результаты измерения шероховатости показали как ее увеличение, так и уменьшение после ЭПП. Отметим, что даже там, где ЭПП произошло, снижение шероховатости ниже, чем достигаемое в процессе ЭПН, которое, как известно, сопровождается анодным растворением. Сульфатный электролит, хорошо зарекомендовавший себя при ЭПП аустенитной нержавеющей стали [22], демонстрирует явное преимущество перед хлоридным раствором только при полировании бороцементованной стали. Азотированная сталь примерно одинаково полируется в обоих электролитах. Образцы, нитроцементованные в карбамидном электролите, могут слегка полироваться в хлоридном растворе.
Таблица 2.
Изменения шероховатости поверхности и массы образцов после ЭПН и последующей обработки в различных электролитах. Знаки обозначают убыль (–) или прирост (+) соответствующего значения по сравнению с предыдущим этапом обработки
Способ ЭПН | После ЭПН | После ЭПП в сульфате аммония | После ЭПП в хлориде аммония | |||
---|---|---|---|---|---|---|
ΔRa, мкм | Δm, г | ΔRa, мкм | Δm, г | ΔRa, мкм | Δm, г | |
Нитроцементация-1 | –0.70 | –0.2849 | +0.13 | –0.0393 | –0.05 | –0.0401 |
Нитроцементация-2 | –0.61 | –0.1633 | –0.03 | –0.0466 | +0.39 | 0.0422 |
Бороцементация | –0.69 | –0,2241 | –0.08 | –0.0253 | –0.01 | –0.0403 |
Азотирование | –0.45 | –0.1034 | –0.15 | –0.0112 | –0.13 | –0.0347 |
Борирование | –0.64 | –0.1378 | +1.39 | –0.0357 | +0.84 | –0.0518 |
Есть основания считать, что неодинаковые результаты табл. 2 связаны с неоднородной структурой оксидных слоев, не исключая и различия в их составе. Сульфат- и хлорид-ионы активируют растворение железа за счет легкого образования нестабильных адсорбционных комплексов Fe · H2Oадс · ${\text{SO}}_{{4\,{\text{адс}}}}^{{2 - }}$ и Fe · H2Oадс · ${\text{Cl}}_{{{\text{адс}}}}^{ - }$ [21]. По этой причине характеристики полирования существенно зависят от состава обрабатываемого материала, что влечет за собой различные составы электролитов, рекомендуемые для полирования углеродистых и легированных сталей.
Анализ поверхности показал (рис. 2), что после полирования в растворе хлорида аммония происходит ее осветление за счет интенсивного удаления оксидного слоя. При полировании в растворе сульфата аммония такое не наблюдается, что связано с пассивацией поверхности действием сульфат-ионов. Пассивирующее действие сульфат-ионов подтверждается и, как правило, меньшей убылью массы образцов при полировании в растворе сульфата аммония по сравнению с полированием в хлоридном электролите. Исключение составляют образцы после нитроцементации в электролите, содержащем нитрат аммония, который является не только источником азота, но и активным окислителем стальной поверхности. Отметим также, что влияние анионного состава электролита на убыль массы является аргументом в пользу электрохимического механизма ЭПП. Удаление микровыступов на поверхности детали под действием электрического разряда в ПГО нельзя исключать, но такой механизм объясняется умозрительными конструкциями без экспериментального подтверждения [23].
Результаты коррозионных испытаний показали (табл. 3), что после удаления практически всего оксидного слоя ЭПП в хлоридном электролите плотность тока коррозии увеличивается во всех случаях, кроме азотированных образцов. В этом случае защитную роль вместо оксидов выполняют нитриды железа. После ЭПН другими способами нитриды в поверхностном слое отсутствуют или их количество незначительное. Полирование в растворе сульфата аммония показало дополнительное снижение плотности тока коррозии практически во всех случаях в 1.2–1.8 раза, кроме ЭПП образцов из стали 20, подвергшихся нитроцементации в карбамидном электролите. Такие результаты позволяют предположить, что улучшение коррозионной стойкости наблюдается только в тех случаях, когда образуемый при ЭПН оксидный слой имеет рыхлую пористую структуру и его удаление снижает плотность тока коррозии. Не исключено, что существенную роль играет пассивирующее действие сульфат-ионов. Практически полное удаление оксидного слоя, как это было показано на примере полирования в хлоридном электролите, приводит к снижению коррозионной стойкости по данному показателю.
Таблица 3.
Результаты коррозионных испытаний образцов после ЭПН и ЭПП в различных электролитах. Значение плотности тока коррозии до ЭПН составляло 40.8 мкА/см2
Способ ЭПН | Плотность тока коррозии, мкА/см2 | ||
---|---|---|---|
после ЭПН | после ЭПП в сульфате аммония | после ЭПП в хлориде аммония | |
Нитроцементация-1 | 20.8 | 27.0 | 27.5 |
Нитроцементация-2 | 30.8 | 25.4 | 36.5 |
Бороцементация | 19.7 | 14.9 | 30.8 |
Азотирование | 20.0 | 13.1 | 10.7 |
Борирование | 39.3 | 21.6 | 41.9 |
Если рассматривать коррозионное поведение относительно значений потенциала коррозии (рис. 3), то практически полное удаление оксидного слоя полированием в растворе хлорида аммония приводит к увеличению его значения во всех случаях, кроме ЭПП образцов из стали 45, подвергшихся борированию. В этом случае более эффективным является полирование борированных образцов в растворе сульфата аммония. Такие различия в изменении потенциала коррозии можно связать с неоднородностью состава поверхностного слоя.
Рис. 3.
Поляризационные кривые образцов до и после ЭПН в водных электролитах и при температурах, соответствующих данным табл. 1: а – нитроцементация-1, б – нитроцементация-2, в – бороцементация, г – азотирование, д – борирование, а также после ЭПП в различных электролитах. Обозначения: 1 – необработанный образец, 2 – образец после ЭПН, 3 – образец после ЭПП в сульфате аммония, 4 – образец после ЭПП в хлориде аммония.
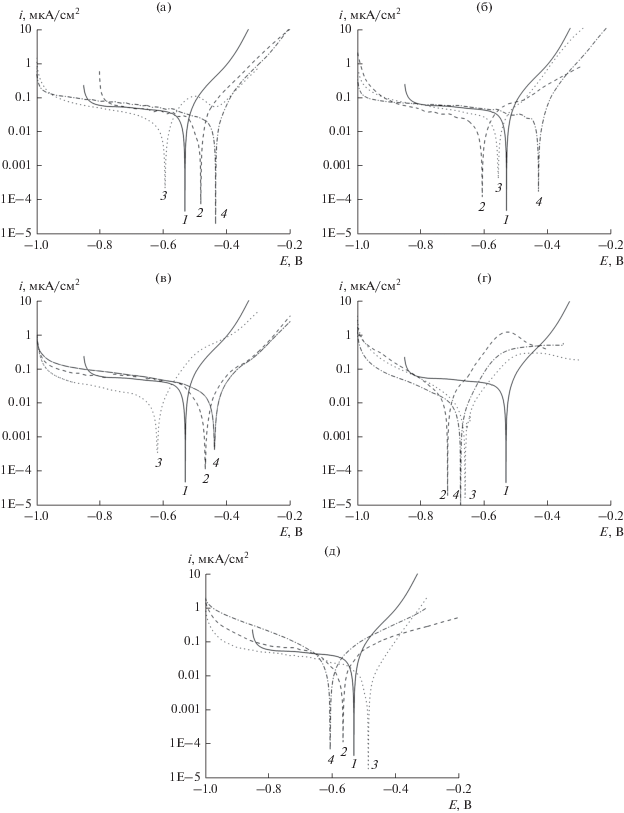
ЗАКЛЮЧЕНИЕ
ЭПП углеродистых сталей после анодного насыщения углеродом, азотом, бором и их сочетаниями обнаружило различный характер изменений в морфологии поверхности, ее шероховатости и коррозионной стойкости в 3.5%-ном растворе хлорида натрия. Во всех случаях диффузионного насыщения образуется наружный оксидный слой, наиболее пористый после бороцементации в электролитах на основе глицерина и борной кислоты, и наименее пористый после нитроцементации в карбамидном электролите или борирования в растворе борной кислоты. ЭПП в сульфатном электролите приводит к относительно слабому травлению без изменения морфологии и в пределах сплошного оксидного слоя. Для раствора хлорида аммония характерно травление с большей убылью массы, частичным удалением сплошного оксидного слоя и некоторым осветлением поверхности. Полирование в сульфатном электролите способно снизить шероховатость поверхности по параметру Ra на 0.03–0.15 мкм у образцов, нитроцементованных в растворе нитрата аммония и глицерина, а также борированных или азотированных в соответствующих электролитах. Положительные результаты ЭПП в растворе хлорида аммония ради уменьшения поверхностной шероховатости обнаружены только для азотированных образцов.
ЭПН цементованных, азотированных и борированных стальных образцов можно считать перспективным с точки зрения коррозионных токов. Плотность тока коррозии в 3.5%-ном растворе хлорида натрия максимально снижается от 40.8 мкА/см2 у необработанной стали до 19.7 мкА/см2 после бороцементации, минимально до 30.8 мкА/см2 после нитроцементации в нитратно-глицериновом электролите и почти не изменяется после борирования. ЭПП в сульфатном электролите дает возможность дополнительно снизить плотность тока коррозии всех изученных образцов за исключением нитроцементованного в карбамидном электролите. Наоборот, раствор хлорида аммония во всех случаях уменьшает сопротивление коррозии, кроме азотированного образца, где достигается наименьшая плотность тока коррозии 10.7 мкА/см2.
Список литературы
Yerokhin, A.L., Nie, X., Leyland, A., Matthews A., and Dowey, S.J., Plasma electrolysis for surface engineering, Surf. Coat. Technol., 1999, vol. 122, p. 73.
Aliofkhazraei, M., Rouhaghdam, A. Sabour, and Gupta, P., Nano-Fabrication by Cathodic Plasma Electrolysis, Crit. Rev. Solid. State, 2011, vol. 36, p. 174.
Parfenov, E.V., Yerokhin, A., Nevyantseva, R.R., Gorbatkov, M.V., Liang, C.-J., and Matthews, A., Towards smart electrolytic plasma technologies: An overview of methodological approaches to process modeling, Surf. Coat. Technol., 2015, vol. 269, p. 2.
Krivenko, A.G., Manzhos, R.A., and Kotkin, A.S., Plasma-assisted electrochemical exfoliation of graphite in the pulsed mode, High Energy Chem., 2018, vol. 52, no. 32, p. 272.
Aliev, M.Kh., Sabour, A., and Taheri, P., Study of corrosion protection of different stainless steels by nanocrystalline plasma electrolysis, Prot. Met. Phys. Chem., 2008, vol. 44, no. 4, p. 402.
Курбанбеков, Ш.Р. Модификация структуры и механических свойств поверхностных слоев стали 12Х18Н10Т при электролитно-плазменной обработке, Дисс. … доктора философии (PhD). Восточно-Казахстанский государственный технический университет им. Д. Серикбаева. Усть-Каменогорск, 2014. 120 с. [Kurbanbekov, Sh.R., Modification of the structure and mechanical properties of the steel 12Cr18N10T surface layers at plasma electrolytic treatment (in Russian), D. Serikbayev East Kazakhstan State Technical University, Ust-Kamenogorsk, 2014. 120 p.]
Кусманов, С.А., Дьяков, И.Г., Белкин, П.Н. Теоретические основы электролитно-плазменного нагрева и его применение для диффузионного насыщения металлов и сплавов. Кострома: Изд-во Костром. гос. ун-та. 2017. 420 с. [Kusmanov, S.A., Dyakov, I.G., and Belkin, P.N., Theoretical bases of plasma electrolytic heating and its application for diffusion saturation of metals and alloys (in Russian), Kostroma: Kostroma State University, 2017. 420 p.]
Чернова, Г.П., Богдашкина, Н.Л., Паршутин, В.В., Ревенко, В.Г., Томашов, Н.Д., Белкин, П.Н., Пасинковский, Е.А., Факторович, А.А. Электрохимическое и коррозионное поведение стали 40Х, азотированной в «электролитной плазме». Защита металлов. 1984. Т. 20. № 3. С. 408. [Chernova, G.P., Bogdashkina, N.L., Parshutin, V.V., Revenko, V.G., Tomashov, N.D., Belkin, P.N., Pasinkovsky, E.A., and Faktorovich, A.A., Electrochemical and corrosion behavior of 40KH steel nitrated in “electrolyte plasma,” Protection of metals (in Russian), 1984, vol. 20, no. 3, p. 408.]
Andrei, V., Vlaicu, Gh., Fulger, M., Ducu, C., Diaconu, C., Oncioiu, Gh., Andrei, E., Bahrim, M., and Gheboianu, A., Chemical and structural modifications induced in structural materials by electrochemical processes, Romanian Reports in Physics, 2009, vol. 61, no. 1, p. 95.
Ревенко, В.Г., Чернова, Г.П., Паршутин, В.В., Богдашкина, Н.Л., Томашов, Н.Д. Белкин, П.Н., Пасинковский, Е.А. Влияние процесса азотирования в электролите на защитные свойства конверсионных покрытий. Защита металлов. 1988. Т. 24. № 2. С. 204. [Revenko, V.G., Chernova, G.P., Parshutin, V.V., Bogdashkina, N.L., Tomashov, N.D. Belkin, P.N., and Pasinkovsky, E.A., Effect of electrolytic nitriding on the protective properties of conversion coatings, Protection metals (in Russian), 1988, vol. 24, no. 2, p. 204.]
Wu, J., Xue, W., Wang, B., Jin, X., Du, J., and Li, Y., Characterization of carburized layer on T8 steel fabricated by cathodic plasma electrolysis, Surf. Coat. Technol., 2014, vol. 245, p. 9.
Кусманов, С.А., Гришина, Е.П., Белкин, П.Н., Кусманова, Ю.В., Кудрякова, Н.О. Повышение коррозионной стойкости малоуглеродистых сталей электролитно-плазменным насыщением азотом и углеродом. Металловедение и терм. обработка. 2017. Т. 740. № 2. С. 52. [Kusmanov, S.A., Grishina, E.P., Belkin, P.N., Kusmanova, Yu.V., and Kudryakova, N.O., Raising the Corrosion Resistance of Low-Carbon Steels by Electrolytic-Plasma Saturation with Nitrogen and Carbon, Met. Sci. Heat Treat., 2017, vol. 59, no. 1, p. 117.]
Tavakoli, H., Mousavi Khoie, S.M., Rasooli, F., Marashi, S.P.H., and Momeni, F., Electrochemical and physical characteristics of the steel treated by plasma-electrolysis boronizing, Surf. Coat. Technol., 2015, vol. 276, p. 529.
Taheri, P., Dehghanian, Ch., Aliofkhazraei, M., and Rouhaghdam, A.S., Evaluation of Nanocrystalline Microstructure, Abrasion, and Corrosion Properties of Carbon Steel Treated by Plasma Electrolytic Boriding, Plasma Process. Polym., 2007, vol. 4, p. S711.
Alavi, S.H., Dehghanian, C., and Taheri, P., Investigation of corrosion behaviour of carbon steel coated by pulsed plasma electrolytic boronising technique in 35 wt-% NaCl aqueous solution, Surf. Eng., 2011, vol. 27, p. 509.
Wang, B., Xue, W., Wu, J., Jin, X., Hua, M., and Wu, Z.L., Characterization of surface hardened layers on Q235 low-carbon steel treated by plasma electrolytic borocarburizing, J. Alloys Compd., 2013, vol. 578, p. 162.
Кусманов, С.А., Тамбовский, И.В., Наумов, А.Р., Дьяков, И.Г., Колесникова, И.А., Белкин, П.Н. Анодная электролитно-плазменная бороцементация малоуглеродистой стали. Физикохимия поверхности и защита металлов. 2017. Т. 53. № 3. С. 321. [Kusmanov, S.A., Tambovsky, I.V., Naumov, A.R., Dyakov, I.G., Kolesnikova, I.A., and Belkin, P.N., Anodic Electrolytic-Plasma Borocarburizing of Low-Carbon Steel, Prot. Met. Phys. Chem. Surf., 2017, vol. 53, no. 3, p. 488.]
Реснер, Э., Маркс, Г., Зайцев, В.А., Сухотин, А.М. Износ электрода при обработке малоуглеродистой стали в электролитной плазме при анодном процессе. Электрон. обработка материалов. 1983. № 3. С. 59. [Resner, E., Marks, G., Zaytsev, V.A., and Suchotin, A.M., Electrode wear when processing steel in electrolyte plasma during anodic process, Elektron. obrabotka materialov (in Russian), 1983, no. 3, p. 59.].
Смыслова, М.К., Таминдаров, Д.Р., Самаркина, А.Б. Влияние электролитно-плазменной обработки на физико-химическое состояние поверхности и механические свойства лопаток паровых турбин из стали 20Х13. Авиационно-космическая техника и технология. 2011. Т. 84. № 7. С. 25. [Smyslova, M.K., Tamindarov, D.R., and Samarkina, A.B., Effect of electrolytic-plasma treatment on the physicochemical state of the surface and mechanical properties of steam turbine blades made of 20Х13 steel, Aerospace Engineering and Technology (in Russian), 2011, vol. 84, no. 7, p. 25.]
Smirnov, A.A., Kusmanov, S.A., Kusmanova, I.A., and Belkin, P.N., Effect of Electrolyte Depletion on the Characteristics of the Anodic Plasma Electrolytic Nitriding of a VT22 Titanium Alloy, Surf. Eng. Appl. Electrochem., 2017, vol. 53, no. 5, p. 413.
Иванова, Н.П., Синькевич, Ю.В., Шелег, В.К., Янковский, И.Н. Механизм анодного растворения коррозионностойких и конструкционных углеродистых сталей в условиях электроимпульсного полирования. Наука и техника. 2013. № 1. С. 24. [Ivanova, N.P., Sinkevich, Yu.V., Sheleg, V.K., and Yankovsky, I.N., Mechanism of anodic dissolution of corrosion-resistant and structural carbon steels under conditions of electropulse polishing, Science and Technology (in Russian), 2013, no. 1, P. 24].
Чиркунова, Н.В., Воленко, А.П. Мулюков, Р.Р., Шлом, М.В. Совершенствование технологии электролитно-плазменного полирования аустенитной нержавеющей стали. Письма о материалах. 2013. Т. 3. С. 309. [Chirkunova, N.V., Volenko, A.P., Mulyukov, R.R., and Shlom, M.V., Improving the technology of electrolytic-plasma treatment of austenitic stainless steel, Lett. Mater., 2013, vol. 3, no. 4, p. 309.]
Веселовский, А.П., Кюбарсэп, С.В., Ушомирская, Л.А. Особенности электролитно-плазменной обработки металлов в нетоксичных электролитах. Металлообработка. 2002. № 6. С. 29. [Veselovsky, A.P., Kubarsep, S.V., and Ushomirskaya, L.A., Features of plasma electrolytic treatment of metals in non-toxic electrolytes, Met. Proc. (in Russian), 2002, no. 6, P. 29.]
Дополнительные материалы отсутствуют.
Инструменты
Электрохимия