Электрохимия, 2021, T. 57, № 3, стр. 131-141
Нефтяной кокс как активный материал отрицательного электрода литий-серных аккумуляторов
Е. В. Кузьмина a, *, Е. В. Карасева a, Н. В. Чудова a, А. Л. Иванов a, В. С. Колосницын a, **
a Уфимский Институт химии Уфимского федерального исследовательского центра РАН
450054 Уфа, просп. Октября, 69, Россия
* E-mail: kuzmina@anrb.ru
** E-mail: kolos@anrb.ru
Поступила в редакцию 12.03.2020
После доработки 22.06.2020
Принята к публикации 07.07.2020
Аннотация
В работе рассматривается возможность использования углеродных материалов на основе нефтяного кокса в качестве дешевого и доступного активного материала отрицательных электродов для литий-серных аккумуляторов. Выполнены сопоставительные исследования характеристик литий-серных ячеек с отрицательными электродами на основе металлического лития, графита и нефтяного кокса. Установлено, что термообработанный нефтяной кокс может быть успешно использован в качестве активного материала отрицательных электродов литий-серных аккумуляторов с приемлемыми энергетическими характеристиками. При прочих равных условиях литий-серные ячейки с отрицательными электродами на основе термообработанного нефтяного кокса обладают бóльшей длительностью циклирования по сравнению с ячейками на основе металлического лития и графита. Это объяснено более медленной деструкцией компонентов электролитных систем на отрицательном электроде в процессе циклирования литий-серных ячеек. Показано, что применение в литий-серных аккумуляторах отрицательных электродов на основе нефтяного кокса позволяет существенно увеличить длительность циклирования и снизить их стоимость.
ВВЕДЕНИЕ
Электрохимическая система литий-сера вызывает большой интерес для создания энергоемких накопителей энергии благодаря высокой теоретической удельной энергии, низкой стоимости и доступности активных материалов, безопасности для природы и человека. Работы по созданию литий-серных аккумуляторов (ЛСА) ведутся с 70‑х годов ХХ столетия, но до сих пор не увенчались успехом.
Разработка ЛСА ведется по нескольким направлениям. Разрабатываются ЛСА с жидкими, полимерными и твердыми электролитами [1, 2]. В качестве активного компонента отрицательных электродов ЛСА применяются металлический литий, графит, кремний и другие материалы [3]. Как активный материал положительного электрода используется элементарная сера, сероуглеродные композиты, серосодержащие полимеры [4]. Применяемые активные материалы положительных и отрицательных электродов, состав и тип электролитных систем определяют как энергетические, так и эксплуатационные характеристики ЛСА.
Одной из проблем, требующей решения для создания коммерчески приемлемых ЛСА, является проблема длительности их циклирования.
Длительность циклирования ЛСА определяется рядом факторов:
• скоростью деструкции компонентов электролитных систем на отрицательном электроде;
• интенсивностью образования на отрицательном электроде мелкодисперсных осадков лития;
• степенью пассивации поверхности углеродного каркаса положительного электрода труднорастворимыми продуктами электрохимических реакций.
Основными факторами, ограничивающими длительность циклирования литий-серных аккумуляторов, являются деструкция компонентов электролитных систем на отрицательном литиевом электроде и диспергация металлического литиевого электрода в процессе длительного циклирования.
Длительность циклирования ЛСА может быть увеличена заменой металлического литиевого электрода на графитовый электрод [5, 6]. В качестве источника ионов лития и активного компонента положительного электрода ЛСА в этом случае предлагается использовать сульфид лития [7‒10], который легко получается карботермическим восстановлением сульфата лития – дешевого и доступного реагента [11–16].
Графитовые электроды получили широкое применение в качестве отрицательных электродов литий-ионных аккумуляторов (ЛИА) [17, 18]. Однако необходимо отметить, что, несмотря на широкое распространение, графитовые электроды обладают рядом существенных недостатков, основными из которых являются высокая чувствительность к составу и качеству электролитных систем (условиям формирования SEI) и возможность образования мелкодисперсных осадков металлического лития на их поверхности при заряде литий-ионных аккумуляторов относительно высокими скоростями, поскольку потенциал интеркаляции ионов лития в графит близок к потенциалу осаждения металлического лития.
Интеркаляция ионов лития в твердые неупорядоченные углероды протекает при более высоких значениях потенциалов, что снижает вероятность электрохимического осаждения лития. Более того, неупорядоченные углероды обладают бóльшей удельной емкостью, бóльшей длительностью циклирования, способностью циклироваться при более высоких плотностях тока, более низкой стоимостью производства [19]. Неупорядоченные углероды предложено использовать в качестве отрицательных электродов литий-ионных аккумуляторов [20, 21] и литий-ионных конденсаторов [22–25]. Недостатком отрицательных электродов на основе неупорядоченных углеродов является большая необратимая потеря емкости на первом цикле [19]; она может быть устранена предварительным литированием неупорядоченных углеродов [22, 24].
Мы предположили, что в качестве дешевого и доступного активного материала отрицательных электродов для литий-серных аккумуляторов могут быть использованы углеродные материалы на основе нефтяного кокса, которые представляют собой неупорядоченные углероды. Целью работы было оценить возможность и целесообразность применения в качестве активного материала отрицательных электродов литий-серных аккумуляторов нефтяного кокса и провести сопоставительные исследования характеристик литий-серных ячеек с отрицательными электродами на основе металлического лития, графита и нефтяного кокса.
ЭКСПЕРИМЕНТАЛЬНАЯ ЧАСТЬ
Объекты исследования
Объектами исследования были литий-серные ячейки с отрицательными электродами, изготовленными из металлической литиевой фольги (100 мкм, Battery Grade, China Energy Lithium Ltd.), графита (Degussa, LITARIONTM AC 3422) и термообработанного нефтяного кокса электродного (НКЭ, ТУ 38.1011320-90).
Нефтяной кокс подвергали термической обработке в собственных парах, выдерживая образцы при 1000°С в течение 10 ч в закрытом керамическом тигле. Навеску НКЭ помещали в керамический тигель (2/3 от объема), закрывали крышкой, устанавливали в холодную муфельную печь и нагревали со скоростью 10°С/мин. По достижении 1000°С образец выдерживали в течение 10 ч, выключали нагрев и после охлаждения печи до 800°С образец, не открывая тигель, переносили в эксикатор для охлаждения до комнатной температуры.
Удельную площадь поверхности исходного и термообработанного НКЭ оценивали методом сорбции красителей (метиловый оранжевый – МО) [26]. Удельное объемное сопротивление образцов нефтяного кокса измеряли в кондуктометрических ячейках с блокирующими электродами, изготовленных из нержавеющей стали, при фиксированном давлении 6.4 × 104 кг/см2. Ошибка эксперимента не превышала 3%.
КР-спектры углеродных материалов были зарегистрированы с помощью конфокального рамановского микроспектрометра HoribaJobinYvonXploraPlus (HORIBA) в диапазоне волновых чисел 500–3500 см–1, длина волны лазерного излучения составляла 532 нм. Для каждого образца исследуемого материала регистрировали 3–5 КР-спектров в различных точках, затем полученные спектры усредняли. О степени дефектности углеродной поверхности судили по соотношению интенсивностей D и G полос в КР-спектрах.
Термограммы углеродных материалов регистрировали в атмосфере собственных паров в закрытых корундовых тиглях на модернизированном дериватографе системы F. Paulik, J. Paulik, L. Erdei венгерской фирмы “МОМ”. Масса навесок составляла 100 мг, скорость нагрева 5°С/мин.
Отрицательные углеродные электроды представляли собой слой смеси, состоящей из 94 мас. % активного материала (нефтяной кокс или графит), 1 мас. % сажи (Super P) и 5 мас. % связующего (LA-132), нанесенный на медную фольгу толщиной 16 мкм. Содержание НКЭ или графита в электродах составляло 5.7 мг/см2.
Положительные серные электроды представляли собой однородный слой смеси, содержащей 70 мас. % S (ос. ч. 15-3, Россия), 10 мас. % углеродной сажи Ketjenblack® EC-600JD (Akzo Nobel) и 20 мас. % полиэтиленоксида (ПЭО, ММ 4 × 106, Sigma Aldrich), нанесенный на алюминиевую фольгу с углеродным покрытием толщиной 17 мкм (Tob New Energy, Китай) [27]. Содержание серы в электродах составляло 0.9 мг/см2, что соответствовало поверхностной емкости 1.5 мА ч/см2.
Во всех электрохимических ячейках сепаратором был 1 слой микропористого полипропилена Celgard®3501, а электролитом – 1 М раствор LiClO4 в сульфолане. Количество электролита в литий-серных ячейках составляло 4 мкл/мА ч (S).
Перед сборкой литий-серных ячеек углеродные электроды предварительно литировали. Для этого собирали ячейки с металлическими литиевыми и углеродными электродами и подвергали пяти формовочным зарядно-разрядным циклам при плотности тока 0.1 мА/см2. Диапазон напряжений циклирования ячеек с электродами на основе графита 0.01–0.5 В и НКЭ – 0.05–1.0 В относительно литиевого электрода. После 5 формовочных циклов ячейки переносили в перчаточный бокс, литированные углеродные электроды извлекали из ячеек и устанавливали в ячейки с серными электродами.
Условия циклирования литий-серных ячеек: плотность тока заряда 0.1 мА/см2, разряда – 0.2 мА/см2. Диапазон напряжений циклирования 1.5–2.8 В для ячеек с литиевым электродом и 1.0–2.8 В для ячеек с отрицательными литированными углеродными электродами.
Все операции по сборке электрохимических ячеек выполняли в перчаточном боксе в атмосфере сухого воздуха (содержание воды не превышало 2 ppm).
После сборки все электрохимические ячейки выдерживали при 30°С в течение 24 ч для установления равновесия. Точность стабилизации температуры составляла ±0.1°С.
Гальваностатическое зарядно-разрядное циклирование осуществляли с помощью батарейного тестера BT-05PG (УфИХ УФИЦ РАН) [28]. Результаты циклирования обрабатывали с помощью специального программного обеспечения ElChemLab, Data Analyzer [29, 30].
Расчет удельной энергии литий-серных ячеек
Расчет весовой и объемной удельной энергии электродных модулей литий-серных ячеек выполняли по уравнениям (1) и (2) с помощью программного обеспечения ElChemLab, Battery Designer [31]:
где Wm – удельная весовая энергия электродного модуля ячеек, Вт ч/кг; U – среднее напряжение разряда, В; Q – емкость ячейки, А ч; m – масса электродного модуля ячейки, кг; WV – удельная объемная энергия электродного модуля ячеек, Вт ч/л; V – объем электродного модуля ячейки, л.РЕЗУЛЬТАТЫ И ОБСУЖДЕНИЕ
Исходный НКЭ не обладает электрохимической активностью. Удельное сопротивление НКЭ составляет 1.4 × 107 Ом см, а удельная площадь поверхности, определенная методом сорбции метилового оранжевого, составила 0.2 м2/г [32]. После термической обработки удельное объемное сопротивление нефтяного кокса понизилось до 0.03 Ом см, что в 20 раз ниже удельного сопротивления промышленного синтетического графита (0.6 Ом см), а удельная площадь поверхности НКЭ увеличилась с 0.2 до 6.8 м2/г. Удельная площадь поверхности графита составляла 1.2 м2/г по МО.
Термообработка нефтяного кокса оказала влияние на его термические свойства и спектры комбинационного рассеяния.
На термограмме нефтяного кокса на термогравиметрической кривой первоначально наблюдается небольшое увеличение массы (280°С) (рис. 1), которое может быть объяснено окислением функциональных групп соединений, входящих в состав нефтяного кокса, кислородом воздуха с образованием нелетучих кислородсодержащих продуктов. Термодеструкция нефтяного кокса осуществляется в три стадии. На первой стадии в диапазоне 425–650°С происходит потеря 30% массы образца кокса. На второй стадии в диапазоне 650–900°С потеря массы кокса составляет 25%. На третьей стадии в диапазоне 900–1000°С происходит потеря еще 20% массы образца кокса. Из формы термогравиметрических кривых следует, что наиболее быстро термодеструкция нефтяного кокса протекает на первой и второй стадиях.
Рис. 1.
Термограммы углеродных материалов для отрицательных электродов: 1 – исходный НКЭ, 2 – НКЭ, подвергнутый термообработке (1000°С, 10 ч), 3 – графит.
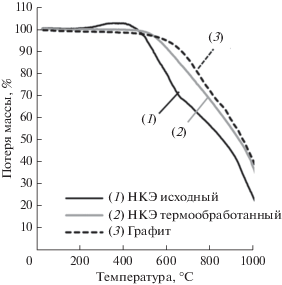
На термогравиметрической кривой нефтяного кокса, термообработанного при 1000°С в течение 10 ч, участка увеличения массы не наблюдается. После термообработки термостабильность нефтяного кокса увеличивается, потеря массы начинается лишь при температуре 530°С. Графит – термостабильнее по сравнению с термообработанным нефтяным коксом. Температура начала потери массы графита составляет 665°С.
Спектры комбинационного рассеяния исходного и термообработанного нефтяного кокса подобны (рис. 2), но имеют некоторые различия. В КР-спектрах как исходного, так и термообработанного нефтяного кокса наблюдаются две широкие перекрывающиеся полосы с максимумами 1332 и 1582 см–1, относящиеся к D- и G-полосам углеродной решетки [33, 34]. После термообработки ширина D- и G-полос уменьшается и изменяется соотношение их интенсивностей. Так, до термообработки ID/IG = 0.8, а после термообработки ID/IG = 1.1. Наблюдаемые изменения соотношения интенсивностей G- и D-полос указывают на некоторое упорядочение структуры кристаллической решетки нефтяного кокса после термообработки и увеличение доли sp3-гибридизованных атомов углерода по сравнению с sp2-гибридизованными [35, 36]. Уменьшение интенсивности G-полосы и отсутствие полосы G' (2700 см–1) в КР-спектрах термообработанного нефтяного кокса указывают на то, что при его термообработке при температуре 1000°С в течение 10 ч не происходит его графитизации.
Рис. 2.
КР-спектры углеродных материалов для отрицательных электродов: (а) исходный НКЭ, (б) НКЭ, подвергнутый термообработке (1000°С, 10 ч), (в) графит.
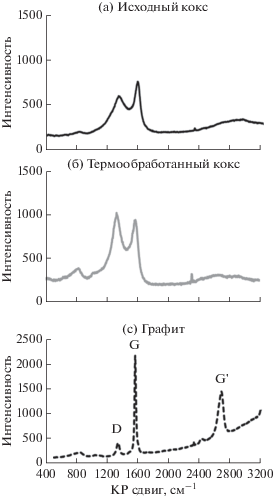
Формы зарядных и разрядных кривых ячеек с электродами на основе термообработанного нефтяного кокса отличаются от форм кривых, зарегистрированных для литий-углеродных ячеек с электродами на основе графита, и подобны зарядно-разрядным кривым ячеек с электродами на основе структурно неупорядоченных углеродов [37–39]. Зарядные кривые представляют собой вогнутые относительно оси абсцисс кривые (рис. 3а). Заряд ячеек с электродами на основе нефтяного кокса осуществляется в диапазоне 0.05–1.0 В. Среднее напряжение заряда литий-НКЭ ячеек составило около 0.4 В и разряда 0.5 В. Среднее напряжение заряда литий-графитовых ячеек составило около 0.1 В, а разряда – около 0.2 В. Среднее напряжение литий-литиевых ячеек при циклировании составило порядка 0.01 В.
Рис. 3.
Зарядно-разрядные кривые ячеек с отрицательными электродами на основе металлического лития, графита и нефтяного кокса электродного, подвергнутого термообработке (1000°С, 10 ч) (а) и разрядные кривые литий-серных ячеек с этими электродами (б). Активный материал отрицательных электродов приведен в легенде.
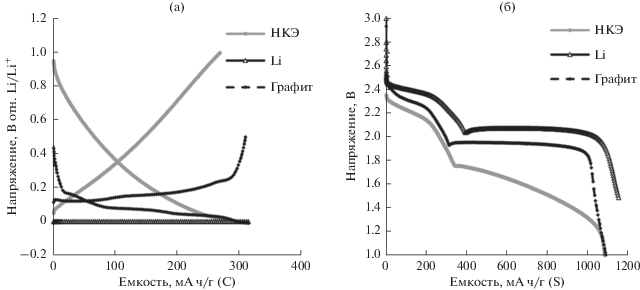
При заряде литий-углеродных ячеек происходит интеркаляция ионов лития в углеродные частицы (уравнение (3)), а при разряде осуществляется обратный процесс (уравнение (4)):
(3)
$x{\text{L}}{{{\text{i}}}^{ + }} + {{{\text{C}}}_{y}} + x{\text{e}} \to {\text{L}}{{{\text{i}}}_{x}}{{{\text{C}}}_{y}},$(4)
${\text{L}}{{{\text{i}}}_{x}}{{{\text{C}}}_{y}} \to z{\text{L}}{{{\text{i}}}^{ + }} + {\text{L}}{{{\text{i}}}_{x}}_{{--z}}{{{\text{C}}}_{y}} + z{\text{e}}.$Разрядные кривые литий-серных ячеек (ЛСЯ) с отрицательными электродами на основе различных активных материалов подобны, но имеют некоторые различия (рис. 3б). Природа активного материала отрицательного электрода слабо влияет на форму высоковольтных участков разрядных кривых, но оказывает существенное влияние на форму низковольтных участков. В отличие от разрядных кривых ЛСЯ с отрицательными электродами на основе металлического лития и графита, низковольтный участок разрядной кривой ЛСЯ с отрицательным электродом на основе нефтяного кокса имеет существенный наклон.
Подобие форм разрядных кривых литий-серных ячеек с различыми отрицательными электродами указывает на сохранность механизма электрохимического восстановления серы на положительном электроде. При разряде литий-серных ячеек на положительном электроде, через ряд промежуточных стадий, происходит электрохимическое восстановление серы первоначально до тетрасульфида лития (высоковольтная площадка на разрядной кривой, уравнение (5)), а затем тетрасульфид лития восстанавливается до дисульфида и сульфида лития (низковольтная площадка на разрядной кривой, уравнение (6)).
(5)
${{{\text{S}}}_{8}} + {\text{ }}4{\text{L}}{{{\text{i}}}^{ + }} + {\text{ }}4{\text{e}} \to {\text{ }}2{\text{L}}{{{\text{i}}}_{2}}{{{\text{S}}}_{4}},$(6)
$2{\text{L}}{{{\text{i}}}_{2}}{{{\text{S}}}_{4}} + 8{\text{L}}{{{\text{i}}}^{ + }} + 8{\text{e}} \to 2{\text{L}}{{{\text{i}}}_{2}}{{{\text{S}}}_{2}} + 4{\text{L}}{{{\text{i}}}_{2}}{\text{S}}{\kern 1pt} \downarrow {\kern 1pt} .$На отрицательном электроде при разряде литий-серных ячеек происходит электрохимическая деинтеркаляция ионов лития из углеродных электродов (уравнение (4)) и электрохимическое растворение лития из металлического литиевого электрода (уравнение (7)).
Среднее разрядное напряжение ЛСЯ с металлическим литиевым электродом составило 2.1 В, с графитовым отрицательным электродом 1.9 В и с электродом на основе нефтяного кокса 1.7 В. Среднее разрядное напряжение литий-серных ячеек с графитовым электродом ниже среднего разрядного напряжения ЛСЯ с литиевым электродом на 0.2 В, а ячеек с электродом на основе НКЭ – на 0.4 В. Таким образом, напряжение разряда литий-серных ячеек с углеродными отрицательными электродами меньше на величину разрядных напряжений литий-углеродных ячеек (рис. 3а).
Природа активного материала отрицательного электрода оказывает существенное влияние на скорость снижения емкости ЛСЯ в процессе циклирования (рис. 4). На начальных этапах скорость уменьшения разрядной емкости литий-серных ячеек слабо зависит от природы активного материала отрицательного электрода (рис. 4а). Начальный спад емкости обусловлен перераспределением серы по толщине положительного электрода и объему ячеек [27]. Однако длительность циклирования11 ЛСЯ с отрицательными электродами на основе различных активных материалов значительно различается: длительность циклирования ячеек с металлическими литиевыми электродами составила – 270 циклов, с графитовыми электродами – 300 циклов, с электродами на основе термообработанного нефтяного кокса – около 700 циклов.
Рис. 4.
Изменение разрядной емкости (а), кулоновской (б) и энергетической (в) эффективности циклирования литий-серных ячеек с отрицательными электродами на основе различных активных материалов. Активный материал отрицательных электродов приведен в легенде.
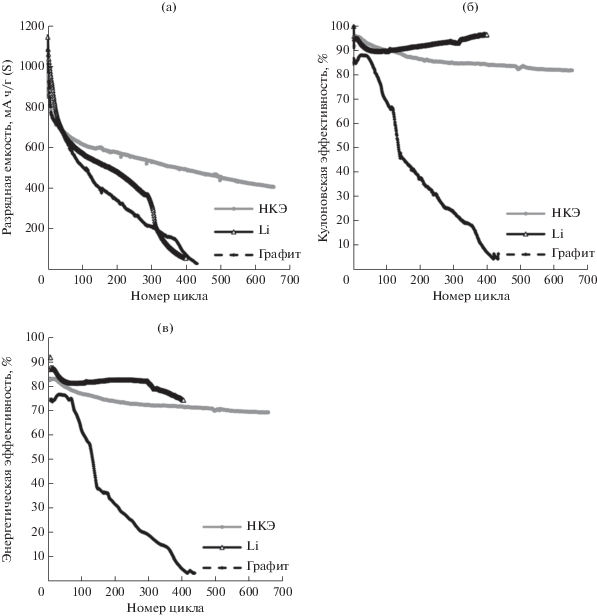
На основе анализа форм кривых потери емкости литий-серных ячеек в процессе циклирования можно заключить, что, поскольку состав и конструкция литий-серных ячеек отличаются только составом и конструкцией отрицательных электродов, пассивация поверхности углеродного каркаса положительных элекродов во всех исследуемых литий-серных ячейках происходит примерно с одинаковой скоростью. Однако деструкция компонентов электролитных систем и образование мелкодисперсных осадков лития на отрицательных электродах осуществляется с существенно различной скоростью, которая уменьшается в следующем ряду – металлический литий > > графит > НКЭ.
На начальных этапах циклирования кулоновская эффективность циклирования ЛСЯ с отрицательными электродами на основе металлического лития и модифицированного НКЭ составляет 95%, а графита – 85–90% (рис. 4б). По мере циклирования кулоновская эффективность циклирования ЛСЯ с литиевыми электродами первоначально несколько снижается и затем увеличивается до 98%. Кулоновская эффективность циклирования ЛСЯ с термообработанным нефтяным коксом плавно уменьшается и затем, достигнув 82–84%, стабилизируется. Кулоновская эффективность ЛСЯ с отрицательными электродами на основе графита в процессе зарядно-разрядного циклирования уменьшается.
Эффективность преобразования энергии в ЛСЯ существенно зависит от природы активного материала отрицательных электродов. На начальных циклах она составляет 90% для ячеек с отрицательным литиевыми электродами, 83–85% – с отрицательными электродами на основе термообработанного нефтяного кокса и 75–80% – с отрицательными графитовыми электродами (рис. 4в). Изменение эффективности преобразования энергии в процессе циклирования в ЛСЯ с отрицательными электродами на основе НКЭ и графита происходит аналогично изменению кулоновской эффективности. Эффективность преобразования энергии в ЛСЯ с литиевыми электродами первоначально уменьшается, затем слабо увеличивается и снова снижается.
Природа активного материала отрицательного электрода и его конструкция оказывают влияние на энергетические характеристики ЛСА. Поскольку удельная энергия аккумуляторов определяется не только весом материалов, необходимых для их работы, но и весом корпуса, сравнение энергетических характеристик различных прототипов аккумуляторов удобнее всего производить на уровне электродных модулей. Нами были рассчитаны удельная весовая и удельная объемная энергия электродных модулей ЛСЯ с отрицательными электродами на основе различных активных материалов. Так как в аккумуляторных ячейках используются двусторонние электроды, мы при расчетах энергетических характеристик электродных модулей толщину и массу токовых коллекторов отрицательного и положительного электродов принимали равной половине измеренных величин. Принятые при расчетах энергетических характеристик параметры компонентов ЛСЯ приведены в табл. 1.
Таблица 1.
Параметры компонентов, принятые при расчетах энергетических характеристик электродных модулей литий-серных ячеек
Параметр | Значение |
---|---|
Положительный электрод | |
Содержание, мас. % | |
Серы | 70 |
Токопроводящей добавки | 10 |
Связующего | 20 |
Поверхностная емкость, мА ч/см2 | 3 |
Пористость электродного слоя, % | 25 |
Глубина конверсии серы, % | 75 |
Толщина токового коллектора (Al), мкм | 16 |
Масса токового коллектора (Al), г/см2 | 0.0042 |
Сепаратор | |
Толщина, мкм | 20 |
Пористость, % | 50 |
Масса, г/см2 | 0.0012 |
Материал | Полипропилен |
Электролит | |
Количество, мкл/(мА ч (S)) | 2 |
Плотность, г/см3 | 1.32 |
Отрицательные электроды | |
Толщина литиевой фольги, мкм | 60 |
Содержание, мас. % | |
Углерода (активный компонент) | 94 |
Токопроводящей добавки | 1 |
Связующего | 5 |
Поверхностная емкость, мА ч/см2 | 3.3 |
Пористость электродного слоя, % | 25 |
Толщина токового коллектора (Cu), мкм | 14 |
Масса токового коллектора (Cu), г/см2 | 0.012 |
Расчетные величины весовой и объемной удельных энергий электродных модулей ЛСЯ с отрицательными электродами на основе различных активных материалов суммированы в табл. 2. Рассчитанные величины весовой удельной энергии электродных модулей ЛСЯ с отрицательными электродами на основе графита и термообработанного нефтяного кокса сопоставимы с удельной энергией литий-ионных ячеек. Замена углеродных электродов на металлический литиевый электрод существенно увеличивает удельную весовую энергию, но при этом удельная объемная энергия изменяется незначительно.
Таблица 2.
Расчетные величины удельной объемной и весовой энергий электродных модулей литий-серных ячеек с отрицательными электродами на основе различных активных материалов
Активный материал отрицательного электрода | Среднее разрядное напряжение, В | Удельная объемная энергия, Вт ч/л | Удельная весовая энергия, Вт ч/кг |
---|---|---|---|
Литий | 2.1 | 453 | 385 |
Графит | 1.9 | 414 | 199 |
НКЭ | 1.7 | 370 | 178 |
ЗАКЛЮЧЕНИЕ
Проведенные исследования показали, что термообработанный нефтяной кокс может быть успешно использован в качестве активного материала отрицательных электродов литий-серных аккумуляторов. Литий-серные ячейки с отрицательными электродами на основе термообработанного нефтяного кокса обладают бóльшей длительностью циклирования, что объясняется более медленной деструкцией компонентов электролитных систем на отрицательном электроде в процессе их циклирования. Применение в литий-серных аккумуляторах отрицательных электродов на основе нефтяного кокса позволяет существенно увеличить длительность циклирования и снизить их стоимость.
Список литературы
Fan, L., Deng, N., Yan, J., Li, Z., Kang, W., and Cheng, B., The recent research status quo and the prospect of electrolytes for lithium sulfur batteries, Chem. Engineering J., 2019, vol. 369, p. 874. https://doi.org/10.1016/j.cej.2019.03.145
Wang, H.C., Cao, X., Liu, W., and Sun, X., Research Progress of the Solid State Lithium-Sulfur Batteries, Front. Energy Res., 2019, no. 112. https://doi.org/10.3389/fenrg.2019.00112
Liang, X., Yun, J., Wang, Y., Xiang, H., Sun, Y., Feng, Y., and Yu, Y., A new high-capacity and safe energy storage system: lithium-ion sulfur batteries, Nanoscale, 2019, vol. 11, no. 19140. https://doi.org/10.1039/c9nr05670j
Li, F., Liu, Q., Hu, J, Feng, Y., He, P., and Ma, J., Recent advances in cathode materials for rechargeable lithium-sulfur batteries, Nanoscale, 2019, vol. 11, no. 15418. https://doi.org/10.1039/c9nr04415a
Zeng, P., Han, Y., Duan, Z., Jia, G., Huang, L., and Chen, Y., A stable graphite electrode in superconcentrated LiTFSI-DME/DOL electrolyte and its application in lithium-sulfur full battery, Mater. Res. Bull., 2017, vol. 95, p. 61. https://doi.org/10.1016/j.materresbull.2017.07.018
Xiong, X., Yan, W., You, C., Zhu, Y., Chen, Y., Fu, L., Zhang, Y., Yu, N., and Wu, Y., Methods to Improve Lithium Metal Anode for Li-S Batteries, Front. Chem., 2019, vol. 7, article 827. https://doi.org/10.3389/fchem.2019.00827
Fu, Y., Su, Y.S., and Manthiram, A., Li2S-Carbon Sandwiched Electrodes with Superior Performance for Lithium-Sulfur Batteries, Adv. Energy Mater., 2014, vol. 4, no. 1300655. https://doi.org/10.1002/aenm.201300655
Wu, Y., Momma, T., Yokoshima, T., Nara, H., and Osaka, T., High performance sulfur graphite full cell for next generation sulfur Li-ion battery, J. Power Sources, 2018, vol. 388, p. 5. https://doi.org/10.1016/j.jpowsour.2018.03.051
Shi, P., Zhou, X., Wang, Y., Liang, X., Sun, Y., Cheng, S., Chen, C., and Xiang, H., Advanced Lithium Ion Sulfur Battery Based on Spontaneous Electrochemical Exfoliation/Lithiation of Graphite in Nonaqueous Electrolytes, ACS Appl. Energy Mater., 2019, vol. 2, no. 5, p. 3798. https://doi.org/10.1021/acsaem.9b00480
Karaseva, E. and Kolosnitsyn, V., Lithium sulphide battery and method for producing the same, Patent EP 1 867 000 B1, date of publication and mention of the grant of the patent: 05.10.2011 Bulletin 2011/40.
Liu, J., Nara, H., Yokoshima, T., Momma, T., and Osaka, T., Micro-scale Li2S–C composite preparation from Li2SO4 for cathode of lithium ion battery, Electrochim. Acta, 2015, vol. 183, p. 70. https://doi.org/10.1016/j.electacta.2015.07.116
Li, Z., Zhang, S., Zhang, C., Ueno, K., Yasuda, T., Tatara, R., Dokko, K., and Watanabe, M., One-pot pyrolysis of lithium sulfate and graphene nanoplatelet aggregates: in situ formed Li2S/graphene composite for lithium-sulfur batteries, Nanoscale, 2015, vol. 7, p. 14385. https://doi.org/10.1039/c5nr03201f
Ye, F., Noh, H., Lee, J., Lee, H., and Kim, H.-T., Li2S/carbon nanocomposite strips from a low-temperature conversion of Li2SO4 as high-performance lithium-sulfur cathodes, J. Mater. Chem. A, 2018, vol. 6, p. 6617. https://doi.org/10.1039/c8ta00515j
Shi, J., Zhang, J., Zhao, Y., Yan, Z., Hart, N., and Guo, J., Synthesis of Li2S-carbon cathode materials via carbothermic reduction of Li2SO4, Front. Energy Res., 2019, vol. 7, no. 53. https://doi.org/10.3389/fenrg.2019.00053
Карасева, Е.В., Шеина, Л.В., Колосницын, В.С. Синтез сульфида лития карботермическим восстановлением сульфата лития нефтяным коксом. Журн. прикл. химии, 2020. Т. 93. № 12 (в печати) [Karaseva, E.V., Sheina, L.V., and Kolosnitsyn, V.S., Synthesis of lithium sulfide by carbothermic reduction of lithium sulfate with petroleum coke, Russ. J. App. Chem., 2020, vol. 93, no. 12 (in press)].
Wang, C., Cai, W., Li, G., Liu, B., and Li, Z., In-situ synthesis of Li2S-loaded amphiphilic porous carbon and modification of Li2S electrode for long life Li2S battery, ChemElectroChem, 2018, vol. 5, no. 1, p. 112. https://doi.org/10.1002/celc.201700914
Chae, S., Choi, S.-H., Kim, N., Sung, J., and Cho, J., Integration of Graphite and Silicon Anodes for the Commercialization of High-Energy Lithium-Ion Batteries, Angew. Chem. Int. Ed., 2019, vol. 59, no. 1, p. 110. https://doi.org/10.1002/anie.201902085
Borah, R., Hughson, F.R., Johnston, J., and Nann, T., On battery materials and methods, Materials Today Advances, 2020, vol. 6, no. 100046. https://doi.org/10.1016/j.mtadv.2019.100046
Buiel, E. and Dahn, J.R., Li-insertion in hard carbon anode materials for Li-ion batteries, Electrochim. Acta, 1999, vol. 45, no. 1–2, p. 121. https://doi.org/10.1016/S0013-4686(99)00198-X
Väli, R., Jänes, A., Thomberg, T., and Lust, E., Synthesis and characterization of D-glucose derived nanospheric hard carbon negative electrodes for lithium- and sodium-ion batteries, Electrochim. Acta, 2017, vol. 253, p. 536. https://doi.org/10.1016/j.electacta.2017.09.094
Sun, H., He, X., Ren, J., Li, J., Jiang, C., and Wan, C., Hard carbon/lithium composite anode materials for Li-ion batteries, Electrochim. Acta, 2007, vol. 52, no. 13, p. 4312. https://doi.org/10.1016/j.electacta.2006.12.012
Zhang, J., Liu, X., Wang, J., Shi, J., and Shi, Z., Different types of pre-lithiated hard carbon as negative electrode material for lithium-ion capacitors, Electrochim. Acta, 2016, vol. 187, p. 134. https://doi.org/10.1016/j.electacta.2015.11.055
Kim, J.-H., Kim, J.-S., Lim, Y.-G., Lee, J.-G., and Kim, Y.-J., Effect of carbon types on the electrochemical properties of negative electrodes for Li-ion capacitors, J. Power Sources, 2011, vol. 196, no. 23, p. 10490. https://doi.org/10.1016/j.jpowsour.2011.08.081
Gourdin, G., Smith, P.H., Jiang, T., Tran, T.N., and Qu, D., Lithiation of amorphous carbon negative electrode for Li ion capacitor, J. Electroanalyt. Chem., 2013, vol. 688, p. 103. https://doi.org/10.1016/j.jelechem.2012.08.029
Li, B., Zheng, J., Zhang, H., Jin, L., Yang, D., Lv, H., Shen, C., Shellikeri, A., Zheng, Y., Gong, R., Zheng, J.P., and Zhan, C., Electrode materials, electrolytes, and challenges in nonaqueous lithium-ion capacitors, Adv. Mater., 2018, vol. 30, no. 1705670. https://doi.org/10.1002/adma.201705670
Кузьмина, Е.В., Дмитриева, Л.Р., Карасева, Е.В., Колосницын, В.С. О возможности применения метода сорбции красителей для определения удельной поверхности углеродных материалов для литий-серных аккумуляторов. Изв. Уфимского научного центра РАН. 2020, №2, с. 29. [Kuzmina, E.V., Dmitrieva, L.R., Karaseva, E.V., and Kolosnitsyn, V.S., On the possibility of applying the dye sorption method to determine the specific surface area of carbon materials for lithium-sulfur batteries, Izvestiya Ufimskogo Nauchnogo Tsentra RAN, 2020, (in Russian) 2020, no. 2, p. 29.] https://doi.org/10.31040/2222-8349-2020-0-2-29-34]
Kuzmina, E., Karaseva, E., Ivanov, A., and Kolosni-tsyn, V., On the factors affecting aging and self-discharge of lithium–sulfur cells. Effect of positive electrode composition, Energy Technol., 2019, no. 1900134, https://doi.org/10.1002/ente.201900134
Мочалов, С.Э., Антипин, А.В., Нургалиев, А.Р., Колосницын, В.С. Многоканальный потенциостат-гальваностат для циклических испытаний аккумуляторов и электрохимических ячеек. Электрохим. энергетика. 2015. Т. 15. № 1. С. 45. [Mochalov, S.E., Antipin, A.V., Nurgaliev, A.R., and Kolosnitsyn, V.S., Multichannel potentiostat-galvanostat for cycling of batteries and electrochemical cells, Elektrokhim. energetika (in Russian), 2015, no. 1(15), p. 45.]
Свид. 2019611773 РФ. Свидетельство об официальной регистрации программы для ЭВМ. “ElChemLab, Data Analyzer” / Д. В. Колосницын; правообладатель УФИЦ РАН (RU). Опубл. 04.02.2019, Реестр программ для ЭВМ. 1 с. [2019611773 RF. ElChemLab, Data Analyzer” / D.V. Kolosnitsyn; UFRC RAS (RU). – published. 07.02.2019.]
Колосницын, Д.В., Кузьмина, Е.В., Карасева, Е.В. Автоматизация обработки данных электрохимических исследований аккумуляторных ячеек. Электрохим. энергетика. 2019. Т. 19. № 4. С. 186. [Kolosnitsyn, D.V., Kuzmina E.V., and Karaseva, E.V., Data processing automatization of electrochemical studies of battery cells, Elektrokhim. energetika (in Russian), 2019, no. 19(4), p. 186. https://doi.org/10.18500/1608-4039-2019-19-4-186-197]
Свид. 2019611983 РФ. Свидетельство об официальной регистрации программы для ЭВМ. “ElChemLab, Battery Designer” / Д.В. Колосницын; правообладатель УФИЦ РАН (RU) – опубл. 07.02.2019, Реестр программ для ЭВМ – 1 с. [2019611983 RF. “ElChemLab, Battery Designer” / D.V. Kolosnitsyn; UFRC RAS (RU) – published. 07.02.2019]
Kuzmina, E., Chudova, N., Prosochkina, T., Karaseva, E., and Kolosnitsyn, V., Electrochemical Properties of Petroleum Coke As Active Material of Negative Electrode in Lithium Batteries, Meeting abstract of 235th ECS Meeting, 26.05.2019-30.05.2019, Dallas, Texas, Abstract MA2019-01 236 http://ma.ecsdl.org/content/MA2019-01/2/236.abstract?sid=9872a 494-ecdb-4c30-91f2-8860f1c27031.
Cuesta, A., Dhamelincourt, P., Laureyns, J., Martinez-Alonso, A., and Tascón, J.M.D., Raman microprobe studies on carbon materials, Carbon, 1994, vol. 32, no. 8, p. 1523. https://doi.org/10.1016/0008-6223(94)90148-1
Тихомиров, С., Кимстач, Т. Спектроскопия комбинационного рассеяния – перспективный метод исследования углеродных наноматериалов. Аналитика. 2011. Т. 1. № 1. С. 28. [Tikhomirov, S. and Kimstach, T., Spectroscopy of Raman scattering is a promising method for the investigation of carbon nanomaterials, Analitika (in Russian), 2011, no. 1(1), p. 28.]
Хабибуллина, И.А., Ситников, Н.Н., Казаков, В.А., Сигалаев, С.К. Синхронный термический анализ и спектроскопия комбинационного рассеяния света как взаимодополняющие методы диагностики аллотропных форм углерода. Изв. вузов. Химия и хим. технология. 2016. Т. 59. № 8. С. 34. [Khabibullina, I.A., Sitnikov, N.N., Kazakov, V.A., and Sigalaev, S.K., Simultaneous thermal analysis and raman spectroscopy as complementary methods of diagnostics of carbon allotropic forms, Izv. Vyssh. Uchebn. Zaved. Khim. Khim. Tekhnol. (in Russian), 2016, no. 59(8), p. 34.]
Пантелеева, М.В. Описание спектроскопии комбинационного рассеяния света в разупорядоченной структуре углерода. Образование и наука в России и за рубежом. 2018. Т. 42. № 7. С. 130. [Panteleeva, M.V., Description of Raman spectroscopy of light scattering in disordered carbon structure, Obrasovanie i nauka v rossii i za rubezhom (in Russian), 2018, no. 42(7), p. 130.]
Kim, J.-H., Kim, J.-S., Lim, Y.-G., Lee, J.-G., and Kim, Y.-J., Effect of carbon types on the electrochemical properties of negative electrodes for Li-ion capacitors, J. Power Sources, 2011, vol. 196, p. 10490. https://doi.org/10.1016/j.jpowsour.2011.08.081
Юан, М., Лиу, В., Жу, Ё., Су, Ё. Электрохимические эксплуатационные характеристики литий-ионных конденсаторов с различными типами отрицательных электродов. Электрохимия. 2014. Т. 50. С. 662. https://doi.org/10.7868/S042485701402008X [Yuan, M., Liu, W., Zhu, Y., and Xu, Y., Electrochemical Performance of Lithium Ion Capacitors with Different Types of Negative Electrodes, Russ. J. Eleсtrochem., 2014, vol. 50, p. 594. https://doi.org/10.1134/S1023193514020074]
Дубасова, В.С., Фиалков, А.С., Каневский, Л.С., Михайлова, В.А., Николенко, А.Ф., Пономарева, Т.А., Зайчиков, С.Г., Бавер, А.И., Смирнова, Т.Ю. Зависимости электрохимических характеристик отрицательного электрода литий-ионного аккумулятора от структурных параметров и поверхностных свойств углеродного материала. Электрохимия. 2004. Т. 40. С. 415. [Dubasova, V.S., Fialkov, A.S., Kanevsky, L.S., Mikhailova, V.A., Nikolenko, A.F., Ponomareva, T.A., Zaichikov, S.G., Baver, A.I., and Smirnova, T.Yu., Electrochemical Characteristics of the Negative Electrode in Lithium-Ion Batteries: Effect of Structure and Surface Properties of the Carbon Material, Russ. J. Eleсtrochem., 2004, vol. 40, p. 369. https://doi.org/10.1023/B:RUEL.0000023926.93541.1a]
Дополнительные материалы отсутствуют.
Инструменты
Электрохимия