Журнал физической химии, 2020, T. 94, № 3, стр. 364-370
Физико-химическая механика синтеза борсодержащих композиционных порошков
А. И. Малкин a, *, В. А. Клюев a, Д. А. Попов a, А. А. Рязанцева a, В. И. Савенко a
a Российская академия наук, Институт физической химии и электрохимии им. А.Н. Фрумкина
Москва, Россия
* E-mail: mlkn@list.ru
Поступила в редакцию 02.08.2019
После доработки 02.08.2019
Принята к публикации 03.09.2019
Аннотация
Методом механического легирования синтезированы композиционные порошки СВС-составов “Al–2В” и “Ti–2B”. Исследована эволюция структурно-морфологических характеристик и фракционного состава порошков в процессе механической обработки. Проведен сравнительный анализ кинетики формирования композиционных порошков, обсуждается связь кинетики со свойствами металлического компонента.
Композиционные порошки “металл–бор” представляют значительный интерес для множества практических приложений. Порошки такого состава используются в СВС-технологиях синтеза борсодержащих соединений для изготовления различных конструкционных и функциональных композиционных материалов [1]. Перспективным направлением является применение борсодержащих композиционных порошков в энергетических конденсированных системах [2].
Простой и технологичный метод изготовления таких композиционных порошков основан на совместной механической обработке компонентов в охлаждаемых шаровых мельницах-активаторах [3–5]. Характеристики конечного продукта определяются технологическим режимом – интенсивностью и продолжительностью обработки, интенсивностью охлаждения, составом размольной среды, размерами частиц и физико-механическими свойствами исходных порошков.
В зависимости от механических свойств и размеров частиц исходной смеси могут реализовываться различные сценарии формирования композиционных частиц. Рассматриваемые в настоящей работе системы в исходном состоянии содержат относительно грубодисперсные порошки пластичных металлов и высокодисперсный порошок бора, отличающегося высокой твердостью и прочностью.
Качественная картина синтеза композиционных порошков “металл–бор” является универсальной для процессов механического легирования, используемых для изготовления дисперсно-упрочненных композиционных материалов [5, 6]. В ходе совместной обработки происходит интенсивное внедрение твердых субмикронных частиц бора в приповерхностные слои относительно крупных и пластичных частиц металла и, в дальнейшем, композиционных частиц. Одновременно протекают два конкурирующих процесса – разрушение и “холодная сварка” частиц. Следствием чередования этих процессов является гомогенизация состава частиц с увеличением продолжительности обработки. В итоге формируется композиционный порошок с развитой межфазной поверхностью между компонентами. Многократное интенсивное механическое воздействие на порошковую смесь приводит к формированию высокодефектной, далекой от равновесия атомной структуры композиционных частиц.
Исследование влияния механоактивации на структуру и реакционную способность представляет собой быстро развивающееся направление физической химии энергетических конденсированных систем. Обзор работ в этом направлении представлен в [1]. Основная проблема состоит в установлении зависимости “технология–структура–свойства” механоактивированных энергетических материалов.
В первую очередь необходимо сформулировать детальный количественный сценарий процесса формирования композиционного порошка. Детализация этого процесса и сравнение количественных характеристик эволюции состава и структуры композиционного порошка для отличающихся по физико-механическим свойствам металлов необходима для разработки теоретических основ технологии синтеза. С практической точки зрения значительный интерес представляют борсодержащие системы, в частности, композиции состава “алюминий–бор” и “титан–бор”, отличающиеся высокой теплотой сгорания в окислительных средах. Механоактивация таких систем дает принципиальную возможность управления как скоростью реакции между компонентами, так и скоростью горения композиционных частиц. Результаты исследований влияния механоактивации на структуру и свойства композиций “титан–бор” приведены в [1, 7, 8]. В работах [5, 8, 9] представлены результаты исследований структуры механоактивированных порошков “алюминий–бор” с различным соотношением компонентов и свойств компактных материалов на их основе. Однако имеющихся в настоящее время данных недостаточно ни для выбора рациональной технологии синтеза, ни для выявления взаимосвязи процессов, ответственных за формирование композиционных порошков этого класса. По этим причинам представляется целесообразным исследование кинетики формирования композиционных порошков и оценка влияния физико-механических свойств металлического компонента на процесс синтеза. Ниже представлены результаты сравнительных исследований влияния продолжительности обработки на структуру, морфологию и фракционный состав композиционных порошков “Al–2В” и “Ti–2B”.
ЭКСПЕРИМЕНТАЛЬНАЯ ЧАСТЬ
В экспериментах использовались порошки алюминия марки АСД-1, титана марки ПТС-1 и аморфного бора марки Б-99В. Обработка порошковых смесей осуществлялась в лабораторной планетарно-центробежной мельнице-активаторе с водяным охлаждением АГО-2У при загрузке смеси 10 г, шаровой загрузке – 100 г шаров диаметром 6 мм из сплава ШХ-15, скорости вращения барабанов 1061.5 об./мин. Продолжительность обработки составляла от 3 до 21 мин. В качестве размольной среды использовался химически чистый гексан.
Структурно-морфологические исследования проводились методами электронной микроскопии, рентгеноспектрального микроанализа и рентгеновской дифрактометрии. Использовался электронный микроскоп JSM-6460LA с приставкой энергодисперсионного микроанализа EDAX. Энергия первичного электронного пучка составляла 15 кэВ, ток на образце – 1 нА, угол между поверхностью образца и детектором – 40°. При определении объемной концентрации элементов использовалась программа ZAF-коррекции. Исследованию подвергались образцы порошковых проб двух типов: таблетки толщиной около 1 мм, изготовленные на ручном прессе, и россыпь частиц на проводящей липкой ленте.
Для установления характера распределения частиц бора в объеме композиционных частиц и количественной оценки содержания бора в них изготавливались специальные образцы: композиционные порошки смешивались с порошком полимера, смесь прессовалась и отверждалась при повышенной температуре, после чего проводилась шлифовка и травление шлифов потоком ионов аргона.
Дифрактометрические измерения проводились на рентгеновском дифрактометре EMPYREAN (CuKα-излучение) в диапазоне углов 5–140°. При расчетах учитывались две длины волны 1.5406 и 1.5444 с соотношением интенсивностей в спектре 2 : 1. Для всех порошкограмм проводилось полнопрофильное уточнение методом Ритвельда.
Фракционный состав порошков определялся на жидкофазном лазерном дифрактометрическом анализаторе высокого разрешения Microtrac S3500. Для устранения слабосвязанных агрегатов порошковые пробы подвергались ультразвуковому диспергированию в течение 3 мин.
Результаты рентгеноспектрального микроанализа прессованных образцов в зависимости от продолжительности обработки в гексане представлены на рис. 1, 2. Необходимо пояснить, что полученные на прессованных образцах формальные значения относительного содержания компонентов ни в коей мере не соответствуют реальным, составляющим, вне зависимости от времени обработки, приблизительно “55% Al – 45% В” и “69% Ti – 31% В”. Приведенные зависимости в действительности отражают кинетику внедрения бора в металл и гомогенизацию состава композиционного порошка. На начальной стадии обработки обе смеси содержат большое количество свободного бора, порошок которого обладает низкой насыпной плотностью, занимает большой относительный объем и обладает значительно меньшим коэффициентом поглощения рентгеновского излучения, чем алюминий и титан. В результате кажущееся общее содержание бора значительно превышает реальное. С увеличением продолжительности обработки содержание свободного бора снижается, так что содержание бора в объеме композиционных частиц приближается к предельной величине.
Рис. 1.
Условное относительное содержание элементов (С) в прессованных образцах композиции “Al–2В” в зависимости от времени обработки (t).
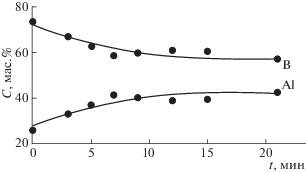
Рис. 2.
Условное относительное содержание элементов в прессованных образцах композиции “Ti–2B” в зависимости от времени обработки.
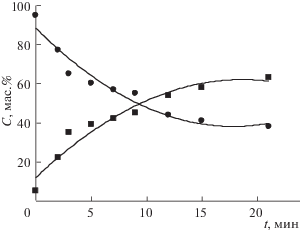
Естественной характеристикой кинетики гомогенизации является скорость изменения кажущегося соотношения компонентов. При этом необходимо иметь в виду, что даже при достижении предельного насыщения композиционных частиц бором значения концентраций, полученные по данным рентгеноспектрального микроанализа прессованных образцов, могут существенно отличаться от реальных [10].
Из сравнения зависимостей рис. 1 и 2 видно, что скорости гомогенизации в исследуемых системах значительно отличаются друг от друга. В системе “Al–2В” кажущееся соотношение компонентов стабилизируется при продолжительности обработки 7 мин и в дальнейшем практически не меняется. В системе “Ti–2В” тенденция возрастания кажущегося содержания титана сохраняется вплоть до максимальной продолжительности 21 мин, хотя скорость процесса гомогенизации с увеличением продолжительности обработки становится значительно меньше, чем на начальной стадии.
Результаты дифрактометрических исследований свидетельствуют об отсутствии в составе композиционных порошков заметного количества кристаллических боридов титана и алюминия. Тем не менее, нельзя исключить возможность незначительного содержания таких фаз в аморфизованном состоянии. Отметим также, что слабый узкий пик при угле 2θ = 28.10°, наблюдавшийся на порошкограммах исходных смесей и отвечающий кристаллическому гидроксиду бора, полностью исчезает уже при минимальной продолжительности обработки 3 мин.
При обработке порошковой смеси “Ti–2B” обнаружено появление небольшого количества двух кубических фаз – X-фазы, близкой по структуре к Zr0.4Ti1.0 и Y-фазы, близкой к структуре С0.3N0.7Ti. Возникновение X-фазы зафиксировано при времени обработки более 5 мин, Y-фаза появляется после 9 мин обработки. Содержание X-фазы не изменяется с увеличением продолжительности, содержание Y-фазы монотонно возрастает; при обработке в течение 21 мин объемная доля примесных фаз становится одинаковой. При этом суммарное содержание этих фаз не превышает несколько объемных процентов. Причина появления и реальный состав кубических фаз нуждается в уточнении. Возможно, X-фаза появляется в результате распада твердого раствора примесей, изначально содержащихся в титане, а появление Y-фазы обусловлено взаимодействием титана с компонентами размольной среды.
Частицы бора, как исходного, так и в составе композиционных порошков, находятся в рентгеноаморфном состоянии. Зависимости основных характеристик микроструктуры алюминиевой и титановой составляющих композиционных порошков от продолжительности обработки в гексане представлены в таблице 1. На начальной стадии обработки размеры области когерентного рассеяния (ОКР) и величина постоянной решетки алюминиевой матрицы резко снижаются; микродеформации второго рода, характеризующие напряжения в субзернах и блоках мозаики, при этом возрастают. С увеличением продолжительности изменение параметров микроструктуры приобретает немонотонный характер.
Таблица 1.
Размеры ОКР и постоянные решетки металлического компонента систем “Al–2В” и “Ti–2B”
t, мин | Al | Ti | |||
---|---|---|---|---|---|
Dокр, нм | а, Å | Dокр, нм | а, Å | с, Å | |
0 | 115 | 4.0494(1) | 112 | 2.950(1) | 4.683(1) |
3 | 108.5 | 4.0487(4) | 26 | 2.951(1) | 4.686(1) |
5 | 39.5 | 4.0451(2) | 23 | 2.950(1) | 4.685(1) |
7 | 39.2 | 4.0411(2) | 23 | 2.950(1) | 4.689(2) |
9 | 61.9 | 4.0475(5) | 18 | 2.949(2) | 4.689(2) |
12 | 84.8 | 4.0474(5) | 16 | 2.948(3) | 4.693(2) |
15 | 50.2 | 4.0470(6) | 15 | 2.950(7) | 4.699(7) |
21 | 43.4 | 4.0482(4) | 10 | 2.948(12) | 4.708(11) |
Иное поведение демонстрируют параметры микроструктуры титана. С увеличением длительности обработки размер ОКР титановой матрицы монотонно снижается, достигая величины около 10 нм при максимальной длительности обработки. Параметр а ГПУ-решетки титана остается практически постоянным, тогда как параметр с и объем элементарной ячейки значительно возрастают.
Характер эволюции фракционного состава смесей “Al–2В” и “Ti–2B” также существенно различается. По мере увеличения продолжительности обработки изначально бимодальные распределения, обусловленные большим различием в размерах частиц бора и титана и алюминия, трансформируются в одномодальные. Субмикронная фракция, содержащая преимущественно свободный, не внедренный в металлы бор и составляющая в исходной смеси около 5% общего объема частиц, практически полностью исчезает при продолжительности обработки более 7 мин. Однако в порошковой системе “Al–2В” появляется заметное количество крупных частиц, отсутствовавших в исходной смеси, тогда как в системе “Ti–2B” верхняя граница распределения сдвигается влево – размер частиц наиболее крупной фракции снижается. Кинетику изменения фракционного состава иллюстрируют представленные на рис. 3 основные статистические характеристики порошковых систем в зависимости от времени обработки. Как видно из приведенных зависимостей, средние размеры частиц “Al–2В” и медиана распределения относительного объема наиболее быстро возрастают на начальной стадии механоактивации, при продолжительности обработки 3–7 мин. С увеличением продолжительности процесс укрупнения тормозится и изменение основных статистических параметров фракционного состава становится немонотонным. В системе “Ti–2B”, напротив, монотонное снижение среднего размера частиц и медианы распределения имеет место вплоть до максимальной продолжительности обработки. Зависимости удельной площади поверхности порошков, вычисленные по модели сферических частиц, представлены на рис. 4, 5.
Рис. 3.
Зависимости среднеобъемного размера частиц и медианы распределения относительного объема от времени обработки: 1, 2 – средний размер и медиана в композиции “Al–2В”; 3, 4 – средний размер и медиана в композиции “Ti–2B”.
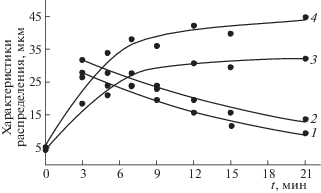
В процессе обработки морфология частиц обеих систем претерпевает значительные изменения. При продолжительности обработки 3–7 мин значительную объемную долю порошковой смеси “Al–2В” составляют частицы анизометричной пластинчатой формы. С увеличением продолжительности доля таких частиц резко снижается. При обработке в течение 9 мин и более основной объем порошковой системы представлен изометричными частицами с остроугольным габитусом.
В композиционных порошках “Ti–2B” основную массу составляют округлые изометричные частицы неправильной формы, хотя небольшая доля относительно крупных пластинчатых частиц сохраняется при всех временах обработки. В отличии от системы “Al–2В” частицы имеют развитый микрорельеф с характерным масштабом около 1 мкм. Съемки в собственном излучении компонентов свидетельствуют о высокой концентрации частиц бора в поверхностном слое композиционных частиц.
ОБСУЖДЕНИЕ РЕЗУЛЬТАТОВ
Полученные экспериментальные данные позволяют проследить эволюцию структурно-морфологических характеристик композиционных порошков в процессе механической обработки. Ясно, что формирование внутренней структуры и фракционного состава порошков является результатом нескольких взаимозависимых процессов, соотношение скоростей которых существенно зависит от физико-механических характеристик металлического компонента. Изменения компонентного состава и параметров блочной структуры обусловлено внедрением высокодисперсных частиц бора в металл и конкуренцией процессов фрагментации зерен и динамической рекристаллизации матричного металла. Изменение фракционного состава определяется конкурирующими процессами разрушения частиц и их агрегации за счет “холодной сварки”. Оценить влияние свойств металлического компонента на относительную интенсивность перечисленных процессов можно на основе сравнительного анализа кинетики формирования композиционных порошков “Al–2В” и “Ti–2B”.
На начальной стадии обработки смеси “Al–2В”, при продолжительности обработки 3–7 мин, преобладает укрупнение частиц за счет внедрения высокодисперсного бора в алюминий и “холодной сварки”. Плотность распределения относительного объема по размеру частиц сдвигается вправо. С возрастанием продолжительности и увеличением доли крупных фракций процесс укрупнения, как видно из рис. 3, тормозится. Стабилизация содержания бора в объеме композиционных частиц и основных статистических характеристик фракционного состава происходит практически одновременно. Морфология частиц композиционного порошка свидетельствует о квазихрупком характере разрушения. Сравнение морфологии механоактивированных частиц чистого алюминия и композиционного порошка позволяет сделать вывод, что причина заключается в насыщении композиционных частиц бором.
Эволюция блочной структуры алюминиевой составляющей начинается с резкого снижения размеров ОКР. Снижение размера блоков сопряжено с появлением в объеме кристаллитов больших сжимающих напряжений, проявляющихся в снижении постоянной решетки. Максимум сжимающих напряжений реализуется при продолжительности 7 мин и минимальном размере ОКР. Оценка максимального напряжения в предположении, что кристаллиты находятся в состоянии равномерного всестороннего сжатия, дает величину около 380 МПа. Соответствующая энергия упругой деформации составляет около 0.32 Дж/г. На стадии немонотонного изменения параметров структуры, при продолжительности обработки 9–21 мин, напряжения изменяются в интервале 50–100 МПа, что отвечает удельной энергии упругой деформации 0.005–0.020 Дж/г.
При обработке смесей “Ti–2B” происходит монотонное снижение размера частиц. Среднеобъемный размер уменьшается от 32 мкм в исходной смеси до 14 мкм при продолжительности обработки 21 мин; медиана распределения относительного объема и децильный показатель Д90 снижаются соответственно с 30 и 60 мкм до 10 и 28 мкм. Морфология композиционных частиц свидетельствует о преимущественно вязком характере разрушения. При этом крупная фракция, составляющая около 10% от общего объема содержит, главным образом, анизометричные частицы пластинчатой формы. При времени обработки более 9–12 мин содержание свободного бора в системе, как показывает седиментационное выделение и рентгеноспектральный микроанализ мелкой фракции, мало. Однако распределение частиц бора в объеме композиционных частиц не является однородным – поверхностные слои переобогащены бором.
Изменение блочной структуры титана, в отличие от алюминия, сопровождается возникновением больших по величине растягивающих напряжений. Оценки в рамках теории упругости по данным таблицы 1 показывают, что максимальное напряжение, направленное по гексагональной оси, возрастает от 120 МПа при продолжительности обработки 7–9 мин до 560 и 870 МПа при обработке в течение 15 и 21 мин. Энергия упругой деформации увеличивается соответственно от 0.04 Дж/г до 0.27 и 0.66 Дж/г.
В избыточную свободную энергию композиционного порошка вносят вклад также дефекты в объеме кристаллитов, межфазные и межкристаллитные границы. Вкладом дефектов в объеме наноразмерных кристаллитов обычно можно пренебречь, поскольку высокие напряжения в процессе формирования блочной структуры приводят к выдавливанию подвижных дефектов в границы.
Для оценки удельной энергии межфазных границ можно, в пренебрежении адгезией, использовать величину суммы поверхностных энергий компонентов. При среднем размере частиц бора 0.5 мкм, что согласуется с данными электронной микроскопии, это приводит к величинам порядка 5–8 Дж/г для обеих систем. При малом содержании свободного бора в системе вклад энергии межфазных границ должен быть практически постоянным.
Полученные экспериментальные данные не позволяют дать непосредственную оценку свободной энергии межкристаллитных границ. Можно, однако, оценить величину удельной площади границ. В системе “Al–2В” удельная площадь поверхности межкристаллитных границ, достигающая максимума в 30 м2/г при обработке продолжительностью 7 мин, принимает значения от 14 м2/г при 12 мин и вновь возрастает до 28 м2/г при 21 мин. Начальная стадия завершается формированием предельно измельченной блочной структуры алюминиевого компонента. В дальнейшем площадь границ изменяется немонотонно. В системе “Ti–2B” удельная площадь межкристаллитных границ возрастает от 37 м2/г при семиминутной обработке и до 53 и 85 м2/г при обработке продолжительностью 12 и 21 мин. Используя типичные значения для энергии границ зерен в алюминии и титане, полученные в рамках модели [11], можно полагать, что вклад границ в избыточную энергию композиционных порошков не превышает 20–25 Дж/г для композиции “Al–2В” и 50–60 Дж/г для “Ti–2B”.
Приведенные оценки не могут претендовать на более или менее точное количественное описание эволюции структуры и энергетических характеристик композиционных частиц. Они, однако, помогают прояснить причины и взаимосвязь процессов, в результате которых формируется внутренняя структура частиц и фракционный состав композиционного порошка.
Хорошо известно, что интенсивность процесса “холодной сварки” определяется, при прочих равных условиях, пластичностью металлического компонента [5]. Укрупнение частиц смеси “Al–2В” на начальной стадии обработки объясняется низкой величиной предела текучести алюминия. Однако повышение содержания бора в композиционных частицах влечет за собой повышение предела текучести – дисперсионное упрочнение. С другой стороны, повышение содержания бора должно приводить к снижению предела прочности композиционного материала из-за низкой прочности адгезионных контактов между компонентами. В итоге процессы разрушения и “холодной сварки” уравновешиваются. Из полученных результатов следует, что это происходит при содержании бора, близком к предельному.
Предел текучести титана на порядок выше, чем у алюминия. По этой причине интенсивность процесса “холодной сварки” в системе “Ti–2B” относительно мала. Внедрение частиц бора приводит к дальнейшему снижению роли “холодной сварки”. В результате не только фракционный состав, но и внутренняя структура композиционных частиц “Ti–2B” и “Al–2В” оказываются существенно различными. Как следует из данных рентгеноспектрального микроанализа шлифованных образцов, содержание бора в центральной зоне и на периферии частиц “Al–2В” приблизительно одинаково, хотя и не является равномерным. В частицах “Ti–2B”, напротив, содержание бора в приповерхностных слоях значительно превышает среднее. Различие в характере эволюции блочной структуры также объясняется высокой пластичностью алюминия по сравнению с титаном. В системе “Al–2В” установление динамического равновесия между процессами фрагментации и рекристаллизации происходит при относительно небольших временах обработки. В дальнейшем изменение размера ОКР и внутренних напряжений приобретает осцилляторный характер с периодом не более 3 мин. При этом небольшие, но значимые осцилляции параметров фракционного состава коррелируют с изменением параметров блочной структуры. По-видимому, это обусловлено зависимостью предела текучести алюминия от параметров блочной структуры. В системе “Ti–2B” релаксационные процессы являются сравнительно медленными и не препятствуют измельчению блоков вплоть до максимальной продолжительности обработки 21 мин.
Что касается энергетических характеристик, то полная избыточная энергия порошка многократно меньше теплоты реакции между компонентами и не может играть заметной роли в энергетическом балансе СВС-превращения. Однако величина избыточной энергии дефектной структуры является показателем повышения химической активности и изменения теплофизических характеристик металлической компоненты.
Таким образом, основным результатом работы является определение количественных закономерностей формирования структурно-морфологических характеристик и фракционного состава композиционных порошков “Al–2В” и “Ti–2B”. Установлено, что внутренняя структура композиционных частиц исследованных систем и кинетика ее формирования существенно различны, что объясняется различием в механическом поведении металлических компонентов. Соотношение скоростей основных процессов, определяющих эволюцию порошков, контролируется степенью насыщения композиционных частиц бором. В системе “Al–2В” насыщение приводит к резкому падению интенсивности “холодной сварки”, стабилизации фракционного состава и осцилляционному поведению параметров блочной структуры вследствие установления динамического равновесия между процессами фрагментации блоков и рекристаллизации. В системе “Ti–2B”, отличающейся сравнительно высоким пределом текучести, происходит монотонное измельчение как самих композиционных частиц, так и их блочной структуры.
Авторы выражают благодарность А.Д. Алиеву и А.А. Ширяеву за проведение электронно-микроскопических и дифрактометрических исследований. Эксперименты выполнены на оборудовании ЦКП ФМИ ИФХЭ РАН.
Список литературы
Рогачев А.С., Мукасьян А.С. Горение для синтеза материалов: введение в структурную макрокинетику. М.: Физматлит, 2013.
Мельников В.Э. Современная пиротехника. М.: 2014. 480 с.
Gilman P.S., Benjamin J.S. //Ann. Rev. Mater. Sci. 1983. V. 13. P. 279.
Gilman P.S., Nix W.D. // Met. Trans. A. 1983.V. 12. № 5. P. 813.
Кузьмич Ю.В., Колесникова И.Г., Серба В.И., Фрейдин Б.М. Механическое легирование. М.: Наука, 2005.
Шелимов К.Б., Бутягин П.Ю. // Докл. АН. 1991. Т. 316. № 6. С. 1439
Бутягин П.Ю. // Там же. 1993. Т. 331. № 3. С. 311
Фрейдин Б.М., Кузьмин Ю.В., Лейф В.Э. и др. // Металлы. 1991. № 6. С. 40.
Фрейдин Б.М., Кузьмин Ю.В., Серба В.И. и др. // Вопр. матер. 2002. № 1 (29). С. 415.
Гиммельфарб Ф.А. Рентгеноспектральный микроанализ слоистых материалов. М.: Металлургия, 1986. 152 с.
Чувильдеев В.Н. Неравновесные границы зерен в металлах. Теория и приложения. М.: Физматлит, 2004.
Дополнительные материалы отсутствуют.
Инструменты
Журнал физической химии