Журнал физической химии, 2021, T. 95, № 10, стр. 1501-1507
Влияние состава катализатора и условий процесса на эффективность феррита кобальта в разложении оксида азота (I)
К. О. Денисова a, А. А. Ильин a, *, А. П. Ильин a, Ю. Н. Сахарова a
a Ивановский государственный химико-технологический университет
Иваново, Россия
* E-mail: ilyin@isuct.ru
Поступила в редакцию 08.02.2021
После доработки 17.02.2021
Принята к публикации 19.02.2021
Аннотация
Исследован процесс получения катализатора разложения оксида азота (I) путем механохимического синтеза феррита кобальта из смеси оксалатов и железа. Установлено, что применение предварительной механохимической активации исходных компонентов в ролико-кольцевой вибрационной мельнице позволяет снизить температуру синтеза феррита кобальта до 300°С и, как следствие, получить продукт с более развитой удельной поверхностью и пористой структурой. Исследованы каталитические свойства феррита кобальта с различным соотношением основных компонентов СоО : Fe2O3 = 0.7–1.3 в интервале температур 100–500°С. Доказано, что при увеличении содержания СоО в составе феррита кобальта до соотношения 1.3 приводит к снижению 50-го % разложения N2O с 420 до 370°С. Выявлено влияние наличия водяного пара, O2, H2 в реакционном технологическом газе, установлено влияние давления и температуры на активность катализатора на основе феррита кобальта в реакции разложения N2O.
Оксид азота (I) практически всегда является сопутствующим продуктом в процессах, связанных с химической переработкой соединений связанного азота и сжигания органического топлива. Он принадлежит к числу мощных парниковых газов из-за его длительного воздействия на атмосферу (110–150 лет). Его влияние на окружающую среду в 310 раз сильнее, чем у СO2 [1, 2].
Возрастающие объемы выбросов N2O вследствие интенсификации химических производств, увеличения количества транспортной техники и шахтных разработок свидетельствуют об актуальности работ по совершенствованию существующих средств защиты атмосферы Земли и воздуха рабочих зон [3].
Одним из источников выбросов оксида азота (I) в атмосферу является производство азотной кислоты. Общий объем производства HNO3 в России превышает 23.7 млн т/год [1]. В данном производстве образование закиси азота возможно по двум химическим маршрутам:
1. В процессе окисления аммиака в каталитическом реакторе оксид азота (I) образуется в качестве нецелевого побочного продукта:
(1)
$4{\text{N}}{{{\text{H}}}_{3}} + 4{{{\text{O}}}_{2}} \to 2{{{\text{N}}}_{{\text{2}}}}{\text{O}} + 6{{{\text{H}}}_{{\text{2}}}}{\text{O}}.$2. В процессе низкотемпературного каталитического восстановления оксидов азота аммиаком; N2O образуется в качестве продуктов реакции:
(2)
$2{\text{N}}{{{\text{H}}}_{3}} + 8{\text{NО}} \to 5{{{\text{N}}}_{{\text{2}}}}{\text{O}} + 3{{{\text{H}}}_{{\text{2}}}}{\text{O}},$(3)
$4{\text{N}}{{{\text{H}}}_{3}} + 3{{{\text{O}}}_{2}} + 4{\text{NO}} \to 4{{{\text{N}}}_{{\text{2}}}}{\text{O}} + 6{{{\text{H}}}_{{\text{2}}}}{\text{O}}.$В промышленности низкотемпературное селективное восстановление оксидов азота в выхлопных газах происходит при температурах 300–330°С с применением алюмованадиевых катализаторов. При этом остаточное содержание оксидов азота в выхлопных газах не должно превышать 0.005%. Кроме оксидов азота в газе содержится водяной пар в количестве 2.5%, кислород около 4% и азот [3]. Каталитическая очистка осуществляется при давлении, соответствующем давлению в абсорбционной колонне, то есть при 0.716 МПа – в схеме УКЛ-7 и 1.11 МПа – в схеме АК-72 [4, 5].
Эффективность процесса каталитического восстановления оксида азота (I) определяется, прежде всего, активностью применяемого катализатора. Наиболее высокой каталитической активностью обладают катализаторы на основе платины, родия и палладия, содержание которых в катализаторах колеблется в пределах 0.1–2 мас. % и железосодержащие цеолиты [6]. Кроме того, было показано, что цеолиты с различной структурой каркаса могут быть использованы для разложения N2O. Цеолиты MFI (ZSM-5), бета (BEA) и феррьерит (FER), выступают в качестве носителей Fe [7]. В работе [7] установлено, что низкомодульный цеолит Fe-FER был наиболее активным, достигая конверсии 85% при 450°C. Катализаторы на основе драгоценных металлов очень дороги, поэтому ведутся изыскания катализаторов, не содержащих благородных металлов. Такие катализаторы, как правило, менее активны, однако целесообразность их использования диктуется широкой доступностью и низкой стоимостью [8].
Известно значительное количество работ, в которых исследуются катализаторы для процесса разложения оксида азота (I) при температуре 700°С и выше [8, 9]. В настоящее время все большее распространение получают катализаторы, полученные на основе оксидов кобальта II–III путем их промотирования добавками Fе2О3, ZnO, CuO, Сr2О3, MgO, Al2O3, NiO [8–13]. В работах [9, 10] было установлено, что железосодержащие цеолиты и смешанные оксиды со структурами шпинели (CoFe2O4/CeO2, Al2O3) и перовскита (La0.8Ce0.2CoO3) являются перспективными катализаторами для низкотемпературного разложения N2O. В работе [12] представлены результаты по соотношению основных компонентов катализатора Co3O4/CeO2. Показано, что добавление оксида кобальта в носитель CeO2 значительно увеличивает степень разложения N2O и понижает температуру процесса. Наилучшие характеристики катализатора для разложения N2O объясняются, главным образом, содержанием активных центров на поверхности Co2+ в сочетании с их повышенным окислительно-восстановительным и текстурным воздействием.
Из представленных исследований катализаторов разложения оксида азота (I) можно выделить оксидные каталитические системы на основе 3d-металлов, как правило, обладающие высокой каталитической активностью, но, при этом имеющих низкую стоимость по сравнению с металлами платиновой группы. Такие катализаторы могут применяться в широкой температурной области в зависимости от их свойств.
Особый интерес представляют оксиды со структурой шпинели, содержащие в своем составе оксиды кобальта (II) и железа (III), проявляющие высокую активность благодаря способности легко образовывать поверхностные кислородные вакансии, которые играют роль активных центров в каталитическом разложении оксида азота (I).
В работах [13, 14] исследована активность железокобальтового катализатора на основе феррита кобальта в процессе разложения оксида азота (I). Было установлено, что введение избытка оксида кобальта в состав катализатора приводит к увеличению концентрации бренстедовских и льюисовских центров, что позволяет понизить температуру конверсии N2O с 540 до 463°C. Полученные экспериментальные данные свидетельствуют об изменении кислотно-основного состояния поверхности железокобальтового катализатора на основе феррита кобальта при его модифицировании оксидом кобальта (III), что способствует развитию представлений о механизме взаимодействия основного катализатора в процессе разложения оксида азота (I). Установлено, что реакционная способность катализаторов по отношению к газам восстановителям определяется в первую очередь активностью окислительно-восстановительного взаимодействия с участием хемосорбированных форм кислорода на поверхности. Следует отметить, что в реальных условиях отходящие газы производств азотной и адипиновой кислот помимо закиси азота содержат кислород и водяной пар [14], которые могут оказывать ингибирующее действие на активность катализатора.
По этой причине в данной работе исследовано влияние технологических факторов на каталитические свойства CoFe2O4 в реакции разложения N2O. Кроме того изучено влияние присутствия кислорода, водяного пара и водорода в реакционном газе на процесс обезвреживания N2O, а также необходимо установить влияние соотношения CoO : Fe2O3 и давления в реакторе на процесс каталитического разложения оксида азота (I).
ЭКСПЕРИМЕНТАЛЬНАЯ ЧАСТЬ
Образцы катализатора приготовлены путем совместной механической активации компонентов – оксалатов железа (FeC2O4 ⋅ 2H2O) и кобальта (CoC2O4 ⋅ 2H2O), взятых с различным соотношением (в пересчете на оксиды CoO : Fe2O3 = = 0.7–1.3). Механическая активация проводилась в ролико-кольцевой вибрационной мельнице VM-4 (Чехия) с частотой колебания 930 мин–1. Амплитуда вибрации в радиальном направлении – 10 мм, в аксиальном – 1 мм; масса мелющих тел –1194 г, масса загружаемого материала – 20.0–40.0 г при достигаемом ускорении 3g.
Метод качественного рентгеновского анализа исследуемых образцов был проведен на дифрактометре ДРОН-3М с использованием CuKα-излучения. Съемку профилей интерференционных линий проводили при ширине щелей 0.5 × 0.5 мм, шаге съемки 0.01° и скорости вращения гониометра 2К/мин по шкале. Размеры областей когерентного рассеяния (Dокр) и среднеквадратичное значение микродеформаций ε были рассчитаны по данным рентгеноструктурного анализа методом ГАФРЛ.
Площадь поверхности, изотермы адсорбции-десорбции и данные по распределению пор по размерам получены на приборе Sorbi-MS, методом БЭТ по низкотемпературной адсорбции – десорбции азота.
Каталитическую активность экспериментальных образцов исследовали на установке проточного типа ПКУ-2. Катализатор фракции 0.25–0.5 мм загружали в стальной реактор. Состав исходной реакционной смеси: N2 – 99%, N2O – 1%. При изучении влияния состава среды на процесс разложения N2O в реакционную газовую смесь дополнительно дозировали: H2 – 1–3%, О2 – 1–3%, Н2О – 1–3%. Объемная скорость газа составляла 20 000 ч–1. Для определения продуктов реакции использовался газовый хроматограф Кристаллюкс – 4000 М. (Экспериментальная часть работы выполнена на приборах Центра коллективного пользования ИГХТУ авторами лично.)
ОБСУЖДЕНИЕ РЕЗУЛЬТАТОВ
Как следует из проведенного аналитического обзора [10, 11] опубликованных работ, наиболее “удобным” объектом изучения механизма формирования структуры феррита кобальта являются оксалаты кобальта и железа. В образцах состава CoO : Fe2O3 образуется феррит кобальта CoFe2O4, который имеет структуру шпинели [12–14].
Для установления фазового состава полученных образцов проводился рентгенофазовый и рентгеноструктурный анализ при различном времени активации оксалатов кобальта и железа. Установлено, что в процессе механической обработки смеси не происходит разложения оксалатов и не образуются новые продукты. Увеличение времени обработки до 45 мин лишь приводит к уменьшению интенсивности характеристических рентгеновских рефлексов.
Методом рентгенофазового анализа установлено, что термическая обработка стехиометрической смеси, подвергнутой механической активации при температуре 300°С, приводит к появлению набора рефлексов, характерных для феррита кобальта с наименьшей интенсивностью пиков, и к кристаллизации без изменений в полученных фазах (рис. 1). С увеличением температуры прокаливания образцов феррита кобальта, его кристаллическая структура становится более совершенной, что находит свое отражение в увеличении интенсивности рентгеновских рефлексов.
Рис. 1.
Рентгенограммы продуктов термической обработки FeC2O4 ⋅ 2H2O и CoFe2O4 ⋅ 2H2O. Температура прокаливания, °C: 300 (а), 350 (б), 400 (в), 450 (г). Индексируемые фазы: 1 – CoFe2O4, 2 – Co3O4.
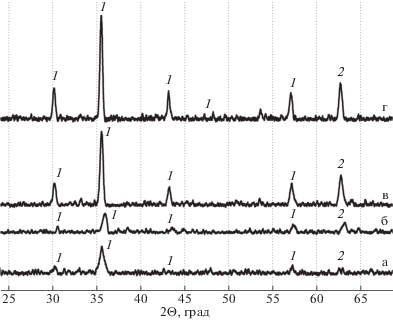
Средний размер кристаллитов, определенный из величин уширений рентгеновских рефлексов, изменялся в диапазоне от 18 нм до 30 нм в зависимости от температуры прокаливания 300–450°С. Из данных, приведенных в таблице 1, следует, что с ростом температуры синтеза совершенство структуры кристаллов растет и уширение дифракционных линии образцов, синтезированных при высоких температурах, обусловлено, главным образом, малым размером кристаллитов (порядка 20–30 нм).
Таблица 1.
Структурно-механические характеристики CoFe2O4
Т, °С | 300 | 350 | 400 | 450 | |
---|---|---|---|---|---|
а, Ǻ | (0.7) | 8.352 | 8.351 | 8.351 | 8.35 |
(1.0) | 8.288 | 8.316 | 8.378 | 8.377 | |
(1.3) | 8.262 | 8.278 | 8.288 | 8.320 | |
Sуд, м2/г | (0.7) | 89.5 | 64.5 | 26.8 | 8.8 |
(1.0) | 117 | 87 | 34.2 | 10.7 | |
(1.3) | 197 | 131 | 118 | 109 | |
Dокр, Ǻ | (0.7) | 286 | 291 | 300 | 324 |
(1.0) | 262 | 262 | 264 | 299 | |
(1.3) | 204 | 208 | 210 | 280 | |
ε, % | (0.7) | 0.38 | 0.32 | 0.22 | 0.18 |
(1.0) | 0.48 | 0.4 | 0.30 | 0.21 | |
(1.3) | 0.72 | 0.65 | 0.60 | 0.62 | |
V, см3/г | (0.7) | 0.138 | 0.117 | 0.042 | 0.017 |
(1.0) | 0.151 | 0.138 | 0.063 | 0.023 | |
(1.3) | 0.215 | 0.178 | 0.091 | 0.037 |
Изменение удельной площади поверхности существенно зависит от формы и размера частиц. В таблице 1 представлена зависимость удельной поверхности и размер кристаллов от соотношения Co : Fe в структуре феррита кобальта. Было замечено резкое уменьшение размера кристаллитов с 260 до 190 нм при увеличении содержания оксида кобальта с 0.7 до 1.3 в составе феррита кобальта. Наблюдаемое уменьшение размера кристаллитов может быть связано с увеличением размеров элементарной ячейки и заменой ионов Fe3+ ионами Co2+, чем меньше размер частиц, тем больше удельная поверхность, которая составляет 197 м2/г для образца с соотношением компонентов CoO : Fe2O3 = 1.3.
Синтезированные материалы имеют развитую поверхность. Следовало предположить наличие у таких образцов адсорбционной и каталитической активности.
Влияние соотношения CoO : Fe2O3 на активность катализатора в реакции разложения N2O
Оксид азота (I) является достаточно стабильным и нереакционноспособным при температуре и давлении окружающей среды [15]. N2O экзотермически разлагается с заметной скоростью только при температуре выше 800°C по реакции:
(4)
${{{\text{N}}}_{{\text{2}}}}{\text{O}} \to {{{\text{N}}}_{2}} + (1{\text{/}}2){{{\text{O}}}_{2}}.$Полного термического разложения N2O практически невозможно достичь без катализатора.
Наибольшее влияние на конверсию закиси азота оказывает температура, при которой происходит процесс. Также степень разложения N2O на азот и кислород зависит от давления в каталитическом реакторе и состава реакционного газа [16].
Как следует из представленных данных (рис. 2), наиболее активным катализатором в реакции разложения N2O является образец, полученный путем прокаливания при 300°С механоактивированной смеси оксалатов кобальта и железа в соотношении CoO : Fe2O3 = 1.3. Степень разложения N2O на данном образце составляет 100% при температуре 463°С. Уменьшение содержания CoO в образцах приводит к значительному снижению каталитической активности, особенно в области температур 300–450°С. Так, CоFe2O4 стехиометрического состава показывает 50%-ную степень разложения оксида азота (I) при 403°C. Уменьшение соотношения CoO : Fe2O3 до 0.7 приводит к увеличению температуры 50%-го разложения N2O до 422°C. Следует отметить, что соотношение СоО : Fe2O3 не оказывает существенного влияния на температуру полного разложения закиси азота, которая составляет 475–490°С при атмосферном давлении. Для сравнения показана активность цеолитного катализатора Fe – ZSM-5, содержащего 0.16 мас.% Fe2O3, имеющего 50%-ную конверсию N2O при 550°C [7]. При равных условиях катализатор на основе цеолита показал более низкие каталитические характеристики для процесса разложения N2O.
Рис. 2.
Влияние соотношения CoO : Fe2O3 на активность катализатора в реакции разложения N2O. I – Fe – ZSM-5 [7], соотношение CoO : Fe2O3: II – 0.7; III – 1; IV – 1.3, tпр.= 300°C; α – степень конверсии.
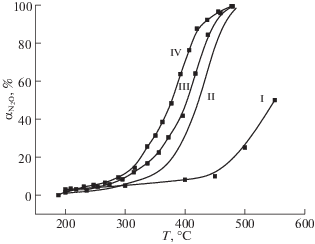
Влияние давления
В производстве азотной кислоты восстановление оксидов азота, содержащихся в выхлопных газах, в разных схемах производства может осуществляться при давлении от 0.4 до 1.1 МПа [4, 17]. Давление – один из основных, наряду с температурой параметров, оказывающий влияние на процесс разложения N2O. По этой причине нами были проведены более детальные исследования влияния давления на процесс разложения закиси азота. На рис. 3 представлена зависимость степени разложения N2O от давления. Показано, что увеличение давление с 0.1 МПа до 1.1 МПа позволяет увеличить степень разложения закиси азота в 6 раз. Так, например при температуре 310°С и давлении 0.1 МПа степень разложения составляет всего лишь 17%, а при 1.1 МПа 100%.
Рис. 3.
Влияние давления на активность катализатора на основе CoFe2O4. Соотношение CoO : Fe2O3 = 1.3; Давление в реакторе Ризб, МПа: 1 – 0.1, 2 – 0.2, 3 – 0.4, 4 – 0.6; 5 – 0.8; 6 – 1.1.
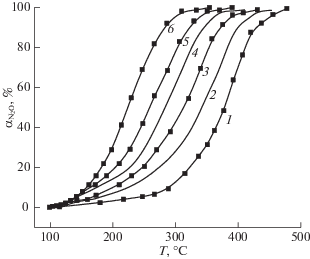
Таким образом увеличение давление позволяет в 6–7 раз снизить объем катализатора и увеличить объемную скорость газа. Увеличение температуры 100-% приращения N2O снижает температуру разложения N2O с 475°С до 311°С.
Влияние водяного пара и кислорода на разложение N2O
Процессы образования азотной кислоты в промышленной практике протекают как при поглощении оксидов азота водой, так и в условиях конденсации паров реакционной воды в нитрозных газах при их охлаждении [17, 18].
В присутствии водяного пара увеличивается температура зажигания катализатора. В результате полное разложение N2O достигается при температуре 320°С при содержании водяного пара в количестве 1%. Увеличение содержания водяного пара в газовой смеси до 3% вызывает более существенное изменение температурного интервала работы катализатора. Так, температура полного разложения N2O составляет более 400°С. При наличии водяного пара в газовой смеси снижение температуры работы катализатора может быть достигнуто, лишь изменением соотношения основных компонентов, при одинаковых условиях работы. В результате увеличения содержания оксида кобальта до соотношения CoO : Fe2O3 = 1.3 температура полного разложения снизилась с 420°С до 360°С (рис. 4).
Рис. 4.
Влияние водяного пара на разложение N2O. Соотношение СоO : Fe2O3 =1.3; Состав газа: 1 – N2 – 99%, N2O – 1%; 2 – N2 – 98%, N2O – 1%, H2O – 1%; 3 – N2 – 96%, N2O – 1% H2O – 3%. Давление в реакторе: 0.9 МПа.
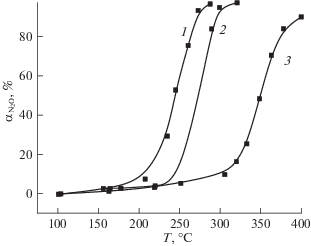
Ингибирование кислородом реакции разложения N2O более интенсивно в оксидах с более низкой теплотой образования [19, 20]. Учитывая, что теплота образования является характеристикой прочности связи металл–кислород, влияние кислорода на разложение N2O рационализировано на основе связи металл–кислород [21–23].
На рис. 5 показана каталитическая активность феррита кобальта составом CoO : Fe2O3 = 1.3 в реакции разложения закиси азота в присутствии кислорода при давлении 0.2 МПа. Процесс рекомбинации кислорода на феррите кобальта с преобладанием CoO типа шпинели происходит намного проще и почти непосредственно следует за разрывом связи O – N2 [24]. Шпинели кобальта более устойчивы к окислению в трехвалентные оксиды так, как обладают поверхностно-окислительно-восстановительным потенциалом пары для оксидных катализаторов [25]. Следует отметить, что активность катализатора восстанавливается при удалении кислорода из исходного газа. Этот результат ясно указывает на то, что ингибирование вызвано обратимой адсорбцией кислорода с активных центров поверхности феррита кобальта. Исследование подтверждает, что существует конкурентная адсорбция между оксидом азота (I) и молекулярным кислородом по центрам адсорбции, доступных на поверхности феррита кобальта.
Рис. 5.
Влияние присутствия кислорода в газовой смеси на процесс разложения N2O. Давление в реакторе Ризб = 0.2 МПа. Соотношение CoO : Fe2O3 = 1.3. Состав исходной газовой смеси: 1 – N2 – 99%, N2O – 1%; 2 – N2 – 98%, N2O – 1%, О2 – 1%; 3 – N2 – 96%, N2O – 1%, О2 – 3%.
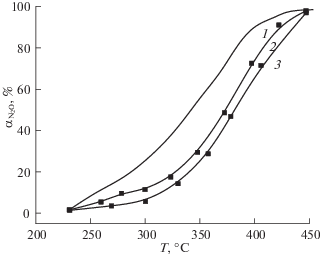
Таким образом, методом механохимического синтеза была приготовлена серия оксидных катализаторов со структурой шпинели соотношением компонентов CoO : Fe2O3 = 0.7–1.3. Показано, что при возрастании содержания оксида кобальта с 0.7 до 1.3 происходит увеличение удельной поверхности образцов с 95 до 197 м2/г и снижение степени кристалличности шпинели, за счет повышения дисперсности первичных частиц и дисперсности. Установлена корреляция между каталитической активностью образцов в реакции разложения закиси азота и количеством содержания оксида кобальта (в пересчете на CoO). Максимальной активностью характеризуется образец CoFe2O4 с соотношением компонентов CoO : Fe2O3 = 1.3, для которого наблюдается снижение температуры процесса разложения N2O на 40–80°С. При предварительной обработке катализатора в He наблюдалась более высокая активность, чем при предварительной обработке в N2O. Выявлено обратимое влияние водяного пара и кислорода на активность катализатора в реакции разложения закиси азота.
Практическая часть работы выполнена в рамках плана работ лаборатории синтеза, исследований и испытания каталитических и адсорбционных систем для процессов переработки углеводородного сырья (созданная при поддержке Минобрнауки РФ на 2012–2022) тема № FZZW-2020-0010) и при стипендиальной поддержке Президента РФ (№ 15493ГУ/2020).
Список литературы
Богачев А.П., Слободчиков А.М., Хомяк В.В. // Ученые заметки ТОГУ. 2017. Т. 8. № 1. C. 92.
Закиров В.А. // Химия и жизнь. 2012. № 4. С. 18.
Исупова Л.А., Иванова Ю.А. // Кинетика и катализ. 2019. Т. 60. № 6. C. 725–740. https://doi.org/10.1134/S0453881119060054
Ильин А.П., Кунин А.В. Производство азотной кислоты. СПб.: Лань, 2013. 256 с.
Денисова К.О., Ильин А.А., Румянцев Р.Н. и др. // Рос. хим. журн. 2017. Т. 61. № 2. С. 46.
Richards N., Nowicka E., James H.C. et al. // Topics in Catalysis. 2018. V. 61. № 18–19. P. 1983. https://doi.org/10.1007/s11244-018-1024-0
Sklenak S., Andrikopoulos P.C., Boekfa B. // J. Catal. 2010. V. 272. № 2. P. 262. https://doi.org/10.1016/j.jcat.2010.04.008
Колесников И.М. Катализ в газонефтяной отрасли. М.: 2012. 471 с.
Темкин М.И., Морозов Н.М., Апельбаум Л.О. и др. // Проблемы физической химии. 1959. № 2. С. 14.
Морозов И.М., Лукьянова М.И., Темкин М.И. // Кинетика и катализ. 1966. № 1. С. 172.
Maniak G., Stelmachowski P. // Catalysis communication. 2011. № 15. P. 127. https://doi.org/10.1016/j.catcom.2011.08.027
Кузьмина Р.И., Севостьянов В.П. // Рос. хим. журн. о-ва им. Д.И. Менделеева. 2000. Т. 44. № 1. С. 71.
Денисова К.О., Ильин А.А., Румянцев Р.Н. и др. // Теорет. основы хим. технологии. 2020. Т. 54. № 6. С. 784. https://doi.org/10.31857/S004035712005005X
Денисова К.О., Ильин А.А., Румянцев Р.Н. и др. // Журн. общ. химии. 2020. Т. 90. № 6. С. 948. https://doi.org/10.31857/S0044460X20060169
Pirngruber G.D., Frunz L., Pieterse J.A.Z. // J. of Catalysis. 2006. V. 243. № 2. P. 340. https://doi.org/10.1016/j.jcat.2006.08.006
Obalova L., Maniak G., Karásková K. et al. // Catalysis Communications. 2012. V. 12. P. 1055. https://doi.org/10.1016/j.catcom.2011.03.017
Russo N., Fino D., Saracco G. et al. // Catalysis Today. 2007. V. 46. № 12. P. 4226. https://doi.org/10.1021/ie0612008
Lykaki M., Papista E. // Catalysts. 2019. № 9. P. 233. https://doi.org/10.3390/catal9030233
Ильин А.А., Румянцев Р.Н., Дубова И.А. и др. // Изв. вузов. Хим. и хим. технол. 2012. Т. 55. № 10. С. 75.
Иванова Ю.А., Сутормина Е.Ф., Исупова Л.А. // Кинетика и катализ. 2020. Т. 61. № 4. С. 577. https://doi.org/10.31857/S0453881120040103
Javoy S., Mevel R., Paillard C.E. // J. of Chemical Kinetics. 2009. V. 5. № 41. P. 357. https://doi.org/10.1002/kin.20401
Агаев С.А., Гасан-заде Г.А., Султанов М.Ю. // Азербайджанский хим. журн. 1978. № 1. С. 19.
Гайдей Т.П. // Физико-химические аспекты предельных состояний и структурных превращений в сплошных средах, материалах и технических системах. 2018. С. 34.
Cho C.M., Nunotani N., Imanaka N. // J. of Asian ceramic societies. 2019. V. 7. № 4. P. 518. https://doi.org/10.1080/21870764.2019.1675941
Grzybek G., Stelmachowski P., Stanek J.J. // Catalysis Communications. 2011. V. 1. № 15. P. 127. https://doi.org/10.1016/j.catcom.2011.08.027
Дополнительные материалы отсутствуют.
Инструменты
Журнал физической химии