Журнал физической химии, 2021, T. 95, № 9, стр. 1297-1303
Упрочнение волокнистых композитов наночастицами
a Институт проблем химической физики Российской академии наук
142400 Черноголовка, Московской обл., Россия
* E-mail: irzhak@icp.ac.ru
Поступила в редакцию 08.12.2020
После доработки 08.12.2020
Принята к публикации 21.12.2020
Аннотация
Рассмотрены способы и механизмы упрочнения полимерных волокнистых композитов путем модификации матриц наночастицами и прививки последних на волокна: химическое осаждение из паровой фазы, электрофоретическое и химическое взаимодействие.
ВВЕДЕНИЕ
В качестве конструкционных материалов в авиакосмической промышленности, авто- и судостроении широко распространены полимерные композиты (ПК), армированные стеклянными, углеродными, органическими и другими волокнами. Тем не менее проблема их усовершенствования стоит в настоящее время и будет всегда актуальной из-за постоянно растущих требований к материалам, которые предъявляет к ним технический прогресс. Одним из перспективных подходов является использование наночастиц (НЧ) для усиления межфазного взаимодействия волокно–матрица [1], по существу, способ совмещения нано- и волокнистых композитов, на первый взгляд, принципиально различающихся: в первых НЧ служат для модификации свойств матрицы, во-вторых матрица используется для реализации свойств волокон.
Граница раздела между слоями ламинированных ПК является “слабым звеном”, ибо межслойная область лишена армирования волокном и разрушается, в первую очередь, из-за расслоения и растрескивания матрицы. Отсюда следуют способы упрочнения ПК. Одним из хорошо зарекомендовавших себя методов повышения устойчивости композитов к повреждениям и расслоению является повышение ударной вязкости матрицы, в частности, путем введения эластифицирующих агентов [2]. Альтернативные подходы к упрочнению без использования связующих применяют встроенные усиливающие элементы, иногда называемые микрозакреплениями, либо через часть ламината, либо через всю толщину сборки, чтобы снизить риск расслоения или отслоения слоев. Формирование трехмерной структуры (3D) ведет к тому, что расслоение или отслоение требует выдергивания или разрушения таких микрозакреплений [3, 4]. НЧ могут быть употреблены как с целью модификации матриц [5], так и для создания 3D-структур путем прививки на волокна [6].
МОДИФИКАЦИЯ МАТРИЦ
Наполнение полимеров НЧ придает им уникальные свойства, даже будучи в низкой концентрации. Например, добавка 5% графена [7], или 2.5% углеродных квантовых точек [8] существенно увеличивают ударную вязкость, а 3% монтмориллонита (ММТ) ведет к возрастанию трещиностойкости эпоксидного полимера [9]. Следует ожидать аналогичный эффект в ПК.
Действительно, в работе [10] различные НЧ, такие как коллоидный диоксид кремния, технический углерод и углеродные нанотрубки (УНТ), были использованы для оптимизации эпоксидной матрицы армированного стекловолокном композита. Нанометровый размер позволил применять их в качестве армирующих частиц в стеклопластиках, изготовленных методом литья. Во время отверждения было приложено электрическое поле, чтобы ориентировать нанонаполнители в z-направлении. Прочность на межслойный сдвиг композитов, модифицированных НЧ, была значительно увеличена: максимум на 24.5% (УНТ), минимально на 7.5% (технический углерод), а вязкость разрушения увеличилась на 42% при добавлении 0.3 мас. % УНТ.
А.К. Pathak и др. [11] рассмотрели методы усиления углепластиков с использованием графена для модификация связующего (рис. 1). Как видно, максимальные значения свойств: межслоевой прочности (ISS), изгибных прочности (σ) и модуля (Е) – приходятся на 0.3 мас. %. По мнению авторов, увеличение прочности может быть результатом усиления межфазного взаимодействия волокна с эпоксидной матрицей через оксид графена. Однако нужно учитывать его способность повышать трещиностойкость полимера [12]. Снижение эффективности с ростом концентрации НЧ обычно связывают с агрегацией последних.
Рис. 1.
Зависимости механических свойств углепластика от концентрации оксида графена: межфазная прочность на сдвиг (а), изгибные прочность (б) и модуль (в); С – концентрация оксидов графена в эпоксидном связующем. Данные [11].
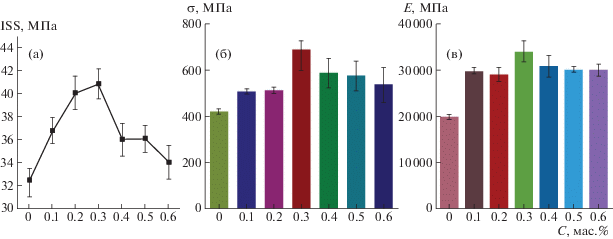
Сравнение стеклоппластиков при одинаковой приложенной циклической нагрузке 220 МПа показало [13], что усталостная долговечность образцов с добавкой 0.1 мас. % графена и однослойных УНТ увеличилась примерно в три и двенадцать раз, соответственно. Высокая эффективность последних очевидна.
В работе [14] в связующее углепластика добавляли 1.5 мас. % многослойных УНT, которые были ориентированы в поперечном направлении с помощью магнитного поля. Этому процессу способствовало добавление магнитных НЧ, которые в процессе отверждения прилипали к УНТ за счет адсорбции. Такая процедура привела к значительному увеличению трансверсальной жесткости углепластика (рис. 2).
Рис. 2.
Зависимости трансверсальных свойств углепластика (1–3) и матрицы (4, 5) от состава: кривые деформации (а), модуль (б). Углепластик с добавкой ориентированных УНТ (1), неориентированных УНТ (2), без добавки (3); матрица с добавкой УНТ (4), без добавки (5); F – нагрузка, ε – деформация. Данные [14].
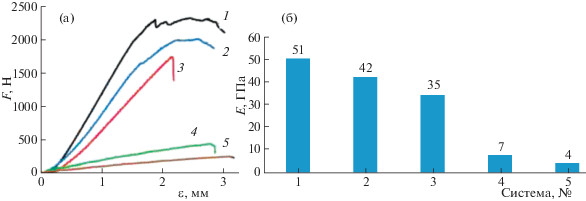
А.Э. Дворецкий и др. [15] предположили, что при изготовлении препрега с наномодифицированным связующим УНТ осаждаются, в основном, на поверхности жгутов углеродной ткани и образуют в межслоевом пространстве слой НК толщиной ∼2 мкм с содержанием УНТ ∼0.5–1 мас. % вместо исходных 0.008%. Авторы считают, что формированием именно такой структуры композита из чередующихся однонаправленных слоев микроволокон и матов-прокладок из НК можно объяснить увеличение прочности межслоевого сдвига благодаря улучшению упруго-прочностных характеристик слоя связующего в зазоре между слоями волокон.
Однако приведенные в обзоре [16] данные показывают, что в эпоксидных НК порог перколяции находится в интервале 10–3–10–1 мас. %. Таким образом, нет нужды в допущении концентрирования УНТ в межфазном слое и запрете проникновения НЧ в межволоконное пространство.
В работе [17] показано, что среднее увеличение прочности и модуля упругости при изгибе углеродных тканых композитов при добавке 1.5 мас. % карбоксилированных многослойных УНT повысились на 28% и 19% соответственно. Кроме того, ударная вязкость выросла на 33%. С помощью моделирования методом конечных элементов продемонстрировано, что при изгибе по оси доминируют волокна, а при изгибе поперек оси доминирует матрица.
Диспергирование 0.5 мас. % фуллерена в матрице углепластика увеличило прочность на растяжение и сжатие всего лишь на 2–12%, зато вязкость межслойного разрушения выросла примерно на 60% [18]. Этот эффект обусловлен тем, что небольшое количество фуллерена (0.1–1 мас. %) увеличивает вязкость разрушения самой эпоксидной матрицы.
Такое же воздействие оказывает ММТ [19]: вязкость межслойного разрушения увеличивается на 85% при введении в эпоксидную смолу 4% НЧ, прочность на изгиб растет на 38% при добавке 2% ММТ.
В работе [20] обсуждается вопрос о синергизме на примере углеродных нановолокон (УНВ). На рис. 3 приведены кривые сопротивления росту трещин при квазистатической нагрузке для неармированных и армированных по всей толщине ламинатов, содержащих 0.82 об. % УНВ и/или 0.5 об. % z-штифтов.
Рис. 3.
Кривые сопротивления росту трещин при квазистатической нагрузке для неармированных (1) и армированных по всей толщине ламинатов, содержащих УНВ (2), z-штифты (3) и (4) УНВ + z-штифты; E – энергия межслоевого разрушения, l – длина расслоения. Данные [20].
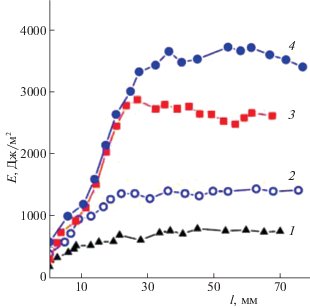
Как видно, УНВ в меньшей степени, z-штифты эффективнее препятствуют расслоению углепластика. Однако совместное воздействие более результативно. Причем на первой стадии, по-видимому, определяющую роль играет каркас, сформированный z-штифтами (растущие участки кривых 3 и 4). Тормозящее действие УНВ проявляется (кривая 4) только на стадии запределивания кривой 3. Любопытно, что в этой области развития трещины УНВ сами по себе столь же неэффективны (кривая 2). Важно отметить, что при одновременном использовании УНВ и z-штифтов они обеспечивали гораздо большее повышение трещиностойкости. УНВ эффективны для повышения вязкости межслойного разрушения при квазистатическом нагружении за счет собственных (т.е. удвоения или разветвления трещин и роста пустот в эпоксидной смоле) и внешних (т.е. перекрытия трещин и вытягивания УНВ) механизмов. Z-штифты вызывают значительное внешнее упрочнение, прежде всего, за счет перекрытия трещины.
Более эффективным использованием НЧ, чем модификация матриц, является обработка волокон. Так, например, повышение прочности на межфазный сдвиг на 45.2% и 10.14% было достигнуто для композитов на основе волокон, модифицированных УНТ, и композитов на основе матрицы, армированной УНТ, соответственно [21]. Влияние армирования наноглиной, локализованной на границе раздела волокно/матрица и распределенной по матрице, на путь трещины, механизмы повреждения и усталостные характеристики исследовали в численных экспериментах [22]. Было обнаружено, что в первом случае композиты обеспечивают более высокий срок службы и устойчивость к повреждениям, чем композиты с НЧ, распределенными в матрице.
ОБРАБОТКА ВОЛОКОН
Методы обработки поверхности существенно влияют на шероховатость, поверхностную энергию и активные химические группы волокон. Разработаны следующие способы.
Химическое осаждение из паровой фазы (CVD) – это подход grafting out, который при высоких покрытиях облегчает перпендикулярное выравнивание УНТ на поверхности углеродных волокон [23]. Существенным недостатком метода является то, что нанесение катализаторов и температурное воздействие на волокна обычно приводит к ухудшению их механических свойств.
Электрофоретический метод grafting to обеспечивает равномерное осаждение НЧ с высокой скоростью. Однако надо учитывать необходимость иметь в системе электропроводящие элементы, каковыми являются, например, углеродные волокна. Ориентация УНТ отличается от достигаемой при CVD: они преимущественно лежат на поверхности волокна [24].
В случае химической прививки grafting to требуется активация как волокон, так и НЧ. Например, прививка УНТ на углеродное волокно включает карбоксилирование первых, а второе нужно функционализировать аминовыми, карбоксильными или гидроксильными группами [25].
Особое место занимает метод модификации поверхностного слоя волокон путем включения НЧ, но без прививки.
Метод CVD
В работе [26] многослойные УНT были синтезированы на углеродных волокнах методом CVD. Ориентацию и длину (16.6–108.6 мкм) УНT определили силанизация поверхности волокна и время роста (30–120 мин). С увеличением последнего росла удельная поверхность с 22.7 до 60.2 м2/г. При этом растет смачиваемость волокна связующим. В то же время прочность на разрыв постоянно снижается. В частности, при росте в течение 120 мин последняя уменьшается примерно на 33.5% от исходной. Значительное увеличение межфазной прочности на сдвиг до 175% достигается для выровненных УНT длиной 47.2 мкм (47.8 МПа) по сравнению с исходными волокнами (17.4 МПа). Но волокна с привитыми УНТ длиной 63.5 и 108.6 мкм показали небольшое снижение межфазной прочности, возможно, из-за асимметричности покрытия.
K. Kim и др. [27] нашли, что прочность на разрыв углеродных волокон увеличена более чем на 14% за счет каталитического (Ni) роста УНТ на их поверхности. Прочность на межфазный сдвиг при этом значительно (∼470%) повышается. Использование биметаллического катализатора Ni-Fe было ключевым для синтеза УНТ при относительно низкой (500°C) температуре [28]. В этих условиях диффузия катализатора в углеродные волокна при CVD была ингибирована, что способствовало равномерному росту УНТ только на поверхности и минимизировало внутренние структурные изменения волокон.
Электрофоретические методы
Q. Song и др. [29] получили композит с углеродной матрицей, причем для нанесения УНТ на карбоновые волокна применяли электрофорез. Показано, что дисперсия УНТ на поверхности волокна однородна, проникновение их в жгут также хорошее. Привитые УНТ произвольно ориентированы и лежат в плоскости, параллельной оси волокна. После прививки УНТ в течение 4, 8, 15, 30 и 60 с предел прочности жгута на разрыв увеличился с 380 до 433, 455, 508, 567 и 652 МПа соответственно. Напротив, предел прочности композитов, усиленных УНТ, выращенными методом CVD, составлял всего 268 МПа.
При включении УНТ в углепластик тем же способом прочность на межфазный сдвиг увеличился на 124% [30]. Методом фрактографического анализа было установлено, что в структуре гибридной поверхности заметно уменьшились длина вытягивания волокна и размер трещин между волокном и матрицей, что указывает на улучшение передачи напряжения и повышение прочности на межфазный сдвиг.
В процессе производства промышленные углеродные волокна после химической обработки поверхности, такой как электролитическое окисление, кислотная промывка и плазменная обработка, всегда покрываются тонкой пленкой проклеивающего агента, который обычно представляет собой раствор или эмульсию, состоящую из полимерных компонентов и вспомогательных веществ. Химическая обработка поверхности может увеличить количество активных функциональных групп на поверхности волокна, а процесс проклейки в основном направлен на защиту волокон от повреждений и повышение совместимости между волокном и матрицей. Проклеивающий агент изменяет свойства поверхности углеродного волокна, его смачиваемость и химическое взаимодействие с эпоксидными матрицами [31].
В работе [32] после электрофоретического осаждения проводили процесс проклейки. Слой УНТ был защищен пленкой полифталазинонэфиркетона. Введение УНТ в композит, армированный углеродным волокном, привело к увеличению прочности на межслойный сдвиг на 35.6%.
В работе [33] для стимулирования диспергирования НЧ оксида графена (OГ) в матрице и улучшения межфазной адгезии между OГ и эпоксидной матрицей НЧ были химически модифицированы циануровой кислотой и диэтилентриамином. Функционализированный OГ равномерно распределился по поверхности волокон. В результате было получено значительное увеличение (104.2% и 100.2%) прочности на межфазный и на межслойный сдвиг, модуля и прочности на изгиб (рис. 4).
Рис. 4.
Свойства композитов при изгибе: (а) кривые деформации, (б) прочность и модуль упругости. Композит без добавки (1), с добавкой нефункционализированных (2) и функционализированных ОГ (3–6); концентрация, мас. %: 0 (1), 0.5 (2, 4), 0.1 (3), 1.0 (5) и 1.5 (6); σ – напряжение, ε – деформация. Данные [33].
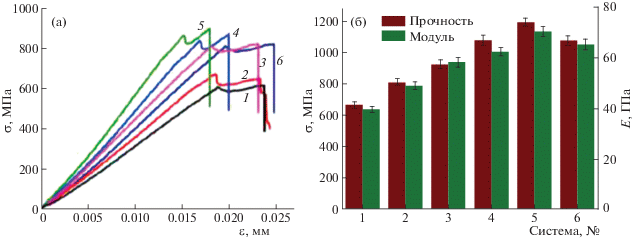
Как видно, оптимальной является концентрация 1.0 мас. % функционализированного ОГ в проклеивающих слоях углепластика. При этом предельная деформация падает (рис. 4а, кривая 5).
J. Zhang и др. [34] изучали процессы осаждения УНТ на поверхность стекловолокна, которые включали электрофоретическое осаждение и традиционный метод нанесения покрытия погружением. Оказалось, что первый метод по сравнению со вторым обеспечивает более однородное и непрерывное распределение нанотрубок на поверхности стекловолокна. Когда волокна смешиваются с эпоксидной смолой, УНТ заметно не мигрируют от поверхности стекловолокна из-за перепутанности нанотрубок. В результате сопротивление межфазному сдвигу микропластика из одиночного волокна увеличилось более чем на 30%.
B работе [35] утверждается, что электрофоретическое осаждение – многообещающий метод нанесения однослойных УНТ на непроводящие стеклоткани и изготовления композитов при большой загрузке НЧ, расширяющий возможности применения композитов из стеклопластика. Принимая во внимание изоляционные свойства, стеклоткань закреплялась на стальной пластине и использовалась в качестве отрицательного электрода, чтобы положительно заряженные НЧ могли к нему мигрировать. Другая стальная пластина использовалась в качестве положительного электрода.
Методы химической прививки
Прививка НЧ на углеродные волокна ограничивается низкой реакционной способностью графитового углерода. Следовательно, существует потребность в создании новых методов прививки с универсальными функциональными группами. Таковыми, например, являются карбоновые кислоты, которые могут взаимодействовать со многими органическими и неорганическими материалами.
F. Zhao и Y. Huang [36] с целью изменения поверхностной энергии, увеличения смачиваемости или шероховатости поверхности углеродных волокон для улучшения их связи с матрицей функционализировали НЧ силсесквиоксана. Для этого сначала проводили реакцию окисленных азотной кислотой волокон с этилендиамином, а затем аминогруппы реагировали с НЧ. В результате функционализации углеродных волокон межфазная прочность увеличивается с 46.8 МПа до 80.6 МПа. Влияние прививки НЧ на межфазные свойства композитов при динамической нагрузке демонстрирует рис. 5, на котором показано изменение действительного модуля (E') и $\operatorname{tg} \delta $ в зависимости от температуры для композитов, армированных необработанными и модифицированными углеродными волокнами. Как видно, E' увеличился с 56 до 65 ГПа ниже Tg и с 2.9 до 4.1 ГПа выше Tg. Температура стеклования композитов с необработанными волокнами составляла ∼139°C, а Tg модифицированных композитов ∼152°C.
Рис. 5.
Изменение действительного модуля E' (1, 2) и $\operatorname{tg} \delta $ (1', 2') в зависимости от температуры для композитов, армированных необработанными (1, 1') и модифицированными (2, 2') углеродными волокнами. Данные [36].
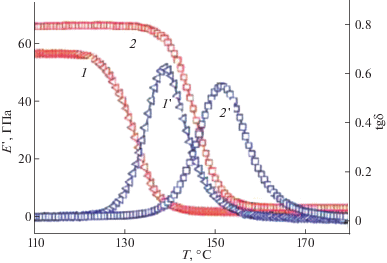
Высокая кристалличность арамидных волокон делает их поверхность химически инертной и микроскопически гладкой. В результате их адгезионная связь с большинством матриц плохая, и обычно требуется обработка поверхности для усиления взаимодействия [37]. Одним из подходов является прививка таких НЧ, как УНТ [38, 39], ОГ [40], TiO2 [41], ZnO [42].
W. Chen и др. [38] предложили следующий подход. Для введения аминогрупп, с которыми реагировали многослойные УНТ, функционализированные COCl, кевларовые волокна были обработаны раствором, состоящим из гексаметилендиизоцианата, 1,4-диазабициклооктана и толуола. После прививки УНТ межфазная прочность композита выросла с 37.5 до 49.1 МПа.
В работе [40] для создания на поверхности волокон Кевлара слоя, содержащего аминогруппы, провели сополимеризацию аллиламина и октадиена (мольное соотношение 3/1) с использованием плазмы. Затем функционализированные волокна обработали 10-процентным раствором ОГ с рН, равным 6 или 9. Лучший результат получен во втором случае: среднее значение прочности на разрыв модифицированных волокон выросло на ∼8%, межфазная прочность на сдвиг увеличилась на 44.7%.
Модификация поверхностного слоя
В работе [43] раствор УНТ/полиакрилонитрил был распылен на поверхности тканых материалов из углеродных волокон, и УНТ были зафиксированы в поверхностном слое волокон термической обработкой при 300°C. Композиты с УНТ были изготовлены с использованием тканых материалов путем сборки из стекломатов при вакуумной упаковке (VARTM) [44]. Углепластик с УНТ показал повышение прочности на разрыв на 22% по сравнению с исходным композитом.
M. Rafiee с соавторами [45–47] разработали производственный подход изготовления стеклопластиков с применением НЧ при одновременном армировании матрицы и волокон, воспользовавшись методом VARTM. НЧ добавлялись в композиты в два приема: один для проклейки ткани, другой – для усиления матрицы. Проклейку стекломатов раствором заданного состава проводили при помощи пистолета-распылителя внутри вытяжного шкафа с целью обеспечения полного испарения растворителя. Использование НЧ (УНТ, графен, ОГ и т.п.) привело к значительному улучшению механических [45], теплофизических [46] и усталостных [47] свойств стеклопластиков.
ЗАКЛЮЧЕНИЕ
Данный обзор не претендует на исчерпывающее изложение и анализ всех опубликованных к настоящему времени результатов по применению НЧ для усиления волокнистых композитов. В частности, проигнорирован обзор A. Мirabedini и др. [48], в котором рассмотрены углепластики с использованием для этих целей графена. В задачу предлагаемой статьи входит демонстрация синергизма при совмещении нано- и волокнистых композитов. Подчеркнуто, что прививка НЧ на волокна более эффективна, чем модификация матрицы.
Работа выполнена в рамках госзадания ИПХФ РАН (регистрационный номер темы АААА-А19119032690060-9).
Список литературы
Куперман А.М., Горбаткина Ю.А., Турусов Р.А. // Хим. физика. 2012. Т. 31. № 8. С. 50.
Водовозов Г.А., Осипчик В.С., Мараховский К.М. и др. // Успехи химии хим. технологии. 2015. Т. 29. № 10. С. 20.
Park Y.-B., Lee B.-H., Kweon J.-H., Choi J.-H. and Choi I.-H. // Compos. Struct. 2012. V. 94. № 2. P. 625.
Yun J.-H., Choi J.-H. and Kweon J.-H. // Compos. Struct. 2014. V. 108. P. 409.
Saghafi H., Fotouhi M., Minak G. // Appl. Sci. 2018. V. 8. № 12. P. 2406.
Wu Q., Zhao R., Ma Q. and Zhu J. // Compos. Sci. Technol. 2018. V. 163. P. 34.
Hussein S.I. // Nano Hybrids Compos. 2018. V. 22. P. 23.
Gobi N., Vijayakumar D., Keles O., Erogbogbo F. // ACS Omega. 2017. V. 2. № 8. P. 4356.
Kusmono K., Wildan M.W., Mohd Ishak Z.A. // Int. J. Polym. Sci. 2013. V. 2013. ID 690675.
Wichmann M.H.G., Sumfleth J., Gojny F. H., Quaresimin M., Fiedler B., Schulte K. // Eng. Fract. Mech. 2006. V. 73. № 16. P. 2346.
Pathak A.K., Borah M., Gupta A. et al. // Compos. Sci. Technol. 2016. V. 135. P. 28.
Wan Y.-J., Tang L.-C., Gong L.-X. et al. // Carbon. 2014. V. 69. P. 467.
Bourchak M., Algarni A., Khan A., Khashaba U. // Compos. Sci. Technol. 2018. V. 167. P. 164.
Aldajah S., Haik Y. // Mater. Design. 2012. V. 34. P. 379.
Дворецкий А.Э., Демичев В.И., Александров Н.Г. и др. // Констр. композ. матер. 2017. № 3. С. 34
Chen Y., Pan F., Guo Z. et al. // J. Mech. Phys. Solid. 2015. V. 84. P. 395.
Soliman E., Kandil U., Taha M. // Materials. 2014. V. 7. № 6. P. 4640.
Ogasawara T., Ishida Y., Kasai T. // Compos. Sci. Technol. 2009. V. 69. № 11–12. P. 2002.
Xu Y., Hoa S.V. // Compos. Sci. Technol. 2008. V. 68. № 3–4. P. 854.
Ladani R.B., Ravindran A.R., Wu S. et al. // Compos. Sci. Technol. 2016. V. 131. P. 98.
Zhao Z., Teng K., Li N. et al. // Compos. Struct. 2017. V. 159. P. 761.
Dai G., Mishnaevsky L. // Compos. Sci. Technol. 2014. V. 91. P. 71.
Kim K.J., Yu W.-R., Youk J.H., Lee J. // Phys. Chem. Chem. Phys. 2012. V. 14. № 40. P. 14041.
Guo J., Lu C. // Carbon. 2012. V. 50. № 8. P. 3101.
Laachachi A., Vivet A., Nouet G. et al. // Mater. Lett. 2008. V. 62. № 3. P. 394.
Lv P., Feng Y., Zhang P. et al. // Carbon. 2011. V. 49. № 14. P. 4665.
Kim K.J., Yu W.-R., Youk J.H., Lee J. // Carbon. 2013. V. 54. P. 258.
Lee G., Youk J.H., Lee J. et al. // Diamond Relat. Mater. 2016. V. 68. P. 118.
Song Q., Li K., Li H., Fu Q. // J. Mater. Sci. Technol. 2013. V. 29. № 8. P. 711.
Li Q., Church J.S., Naebe M., Fox B.L. // Carbon. 2016. V. 109. P. 74.
Ma Q., Gu Y., Li M., Wang S., Zhang Z. // Appl. Surface Sci. 2016. V. 379. P. 199.
Zhang S., Liu W.B., Hao L.F. et al. // Compos. Sci. Technol. 2013. V. 88. P. 120.
Ma L., Zhu Y., Feng P. et al. // Compos. B. 2019. V. 176. № 10. ID 107078.
Zhang J., Zhuang R., Liu J. et al. // Carbon. 2010. V. 48. № 8. P. 2273.
Li J., Wu Z., Huang C., Li L. // Compos. Sci. Technol. 2014. V. 104. P. 81.
Zhao F., Huang Y. // J. Mater. Chem. 2011. V. 21. № 11. P. 3695.
Fan W., Tian H., Wang H. et al. // Polym. Test. 2018. V. 72. P. 147.
Chen W., Qian X.-M., He X.-Q. et al. // J. Appl. Polym. Sci. 2012. V. 123. № 4. P. 1983.
O’Connor I., Hayden H., Coleman J.N. // Small. 2009. 5. № 4. P. 466.
Hussain S., Yorucu C., Ahmed I. et al. // Surf. Coat. Technol. 2014. V. 258. P. 458.
Wang B., Duan Y., Zhang J. // Mater. Design. 2016. V. 103. P. 330.
Patterson B.A., Sodano H.A. // ACS Appl. Mater. Interfac. 2016. V. 8. № 49. P. 33963.
Lee G., Ko K.D., Yu Y.C. et al. // Compos. A. 2015. V. 69. P. 132.
McCrary-Dennis M.C., Okoli O.I. // J. Reinforc. Plast. Compos. 2012. V. 31. № 24. P. 1687.
Rafiee M., Nitzsche F., Laliberte J. et al. // Polym. Compos. 2019. V. 40. № S2. P. E1732.
Rafiee M., Nitzsche F., Laliberte J. et al. // Compos. B. 2019. V. 164. P. 1.
Rafiee M., Hosseini Rad S., Nitzsche F. et al. // Polymers. 2020. V. 12. № 9. P. 2135.
Mirabedini A., Ang A., Nikzad M. et al. // Adv. Sci. 2020. V. 7. № 11. ID 1903501.
Дополнительные материалы отсутствуют.
Инструменты
Журнал физической химии