Журнал физической химии, 2022, T. 96, № 6, стр. 816-821
Получение консолидированных углеродных наноматериалов методом искрового плазменного спекания
Е. В. Суслова a, *, Е. А. Архипова a, Д. О. Московских b, С. В. Максимов a, О. Я. Исайкина a, Т. М. Иванова c, С. В. Савилов a, c
a Московский государственный университет имени М.В. Ломоносова,
Химический факультет
119991 Москва, Россия
b Национальный исследовательский технологический университет “МИСиС”
119049 Москва, Россия
c Институт общей и неорганической химии им. Н.С. Курнакова РАН
119071 Москва, Россия
* E-mail: suslova@kge.msu.ru
Поступила в редакцию 08.11.2021
После доработки 08.11.2021
Принята к публикации 10.11.2021
- EDN: SPAIGL
- DOI: 10.31857/S0044453722060267
Аннотация
Малослойные графитовые фрагменты (МГФ), содержащие 8–10 графеновых слоев, обработаны при температурах 600–1800°С и давлениях 10–50 МПа методом искрового плазменного спекания. Установлено, что при температуре 600°С порошки МГФ не консолидировались; спекание с образованием таблеток происходило при 1200–1800°С. Показано, что с увеличением как температуры, так и давления спекания графитовая структура совершенствовалась, количество углеродных слоев возрастало до 15–20; все спеченные образцы мезопористые.
Метод искрового плазменного спекания (ИПС), заключающийся в электростимулированном спекании при одновременном воздействии высоких температуры и давления, как правило, не приводит к укрупнению зерен, а во многих случаях позволяет получать материалы со значениями плотностей, близкими к теоретически рассчитанным. Метод описан для получения плотных консолидированных образцов металлов, интерметаллидов, оксидов, композитов и др. [1].
ИП-спеканием получены консолидированные без связующего образцы углеродных нанотрубок (УНТ) [2, 3], окисленных УНТ [3] фуллеренов [4, 5], графена [6], углеродных нановолокон [7], малослойных графитовых фрагментов (МГФ) [8–10] и др. Полученные консолидаты МГФ [9], УНТ или композитов УНТ-МГФ [10] не разрушаются даже после окисления парами азотной кислоты в газовой фазе. При ИП-спекании оксида графена при невысоких температурах 200–400°С и давлении 50 MПa получены 3D-пористые биосовместимые материалы [6]. Их плотность возрастала с увеличением температуры обработки до 1.45 гсм‒3 за счет формирования между графеновыми листами новых С–С-связей и одновременным элиминированием кислорода и восстановлением оксида графена до графена [6]. Спекание без давления при 1100–1500°С электрохимически эксфолиированного графита также приводит к эффективному удалению кислород-содержащих групп без изменения морфологии частиц. Полученный материал был использован в качестве электродов устройств накопления и хранения энергии [11]. При экстремальном увеличении температуры и давления ИПС (1850°С, 80 MPa) массивы из 10–30 графеновых пластин спекались с формированием монолитных образцов [12]. Однако подводимой внешней энергии ИПС оказалось достаточно, чтобы графитовые плоскости повреждались и заламывались под углом 90°. При ИП-спекании МГФ возможно образование монолитов [8] или фазовое превращение МГФ с образованием луковичных углеродных структур [9].
Цель настоящей работы – получение нерассыпающихся консолидированных методом ИПС образцов МГФ и исследование их свойств, выявление корреляций между условиями ИПС и характеристиками консолидатов, уточнение условий ИПС, при которых происходят фазовые переходы аллотропных модификаций углерода.
ЭКСПЕРИМЕНТАЛЬНАЯ ЧАСТЬ
Частицы МГФ синтезировали пиролитичеcким разложением гексана (“х.ч.”, “Реахим”) при 900°С в присутствии темплата MgO (SBET = 140 м2 г–1) в кварцевой трубе диаметром 500 мм в потоке 1000 мл мин–1 азота (99.999 %, ООО “Логика”) в течение 30 мин [13]. Темплат MgO удаляли кипячением препаратов в соляной кислоте в течение 8 ч с последующей промывкой дистиллированной водой до нейтрального значения pH промывных вод. Полученные образцы сушили 24 ч при 120°С. Отсутствие MgO в составе МГФ подтверждено гравиметрически.
Спекание осуществляли в ИПС установке Labox-625 (Sinterland, Japan) в течение 5 мин при 600–1800°С и аксиальном давлении 10–50 МПа со скоростью нагрева 100 К мин-1. Спекание проводили в листах графлекса толщиной 0.5 мм, который потом отслаивали с поверхности образцов. Диаметр спеченных объемных образцов (таблеток) составил 15 мм. Спеченные образцы обозначены МГФ_T_P, где T и P – это температура и давление обработки (табл. 1). При 600°С консолидаты получить не удалось: таблетки рассыпались после ИПС. Образцы МГФ_1200_P и МГФ_1800_P были получены в виде твердых таблеток.
Таблица 1.
Обозначения и условия получения образцов
Образец | Условия ИПС | |
---|---|---|
Т, °C | Р, MPa | |
МГФ | – | – |
МГФ_600_10 | 600 | 10 |
МГФ_600_30 | 600 | 30 |
МГФ_1200_10 | 1200 | 10 |
МГФ_1200_30 | 1200 | 30 |
МГФ_1800_10 | 1800 | 10 |
МГФ_1800_30 | 1800 | 30 |
МГФ_1800_50 | 1800 | 50 |
Морфологию УНМ исследовали с использованием просвечивающей электронной микроскопией (ПЭМ) на приборе “JEOL 2100F/Cs” (“JEOL Ltd.”, Япония) с ускоряющим напряжением 200 кВ.
Спектры комбинационного рассеяния (КР) регистрировали при комнатной температуре на спектрометре LabRamHR800 UV (“HoribaJobinYvon”, Япония) с дифракционной решеткой 500 шт/мм. Для возбуждения спектров применяли излучение ионного аргонового лазера (514.53 нм), мощность излучения на образце ~5–7 мВт. Облучение образцов и сбор рассеянного излучения осуществляли с помощью присоединенного к спектрометру оптического микроскопа Olympus BX41 через линзу с фокусным расстоянием 40 мм. Для каждого образца КР-спектры получали в трех точках и усредняли.
Значения удельной площади поверхности определяли методом низкотемпературной адсорбции азота на приборе Autosorb-1C/QMS (Quantachrome Inc., США). Перед измерениями все образцы дегазировали в вакууме в течение 3 ч при 300°С. Распределение пор по размерам рассчитывали с использованием модели BJH.
ОБСУЖДЕНИЕ РЕЗУЛЬТАТОВ
Частицы МГФ, согласно данным ПЭМ, повторяли форму MgO темплата (рис. 1а) и содержали в среднем 8–10 графеновых листов, сложенных в стопку (рис. 1б). При температуре обработки 600°С в морфологии образцов не наблюдалось каких-либо существенных изменений (рис. 1в–1з). При 1200°С и 10 МПа края углеродных листов частиц МГФ изгибались, появлялись фрагменты с меньшим количеством слоев (рис. 1ж, з), а при увеличении давления до 30 МПа количество углеродных слоев увеличивалось до 15–20, слои становились менее дефектными (рис. 1и, 1к). Образцы МГФ_1800_P характеризовались существенным увеличением толщины частиц МГФ с одновременным выравниваем углеродных слоев (рис. 1л–1р).
Рис. 1.
Изображения ПЭМ исходных МГФ (а, б), и МГФ после ИП-спекания при 600°С и 10 МПа (в, г), 600°С и 30 МПа (д, е), 1200°С и 10 МПа (ж, з), 1200°С и 30 МПа (и, к), 1800°С и 10 МПа (л, м), 1800°С и 30 МПа (н, о), 1800°С и 50 МПа (п, р).
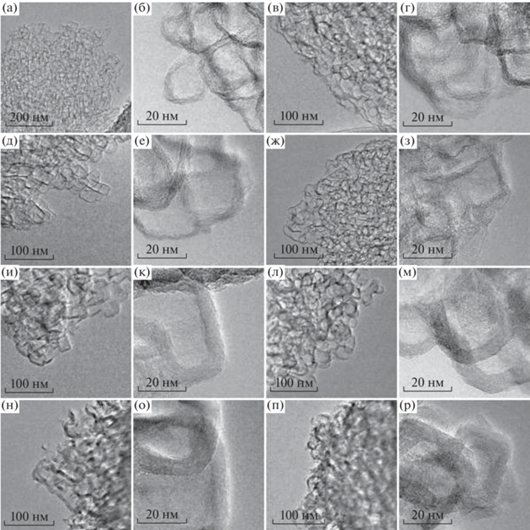
КР-спектры углерода, как правило, содержат D, G и 2D линии при 1355–1360, 1581 и 2700 см–1. Линии D и G соответствуют радиальной дыхательной моде Alg и валентным колебаниям E2g ароматического кольца C6 [14]. Линия 2D является обертоном D-линии. В КР-спектрах МГФ и МГФ после ИПС при 600, 1200°C G-линия смещена, а ее максимум приходится на 1600–1610 см–1 (рис. 2), что характерно при разупорядочении графитовой структуры, а также для частиц маленького размера [14]. Соотношение интегральных интенсивностей D- и G-линий ID/IG уменьшается при уменьшении дефектности углеродных материалов и при уменьшении sp3-гибридизованных концевых атомов углерода. Для всех спеченных образцов соотношение ID/IG меньше, чем для исходных МГФ (рис. 2). Наиболее заметно значение ID/IG понижается для образцов МГФ_1800_P, что связано с существенным увеличением температуры обработки. Также появляются высокоинтенсивные 2D-линии и обертон D + G, характерные для фазы графита. Таким образом, при повышении температуры ИПС происходило “залечивание” дефектов и совершенствование графитовой структуры, что ранее было показано в случае ИП-спекания УНТ [2, 15–17].
Рис. 2.
КР-спектры МГФ до и после ИП-спекания. В скобках рядом со спектрами указаны соотношения ID/IG.

На рис. 3 представлены изотермы адсорбции азота при 77 К. Они относятся к IV типу и имеют гистерезис типа H3 по классификации ИЮПАК, что свидетельствует о мезопористости. Значения удельной площади поверхности SБЭТ уменьшаются с увеличением температуры спекания (табл. 2). Влияние давления на SБЭТ ощутимо заметно лишь для образцов МГФ_1800_P: с увеличением P значения SБЭТ уменьшаются быстрее, чем с увеличением температуры.
Таблица 2.
Значения SБЭТ, общий объем (V) и средний диаметр (d) пор МГФ до и после ИП-спекания, вычисленные согласно модели BJH
Образец | SБЭТ, м2 г–1 | V, см3 г–1 | d, Å |
---|---|---|---|
МГФ | 550 | 1.89 | 88 |
МГФ_600_10 | 554 | 1.72 | 37 |
МГФ_600_30 | 573 | 1.88 | 79 |
МГФ_1200_10 | 502 | 1.43 | 80 |
МГФ_1200_30 | 517 | 1.26 | 37 |
МГФ_1800_10 | 501 | 1.16 | 37 |
МГФ_1800_30 | 446 | 0.81 | 39 |
МГФ_1800_50 | 340 | 0.53 | 39 |
Распределение пор по размерам, согласно модели BJH [18], представлено на рис. 4. Общий объем и средний размер пор уменьшаются с увеличением как температуры, так и давления ИПС (табл. 2). Для образцов МГФ и МГФ_600_P в распределении пор наблюдаются два максимума при 49 и 117 Å, которые при повышении температуры до 1200–1800°С превращаются в один при ~40 Å (рис. 4). Благодаря мезопористости и высоким значениям SБЭТ ИП-спеченные материалы могут быть подходящими в качестве адсорбентов [8], катализаторов [19] или их носителей и электродов устройств накопления и хранения энергии [11].
Консолидация происходит за счет уплотнения частиц и возникновения перешейков между ними и связана с процессами, происходящими на поверхности частиц. В случае спекания однофазной системы при постоянной температуре можно выделить не менее шести одновременно протекающих процессов: поверхностная, объемная и зернограничная диффузия вещества, испарение и переход в газовую фазу атомов и ионов, которые участвуют в образовании плазмы, перекристаллизация поверхности.
Процессы, проходящие при ИП-спекании УНМ ранее неоднократно обсуждались [1–3, 15]. В случае УНТ и МГФ возможны фазовые переходы с образованием графеновых листов, связывающих отдельные УНТ [3, 15] или частицы МГФ [9] в объединенные структуры. Резистивный нагрев УНМ может приводить к локальному перегреву в непроводящих точках и в местах с поверхностно-непроводящей пленкой, вследствие чего происходит пробой с образованием плазмы и последующим массопереносом через газовую фазу [1–3, 9, 20, 21]. Уплотнению и усадке образцов во время ИПС способствует высокое давление, которое равномерно распределяется в объеме образцов [1].
В настоящей работе нагрев до 600°С, вероятно, оказался недостаточным для перекристаллизации через газовую фазу и объединения отдельных фрагментов в общие структуры, поэтому порошки МГФ рассыпались. Отметим, что ранее образцы аморфного углерода также не удалось консолидировать при существенно более высоких значениях температуры и давления ИПС (1100–1300°C, 35 МПа) [22]. В настоящей работе показано, что никаких фазовых превращений МГФ не происходило, а графитовая структура лишь совершенствовалась.
В заключение следует отметить, что прогнозировать результаты при ИП-спекании углеродных наноматериалов достаточно сложно ввиду неоднородности структуры партий препаратов, полученных даже при одинаковых условиях синтеза. На возможность осуществления фазовых переходов в первую очередь влияют температура ИПС и сопротивление частиц порошков.
Список литературы
Hu Z.Y., Zhang Z.H., Cheng X.W. et al. // Mat. Design. 2020. V. 191. P. 108662. https://doi.org/10.1016/j.matdes.2020.108662
Suslova E., Savilov S., Egorov A. et al. // Micropor. Mesopor. Mat. 2020. V. 293. P. 109807. https://doi.org/10.1016/j.micromeso.2019.109807
Suslova E.V., Chernuak S.A., Maksimov S.V., Savilov S.V. // Carbon. 2020. V. 168. P. 597. https://doi.org/10.1016/j.carbon.2020.07.026
Zhang F., Ahmed F., Holzhuter G., Burkel E. // J. Cryst. Growth. 2012. V. 340. P. 1.
Jun T.S., Park N.H., So D.S. et al. // J. Korean Cryst. Growth Cryst. Technol. 2013. V. 23. P. 27.
Chakravarty D., Tiwary C.S., Woellner C.F. et al. // Adv. Mater. 2016. V. 28. P. 8959. https://doi.org/10.1002/adma.201603146
Kanari M., Tanaka K., Baba S., Eto M. // Carbon. 1997. V. 35. № 10–11. P. 1429.
Strokova N., Savilov S., Xia H. et al. // Z. Phys. Chem. 2016. V. 230. P. 1719. 2016.https://doi.org/10.1515/zpch-2016
Suslova E.V., Epishev V.V., Maslakov R.I. et al. // Appl. Surf. Sci. 2020. V. 535. P. 147724. https://doi.org/10.1016/j.apsusc.2020.147724
Суслова Е.В., Епишев В.В., Максимов С.В. и др. // Журн. физ. химии. 2021. Т. 95 (7). С. 1068.
Gong Y., Ping Y., Li D. et al. // Appl. Surf. Sci. 2017. V. 397. P. 213.
Nieto A., Lahiri D., Agarwal A. // Carbon. 2012. V. 50. P. 4068.
Savilov S.V., Strokova N.E., Ivanov A.S. et al. // Mat. Res. Bull. 2015. V. 69. P. 13.
Сморгонская Э.А., Звонарева Т.К., Иванова Е.И. и др. // Физика тв. тела. 2003. Т. 46. Вып. 9. С. 1579.
Ham H., Park N.H., Kang I. et al. // Chem. Commun. (J. Chem. Soc. Sect. D). 2012. V. 48. P. 6672.
Laurent C., Chevallier G., Weibel A. et al. // Carbon. 2008. V. 16. P. 1812.
Yamamoto G., Sato Y., Takahashi T. et al. // J. Mater. Res. 2006. V. 21. P. 1537.
Sing K.S.W., Everett D.H., Haul R.A.W. et al. // Pure Appl. Chem. 1985. V. 57. P. 603.
Savilov S., Suslova E., Epishev V. et al. // Nanomat. 2021. V. 11. P. 352. https://doi.org/10.3390/nano11020352
Olevsky E.A., Kandukuri S., Froyen L. // J. Appl. Phys. 2007. V. 102. P. 114913. https://doi.org/10.1063/1.2822189
Сивцов А.А., Герасимов Д.Ю., Евдокимов А.А. // Российские нанотехнол. 2015. Т. 10. С. 777.
Sakamoto N., Shida S. // Diam. Relat. Mater. 2014. V. 50. P. 97.
Дополнительные материалы отсутствуют.
Инструменты
Журнал физической химии