Журнал физической химии, 2023, T. 97, № 4, стр. 570-574
Ингибирование образования пирофорных коррозионных отложений
И. И. Реформатская a, *, И. Р. Бегишев a, И. И. Ащеулова a, А. Н. Подобаев b, Д. А. Петрилин a, А. В. Бабурин a
a Академия государственной противопожарной службы МЧС России
Москва, Россия
b Московский политехнический университет
Москва, Россия
* E-mail: reformir@yandex.ru
Поступила в редакцию 17.05.2022
После доработки 08.10.2022
Принята к публикации 10.10.2022
- EDN: TGQVEU
- DOI: 10.31857/S0044453723040246
Аннотация
В результате лабораторных исследований и натурных испытаний установлено, что основной причиной самовозгораний резервуаров с сернистой нефтью является присутствие в продуктах коррозии внутренних поверхностей их стенок дисульфида железа, являющегося пирофорным соединением. При ведении азота в парогазовую фазу резервуара существенно снижается скорость коррозии металла, прекращается образование пирофоров и снижается вероятность их самовозгорания.
ВВЕДЕНИЕ
На предприятиях по добыче, подготовке, хранении и транспортировке нефти в качестве сырьевых, технологических и товарных резервуаров используют тонкостенные резервуары, изготовленные из углеродистых или низколегированных сталей. Товарные резервуары предназначены для сбора и хранения подготовленной (товарной) нефти, сырьевые и технологические – для предварительного отстоя нефти и отделения от нее пластовой воды. Толщина стенки резервуаров объемом 2000 и 5000 м3 составляет соответственно 2.0–4.3 мм и 2.0–7.8 мм, толщина кровли 3.0–3.5 мм.
Согласно статистическим данным наземные вертикальные резервуары (резервуар вертикальный стальной – РВС) являются наиболее пожароопасными участками нефтеперерабатывающих предприятий [1]. В качестве основных причин возгорания авторы указывают коррозию, механический и физический износ. Поскольку вопросы механического износа не входят в круг проблем, рассматриваемых в настоящей статье, мы сфокусируемся на причинах возгорания, связанных с коррозией. Ранее было показано, что кровля резервуаров и верхние пояса, контактирующие с парогазовым пространством, подвергаются остро локализованной коррозии [2–7]. При хранении сернистой нефти скорость коррозии может достигать 1.5 мм/год [8].
С целью снижения скорости коррозии стальных конструкций применяют летучие ингибиторы коррозии (ЛИК) [9, 10]. Имеется опыт применения ЛИК для защиты от коррозии нефтепроводов [11–13]. Известно, что возможно их использование для защиты от коррозии конструкций с нарушениями герметичности [14], наличием конденсата влаги на поверхности [15] и в сероводородсодержащей среде [16]. Именно такие условия создаются на внутренней поверхности нефтяных резервуаров, однако использование ЛИК как ингибиторов коррозии эффективно при защите стальных конструкций от равномерной коррозии, а коррозия внутренней поверхности нефтяных резервуаров развивается по механизму питтинговой или язвенной. Хорошо известно, что использование ингибиторов для предотвращения питтинговой коррозии имеет положительный эффект только при защите вновь вводимого в строй оборудования, когда коррозионный процесс еще не начал развиваться. Однако в настоящее время большая часть отечественных нефтяных резервуаров находится в эксплуатации уже длительное время и имеет ту или иную степень изношенности, что не позволяет рассматривать ингибиторную защиту как эффективный способ противокоррозионной защиты.
Традиционным способом противокоррозионной защиты внутренней поверхности РВС является нанесение защитных покрытий [8, 17–19]. Однако в резервуарах с сернистой нефтью практически все выпускаемые в настоящее время лакокрасочные покрытия не обладают высокой защитной способностью [20]. Напротив, в местах их отслоения происходит интенсификация коррозионного процесса и, как следствие, интенсификация образования коррозионных отложений.
Все рассмотренные способы направлены на снижение скорости коррозии внутренней поверхности резервуаров и не могут оказать значительного влияния на химический состав коррозионных отложений. Опасность коррозии РВС связана не только с потерей конструкции эксплуатационных свойств, но и с пирофорными свойствами коррозионных отложений, образующихся на участках внутренней поверхности резервуаров с сернистой нефтью, контактирующих с газовой фазой.
Целью работы является нахождение способов ингибирования образования пирофорных коррозионных отложений и выяснение возможности их перевода в непирофорную форму.
МЕТОДИКА ЭКСПЕРИМЕНТА
В лабораторных условиях определяли скорость образования коррозионных отложений. В качестве корродирующего металла использовали образцы стали 20 размером 20 × 30 × 0.5 мм, площадью 12 см2, массой не более ~4.7 г. Вблизи одной из коротких сторон образцов для их крепления просверливали отверстие диаметром 2–3 мм. Длительность лабораторных испытаний составляла до ~11 000 ч с интервалом извлечения образцов 1500–2000 ч. Скорость роста коррозионных отложений (мм/год) рассчитывали исходя из их общей массы и плотности, а также площади поверхности металла, на которой они образовались. Данные лабораторных испытаний сравнивали с результатами, полученными за то же время в натурных условиях (резервуары с сернистой нефтью).
Для имитации условий, реализующихся в резервуарах, были сконструированы и собраны специальные установки, позволяющие размещать образцы в газовой фазе над уровнем нефти, а также регулировать состав газовой фазы. Испытания проводили в естественной газовой фазе резервуаров с сернистой нефтью и газовых смесях на основе N2 с содержанием кислорода (%): 0; ~5.3; ~6.8; ~12.5; ~21.
По результатам испытаний на аналитических весах с точностью взвешивания 1 × 10–6 г определяли массу коррозионных отложений, образовавшихся на поверхности образцов за время испытаний. После определения массы коррозионных отложений их химический состав определяли методом энергодисперсионного анализа с использованием электронного микроскопа JEOL, оснащенного 25-канальной энергодисперсионной приставкой. Определяли общий химический состав отложений и химический состав отдельных кристаллитов, входящих в общий состав отложений. Для сравнения исследовали состав коррозионных отложений, образовавшихся на внутренней поверхности резервуаров с сернистой нефтью после их длительной эксплуатации.
Перед проведением анализа для повышения электропроводности отложений их помещали в специально сконструированные графитовые кюветы, на дно которых был предварительно нанесен проводящий клей. Затем на анализируемую поверхность отложений методом вакуумного напыления наносили тонкий слой золота.
Анализ проводили при ускоряющем напряжении на катоде 15 кВ, время сбора сигнала составляло 150–200 с, диаметр электронного пучка и глубина его проникновения в анализируемый объект – 1 мкм, максимальная чувствительность – 10–3 мас. %. Использовали три режима анализа: в точке – площадь анализируемой поверхности равна диаметру пучка; определение состава отдельных кристаллитов; определение общего химического состава отложений – размеры анализируемого объекта ~2000 × 2000 × 1 мкм (средний анализ по поверхности). При обработке результатов количественного анализа значащими считали концентрации элементов, не превышающие среднеквадратичную ошибку их определения.
Первоначально анализировали содержание в отложениях элементов, присутствующих в стали и парогазовой фазе: Fe, Cr, Ni, Mn, Si, Al, Ca, K, S, Cl, Na, Mg, Ti, P, Cu, Zn, Cl, V, Bi, Pb, O. В дальнейшем ограничились анализом элементов, присутствующих в надежно идентифицируемых количествах – Fe, Cr, Ni, Mn, S, O.
ОБСУЖДЕНИЕ РЕЗУЛЬТАТОВ
При всех использованных составах газовой фазы масса коррозионных отложений возрастает с течением времени (рис. 1), однако вне зависимости от времени испытаний наибольшая масса отложений образуется в естественной газовой фазе резервуаров с сернистой нефтью. Снижение концентрации кислорода в газовой фазе приводит к снижению массы коррозионных отложений, образовавшихся на поверхности образцов при одинаковом времени их экспозиции. Основными компонентами отложений, сформировавшихся на внутренней поверхности резервуаров с сернистой нефтью при их многолетней эксплуатации с естественной газофазной средой, являются железо и сера (рис. 2). В среднем отношение количества атомов железа к атомам серы равно 1 : 4, что в 2 раза превышает ее количество, необходимое для образования пирита (FeS2). Действительно, результаты анализа отдельных кристаллитов и внешний вид отложений свидетельствует об их гетерофазности, причем основная часть состава представлена двумя типами соединений – желтыми кристаллами серы и коричневатыми кристаллами пирита.
Рис. 1.
Зависимости общей массы отложений, образовавшихся на поверхности образцов площадью 12 см2, от времени экспозиции в газовой фазе. Состав газовой фазы: 1 – ~5.3% O2 + N2; 2 – ~6.8% O2 + N2; 3 – ~12.5% O2 + N2; 4 – ~21% O2 + N2; 5 – естественная газофазная среда, образующаяся в резервуарах с сернистой нефтью.
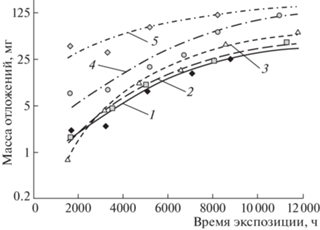
Рис. 2.
Содержание серы (1) и железа (2) в отложениях, образовавшихся на поверхности образцов стали 3, размещенных в резервуарах с естественной парогазовой фазой; l – расстояние от стенки резервуара.
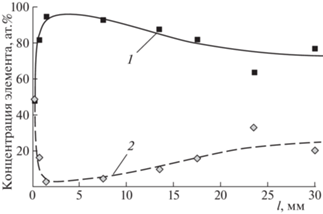
Состав отложений, образовавшихся на поверхности стали 3 в лабораторных условиях, зависит от состава газовой фазы (рис. 3). В коррозионных отложениях, сформировавшихся в газовой фазе с содержанием 21.0–5.3 об. % кислорода, содержание серы в их составе составляет 60–80 ат. %, следовательно, в указанном диапазоне составов газофазной среды стабилизировавшиеся по составу коррозионные отложения можно идентифицировать как пирит – дисульфид железа FeS2 с примесью кристаллической серы. На это указывает и внешний вид коррозионных отложений, где наряду с коричневым пиритом наблюдаются желтые кристаллы серы.
Рис. 3.
Зависимости содержания серы (1, 2, 3), железа (4, 5, 6) и кислорода (3, 6, 9) в коррозионных отложениях от времени экспозиции образцов резервуарной стали в газовой фазе, содержащей кислород в количестве: 21 об. % (1, 4, 7); 12.5 об. % (2, 5, 8); 5.3 об. % (3, 6, 9).
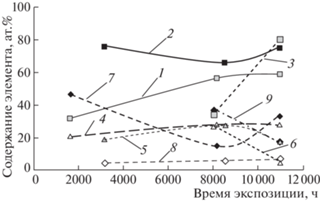
Однако при низком содержании кислорода в газовой фазе (5.3–6.8 об. %) первоначально образуется непирофорный моносульфид железа FeS, который с течением времени доокисляется до пирофорного FeS2. При содержании кислорода менее 5 об. % единственным серосодержащим соединением в составе коррозионных отложений оказывается FeS.
Скорость накопления массы коррозионных отложений с течением времени в значительной степени зависит от состава парогазовой фазы (рис. 4).
Рис. 4.
Зависимости скорости роста коррозионных отложений от времени экспозиции образцов резервуарной стали в атмосфере состава: 1 – N2 + 5.3 об. % O2; 2 – N2 + 6.8 об. % O2; 3 – N2 + 12.5 об. % O2; 4 – N2 + 21 об. % O2; 5 – естественная газофазная среда резервуаров с сернистой нефтью.
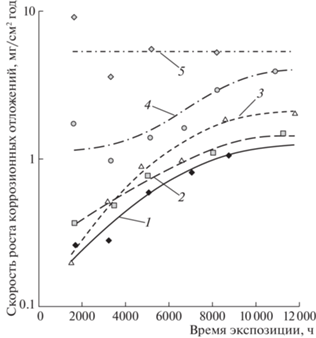
Вне зависимости от состава газовой фазы скорость роста коррозионных отложений увеличивается с течением времени.
В условиях естественной аэрации (21 об. % кислорода) скорость роста коррозионных отложений существенно выше, чем при содержании кислорода 12–5.3 об. % (рис. 4, кривые 1–4). Наиболее высокая скорость роста коррозионных отложений соответствует естественной газовой фазе резервуаров с сернистой нефтью (рис. 4, кривая 5).
Экспериментальные результаты нашли однозначное подтверждение при замене естественной парогазовой фазы резервуаров с сернистой нефтью на атмосферу азота (содержание кислорода <5 об. %). Как видно (рис. 5), перевод резервуаров на эксплуатацию с азотной подушкой (азотсодержащей газофазной средой) приводит не только к изменению доли свободной серы в отложениях (она существенно снижается), но и замене пирофорного дисульфида железа на пожаровзрывобезопасный моносульфид (отложения представляют собой смесь троилита с оксидами и гидроксидами железа). Некоторая доля свободной серы в отложениях все же присутствует, но это не оказывает решающего влияния на пирофорные свойства отложений.
Рис. 5.
Зависимости содержания серы (1, серые точки) и железа (2, черные точки) в составе пирофорных отложений, образующихся в резервуарах, переведенных на азотную подушку, от времени эксплуатации резервуара. Точки разной конфигурации относятся к данным, полученным при изучении состава отложений, извлеченных из различных резервуаров.
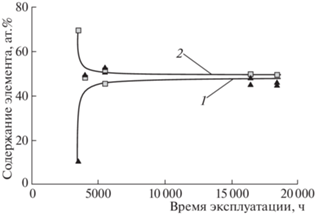
Таким образом, замена естественной парогазовой фазы резервуаров с сернистой нефтью на атмосферу азота приводит к ингибированию образования пирофорных коррозионных отложений и их переводу в непирофорную форму FeS.
ВЫВОДЫ
1. Основной причиной возгорания резервуаров с сернистой нефтью является коррозия их внутренних поверхностей в парогазовой фазе.
2. При естественном содержании кислорода в среде (~21%), коррозия внутренних поверхностей резервуаров имеет локальный характер и протекает наиболее интенсивно. В этих условиях в продуктах коррозии присутствует пирофорный дисульфид железа.
3. Введение азота в резервуар прекращает образование пирофорного дисульфида железа, при этом снижается скорость коррозии металла резервуара.
Список литературы
Мальцев А.В., Кочегаров А.В., Зубков Д.В. // Вестн. Воронежского института ГПС МЧС России (Современные проблемы гражданской защиты). 2017. № 4 (25) С. 128.
Заседателева Н.А., Реформатская И.И., Подобаев А.Н., Бегишев И.Р. // Материалы 14-й научно-технической конференции “Системы безопасности” – СБ-2005 Международного форума информатизации. 2005. С. 194.
Шишканов Б.А., Бегишев И.Р., Реформатская И.И. // Материалы 15-й научно-технической конференции “Системы безопасности” – СБ-2006 Международного форума информатизации. 2006. С. 178–180.
Заседателева Н.А., Шишканов Б.А., Ащеулова И.И. и др. // Материалы 15-й научно-технической конференции “Системы безопасности” – СБ-2006 Международного форума информатизации. 2006. С. 151.
Нисельсон Л.Н., Бегишев И.Р., Шишканов Б.А. и др. // Практика противокоррозионной защиты. 2008. № 4 (50). С. 8.
Крикунов А.А., Ленский А.Б., Бегишев И.Р. и др. // Технические газы. 2012. № 1. С. 62.
Пашкевич К.Л., Шишканов Б.А., Крикунов А.А. и др. // Инженерная практика. 2019. № 10. С. 66.
Бегишев И.Р., Реформатская И.И., Подобаев А.Н., Ащеулова И.И. // Практика противокоррозионной защиты. 2020. Т. 25. № 1. С. 44.
Гоник А.А., Калимуллин А.А., Сафонов Е.Н. Защита нефтяных резервуаров от коррозии. Уфа: РИЦАНК “Башнефть”, 1996. 264 с.
Андреев Н.Н., Гончарова О.А. // Коррозия: материалы, защита. 2012. № 7. С. 26.
Андреев Н.Н., Гончарова О.А. // Там же. 2012. № 8. С. 23.
Andreev N.N., Anufriev N.G., Sivokon I.S. // Intern. J. of Corrosion and Scale Inhibition. 2013. V. 2. № 1. P. 17.
Andreev N.N., Kuznetsov Yu.I. // Ibid. 2013. V. 2. № 1. P. 39.
Gedvillo I.A., Oleinik S.V., Sivokon I.S., Andreev N.N. // Ibid. 2013. V. 2. № 4. P. 287.
Андреев Н.Н., Лавринова Н.В., Лебедева Н.А. // Защита металлов. 2007. Т. 43. № 3. С. 276.
Кузнецов Ю.И., Андреев Н.Н., Гончарова О.А., Агафонкин А.В. // Коррозия: материалы, защита. 2009. № 10. С. 29.
Розенфельд И.Л., Рубинштейн Ф., Жигалова К. Защита металлов от коррозии лакокрасочными покрытиями. М.: Химия, 2001. 224 с.
Гоник А.А. Коррозия нефтепромыслового оборудования и меры ее предупреждения – 2-е изд., перераб. и доп. М.: Недра, 1976. 192 с.
Фахрисламов Р.З. // Строительство: наука и образование. 2014. № 1. С. 4.
Головин В.А., Ильин А.Б., Щелков В.А. и др. // Коррозия: материалы, защита. 2015. № 1. С. 14.
Дополнительные материалы отсутствуют.
Инструменты
Журнал физической химии